Azbil BC-R25 Series User manual

Thank you for purchasing the BC-R25
Series. This manual contains information
for ensuring the correct use of the BC-R25
Series.
This manual should be read by those who
design and maintain equipment that uses
the BC-R25 Series.
It also provides necessary information
for installation, maintenance, and
troubleshooting. Be sure to keep this
manual nearby for handy reference.
No. CP-SP-1388E
BC-R25 Series
Burner Controller
User's Manual

NOTICE
Be sure that the user receives this manual before the product is used.
Copying or duplicating this user’s manual in part or in whole is forbidden.
The information and specifications in this manual are subject to change
without notice.
Considerable effort has been made to ensure that this manual is free from
inaccuracies and omissions. If you should find an error or omission, please
contact Azbil Corporation.
In no event is Azbil Corporation liable to anyone for any indirect, special or
consequential damages as a result of using this product.
© 2015 Azbil Corporation All Rights Reserved.

i
Conventions Used in This Manual
■To prevent injury to the operator and others, and to prevent property damage, the following types of safety
precautions are indicated:
■In describing the product, this manual uses the icons and conventions listed below.
Use caution when handling the product.
The indicated action is prohibited.
Be sure to follow the indicated instructions.
Handling Precautions:
Handling Precautions indicate items that the user should pay attention to when handling
this module.
Note: Notes indicate information that might benefit the user.
This indicates the item or page that the user is requested to refer to.
(1)(2)(3) Numbers within parentheses indicate steps in a sequence or parts of an explanation.
WARNING Warnings are indicated when mishandling this product might result in
death or serious injury.
CAUTION Cautions are indicated when mishandling this product might result in
minor injury to the user, or physical damage to the product.

ii
Safety Precautions
WARNING
Use this device with combustion equipment that is started and stopped at least once in a 24-hour
period.
This device cannot be used with combustion equipment that operates continuously for 24 hours or
longer.
Before removing, mounting, or wiring the BC-R25 Series, be sure to turn off the power to the
BC-R25 Series and all connected devices. Failure to do so might cause electric shock.
If lockout occurs, reset it only after removing the cause. Also, do not enter reset input repeatedly.
Operating this product improperly could result in a serious combustion equipment accident.
Never input a reset command from a remote location. Because it is difficult to make a safety check
when far from the equipment, there is an increased risk of explosion.
This device is equipped with functions that are extremely important for the safe operation of combustion
equipment. Be sure to follow the instructions given in this manual.
Check the model number carefully and check that the sequence timing is as specied by the combustion
equipment manufacturer. Installing the wrong model can result in an explosion hazard.
Do not touch terminal 14 (F) immediately after the power has been turned o. Because the terminal retains
an electrical charge, there is a danger of electric shock.
Do not use the monitor output or alarm relay output as safety output.
This device has an operating life and should be replaced within that time. Continued use beyond the
lifespan may result in device failure.
Do not start regular operation of the equipment without rst completing the adjustments and tests for this
device, as well as the tests specied by the equipment manufacturer.
Do not disassemble this device. Malfunction, device failure, or electric shock may result.
CAUTION
In order to use this product correctly, be sure to follow this manual, the manuals for any associated
devices, and the manuals for the combustion equipment. When designing a flame safeguard
control system, please consult with a representative of the azbil Group.
Installation, wiring, inspection, adjustment, maintenance, etc. should be carried out only by trained
and experienced technicians who have knowledge and technical skills related to this product and
associated equipment.
Be sure to use this device correctly, within the ranges specified in this user's manual. Otherwise
device failure or malfunction could result.
Avoid installing the device where it will be subject to conditions such as the following. Otherwise
device failure could result.
• Certain chemicals or corrosive gases
• High temperatures
• Splashing water or excessive humidity.
• Prolonged vibration

iii
CAUTION
Wire this device in compliance with established norms, using the types of wire and wiring methods
specified in this manual. Otherwise there is a risk of device failure or malfunction.
Carry out maintenance and inspection correctly according to the methods, procedures,
replacement cycles, etc., specified in this manual.
When discarding this product, dispose of it as industrial waste, following local regulations.
Do not connect a load that exceeds the rating stated in the specifications to the control load
terminals (terminals 2–1, 2–6, 2–7, or 2–8), and do not short-circuit the load. Doing so will burn out
the internal fuse, making the device unusable. To comply with CE standards, it is necessary to take
measures to prevent the use of a device whose relay contacts can be damaged by a connected
load that exceeds the rating or by a load short-circuit. For this reason, this device uses an internal
fuse that cannot be replaced.

iv
Contents
Conventions Used in This Manual
Safety Precautions
Chapter 1. Overview
■Instructions for proper use ……………………………………………………………… 1
■Precautions on facility design …………………………………………………………… 1
■Most important points for ensuring safety …………………………………………… 1
■Model number …………………………………………………………………………… 2
■Related equipment ……………………………………………………………………… 3
Chapter 2. Installation, Wiring
■Installation method ……………………………………………………………………… 5
■Cautions regarding installation ………………………………………………………… 6
■Installation orientation …………………………………………………………………… 6
■DIN rail mounting ………………………………………………………………………… 6
■Mounting in a panel ……………………………………………………………………… 7
■Mounting/removing the device and sub-base (sold separately) …………………… 7
■Terminal numbers, front panel item names …………………………………………… 8
■Example of wiring connection with external device …………………………………10
Chapter 3. Operation
■Names of parts ……………………………………………………………………………13
■Operation …………………………………………………………………………………13
■Trial operation mode ………………………………………………………………………16
■Function selection mode (for POC and host communications (RS-485) address)……18
■Host communication settings using the Smart Loader Package (SLP-BCR) …………20
Chapter 4. Explanation of Operation
■Example of wiring connection with external device: Internal block diagram ………21
■Example sequence …………………………………………………………………………23
■Alarm and occurrence sequence …………………………………………………………37
Chapter 5. Trial Operation and Adjustment
■Preliminary inspection ……………………………………………………………………38
■Inspection procedure ……………………………………………………………………38
■Ignition spark response (UV sensor) ……………………………………………………39
■Measurement of flame voltage …………………………………………………………40
■Pilot turn-down test ………………………………………………………………………42
■Safety shutoff check ………………………………………………………………………43

v
Chapter 6. Maintenance and Inspection
■General maintenance and inspection ……………………………………………………44
■Maintenance and inspection cycle ………………………………………………………44
■Alarm codes and details …………………………………………………………………45
■Failure inspection flow ……………………………………………………………………46
Chapter 7. Specifications
■External dimensions ………………………………………………………………………49


