IBM 1403 User manual

Fo
r
m
`7"1J-6443
-1
tamer Engineering
Reference
an«i
International
Business Machines Corp ration
Data Processing Division
112
East Post Road,
White Prins, N
. '.
Printer

Printer
El
r
1
r
J r
V`
Customer Engineering
Reference Manual
L J
Issued to•
Branch Office-
Department:
Address•
If this manual is mislaid, please
return it to the above address

Contents
PREVENTIVE MAINTENANCE
APPROACH TO PREVENTIVE MAINTENANCE
PREVENTIVE MAINTENANCE PROCEDURES
5
5
Chain to Type Array Reassembly
Lower Plate to Type Array Assembly
Adjust Magnetic Read Head
Magnetize Timing Disk
18
19
21
21
INSTALLATION PROCEDURE
HAMMER UNIT
21
Hammer Unit Removal
21
Base Installation
6
Position the Hammer Unit (Factory and Field) ....
21
Three-Phase Motor Rotation
6
Remove Hammer Magnet Assembly
22
Systems Check-Out
6
Individual Hammer Magnet Coil Replacement
22
Hammer Removal
22
REMOVALS AND ADJUSTMENTS
RIBBON UNIT
22
COVER REMOVAL
7
Remove Ribbon Drive Unit
22
Top Forms Guide
7
Position Ribbon Drive Unit
22
Front Cover
7
Adjust Ribbon Skew
24
Top Cover
7
Adjust Ribbon Shield and Print Line Indicator ....
24
Inner Front Cover
7
Remove Lower Ribbon and Brake Assembly
24
MANUAL CONTROLS — ADJUSTMENTS
7
Remove Upper Ribbon Drive and Brake Assembly ..
24
Horizontal Print Alignment Lever
Horizontal Print Alignment Vernier
Vertical Print Alignment Knob
7
7
7
Disassemble Ribbon Drive and Brake Assembly ...
Ribbon Clutch Adjustment — Out of Machine
Ribbon Drive Motor Positioning
25
25
25
Print Control Dial
7
HYDRAULIC UNIT
27
Forms Width Vernier
9
Hydraulic Unit Removal
27
Manual Clutch and Line-Selection Lever
10
Hydraulic Unit Replacement
28
FORMS POSITIONING
10
Hydraulic Unit Reservoir Removal
28
Tractor Shafts and Tractor Guide Bars
10
Remove Control Valve Assembly
28
Removal of Individual Pin Feed
12
Hydraulic Unit Reassembly
28
Forms Tractor Adjustments
12
Hydraulic Pump Drive Belt Tension
29
Position Upper and Lower Tractor Drive Shafts
Install Tractors
12
12
CARRIAGE CONTROLS
Space Control Magnets Adjustments
29
29
Replace Tractor Shafts and Guide Bars
Tractor Jam-Detection Device Adjustments
Forms Stacker Assembly Adjustment
13
13
13
Space Control Valves Adjustments
Skip Control Magnets Adjustments
Skip Control Valves Adjustments
30
31
31
BASE ADJUSTMENTS
13
Hydraulic Detent Stop Adjustments
31
Grounding of Forms Carts
13
Space Needle Valve Adjustments
31
Level Left Shock Mount
13
Skip Needle Valve Adjustment
Remove Translator Frame
13
(2-Speed Carriage Machines)
31
Position Translator Frame
14
Bypass Needle Valve Adjustments
32
Remove Movable Base
14
Single-Space Single-Shot Adjustments
32
Remove Movable Base Eccentric Shaft
14
Emitter Brush Adjustments
33
Adjust Movable Base
14
Carriage Tape Brushes ( Statically) Adjustments ....
33
Remove T-Casting
15
Carriage Tape Brushes (Dynamically) Adjustments 34
Replace T-Casting
15
Position T-Casting (Factory)
15
LOCATIONS AND VOLTAGE SPECIFICATIONS
Position T-Casting Horizontally (Field)
Position T-Casting Vertically (Field)
Adjust T-Casting Latch
16
16
16
Voltage
Voltage Variation
Serial Plate
36
36
36
TYPE ARRAY (Cartridge Assembly)
17
Ground
36
Type Array Removal
17
Connectors
36
Type Array Disassembly — Out of Machine
17
Resistors
36
Center and Upper Plate Reassembly —
Main-Line Switch
36
Flat Idler Spring
18
Convenience Outlets
36
Center and Upper Plate Reassembly —
Terminal Blocks
36
Coil Idler Spring
18
Thermistors
36
© 1960, 1961 by International Business Machines Corporation

~.
(
Preventive Maintenance
Approach to Preventive Maintenance
The prime objective of any maintenance activity is to pro-
vide maximum machine availability to the customer. Unless
a preventive maintenance operation reduces machine down-
time, it is unnecessary.
Do not adjust or disassemble a unit that is working prop-
erly, even if tolerances vary from specifications.
Be visually alert for trouble indications any time you
service the machine. Look for corrosion, wear, cracks,
burned contacts, and loose connections. Watch for filters
clogged with dirt.
Preventive Maintenance Procedures
The three basic steps of preventive maintenance are clean,
lubricate, and inspect. Do not do more than scheduled pre-
ventive maintenance on equipment which is operating satis-
factorily. Refer to Figure 1.
Apply lubrication only in the quantity necessary to
supply that immediate area involved.
Wipe off excess.
On
the 1403, special care must be taken to keep lubricants
away from:
Ribbon
Cover seals
Paper path
Rubber dampers
Electrical wiring
Grommets
Magnetic clutch disk
P M ROUTINE
CODE
UNIT
FREQ
(Weeks)
LUBRICATE
CLEAN
OBSERVE
5
DRIVE
Type Array
Type Array
Drive
4
Fill right oil reservoir in T-
casting
0
6.
Clean type array with vacuum
cleaner as required.
Check that reservoir never
runs dry. Check that oil is
being used (reaches chain).
Fill plastic oil reservoir at
rear of T-casting
0
9.
Check that reservoir never
runs dry. Check that oil is
being used.
2
PRINT
Ribbon
Toggle plate pivot
0
6.
Reverse toggle spring anchor
0
24. Skew roller pivot
0
6.
Sense finger pivot
0
6,
Excessive oil and grease must
be wiped from all areas to
prevent any contamination of
ribbon.
Check for wear.
5
DRIVE
Ribbon
Drive Unit
-
13
All gears
0
70 (light film), All
bearings, pivots, and clutch
shafts
0
6.
Friction disk inter-
poser stud and ball
0
6.
Pinion spline 06.
Keep friction drag surfaces oil
free. Excessive oil and grease
must be wiped from all sur-
faces to prevent any contain-
ination of ribbon.
Check for wear and binds.
Check for correct operation.
Lube only when
surface appears dry.
0
BLOWERS
Hammer Unit
Replace blower air filter as
necessary.
1
FEED
Tractor
Stacker
Light film of lubriplate
0
70
on tractor drive gears,
tractor ramps, and tractor
shafts.
Check tractor adjustments as
required.
Bevel drive gears
0
70. (Use
light film of grease only).
Friction drive shaft
0
6. Lift
shaft '
0
6.
Clean as necessary.
Check for broken friction
springs as required.
Check for wear on friction
drive roll.
2
PRINT
Hammer Unit
Strip residual
and strip re-
sidual fasten-
ing bands
Type Array
Drum
Hammer magnet armature
pivots
0
6. Hammer surfaces
that contact armatures (light
film
0
6.)Armature backstops
(light film
0
6.)
Check for loose hammers.
Check for loose magnet coils.
Check for worn residuals on
hammer magnet face (core).
Replace every 26 weeks
Clean type array with vacuum
cleaner as required.
Check for proper tension in
chain (316" sag of slugs at
front of type array when type
array is held with front side
down).
Wipe off surface of timing
disk with clean cloth.
Check and clean as necessary.
3
EMITTER
Emitter
Contact Rolls
26
Emitter surface #6 (light
film)
Check for worn brushes.
Check for pitted surface.
Contact roll bearings
0
6.
Clean contact rolls as necess-
ary.
Check tape brushes for loose
strands.
5
DRIVE
Ribbon
Drive Unit
Hydraulic
Unit
6-8 Line
Drive
Ribbon
drive motor (2 all
cups)
0
6.
Blower motor (2 oil cups)
0
6.
Check timing belt for tension.
Only when leakage is appar-
ent, check proper hydraulic
fluid level. (Approx. to
bottom of coils).
Light film
0
70 on active sur-
faces of all gears, shift fork,
summing plate, and detent
wheels.
Detent arm pivots and rollers
0
6.
Check for correct operation.
9
MISC
Frame
T-Casting
Ph eonolic
Support
Chock
Use light film of
0
24
on act-
ive surfaces of gears, slides,
guides, and levers as re-
quired. Use
0
6 on bearings,
bushings, and pivots as re-
quired.
Check for and binds.
Check adjustments as required.
1403
Figure 1. IBM 1403 PM Routine
PREVENTIVE MAINTENANCE
5

Timing Disk Housing
Cylindrical Nut
Stop Collar
T Casting
Read Head
—
Timing
Disk
Oil Reservoir
Timing Disk Drive Gear
Movable Base
Mount Block
Mechanical Latch Interlock
Print Control Dial
< /
\
>
\
\ \ Connecting
Bolt
Hollow Shaft
Type Array
Drive Motor
Interlock Switch
Limit Stud
Print Timing Slide
Oiler
Knurled Bushing
T -
Casting Lock Lever
~
e
~
Figure 3.
Left End of T-Casting
2. Set up the system.
a.
Program to print continuous lines of H's.
b.
Press the start key.
3. Position the read head for correct horizontal print
alignment.
a.
Hold the print control dial at the correct setting.
b.
Position the cylindrical bolt. Turn the bolt with a
screwdriver and determine the left and right limit of
character cut off.
c.
Turn the bolt to the position midway between the
limits found.
4. Press the carriage stop key.
5. Examine the printing for alignment. Individual posi-
tion misalignment can be corrected by adjusting individual
hammer magnets for armature to core clearance.
Forms Width Vernier
1. Prepare to adjust vernier.
a.
Remove knobs.
b.
Remove the inner front cover.
c.
Remove the gear guard.
d.
Replace the knobs.
e.
Locate the left forms tractors in corresponding
slots in the tractor guide bars.
f.
Locate the right forms tractors in corresponding
holes in face of the removable slides.
g.
Locate the forms tractors apart at the extremes of
the guide bars.
2. Adjust the left tractor pin feeds horizontally (in a
vertical line) .
l
Figure 2. Translator Frame
8
REMOVALS AND ADJUSTMENTS
9

Figure 4. 6-8 Line Drive
~
6
a.
Place a straight edge along the pin feeds to check
for alignment.
b.
Shift the tractor guide bars to align the pin feeds
within 0.005". There are two screws in each end of the
bar.
c.
Keep the left horizontal surface of guide bar
against the corresponding horizontal lip of the printer
casting.
3. Adjust the right tractor pin feeds.
a.
Orient the horizontal adjusting screws and vertical
drive collar to align the right pin feeds within 0.005"
horizontally (in a vertical line) .
b.
Place a straight edge along the pin feeds to check
for alignment.
c.
It may be necessary to reposition the horizontal
adjusting screws in relation to the collars and gears to
obtain adjustment.
d.
Position the friction nuts and collars for a maxi-
mum end play of 0.002".
4. The forms width vernier must operate with light
finger force.
5. After this adjustment has been made, adjust the verti-
cal position of the right ends of the upper and lower tractor
guide bars for free movement of tractor assemblies.
Manual Clutch and Line
-
Selection Lever (Figure 4)
1. Prepare for adjustment.
a.
Move the translator frame to the left.
b.
Remove the front inner cover.
c.
Remove the manual clutch knob.
d.
Remove the manual advance knob.
e.
Remove the rear 1403 cover.
2. Check the adjustment of the manual clutch and the
line-selection lever assembly.
a. Check for clearance:
(1)
For a minimum end play of the detent arms
on the shaft.
(2)
For a minimum of 0.025" between the detent
and the detent wheel when the detent is inoperative.
(3)
Between the tines of the shift fork and the
slide gear hub.
b. Check for alignment:
(1)
of the detent arms to the slots in the camming
plate.
(2)
of the detent wheels to the detent arms.
c. Check for correct operation that:
(1)
the clutch shifts from 6- to 8-line drive and
vice versa.
(2)
the spring causes correct operation of the de-
tent arms and wheels (there should be a force of
4
1
/
z
to 6
1
/
2
pounds on the detent arm).
(3)
the detent arm roller seats fully in the detent
wheel when the detent is operative.
3. If the conditions in step 2 are met, no further adjust-
ment is necessary. Proceed to step 12.
4. Further prepare to adjust the manual clutch and line-
selection lever assembly.
a.
Unhook the detent arm springs.
b.
Loosen both the detent wheels.
c.
Slide the right detent wheel to the right.
d.
Loosen the detent arm collars.
e.
Slide the detent arms to the left.
f.
Loosen the camming plate on the shift fork so that
the plate is just free to slide.
g.
Loosen the set screw that holds the camming plate
stop rod.
h. Wedge the paper between the shift fork tines and
hub of shift gear to center around shift gear hub.
5. Position the shift fork on the shift rack for gear mesh
and clearance.
a.
Detent the shift rack in 6-line drive at the right.
b.
Position the shift fork on the shift rack so that the
slide gear meshes with the 6-line driving and driven
gears and has clearance to the casting.
c.
Rotate the shift fork around the shift rack to center
the shift fork around the shift gear hub.
d.
Clamp the shift fork to the shift rack.
6. Align the detent arms to the camming plate.
a.
Set the slide gear to 6-line drive position.
b.
Align the detent arms with the left two slots in the
camming plate.
c.
Tighten the collars to hold the detent arms in
position.
7. Adjust for a clearance between the detent wheels and
the detent arms of 0.025" with the manual clutch in either
6- or 8-line drive.
a.
Turn the 6- and 8-line gear idler to a position
where it does not move when the slide gear is shifted
from the 6-line drive to the 8-line drive or, vice versa.
b.
Set the slide gear to the 8-line neutral position.
c.
Slide the right detent wheel opposite the right de-
tent arm.
d.
Use the rubber band to hold the right arm against
detent.
e.
Adjust the camming plate roller stop to provide a
0.025" clearance between the detent arm and tooth of
the right detent wheel.
f.
Tighten the set screw to hold the camming plate
roller stop rod.
g.
Rehook the springs on the detent arms.
h.
Clamp the camming plate to the shift fork.
8. Align the detent wheels to the detent arms.
a.
Set the manual clutch to 8-line neutral.
b.
Align the left detent wheel to the left detent arm.
c.
Clamp the left detent wheel to the tractor shaft.
d.
Set the manual clutch to 6-line neutral.
e.
Align the right detent wheel to the right detent
arm.
f.
Clamp the right detent wheel to the tractor shaft.
g.
Check the operation of the manual clutch for four
manually operated spaces.
h.
Re-adjust as necessary.
9. Set the spring tension to provide 41/2 to 6
1
/z pounds
force on the detent arm when it is engaged in the detent
wheel.
10. Remove the paper from between the shift fork tines
and the shift gear hub.
11. Position clutch interlock switch.
a.
Switch to make when the plunger is within 3/2 of
bottoming in the grooves of the shift rod.
b.
Position the switch to obtain this adjustment.
12. Replace the remaining parts in reverse order.
Forms Positioning
Tractor Shafts and Tractor Guide Bars
This procedure is given for the removal of the upper and
lower tractors, the tractor guide bars, and the drive shafts.
If only one set is to be removed, do only so much of each
step that will allow the desired set to be removed.
10
REMOVALS AND ADJUSTMENTS
11

