Texas Instruments TPS2390EVM User manual
















This manual suits for next models
1
Other Texas Instruments Control Unit manuals
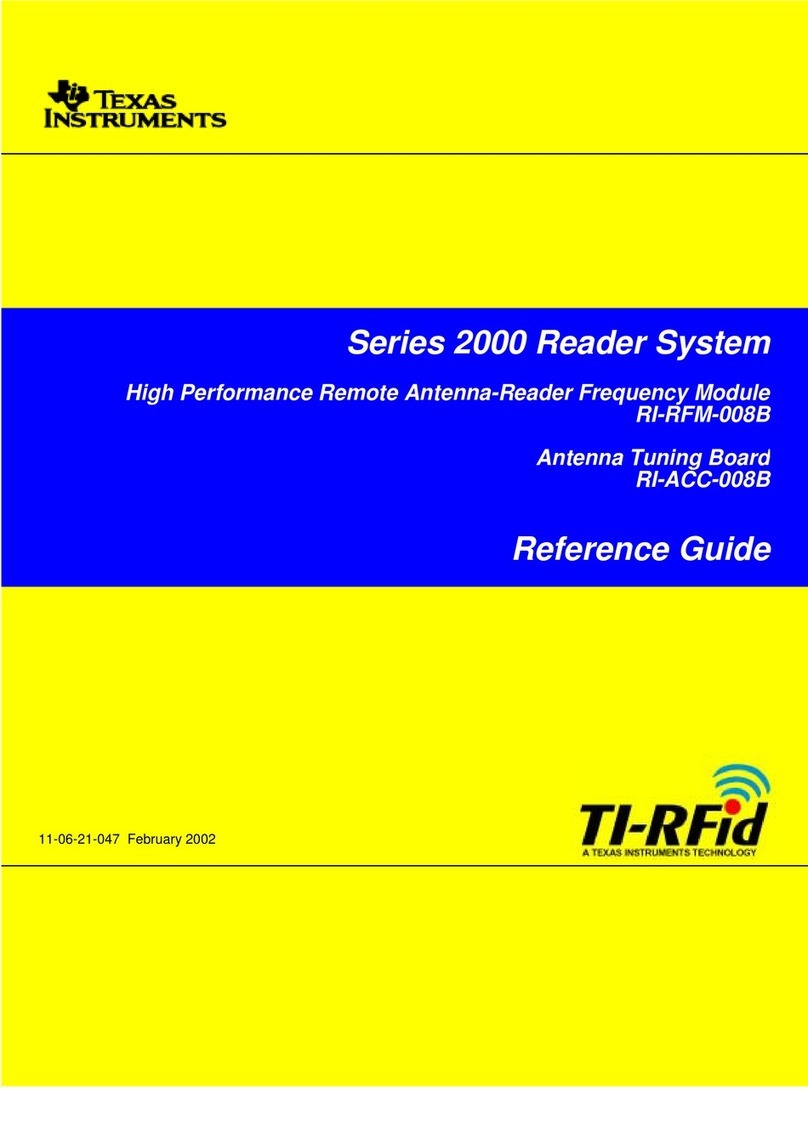
Texas Instruments
Texas Instruments 2000 series User manual