1
Chapter 1. Overview
BC-R25 burner controllers are designed for batch operation of combustion equipment (at least one start and stop
in a 24-hour period). The BC-R25 automatically executes ignition, flame monitoring, and fuel shutoff for ON/OFF-
controlled gas burners and oil burners. Its features include a 7-segment LED display that is useful for maintenance
and a test mode that is convenient for trial runs & adjustment. In addition, it is equipped with host communication
(RS-485) and Smart Loader Package compatibility, which make more detailed monitoring and troubleshooting
possible.
•7-segment display for sequence codes and alarm codes.
•LED indicators show whether there is a flame signal and whether lock-out is present.
•The monitor outputs the operating status of the flame signal, ignition failure, flame failure and lock-out
interlock.
•Perform fault diagnosis for the internal control relay circuit.
•The product is designed so that it cannot be restarted in the case of lock-out due to ignition failure, false
flame or other causes, unless it is reset manually.
•The design complies with JIS C 9730-2-5 and JIS C 9730-1.
•The air-flow switch (OFF/ON) is checked before and after start check. (JIS B 8407)
•POC (proof of closure) function based on shutoff valve closure confirmation switch input.
•Host communication (RS-485) allowing remote observation of status
•DIN rail mounting and sub-base structure are provided for easy installation and replacement
Instructions for proper use
• This device has functions that are extremely important for the safe operation
of combustion equipment. Therefore, use the device correctly, according to this
user's manual.
• The device must be installed, wired, maintained, inspected and adjusted by
experienced specialists who have gained knowledge and skills concerning
combustion equipment and combustion safety devices.
Precautions on facility design
The facilities that use the combustion safety device must be designed taking into
careful consideration the following safety guidelines and the like.
If the system is designed to a foreign specification, refer to laws and standards in the
relevant country.
•“Technical Policy on Safety Standards for Combustion Equipment in Industrial
Furnaces,” by the Ministry of Health, Labour and Welfare
•"GeneralSafetyCodeforIndustrialCombustionFurnaces"-JISB8415
•“ForcedDraughtBurners-Part1:GasBurners”-JISB8407-1
•“ForcedDraughtBurners-Part2:OilBurners”-JISB8407-2
•“IndexofSafetyTechnologyofIndustrialGasCombustionEquipment,”byJapan
GasAssociation
•“SaftyGuidelineforGasBoilerCombustionEquipment”byTheJapanGas
Association
Most important points for ensuring safety
The design must take into consideration the following points to ensure safety.
1. Connect loads directly to the device.
2. Make sure that the start check circuit operates correctly at startup.
3. Do not make a manual operation circuit or other bypass circuit for any loads.
4. Use a redundant shutdown system for both main valve and pilot valve.

2
Chapter 1. Overview
Model number
(Note: The dedicated sub-base and sideboard are not provided with the BC-R25 series controller. Order them
separately.)
zDirect ignition type
III III IV VVI VII Example: BC-R25B1J0500
III III IV VVI VII Description
Base
model
number
Commu-
nications
function
Flame
detector
Power
supply
Function
code
Timing
Code
Additional
functions
BC-R Burner Controller
25 RS-485, with Smart Loader Package function
BFlame rod (Ionization)
C UV sensor (AUD100/110)
1100 Vac
2200 Vac
6220 Vac
JDirect ignition type
050 Pre-purge time 35 s
086 Pre-purge time 45 s
122 Pre-purge time 60 s
158 Pre-purge time 3 min
0None
D With inspection record (with data)
zInterrupted pilot type
III III IV VVI VII Example: BC-R25B1G0500
III III IV VVI VII Description
Base
model
number
Commu-
nications
function
Flame
detector
Power
supply
Function
code
Timing
Code
Additional
functions
BC-R Burner Controller
25 RS-485, with Smart Loader Package function
BFlame rod (Ionization)
C UV sensor (AUD100/110)
1100 Vac
2200 Vac
6220 Vac
G Interrupted pilot type
050 Pre-purge time 35 s
086 Pre-purge time 45 s
122 Pre-purge time 60 s
158 Pre-purge time 3 min
0None
D With inspection record (with data)

3
Chapter 1. Overview
Related equipment
zCompatible flame detector (sold separately)
•Flame detector UV sensor
Model number Name Notes
AUD15C1000 Advanced UV sensor
Tube unit
Use a dedicated socket for the AUD100C/110C/120C
AUD100C100 _ Advanced UV ame detector (Lead wire model
without AUD15C)
AUD15C1000, sold separately
AUD100C1000-A15 Advanced UV ame detector (Lead wire model
with AUD15C)
AUD15C1000 in package
AUD110C100 _ Advanced UV ame detector (Terminal block
model without AUD15C)
AUD15C1000, sold separately
AUD110C1000-A15 Advanced UV ame detector (Terminal block
model with AUD15C)
AUD15C1000 in package
AUD120C120 _ Advanced UV ame detector (1/2-inch
mounting model)
Without G1/2 adapter, AUD15C1000, sold separately
AUD120C121 _ With G1/2 adapter, AUD15C1000, sold separately
_: 0: standard product. D: with inspection record (with data).
T: tropicalization (AUD110C only).
B: inspection record (with data) and tropicalization (AUD110C only).
•Flame rod
Model number Name Notes
C7007A Flame rod holder
C7008A Flame rod assembly
zOptional parts (sold separately)
Model number Product name Notes
BC-R05A100 Dedicated sub-base for BC-R Required for all products in the BC-R25 series
81447514-001 Connector for front wiring Contains one
Weidmueller model number : BL3.5/11F
Compatible wire: 0.2–1.5 mm2(28–14 AWG)
81447514-002 Connector for front wiring
(for right-side wiring)
Contains one
Weidmueller model number : BL3.5/11/270F
Compatible wire: 0.2–1.5 mm2(28–14 AWG)
81447515-001 Side boards (2) Contains two
Not included in the sub-base
SLP-BCRJ71 Smart Loader Package
(no cable)
Compatible with BC-R25 (with communications
functions)
814 4117 7- 0 01 USB loader cable
FSP136A10 0 Analog ame meter
81447519-001 Jack cover Contains one
81447531-001 Front connector cover Mounting screw supplied

