GEM F60 User manual

GEMÜ F60
Motorized filling valve
Operating instructions
EN
further information
webcode: GW-F60

All rights including copyrights or industrial property rights are expressly reserved.
Keep the document for future reference.
© GEMÜ Gebr. Müller Apparatebau GmbH & Co. KG
07.11.2019
www.gemu-group.com2 / 24GEMÜ F60

Contents
1 General information .................................................. 4
1.1 Information ......................................................... 4
1.2 Symbols used ..................................................... 4
1.3 Definition of terms ............................................. 4
1.4 Warning notes .................................................... 4
2 Safety information .................................................... 5
3 Product description ................................................... 5
5 Order data ................................................................. 8
6 Technical data .......................................................... 9
7 Dimensions ............................................................... 12
8 Manufacturer's information ....................................... 15
8.1 Delivery ............................................................... 15
8.2 Packaging ........................................................... 15
8.3 Transport ............................................................ 15
8.4 Storage ............................................................... 15
9 Installation in piping .................................................. 15
9.1 Preparing for installation ................................... 15
9.2 Installation with clamp connections ................. 16
9.3 Installation with butt weld spigots .................... 16
10 Electrical connection ................................................. 16
11 Commissioning ......................................................... 16
12 Troubleshooting ........................................................ 17
13 Inspection/servicing .................................................. 18
14 Removal from piping ................................................. 21
15 Disposal .................................................................... 21
16 Returns ..................................................................... 21
17 Declaration of Incorporation according to 2006/42/
EC (Machinery Directive) ........................................... 22
18 Declaration of conformity according to 2014/30/EU
(EMC Directive) ......................................................... 23
GEMÜ F60www.gemu-group.com 3 / 24

www.gemu-group.com4 / 24GEMÜ F60
1 General information
1 General information
1.1 Information
– The descriptions and instructions apply to the stand-
ard versions. For special versions not described in this
document the basic information contained herein ap-
plies in combination with any additional special docu-
mentation.
– Correct installation, operation, maintenance and repair
work ensure faultless operation of the product.
– Should there be any doubts or misunderstandings, the
German version is the authoritative document.
– Contact us at the address on the last page for staff
training information.
1.2 Symbols used
The following symbols are used in this document:
Symbol Meaning
Tasks to be performed
Response(s) to tasks
– Lists
1.3 Definition of terms
Working medium
The medium that flows through the GEMÜ product.
PD
PD = Plug Diaphragm
1.4 Warning notes
Wherever possible, warning notes are organised according to
the following scheme:
SIGNAL WORD
Type and source of the danger
Possible
symbol for the
specific
danger
Possible consequences of non-observance.
Measures for avoiding danger.
Warning notes are always marked with a signal word and
sometimes also with a symbol for the specific danger.
The following signal words and danger levels are used:
DANGER
Imminent danger!
▶Non-observance can cause death or
severe injury.
WARNING
Potentially dangerous situation!
▶Non-observance can cause death or
severe injury.
CAUTION
Potentially dangerous situation!
▶Non-observance can cause moderate
to light injury.
NOTICE
Potentially dangerous situation!
▶Non-observance can cause damage to
property.
The following symbols for the specific dangers can be used
within a warning note:
Symbol Meaning
Danger of explosion
Corrosive chemicals
Hot plant components!
Danger - high voltage!

www.gemu-group.com 5 / 24 GEMÜ F60
2 Safety information
The safety information in this document refers only to an in-
dividual product. Potentially dangerous conditions can arise
in combination with other plant components, which need to
be considered on the basis of a risk analysis. The operator is
responsible for the production of the risk analysis and for
compliance with the resulting precautionary measures and
regional safety regulations.
The document contains fundamental safety information that
must be observed during commissioning, operation and
maintenance. Non-compliance with these instructions may
cause:
– Personal hazard due to electrical, mechanical and
chemical effects.
– Hazard to nearby equipment.
– Failure of important functions.
– Hazard to the environment due to the leakage of dan-
gerous materials.
The safety information does not take into account:
– Unexpected incidents and events, which may occur
during installation, operation and maintenance.
– Local safety regulations which must be adhered to by
the operator and by any additional installation person-
nel.
Prior to commissioning:
1. Transport and store the product correctly.
2. Do not paint the bolts and plastic parts of the product.
3. Carry out installation and commissioning using trained
personnel.
4. Provide adequate training for installation and operating
personnel.
5. Ensure that the contents of the document have been fully
understood by the responsible personnel.
6. Define the areas of responsibility.
7. Observe the safety data sheets.
8. Observe the safety regulations for the media used.
During operation:
9. Keep this document available at the place of use.
10. Observe the safety information.
11. Operate the product in accordance with this document.
12. Operate the product in accordance with the specifica-
tions.
13. Maintain the product correctly.
14. Do not carry out any maintenance work and repairs not
described in this document without consulting the manu-
facturer first.
In cases of uncertainty:
15. Consult the nearest GEMÜ sales office.
3 Product description
3.1 Construction
3.1.1 Flow direction
over the seat
(15-27°)
21°
9°
9°
1 → 2, optimal draining and filling properties
3 Product description

www.gemu-group.com6 / 24GEMÜ F60
3 Product description
under the seat
(15-27°)
21°
9°
9°
2 → 1, better pressure stability and higher flow
3.1.2 PD seal system
Actuator
Depression for the hook
wrench
Leak detection hole
Vent hole
Opening protection
Vent hole
Opening protection
PTFE diaphragm
(PD)
Stainless
steel body
3.2 Description
The GEMÜ F60 motorized 2/2-way filling valve is designed
for extremely precise and fast filling processes in aseptic and
hygienic areas of application. GEMÜ F60 enables activation
in real time, ultra-quick load cycles and high flow rates of up
to 6600 litres per hour. The sealing concept of the valve is
based on the GEMÜ PD design, whereby the actuator is her-
metically separated from the medium. All actuator parts (ex-
cept the seals) are made from stainless steel.
3.3 Function
The product is an electrically operated 2/2-way filling valve
made of stainless steel. The GEMÜ F60 2/2-way filling valve
is designed for use in piping systems. The product is non-
self-locking and can be easily moved without force when de-
energized. External leak tightness is nevertheless ensured.
An external controller is required to operate the valve. The
valve does not work without a controller.
With this external controller, the filling valve offers flexible
and fast program changes thanks to freely programmable
filling curves.
The external controller is not included in the scope of deliv-
ery.

