AMGO 408-P Manual


CONTENTS
Product Features and Specifications ......................................................1
Installation Requirement ……………………………………………………………………………….2
Steps of Installation ….........................................................................3
Exploded View ..................................................................................23
Test Run ………....................................................................................26
Operation Instruction .........................................................................28
Maintenance .....................................................................................28
Trouble Shooting ...............................................................................29
Parts List ..........................................................................................30

1
I. PRODUCT FEATURES AND SPECIFICATIONS
4-POST MODEL 408-P FEATURES
· Single point manual safety release.
· Four mechanical locking devices, each equipped with both primary
and secondly safety locks.
· Powerside column can be installed at both side, front or rear.
· Non-skid diamond platforms and adjustable safety lock ladders.
· Optional kits:Sliding jack with hand pump, caster kits, Jack tray, plastic oil tray.
MODEL 408-P SPECIFICATIONS
Model
Lifting
Capacity
Lifting
Height
Lifting
Time
Overall Length
(Inc. Ramps)
Overall
Width
Width
Between
Columns
Gross
Weight
Motor
408-P
8,000 lbs
73-3/4”
80S
207”
109-5/8”
96”
1808 lbs
2.0HP
Fig. 1

2
II. INSTALLATION REQUIREMENT
A. TOOLS REQUIRED
Tape Measure (295-1/4”)
Hammer
Level Bar
English Spanner (12")
Wrench set
Carpenter’s Chalk
Screw Sets
Pliers
Lock Wrench
Socket Head Wrench
(12#, 13#, 14#, 15#, 17#, 19#, 24#, 30#) (3#, 5#, 6#, 8#)
Fig. 2

3
B. SPECIFICATIONS OF CONCRETE (See Fig. 3)
Specifications of concrete must be adhered to the specification as following.
Failure to do so may result in lift and/or vehicle falling.
1. Concrete must be thickness 4”minimum and without reinforcing steel bars, and
must be dried completely before the installation.
2. Concrete must be in good condition and must be of test strength 3,000psi
(210kg/cm²) minimum.
3. Floors must be level and no cracks.
C. POWER SUPPLY
The electrical source must be 2.0HP minimum. The source cable size must be
2.5mm² and in good condition of contacting with floor.
III. STEPS OF INSTALLATION
A. Check the parts before assembly
1. Packaged lift and Hydraulic Power Unit (See Fig. 4).
Fig. 4
Fig. 3
Concrete intensity must be 3,000psi (210kg/cm²) minimum.
Optional Plastic oil tray

4
2. Open the outer packing carefully, check the parts according to the shipment list.
(See Fig. 5).
3. Take off the drive-thru ramps and columns (See Fig.6).
4. Loose the screws of the upper package stand, take off the offside platform, take out
the parts inside the power-side platform, then remove the package stand.
5. Move aside the parts and check the parts according to the shipment parts list
(See Fig. 7).
Fig. 6
Powerside
Platform
Drive-in
Ramp
Offside
Platform
Cross
Beam
Column
Fig. 5
Parts box
62
Fig. 7
Shipment
Parts List

5
6. Open the carton of parts and check the parts according to the parts box list
(See Fig. 8).
7. Check the parts of the parts bag according to the parts bag list (See Fig. 9).
B. Use a carpenter’s chalk line to establish installation layout as per Table 1
Make sure the size is right and base is flat (see Fig. 10).
Note: Reserve space front and behind the installation site.
B
A
C
1
Fig. 8
Fig. 9
Fig. 10
Use a carpenter’s chalk line to establish
installation layout
2

6
C. Install cross beams (See Fig.11, Fig.12).
MODEL
A
B
C
408-P
173-1/4”
109-5/8”
205”
Fig. 11
Hole towards inside
6
3
The powerside column need to be installed
according to the installed position of the
safety lock release handle.
Fig. 12