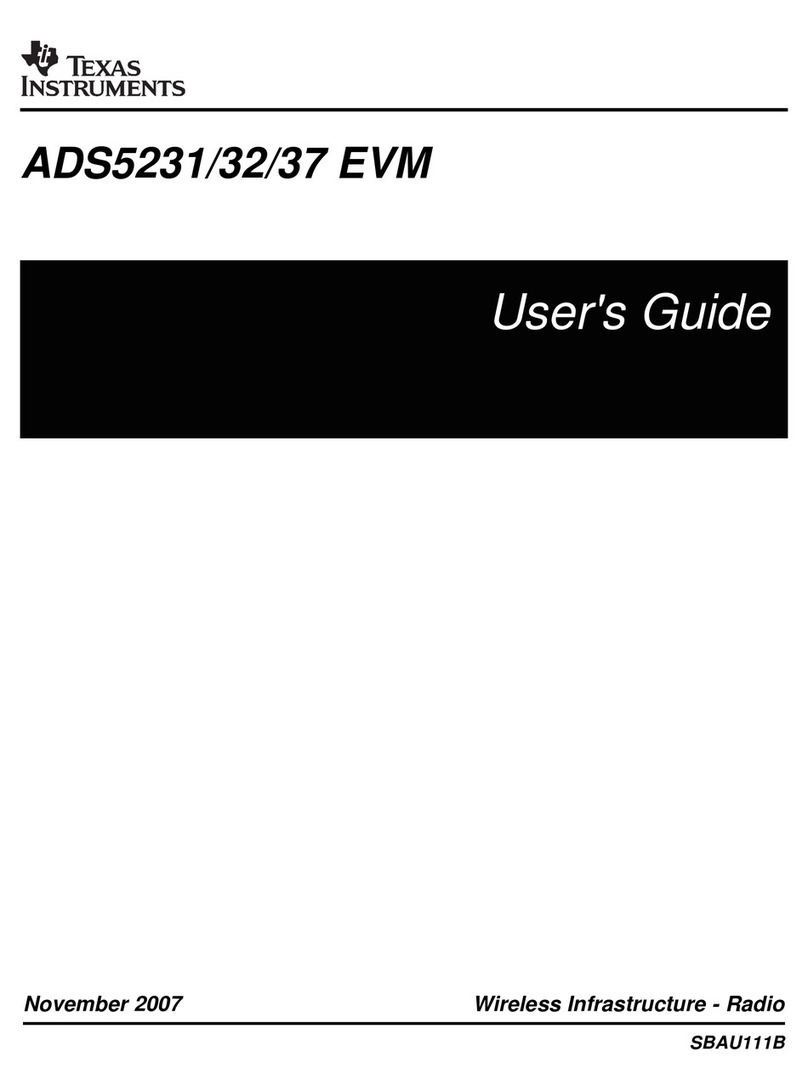
Texas Instruments
Texas Instruments ADS5237 EVM User manual
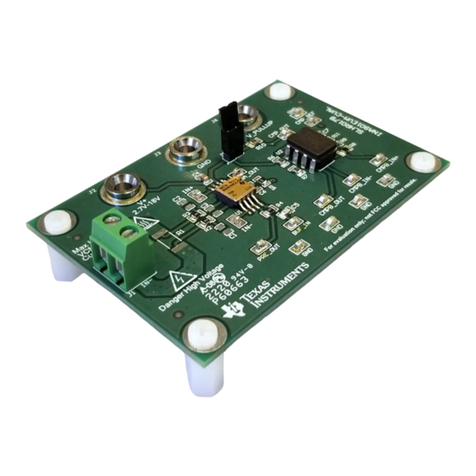
Texas Instruments
Texas Instruments INA901EVM-CVAL User manual
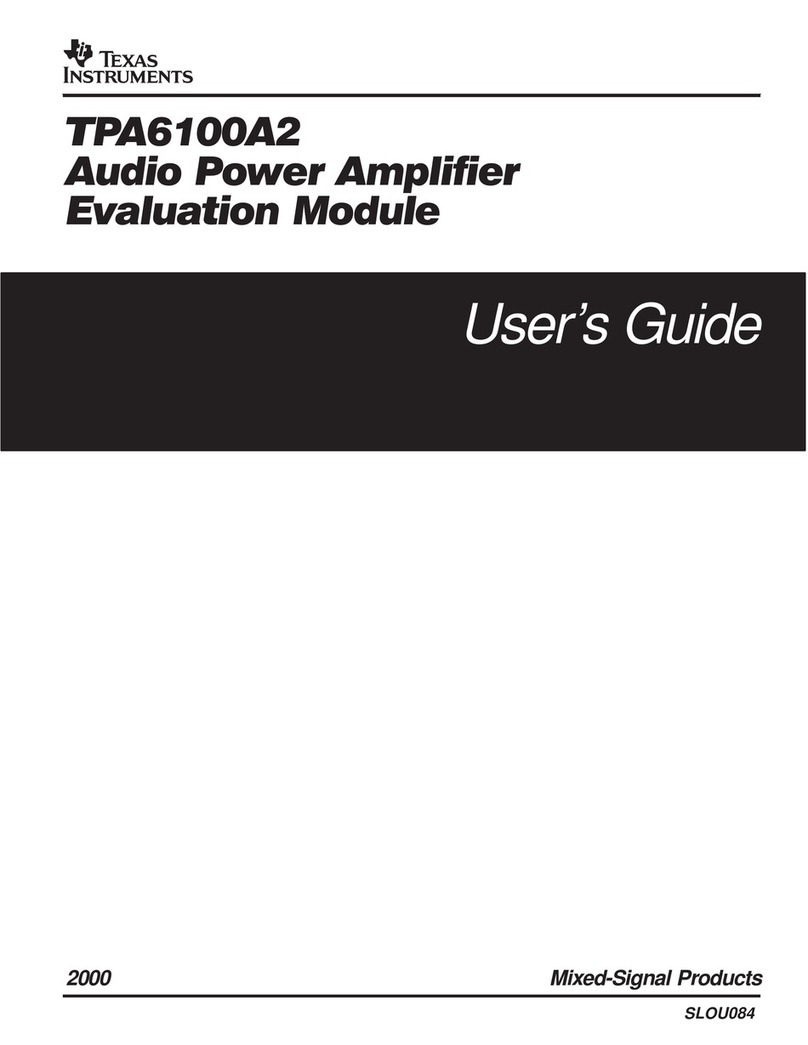