www.gemu-group.com 7 / 24 GEMÜ F60
4 Correct use
DANGER
Danger of explosion
▶Risk of death or severe injury.
●Do not use the product in potentially
explosive zones.
WARNING
Improper use of the product!
▶Risk of severe injury or death.
▶Manufacturer liability and guarantee will be void.
●Only use the product in accordance with the operating
conditions specified in the contract documentation and
this document.
The product is designed for installation in piping systems
and for controlling a working medium.
The product is not intended for use in potentially explosive
areas.
●Use the product in accordance with the technical data.
4 Correct use

5 Order data
The order data provide an overview of standard configurations.
Please check the availability before ordering. Other configurations available on request.
Order codes
1 Type Code
Stainless steel PD valve, motorized F60
2 DN Code
DN 10 10
DN 15 15
DN 20 20
3 Body configuration Code
2/2-way body D
4 Connection type Code
Spigot
Spigot DIN 0
Spigot EN 10357 series B,
formerly DIN 11850 series 1
16
Spigot EN 10357 series A (formerly DIN 11850
series 2) / DIN 11866 series A
17
Spigot ASME BPE / DIN 11866 series C 59
Clamp
Clamp DIN 32676 series A 86
Clamp ASME BPE 88
5 Valve body material Code
1.4435, investment casting C3
6 Seal material Code
PTFE 5
7 Valve body adaptor Code
Adaptor for PD size 3 3
8 Electric actuator size Code
F60 with external dia. 32.0 mm 3
9 Voltage/frequency Code
48 V DC D1
10 Control module Code
OPEN/CLOSE, positioner and process controller
with CANopen, Profinet, Ethernet IP, EtherCAT
interface
LN
11 Cable length Code
3.0 m 3
12 Surface Code
Ra ≤ 0.8 µm (30 µin.) for media wetted surfaces,
in accordance with DIN 11866 H3,
mechanically polished internal
1502
13 Seat diameter Code
20 mm H
14 Special version Code
Special version for 3A M
Order example
Order option Code Description
1 Type F60 Stainless steel PD valve, motorized
2 DN 15 DN 15
3 Body configuration D 2/2-way body
4 Connection type 17 Spigot EN 10357 series A (formerly DIN 11850 series 2) / DIN 11866
series A
5 Valve body material C3 1.4435, investment casting
6 Seal material 5 PTFE
7 Valve body adaptor 3 Adaptor for PD size 3
8 Electric actuator size 3 F60 with external dia. 32.0 mm
9 Voltage/frequency D1 48 V DC
10 Control module LN OPEN/CLOSE, positioner and process controller
with CANopen, Profinet, Ethernet IP, EtherCAT interface
11 Cable length 3 3.0 m
12 Surface 1502 Ra ≤ 0.8 µm (30 µin.) for media wetted surfaces,
in accordance with DIN 11866 H3,
mechanically polished internal
13 Seat diameter H 20 mm
14 Special version M Special version for 3A
5 Order data
www.gemu-group.com
8 / 24
GEMÜ F60

6 Technical data
6.1 Medium
Working medium: Corrosive, inert, gaseous and liquid media which have no negative impact on the physical and
chemical properties of the body and diaphragm material.
6.2 Temperature
Media temperature: -10 to 140 °C
Sterilisation temperature: Hot water max. 4 bar at 140 °C, max. 60 min
Steam max. 2 bar at 140 °C, max. 60 min
Ambient temperature: -10 to 60 °C
Storage temperature: 0 to 40 °C
Speed of temperature
change:
max. 0.5 °C/min
6.3 Pressure
Operating pressure: over the seat max. 7 bar (1 → 2)
under the seat max. 6 bar (2 → 1)
Pressure/temperature
correlation:
Process:
-30 -10 10 30 50 70 90 110 130 150
9
8
7
6
5
4
3
2
1
00
Pressure [bar]
Temperature [°C]
GEMÜ F60www.gemu-group.com 9 / 24
6 Technical data

Pressure/temperature
correlation: Hot water, steam
9
8
7
6
5
4
3
2
1
0
80 90 100 110 120 130 140 150
Temperature [°C]
Temperature [C]
Pressure [bar]
Hot water
Steam
Hot water max. 4 bar at 140 °C, max. 60 min
Steam max. 2 bar at 140 °C, max. 60 min
Leakage rate: Seat seal Standard Test procedure Leakage rate Test medium
EPDM, FPM, PTFE DIN EN 12266-1 P12 A Air
Kv values: DN Code Flow direction
over the seat [1 → 2]
Flow direction
under the seat [2 → 1]
10 17 2.7 m³/h 2.8 m³/h
15 17 6.1 m³/h 6.6 m³/h
Kv values in m³/h
6.4 Product compliance
Machinery Directive: 2006/42/EU
Food: FDA
USP Class VI
Regulation (EC) No. 1935/2004
Regulation (EC) No. 10/2011
EHEDG certified
6.5 Mechanical data
Protection class: Actuator and cable exit: IP69K acc. to EN 60529
Connector plug: IP65/IP67 acc. to EN 60529 when plugged in
Weight: Actuator size 3 Valve assembly approx. 2,300 g
Body
Spigot 0.30 kg
Clamp 0.22 kg
Operating time: adjustable, max. 200 mm/s
Cycle duties: Cycle duties (over 10 million)
The cycle duties depend on the operating parameters. High pressures and media temperatures
can lead to a shorter service life.
www.gemu-group.com
10 / 24
GEMÜ F60
6 Technical data

