Congatec conga-QMX8X User manual

Copyright © 2019 congatec AG QX8X_SDS_q10.indd 1/10
conga-QMX8X Sample Distribution Set
Quick Start Guide
Revision 1.0

Copyright © 2019 congatec AG QX8X_SDS_q10.indd 2/10
Preface
This quick start guide provides information on the contents of the
conga-QMX8X sample distribution set and how to set it up.
Disclaimer
The information contained within this quick start guide, including but not
limited to any product specification, is subject to change without notice.
congatec AG provides no warranty with regard to this guide or any other
information contained herein and hereby expressly disclaims any implied
warranties of merchantability or fitness for any particular purpose with
regard to any of the foregoing. congatec AG assumes no liability for any
damages incurred directly or indirectly from any technical or typographical
errors or omissions contained herein or for discrepancies between the
product and this guide. In no event shall congatec AG be liable for any
incidental, consequential, special, or exemplary damages, whether based
on tort, contract or otherwise, arising out of or in connection with this
guide or any other information contained herein or the use thereof.
Intended Audience
This guide is intended for technically qualified personnel. It is not intended
for general audiences.
Lead-Free Designs (RoHS)
All congatec AG designs are created from lead-free components and are
completely RoHS compliant.
Electrostatic Sensitive Device
All congatec AG products are electrostatic sensitive devices. They are enclosed
in static shielding bags, and shipped enclosed in secondary packaging
(protective packaging). The secondary packaging does not provide electrostatic
protection.
Do not remove the device from the static shielding bag or handle it, except
at an electrostatic-free workstation. Also, do not ship or store electronic
devices near strong electrostatic, electromagnetic, magnetic, or radioactive
fields unless the device is contained within its original packaging. Be aware
that failure to comply with these guidelines will void the congatec AG Limited
Warranty.
Copyright Notice
Copyright © 2019, congatec AG. All rights reserved. All text, pictures and
graphics are protected by copyrights. No copying is permitted without written
permission from congatec AG.
congatec AG has made every attempt to ensure that the information in this
document is accurate yet the information contained within is supplied “as-is”.
Trademarks
Product names, logos, brands, and other trademarks featured or referred to
within this guide, or the congatec website, are the property of their respective
trademark holders. These trademark holders are not affiliated with congatec
AG, our products, or our website.
Certification
congatec AG is certified to DIN EN ISO 9001 standard.
C
E
R
T
I
F
I
C
A
T
I
O
N
I
S
O
9
0
0
1
TM

Copyright © 2019 congatec AG QX8X_SDS_q10.indd 3/10
Warranty
congatec AG makes no representation, warranty or guaranty, express
or implied regarding the products except its standard form of limited
warranty (“Limited Warranty”) per the terms and conditions of the
congatec entity, which the product is delivered from. These terms and
conditions can be downloaded from www.congatec.com. congatec AG
may in its sole discretion modify its Limited Warranty at any time and from
time to time.
The products may include software. Use of the software is subject to the
terms and conditions set out in the respective owner’s license agreements,
which are available at www.congatec.com and/or upon request.
Beginning on the date of shipment to its direct customer and continuing
for the published warranty period, congatec AG represents that the
products are new and warrants that each product failing to function
properly under normal use, due to a defect in materials or workmanship
or due to non conformance to the agreed upon specifications, will be
repaired or exchanged, at congatec’s option and expense.
Customer will obtain a Return Material Authorization (“RMA”) number
from congatec AG prior to returning the non conforming product freight
prepaid. congatec AG will pay for transporting the repaired or exchanged
product to the customer.
Repaired, replaced or exchanged product will be warranted for the
repair warranty period in effect as of the date the repaired, exchanged or
replaced product is shipped by congatec, or the remainder of the original
warranty, whichever is longer. This Limited Warranty extends to congatec’s
direct customer only and is not assignable or transferable.
Except as set forth in writing in the Limited Warranty, congatec makes no
performance representations, warranties, or guarantees, either express or
implied, oral or written, with respect to the products, including without
limitation any implied warranty (a) of merchantability, (b) of fitness for a
particular purpose, or (c) arising from course of performance, course of
dealing, or usage of trade.
congatec AG shall in no event be liable to the end user for collateral or
consequential damages of any kind. congatec shall not otherwise be
liable for loss, damage or expense directly or indirectly arising from the
use of the product or from any other cause. The sole and exclusive remedy
against congatec, whether a claim sound in contract, warranty, tort or any
other legal theory, shall be repair or replacement of the product only.
Technical Support
congatec AG technicians and engineers are committed to providing the best
possible technical support for our customers so that our products can be easily
used and implemented. We request that you first visit our website at www.
congatec.com for the latest documentation, utilities and drivers, which have
been made available to assist you. If you still require assistance after visiting our
website then contact our technical support department by email at support@
congatec.com