Prepare to remove tractor guide bars and tractor drive
shafts.
1.
Remove the forms.
2.
Remove the binary paper guides from the tractor
guide bars.
3.
Remove the inner front cover.
4.
Remove the upper and lower forms guide bars with
the jam bars attached.
5.
Remove the jam contact mountings from the tractor
guide bars.
6.
Remove the wires from the form stop contacts at the
terminal block.
7.
Shift the T-casting to the left.
8.
Remove the gear guard.
Separate vertical shaft of forms width vernier. Loosen
the set screws in the vertical coupling of the forms width
vernier. Move the vertical coupling up onto the upper shaft
and lock to the shaft.
Remove the bearing caps.
1.
Loosen the screws that prevent bearing end shake (at
right).
2.
Remove the two bearing holding screws (at right)
for each bearing cap.
3.
Shift T-casting to the right.
4.
Remove the two bearing cap holding screws (at left)
for each bearing cap.
5.
Remove both bearing caps.
Remove the tractor guide bar and the tractor shaft.
1.
Remove the two screws and the slide-retainer-plate
at the left end of one of the tractor guide bars.
2.
Remove the two holding screws at the right end of
the same tractor guide bar.
3.
Lift the tractors, the guide bar, and the shaft out and
to the left to clear the T-casting.
Repeat step 5 for other assembly.
Remove Individual Pin Feed
Prepare for removal.
1.
Open the T-casting.
2.
Remove the forms.
3.
Open the tractor door.
Remove the tractor paper guides.
1.
Remove the tractor paper guide farthest from the
hinge of the door.
2.
Remove the tractor guide on the other side of the
pin feeds.
Align the pin-feed holding pins with the slot in the frame
spacer plate (the end nearest the drive shaft).
1.
Turn the tractor shaft until one holding pin aligns
with the slot.
2.
Use a similar pin to push the installed pin towards
the center of the machine.
3.
Repeat step 2 for the second holding pin.
Remove the pin feed by lifting. Insert the new pin feed.
Replace the pin feed holding pins.
1.
Insert the second pin.
2.
Turn the tractor shaft until the first holding pin hole
is aligned with the slot.
3.
Insert the first pin.
NOTE:
Pins are to be flush or slightly recessed.
Replace the tractor paper guides in reverse order. (See
Forms Tractor Adjustments.)
Forms Tractor Adjustments
Adjust the belt tension.
1.
Maintain parallelism between the axes of the rotation
of the drive sprocket and of the movable sprocket.
2.
Position the movable sprocket stud for a minimum
slack at the point of tightest engagement.
a.
Insure that belt tension is not excessive.
b.
Tighten the sprocket stud.
Position beveled ramps.
1.
The point of the ramp must point in the direction
opposite to the belt motion.
2.
Position the ramp for a clearance to the respective
sprocket hub of 0.002" to 0.007".
3.
Clamp in position.
Position the tractor paper guides.
1.
Align the edge of the paper guide nearest the door
pivot plate flush to the pivot plate.
2.
Position the underneath side of the paper guide flush
against the edge of the spacer plate.
3.
With the conditions in steps 1 and 2 established,
secure both paper guide and mounting block with their
front surfaces flush to the front edge of the spacer plate.
4.
Position the lower edge of the adjacent paper guide
against the lower edge of the paper guide nearest the door
pivot, maintaining the upper edges parallel.
5.
Fasten the adjacent paper guide to the tractor frame.
Position the tractor door for a clearance of paper guide
plates to the door runners of 0.048" to 0.056".
1.
Loosen the pivot plate.
2.
Screw the door stop in below the correct door setting.
3.
Insert two sets of feeler gages with the correct setting.
4.
Force the door against the feeler gages.
5.
Tighten the pivot plate.
6.
Set the door stop to hold the door at the correct
clearance.
Position the form stop switch to make when the form
stop lever is within 9 2"" of the front surface of the paper
guide.
Position Upper and Lower Tractor Drive Shafts
First, check the forms width vernier. Prepare to adjust the
drive shafts.
1.
Position the left forms tractors in the corresponding
slots in the tractor guide bar.
2.
Position the right forms tractors in the corresponding
holes in the face of the movable slides.
3.
Place a form in the forms tractors.
Check the position of the upper drive shaft to the lower
tractor drive shaft. The form must fit in tractors with a
minimum slack in paper. Feed the forms manually and
check for no elongation of the pin feed holes (this may
occur under power).
If the condition just described is met, the adjustment is
complete. Replace any remaining parts in reverse order.
If necessary, adjust the upper tractor drive shaft in relation
to the lower tractor drive shaft.
1.
Loosen the upper tractor shaft drive gear.
2.
Manually rotate the shaft to remove slack.
3.
Clamp the drive gear to the shaft.
Replace any remaining parts in reverse order.
Install Tractors
This procedure refers to both the upper and the lower
assembly. Place the tractor shaft and the guide bar in rela-
tive positions on a flat surface.
Install the tractors on the drive shaft.
1.
Slide the drive shaft through the square drive hub
on the right tractor.
2.
Turn the left tractor drive until the pins line up with
those on the right tractor and, at the same time, the drive
hub lines up with the drive shaft.
3.
Slide the drive shaft through the square drive hub
on the left tractor.
Install the tractors on the guide bar. Slide the guide bar
through right and left tractors.
Replace Tractor Shafts and Guide Bars
Place the tractors, the guide bar, and the tractor shaft in
the machine.
1.
Set the assembly in the machine.
2.
Insert the screws in the slide-retainer plate and the
guide bar at the left and turn the screws in a few turns.
3.
Insert the holding screws at the right end of the guide
bar and turn in until nearly snug.
Repeat this step for the other assembly.
Install the bearing caps.
1.
Slide the bearing and bearing retainer ring in position.
2.
Place the bearing cap in position.
3.
Insert the two right bearing cap holding screws and
tighten until almost snug.
4.
Insert the two left bearing cap holding screws and
tighten.
5.
Snug up the bearing end screws.
6.
Tighten the right bearing cap holding screws.
7.
Tighten the bearing end screws.
Repeat this step for the other assembly.
Position the tractor guide bars.
1.
Slide the tractors apart to extreme positions.
2.
Position the tractor guide bars against the lip on the
printer casting at the left.
3.
Shift the guide bars horizontally to vertically position
the left tractor pins on the upper guide bar within 0.002"
of the left tractor pins on the lower guide bar. Use a straight
edge laid along the tractor pins for determining vertical
alignment.
Connect the vertical shaft of the forms width vernier.
1.
Loosen the set screws in the vertical coupling and
slide into engagement with the upper and lower shaft.
2.
Clamp the coupling to both shafts.
Perform the following adjustments:
1.
Adjust the forms width vernier.
2.
Position the upper and lower tractor drive shafts.
Replace the remaining parts in reverse order.
Tractor Jam-Detection Device Adjustments
This applies to both upper and lower detention devices.
Check the jam-detection device.
1.
The jam bail must rest against both the left and right
tractor doors.
2.
The rear edge of the bail mounting brackets must be
flush to the rear side of the forms support bar.
3.
When applied at operating edge of bail, the bail move-
ment must be free.
4.
A force of
1
/2
pound (225 grams) must move bail away
from the tractor door.
5.
The switch plunger must be 0.010" to 0.015" past
the toggle point when the bail is resting against the tractor
doors.
6.
The switch plunger must be free of the bail when the
tractor doors are opened against the form guide support bar.
If these conditions in step 2 are met, no further adjust-
ment is necessary.
Adjust the jam-detection bail.
1.
Loosen the bail mounting brackets.
2.
Rest the bail against both form tractors.
3.
Position the rear edge of the mounting bracket flush
to the rear side of forms guide support bar within 0.005".
4.
Tighten the mounting bracket in position.
Adjust bail torsion spring.
1.
Loosen the lock nut on the spring stud.
2.
Turn the screw and tighten the lock nut.
3.
Check for a
1
/2
pound force to move the bail away
from the tractors.
4.
Re-adjust as necessary.
Position the bail switch.
1.
Loosen the holding screws.
2.
Insure that the jam bar is against the tractor cover.
3.
Locate the switch so that the switch plunger is moved
0.010" to 0.015" past the toggle point.
4.
Tighten the holding screws.
Forms Stacker Assembly Adjustment
1.
Stacker tension springs are to be adjusted to feed rolls
to a point of tangency without compressing spring. (Too
much tension will tear the paper).
2.
Bevel gears on countershaft assembly, and friction
drive shaft assembly are to be positioned for .002" to .004"
wink and alignment of the crown points of each gear; i.e.,
full tooth engagement.
3.
If the teeth do not engage correctly, both shafts will
have to be repositioned. Check again for .002" to .004"
wink after obtaining the correct tooth engagement.
Base Adjustments
Grounding of Forms Carts
Adjust the forms cart guides so that their contact springs
press firmly against the sides of both the front and rear
carts when they are in position.
Level Left Shock Mount
Level the left shock-mount support casting so that it is
parallel to the printer casting within
1
/8"
in the:
1.
left to the right plane.
2.
front to the back plane.
Adjust the two front and back jackscrews to obtain this.
Remove Translator Frame (Figure 2)
Prepare to remove the translator frame.
1.
Remove the forms.
2.
Remove the top paper guide.
3.
Remove the paper guide at the bottom of the trans-
lator frame.
4.
Remove the front paper guide ( below the translator
frame) .
5.
Remove the ground wire to the translator frame.
6.
Lower the translator frame to the lowest position
with the vertical print alignment knob.
7.
Remove the bumper stop stud,
a.
from the left end of the translator frame.
b.
from the right end of the translator frame.
Remove the tractor shafts and the tractor guide bars.
Remove the T-casting. Remove the hammer unit. Free the
translator frame.
12
REMOVALS AND ADJUSTMENTS
13

~
L
1.
Remove both eccentric stop studs at the bottom rear
of the translator frame.
2.
Loosen both eccentric stop studs at the bottom front
of the translator frame.
3.
Remove the clip on the horizontal print alignment
vernier shaft.
4.
Unscrew the vernier shaft from the translator frame.
5.
Move the horizontal print alignment lever to the
extreme right.
6.
Remove the stop blocks at the top front of the trans-
lator frame.
Remove the translator frame.
1.
Lift the translator frame just enough to take the full
weight of the frame.
2.
Slide the bottom of the frame so that the frame is
clear of the printer casting.
3.
Tilt the top of the frame to the rear, and withdraw
the frame from the front of the machine.
Re-install in reverse order.
Perform the following adjustments:
1.
Position the translator frame.
2.
Position the T-casting front to rear (field).
3.
Position the T-casting vertically (field).
Replace the remaining parts in reverse order.
Position Translator Frame (Figure 2)
Check that the six guide rollers rest against their respective
guiding surfaces. Adjust for 0.002" minimum clearance be-
tween the printer casting and both:
1.
Upper front guide blocks.
2.
Lower rear guide studs.
3.
Lower front guide studs.
Check for freedom of movement of the translator frame
along the printer casting.
Remove Movable Base (Figure 5)
Prepare to remove movable base.
1.
Remove the ribbon.
2.
Remove the type array ( cartridge assembly) .
3.
Remove the cover over the terminal block on the rear
of the T-casting.
4.
Snap out the plastic oil reservoir under the T-casting.
5.
Remove the upper shield over the print control dial.
6.
Remove the screws in the front shield of the print
control dial.
7.
Remove the screws in the movable base front gibs.
8.
Remove the lower ribbon guide.
9.
Work enough slack in the read head cable (untape
the cables if necessary) to allow the movable base to be
lifted clear of the T-casting.
Remove the movable base.
1.
Carefully lift the base up off the eccentric bearing
blocks.
2.
Carefully raise the base so that the print control dial
assembly clears the T-casting lock lever so that read head
cable is not damaged.
Reassemble in reverse order and adjust the movable base
during reassembly.
Remove Movable Base Eccentric Shaft (Figure
5)
Prepare for removal.
1.
First, remove the movable base.
2.
Remove the forms thickness control lever sector.
Free the movable base eccentric shaft.
1. Support the right end of the eccentric shaft and the
drive-out pin (the small end is up) in the forms thickness
control lever.
2.
Remove the forms thickness control lever from the
shaft.
3.
Remove the friction clamp from the right end of the
shaft.
NOTE:
The friction clamp provides the necessary
friction to hold the thickness control lever in position
(A to E) without binding. The shaft must move in the fric-
tion clamp for operator setting of the thickness control
lever.
4.
Loosen the screws in the collar that holds the right
eccentric bearing block, and slide the collar to the right.
5.
Remove the screws under the T-casting that holds
the left and the right bearing blocks to the T-casting.
Remove the eccentric shaft.
1.
Lift the left end of the eccentric shaft so that it clears
the T-casting.
2.
Withdraw the shaft to the left, carefully sliding the
shaft through the right eccentric bearing block.
CAUTION:
The right eccentric holds the oil line and the wick that
oils the type array.
Replace the movable base eccentric shaft in reverse order
and adjust the movable base during assembly.
Adjust Movable Base (Figure 5)
Remove the ribbon and type array.
Check the adjustment of movable base.
1.
The two eccentric shaft support bearings are seated
against the front shoulders of the recess in the T-casting.
2.
A wink of 0.002" exists between the motor drive gear
and the type idler gear
at the point of tightest engagement.
3.
The movable base sets on the T-casting with a maxi-
mum vertical clearance of 0.001".
4.
The movable base slides freely in the horizontal plane.
If the conditions just stated are met, no further adjust-
ment is necessary. Replace the remaining parts in reverse
order.
Further prepare to adjust the movable base.
1.
Remove the cover over the terminal block on the rear
of the T-casting.
2.
Snap out the plastic oil reservoir under the T-casting.
Adjust the clearance of the eccentric shaft support bear-
ings to the front shoulders of the recesses in the T-casting.
1.
Set the print impression control lever to E.
2.
Loosen the mounting screws (under the T-casting)
for the eccentric shaft support bearing.
3.
Position the bearing against the front recess in the
T-casting with a maximum clearance of 0.001".
4.
Tighten the mounting screws.
Adjust the movable base to the T-casting for a maximum
clearance of 0.001".
1.
Tighten the two front gibs that hold the movable
plate to the T-casting ( screws under T-casting) .
2.
Loosen the screws in the lower ribbon guide bar (two
ears hold the movable base against the T-casting) .
3.
Press down hard on the movable base.
4.
Press the ears of the lower ribbon guide bar against
movable base.
5.
Tighten the screws in the lower ribbon guide bar
while maintaining pressure as stated in steps 3 and 4.
Adjust the clearance of the motor drive gear to the type
idler gear. ( Type array was previously removed.)
1. Loosen the adjusting block screw. (The block is under
the movable base, and fits over the stud in the T-casting.
It positions the movable base right to left.)
2.
Turn the idler gear to obtain the tightest mesh with
the motor drive gear.
3.
Slide the movable base left to right to obtain a wink
between the idler gear and the motor drive gear of 0.002"
at the point of tightest engagement.
4.
Tighten the adjusting block screw and recheck clear-
ance. Wink must be present with no stress on motor shaft.
Replace the remaining parts in reverse order.
Remove T
-
Casting (Figure
5)
Prepare for removal.
1.
Remove the ribbon.
2.
Remove the ribbon drive unit.
3.
Remove the type array (cartridge assembly)
4.
Remove the wires to the T-casting.
5.
Remove the front cover.
6.
Remove the right cover.
7.
Remove the inner front cover.
Remove the movable base (or remove the read head).
Free the hinge pin.
1. Open the T-casting.
2. Remove the ribbon guide and print line indicator
from the hinge.
3. From the rear side of the T-casting, drive pins from
a.
upper eccentric bearing.
b.
lower eccentric bearing.
4. Loosen the collars on the hinge pin.
5. Remove the screw that is screwed into the hinge pin
through the horizontal hole in the upper arm of the T-cast-
ing.
6. Carefully close and lock the T-casting.
7. Loosen the set screw in the upper hinge pin bushing.
8. Loosen the set screw that locks lower eccentric bear-
ing.
Remove the T-casting.
1.
Remove the hinge pin and catch parts as they are
freed by hinge pin.
2.
Unlock the T-casting while supporting the weight of
the casting.
3.
Slide the T-casting out toward the front to clear the
translator frame.
Replace T
-
Casting (Figure
5)
Prepare to reinstall the T-casting.
1.
Insure that the hinge pin will slide through all parts.
2.
Slide the hinge pin through the upper bearing hole
in the T-casting.
3.
Thread the upper eccentric bearing on the hinge pin.
4.
Thread the lower eccentric bearing on the hinge pin.
5.
Slide the hinge pin into the lower bearing hole in the
T-casting.
Locate the eccentric bearings in the T-casting to enable,
in a later step after the T-casting has been installed, the
pinning of bearings to the hinge pin.
1. Locate the lower eccentric bearing rotationally.
a.
Rotate the bearing around the hinge pin so that
high side of the eccentric is to the right.
b.
Further rotate the bearing so that the high side of
the eccentric rotates 45° toward the rear.
c.
Work the eccentric into the lower bearing hole.
d.
Insert the taper pin (finger tight) into the bearing
and the hinge pin.
2. Locate upper eccentric bearing rotationally.
a. Rotate the upper bearing around the hinge pin
until it lines up with the upper bearing hole.
b.
Work the bearing into the upper hole.
c.
Insert the taper pin (finger tight) into the bearing
and the hinge pin.
3. Position the bearings vertically.
a.
Slide the hinge pin and bearings vertically until the
horizontal screw hole in the hinge pin is at the same
level as the center of the horizontal hole in the upper
arm of the T-casting.
b.
Insert the set screw and lock the lower eccentric
bearing to the lower arm of the T-casting.
c.
Remove the taper pins.
d.
Withdraw the hinge pin.
Prepare the translator frame for the. T-casting replace-
ment.
1.
Place the bushing in the upper arm of the translator
frame and lock the bushing as high as possible in the arm.
2.
Place thrust washer over the jackscrew in the lower
arm of the translator frame, align the hole centers, and
scotch-tape the washer to the jackscrew.
Set the T-casting into position.
1.
Gather all loose parts that fasten to the hinge pin
( including the hinge pin) and set them on the printer so
that they will be close at hand when needed.
2.
Lift the T-casting into position on the translator frame,
keeping the right end high so that the thrust washer is not
dislodged.
3.
Actuate the T-casting lock lever until the latch just
engages the latch catch.
Install the hinge pin.
1.
Slide the hinge pin through the bushing in the upper
arm of the translator frame.
2.
Slide the hinge pin through the upper eccentric bear-
ing in the upper arm of the T-casting.
3.
Thread the hinge pin through the loose parts in cor-
rect order and in correct relation to the T-casting.
4.
Slide the hinge pin into the lower eccentric bearing.
5.
Slide the hinge pin through the thrust washer into
the jackscrew.
Fasten the eccentric bearings to the hinge pin.
1.
Align the lower pin hole in the hinge pin to the pin
hole in the lower bearing.
2.
Insert the taper pin into the holes just aligned.
3.
Align the pin hole in the upper eccentric bearing to
the upper pin hole in the hinge pin.
4.
Insert the taper pin into the holes just aligned.
5.
Drive in both taper pins.
Position the hinge pin.
1.
Turn the hinge pin until the high side of the eccentrics
are to the right.
2.
Insert the screw through the hole in the upper arm
of the T-casting, and screw through the hinge pin.
3.
Free the bushing in the upper arm of the translator
frame, and force the bushing against the T-casting.
Perform these adjustments:
1.
Position the T-casting front to rear (field) .
2.
Position the T-casting vertically ( field) .
3.
Adjust the ribbon shield assembly.
Replace remaining parts in reverse order.
Position T
-
Casting (Factory)
Position the T-casting vertically (factory specification and
adjustment) .
1. The lower T-casting bushing to be located vertically
to provide 0.570" ± 0.005" between the lower surface of
REMOVALS AND ADJUSTMENTS
15
14