Texas Instruments
Texas Instruments TPA6100A2 User manual
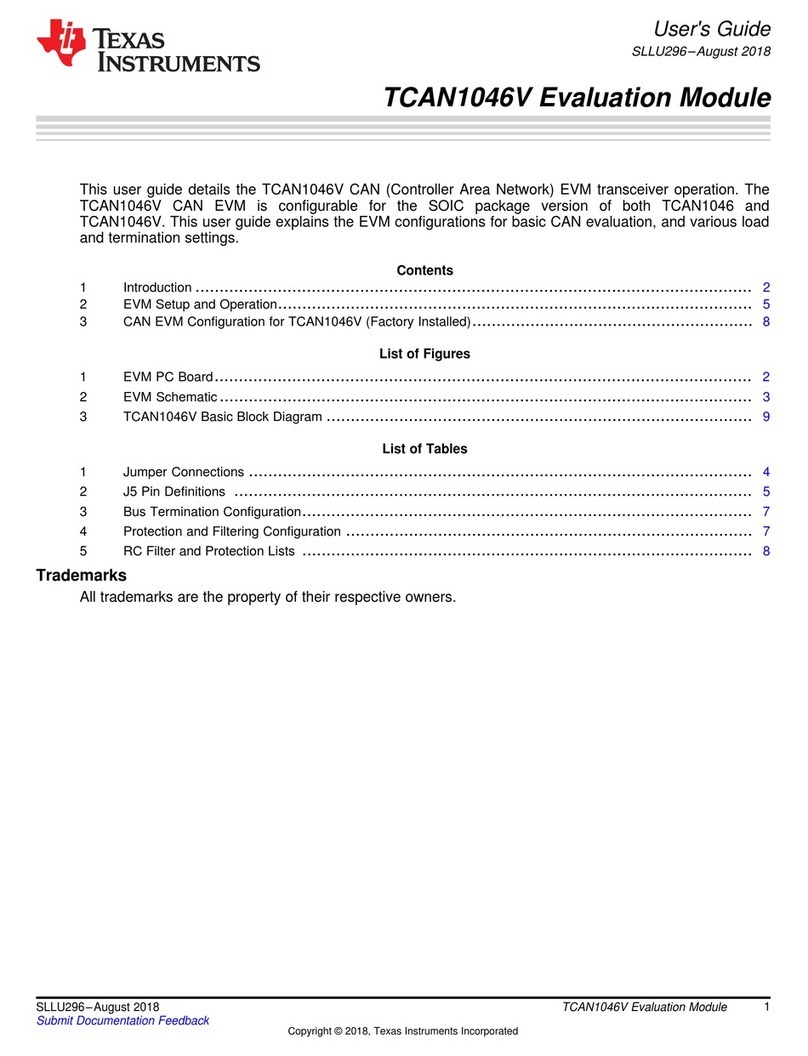
Texas Instruments
Texas Instruments TCAN1046V User manual
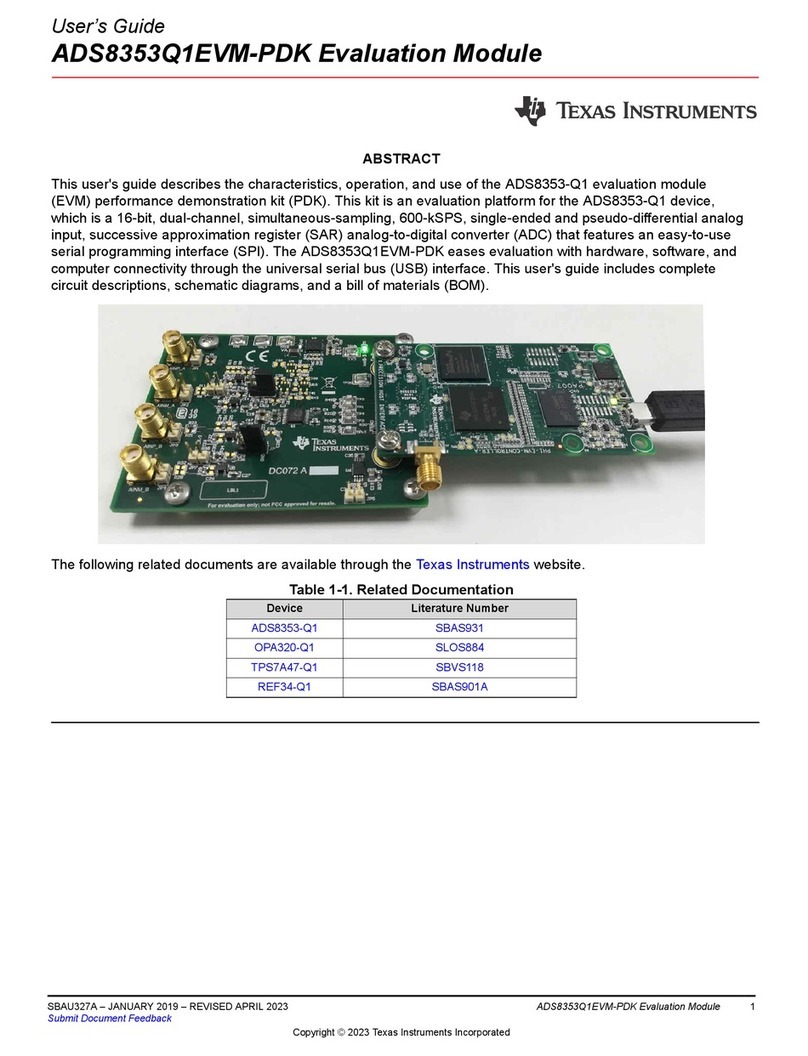
Texas Instruments