Copyright © 2019 congatec AG QX8X_SDS_q10.indd 4/10
1 Hardware
1.1 conga-QMX8X and conga-QEVAL
The conga-QMX8X is designed according to Qseven®specification 2.1 and
features application processors from the NXP i.MX 8X product family with up
to 4 GB LPDDR4 onboard RAM and 64 GB onboard HS400 eMMC 5.1. It is
available in commercial and industrial temperature range.
The conga-QEVAL is designed according to Qseven®specification 2.0 and
supports both x86 and ARM modules. With this dual architecture support,
customers can test modules with different architectures on a single carrier
board, thereby reducing production cost and time. The customers need to
make sure the switches and jumpers for the shared pins are set correctly to
avoid possible malfunction or damage to the module/carrier board.
1.2 Set Content
Part # Name Description Qty
007005 conga-QEVAL/Qseven 2.0
ARM Revision B.4
Qseven 2.0 evaluation carrier board for ARM
based Qseven Modules.
1
016591 conga-QMX8-X/PTT-QuadXP-
3G-LPDDR4 eMMC16
Revision X.1
Qseven 2.1 module with NXP i.MX8 QuadXPlus
processor (Prototype). 3GB LPDDR4 and 16GB
onboard eMMC HS400.
1
016453 conga-QMX8/HSP-T
Revision X.1
Heatspreader. All stand-offs are M2.5 threaded. 1
48000023 RS232 adapter cable MOLEX 6-Pin PicoBlade to two D-SUB 9. 1
10000285 MicroSDHC-Card UHS-I 8GB - Kingston industrial SDCIT/EU Class 10
with preinstalled image.
1
011115 conga-LDVI/EPI LVDS to DVI converter board for digital flat
panels with onboard EEPROM.
1
033331 cab-LVDV-DAT-34-15 15cm data cable LVDS to DVI adapter 1
052147 cab-LVDV-PWR-10-15 15cm power cable LVDS to DVI adapter 1
Note: Future conga-QEVAL revisions (B.5 and later) will provide improved SD
card compatibility and improved audio performance via a congatec specific
audio card. The current sample distribution set includes the conga-QEVAL
revision B.4 and does not include the congatec specific audio card.

Copyright © 2019 congatec AG QX8X_SDS_q10.indd 5/10
1.3 Connecting the Hardware
1. Ensure the hardware is protected from the effects of electrostatic
discharge (ESD).
2. Set the DIP switches as described in section 1.5 "DIP Switch Settings".
3. Set the jumpers as described in section 1.6 "Jumper Settings".
4. Ensure the included microSD card is inserted into the slot of the module.
Note: SD cards with 1.8 V currently not supported by carrier board slot.
5. Attach the RS232 adapter cable to the connector on the module.
6. Attach the
conga-QMX8/HSP-T
heatspreder to the
module by fastening
two screws closest to the edge fingers of the module.
Note:
Put the two screws through the module first.
7. Mount the module with the heatspreader to the carrier board and
fasten the two other screws as shown in the picture below.
8. Connect the conga-LDVI/EPI adapter as shown in the picture below.
9. Connect an AT/ATX PSU or +12 VDC lab PSU to the carrier board.
Note:
ATX mode is currently not supported.
10. To power on the system, switch on the connected PSU.
Note: The power, sleep, and LID buttons currently have limited
functionality. Press the power button to wake up from sleep mode.
Press the power button for five seconds to force shutdown.
cab-LVDV-PWR-10-15
PN: 052147
cab-LVDV-DAT-34-15
PN: 033331
conga-LDVI/EPI
PN: 011115
conga-QEVAL
PN: 007005
RS232 adapter cable
PN: 48000023
conga-QMX8X
PN: 016591
conga-QMX8/HSP-T
PN: 016453
microSDHC-Card
PN: 10000285