.,
\
Drive Gear Adjusting-.-
Screw Block
T -
Lever
\`\
Lower Ribbon Guide
Movable Base\
~,
/
.
N..
__...-
1e
T-Casting
`''
1
Ribbon Shield Bracket
i
I
,
I
I~
Hinge Pin
Friction Clamp
Eccentric Shaft
Oil Reservoir
•
Figure 5. T-Casting
the hammer unit mounting slot in the translator frame and
the top right surface of the movable base.
2. Adjust the shock block on the T-casting to obtain
this dimension measured between the lower surface of the
hammer unit mounting slot in the left side of the trans-
lator frame and the top left end of the movable base.
Position the T-casting front to rear ( factory specification
and adjustment).
1. With the print impression control lever set at C, the
face of the type is to be positioned a distance of 0.716"
±0.002" and parallel to the rear surface of the upper tractor
guide bar within 0.002". This may be accomplished by the
simultaneous adjustment of the eccentric pivot pin on the
right end of the T-casting and the gate latch bumper screw
on the left end of the translator frame.
Position T-Casting Horizontally-Field
(Figures 2 and
5)
This adjustment depends upon the hammer unit being
located correctly front to rear and the type array and
movable base being adjusted correctly on the T-casting.
If doubt exists as to the correctness of these prerequisites,
the factory adjustments must be used.
Prepare to position the T-casting horizontally.
1.
Remove the forms from the machine.
2.
Remove the ribbon shield and print line indicator at
the hinge.
3.
Remove the upper paper guide support bar.
4.
Remove the hammer cover (nose cone) .
5.
Remove the ribbon.
6.
Set the print impression control lever to C.
Check the positioning of the T-casting horizontally.
1.
Lock or hold the T-casting against the gate latch
bumper screw on the left.
2.
Check for a clearance between the face of the ham-
mers and the rear top lip of the type cartridge of 0.078"
(slight drag) .
3.
Check for this clearance both to the left and to the
right.
4.
If the clearance is correct, no adjustment is needed.
Replace the remaining parts in reverse order.
Position the T-casting horizontally.
1.
Loosen the hinge pin set screw at the lower right
end of T-casting.
2.
Turn the vertical eccentrics by turning the hinge pin
with a screwdriver to obtain the correct clearance at the
right end.
3.
Tighten the hinge pin set screw.
4.
Loosen the gate latch bumper screw lock nut.
5.
Turn the gate latch bumper screw to obtain the cor-
rect clearance at the left end. The latch position must be
adjusted correspondingly. This adjustment is accessible
from the rear of the machine ( Figure 5) .
6.
Tighten lock nut.
Replace remaining parts in reverse order.
Position T
-
Casting Vertically
-
Field (Figure
5)
This adjustment depends upon the hammer unit being
located correctly front to rear and the type array and mov-
able base being adjusted correctly on the T-casting.
Prepare to position the T-casting vertically.
1.
Use a two-part form and strip off the last copy, leav-
ing the last carbon exposed to the hammers.
2.
Set up processing unit to print one line of alternate
W's and M's.
3.
Remove the ribbon.
4.
Latch T-casting closed.
5.
Set the print impression control lever to A.
Check the vertical positioning of the T-casting.
1.
Print one line of alternate W's and M's.
2.
Open the T-casting.
3.
Remove the forms.
4.
Observe the imprint of the characters on the hammers.
5.
If the imprint is located evenly between the upper
and lower edges of the hammer faces, no further adjust-
ment is necessary. Replace the ribbon.
Adjust the vertical position of the T-casting.
1. Position the right end of the T-casting.
a.
Loosen the hinge pin bushing set screw in the
upper arm of the translator frame.
b.
Loosen the lower jackscrew lock nut on the lower
right arm of the translator frame.
c.
Turn the upper jackscrew lock nut to obtain the
vertical adjustment.
d.
Tighten the lower jackscrew lock nut.
e.
Force the hinge pin bushing down and tighten the
set screw.
2. Position the left end of the T-casting.
a.
Loosen the chock block on the T-casting to obtain
the vertical adjustment.
b.
Slide the chock block on the T-casting to obtain
the vertical adjustment.
c.
Clamp the chock block to the T-casting.
3. Position the ribbon shield and the print line indicator.
Refer to that adjustment.
4. Recheck the vertical position.
Replace ribbon.
Adjust T
-
Casting Latch (Figure
3)
Remove the interlock switch cover. Check the adjustment
of the T-casting latch.
1. Open the T-casting.
a.
Operate the interlock detent and move the lock
lever to the latched position (handle resting against
stop stud).
b.
Check that the high side of the eccentric is toward
the front and provides positive locking action (high
side 8° ±1° above the horizontal).
c.
Check that the interlock switch just makes when
the latch handle is
1
%6
"
from the latch handle stop stud.
2. Close the T-casting.
3. Check that a 2- to 6-pound force ( applied at the
center of the ball) is required to operate latch.
If the conditions just stated are met, no further adjust-
ment is necessary. Replace the interlock switch cover.
Position the eccentric shaft.
1.
Open the T-casting.
2.
Move the T-casting lock lever to the latched position
( the handle resting against the stop stud) .
3.
Loosen the clamp screw in the handle.
4.
Position the high side of the eccentric toward the
front.
5.
Further position the high side of the eccentric above
the horizontal so that the latch just provides a positive
locking action (8° ± 1° above the horizontal).
6.
Clamp the handle to the eccentric shaft.
Adjust the interlock switch.
1. Position the latch handle %
6
" from the latch handle
stop stud in latching position.
2.
Position the interlock switch actuator on the eccentric
shaft so that the interlock switch just makes.
3.
Lock the actuator to the shaft.
Position the gate latch catch (Figures 2 and 3) .
1.
Loosen the gate latch catch holding screws.
2.
Latch T-casting closed.
3.
Turn the gate latch adjusting screw ( socket head) to
draw the T-casting against the gate latch bumper screw
(hex head).
Adjust the latching force.
1.
Turn in on gate latch adjusting screw
1
6" turn.
2.
Tighten the holding screws.
3.
Latch the T-casting and observe the latching force.
4.
If the latching force is 2 to 6 pounds applied at the
center of the ball, the adjustment is correct.
5.
If the latching force is not correct, loosen the gate
latch catch holding screws and re-adjust the adjusting
screw as necessary.
6.
Tighten the holding screws.
Replace interlock switch cover.
Type Array (Cartridge Assembly)
Type Array Removal
1.
Remove the ribbon.
2.
Remove the four allen head screws which hold the
type array.
3.
A stud at the right in the type array fits into a slot
in the movable base to position the right end of the type
array front to rear.
4.
The boss on the bottom of the drive sprocket fits into
the bearing hole of the timing disk to align the left end
of the type array front to rear and left to right.
5.
Lift out the array.
Replace in reverse order. Be certain that the cartridge
seats firmly on the base. Replace the ribbon.
Type Array Disassembly
-
Out of Machine (Figure 6)
1. First, read the following steps and decide which are
necessary for the job at hand.
The platen should not be
removed from the center plate. The factory adjustment of
16
REMOVALS AND ADJUSTMENTS
17

the four eccentric screws should not be changed.
Also,
notice that for a visual inspection, steps 3, 4 and 5 are not
necessary. The steps are given so that a complete procedure
will be available, if it is needed.
2. Prepare to disassemble the type array.
a.
Remove the ribbon guide bar.
b.
Loosen the three drive sprocket stud-holding
screws.
c.
Place the array upside down on a flat surface with
the drive sprocket to the left.
d.
Remove the six screws that hold the lower plate
to the center plate.
CAUTION: Do not disturb the adjustment of the ec-
centric adjusting screws.
e.
Carefully remove the lower plate.
3. Chain removal procedures: Exercise extreme caution
to
never
bend the chain in a smaller radius than the normal
idler pulley radius. Failure to observe this causes the chain
to kink or, possibly, to break.
a.
Remove the screw and washer in the drive sprocket
stud.
b.
Remove the screws that hold the drive sprocket
stud without turning the assembly over. This can be
done by moving the assembly over the edge of the
bench (table, etc.) far enough to get at the screws.
c.
Support the drive sprocket and chain, and remove
the drive sprocket stud without turning the assembly
over.
d.
Free the chain from the idler pulley end first by
lifting the chain up and off the idler pulley. Carefully
drape this end of the chain across the center of the
idler pulley
being extremely careful not to kink the
chain by causing it to bend in too small a radius.
e.
At this point the chain is still engaged with the
drive sprocket. Grasp chain carefully both front and
rear and slide it to the left so as to free it from the
drive sprocket. Do not use force.
Be careful not to
kink the chain.
f.
Remove the chain from the center plate and the
drive sprocket from the idler pulley end. Be careful
not to kink the chain.
g.
Carefully place the chain in a bath of IBM 6 oil
until it is ready for re-assembly.
The receptacle for the
oil bath must be large enough to accept the chain
without causing damage due to kinking.
4. Do not remove the platen from the center plate. This
assembly is bonded and ground for alignment and clearance
of the platen to the lips of the upper and lower plates.
5. Check the condition of the bond. If the bond is un-
satisfactory (resulting in a tight chain) , the cartridge
should be replaced.
6. Idler pulley removal: To replace the idler pulley or
lubricator,
a.
Turn the array over and rest it on the center plate.
b.
Remove the screw that holds the idler pulley stud.
c.
Remove the six screws that hold the upper plate
to the center plate.
CAUTION: Do not disturb the adjustment of the ec-
centric adjusting screws.
d.
Turn the unit over so that the center plate is up.
e.
Lift the center plate and separate it from the upper
plate far enough to permit removal of the idler pulley
and stud without damaging the platen or lubricator
spring.
7. Carry out chain cleaning procedure prior to reassem-
bly of type array.
Center and Upper Plate Reassembly —
Flat Idler Spring (Figure
6)
Assemble the center and upper plates.
1. Remove the type idler from the type idler stud.
2. Install the type idler stud to the upper plate.
a.
Place the upper plate upside down on a flat surface.
b.
Insert the type idler stud into its recess on the
upper plate.
c.
Insure that the stud is free of binds and that the
spring returns the stud to the right.
d.
Lift the upper plate and fasten the stud to it.
3. Install the center plate and the type idler to the
upper plate.
a.
Place the upper plate upside down on a flat surface.
b.
Place the type idler in the correct relationship to
the center plate.
c.
Work the center plate and the type idler into
position against the upper plate.
d.
Fasten the type idler to the type idler stud.
e.
Lift the upper plate and insert the upper plate
holding screws.
f.
While holding the upper plate against the eccentric
adjusting screws (pushing the lip on the plate
away
from
the platen), tighten the upper plate holding
screws. The contact between the plate and the two
eccentrics
must
be on the surface of the eccentric
away from
the print line side of the cartridge.
Center
and Upper Plate Reassembly—
Coil Idler Spring (Figure 6)
Assemble the center and upper plates.
1.
Place the upper plate upside down on a flat surface.
2.
Place the type idler with the stud and compression
spring in correct relationship with the center plate.
3.
Insure that the idler assembly is free to slide in its
slot in the upper plate.
4.
Lift the type array; insert the upper plate holding
screws, and screw in until they are snug.
Chain to Type Array Reassembly (Figure 6)
1. Clean chain prior to re-installation in the array.
Use
no solvents.
a.
Soak the chain in a bath of IBM 6 oil while it is out
of the array. Allow the chain to lie horizontally. Do
not hang it vertically because of the danger of kinking.
or trapping foreign material between the type slugs.
The receptacle for the oil
must be large enough to ac-
cept the chain without causing damage by kinking.
b.
Lay the chain on a flat surface for cleaning ink and
ribbon waste from the type with a brush.. Brush the
chain as it is held straight,
not where it is curved and
the type slugs are open
as this is apt tö force dirt
between the "butts" of the type slugs. Use a stiff
brush such as an IBM typewriter brush. Use a sweep-
ing motion,,
do not jab or dig with the brush.
c.
Place the chain in a clean IBM 6 oil bath, and work
the chain in the oil for several minutes.
d.
Repeat steps b and c until the chain looks clean.
( Foreign material in between slugs will break a chain.
Also, kinking the chain between slugs will break it.)
e.
Place the chain on a pad of paper towels to drain
for 15 minutes before it is reassembled in the type
array.
2. Prepare to reassemble the chain to the type array.
a. Loosen the holding screw for the type idler stud,
move the type idler to the left against the spring
tension, and snug the holding screw to hold the type
idler in this position.
b.
Place the upper plate upside down on a flat surface
with the type idler to the right.
c.
Adjust the lubricator so that
(1) it does not touch the side of the type idler.
(2 ) it extends J 2' beyond the periphery of the
type idler.
d.
Place the drive sprocket in the center plate with
(1) the slot aligned left to right.
(2) the slot positioned toward the front so that it
lies between the platen ( at the front ) and the bearing
of the drive sprocket ( at the center) .
3. Reassemble the chain to the type array.
a.
Carefully pick up the chain so that it does not kink.
b.
Align the 9 with the filled slot stamped 9 in the
drive sprocket. The 9 is on the "9 0" type slug.
c.
Slide the drive sprocket I/4" to the left keeping the
9 aligned with the slot.
d.
Taking care to maintain timing, pick chain up
front and back and slide to right.
Do not stress chain
or use force in any way.
e.
Opposite end may now be placed over the idler
pulley.
4. Because the upper plate is upside down,
insure that
the chain is upside down.
5. The type slugs are now on top of the lip of the upper
plate. The chain must be aligned flat against the platen so
that slugs will slip into position between the platen and lip.
a.
Stroke the body of the slugs along the length of
the type array just above the lip and below the type
face.
b.
Do not use force.
Difficulty in getting slugs to slip
between the platen and the lip of the upper plate may
be an indication of a kinked chain or loose platen.
6. Fasten the type drive sprocket to the upper plate
without turning the assembly over.
a.
Move the assembly over the edge of the bench
( table, etc.) far enough to insert the drive sprocket
stud; insert the stud.
b.
Insert and tighten the screw that holds the drive
sprocket to the stud.
c.
Insert and tighten the drive sprocket stud holding
screws.
7. Check the chain for freedom and alignment.
a.
Insure that the chain rotates freely without binds.
b.
Insure that the "9" is aligned with the slot in the
drive sprocket.
c.
Insure that the chain is installed correctly.
8. Loosen the holding screw for the type idler stud to
permit the spring tension to help hold the chain in position.
Lower Plate to Type Array Assembly (Figure 6)
1. Reassemble the lower plate.
a.
Place the type array upside down on a flat surface
with the drive sprocket to the left.
b.
Carefully work the lower plate into position on
the center plate, insuring that the lip on the lower
plate slides over the chain.
c.
Insure that the chain is under the lip of the lower
plate.
d.
Insert the six holding screws.
e.
Stand the cartridge up on the upper and lower
plates so that the print side of the cartridge is up.
f.
Loosen the six holding screws in each plate (upper
and lower) to permit the weight of the center plate
and chain to position the center plate. The bottoms of
the eccentric dowels ( side away from the platen) are
resting on the holes in the upper and lower plates.
g.
Tighten all holding screws.
2.
Position the type idler.
a.
Loosen the holding screw for the type idler stud
to free the idler. Be certain the idler can move with
the spring tension.
CAUTION: Block can be misaligned if loosened too
much.
b.
Lift the sprocket end of the type array and stand
the type array on the right end of a .30° angle (type
idler down) .
c.
Using your right thumb and middle finger, place
your thumb on one side of the chain, your finger on
the other. Work slack into the chain down from the
drive sprocket end of the chain to the type idler end of
the chain. Do this approximately four times.
d.
Tighten the holding screw in the type idler stud to
the upper plate. Insure that the stud is not inad-
vertently knocked out of its slot in the upper plate.
e.
Check the position of the type idler stud by hold-
ing the type array so that the chain will hang down
from between the upper and lower plates. Rotate
the chain approximately 2" right and left a few times
to insure that the chain will assume a natural drape
down from the center plate. At the center of the type
array, one half of the body of the type slug should
be visible below the edge of the upper and lower
plates.
3. Again check the chain for freedom and alignment.
a.
Insure that the chain rotates freely without binds
by spinning the chain rapidly by hand in the normal
direction of rotation. It should "coast" slightly after
the finger is removed.
b.
Some spots of drag may be felt when the chain
is turned very slowly. This does not necessarily indi-
cate a bind as long as it meets the requirement of
step a.
c.
Insure that the 9 is aligned with the slot in the
drive sprocket.
d.
Insure that the chain is installed correctly.
4. Check the chain for freedom and clearance.
a.
The chain must move freely ( with 400 to 600
gram force).
CAUTION: Do not use gram gage.
b.
Clearance between the lips on the upper and lower
plates and type slugs must not exceed 0.003". Shadow
printing results from this.
5. If the conditions of step 4 are not met,
a.
Do not disturb the factory adjustment of the eccen-
tric adjusting screws.
b.
Check the re-assembly procedure.
(1) Is the type idler stud positioned to give proper
tension on the chain?
( 2 ) Is the chain correctly positioned beneath the
lips of the upper and lower plates?
(3) Was the chain properly cleaned with foreign
material removed from between the type slugs?
( 4 ) Are the upper and lower plates correctly posi-
tioned against the four eccentric adjusting screws?
( 5) Was the chain lubricator (by the type idler)
correctly positioned?
Q
REMOVALS AND ADJUSTMENTS
19.
18