Texas Instruments ADS8353-Q1 User manual
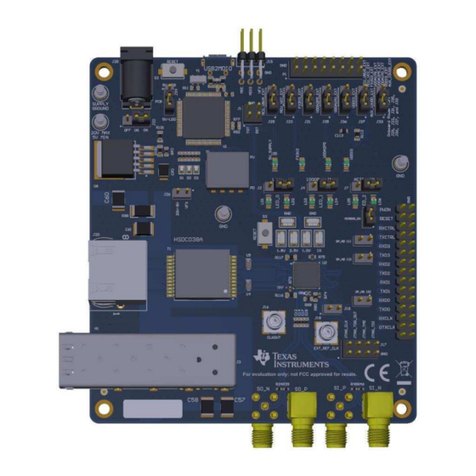
Texas Instruments
Texas Instruments DP83869EVM User manual
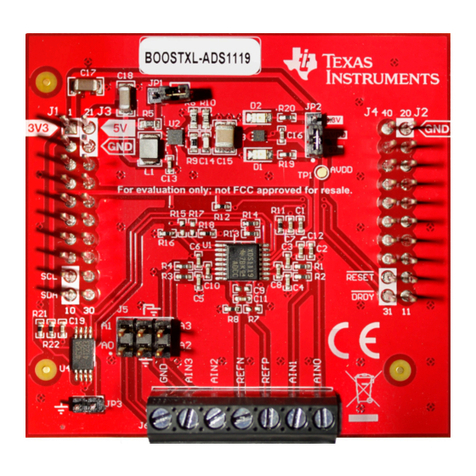
Texas Instruments
Texas Instruments BoosterPack BOOSTXL-ADS1119 User manual