6.6 Electrical data
Humidity: Relative humidity: 5–95%
Absolute humidity: 1–29 g/m³
6.6.1 Supply voltage
Actuator voltage: 48 V DC ± 10%
Logic voltage (simco
drive controller):
24 V DC ± 10%
Maximum current: 6.7 A
Extended standstill
current:
2 A
Rated current: 1.8 A
Maximum power: 150 W
Rated power: ≤ 55 W
Duty cycle: 100%
Reverse battery
protection:
Yes
6.6.2 Electrical connection
Connection: Connection cable with connector
Connector plug: Intercontec series 915 12 + 3-pin
Plug cycles: <500
6.6.3 Connection cable
Cable length: 3 m (extension cable 5 m)
Cable material: PUR
Shield: Twofold shield
Cable colour: Black
Bend radius: Single movement ≥ 3 x D
Moving ≥ 10 x D
Drag chain data: Acceleration 2 m/s²
Bend cycles 1,000,000
Speed 3 m/s
Resistance: Oil resistance in accordance with EN 60811-404
Torsion applications: Not suitable
Approval: UL AWM Style 20233, 80 °C, 300 V
GEMÜ F60www.gemu-group.com 11 / 24
6 Technical data

7 Dimensions
7.1 Actuator dimensions
SW 36
32
307,9
79,2
53
www.gemu-group.com
12 / 24
GEMÜ F60
7 Dimensions

7.2 Body dimensions
7.2.1 Spigot
L
H1
s
c
H3
H2
B
d
DN Connection types code 1)
0 16 17
Material code C3 2)
L ØB c H1 H2 H3 ød s ød s ød s
10 95.0 53.0 20.0 21.5 41.2 51.2 - - - - 13.0 1.5
15 95.0 53.0 20.0 19.5 44.2 54.2 18.0 1.5 18.0 1.0 19.0 1.5
DN Connection types code 1)
59
Material code C3 2)
L ØB c H1 H2 H3 ød s
15 95.0 53.0 20.0 21.5 41.2 51.2 12.70 1.65
20 95.0 53.0 20.0 19.5 44.2 54.2 19.05 1.65
Dimensions in mm
1) Connection type
Code 0: Spigot DIN
Code 16: Spigot EN 10357 series B, formerly DIN 11850 series 1
Code 17: Spigot EN 10357 series A (formerly DIN 11850 series 2) / DIN 11866 series A
Code 59: Spigot ASME BPE / DIN 11866 series C
2) Valve body material
Code C3: 1.4435, investment casting
GEMÜ F60www.gemu-group.com 13 / 24
7 Dimensions

7.2.2 Clamp
H1
B
L
d1
d3
H2
H3
DN Connection types code 1)
86
Material code C3 2)
L ØB c H1 H2 H3 Ød1 Ød3 s
10 121.0 53.0 20.0 21.5 41.2 51.2 10.0 34.0 1.5
15 121.0 53.0 20.0 19.5 44.2 54.2 16.0 34.0 1.5
DN Connection types code 1)
88
Material code C3 2)
L ØB c H1 H2 H3 Ød1 Ød3 s
15 121.0 53.0 20.0 21.5 41.2 51.2 9.40 25.0 1.65
20 121.0 53.0 20.0 19.5 44.2 54.2 15.75 25.0 1.65
Dimensions in mm
1) Connection type
Code 86: Clamp DIN 32676 series A
Code 88: Clamp ASME BPE
2) Valve body material
Code C3: 1.4435, investment casting
www.gemu-group.com
14 / 24
GEMÜ F60
7 Dimensions

www.gemu-group.com 15 / 24 GEMÜ F60
8 Manufacturer's information
The controller required for valve operation is not included in
the scope of delivery.
8.1 Delivery
●Check that all parts are present and check for any dam-
age immediately upon receipt.
The product's performance is tested at the factory. The
scope of delivery is apparent from the dispatch documents
and the design from the order number.
8.2 Packaging
The product is packed in a cardboard box which can be re-
cycled as paper.
8.3 Transport
1. Only transport the product by suitable means. Do not
drop. Handle carefully.
2. After the installation dispose of transport packing mater-
ial according to relevant local or national disposal regula-
tions / environmental protection laws.
8.4 Storage
1. Store the product free from dust and moisture in its ori-
ginal packaging.
2. Avoid UV rays and direct sunlight.
3. Do not exceed the maximum storage temperature (see
chapter "Technical data").
4. Do not store solvents, chemicals, acids, fuels or similar
fluids in the same room as GEMÜ products and their
spare parts.
9 Installation in piping
9.1 Preparing for installation
WARNING
The equipment is subject to pressure!
▶Risk of severe injury or death.
●Depressurize the plant.
●Completely drain the plant.
WARNING
Corrosive chemicals
▶Risk of caustic burns
●Wear suitable protective gear.
●Completely drain the plant.
CAUTION
Hot plant components!
▶Risk of burns!
●Only work on plant that has cooled
down.
CAUTION
Exceeding the maximum permissible pressure.
▶Damage to the GEMÜ product.
●Provide precautionary measures against exceeding the
maximum permitted pressures caused by pressure
surges (water hammer).
CAUTION
Use as step.
▶Damage to the product.
▶Risk of slipping-off.
●Choose the installation location so that the product can-
not be used as a foothold.
●Do not use the product as a step or a foothold.
NOTICE
Suitability of the product!
▶The product must be appropriate for the piping system
operating conditions (medium, medium concentration,
temperature and pressure) and the prevailing ambient
conditions.
9 Installation in piping