4
Chapter 2. Installation, Wiring
WARNING
Never input a reset command from a remote location. Because it is difficult to make a safety check
when far from the equipment, there is an increased risk of explosion.
This device is equipped with functions that are extremely important for the safe operation of
combustion equipment. Be sure to follow the instructions given in this manual.
Check the model number carefully and check that the sequence timing is as specified by the
combustion equipment manufacturer. Installing the wrong model can result in an explosion hazard.
Connect the load (ignition transformer, solenoid valve, etc.) directly to the output terminals of this
device.
If it is not directly connected, combustion safety cannot be ensured.
CAUTION
A ground-fault detection circuit is included in this device. Even if the power supply does not have
high and low potential sides, if a ground fault occurs due to insulation failure of a load such as an
ignition transformer, pilot valve, or main valve, this device will detect the ground fault and safely
shut off and lock out the equipment.
When mounting and wiring, be sure to follow this user's manual or the instruction manuals provided
by the equipment or system manufacturer.
Carry out the wiring work in conformity with the specified standards.
Connect the power supply last to prevent electric shock or damage. Otherwise touching terminals
by mistake may cause electric shock or may damage the device.
Make sure that loads connected to the terminals do not exceed the rating indicated in the
specifications.
Supply power at the voltage and frequency indicated on the model number label of the device.
In keeping with technical standards for electrical equipment, the burner frame must be connected
to an earth ground by a wire having a resistance of less than 100 Ω.
Run the high-voltage ignition transformer cable separately and keep it at least 30 cm away from this
device.
Keep power lines and ignition transformer high-voltage cables separate from the flame detector
wires.
Make sure that ignition transformer high-voltage cables are properly connected to prevent faulty
contact. Faulty contact can generate high-frequency radio waves, causing malfunction.
The ignition transformer ground lead should be connected directly to the burner itself or to a
metallic part electrically connected to the burner.
Be sure to check that the wiring is correct before you turn the power ON. Incorrect wiring can cause
damage or malfunction.
If the wires from this device exceed the recommended length, to prevent malfunction due to
external electrical noise, keep power wiring away from the wires running from the control panel to
the burner controller. After wiring, check that the equipment is operating properly.
Be sure to connect non-voltage contacts to the inputs of this device (terminals 16 to 29).
After the power has been turned ON, leave sufficient time before checking the output. This device
does not operate for about 8 seconds after the power has been turned ON.

5
Chapter 2. Installation, Wiring
CAUTION
The reset input (terminal 24) must be used by this device only. It cannot be shared with any other
BC-R unit.
Output common terminals 4 and 5, and input common terminals 16 and 17 cannot be shared with
any other BC-R unit.
Do not design instrumentation that shuts off the power to this device as soon as alarm output is
generated. Doing so can corrupt this device's operation history records.
To prevent malfunction due to external electrical noise, do not operate the device with the loader
cable except for trial runs, maintenance, and troubleshooting.
If there is an inverter or the like that generates strong electrical noise near this device, take noise-
suppression measures, referring to the user's manual for the noise-generating equipment.
Installation method
WARNING
Ensure you turn off the power of this device and all auxiliary devices when mounting, removing or
connecting the wires of this device. There is a risk of electrical shock.
CAUTION
Mounting, wiring, maintenance, inspection, calibration, etc. should be carried out by a professional
with technical training in combustion systems and flame safeguard control devices.
Do not install where exposed to any of the following:
• Certain chemicals or corrosive gases (ammonia, sulfur, chlorine, ethylene compounds, acids, etc.)
• Dripping water or excessive humidity
• High temperatures
• Sustained long-term vibration
For mounting and wiring, follow the instructions in this user's manual or in the combustion
equipment manufacturer's manual.
A fuse is built into the control load line of this device. Do not short-circuit the load, or the fuse will
melt. If the fuse has melted, replace the device.
When using the device as a burner control system, install it to a control panel that supports IP40 or
more. If IP40 is required for this single device, also use a side board (sold separately). The protection
structure of the device is equivalent to IP10.

6
Chapter 2. Installation, Wiring
Cautions regarding installation
•Take space 50 mm above and below, 50 mm to the left and right, and 80 mm to
the front, as space for removal, wiring, and maintenance.Also,donotinstallthis
device close to electric power devices or other sources of heat.
•This device must be grounded within a grounded and conductive control panel to
ensure safety.
•Do not pull the wiring while it is attached to the device. Doing so can cause
failures of the connectors or the device itself.
Installation orientation
Attachthedeviceintheorientationshownbelow.
Do not install it in the orientations illustrated below.
DIN rail mounting
(1) Pull down the sub-base's DIN rail clamp.
(2)AttachtotheDINrailwhilecheckingaboveandbelowthesub-base.
(3) Push up the DIN rail clamp to attach the sub-base to the DIN rail.
80 mm
Front
Wiring, ducts, etc.
BC-R main
device
50 mm
50 mm
50 mm
50 mm
50 mm
50 mm
Display area
BC-R main
device
BC-R main
device
BC-R main
device
Pull the DIN rail clamp
downwards
Push the DIN rail clamp
upwards to x in place
Attach sub-base to DIN rail

7
Chapter 2. Installation, Wiring
Mounting in a panel
(1) Drill two M4 screw holes into the panel.
(Unit: mm)
(2) Use screws to mount the sub-base on the panel.
(Maximum tightening torque: 1.2 N∙m)
CAUTION
Turn the power off before mounting the device on the sub-base. Otherwise, device failure may
occur.
Mounting/removing the device and sub-base (sold separately)
(Mounting)
(1)Aligntheindentationinthecenterofthetopofthedevice
with the projection on the sub-base.
(2) Once aligned as in (1), push straight downwards slowly.
(3) Tighten the device's retaining screws to secure it in the sub-
base. (Maximum tightening torque: 0.5 N·m)
(Removal)
(1) Remove the retaining screws from the device.
(2) Pull it out horizontally while holding down the sub-base.
62.5
M4
(2 locations)