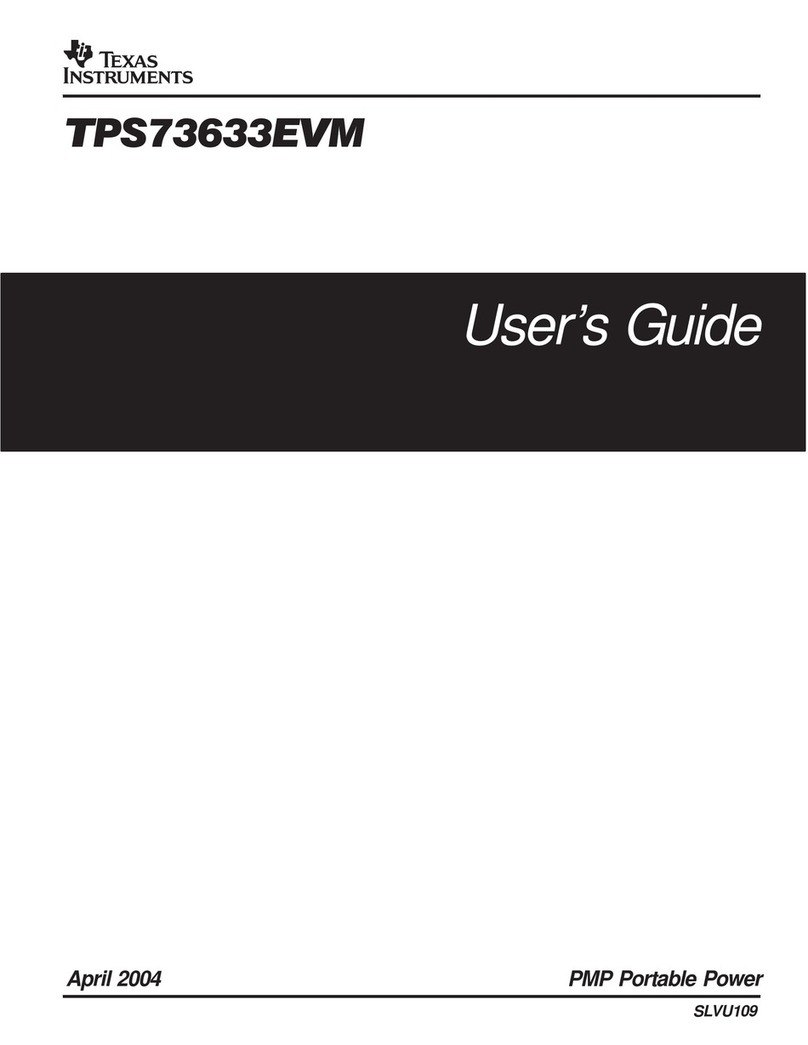
Texas Instruments
Texas Instruments TPS73633EVM User manual
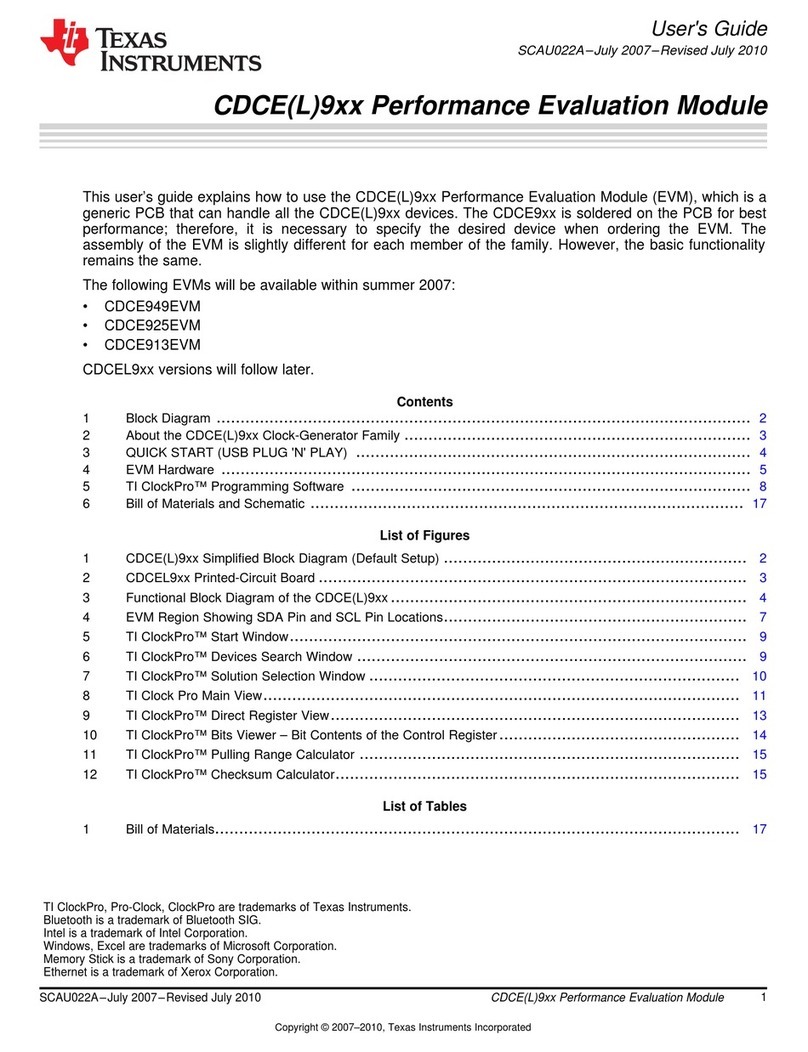
Texas Instruments
Texas Instruments CDCE 9 Series User manual