7
D. Install the Safety Ladders.
1. Take off the pulley safety cover and unscrew a nut of the safety ladders, and then
adjust the four lower nuts to be at the same position. Then install the safety ladder
(See Fig. 13).
2. Install Safety Ladders (See Fig. 14).
This height should
be the same for
four safety ladders
Safety ladder pass through the hole of
the top plate, then tighten the two nuts
Fig. 14
Fig. 13
Safety Ladder is inserted between
Limited Pins of the cross-beam
Safety Ladder
Limited Pin
Limited Pin
Unscrew A nut of the
safety ladders
18
17
Take off the cross
beam plastic cover
Insert the safety ladder
from up to the bottom
between the Limited Pins

8
E. Put the cross beams at the same height and lock on the safety ladder (See
Fig. 15).
Fig. 15
Lifting both cross beams to the
same height, it is recommended
to about 40”of height
The safety device on the
cross beam should lock
into the safety ladders at
the same level
Lifting both cross beams
to the same height.

9
F. Install power side platform.
1. Install the power side platform on the cross beams by a fork lift or manual, offset the
cross beams to the outside till the pulleys of both platforms can rest into the cross
beams’slots (See Fig.15), Install the power side platform and screw up the bolts.
Fig. 16
Offset the cross beam lean outward
when putting the powerside
platform on the cross beams
Offset the cross beam lean
outward when putting the
powerside platform on the cross
beams

10
2. Install tire stop plate with bolts and washer on the platform: Tighten the
platform on cross beam B with bolts, tighten the tire stop plate on cross beam Awith
bolts
Note: The bolts for the side with tire stop plate is longer, pay attention when
choosing the bolts (See Fig.17)
Instruction: 1). This lift is designed in both side (cross beam A and cross beam B) car
in direction, user can install the lift according to the location. Below is the installation for
the side of cross beam Bcar in direction. If choosing the side of cross beam A car in
direction, then install the tire stop plate to the other side.
2). Powerside column can be installed at any position on customers’requirement, but
the power unit must be installed near the side with the safety lock release handle.
Fig. 17
car in direction
5
Cross beam B
Cross beam A
Interchange the installed
position according to
demand
24
26
25
Tighten the platform
with bolts M16*30
27
28
Tighten the bolts
M16*35 with washer

11
G. Install offside platform and plastic block, then install the bolts for the platform
strengthen plate, check the plumbness of columns with level and adjusting with the
shims (See Fig. 18).
Fig. 18
Level bar
Install the bolts
for the platform
strengthen plate
33
9
10
32
Note: DO NOT completely tighten the
limit slide blocks. Loosen 1/4 lap after
tightening.
4
29
30
31
Position the slide blocks along
the bent edges of the columns.
Connect the slide blocks to the
cross beam with bolts.
34

12
H. Illustration for cable installation
1. Pass through the cables from the platform to the columns according to the number of
the cables (See Fig. 19).
NO.
Cable
①
②
③
④
Length (inc. fitting)
115-3/4”
(2940mm)
336”
(8535mm)
171-1/4”
(4350mm)
280-3/8”
(7120mm)
Cable installation diagram
A
C
B
35
36
37
38
Install the cylinder
connecting plate as shown
and pay attention to the
direction of unfilled corner
on the plate.
D
Fig. 19
C
A
D
B

13
2. The cable goes through the cross beam to top plate of columns and be screwed with
cable nuts (See Fig. 20).
Fig. 20
Cable goes between the
big pulley and tension
pulley
Cable pass through top
plate and be screwed
with cable nuts.
17

14
3. Illustration for platform cables (See Fig. 21).
Fig. 21
Cable ○
4
Cable ○
2
Cable ○
2
Cable ○
1
Cable ○
4
Cable ○
3
Cable ○
1
Cable ○
2
Cable ○
4
Cable ○
2
Cable ○
3
Cable ○
4
39
Hex Bolt M10*120
Cable ○
4
Cable ○
2
Limit slider