Copyright © 2019 congatec AG QX8X_SDS_q10.indd 6/10
1.4 Interfaces
COM1
COM0
GND
+12V
GND
GND
GND
GND
GND
GND
Auxiliary
Power
EEPROM
Socket
SPI Header
MOUSE
LPC/GPIO
Header
KEYBOARD
HDA
Header
EEPROM
SO8
Socket
Internal
Use
POWER
ON
SLEEP LID RESET
COM2
Header
ATX
CPU
FAN
SYS.
FAN
LVDS LCD Power
SD/MMC Socket
SATA0 SATA1
Mini PCIE
CMOS
Battery
Speaker
PCIE0
CAN
Digital Display Port (DDI)
MXM Connector
PCIE1
DEBUG Display
PCIE2
PCIE3
U6
Audio Card
Connector
Feature Connector
LAN
USB
OTG
SuperSpeed
USB Ports
USB 1
USB 2
USB2 5.1 Audio Channel
SPDIF
USB3
USB 7
USB 6
USB 5
USB 4
LID WAKE
X35
(front view)
USB 2.0 Port 1
USB 3.0 Port 1
USB 2.0 Port 0
USB 3.0 Port 0
X34
(front view)
5789
1 2 3 4
6
5789
1 2 3 4
6
USB Port 7
USB Port 6
USB Port 5
USB Port 4
USB Port 2
USB Port 3
CN7
(front view)
8 7 6 5 4 3 2 1

Copyright © 2019 congatec AG QX8X_SDS_q10.indd 7/10
1.5 DIP Switch Settings
M13 - DIP Switch (Currently not supported)
Switch # Switch ON Switch OFF
1 Serial download mode Boot from module*
2 SPI flash (U4) on hold SPI flash (U4) normal operation*
SW1 - DIP Switch Selected
I2C Address
Switch 1 Switch 2 Switch 3 Switch 4
ON OFF OFF OFF A0
OFF ON OFF OFF A1
OFF OFF ON OFF A2
OFF* OFF* OFF* ON* WP (Write Protect)
SW2 - DIP Switch
Switch # Switch ON Switch OFF
1 Super I/O enabled* Disabled
2 KBC enabled* Disabled
3 Super I/O address 4Eh Super I/O address 2Eh*
4 POST display enabled* Disabled
SW3 - DIP Switch
Switch # Switch ON Switch OFF
1 LVDS_BL_CTRL enabled* Disabled
2 FAN_PWMOUT enabled* Disabled
3 SPKR enabled* Disabled
4 FAN_TACHOIN enabled* Disabled
SW4 - DIP Switch
Switch # Switch ON Switch OFF
1 Connect SMB clock signal to PCIe clock buffer* Disconnect
2 Connect SMB data signal to PCIe clock buffer* Disconnect
3 Connect SMB clock signal to PCIe slots* Disconnect
4 Connect SMB data signal to PCIe slots* Disconnect
*
Default setting. Change to the setting highlighted in red for conga-QMX8X module.
SW2
X29
X52
X48
X51
X28
X49
X50
X46
X47
SW4
SW1
X44
X9
X2 SW3
X22
SW9
M13
(Not supported yet)
X43
X17
X32
X33
MXM Connector
X1
23 1
23 1
23 1
23 1
2 31 2 31 2 31
2 31
2 31 2 31
23 1
23 1
23 1
23 1
23 1
23 1
35
46 2
1
4
3
2
1
0N
4321
0N
4
3
2
1
0N
4
3
2
1
0N
4
3
2
1
0N
1
4
3
2
21
0N
12
X37
2 31

