Roger PR302 User guide

PR302
v2.0
Installer Manual
Rev. B

PR302 v1.0 Installer Manual EN Rev. B.doc 8/19/2008
- 2 -
Introduction
This document contents minimum information required for electrical installation of PR302 access
controller.
Installation
The PR302 can be installed in indoor location only. All electrical connections must be made before
power supply will be applied. Factory new unit is configured for address ID=00 and has programmed
MASTER PIN (1234) and MASTER card (delivered with the new device). The MASTER card/PIN can
be used for initial testing of the controller - the single use of MASTER card/PIN activates
momentarily REL1 output (for approx. 4s); double, consecutive use of MASTER card/PIN changes
controller’s arming mode and switches IO1 output to reverse state.
All devices working in one access system and connected to the same RS485 communication bus
should have common minus (common GND). This can be achieved by connecting all supply minuses
using additional (separate) wire or connecting each supply minus with earth, however the second
method might create problems when electrical potentials of the earth are not the same in different
parts of the electric installation.
Note: It is forbidden to short positive outputs (DC+) from various sources of power and/or other DC
outputs available in the system.
Setting address
Before controller will be connected to communications bus it should be configured to individual
address (ID number=00..99). The controller’s address can be set manually using Memory Reset
procedure or from PC computer. In order to set/change controller’s address from PC connect it to
any free COM port and then using PR Master program enrol it to database. Once the unit is found by
PR Master use relevant command to change its address and then disconnect it from PC and connect
to designated access installation.
Note: Connecting two or more controllers with the same address will cause communications conflict
on the communication bus.
Power supply
Controller requires 10-15V DC supply and consumes 100mA average current. The power source
should provide DC voltage free of interferences. Using poor quality switched mode power sources
can cause reduction of card reading distance. Always carefully calculate wire gauge used to supply
access controller, note that amount of current required by controller can rise momentary up to
200mA. The GND input to controller is also reference ground for RS485 com. bus and for all signal
lines used in controller.
Door Lock
In most cases door locks are inductive type loads and generate strong voltage surges when
switching to off state. This phenomenal can corrupt electronic circuits and change its behaviour. In
order to protect access controller from these effects, every inductive load (like door lock or any
other coil) should be protected with silicon diode (e.g. 1N4007) connected as close as possible to the
switched device. Also, door locks should be wired using separate pair of wires connected directly to
the source of power.

PR302 v1.0 Installer Manual EN Rev. B.doc 8/19/2008
- 3 -
Inputs
The PR302 offers three programmable inputs (IN1, IN2 and IN3). All of them have the same
electrical structure and can be configured as NO or NC line. Each input is internally biased to supply
plus (+12V) through 5.6kΩresistor what makes that supply plus is observed on the free (not
connected) input. The NO type input goes active when shorted to supply minus (GND). The NC line
in normal state should be connected to GND, it became triggered when connection with GND is
discontinued.
Relay output
The PR302 has one programmable relay output (REL1) which offers single NO/NC/COM contact
24V/1.5A rated. In normal state NC contact is shorted to COM wile NO remains isolated. When
active, NO is shorted to COM while NC remains isolated. When controller is not supplied or supplied
with voltage below its minimum level, relay output remains not active.
Transistor outputs
There are two transistor outputs (IO1 and IO2) available on the PR302 controller, both have
identical electrical structure. When not active (normal state) transistor outputs represent high
impedance, when active (triggered state) outputs short to supply minus (GND). Each output can
switch max. 1A DC while voltage connected to it must not exceed 15V DC. The IO1 and IO2 have
internal over-current protection which switches them off for currents above 1A.
Communication bus
The communications bus consist of three lines: A, B and cable’s shield (SHLD). Electrically, it
represents RS485 standard however neither the daisy chain structure nor terminating resistors are
required. Instead of this free topology of communication bus is allowed, the A/B wires can be laid
down using “three’’, “star” or any combination of them. It is recommended to use UTP cable for A
and B lines however other types of signal cables are accepted as well. The use of shielded cables
should be limited to these installation were strong electromagnetic interferences are expected.
The max. cable distances:
•between communication interface and any controller on the bus: 1200m
•between communication interface and CPR network controller (if installed): 1200m
•between any access controller and CPR network controller (if installed): 1200m
When longer cable lengths are required the UT-3 (RS485/RS422 repeater) or UT-4 interfaces can be
used. Using link built from two UT-3 units communication distance can be extended by 1200m while
using UT-4 serial-to-ethernet converter distance is limited to area covered with computer network.

PR302 v1.0 Installer Manual EN Rev. B.doc 8/19/2008
- 4 -
Connecting readers and extension modules
Access terminals (readers) and extension modules (e.g. XM-2, XM-8) can be connected to controller
through CLK and DTA lines. Controller can operate either with Roger access terminals (using RACS
data output format) or with any other type of readers which are equipped with Wiegand or Magstripe
interfaces. Any type of signal cable can be used for CLK and DTA lines. Each device connected to
controller through CLK/DTA line must have its individual address (0..15) however this rule is valid
for devices using RACS format but not for Wiegand or Magstripe interfaces.
Note: Normally, the maximum guaranteed cable length between controller and any other device
connected to CLK/DTA line is limited to 150m nevertheless when using RACS interface
communication will run satisfactory for up to 500m distances, however it is not guaranteed in every
case.
For best card reading results controller should be installed on non metal surface. When installed on
metal structure the reading range can be reduced up to 50%. This effect can be reduced by placing
non metal spacer (min. 10mm thick) between controller and metal surface where controller is
installed. Readers should be installed on at least 0.5m distance from each other, also two readers
should not be aligned along the same geometrical axes.
Connecting Wiegand and Magstripe readers
Follow schematic drawing below when connecting Wiegand or Magstripe readers to controller. Note,
that to prepare the controller for operation with those type of readers you must make adequate
settings in PR Master program.

PR302 v1.0 Installer Manual EN Rev. B.doc 8/19/2008
- 5 -
Memory Reset
The Memory Reset procedure clears all existing data in memory, restores default settings of
configuration, enables for enrolment of the new MASTER card/PIN and new ID number (address) of
the controller. There are two methods to enter Memory Reset:
•By means of CLK and DTA line
•By means of programming jumpers available on the controller’s PCB
The method by use of CLK and DTA lines doesn’t requires access to the internal space of controller’s
enclosure.