8
Chapter 2. Installation, Wiring
Terminal numbers, front panel item names
zTerminal No.
Front connector terminals
No. Function No. Function
25 Flame voltage output (+) 31 Power supply for monitor output
26 Flame voltage output (-) 32 Monitor output, ame
27 Host communications (RS-485) DA 33 Monitor output, ignition failure
28 Host communications (RS-485) DB 34 Monitor output, ame failure
29 Host communications (RS-485) SG 35 Monitor output, lock-out interlock
30 NC - -
Sub-base terminals
No. Function No. Function
1Blower motor output
(electromagnetic breaker)
13 Alarm output
2 AC power supply (L1) 14 Flame detector (F)
3 AC power supply (L2 (N)) 15 Flame detector (G)
4 Output common 1 16 Input common 1
5 Output common 2 17 Input common 2
6Ignition transformer output 18 NC
7 Pilot valve output 19 NC
8 Main valve output 20 Start input
9NC 21 Air-ow switch input
10 NC 22 Lock-out interlock input
11 NC 23 POC (proof of closure) input
12 NC 24 Contact reset input
Sub-base (sold separately)
Terminal board
Reset switch
DISP switch
Display
Jack *
* Set the POC function as disabled
On BC-R25, also used as a Smart Loader Package jack
Front connector cover
(connector is behind cover)
Front
DIN rail clamp

9
Chapter 2. Installation, Wiring
zConnector for front wiring (81447514-001) terminal layout
zConnector for front wiring (for right side wiring) (81447514-002) terminal layout
25
35
Mounting screw
Wiring
Wiring fastener screw
Mounting screw
25
35
Wiring fastener screw
Mounting screw
Mounting screw
Wiring

10
Chapter 2. Installation, Wiring
Example of wiring connection with external device
(Terminals 1 to 24: sub-base. Terminals 25 to 35: front connector.)
zInterrupted pilot type
Terminal layout of
connector for
front wiring
G
F
+
+
K1
K2
K3
L2 (N)L1
Pilot valve
Main valve
K10
K4
NC
NC
NC
NC
NC
NC
NC
Lock-out interlock
Air-flow switch
Alarm
Power supply
K6
POC (proof of closure)
Combustion
safety
control
circuit
Reset
switch
DISP
switch
*1
Loader
jack
Power supply circuit
10A
Flame
detector
Flame
detector
circuit
Contact reset
Monitor
output
circuit
Ignition transformer
Output common
K5
Input
circuit
(24 Vdc)
24 Vdc
FLAME
ALARM
Flame
Ignition failure
Flame failure
Lock-out interlock
Power supply for monitor output
(100/200 Vac or 24 Vdc)
Start
Input common
FV+
FV-
Flame
voltage
circuit
RS-485
DA
DB
SG
1
3
5
7
8
2
11
12
9
10
6
4
19
20
23
24
21
22
18
34
30
31
32
33
35
25
26
28
27
29
13
15
14
16
17
Display
Blower motor
(electromagnetic
breaker)

11
Chapter 2. Installation, Wiring
zDirect ignition type
Notes
•Use contact reset (terminal 24) input in isolation. It cannot be used in
conjunction with other BC-R contact reset inputs.
•Output common (terminals 4, 5) and input common (terminal 16, 17)
cannot be used in conjunction with other BC-R.
*1 Content in ( ) describes the situation when three-position (Off-Lo-Hi)
control is used. If other than three-position control is used, connect to
main valve (terminal 7).
Terminal layout of
connector for
front wiring
Main valve (Lo solenoid valve)
Main valve (Hi solenoid valve)
*1
*1
Ignition transformer
G
F
+
+
K1
K2
K3
K10
K4
NC
NC
NC
NC
NC
NC
NC
Lock-out interlock
Air-flow switch
Alarm
Power supply
K6
POC (proof of closure)
Combustion
safety
control
circuit
Reset
switch
DISP
switch
Loader
jack
Power supply circuit
10A
Flame
detector
Flame
detector
circuit
Contact reset
Monitor
output
circuit
K5
Input
circuit
(24 Vdc)
24 Vdc
FLAME
ALARM
Flame
Ignition failure
Flame failure
Lock-out interlock
Power supply for monitor output
(100/200 Vac or 24 Vdc)
Start
Input common
FV+
FV-
Flame
voltage
circuit
RS-485
DA
DB
SG
1
3
5
7
8
2
11
12
9
10
6
4
19
20
23
24
21
22
18
34
30
31
32
33
35
25
26
28
27
29
13
15
14
16
17
Display
Output common
Blower motor
(electromagnetic
breaker)
L2 (N)L1