www.gemu-group.com16 / 24GEMÜ F60
10 Electrical connection
NOTICE
Tools
▶The tools required for installation and assembly are not
included in the scope of delivery.
●Use appropriate, functional and safe tools.
1. Ensure the product is suitable for the relevant application.
2. Check the technical data of the product and the materials.
3. Keep appropriate tools ready.
4. Wear appropriate protective gear, as specified in the plant
operator's guidelines.
5. Observe appropriate regulations for connections.
6. Have installation work carried out by trained personnel.
7. Shut off the plant or plant component.
8. Secure the plant or plant component against recommis-
sioning.
9. Depressurize the plant or plant component.
10. Completely drain the plant (or plant component) and let it
cool down until the temperature is below the media va-
porization temperature and cannot cause scalding.
11. Correctly decontaminate, rinse and ventilate the plant or
plant component.
12. Lay piping so that the product is protected against trans-
verse and bending forces, and also from vibrations and
tension.
13. Protect the piping against the total weight of the valve, vi-
brations during operation, as well as torques generated
during assembly and disassembly.
14. Only install the product between matching aligned pipes
(see chapters below).
15. Please note the flow direction (see chapter "Flow direc-
tion").
16. Please note the installation position (see chapter "Install-
ation position").
9.2 Installation with clamp connections
Fig.1: Clamp connection
NOTICE
Gasket and clamp
▶The gasket and clamps for clamp connections are not in-
cluded in the scope of delivery.
1. Keep ready gasket and clamp.
2. Carry out preparation for installation (see chapter "Pre-
paring for installation").
3. Insert the corresponding gasket between the body of the
product and the pipe connection.
4. Connect the gasket between the body of the product and
the pipe connection using clamps.
5. Re-attach or reactivate all safety and protective devices.
9.3 Installation with butt weld spigots
Fig.2: Butt weld spigots
1. Carry out preparation for installation (see chapter "Pre-
paring for installation").
2. Remove the actuator before welding the valve into the
plant (see chapter "Removing the actuator").
3. Adhere to good welding practices!
4. Weld the body of the product in the piping.
5. Allow butt weld spigots to cool down.
6. Mount the actuator on the valve body (see chapter
"Mounting the actuator").
7. Re-attach or reactivate all safety and protective devices.
8. Flush the system.
10 Electrical connection
Establish the electrical connection as described in the con-
troller manufacturer's information.
11 Commissioning
üThe product is installed in piping.
üThe product is connected electrically and the control unit
configured accordingly.
1. Check the leak-tightness and the functioning of the
product (close the product and open it again).
2. Flush the piping system of new plant and following repair
work (the product must be fully open).
ðHarmful foreign matter has been removed.
ðThe product is ready for use.
3. Commission the product.

12 Troubleshooting
Error Error cause Error clearance
Working medium escapes from leak
detection hole
Plug diaphragm faulty Check plug diaphragm for potential
damage, replace plug diaphragm if
necessary
The product doesn't open or doesn't
open fully
Actuator faulty Replace actuator cartridge, replace
actuator if necessary
Plug diaphragm incorrectly mounted Remove actuator, check plug diaphragm
mounting, replace plug diaphragm if
necessary
The product leaks downstream (doesn't
close or doesn't close fully)
Operating pressure too high Operate the product with operating
pressure specified in datasheet
Plug diaphragm incorrectly mounted Remove actuator, check plug diaphragm
mounting, correct if necessary
Foreign matter between plug diaphragm
and valve seat
Remove actuator, remove foreign matter,
check plug diaphragm and valve body for
damage and replace if necessary
Valve body leaks or is damaged Check valve body for potential damage,
replace valve body if necessary
Plug diaphragm faulty Check plug diaphragm for potential
damage, replace plug diaphragm if
necessary
The product leaks between actuator and
valve body
Plug diaphragm incorrectly mounted Remove actuator, check plug diaphragm
mounting, correct if necessary
Bolting between valve body and actuator
loose
Retighten bolting between valve body
and actuator
Plug diaphragm faulty Check plug diaphragm for potential
damage, replace plug diaphragm if
necessary
Actuator/valve body damaged Replace actuator/valve body
Valve body connection to piping leaks Incorrect installation Check installation of valve body in piping
Sealing material faulty Replace sealing material
Valve body leaks Valve body leaks or is corroded Check valve body for damage, replace
valve body if necessary
Valve doesn't open/close or doesn't
open/close fully
Voltage is not connected Connect voltage
Cable ends incorrectly wired Wire cable ends correctly
12 Troubleshooting
www.gemu-group.com 17 / 24 GEMÜ F60

www.gemu-group.com18 / 24GEMÜ F60
13 Inspection/servicing
13 Inspection/servicing
NOTICE
Exceptional maintenance work!
▶Damage to the GEMÜ product.
●Any maintenance work and repairs not described in
these operating instructions must not be performed
without consulting the manufacturer first.
The operator must carry out regular visual examination of the
GEMÜ products depending on the operating conditions and
the potential danger in order to prevent leakage and damage.
The product also must be disassembled and checked for
wear in the corresponding intervals.
1. Have servicing and maintenance work performed by
trained personnel.
2. Wear appropriate protective gear as specified in plant op-
erator's guidelines.
3. Shut off plant or plant component.
4. Secure plant or plant component against recommission-
ing.
5. Depressurize the plant or plant component.
6. Actuate GEMÜ products which are always in the same
position four times a year.
13.1 Replacing the actuator
13.1.1 Removing the actuator
CAUTION
Danger - high voltage!
▶Electric shock.
●Before performing any work on the
GEMÜ product switch off power and
protect circuit from being switched on
again.
WARNING
The equipment is subject to pressure!
▶Risk of severe injury or death.
●Depressurize the plant.
●Completely drain the plant.
CAUTION
Hot plant components!
▶Risk of burns!
●Only work on plant that has cooled
down.
WARNING
Corrosive chemicals
▶Risk of caustic burns
●Wear suitable protective gear.
●Completely drain the plant.
CAUTION
Use of incorrect spare parts!
▶Damage to the GEMÜ product.
▶Manufacturer liability and guarantee will be void.
●Use only genuine parts from GEMÜ.
CAUTION
Risk of cartridge falling out
▶This will damage the cartridge.
●Take care removing the cover, because the cartridge can
come loose in the cover.
1. De-energize the motorized actuator (unplug it from the
controller).
2. Undo the grub screw in the opening protection.
3. Unscrew the motorized actuator from the valve body.
ðIf the product is firmly welded into the plant, the mo-
torized actuator can be removed with a hook wrench
by turning it anticlockwise.
ðIf the product is not installed, the cover must be
clamped in a vice with aluminium jaws.
4. Carefully remove the motorized actuator from the valve
body.
5. Remove the motorized actuator and dispose of it cor-
rectly as necessary.
NOTICE
Important:
▶After disassembly, clean all parts of contamination. Take
care not to damage the parts in the process. Afterwards,
check parts for potential damage. If parts are damaged,
replace them.