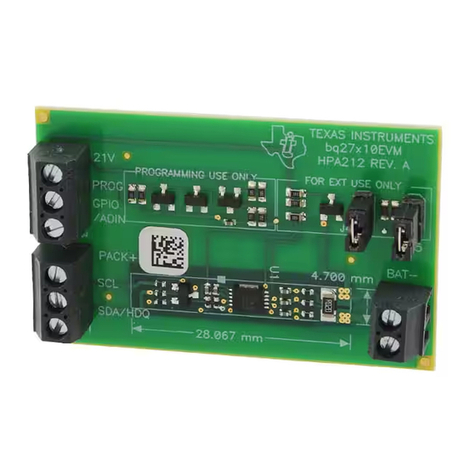
Texas Instruments
Texas Instruments bq27x10EVM User manual
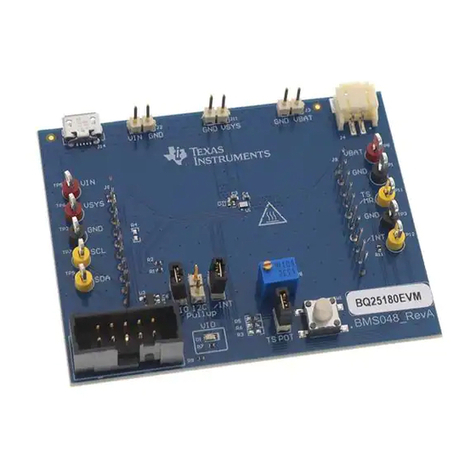
Texas Instruments
Texas Instruments BQ25180 User manual
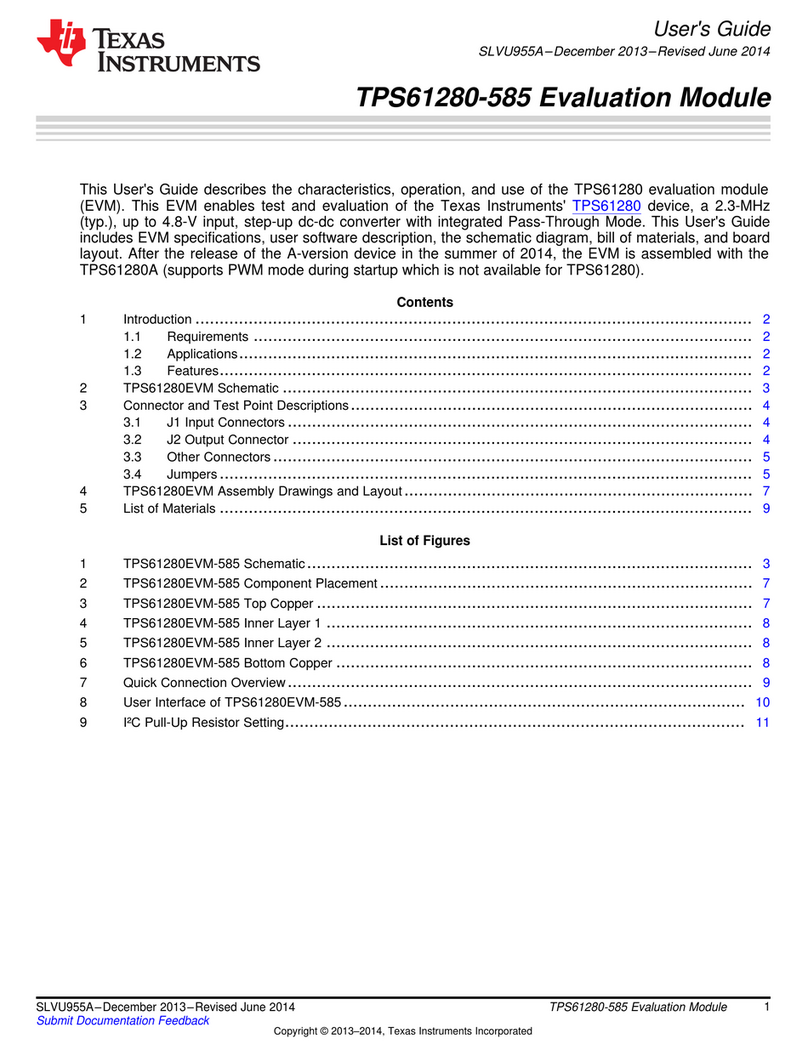