Copyright © 2019 congatec AG QX8X_SDS_q10.indd 8/10
SW9 - DIP Switch
Switch # Switch ON Switch OFF
1 Selects USB 3.0 port 0 (disables USB 2.0 port 6 and 7 of connector X35) Selects USB 2.0 port 6 and 7 (disables USB 3.0 port 0 of connector X34)*
2 Selects USB 3.0 port 1 (disables USB 2.0 port 4 and 5 of connector X35) Selects USB 2.0 port 4 and 5 (disables USB 3.0 port 1 of connector X34)*
3 Routes USB 2.0 signals to port 2 of connector CN7 (disables mini-PCIe) Routes USB 2.0 signals to mini-PCIe connector X31 (disables USB 2.0 port 2)*
4 Routes USB 2.0 port 1 signals to connector X53 (micro USB AB connector) Routes USB 2.0 port 1 signals to USB A connector X34 (disables USB OTG)*
1.6 Jumper Settings
X9 - CAN Term
Pin Configuration
1-2 Enabled
2-3 Disabled*
X17 - RTC Battery
Pin Configuration
1-2 Normal oprtation*
2-3
RTC battery disconnected
X22 - HDMI/DP
Pin Configuration
1-2 HDMI_HPD#*
2-3 DP_HPD#
X28 - PS_ON# Control
Pin Configuration
1-2 via S3#*
2-3 via S5#
X29 - ATX PSON#
Pin Configuration
1-2 ATX Mode*
2-3 AT Mode / Always ON
X32 - WiFi @ mini PCIe
Pin Configuration
1-2 Enabled*
2-3 Disabled
X33 - LAN LEDs
Pin Configuration
1-2 Standby powered*
2-3 Main powered
X37 - USB OTG ID-Pin
Pin Configuration
1-2 X53 USB B ... ID=open*
2-3 X53 USB A ... ID=GND
X43 - PWR_OK (PWGIN)
Pin Configuration
1-2 Pull-up resistor*
2-3 ATX power source
4-6 DC/DC converter
X44 - Debug Display
Pin Configuration
1-2 80h and 84h output*
2-3 90h and 94h output
X46 - LCD BKLT Power
Pin Configuration
1-2 12 V*
2-3 5 V
X47 - LCD Panel Power
Pin Configuration
1-2 3.3 V
2-3 5 V*
X48 - CPU FAN Power
Pin Configuration
1-2 12 V*
2-3 5 V
X49 - +5V_SB ATX PSU
Pin Configuration
1-2 Enabled*
2-3 Disabled
X50 - LCD BKLT_EN
Pin Configuration
1-2 HIGH active*
2-3 LOW active
X51 - SYS. FAN Power
Pin Configuration
1-2 12 V*
2-3 5 V
X52 - SYS. FAN Control
Pin Configuration
1-2 Without control*
2-3 With control
*
Default setting. Change to the
setting highlighted in red for the
conga-QMX8X module.

Copyright © 2019 congatec AG QX8X_SDS_q10.indd 9/10
2 Software
2.1 Starting Up
The conga-QMX8X uses U-Boot as standard bootloader. The bootloader
is GNU GPL open source software. A serial terminal connection is required
in order to display the boot process and to modify the boot behavior. The
boot behavior is controlled via environment variables.
The included RS232 adapter cable has two connectors. The RX/TX signals
are already crossed. Therefore, do NOT use a crossover-cable. Use the
connector labeled "Console" for the u-boot console output. Use the
unlabeled connector for the System Controller Unit (SCU) firmware debug
output.
To establish a terminal connection, a terminal program such as TeraTerm
or Putty can be used.
Use the following communication parameters:
Baud rate:
Data:
Parity:
Stop:
Flow control:
115200
8 bit
none
1 bit
none
The following console output will be displayed when the system is powered on.
2.2 Boot Process
The conga-QMX8X boot process starts at Power On Reset (POR), where
the hardware reset logic forces the ARM core to begin execution. The on-
chip boot ROM loads the SCU and Security Controller (SECO) firmware
before loading the bootloader.
After loading, the bootloader is executed and performs basic system
initialization (serial console, etc.). Afterwards, the environment settings are
parsed and the system boot continues as specified.
Press any key during startup to stop autoboot and to get to u-boot console.
At the u-boot console, the environment settings can be displayed using
the “print” command. In addition, useful functionality is available (such as
memory dump, access to the I2C system, etc.). The “help” command will
display any command supported by the u-boot.
If autoboot is not interrupted by pressing a key, the boot process goes
ahead and the module will boot the Linux operating system that is installed
on the microSD card.
2.3 U-Boot Environment Variables
The u-boot environment is located in SPI Flash (in microSD for prototypes).
One of the benefits of the u-boot bootloader is the possibility to specify its
run time configuration using environment variables.
The environment variables of u-boot can be displayed using the printenv
(or the print) command.
During the boot process, the bootloader evaluates the “bootcmd” variable
and executes it. The boot command tries to load a bootscript or a kernel
from the boot device. If this is successful, the script or kernel will be started,
otherwise a fallback to network boot is performed. The variable “mmcdev”
specifies the mmc boot device. Furthermore, the variable “mmcroot” is
passed to the kernel in order to specify the location of the root filesystem.