Memory Reset by means of programming jumpers:
•Put jumper on MEMORY RESET contacts and wait till LED OPEN (green) will start blinking
•Remove jumper from MEMORY RESET contacts
•Enter new MASTER PIN and press [#] or if you don’t want to program it press [#] key only
•Read any proximity card - this will be a new MASTER card or press [#] to skip this step
•Enter two digits (range 00..00) which will program new ID number (address) for the unit
After this step Memory Rest will be completed and controller returns to normal operations.
Memory Reset by means of CLK and DTA wires:
•Remove all connections from CLK and DTA lines
•Short CLK and DTA lines
•Restart controller (power off/on)
•Wait till LED OPEN (green) starts flashing
•While LED OPEN is flashing remove connection between CLK and DTA lines, controller will
restart with address ID=0 but without MASTER card/PIN
After this step Memory Reset is completed and controller returns to normal operations.
Once the Memory Reset is completed controller restores Default (Factory) Settings, using MASTER
PIN/card you can initially test installation while:
•Single use of MASTER PIN/card triggers REL1 for 4s
•Double use of MASTER PIN/card changes controller’s arming mode and switches IO1 output
to opposite state.

PR302 v1.0 Installer Manual EN Rev. B.doc 8/19/2008
- 6 -
Firmware upgrade
During manufacturing process controller is programmed with latest version of firmware,
nevertheless it can be later upgraded with newer versions. Roger design team continuously work on
enhancements so the new firmware versions are released quite often (every new firmware version is
published on www.roger.pl). Our customers are advised to register at web site so Roger will let
inform when new versions are ready for download. The new firmware can be downloaded without
removal of the controller from live installation. The detailed description of firmware upgrade
procedure can be found in Firmware upgrade.pdf on www.roger.pl.
The new firmware is programmed into the controller by means of communication bus and doesn’t
require de-installation of the unit from its original location. For firmware upgrade the RogerISP v3
program is required. Once the controller is upgraded it should be fully reconfigured, also it is
necessary to update the RACS database which must be aligned with current version of controller’s
firmware (command …Networks/Controllers/Commands/Restart controller and verify
version..).
Note: Whenever new firmware is uploaded into the unit the PR Master program should be also
upgraded to latest available version.

PR302 v1.0 Installer Manual EN Rev. B.doc 8/19/2008
- 7 -
Connection terminals
Name Function
+12V Power supply plus
0V (GND) Power supply minus, also reference ground for inputs, RS485 and
CLK/DTA lines
IN1 IN1 input, internally pulled to supply plus through 5.6kΩresistor
IN2 IN2 input, internally pulled to supply plus through 5.6kΩresistor
IN3 IN3 input, internally pulled to supply plus through 5.6kΩresistor
SHLD RS485 cable’s shield
RS485 A RS485 communication bus, line A
RS485 B RS485 communication bus, line B
CLK RACS Clock & Data interface, line CLOCK
DTA RACS Clock & Data interface, line DATA
TAMPER Tamper switch, line A, 24V/50mA rated
TAMPER Tamper switch, line B, 24V/50mA rated
IO2 IO2 transistor output 15V DC/1.0A
IO1 IO1 transistor output 15V DC/1.0A
REL1-NC REL1 output, normally closed contact, 24V/1.5A rated
REL1-COM REL1 output, common contact, 24V/1.5A rated
REL1-NO REL1 output, normally open contact, 24V/1.5A rated
Technical specification
Supply voltage 10-15 VDC
Current consumption
average 80 mA
Anti-sabotage Isolated contact, NC type, 50mA/24V rated, IP67
Reading distance UP to 12 cm for ISO card (depends on card type)
Cards EM 125 KHz (EM4100/4102 compatible)
Environmental class
(according to
EN50131-1)
Class I, Indoor, temperature: +5°C- +40°C, relative humidity: 10 to
95% (non-condensing)
Ingress protection IP 30
Dimensions 105 X 105 X 31 mm
Weight ~ 140g
Approvals CE

PR302 v1.0 Installer Manual EN Rev. B.doc 8/19/2008
- 8 -
Ordering information
PR302 PR302 access controller
RM-2 Relay module with plastic enclosure, the RM-2 offers two relays with one
NO/NC contact 1.5A/24V rated, relay contacts are protected by over-voltage
components, each relay can be triggered by applying supply plus or minus, the
maximum amount of current required to trigger relay is less then 5mA, two
LEDs to indicate triggering of relevant relay
RM-2 PCB RM-2 PCB module without enclosure
XM-2 Input/output addressable extension module with plastic enclosure, digital
communication according to RACS Clock and Data protocol, two NO/NC inputs
and two relay outputs, each relay offers one NO/NC contact 1.5A/24V rated,
relay contacts protected by over-voltage components, two LEDs to indicate
triggering of relevant relay
XM-2 PCB RM-2 PCB module without enclosure
UT-2 RS232-RS485 communication interface
UT-2USB USB-RS485 communication interface
UT-4 Ethernet-RS485/RS232 communication interface
Contact
Roger sp. j.