Texas Instruments
Texas Instruments TPS61280-585 User manual
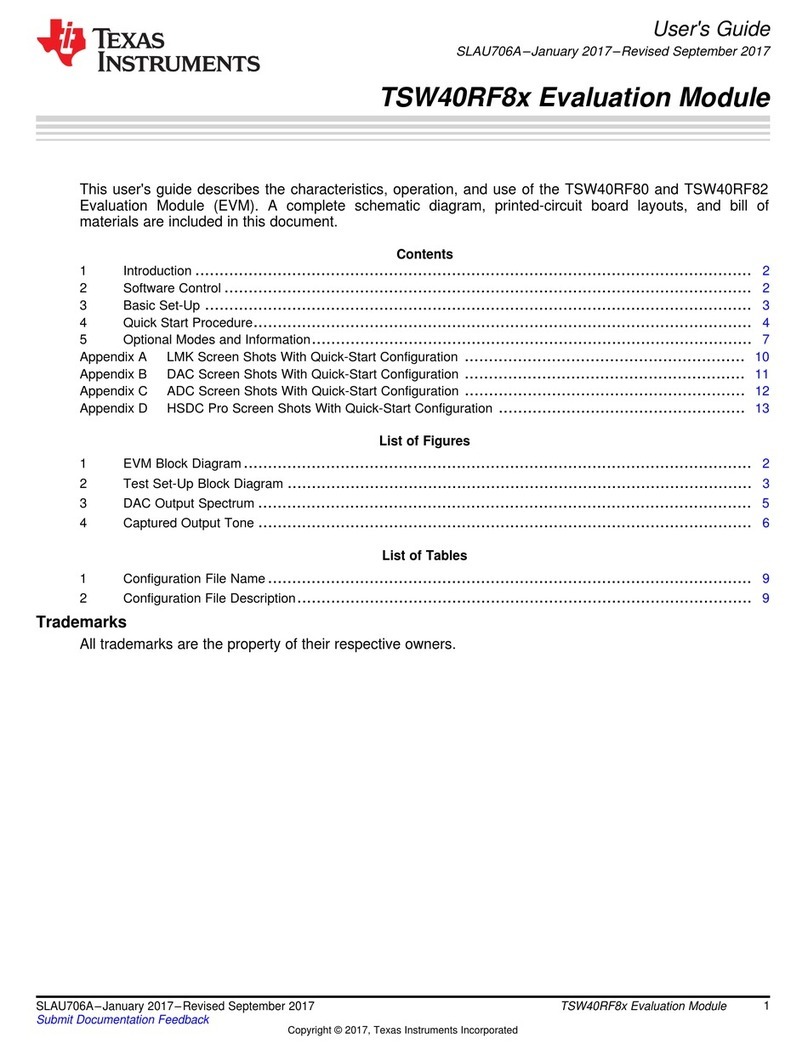
Texas Instruments
Texas Instruments TSW40RF8 Series User manual
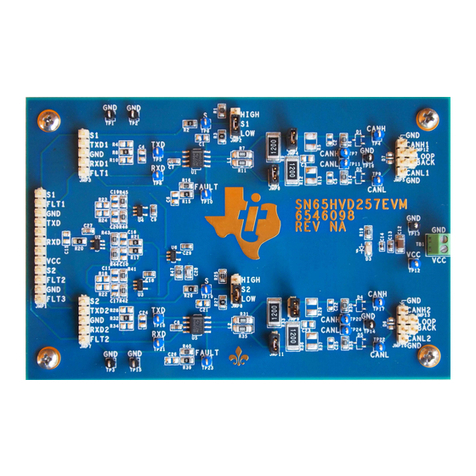
Texas Instruments