Copyright © 2019 congatec AG QX8X_SDS_q10.indd 10/10
The following environment variables are predefined for conga-QMX8X:
Name Default value Description
bootcmd Defines the startup command of the bootloader, i.e.
how the system performs the boot process
fdt_file imx8qxp-cgtqx8x.dtb The device tree blob, might be exchanged in order to
enhance functionality
image Image The name of the kernel image file that is loaded
during boot process
ipaddr not specified Address of the system (used for network boot)
serverip not specified Address of the remote host (used for network boot)
netmask not specified Netmask of the network (used for network boot)
nfsroot not specified The location where the NFS root filesystem is stored
(used for network boot)
mmcdev "1" (onboard microSD) The boot device number (used for mmcboot)
mmcpart "1" (first partition) The number of the bootpartiton on the bootdevice
(used for mmcboot)
mmcroot "/dev/mmcblk1p2 rootwait
rw" (2nd partition on device 1)
The root filesystem (used for mmcboot), might also
be used to extend the kernel command line
Following, some frequently used scripts:
Name Description
mmcboot Boots the system from mmc (with the specified parameters for mmcboot), i.e.
eMMC, SD-card, microSD-card
mmcargs Configures the bootargs for mmcboot
netboot Boots the system from network (with the specified parameters for network boot)
netargs Configures the bootargs for network boot
loadbootscript Used during boot, loads an eventually existing boot script
loadimage Used during boot, loads the kernel
loadfdt Used during boot, loads the device tree blob file
There are several commands to change the behavior of the bootloader and
to customize the boot process. The help command can be used to display
a list of all available commands.
2.4 Linux
By default, the system boots the Linux operating system that is stored on
the microSD card. The operating system image is Yocto.
Booting to the Linux desktop may take some time. This is because the
complete system initialization occurs from a microSD card connected via
a 4-bit interface.
Note
In order to maintain the integrity of the file system, it is recommended to
always shutdown the system cleanly by issuing the command “poweroff”
in the console terminal.
2.5 Additional Information
The software provided with the conga-QMX8X sample distribution set is
based on the Yocto Project (www.yoctoproject.org) and i.MX 8X specific
add-on layers provided by NXP and congatec.
In order to rebuild the root filesystem image, kernel and bootloader for
conga-QMX8X, the complete kernel source, bootloader source and
individual patches can be obtained from the congatec source code
repository:
https://git.congatec.com/imx8x_early_access
Further software documentation can be found here:
https://git.congatec.com/imx8x_early_access/meta-fsl-bsp-release
Note
Contact congatec technical support to get access to the repositories.
Other manuals for conga-QMX8X
1
Table of contents
Other Congatec Control Unit manuals

Congatec
Congatec conga-QMX8X User manual
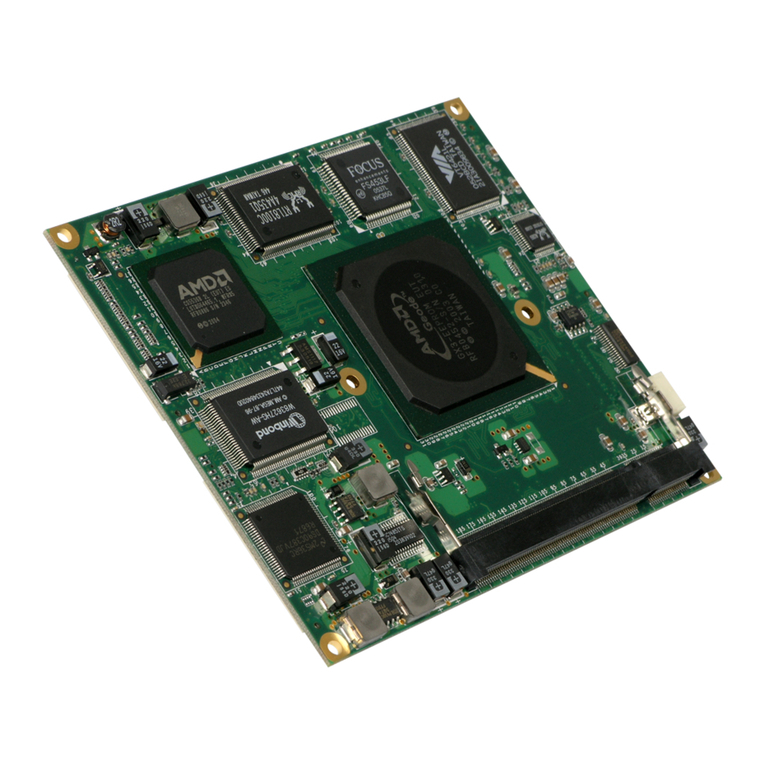
Congatec
Congatec XTX conga-XLX User manual