12
Chapter 2. Installation, Wiring
zWiring to a flame detector (UV sensor)
• AUD100C+AUD15C
• AUD110C+AUD15C
• AUD120C+AUD15C
zWiring to a rectification flame rod
zExample countermeasures against power surges caused by lightning
When using a line surge suppressor as a countermeasure against power surges caused
by lightning, connect it between Terminal 3 and the ground, as shown below.
The mounting brackets of the surge suppressor are crimp-on at the grounded side
and inside and in conducting state.
Therefore, they can be grounded by simply attaching them to a grounded metal
part such as the device cabinet.
When wiring to the power supply, use a lead wire of 0.75mm2(diameter: 0.18, strand
count:30)ormore,whichcomplieswithJISC3306.Attach#187Fastonreceptacleat
one end and make the wire length as short as possible when connecting it.
Blue
White
Terminal 14
*
(F)
(G)
Terminal 15
*
Terminal
Terminal 14 (F)
(G)Terminal 15
F
G
If connection of the blue and white lead wires is reversed, or if the connections
to terminals F and G are reversed, the AUD15C tube unit may be damaged.
*
Blue
White
Terminal 14 *
(F)
(G)
Terminal 15
AUD120C
AUD120C
(Flame)
Terminal 14 (F)
(G)
Terminal 15
2
3
Power supply
Surge absorber
83968019-001
2
3
Power supply
High-voltage side (L1)
Low-voltage side (L2(N))
Line surge absorber
Faston terminal side (187 series)
Mounting bracket side
(grounded side)
to to
Burner Controller
Burner Controller
Table of contents
Other Azbil Controllers manuals