15
I. Install release handle assy. See Fig.22
Noted: Power unit must be installed near the safety release handle.
View B
Cross beam B
Cross beam A
View A
Fig. 22
44
22
45
43
45
45A
43A
Pass through the connecting bar
from the safety lock rotated device
assy. of cross beam A/B
According to the above diagram, fix lock release
handle and the safety lock connecting assy. With
M8*35 hex bolts and washers on cross beam A.
Install extend lock release handle and
plastic ball
View B
According to the above diagram, fix safety lock
connecting bar and safety lock connecting
assy. By M8*35 hex bolts and washers on cross
beam B.
Safety lock
connecting assy.
Safety lock
connecting assy.
Safety lock rotated
device assy.
Safety lock
connecting bar

16
J. Install power unit and connecting tube (See Fig. 23).
Noted: Power unit must be installed near the safety release handle.
1. Install Power unit on the cross beam A
Cross beam B
Cross beam A
View A
Fixing plate
Fig. 23
10
46
9
47
201
Drive- in
direction
40
41
40
42
Fix the connecting tube and the connecting
bar for safety device by M8*25 socket bolts
Connecting tube pass
through the fixing plate

17
2.Install Power unit on the cross beam B (See Fig. 24).
Car-in direction
40
41
40
Cross beam B
Fig. 24
42
Fixing plate
Connecting tube pass
through the fixing plate
Fix the connecting tube and the connecting
bar for safety device by M8*25″socket bolts