Congatec
Congatec COM Express conga-TCA5 User manual
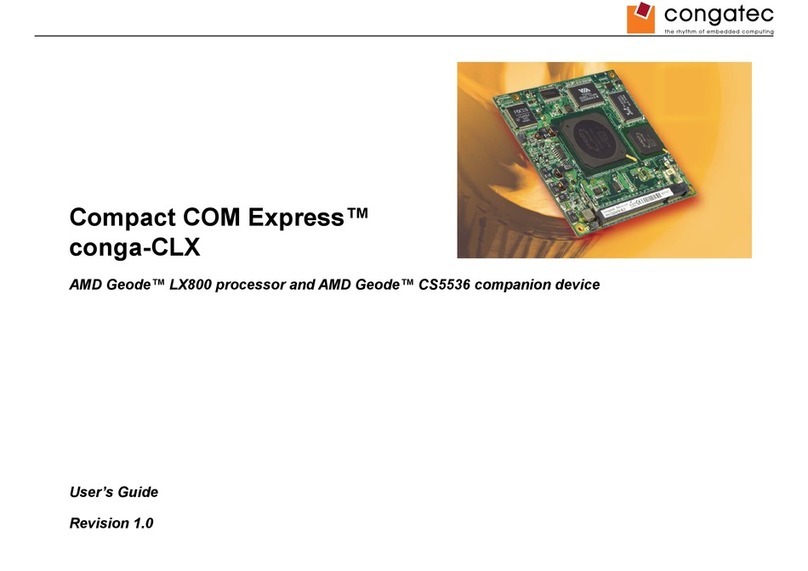
Congatec
Congatec Compact COM Express conga-CLX User manual
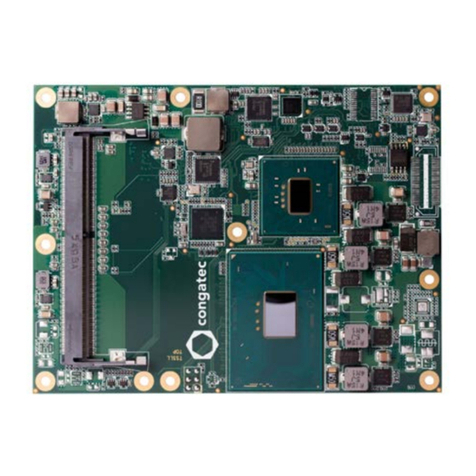
Congatec
Congatec COM Express conga-TS175 User manual
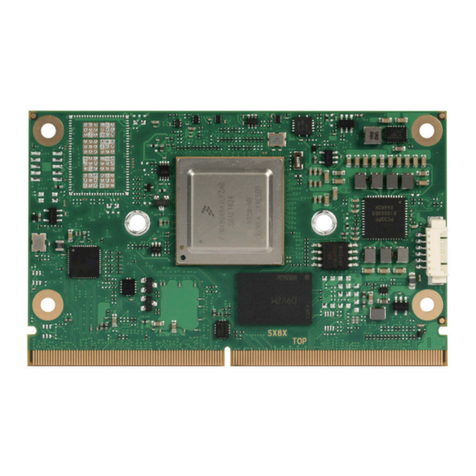
Congatec
Congatec SMARC conga-SMX8-X User manual