82-416 Gosciszewo
Gosciszewo 59
Tel.: +48 (55) 272 01 32
Fax: +48 (55) 272 01 33
e-mail: [email protected]

PR302 v1.0 Installer Manual EN Rev. B.doc 8/19/2008
- 9 -

PR302 v1.0 Installer Manual EN Rev. B.doc 8/19/2008
- 10 -
Other manuals for PR302
2
Table of contents
Other Roger IP Access Controllers manuals
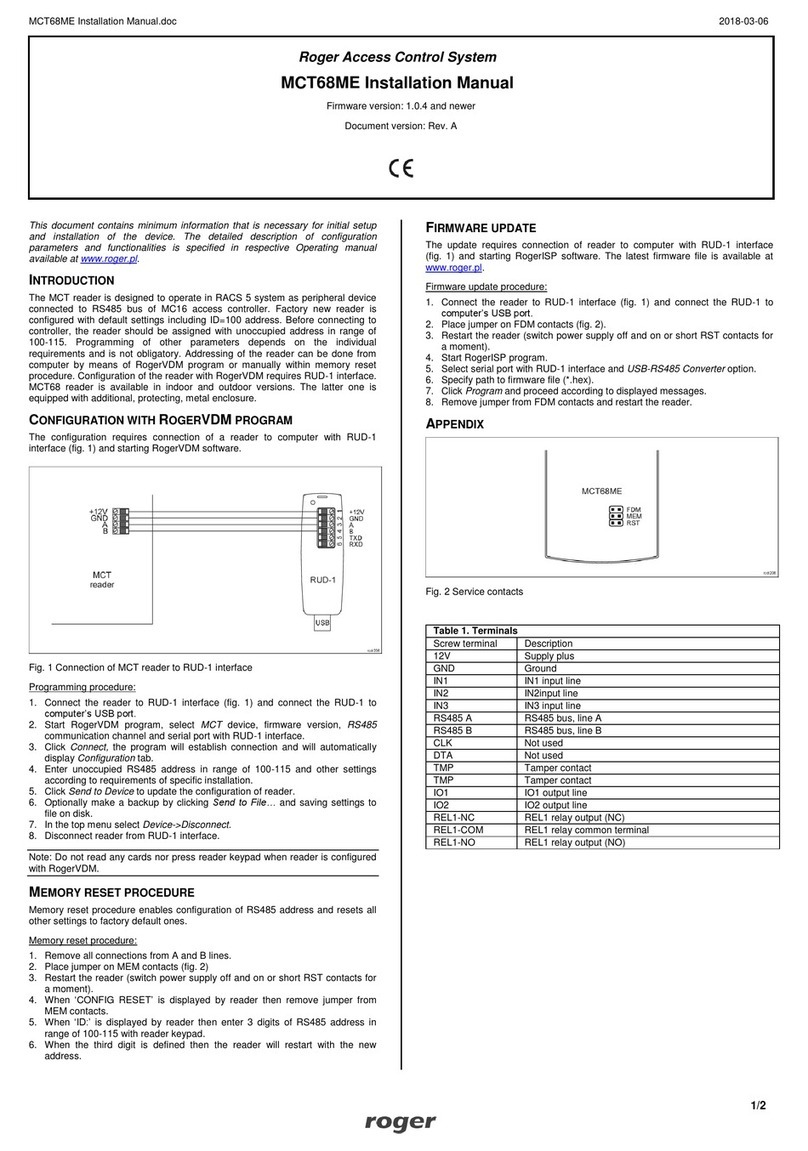
Roger
Roger MCT68ME User manual
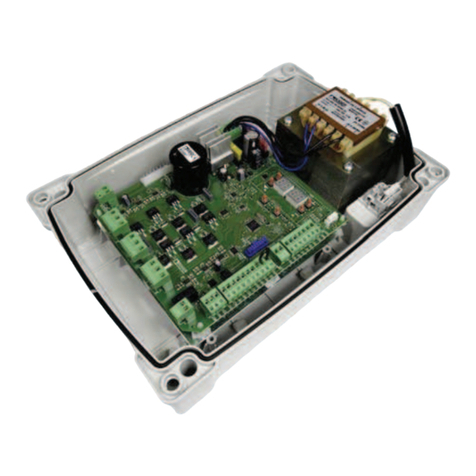
Roger
Roger EDGE1 Series Product manual
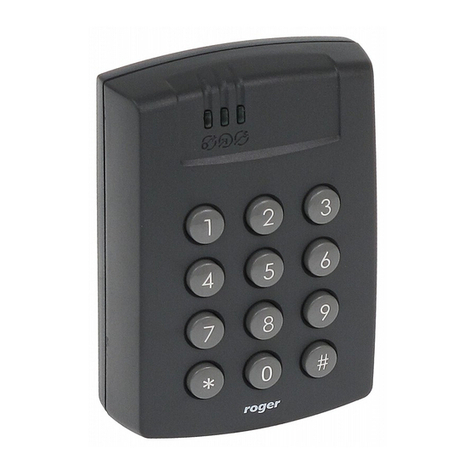
Roger
Roger PR612 User manual
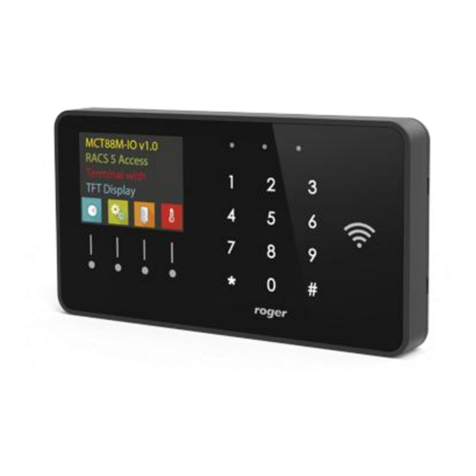
Roger
Roger MCT88M-IO User manual