www.gemu-group.com 19 / 24 GEMÜ F60
13.1.2 Mounting the actuator
1. Mount the motorized actuator on the valve body.
ðIf the valve is firmly welded into the plant, the cover
can be tightened with a hook wrench.
ðIf the valve is not installed, the valve body must be
clamped in a vice with aluminium jaws.
2. Tighten the grub screw in the opening protection.
3. Connect the controller.
4. The valve can be commissioned.
13.2 Replacing the cartridge
13.2.1 Removing the cartridge
1. De-energize the motorized actuator (unplug it from the
controller).
2. Undo the grub screw in the opening protection.
3. Remove the motor from the cover by turning it anticlock-
wise (wrench with wrench size 36). If required, secure the
cover with a hook wrench.
ðIf the valve is firmly welded into the plant, the motor
can be unscrewed with the wrench.
ðIf it is not installed, the valve must be clamped in a
vice (with aluminium jaws) before the motor can be
unscrewed.
4. Pull the motor upwards and release the radial slot.
ðThe motor can be removed.
5. Remove the cover.
ðIf the valve is firmly welded into the plant, the cover
can be unscrewed with a hook wrench.
ðIf it is not installed, the valve must be clamped in a
vice (with aluminium jaws) before the cover can be
unscrewed.
6. Carefully remove the cover.
ðThe cartridge can either be on the valve body or loose
in the cover
7. Remove the cartridge and dispose of it correctly.
13.2.2 Fitting the cartridge
1. Grease the cartridge with a suitable lubricant (e.g. Tunap
Tungrease ST3 grease).
2. Grease the cover with a suitable lubricant (e.g. Tunap
Tungrease ST3 grease).
Klick!
3. Insert the lubricated cartridge into the cover.
4. Press it into the collar of the plug diaphragm until you
hear it click into place.
5. Mount the cover.
ðIf the valve is firmly welded into the plant, the cover
can be tightened with a hook wrench.
ðIf it is not installed, the valve must be clamped in a
vice (with aluminium jaws) before the cover can be
tightened.
6. Hook the motor adaptor back into the radial slot on the
cartridge and press the motor onto the cover.
ðThe actuator spindle of the motor retracts.
13 Inspection/servicing