18
K. Install Hydraulic System
1. For power unit attached to the column of cross beam A(See Fig. 25)
Note: Oil hoses connected to oil cylinder must be passed above the cable to avoid
the oil hose scratched by cable.
a
d
Oil hose passed
above the cable
Oil return hose
passed above
the cable
b
53
Fig. 25
52
The oil hose and oil return hose
pass through the protective hose
and connect to the power unit
c、d
b
a
48
4
55
49
50
55
52
51
50
56
55
54
Oil return hose
c
Retainer
Other manuals for 408-P
1
Table of contents
Other AMGO Lifting System manuals
Popular Lifting System manuals by other brands
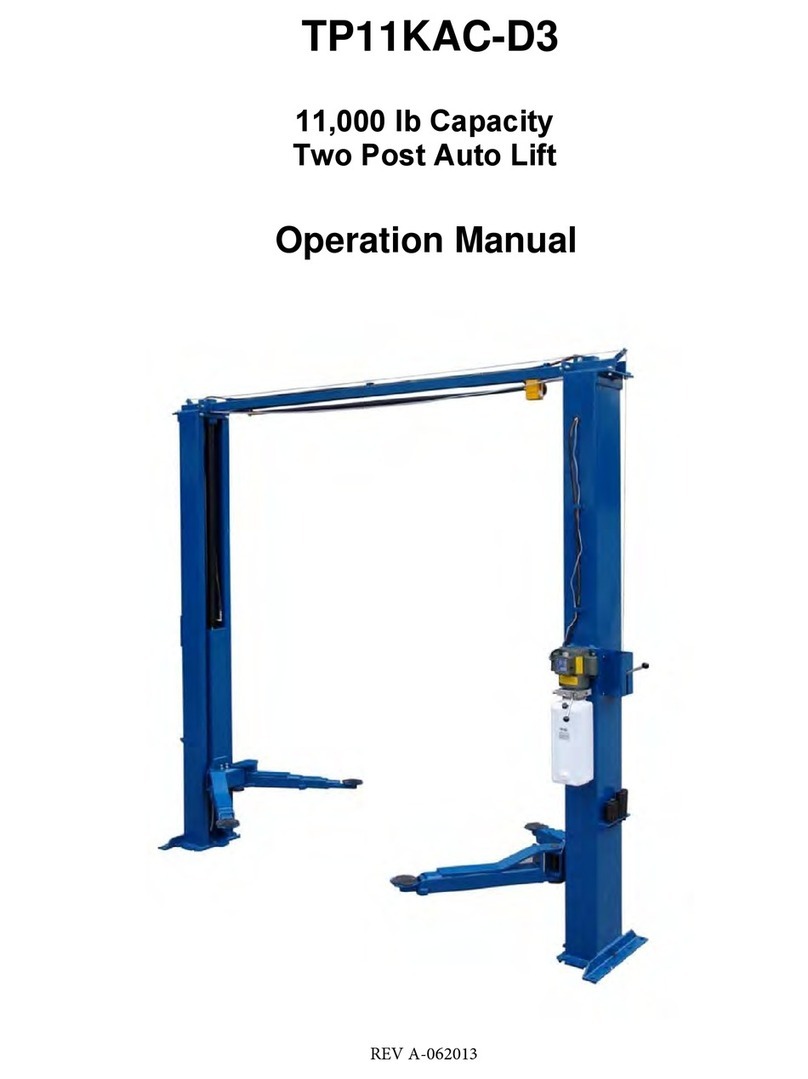
Kernel
Kernel TP11KAC-D3 Operation manual
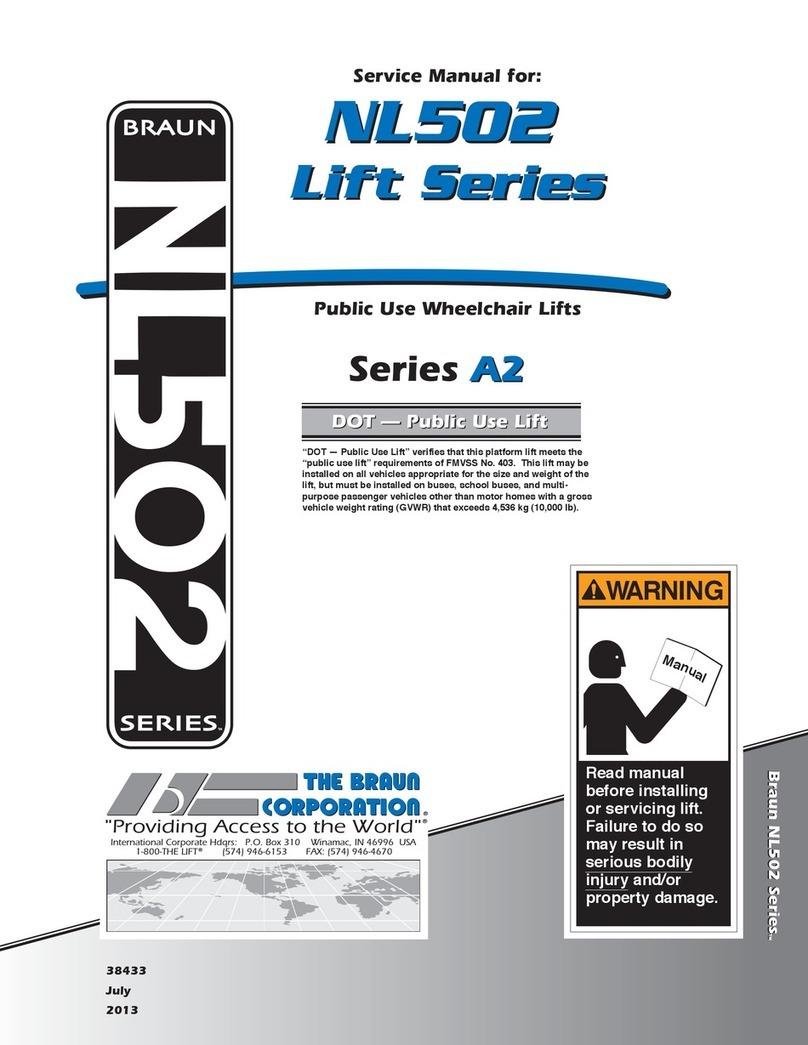
Braun
Braun NL502 Series Service manual
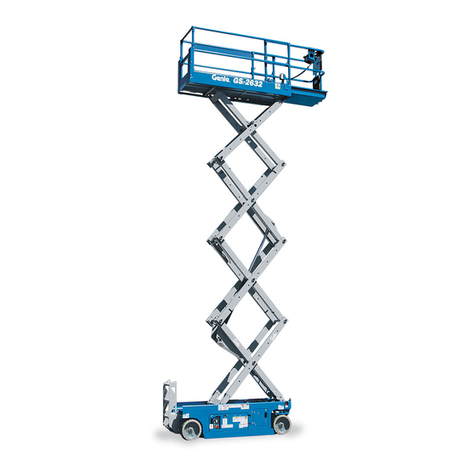
Genie
Genie GS-2632 operators manual with maintenance information
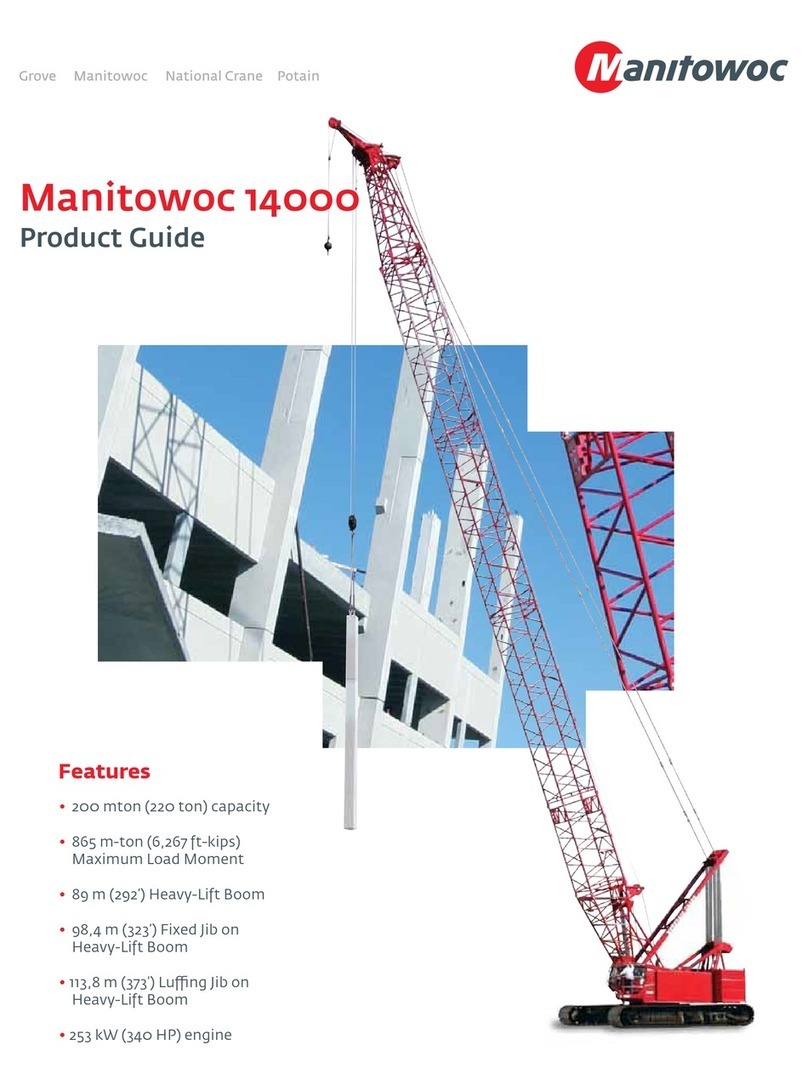
Manitowoc
Manitowoc 14000 Product guide

rav
rav RAV241XL Translation of the original instructions
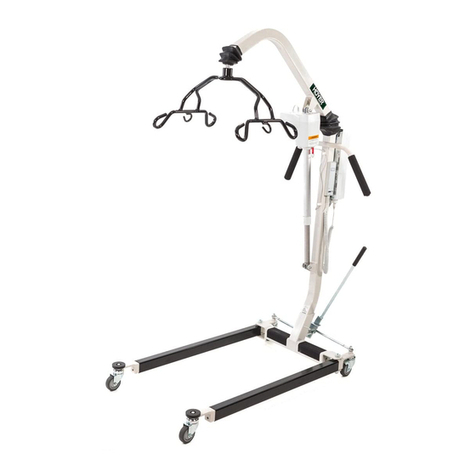
Joerns Healthcare
Joerns Healthcare Hoyer HPL402 User instruction manual & warranty