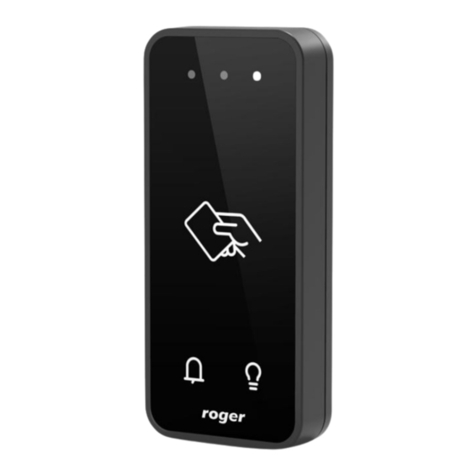
Roger
Roger MCT80M-BLE User manual
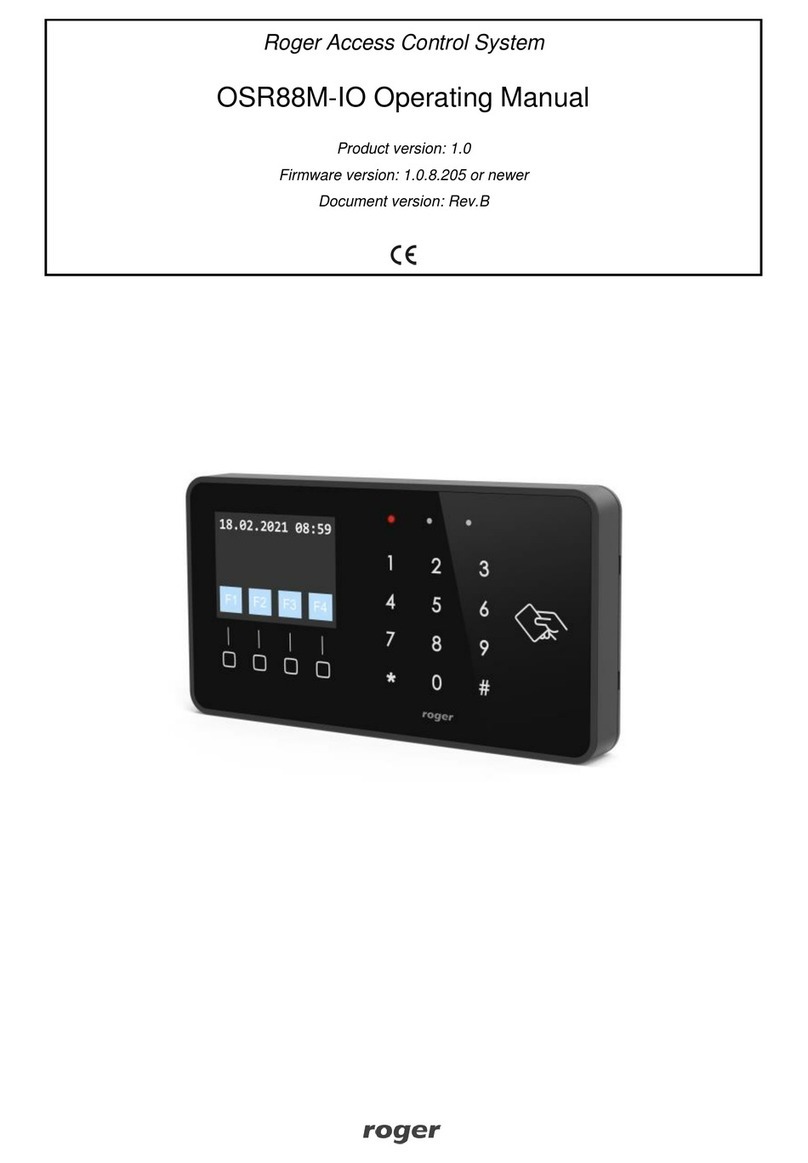
Roger
Roger OSR88M-IO User manual
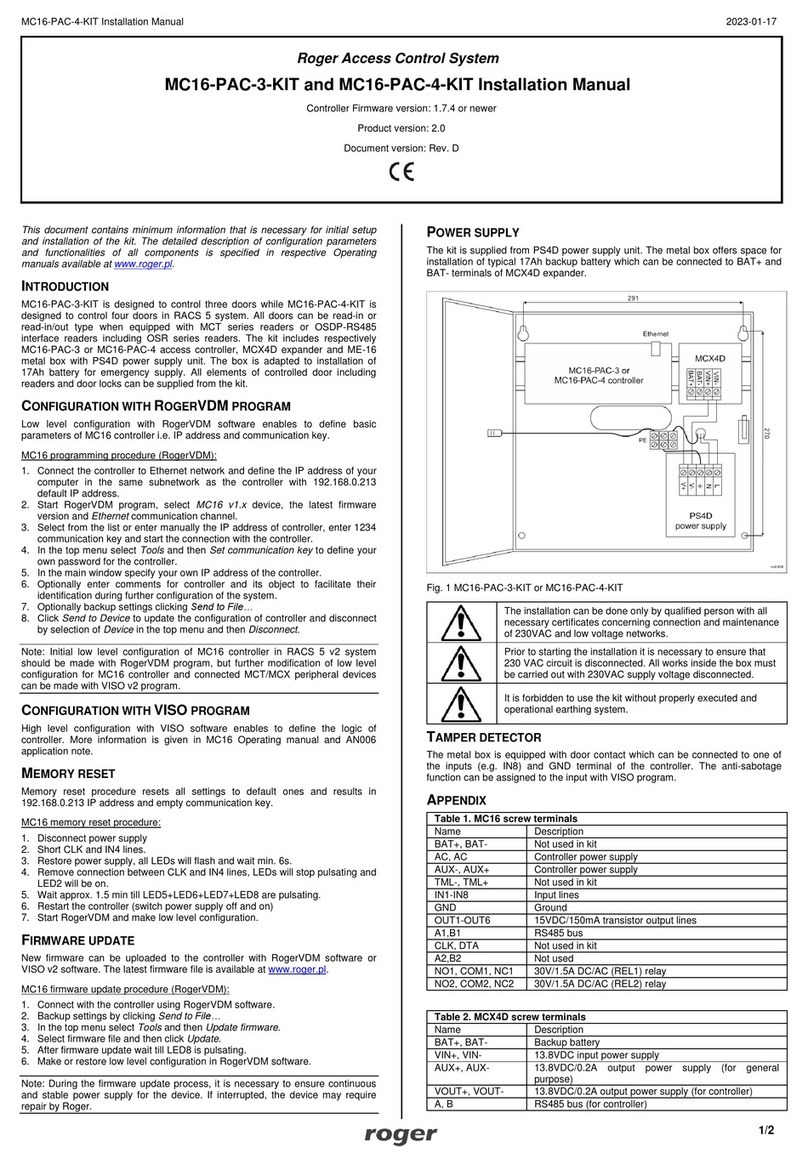
Roger
Roger MC16-PAC-3-KIT User manual
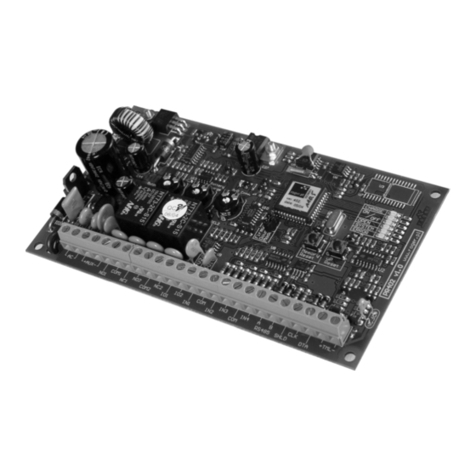
Roger
Roger PR402 User guide