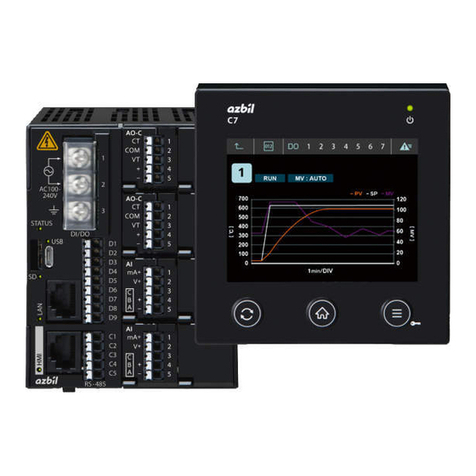
Azbil
Azbil C7G Manual
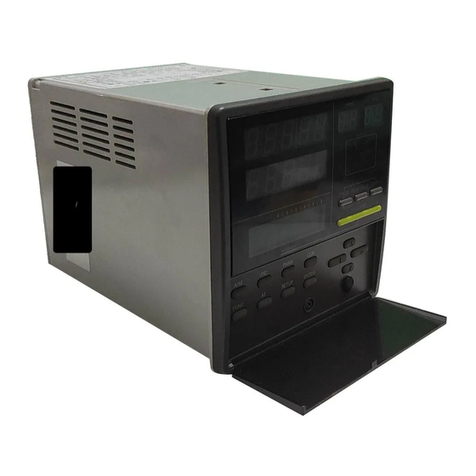
Azbil
Azbil dcp551 mark II User manual
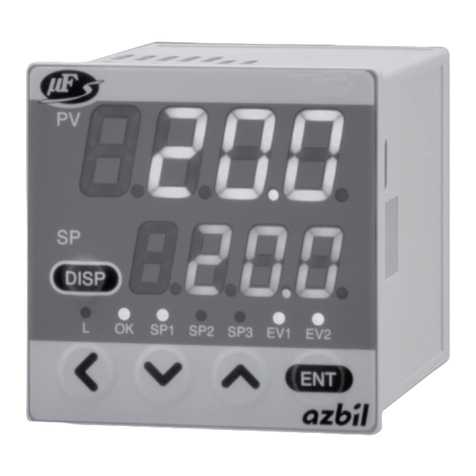
Azbil
Azbil MPC0002 User manual
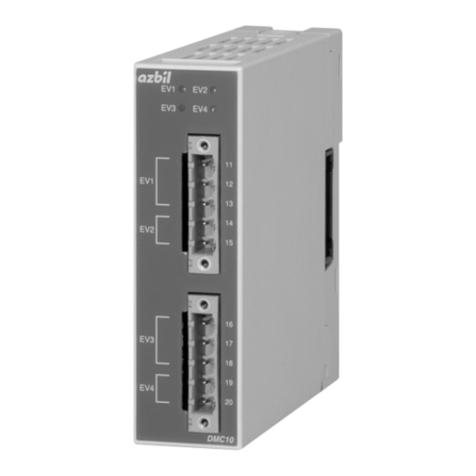
Azbil
Azbil DMC10E User manual
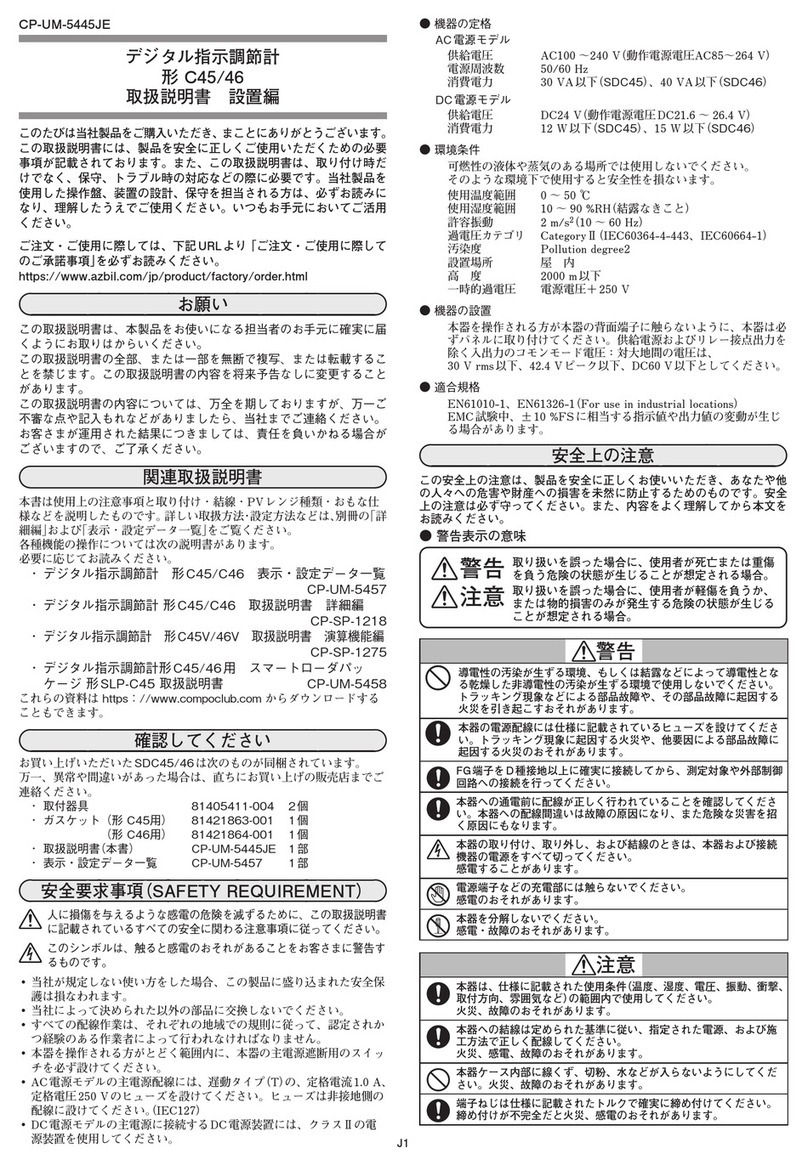
Azbil
Azbil C45 User manual
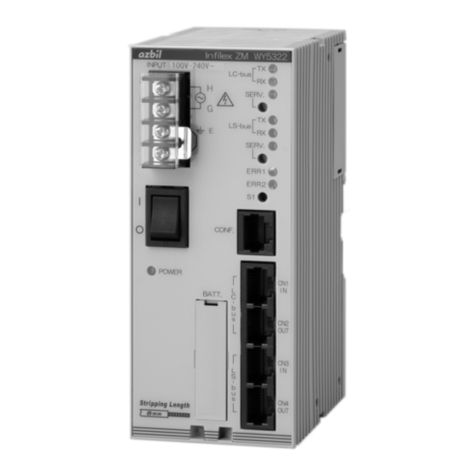
Azbil
Azbil Infilex ZM WY5322 User manual
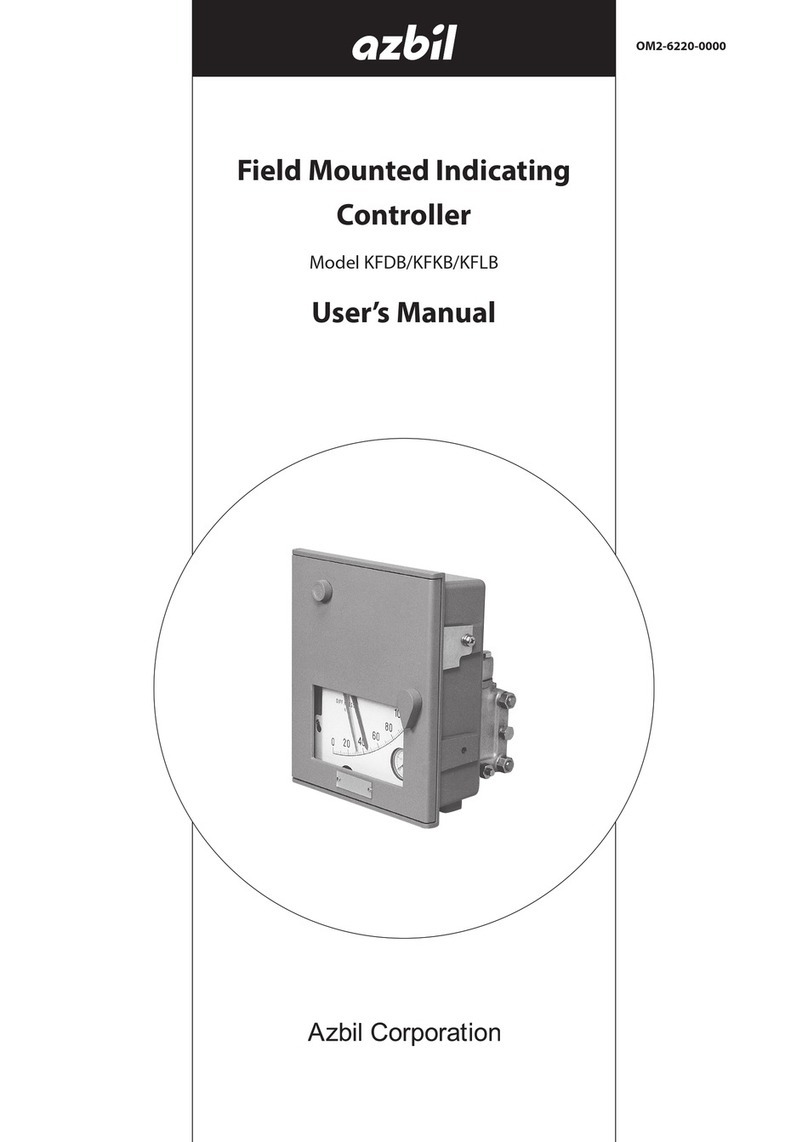
Azbil
Azbil KFDB User manual
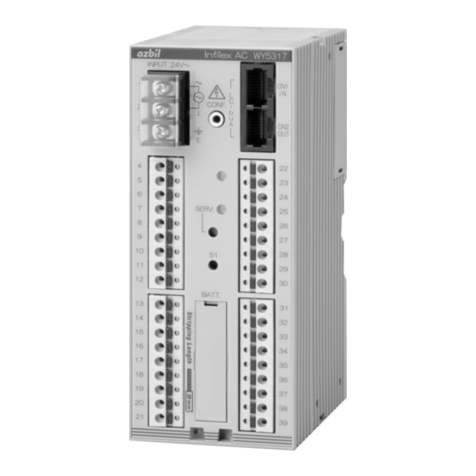
Azbil
Azbil Infilex WY5317C User manual
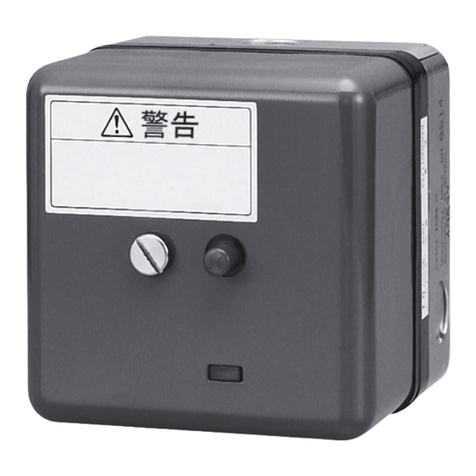
Azbil
Azbil RA890G User manual
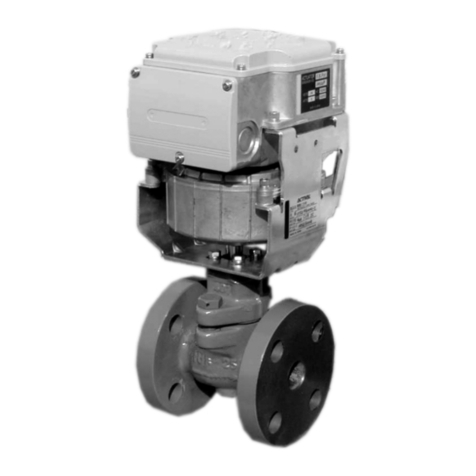
Azbil
Azbil Intelligent Component Series User manual