Lower Plate
0
Idler Stud
-4-Drive Sprocket Stud
~
i
6
Ribbon Guide Bar
Upper Plate
Eccentric Adjusting Screws
N,
Drive Sprocket
Lubricator
~
Platen
Center Plate
Type Idler
Type Slugs
Figure 6. Type Array ( Cartridge Assembly)
6. The factory adjustment of the eccentric adjusting
screws for the upper and lower plates (two for each plate)
should be changed
only in an emergency.
This adjustment
sets the clearance between the platen (or the type slugs)
and the lips of the upper and lower plates. This also adjusts
the relationship between the drive sprocket and the path
of the chain past the platen. The chain must travel in a
path that is tangent to the drive sprocket where the chain
leaves the sprocket. In an emergency situation an attempt
to make this adjustment can be made by adjusting the
plates as close to the chain as possible with no binding of
the chain. It should move freely with 400 to 600 gram force.
Do not use gram gage.
7. Replace the ribbon guide bar.
Adjust Magnetic Read Head (Figure 3)
1. Remove the ribbon and type array.
2. Check the adjustment of the magnetic read head.
a. The read head must be positioned
to
obtain a
clearance to the periphery of the magnetic timing
disk of 0.003" to 0.001".
(1)
Do not use a feeler gage between the read
head and timing disk. The feeler gage, may be shaved,
and these shavings will form a flux bypass at the slots.
(2)
Use a sheet of paper (carriage tape is good)
to determine the high spots by inserting paper between
the read head and the timing disk and rotating disk.
(3)
Remove the paper.
b. At a timing speed of 750 rpm, minimum read head
output voltage must be 100 millivolts peak to peak.
3. If the conditions stated in step 2 are met, no further
adjustment is necessary. Proceed to step 5.
4. If the conditions stated in step 2 are not met, do
one or more of the following:
a.
check for cold solder joints at amplifier wire wrap.
b.
magnetize the timing disk.
c.
replace the read head.
d.
replace the read head and magnetize timing disk.
5. Replace the remaining parts in reverse order.
Magnetize Timing Disk
1. Remove the 1403 cover on the right side.
2.
Check that the connections to the amplifiers do not
have cold solder connection at the wire wrap.
3. Use an edge connector insert that has a 2-watt 300-
ohm resistor connected between pins Q and B, and has pin
D jumpered to pin J.
4. Magnetize the timing disk.
a.
Remove amplifier one.
b.
Remove amplifier two.
c.
Insert the altered edge connector into amplifier one
receptacle.
d.
Turn on the system power.
e.
Run the timing disk for a few revolutions.
f.
Turn off the system power.
g.
Remove the edge connector.
h.
Replace the amplifiers.
5. Check the output and rise time of the head signal.
6. If the rise time is slow, repeat step 4 but use an
altered edge connector that has the 300-ohm resistor con-
nected between pins Q and D and has pin B jumpered to
pin J. This is necessary because of a reverse charge on the
drum.
7. Check the output and rise time of the head signal.
8. Replace the cover on the right side.
Hammer Unit
Hammer Unit Removal (Figure 7)
1.
First, glance through the following steps and decide
which are necessary for the job at hand.
2.
Prepare for removal.
a.
Remove the forms.
b.
Remove the top forms guide.
c.
Remove the service mounts from the inside of the
left front cover.
d.
Slide the rear forms stacker down out of the way.
e.
Open the rear door and remove the inside rear
cover.
f.
Remove the air hose and place out of way.
g.
Loosen the service mount holding screws on the
translator frame.
h.
Install the service mount and tighten the screws.
i.
Remove the hammer unit holding screws.
3. Slide the hammer unit out on the service mount.
4. Disconnect the hammer unit from the printer.
a.
Remove the rear cover from the unit.
b.
Tilt the hammer unit up and remove the upper and
lower covers over the magnets.
c.
Separate quick disconnect electrical connections.
d.
Tilt the hammer unit to the normal position and
remove the cable brackets with the cables attached.
5. Remove the hammer unit from the service mount.
a.
Tilt the hammer unit up ( hammers up) .
b.
Remove the clips on the service mount hand screws.
c.
Remove the hand screws.
d.
Place your forearms with palms of hands up under
hammer unit.
e.
Carefully lift the hammer unit with both arms until
the hammer unit is free of the service mount.
f.
Tilt the unit toward you so that it cannot fall.
g.
Withdraw the unit clear of the machine.
h.
Place the unit on a flat surface.
6. Carefully re-install the hammer unit in reverse order.
CAUTION: Do not let the unit drop. Insure that the mag-
net leads do not bind or interfere with magnet armatures
when the covers are installed.
Position the Hammer Unit
-
Factory
1. Position the hammer unit front to rear ( factory speci-
fication and adjustment).
a.
The positioning of this unit is to be made with the
T-casting locked in place and the print impression
control lever set at C.
b.
The hammer unit is to be positioned in the trans-
lator frame so that the front surface at both ends of
the hammer unit casting ( at print level) are located a
distance of 1.3715" ±0.0015" from the face of the
type characters.
. %•::,
c.
Any single-type slug as measured at the ends of the
type array must be parallel to the front surface of the
hammer unit frames within 0.001".
Position the Hammer Unit
-
Field (Figure 7)
1. This adjustment depends upon the T-casting being
located correctly front to rear and the type array and
movable base being adjusted correctly on the T-casting.
If doubt exists as to the correctness of these prerequisites,
the factory adjustments must be used.
2. Prepare to position the hammer unit horizontally.
a.
Remove the forms from the machine.
b.
Remove the ribbon shield and print line indicator.
c.
Remove the upper paper guide support bar.
d.
Remove the hammer cover (nose cone) .
e.
Remove the ribbon.
f.
Set the print impression control lever to C.
3. Check the positioning of the hammer unit horizontally.
a.
Lock the T-casting against the gate latch bumper
screw on the left.
b.
Check for clearance of 0.078" between the hammer
face and cartridge lip or 0.083" between the hammer
and the type face.
c.
Check for this clearance both to the left and to the
right.
4. If the conditions of step 3 are met, no further adjust-
ment is necessary. Proceed to step 6.
20
REMOVALS AND ADJUSTMENTS
21
~

Figure 7. Hammer Unit
~>
5. Position the hammer unit horizontally.
a.
Loosen the hammer unit mounting screws (2 allen
head screws) .
b.
Hold the hammer unit bushing stop (2) .
c.
Loosen the bushing stop lock nut (2).
d.
Turn the hammer unit bushing stop in the direc-
tion of desired adjustment.
e.
Tighten the bushing stop lock nut.
f.
Tighten the hammer unit mounting screws.
g.
Recheck the hammer unit position.
Hammer Magnet Assembly Removal
1. Prepare to remove hammer magnet.
a.
Slide the hammer unit onto the service mount.
( See
Hammer Unit Removal)
b.
Remove the cover over the hammer magnets.
c.
Remove quick disconnect that goes to the hammer
magnets.
d.
Remove the hammer mounting bar assembly.
2. Remove the hammer unit magnet assembly.
a.
Remove the magnet lead from quick disconnect
fitting, using special removal tool P/N 461043.
b.
Remove the holding screws for the hammer mag-
net assembly.
c.
Lift the assembly from the mounting.
3. Replace the hammer magnet assembly.
a.
Place the assembly into the mounting.
b.
Insert the mounting screws and screw to fit snug.
c.
Insert the eccentric adjusting tool and position for
approximately the same air gap between the arma-
ture and the core at the coil end as other assemblies.
d.
Tighten the mounting screws.
e.
Insert the magnet leads into the quick disconnect
plug.
4. Replace the remaining parts in reverse order.
5. Print and adjust hammer flight time as necessary.
Individual Hammer Magnet Coil Replacement
Only the upper hammer magnet coils may be replaced
without removing the individual hammer magnet assembly
from the hammer casting frame. By "upper" and "lower"
is meant the configuration of the coil of the hammer magnet
assembly, not the location on the hammer casting frame.
To attain access to either upper or lower hammer magnet
assembly and to remove a lower hammer magnet assembly
for coil replacement, refer to
Hammer Magnet Assembly
Removal.
The upper hammer magnet assembly is P/N
474061 (qty. 50 or 66) and the lower is P/N 474060 (qty.
50 or 66). The individual coil for both is P/N 474051 (qty.
100 or 132).
1.
After determining that the coil is defective, remove
old coil by
prying, cutting
or driving it off the core using
care not to
disturb
or damage the yoke itself.
2.
Completely remove old adhesive remaining on core
using ism cleaning fluid, p/rr 450608.
Do not put cleaner on
nylon residual.
3.
Coat the four side surfaces of the core with 3M
(EC 232 or 826) cement P/N 261096 using care not to
allow any adhesive to touch top face of core. Do not use
excessive amount.
4.
Allow a minimum of two minutes for cement to set.
5.
Place on new coil, pressing it to the bottom of the
yoke.
6.
Allow 15 to 20 minutes for the adhesive to dry.
( Exposure to moderate heat will lessen drying time.)
Hammer Removal
1. Prepare for removal.
a.
Open the T-casting.
b.
Open the upper and lower forms guide support
bars.
c.
Remove the forms and move the tractors apart to
their extreme limits.
d.
Remove the binary paper guides from the tractor
guide bars.
e.
Remove the hammer cover.
f.
Remove
holding screws for the print impression
control
bar.
g.
Slide the print impression control bar with the
hammers and hammer mounting bar attached from
the hammer unit. Do not handle the hammer springs.
h.
Place the assembly on a flat surface.
2. Remove the hammer.
a.
Remove the dowel screws that hold the impression
control bar to the hammer mounting bar.
b.
Carefully slide the print impression control bar
out from inside the hammer assemblies.
c.
Lift the hammer mounting bar and remove the
hammer holding
screw.
d.
Lift out the hammer by gripping the base. Do not
bend or scratch the springs.
3. Re-install in reverse order. Install the square inner
surface of the hammer to the rear. Keep the rubber of the
print impression control bar to the rear. Do not damage
the hammers when inserting the print impression control
bar. Visually inspect the hammer installed. Spacing be-
tween adjacent hammers should be 0.014" to 0.022".
4. Replace the remaining parts in reverse order.
5. Check the printing. If the spacing between the adja-
cent printed characters is different, it will be necessary to
adjust the hammer magnet armature air
gap.
Ribbon Unit
Ribbon Drive Unit Removal
1. Prepare for removal.
a.
Remove the ribbon.
b.
Remove the cover over the ribbon and drive.
c.
Remove
the wires to the ribbon drive unit.
2. Remove the ribbon drive unit.
a.
Loosen
the two
screws
on the right in the upper
ribbon casting mounting gib.
b.
Remove the three screws on the left in the gib.
c.
Slide the drive unit to the left and raise it to clear
the lower mounting bar.
d.
Lower the drive unit to clear the upper gib.
3. Reassemble in reverse order, and position the unit
during reassembly.
Position Ribbon Drive Unit
1. Locate the sense finger.
a.
Engage the shift lever in the right stop position.
b.
Loosen the screws in the lower support bar.
c.
Position the left edge of the sense finger a maxi-
mum of 14
4
V
4
" ±
%i
"
from the left upper base of the
T-casting on which is mounted the ribbon spool-
center.
d.
Insure that the drive unit is as far to the right
as
possible in its locating slot when doing step
c.
e.
Tighten the screws in the lower support bar.
22
REMOVALS AND ADJUSTMENTS
23