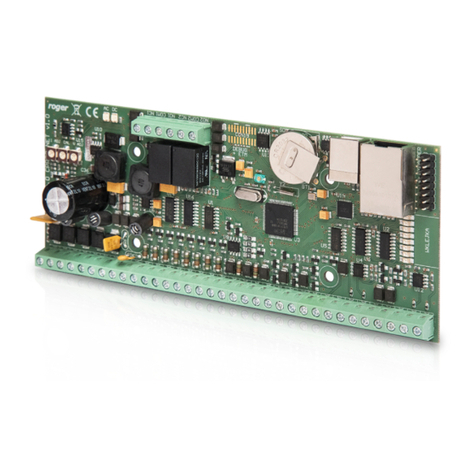
Roger
Roger MC16-SVC User manual
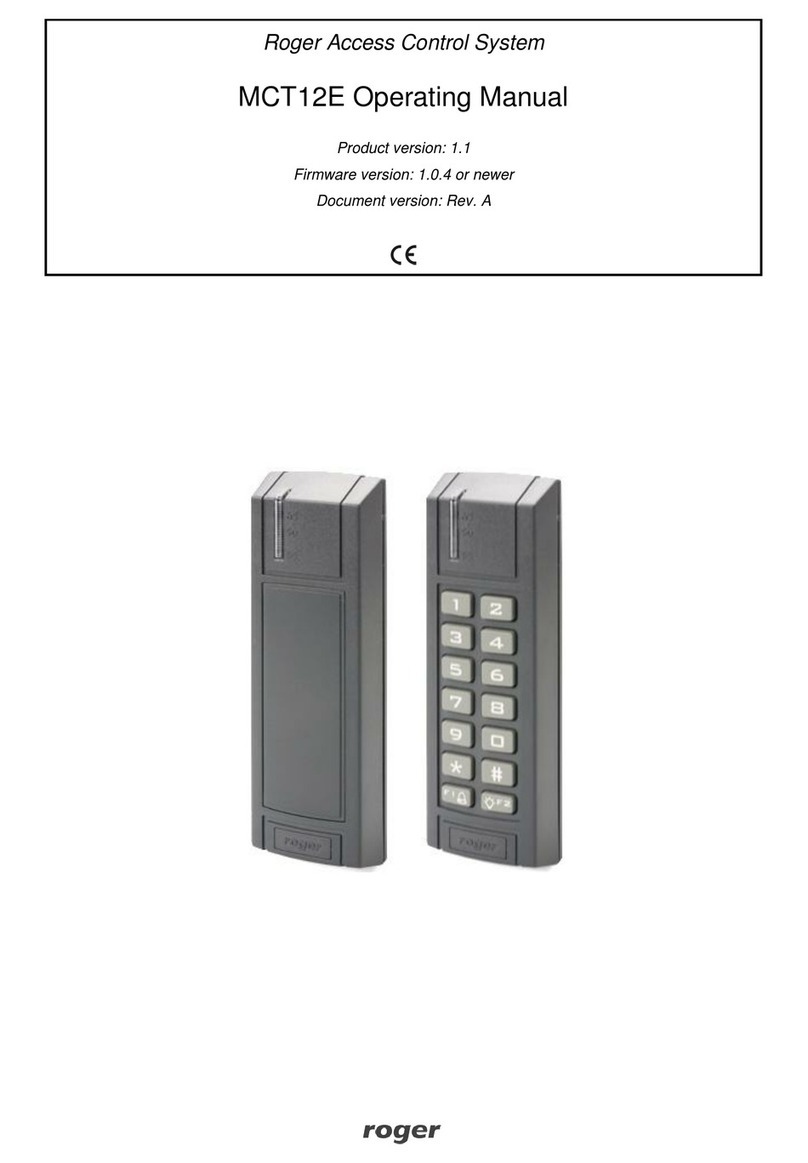
Roger
Roger MCT12E User manual
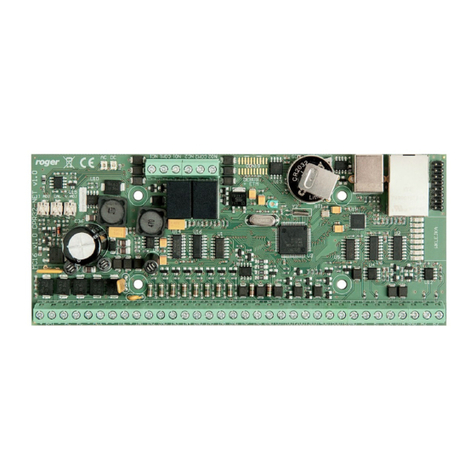
Roger
Roger MC16-PAC-16 User manual
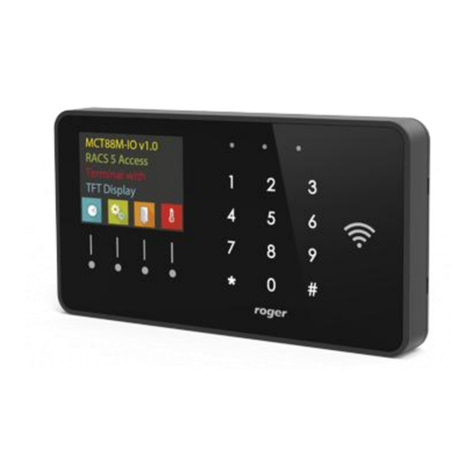
Roger
Roger MCT88M-IO User manual