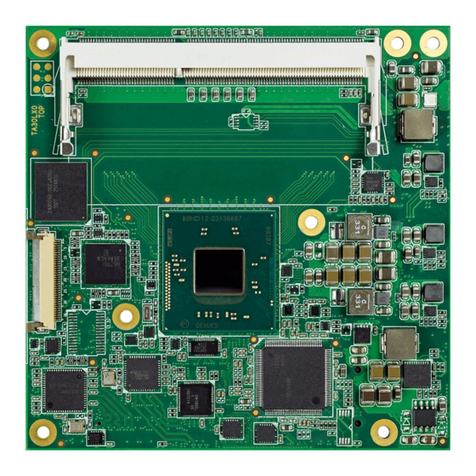
Congatec
Congatec COM Express conga-TCA3 User manual
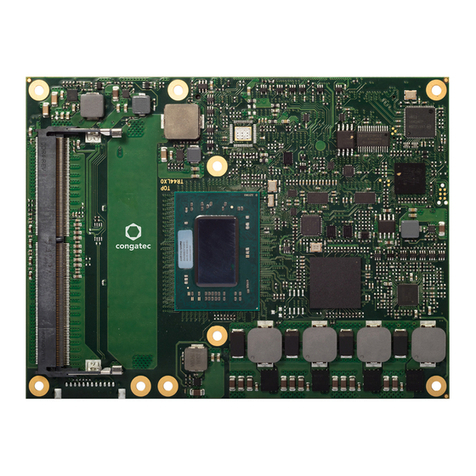
Congatec
Congatec COM Express conga-TR4 User manual
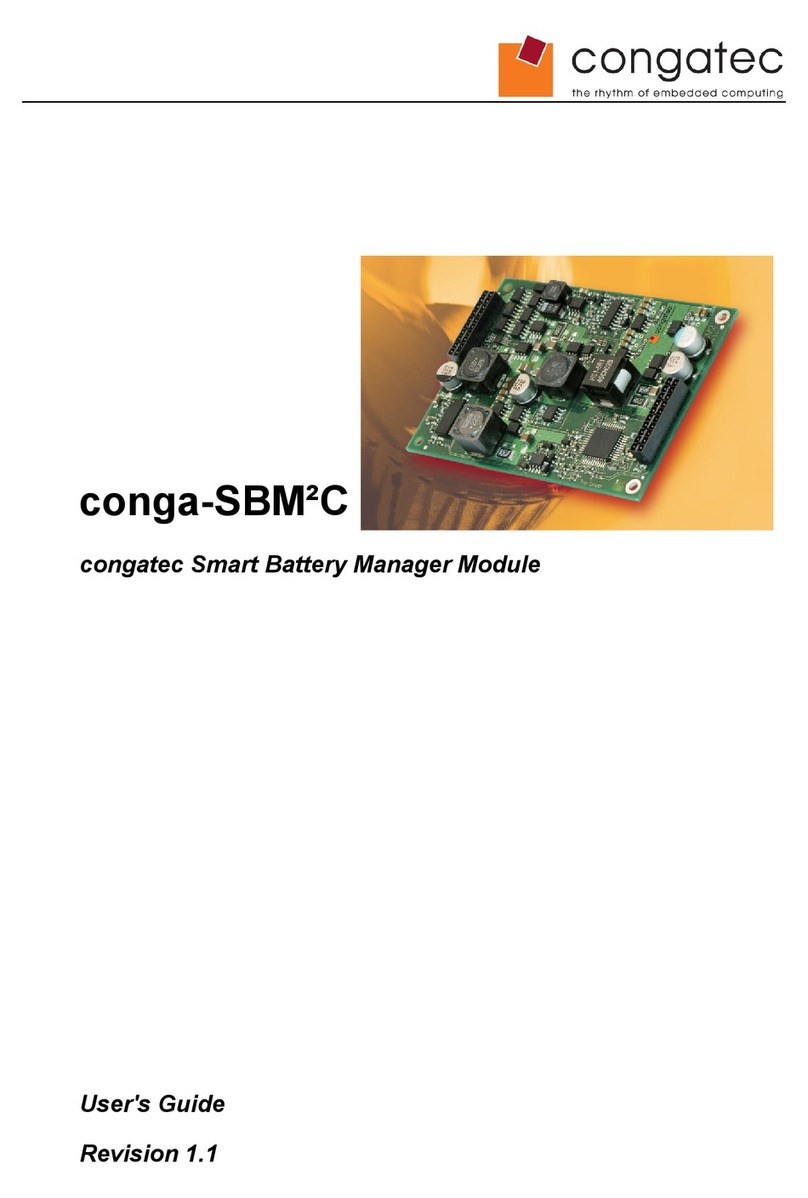
Congatec
Congatec conga-SBM2C User manual

Congatec
Congatec Qseven conga-QMX6 User manual