~
2. Provide freedom of movement.
a.
Loosen the screws in the upper ribbon casting
mounting gib.
b.
Position the gib for a minimum clearance (0.003")
to the ribbon casting without binding the casting as
the unit is moved throughout its lateral range.
c.
Tighten the screws in the gib.
Adjust Ribbon Skew
1. First insure that the ribbon drive unit
a.
is adjusted correctly.
b.
is located correctly.
2. To adjust for the ribbon to skew to the left when
slightly unwinding from the upper spool, loosen the nut
on the left hand ribbon spool center and push the shaft to
the rear.
3. Adjust the angle of the correction roller on the cor-
rection arm (if adjustable) so that the ribbon
a.
corrects to the right.
b.
winds onto the upper spool with the best right
edge alignment.
4. The eccentric in the ribbon skew wheel should be
adjusted to assure clearance between the wheel and the
ribbon when the skew lever is in the latched position.
Adjust Ribbon Shield and Print Line Indicator
1. Prepare to adjust ribbon shield assembly.
a.
Open the T-casting.
b.
Remove the ribbon.
c.
Set the print impression control lever to E.
2. Check the adjustment of the ribbon shield and print
line indicator for the following:
a.
that the key on the ribbon shield bracket enters
freely into the slot in the right end of the movable
base.
b.
that the left end of the ribbon shield bracket
enters freely into the slot in the left end of the
movable base.
c.
that the ribbon shield is parallel to the top surface
of the movable base within 0.005".
d.
that the inner surface of the ribbon shield is within
0.005" to 0.008" of the lower cartridge ribbon guide
at both ends.
e.
that the double-headed screw has a clearance be-
tween the rear side of the inner head and front of the
ribbon shield extension of 0.004" to 0.006".
f.
that when the T-casting is being closed, the key
slot on the left end of the ribbon shield permits free
entry of the key on the translator frame.
3. If the conditions as stated in step 2 are met, no
further adjustment is necessary. Proceed to step 9.
4. Position the ribbon shield bracket.
a.
Loosen the collars on the T-casting hinge pin.
b.
Position the ribbon shield bracket so that the key
on the ribbon shield bracket enters freely into the slot
in the right end movable base.
c.
Tighten the collars on the T-casting hinge pin.
5. Position ribbon shield vertically.
a.
Loosen the screws in the ribbon shield support.
b.
Position the ribbon shield so that the key on the
left end of the ribbon shield enters freely into the
slot in the left end of the movable base.
c.
Tighten the screws in the ribbon shield support.
6. Position the ribbon shield horizontally for a clear-
ance of 0.005" to 0.008" to the cartridge lower ribbon
guide.
a.
Turn the two set screws in the ribbon shield
bracket at the right end of the movable base.
b.
Turn the set screw in the key slot at the left end
of the movable base.
7. Position the double-headed screw,
a. with the ribbon shield set as in step 6.
b. for a clearance between the rear side of the inner
head and the front face of the ribbon shield extension.
(1)
at the right end of the movable base.
(2)
of 0.004" to 0.006".
(3)
by turning the screw.
c. Lock the screw in place.
8. Position the key slot on the left end of ribbon shield.
a.
Loosen the key slot block mounting screws.
b.
Position the ribbon shield in the movable base.
c.
Lift the key slot block with the left middle finger,
keeping the thumb on the type array and reaching
around the left end of the T-casting.
d.
Carefully close the T-casting while aligning the
slot block to the key.
e.
Lock the T-casting closed.
f.
Tighten the upper slot block mounting screw.
g.
Open the T-casting.
h.
Tighten the lower slot block mounting screw.
9. Replace the ribbon.
Lower Ribbon and Brake Assembly Removal
(Figure 8)
1.
Remove the cover over the ribbon assembly.
2.
Remove the ribbon.
3.
Remove the cover over the lower ribbon drive.
4.
Move the ribbon drive unit to the left.
5.
Remove the retaining clip from the ribbon spindle
shaft.
6.
Remove the ribbon spindle shaft.
CAUTION:
Do not
lose the key.
7.
Remove the retaining clip from the drive gear shaft.
8.
Remove the ribbon drive and brake assembly.
9.
Re-assemble in reverse order.
a.
Be certain the key is in the ribbon spindle shaft.
b.
As the ribbon drive and brake assembly is installed,
the reverse drag pawl must be lifted to engage the
reverse drag friction ring.
c.
Check the reverse drag pawl by turning the
spindle. The upper pawl should ratchet when the
upper spindle is turned in a counterclockwise direc-
tion when viewed from the spindle end. The lower
pawl should ratchet when the lower spindle is turned
in a clockwise direction when viewed from the
spindle end.
Upper Ribbon Drive and Brake Assembly Removal
(Figure 8)
1.
Remove the cover over the ribbon assembly.
2.
Remove the ribbon.
3.
Remove the ribbon motor drive gear cover.
4.
Remove the sense arm spring.
5.
Remove the retaining clip to free the sense arm.
6.
Remove the sense arm assembly.
7.
Remove the cover over the upper ribbon drive.
8.
Move the ribbon drive unit to the left.
CAUTION:
Nylon friction disk will probably drop as the
cover and spider spring assembly are removed. Remove the
disk.
9.
Remove the retaining clip from the ribbon spindle
shaft.
10.
Remove the ribbon spindle shaft.
CAUTION:
Do not
lose the key.
11.
Remove the horseshoe clip from the drive gear shaft.
12.
Remove the ribbon drive and brake assembly.
13.
Re-assemble in reverse order.
a.
Be certain the key is in the ribbon spindle shaft.
b.
As the ribbon drive and brake assembly is installed,
the reverse drag pawl must be lifted to engage the
reverse drag friction ring.
c.
As the upper ribbon drive cover is installed, the
nylon friction disk must be held in position and the
spider spring must engage it properly.
d.
Check the reverse drag pawl by turning the
spindle. The upper pawl should ratchet when the
upper spindle is turned in a counterclockwise direc-
tion when viewed from the spindle end. The lower
pawl should ratchet when the lower spindle is turned
in a clockwise direction when viewed from the
spindle end.
Disassemble Ribbon Drive and Brake Assembly
(Figure
8)
1.
After the removal of the drive and brake assembly,
stand the assembly up with the compression plate on top.
2.
While holding the compression plates against spring
tension, remove three horseshoe clips.
3.
Remove the upper compression plate, taking care not
to lose six compression springs which are now free.
4.
Remove the six springs.
5.
Remove the lower compression plate.
6.
Remove the friction ring.
CAUTION:
Note the direc-
tion of the teeth on the friction ring. The teeth on the
upper drive friction ring are opposite to the teeth on the
lower drive friction ring. Therefore, these rings can be
incorrectly assembled.
7.
The friction surfaces of the friction ring, spool driver,
and lower compression plate should be clean and free
from oil.
8.
Re-assemble in reverse order.
a.
Insure that none of the six compression springs are
lost.
b.
Be certain that the friction ring is not installed
backwards. After the assembly is in the machine, the
upper pawl should ratchet when the upper spindle is
turned in a counterclockwise direction when viewed
from the spindle end. The lower pawl should ratchet
when the lower spindle is turned in a clockwise direc-
tion when viewed from the spindle end.
Ribbon Clutch Adjustment - Out of Machine
(Figure 8)
1. Prepare to adjust the ribbon clutch.
a.
Remove the cover and the ribbon assembly.
b.
Remove the ribbon.
c.
Move the ribbon drive unit to the left.
d.
Remove the cover over the left side of the lower
ribbon drive.
2. Remove the lower ribbon drive (not necessary for
clutch removal) .
a.
Remove the horseshoe clip on the lower ribbon
drive assembly.
b.
Remove the lower ribbon drive.
3. Free the ribbon clutch.
a. Remove the horseshoe clip on the ribbon clutch
shaft.
b.
Remove the screws in the clutch magnet housing.
c.
Remove the clutch magnet housing.
4. Remove the ribbon clutch.
a.
Hold the clutch shaft drive gear in the left hand to
prevent it from falling.
b.
Remove the ribbon clutch toward the right.
5. Check the adjustment of the ribbon clutch for
a.
a clearance between the pinion and the shoulder
on the clutch shaft of 0.001" to 0.004".
NOTE:
Step
5a applies to both tooth-style and friction clutches.
Steps 5b through 8 apply to tooth-style clutches only.
b.
a clearance between the clutch armature and the
clutch drive ring of 0.028" to 0.032" when serrations
in the armature are mated with the serrations in the
cylindrical assembly.
c.
a minimum clearance between serrations on the
armature and on the cylindrical assembly of 0.003"
when the armature is seated against the drive ring.
6. If conditions stated in step 5 are met, no further ad-
justment is necessary. Proceed to step 9.
7. Position the cylindrical assembly.
a.
Seat the ribbon clutch output pinion against the
cylindrical assembly.
b.
Position the cylindrical assembly for a clearance
between the pinion and the shoulder on the clutch
shaft of 0.001" to 0.004".
c.
Lock the cylindrical assembly to the shaft.
8. Adjust the clutch drive gear assembly for correct en-
gagement ( Figure 8) .
a.
Seat the pinion against the cylindrical assembly.
b.
Push the armature to engage the serrations.
c.
Position the clutch armature drive ring for a clear-
ance to the armature of 0.028" to 0.032". A double set
of screws (four, two in each hole) hold the ring.
d.
Tighten the setscrews in the armature ring.
e.
Seat the armature against the drive ring.
f.
If a clearance between the serrations of the arma-
ture and the cylindrical assembly of 0.003" minimum
does not exist, repeat adjustments from step c.
9. Replace the clutch shaft assembly in the machine,
taking care that the small key stays in the shaft and that
the shaft goes through the output pinion inside the drive
housing. The clutch pinion and the output pinion must en-
gage their gear trains as this reassembly is done. (A light
pin-punch mark in the side of the key will help keep it in
place if it is loose. )
10. Replace the clutch magnet.
11. Replace the horseshoe clip on the clutch shaft.
12. Check the clutch operation under power by manually
operating the reversing arm.
Ribbon Drive Motor Positioning (Figure 8)
1. Position the motor gear.
a.
Loosen the clamp screws.
b.
Position the gear so that the correction lever arm
and the sense finger arm are operated by the roller on
the gear and so that gear meshes with both clutch
shaft drive gears (0.040" between the motor bushing
and the motor gear) .
c.
Tighten the clamp screws.
2. Position the motor.
a.
Loosen the motor holding screws.
b.
Position the motor to provide a wink of 0.001" to
0.005" between the motor drive gear and the clutch
shaft drive gears at a point of tightest engagement.
24
REMOVALS AND ADJUSTMENTS
25

00
0
0
~~j
~
v
~
%
i
;
•%v
~
isi
i
~~
~
/~
v~
'
i
~
v
,
w
~~.
Figure 8. Ribbon Drive Unit
~
~
Hydraulic Unit
Blower
Figure 9. Hydraulic Unit
Hydraulic Unit
Hydraulic Unit Removal (Figure
9)
1. Remove the 1403 covers.
a.
Remove the front cover.
b.
Remove the rear cover.
c.
Remove the top cover.
d.
Remove the right cover.
e.
Remove the front inner cover.
2. Clear the rear forms stacker area.
a.
Slide the rear forms guide down.
b.
Unfasten the negator spring from the rear forms
guide.
c.
Slide the negator spring all the way up.
3. Remove the gear guards.
a.
Remove the guard over the emitter.
b.
Remove the guard over the hydraulic drive belt.
c.
Remove the guard over the stacker gears.
4. Remove the emitter.
a.
Move the translator frame to the left.
b.
Loosen the set screws that can be reached in the
emitter collar.
c.
Pull down sharply on the hydraulic unit drive belt
to turn the emitter.
d.
Loosen the remaining set screws in the emitter.
e.
Remove the emitter collar.
f.
Remove the emitter.
5. Remove the emitter brush block arm.
a.
Remove the arm spring.
b.
Remove the holding screw.
c.
Remove the retainer screw, retainer spring, and
spring block.
d.
Remove the emitter brush block arm.
e.
Remove the emitter brush block arm pivot collar.
6. Prepare to remove hydraulic unit.
a.
Remove the sense amplifier mounting plate.
b.
Remove the blower.
c.
Drain the oil from the reservoir.
d.
Remove the carriage tape tension idler mounting
plate.
e.
Remove the screws from the rear heat sink resistor
panel.
26
REMOVALS AND
ADJUSTMENTS
27

Space Pump
Skip Pump
\\\
~
r.7
r
,I
~
/ ~~\~
\~
~fI /
Needle Valves
Channel Plates
Check Valve
Hydraulic Motor)
Detent
Filter
Control Valve Assembly
7. Free the hydraulic drive unit.
a. Remove the electrical connections.
(1)
Remove the top cover on the reservoir.
(2)
Unplug the wires within the unit.
(3)
Remove the two screws in the plug on the left
of the unit.
(4 ) Remove the wires from the unit.
(5) Replace the cover over the opening in the top
of the reservoir, and replace two screws to hold the
cover.
b. Remove the drive belt.
(1)
Loosen the electric motor mounting screws.
(2)
Lift the motor enough to free the drive belt.
(3)
Clamp the motor at this position so that it may
be used for support later.
(4)
Remove the drive belt.
c. Remove three holding screws nearest the front
( total of 4 ) for the hydraulic unit (in the reservoir
mounting plate fastened to the printer casting) .
(1)
Remove the front holding screw.
(2)
Remove the center lower holding screw.
(3)
Remove the center upper holding screw.
8. Consider the problem of removing the hydraulic unit.
The unit is now being held by the rear mounting screw
and the boss around the output shaft. Care must be used
not to damage this shaft as the unit is removed. If possible,
it is recommended that two men remove this unit. The unit
must be withdrawn straight out to the right until the out-
put shaft is clear. The electric motor can be used as a rest
while supporting the unit.
9. Remove the hydraulic unit.
a.
Support the unit.
b.
Remove the rear mounting screw.
c.
Remove the unit straight out.
Hydraulic Unit Replacement
1.
Use the utmost care in replacing this unit.
2.
Follow the removal steps in the reverse order.
3.
Do not fill the hydraulic unit with used fluid.
Fill it
with one gallon of new fluid (P/N 477567) which will pro-
vide the proper level (approximately to the bottom of the
coils) . Insure that the fluid drain is closed before filling.
4.
Make any adjustments that are reflected by the work
done inside the unit, and always include these:
a.
the emitter brush.
b.
the tape brushes dynamically.
Hydraulic Unit Reservoir Removal (Figure
9)
1. Remove the 1403 covers.
a.
Remove the front cover.
b.
Remove the rear cover.
c.
Remove the top cover.
d.
Remove the right cover.
e.
Remove the front inner cover.
2. Determine whether the reservoir mounting plate
(fastened to printer casting) has the reservoir fastened
to it from the left or from the right.
3. If the reservoir is fastened from the left,
a.
remove the hydraulic unit ( See
Hydraulic Unit Re-
moval).
b.
proceed to step 5.
4. If the reservoir is fastened from the right,
a.
drain the oil from the reservoir.
b.
remove the sense amplifier mounting plate.
c.
remove the blower.
d.
remove the carriage tape idler mounting plate.
e.
remove the screws from the rear heat sink resistor
panel.
5.
Remove the reservoir. Sixteen screws hold it in place.
6.
Replace in a similar manner, but in reverse order.
7.
Replace the remaining parts in reverse order.
Remove Control Valve Assembly (Figure 10)
1. Remove the 1403 covers.
a.
Remove the front cover.
b.
Remove the rear cover.
c.
Remove the top cover.
d.
Remove the right cover.
e.
Remove front inner cover.
2. Determine whether the reservoir mounting plate fas-
tened to the printer casting has the reservoir fastened to it
from the left or from the right.
3. If the reservoir is fastened from the left,
a.
Remove the hydraulic unit.
(See
Hydraulic Unit
Removal.)
b.
Remove the reservoir. Eight screws hold it in place.
c.
Remove the valve body assembly. Four screws hold
it in position.
d.
Proceed to step 10 of reassembly.
4. If the reservoir is fastened from the right, prepare to
remove the reservoir.
a.
Drain the oil from the reservoir.
b.
Remove the sense amplifier mounting plate.
c.
Remove the blower.
d.
Remove the carriage tape idler.
e.
Remove the screws from the rear heat sink resistor
panel reservoir.
5. Remove the reservoir. Sixteen screws hold it in place.
They are all accessible from the right.
6. Remove the wires from the terminal strip for the con-
trol magnets.
7. Remove the valve body assembly. Four screws hold
it in place.
8. Replace in a similar manner but in reverse order.
9. Replace the remaining parts in reverse order.
Hydraulic Unit Reassembly (Figure 10)
1.
The channel plate assembly should never be separated
from
the reservoir mounting plate (P/N 444320), unless a
pump or motor is replaced.
2.
Any time the hydraulic unit is disassembled where
the channel plate assembly is separated from the reservoir
mounting plate (P/N 444320), it is essential that the sup-
porting bearing for the input shaft of each pump and for
the output shaft be re-adjusted upon assembly.
3.
Reassemble the channel plate assembly to the reser-
voir mounting plate as follows:
a.
Insert the holding screws and leave them loose.
b.
Place the aligning tool
(P/N
450980) around the
output shaft of the motor and over the boss on the
reservoir mounting plate.
c.
This tool will insure that the output shaft is cen-
tered in relation to the outside circumference of the
boss. Consequently, the output shaft will be in align-
ment with the supporting bearing in the casting of
the carriage.
d.
Tighten the holding screws to fasten the channel
plate assembly to the reservoir mounting plate.
e.
Remove the aligning tool.
Figure 10. Hydraulic Unit-Exploded View
4. Install the pump
and the motor oil seals. It is advis-
able to use new oil seals for the space pump and the skip
pump to minimize the possibility of leakage.
5. Reassemble the components, with the exception of
the pump pulleys, on the shafts of the pumps and on the
shaft of the motor. Support each shaft as these components
are pinned to it to prevent any bending of the shaft.
6. Reinstall the outboard bearing flanges as follows:
a. Slide the outboard bearing flanges in place around
the pump shafts and snug the holding screws.
b. Each shaft must be able to rotate freely.
(1)
Rotate each shaft through at least 360° to
check for freedom from binds.
(2)
It may be necessary to re-adjust the outboard
bearing flange by tapping lightly into the correct
position.
c. When the shaft rotates freely without binds, tighten
the holding screws to fasten the outboard bearing
flange securely.
d. Recheck each pump shaft for freedom of rotation
after the holding screws have been tightened.
7. Reinstall the pulleys on the shafts, and fully support
each shaft to prevent bending as the pulley is pinned to
the shaft.
8. Check or make ( as required) all hydraulic unit ad-
justments that can be made with the reservoir removed.
9.
Replace the valve
body
assembly. Four screws hold
it in position.
10.
Replace the reservoir. Sixteen screws hold it in place.
11.
Make the following replacement and adjustments:
a.
replace the hydraulic unit.
b.
adjust the space needle valve.
c.
adjust the skip needle valve.
d.
adjust the bypass needle, valve.
e.
adjust the single-space single shot.
f.
adjust the emitter brush.
g.
adjust the carriage tape brushes dynamically.
Hydraulic Pump Drive Belt Tension
Shift the drive motor in its slots to obtain
1
/8 to 3‘2"
deflec-
tion of the belt halfway between the drive motor and the
eject pump with a force of one pound ( about 450 grams) .
Carriage Controls
Space
Control Magnets Adjustments
1. Spacing and skipping failures are usually caused by
circuit malfunctions, in particular, the emitter brushes.
The hydraulic unit is quite reliable; it should be the last
place to check for malfunctions.
~
28
REMOVALS AND ADJUSTMENTS
29