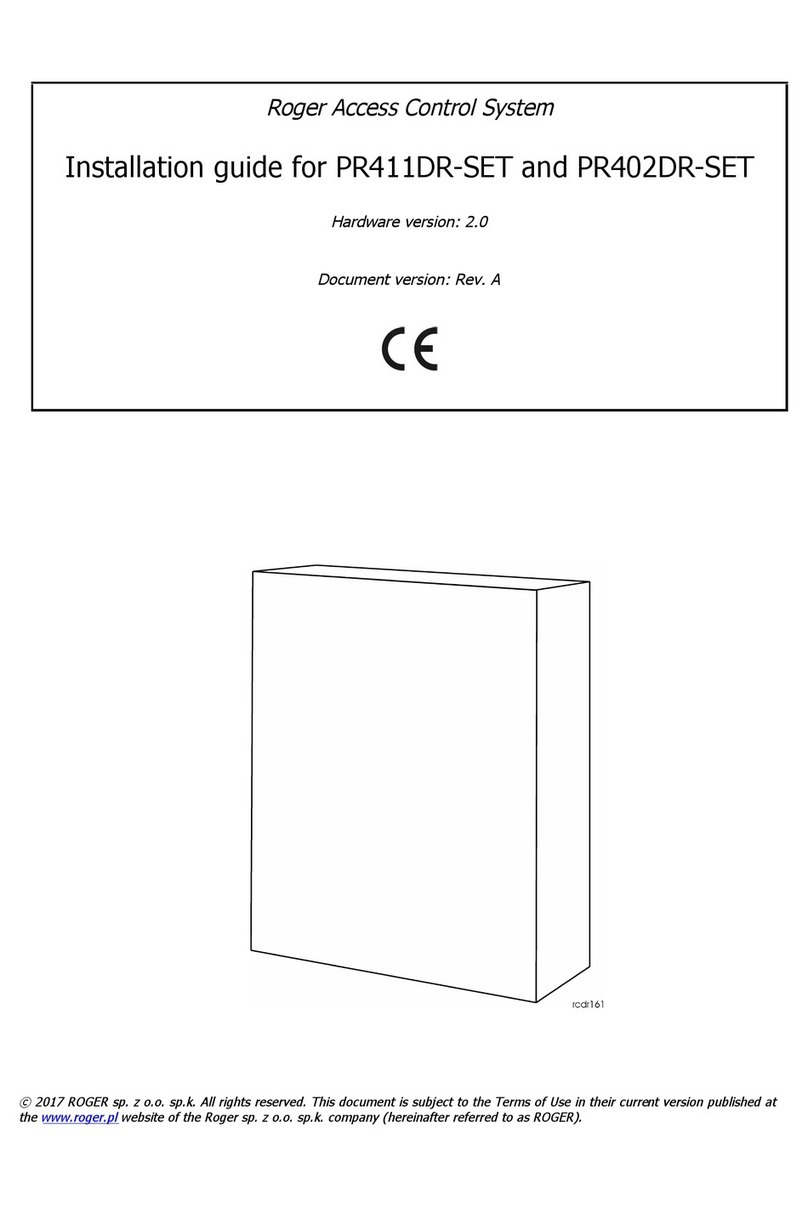
Roger
Roger PR411DR-SET User manual
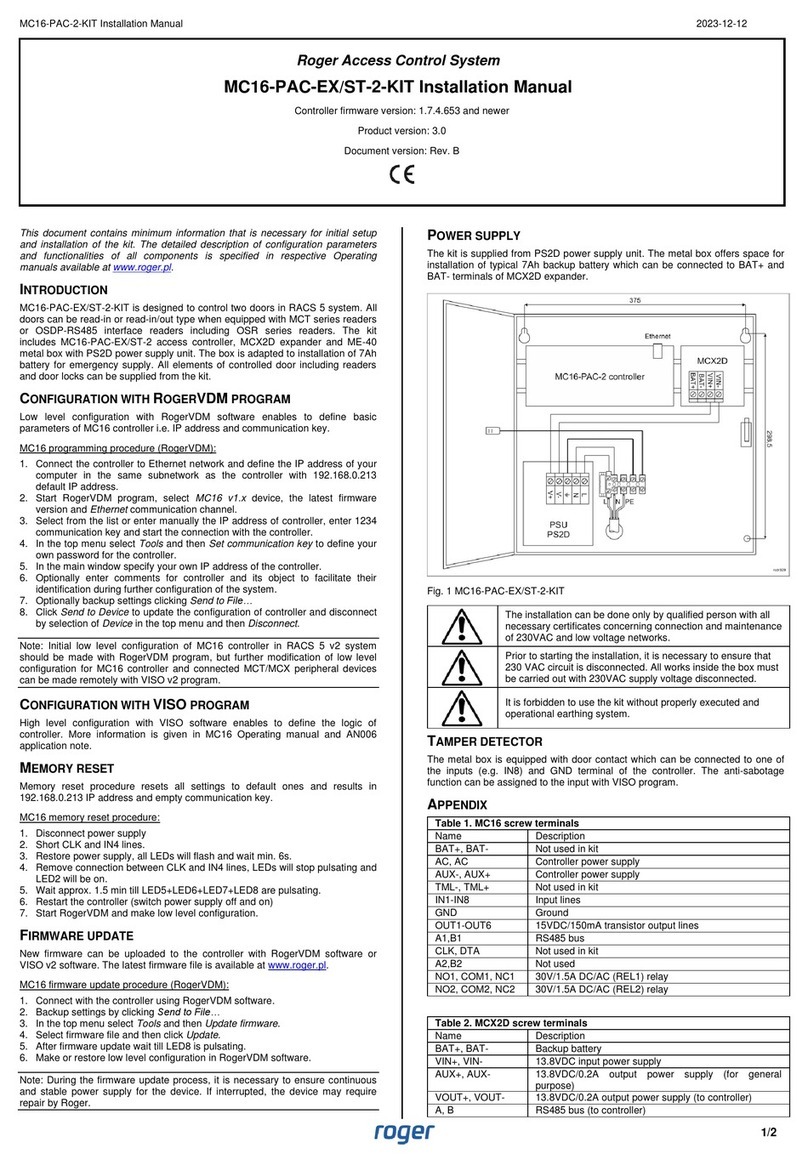
Roger
Roger MC16-PAC-EX/ST-2-KIT User manual
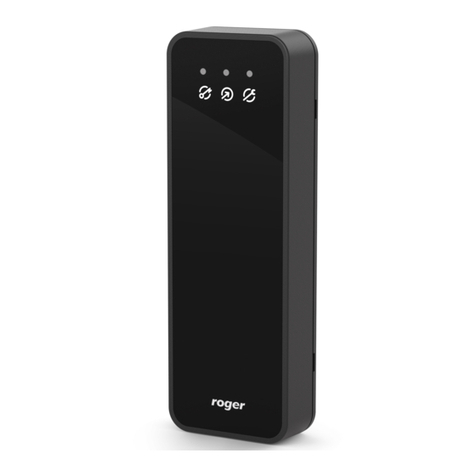
Roger
Roger PRT12MF-DES User manual
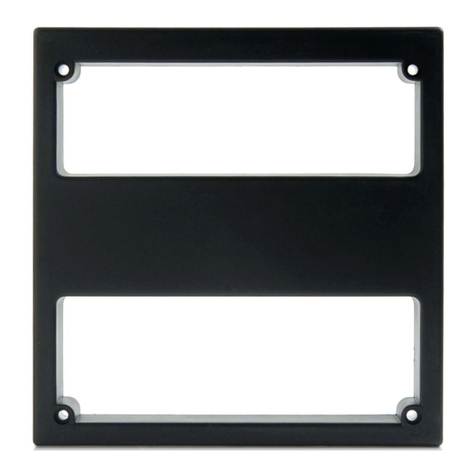
Roger
Roger LRT-1 User manual