www.gemu-group.com20 / 24GEMÜ F60
13 Inspection/servicing
7. Tighten the motor on the cover with a wrench.
ðIf the valve is firmly welded into the plant, the motor
can be tightened with the wrench.
ðIf it is not installed, the valve must be clamped in a
vice (with aluminium jaws) before the motor can be
tightened.
8. Tighten the grub screw in the opening protection.
9. Connect the controller.
10. The valve can be commissioned.
13.3 Replacing the plug diaphragm
13.3.1 Removing the plug diaphragm
CAUTION
Use of incorrect spare parts!
▶Damage to the GEMÜ product.
▶Manufacturer liability and guarantee will be void.
●Use only genuine parts from GEMÜ.
1. De-energize the actuator (unplug it from the controller).
2. Remove the actuator from the valve body.
ðIf the valve is firmly welded into the plant, the actuator
can be unscrewed with a hook wrench.
ðIf it is not installed, the valve must be clamped in a
vice (with aluminium jaws) before the actuator can be
unscrewed.
3. Carefully remove the unscrewed actuator from the valve
body.
4. Unscrew the plug diaphragm from the cartridge by hand
by turning it anticlockwise and dispose of it in line with
regulations.
13.3.2 Mounting the plug diaphragm
1. Screw the plug diaphragm onto the male thread of the
cartridge by turning it clockwise and tighten it until it is
hand tight.
2. Mount the actuator on the valve body.
ðIf the valve is firmly welded into the plant, tighten the
actuator with a hook wrench.
ðIf it is not installed, the valve must be clamped in a
vice (with aluminium jaws) before the actuator can be
tightened.
3. Connect the controller.
4. The valve can be commissioned.
13.4 Cleaning the product
– Clean the product with a damp cloth.
– Do not clean the product with a high pressure clean-
ing device.
Other manuals for F60
1
Table of contents
Other GEM Control Unit manuals
Popular Control Unit manuals by other brands
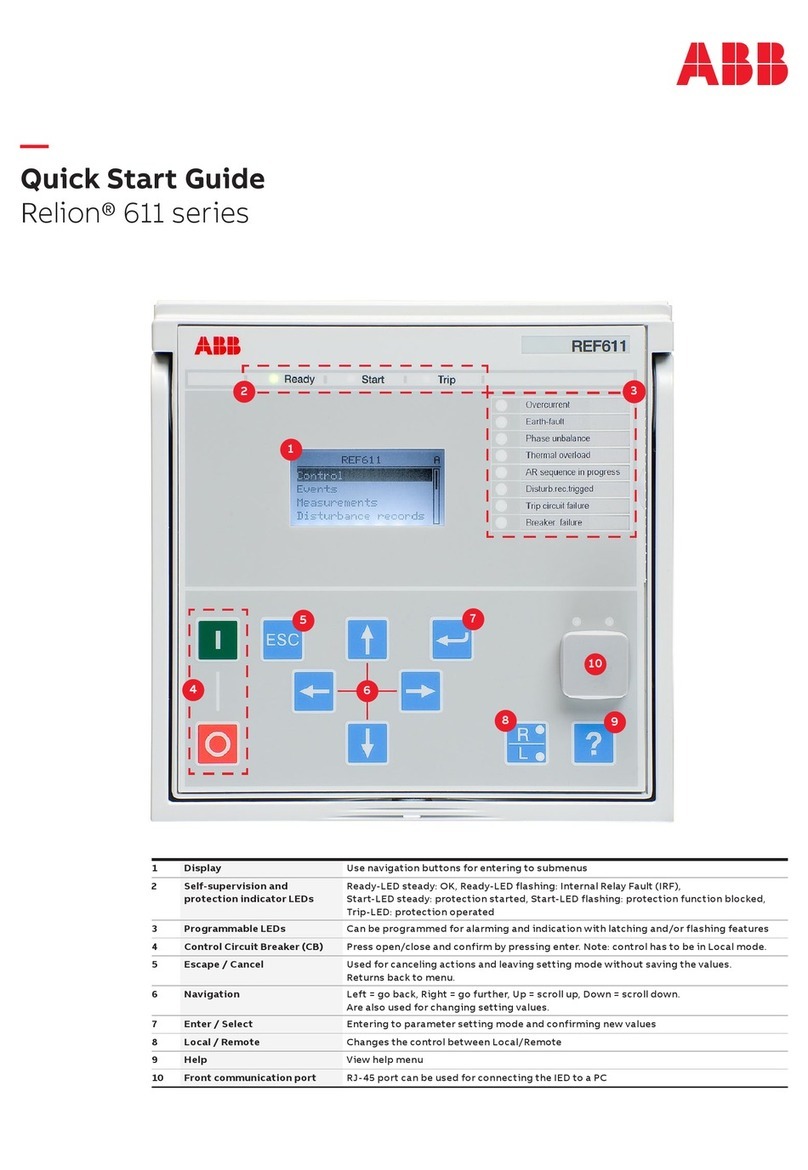
ABB
ABB Relion 611 Series quick start guide
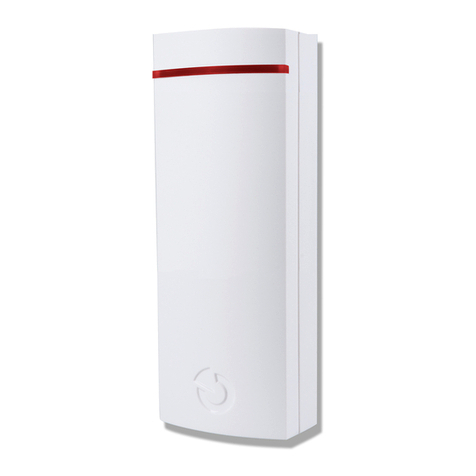
jablotron
jablotron JA-112M Installation
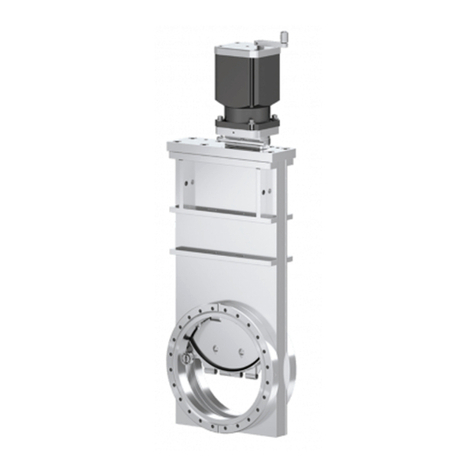
VAT
VAT 10.8 Series Installation, operating, & maintenance instructions
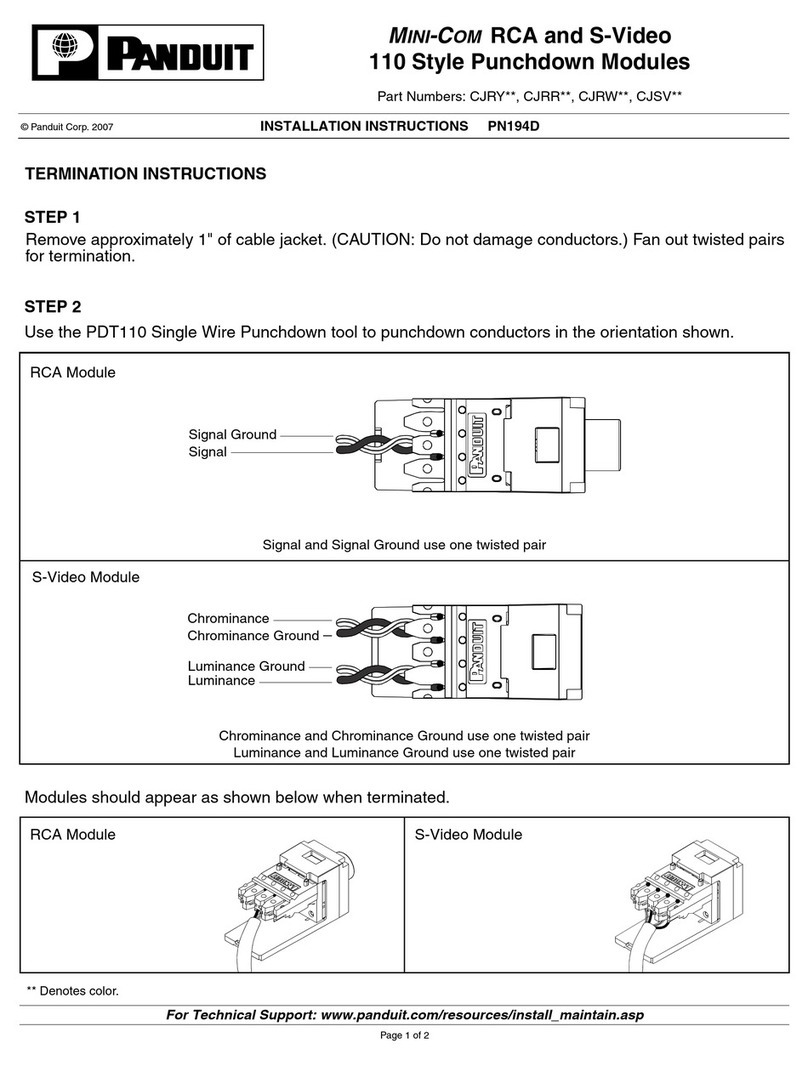
Panduit
Panduit CJRR Series installation instructions