.005"
to
.008"
Adjusting
Screw
.S.
nip
i
~
e .Im
y
m.
03=2E_7(-)
~
Figure 12. Space Magnet Stop Position
.005"
to .008"
C= _.
~~
~
~~
!
11
(
.
~.
0 ®
.020"
to
.025"
-t---Detent Wheel
Detent Piston
Detent Arm-t-
Detent
Eccentric
Backstop
Figure 11. Positioning Space Magnet Armature
2.
Remove the valve body assembly.
3. Turn off the printer main-line switch and leave off
to prevent the operation of the carriage drive motor. Some
of the following adjustments require that the system power
be on so that the hydraulic unit space start and space stop
magnets can be energized.
4. Add or remove the shims under the pivot support
block to obtain .011" to .013" clearance between the start
and stop magnet cores and the armature (Figure 11) . The
nominal clearance between the armature and the magnets
when in the neutral (de-energized) position is 0.011" to
0.013". Some spool valve units have a 0.011" to 0.014"
clearance which is correct. The spool valve adjustments
are not critical. Normally, this adjustment will have to be
changed only if related parts have been replaced.
5. Energize space stop magnets.
a.
Connect the wires to the space stop magnets.
b.
Insulate (tape) individually the ends of the other
wires.
c.
Turn on the system power.
6. With the space stop magnet energized, adjust the
back stop screw nearest the operating rod for .005" to .008"
clearance (preferably .005") between the armature and
the stop magnet cores (Figure 12) .
7. Turn off the system power.
8. Energize space start magnets.
a.
Remove the wires from the space stop magnet
terminals and insert into the space start magnet
terminals.
b.
Turn
on the system power.
9. With the space start magnet energized, adjust the
backstop farthest from the operating rod for .005" to .008"
clearance (preferably .005") between the armature and
the start magnet cores ( Figure 13) .
NOTE:
If it is objectionable to use a steel feeler gage in
the preceding steps because of the attraction of the ener-
gized control magnets, the use of an IBM card to obtain
these adjustments is permissible.
10. Slow operation will result from a clearance of less
than .005". There are no residuals on the armatures or
cores.
11. Turn off the system power.
12. Whenever this adjustment has been made, the space
control valve adjustments must be checked or made.
Adjusting Sore
Figure 13.
Space Magnet
Start Position
Space Control Valves Adjustments
1.
First,
check, or adjust the space control magnets.
2.
Insure that at least half of the lower threaded portion
of the operating rod is screwed into the control valve and
that the locking nut at the upper end of the control valve
is tight.
'3. Turn on the system power.
4. With the space start magnet energized, adjust the nuts
at the top of the operating rod for .009" to .011" clearance
between the top of the valve and the top surface of the
rectangular port in the valve body (Figure 14).
a.
This should result in .009" to .015" clearance be-
tween the bottom of the valve and the lower surface
of the rectangular port with the stop magnet energized
and the armature in the stop position ( Figure 15) .
b.
The nominal adjustments of the .011" to .013"
clearance and the .005" to .008" clearance for the con-
trol magnets will result in a .020" to .024" control
valve travel.
c.
If the .009" to .015" clearance does not fall within
the prescribed dimensions, the space control magnets
must be re-adjusted within tolerance, to obtain the cor-
rect clearance.
5. Turn off the system power.
6. Turn the tab on the lockwashers over to keep the nuts
from loosening during operation.
7. Replace the valve body assembly.
Figure 14. Space Valve
Figure 15. Space Valve
Start Position
Stop Position
Skip Control Magnets Adjustments
NOTE:
Adjust in the same manner as
Space Control Mag-
nets Adjustments.
Skip Control Valve Adjustments
NOTE:
Adjust in the same manner as
Space Control Valves
Adjustments.
Hydraulic Detent Stop Adjustments
1.
Raise the tape brushes to prevent any possible dam-
age to them during this adjustment (if the reservoir can
be removed with hydraulic unit in machine) .
2.
Remove the reservoir that encloses the hydraulic unit.
3.
Insure that the carriage is turned only in the forward
direction. The emitter brushes may be damaged if the
carriage is turned backwards (if the reservoir can be moved
with hydraulic unit in machine) .
4.
Position the backstop with the high side of the eccen-
tric down. This causes the detent arm pounding to tighten
the holding nut.
5.
Adjust the detent backstop for a clearance of .020"
to .025" between the detent arm and the detent wheel
when the arm is held against the backstop (Figure 16) .
6.
Replace the reservoir that encloses the hydraulic unit.
Space Needle Valve Adjustments
1. Set
up the carriage.
a.
Remove the paper from the carriage.
b.
Tape
the form stop contacts closed.
c.
Engage the manual clutch in either the 6 or the 8
lines-per-inch position.
d.
Install an unpunched carriage tape.
e.
Lower the tape brushes.
2. Start the carriage by depressing the carriage restore
key.
3. Before adjusting the needle valve, allow the carriage
to idle for at least fifteen minutes to bring the oil tempera-
ture up to operating level. The hydraulic unit should be
hot to the touch before the needle valve adjustments are
made.
4. Loosen the lock
screw
for the center needle valve
(the center right screw, Figure 17).
Figure 16. Detent Adjustment
5. Adjust the needle valve to cause the detent to nip
as
follows:
a.
Hold a screwdriver against the detent arm at the
notch.
b.
Back off on the center left screw (Figure 17) until
you can feel the detent nip the detent wheel. The im-
pact will be transmitted through the screwdriver.
6. Adjust the needle valve to cause the detent to stop
nipping:
a. Turn down on the center left screw until the detent
stops nipping.
(1)
Press down on the screwdriver, and feel the
play between the detent arm and the detent stop stud.
(2)
Turn down screw gradually until all play dis-
appears.
b. Tighten the lock screw (the center right screw).
7. After this adjustment has been made, the skip needle
valve
must be adjusted.
Skip Needle Valve Adjustment
(2-Speed Carriage Machines)
1. First, the space needle valve must be adjusted.
2. Set up the carriage. Check that
a.
there is no paper in the carriage.
b.
the form stop contacts are closed.
c.
the manual clutch is engaged.
d.
unpunched carriage tape is installed.
e.
the tape brushes are lowered.
3. Start the carriage in a programmed skip to 1 before
print. This should result in a skip to 1 at high speed with
no stop impulse available.
4. Loosen the lock screw for the skip needle valve (the
front right screw, Figure 17).
5. Adjust the skip needle valve as follows:
a.
hold a screwdriver against the detent arm at the
notch.
b.
back off on the front left screw (Figure 17) until
you feel the detent nip the detent wheel. The impact
will be transmitted through the screwdriver.
(1) If no nipping is detected after turning out a
maximum of
five turns,
stop the carriage motor so
cd
.
30
REMOVALS AND ADJUSTMENTS
31

Locking Screws
Needle Valve
Adjusting Screws
By-Pau
Line Space
Skip
~
©
0
that the hydraulic pumps are not moving. Turn down
on the front left screw until it is closed. Then back off
five full turns on this screw. Tighten the lock screw
(the front right screw).
(2) If nipping is detected, adjust the needle valve
to cause the detent to stop nipping. Turn down on
the front left screw until the detent stops nipping.
Press down on the screwdriver, and feel the play
between the detent arm and the detent stop stud.
Turn down screw gradually until all play disappears.
Tighten the lock screw (the front right screw). Stop
the carriage. After this adjustment has been made, the
bypass needle valve must be adjusted.
Bypass Needle Valve Adjustments
1. First, the following adjustments should be made:
a, the space needle valve.
b.
the skip needle valve (on machines with two-speed
carriage).
c.
the single shots within the system that pertain to
the carriage.
2. Insure that the following adjustments are correct:
a.
the tractors.
b.
the tractor drive shafts.
c.
the single-shots within the system that pertains to
the carriage.
3. Insure that the emitter brush is just fully made on a
segment of the emitter.
4. Set up the carriage.
a.
Place the paper in the carriage.
b.
Program for triple space before print.
c.
Engage the manual clutch in the 6 lines-per-inch
position.
d.
Remove the upper front paper guides.
5. Loosen the lock screw for the bypass needle valve
(the rear right screw, Figure 17).
Fixed Orifice in By-Pass only
Figure 17. Needle Valves
6.
Turn in on the bypass needle valve (rear left screw)
until it is closed.
7.
Disengage the detent arm by pressing down in the
notch with a large screwdriver.
8.
Start the carriage by depressing the start key.
9.
Adjust the bypass needle valve as follows:
a. Draw line graphs across the paper while it is
feeding.
(1)
Use the jam bar as a guide.
(2)
Move the pencil at a rate that will show from
4 to 10 triple spaces on a sheet 11 inches wide.
(3)
Too much pencil pressure can cause a drag on
the paper, and, therefore, an erroneous graph.
(4)
The resulting graph should be similar to Fig-
ure 18.
b.
Turn out on the bypass needle valve until the line
graph just resembles Figure 19. Turn out an addi-
tional Y8 or Ke turn and lock in this position.
c.
Tighten the lock screw (the rear right screw).
10.
Stop the machine.
11.
After this adjustment has been made, the following
must be adjusted:
a.
the emitter brush.
b.
the single-space single shot.
c.
the tape drive sprocket and the carriage brushes.
u
Figure 18. Bypass Closed Detent Inoperative
~
Figure 19. Bypass Adjusted Correctly
Single-Space Single-Shot Adjustments
1. Insure that no binds exist when you manually turn
the forms advance knob with the 6-8 knob in neutral.
2. Set up the carriage.
a.
Check that paper is in the carriage.
b.
Check that upper front paper guides are removed.
c.
Check that manual clutch is in 6 lines-per-inch
drive position.
d.
Program for single space before print.
3. Start the carriage by depressing the start key.
4. Draw line graphs on the paper while it is feeding.
a.
Use the jam bar as a guide.
b.
Move the pencil at the rate that will show from
4 to 10 single spaces on a sheet 11 inches wide.
c.
Too much pencil pressure can cause a drag on the
paper, and, therefore, an erroneous graph.
d.
The resulting graph should be similar to Figure 20.
5. Adjust single-space single-shot to produce the desired
result (E2 brush single shot in 1401 system).
Figure 20. Single-Shot Adjusted Correctly
Emitter Brush Adjustments
1. Insure that no binds exist when you manually turn
the forms advance knob with the 6-8 knob in neutral.
2. Set the emitter brushes in the brush holder for a pro-
jection beyond the brush holder of
23‘2" ± %4".
3. Set up
the carriage.
a.
Check that the paper is in the carriage.
b.
Check that the upper front paper guides
are
removed.
c.
Check that the manual clutch is in 6 lines-per-inch
drive position.
d.
Program for triple space before print.
4. Start the carriage by depressing the start key.
5. Draw line graphs on the paper.
6. Shift the brush assembly until the line graph appears
as shown in Figure 21.
a.
There may be a slight overshoot (maximum allow-
able X2")
") on these graphs.
b.
Some overthrow may be necessary on triple space
6 lines-per-inch to prevent
excessive pull
-
in
on double
space 8 lines-per-inch.
7. Check brush setting for double space.
a.
Set the manual clutch to 8 lines-per-inch drive
position.
b.
Program for double space before print.
c.
Start carriage and draw line graphs.
8. Re-adjust the brush assembly as required for the best
line graph of
a.
double
space 8
lines-per-inch.
b.
triple space 6 lines-per-inch.
9. After this adjustment has been made, adjust the tape
drive sprocket and the carriage brushes.
Indicates a brush
out of adjustment
Misadjusiment of a
4
-
brush can cause either
OVERSHOOT
UNDERSHOOT
Figure 21. Emitter Brush Adjusted Correctly
Carriage Tape Brushes (Statically) Adjustments
(Figure 23)
1. Position the tape brushes for 1" +,%
2
" -0" projection
from the brush bolder (Figure 22). CAUTION: The range
of adjustment should be held as close as possible because
of possible difficulties in timing"the stop brushes to the El
brush.
PROJECTION FROM BRUSH HOLDER
Figure 22. Carriage Tape Brush Projection
2.
Adjust the brush separator collars on the pivot rod so
that the brushes are centered in separator slots and for
minimum end shake of separator.
3.
Position the brush holders so that the toe of the
shorter group of strands lines up with the scribed line on
the brush separator when the brushes
are
held even with
the separator.
4.
Position
the brush separator eccentric stop stud for
0.050" ± 0.010" clearance between the brush separator
and the contact rolls.
5.
Adjust the brush separator rod with brush assembly
open and so that brush tips are below active surface of
separator a minimum of
%
4
4 r.
6.
Align the brush tracking by shifting the tape drive
sprocket on the shaft. NOTE: Do not shift the sprocket in
such a way that the tape rides improperly between the
contact rolls.
7.
Position the inner tape guide so that it is below the
active surface of the tape drive sprocket 0.012" ±0.001".
8.
Loosen the outer tape guide on
the
latch shaft and
center the guide around the pin feeds in the drive sprocket
(leave loose).
9.
Position
the latch block within the limits of its mount-
ing hole for these conditions when latched so that the
a.
arc ( cylindrical surface ) of the outer tape guide is
equally divided by the point of contact of the arc and
the drive sprocket.
b.
clearance from the bottom face ( side that faces
pawl)
of latch block to upper side of latch pawl is
0.003" to 0.006".
c.
clearance from the stud in the separator ( left side)
to the brush frame is approximately 0.005".
This may occur due to
carriage drift.
REMOVALS AND ADJUSTMENTS
33
32

10. Position the outer tape guide.
a.
Rotate the guide around the latch shaft until the
clearance between the arc and the drive sprocket is
0.010" to 0.020".
b.
Clamp the guide.
11. Adjust the brush separator support plate so that
a.
with the assembly open the brushes are below the
active surface of the separator.
b.
stop rod does not interfere with the brush separator
as the assembly is closed.
12. Adjust the brush interlock switch actuator so that
a.
interlock switch is made when the brushes are
down.
b.
switch opens before the latch pawl disengages the
latch block.
13. After these adjustments have been made, adjust the
carriage tape brushes dynamically.
CAUTION:
Be sure the stop rod is located so that it will
not contact the raised hub of the contact roll. Blown fuses
may result.
Carriage Tape Brushes (Dynamically) Adjustments
1. Insure that no binds exist when you manually turn
the forms advance knob with the 6-8 knob in neutral.
2. Set up the carriage for dynamic adjustment.
a.
Insert a carriage tape punched with a hole in
channel one.
b.
Remove the forms.
c.
Engage the manual clutch in 6-line drive.
d.
Program a space to zero (no numeric bits) before
print.
3. Set up the scope for
a.
1 ms/division horizontally.
b.
10v/division vertically.
c.
Sync on negative shift of stop brush (at
CE
indi-
cator panel on current machines or at pin 28 on re-
sistor panel on earlier machines).
4. Start carriage by depressing the start key. Stop the
carriage by depressing the carriage stop key.
5. Probe the negative shift of the emitter brush (at
CE
indicator panel on current machines or at pin 38 on resistor
panel on earlier machines).
6. Rotate the tape drive sprocket with respect to its
shaft so that emitter will make 1 millisecond
±
1
/4
milli-
second after the tape stop brush.
O
Figure 23. Carriage Tape Brushes
34
REMOVALS AND ADJUSTMENTS
35