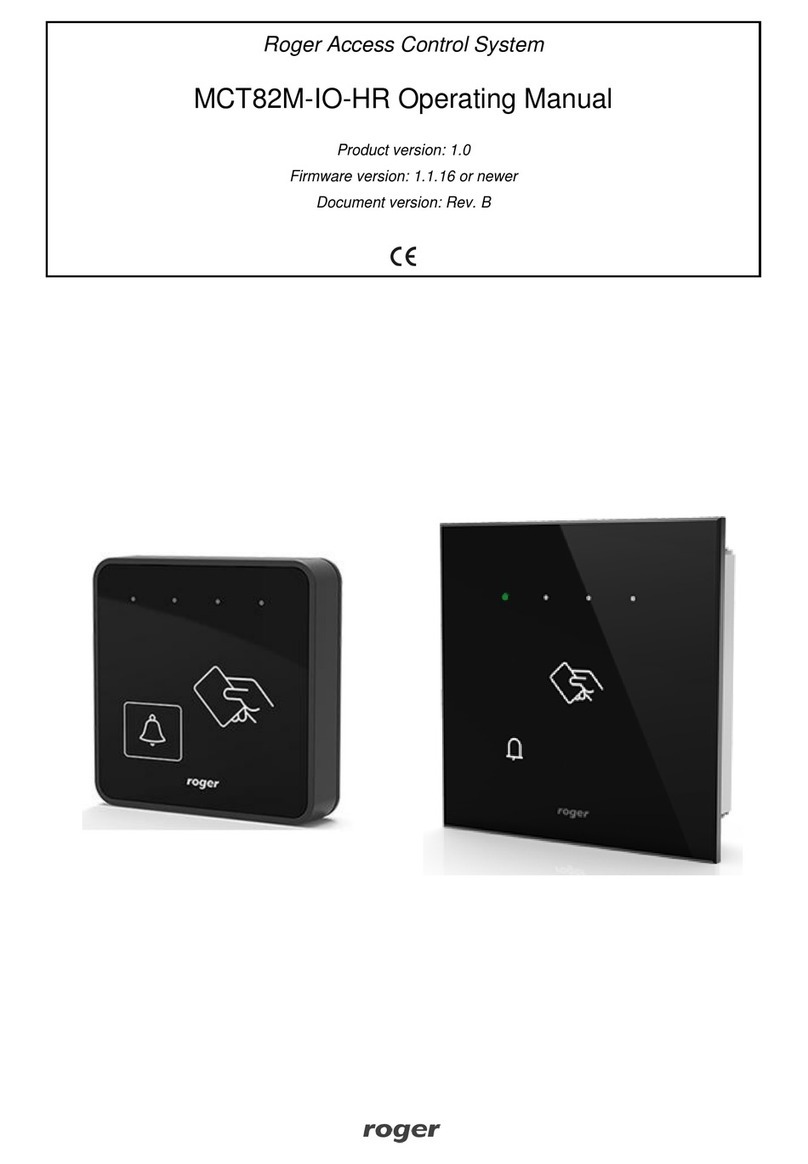
Roger
Roger MCT82M-IO-HR-F User manual
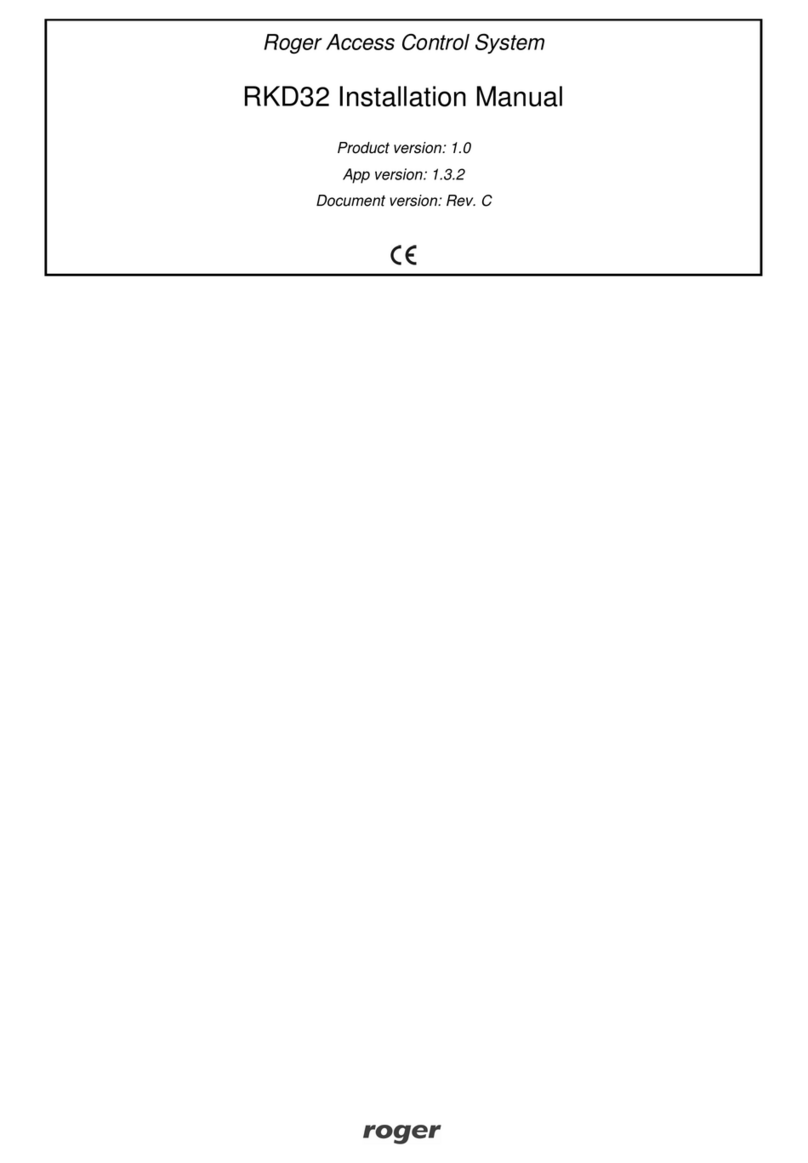
Roger
Roger RKD32 User manual
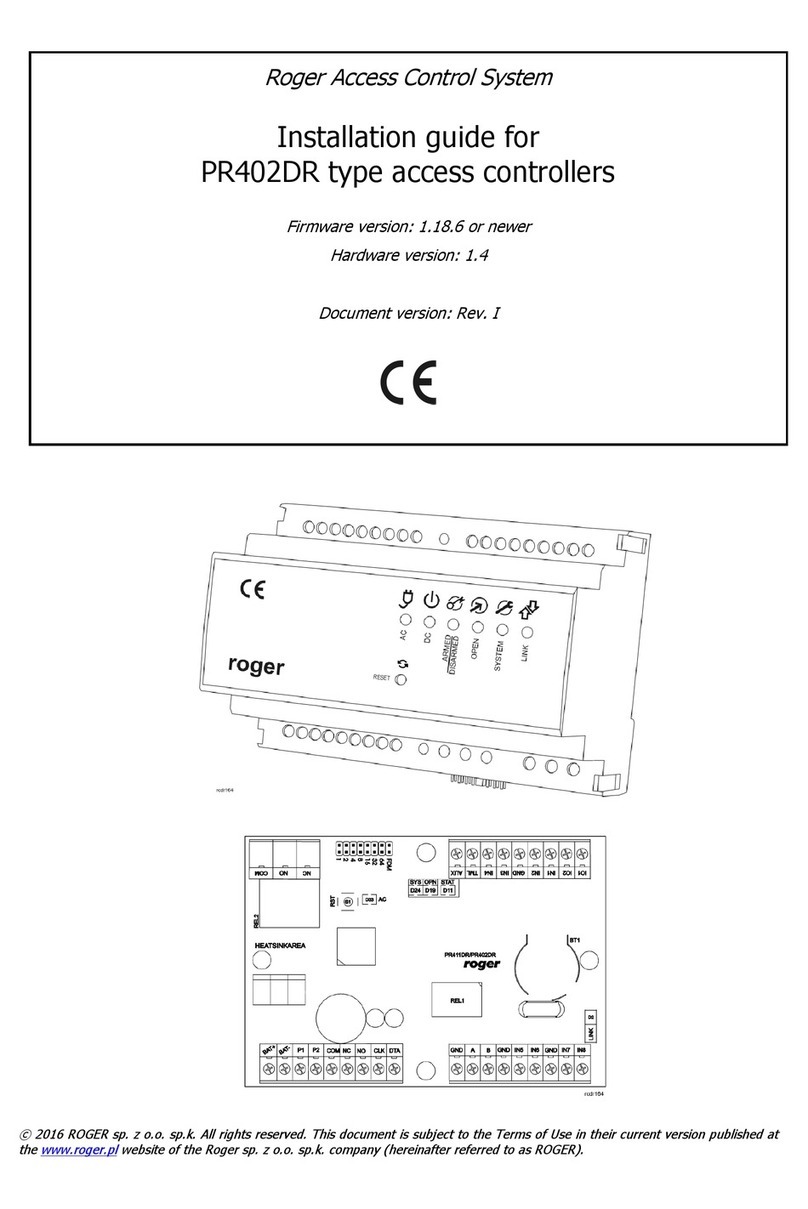
Roger
Roger PR402DR User manual
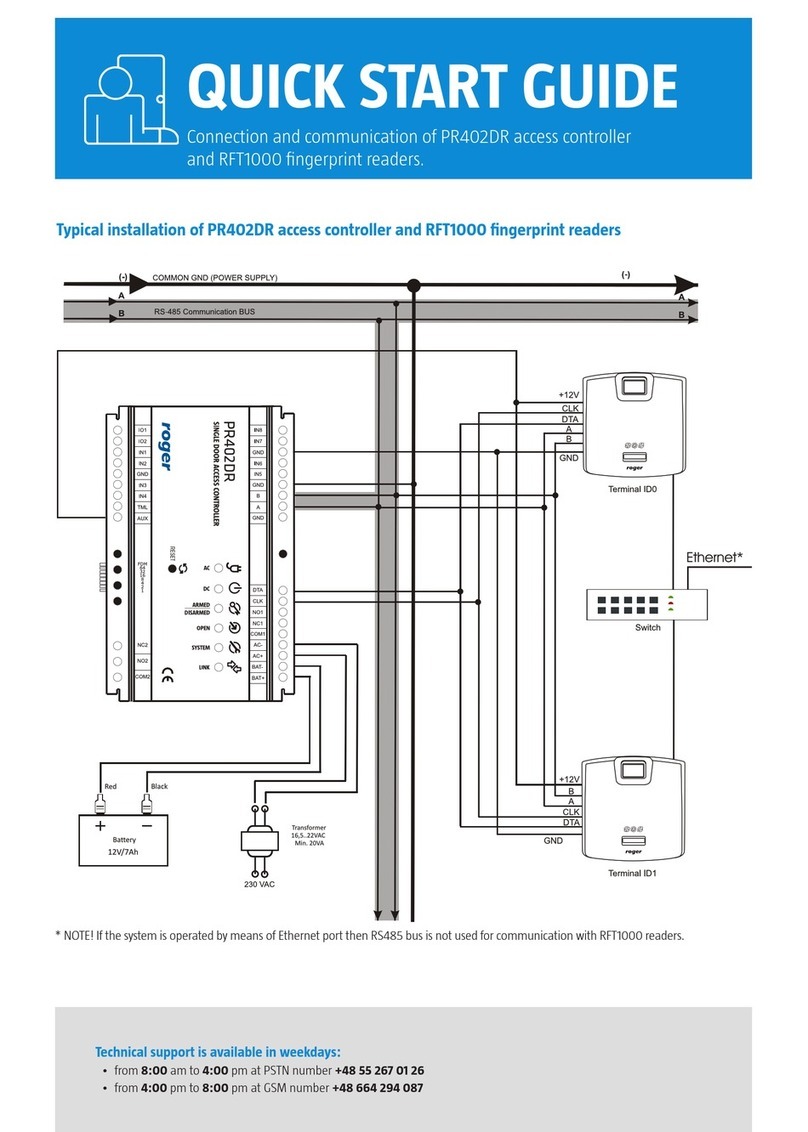
Roger
Roger PR402DR User manual