Pro1 Technologies
Pro1 Technologies Z260W installation manual
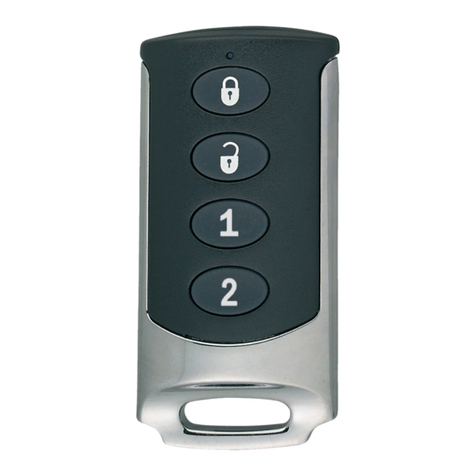
Interlogix
Interlogix RF-KF101-K4 Installation sheet
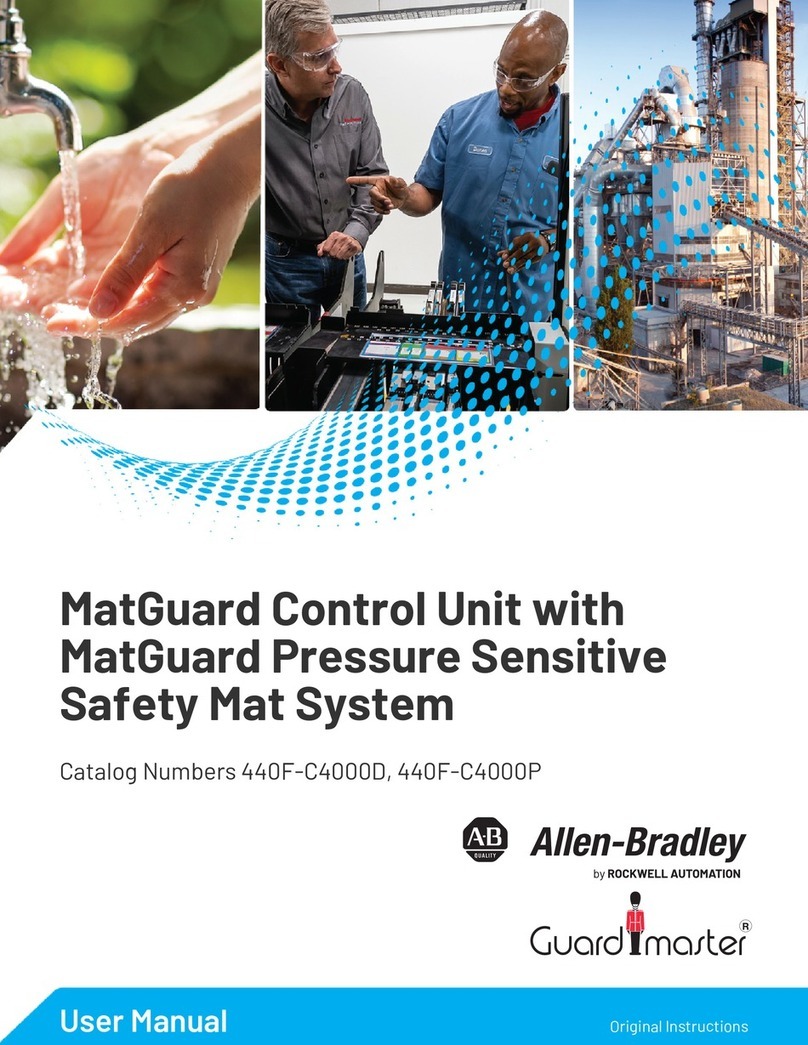
Rockwell Automation
Rockwell Automation Allen-Bradley Guard master 440F-C4000D user manual
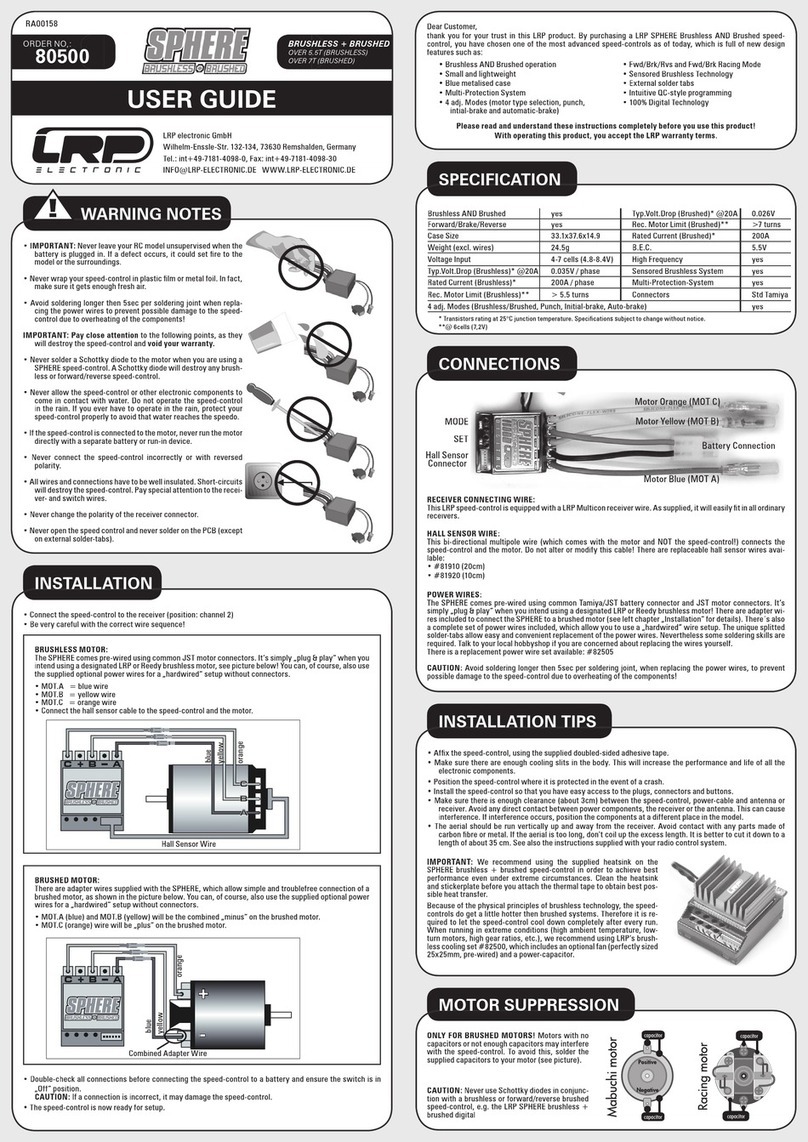