Locations and Voltage Specifications
Voltage
The carriage motor, the type array drive motor, and the
hammer blower motor are 208-230 volts ac 3-phase motors.
WARNING:
Be careful of this voltage.
Voltage Variation
When connected to the system, the printer must continue
to perform all specified functions within the following volt-
age ranges:
Line Voltage ± 10%.
—60 volts dc
±4% at component using voltage
—
6 volts dc
±4% at component using voltage
+ 6 volts dc
-_*4% at component using voltage
—12 volts dc
±4% at component using voltage
+12 volts dc
±4% at component using voltage
—
20 volts do
±4% at component using voltage
Serial Plate
This is mounted on the top surface of the right cover frame.
Ground
The ground connections are made at the left front corner
of the cover frame.
Connectors
The two-signal and one-power connector enter the printer
at the left.
Resistors
These are located at the rear of the printer at the upper
right above the hydraulic unit. The carriage resistors are
mounted on a heat sink behind the hydraulic unit.
Main
-
Line Switch (AC Power)
This is located at the left rear corner of the cover frame.
CAUTION:
This switch is to be used to condition the
printer. Operate it only when the system power is off. It
does not remove all dc voltages.
Convenience Outlet
This is available from underneath at the rear of the printer.
Terminal Blocks
TB-1,
10-position terminal; rear cover frame
TB-2,
8-position terminal; in hydraulic reservoir
TB-3,
3-position terminal; on printer casting at upper left
TB-4,
for hammer magnet; (when installed, blower)
TB-5,
2-position terminal; on ribbon drive unit
TB-6,
4-position terminal; on ribbon drive unit
TB-7,
6-position terminal; on T-casting at left rear
TB-8,
2-position terminal; on T-casting at left rear
Thermistors
These are in series with the hammer magnets and are
located at
,
the rear of the printer on the left.
36
(7-6 1:9M-VO)
Other manuals for 1403
1
Table of contents
Other IBM Printer manuals
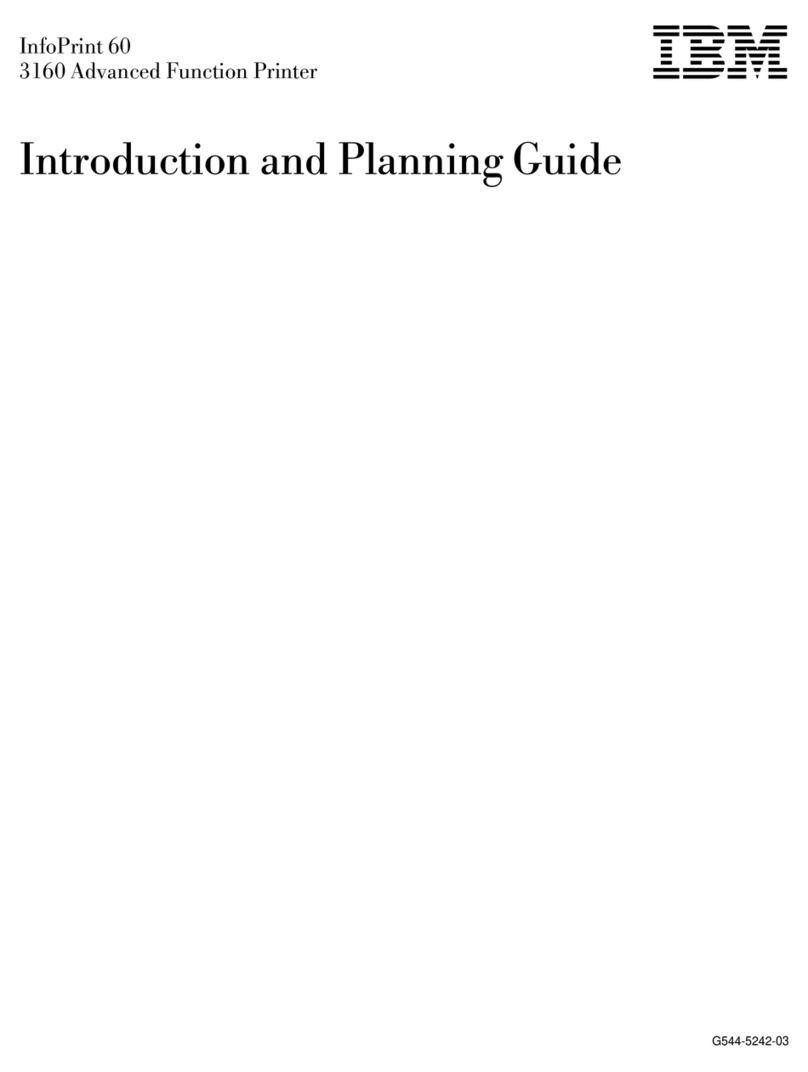
IBM
IBM 3160 Technical manual
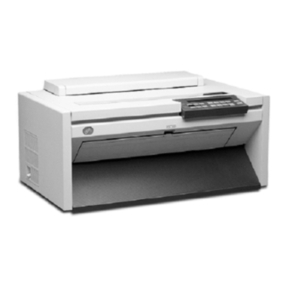
IBM
IBM Deskstar Deskstar 3 User manual
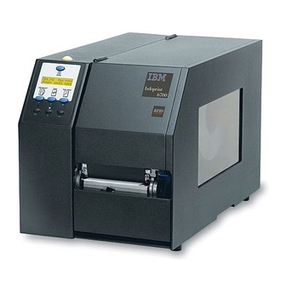
IBM
IBM 4400-006 - 4400 Model 006 B/W Direct Thermal User manual
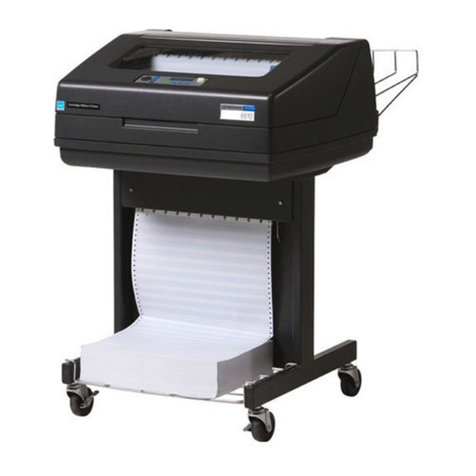
IBM
IBM InfoPrint 6500 User manual
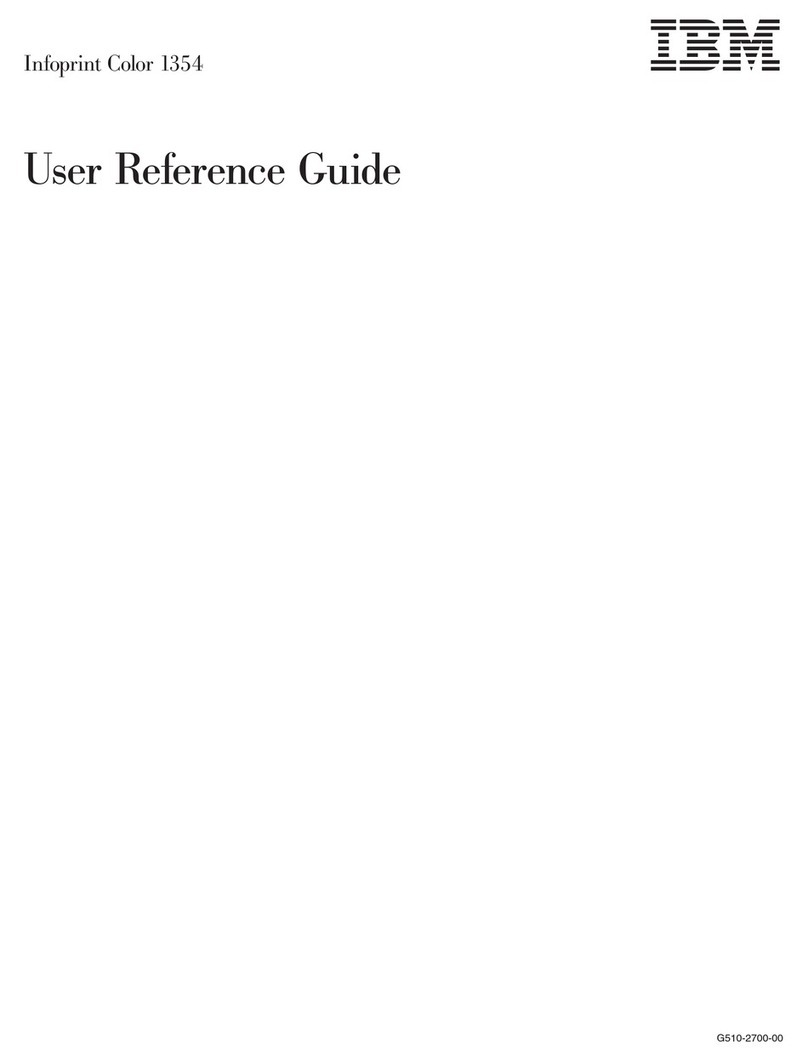
IBM
IBM Infoprint Color 1354 Product information sheet
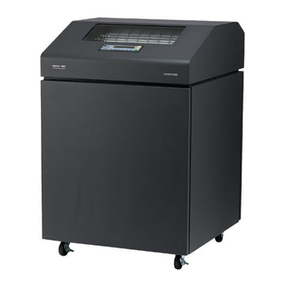
IBM
IBM InfoPrint 6500 User manual
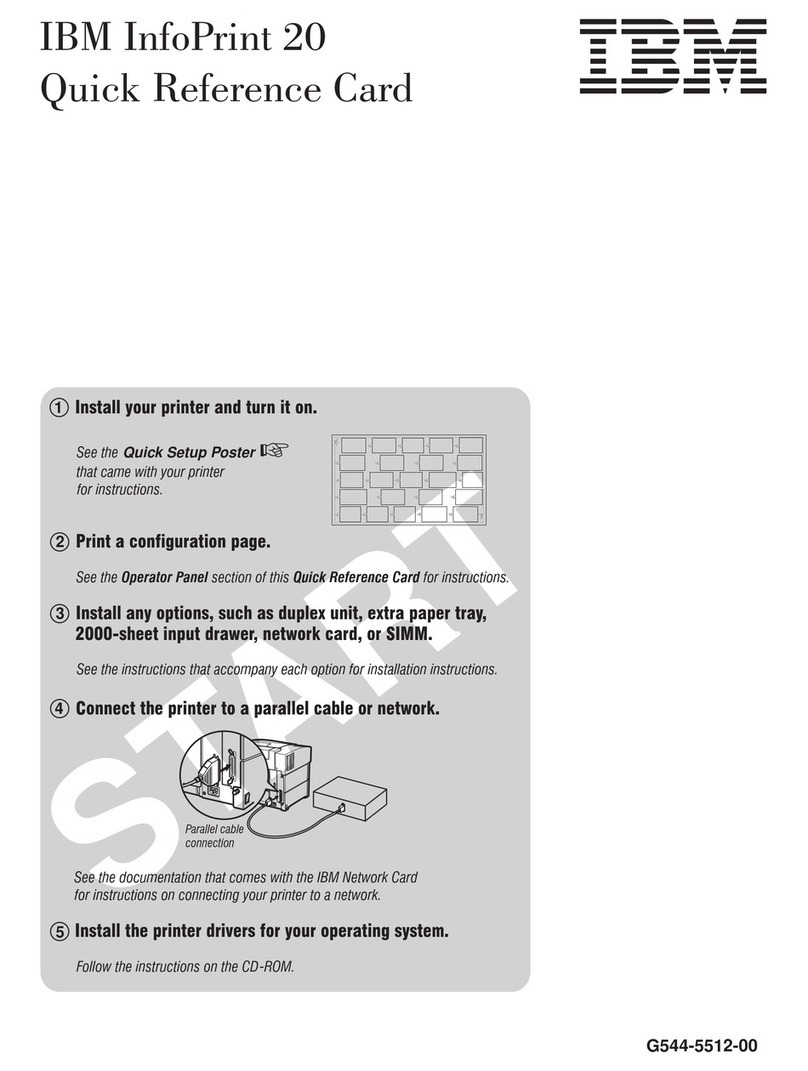
IBM
IBM InfoPrint 20 Reference guide
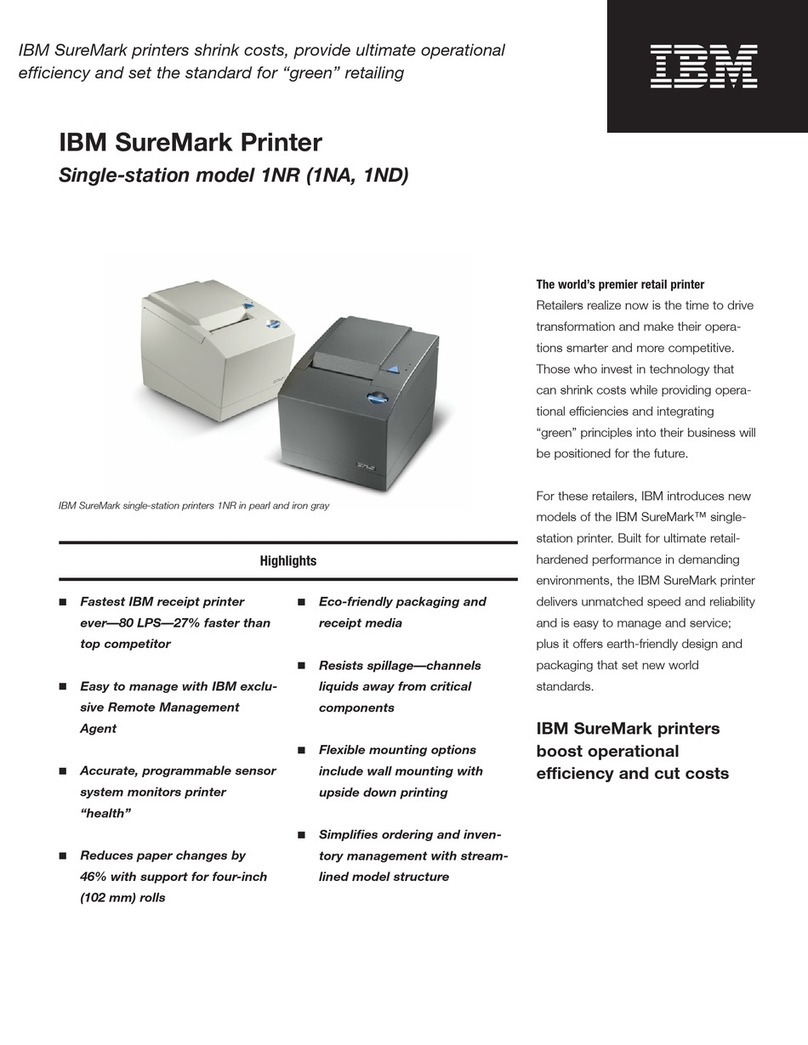
IBM
IBM SUREMARK 1NR User manual
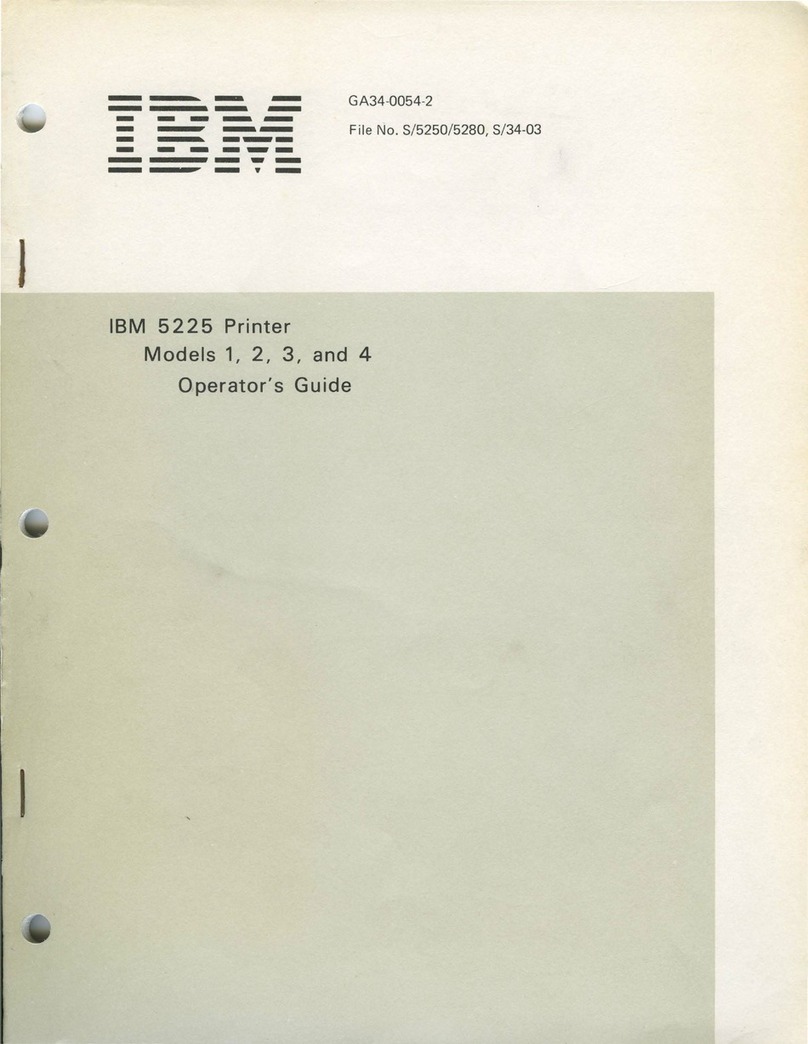
IBM
IBM 5225 Manual
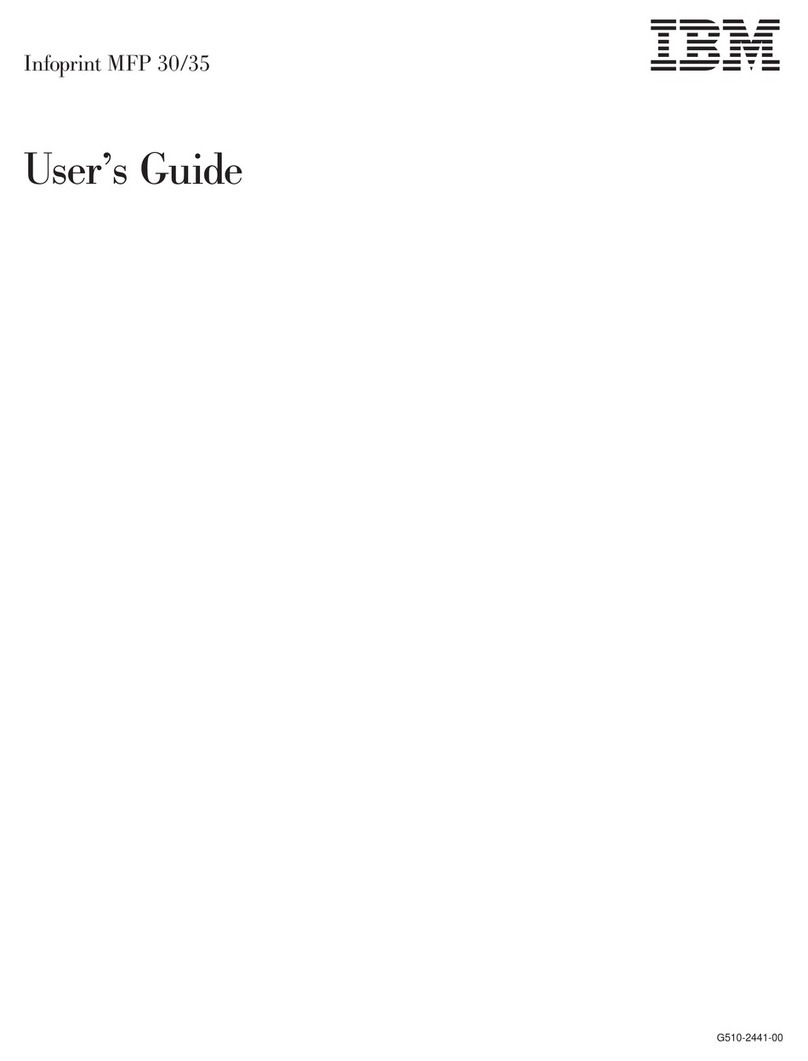
IBM
IBM Infoprint MFP 30 User manual
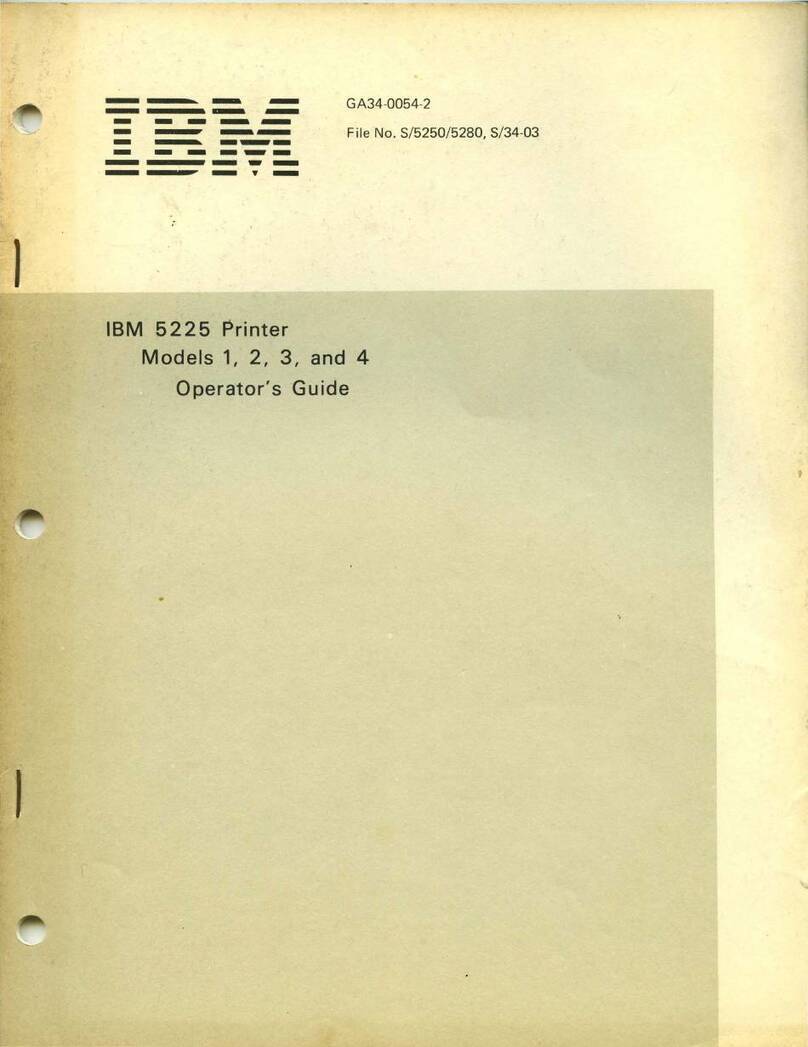
IBM
IBM 5225 1 Manual
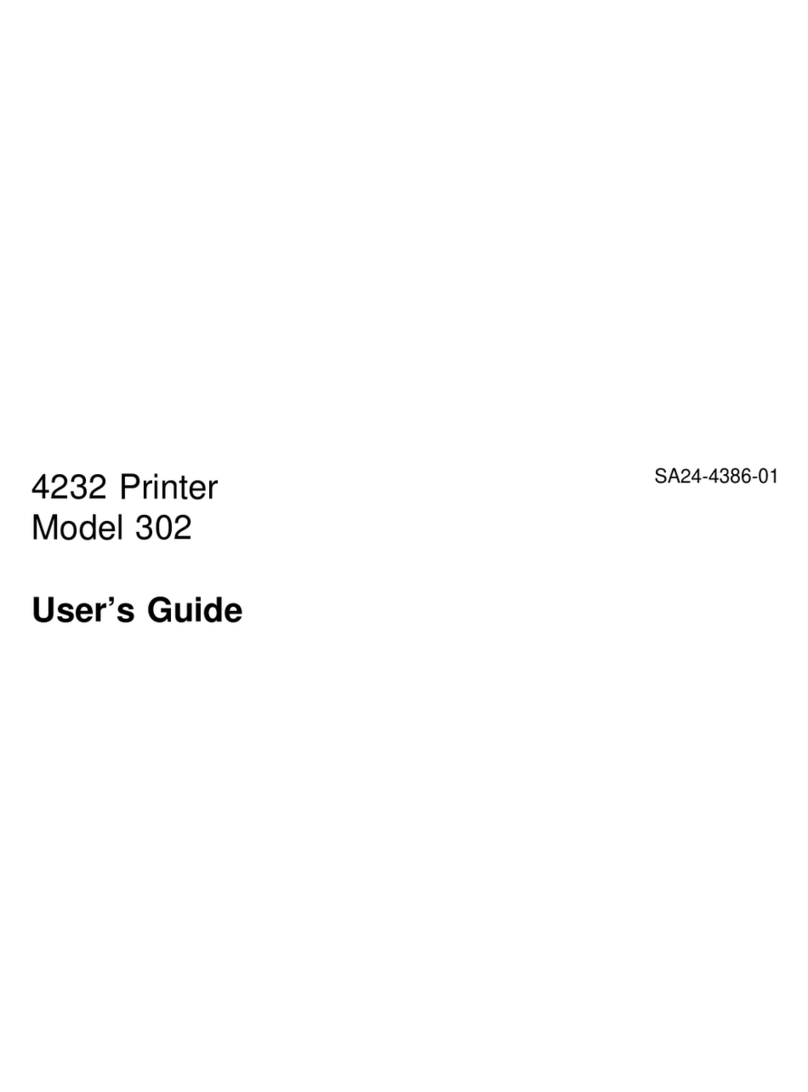
IBM
IBM 4232 PRINTER MODEL 302 User manual
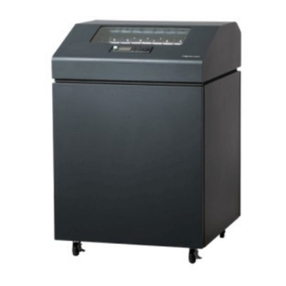
IBM
IBM Infoprint 6500-v05 User manual
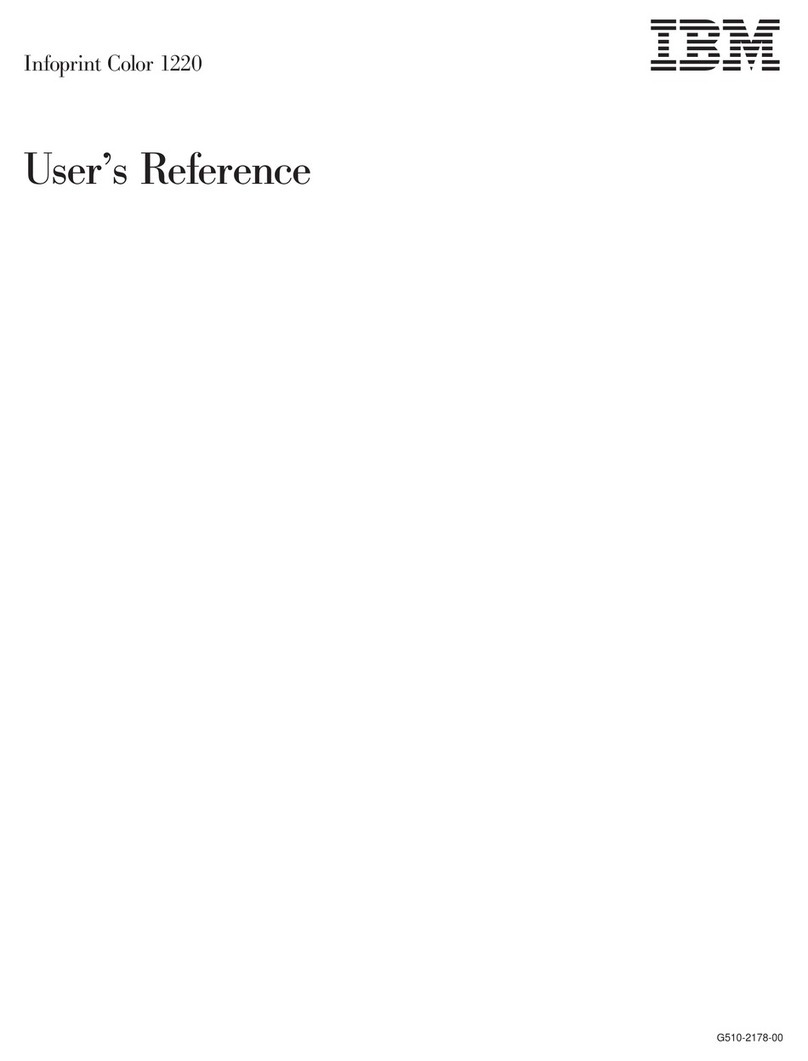
IBM
IBM 1220 Service manual
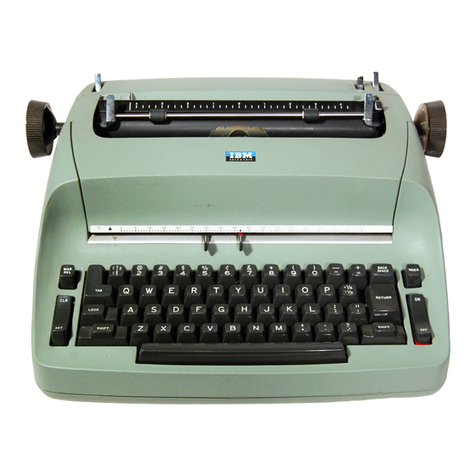
IBM
IBM Selectric I/O Manual
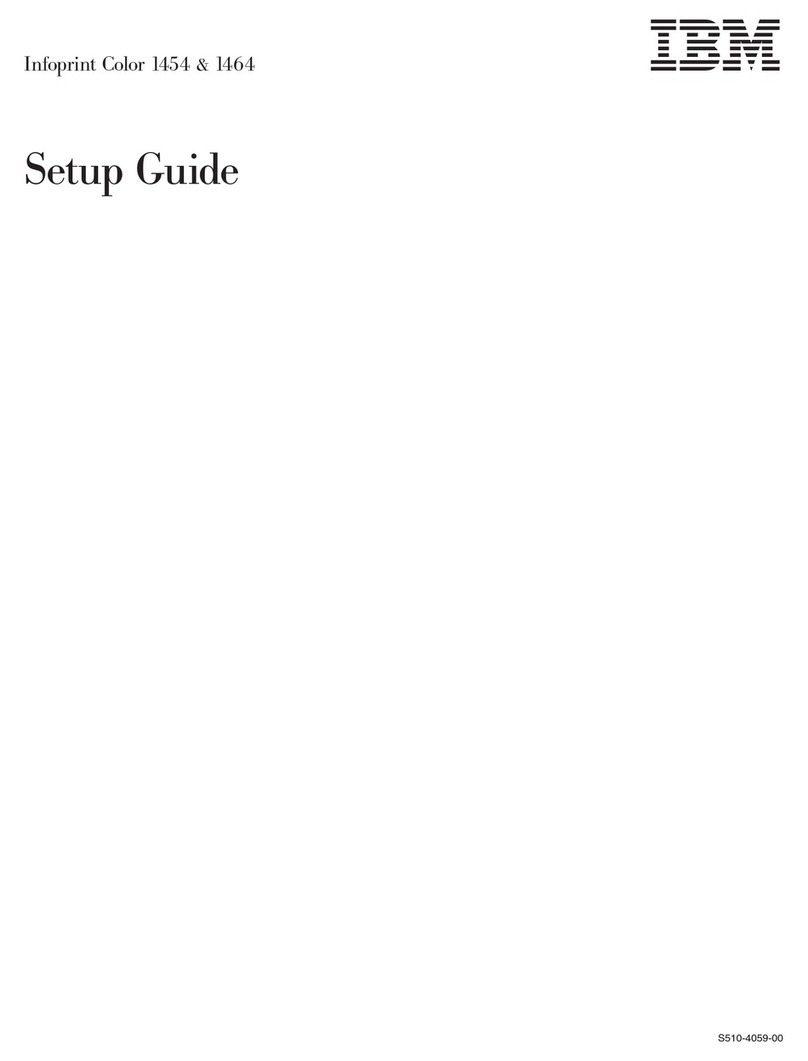
IBM
IBM 1454 User manual