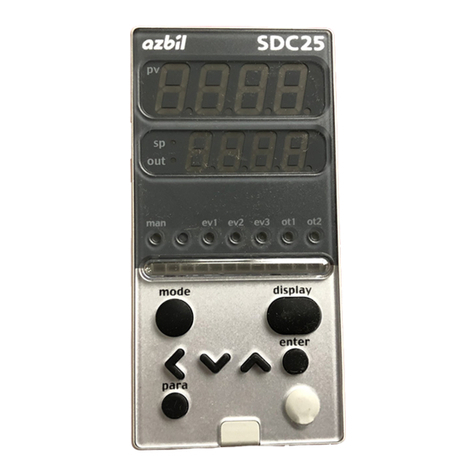
Azbil
Azbil C25 User manual
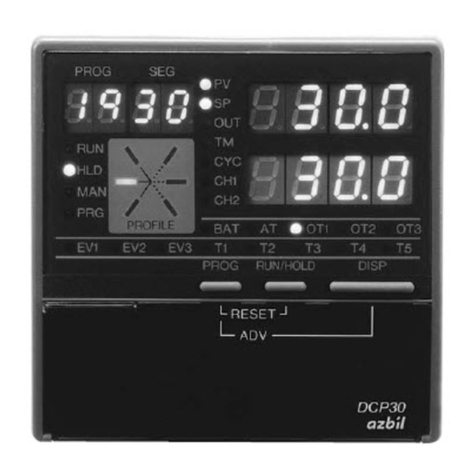
Azbil
Azbil DCP31 User manual
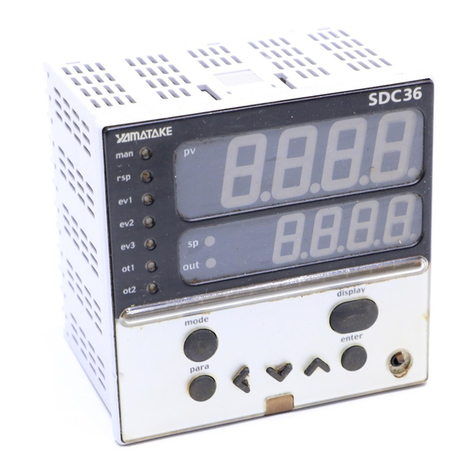
Azbil
Azbil C35 User manual
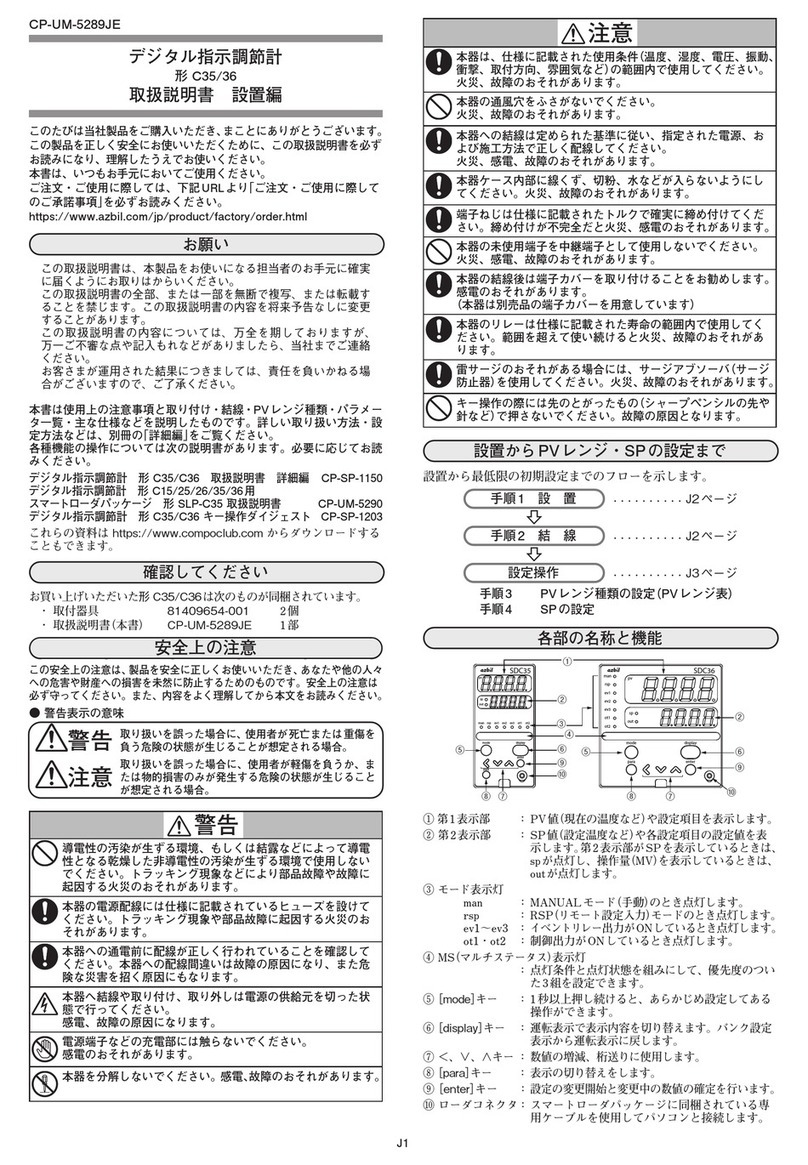
Azbil
Azbil C36 User manual
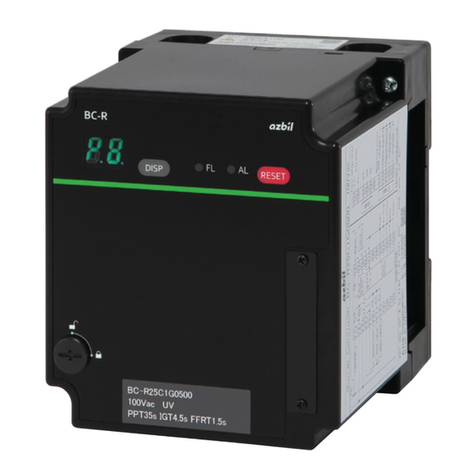
Azbil
Azbil AUR890 Series User manual
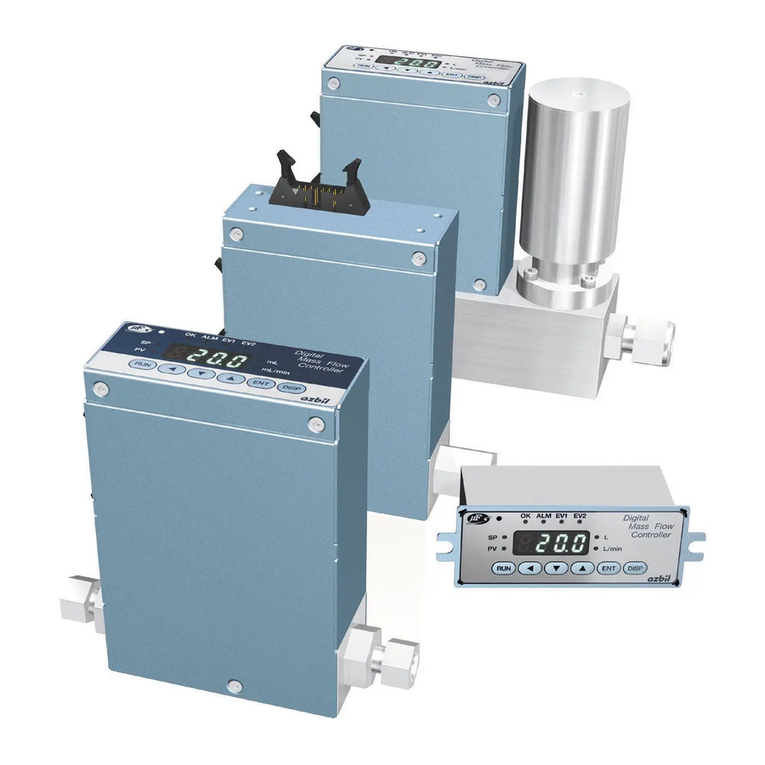
Azbil
Azbil Micro Flow MQV9005 User manual
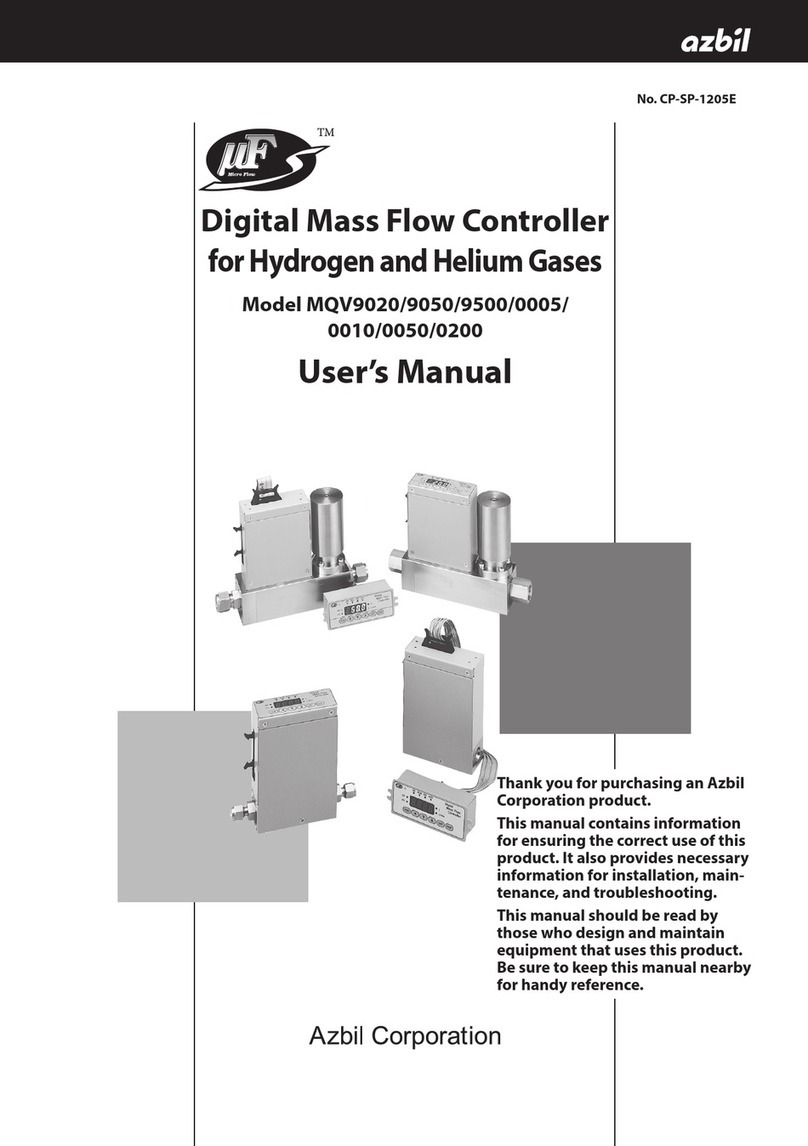
Azbil
Azbil Micro Flow MQV9020 User manual
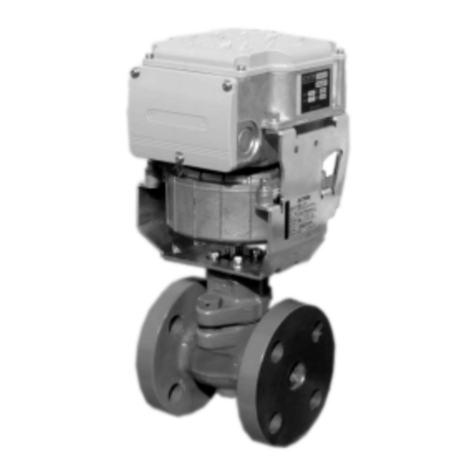
Azbil
Azbil AB-7352-U User manual
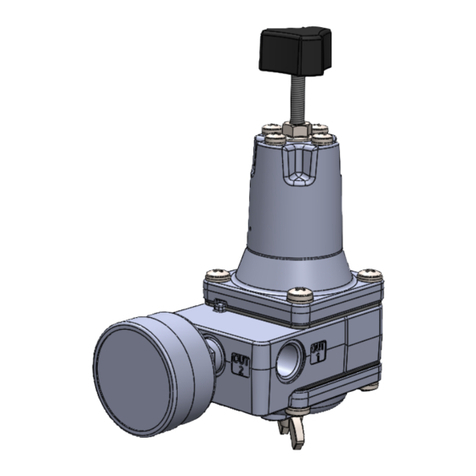
Azbil
Azbil RA1B User manual
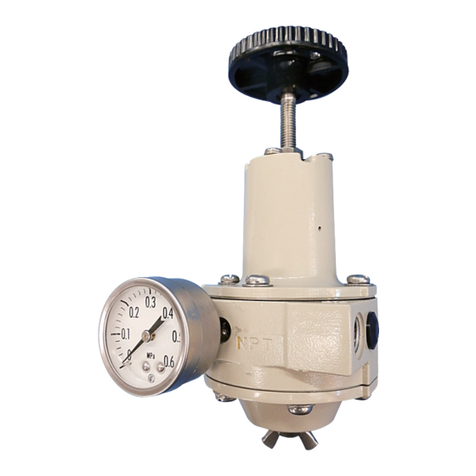
Azbil
Azbil KZ03 Series User manual