LRP electronic
LRP electronic Sphere BRUSHLESS + BRUSHED user guide
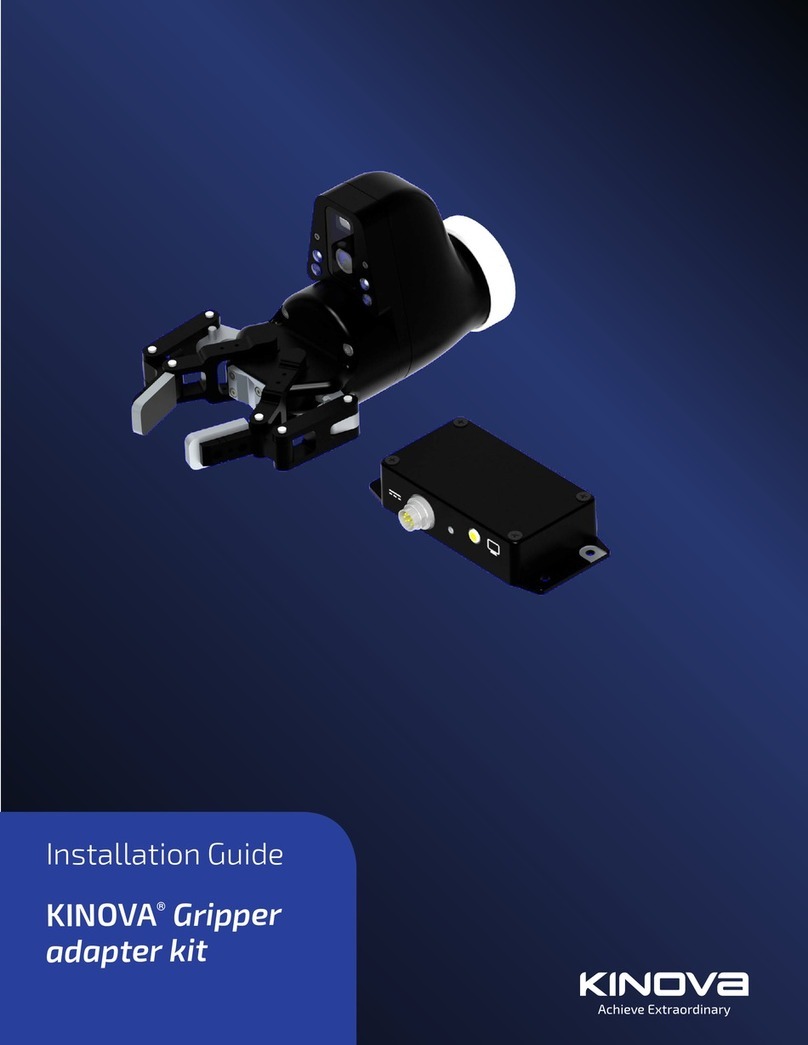
Kinova
Kinova Gripper adapter KR11703-01 installation guide
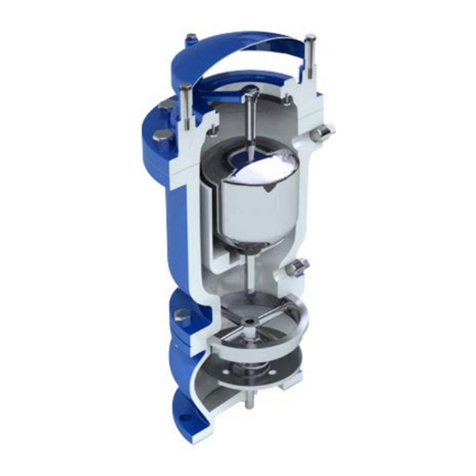
DeZurik
DeZurik APCO AVV-140 instructions

Sanhua
Sanhua TXV Series technical information

LG
LG LGSBWAC95 user manual