IBM
IBM 5256-1 Setup guide
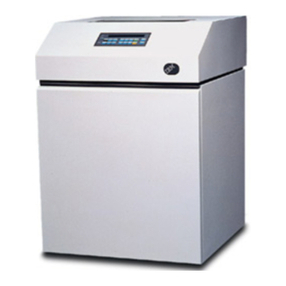
IBM
IBM 6400 - Model 008 B/W Line-matrix Printer Manual
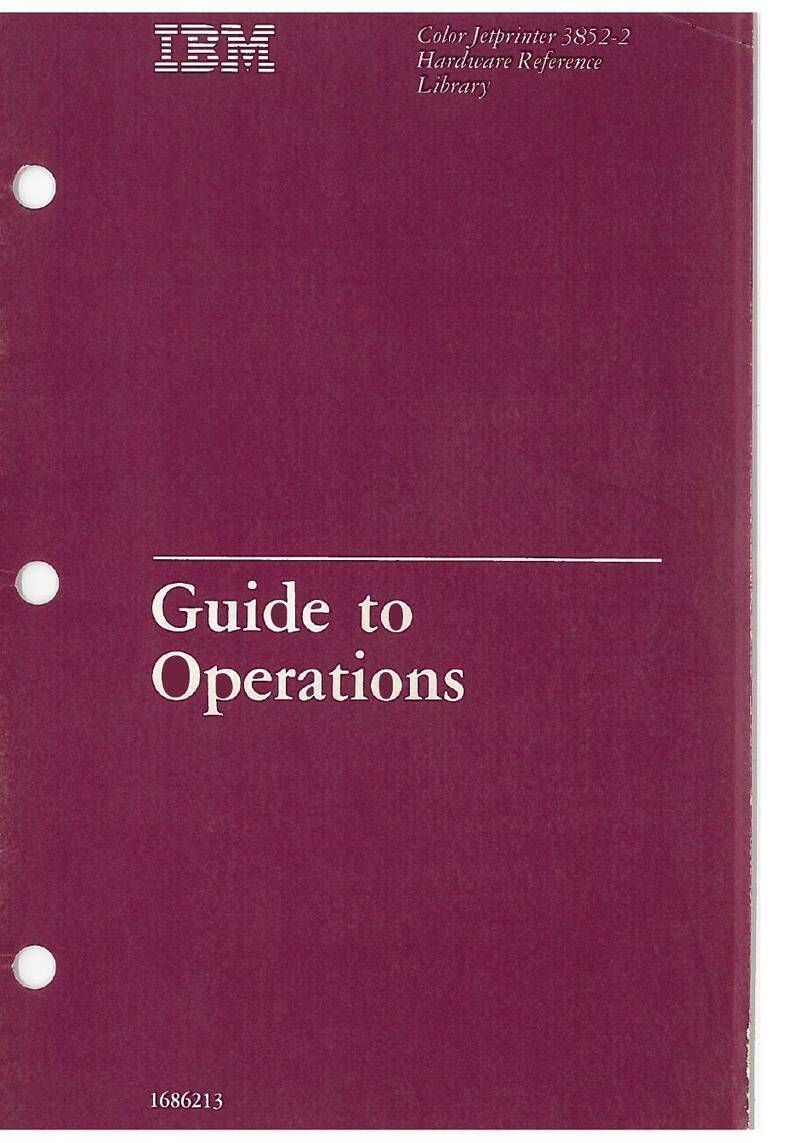
IBM
IBM 3852-2 Application guide
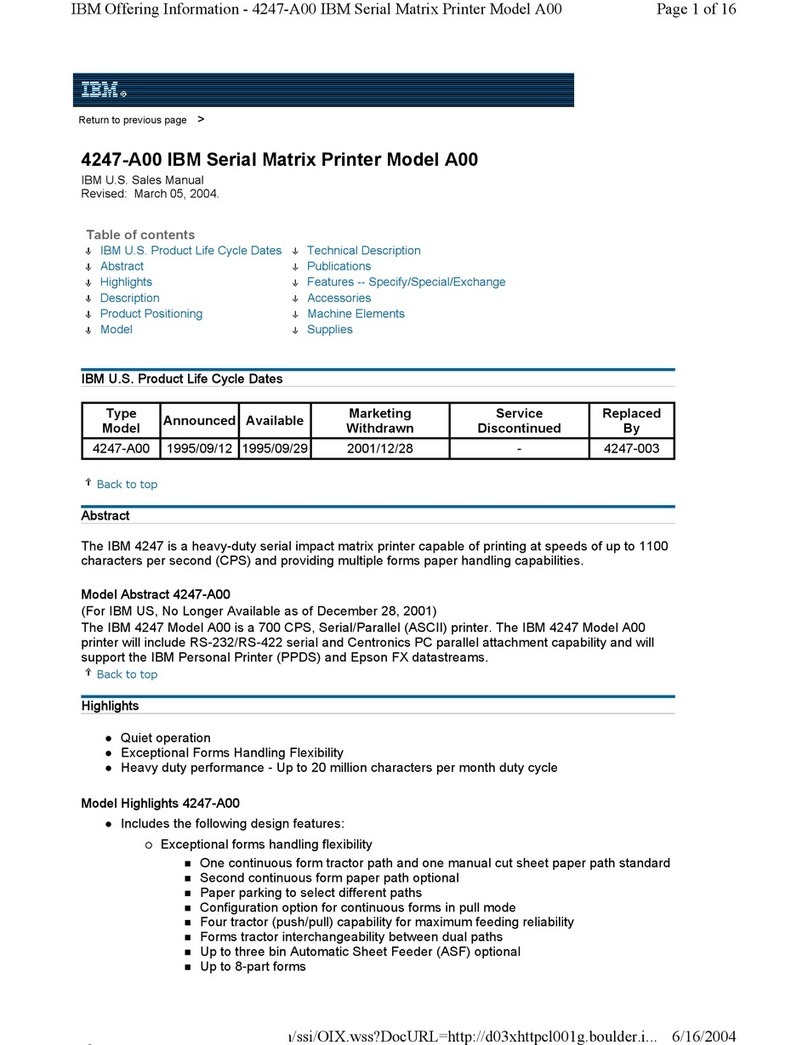
IBM
IBM Model A00 User manual