Texas Instruments SN65HVD257 User manual
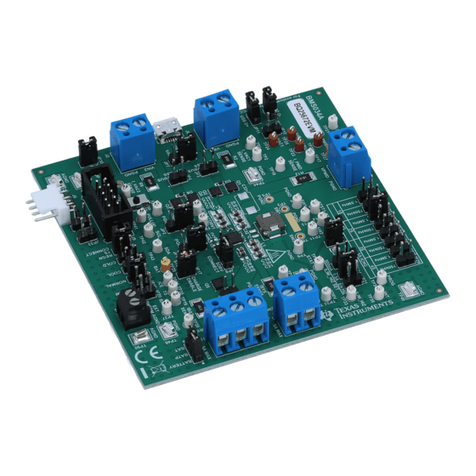
Texas Instruments
Texas Instruments BQ25672EVM User manual
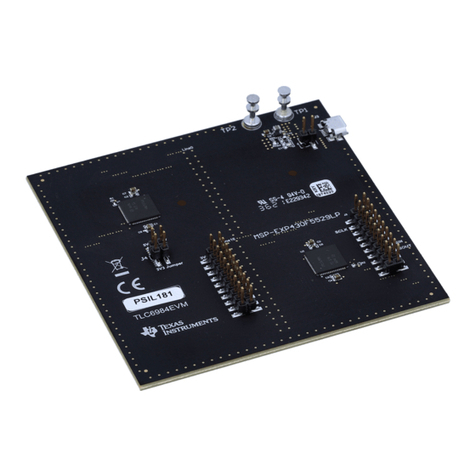
Texas Instruments
Texas Instruments TLC6984 User manual
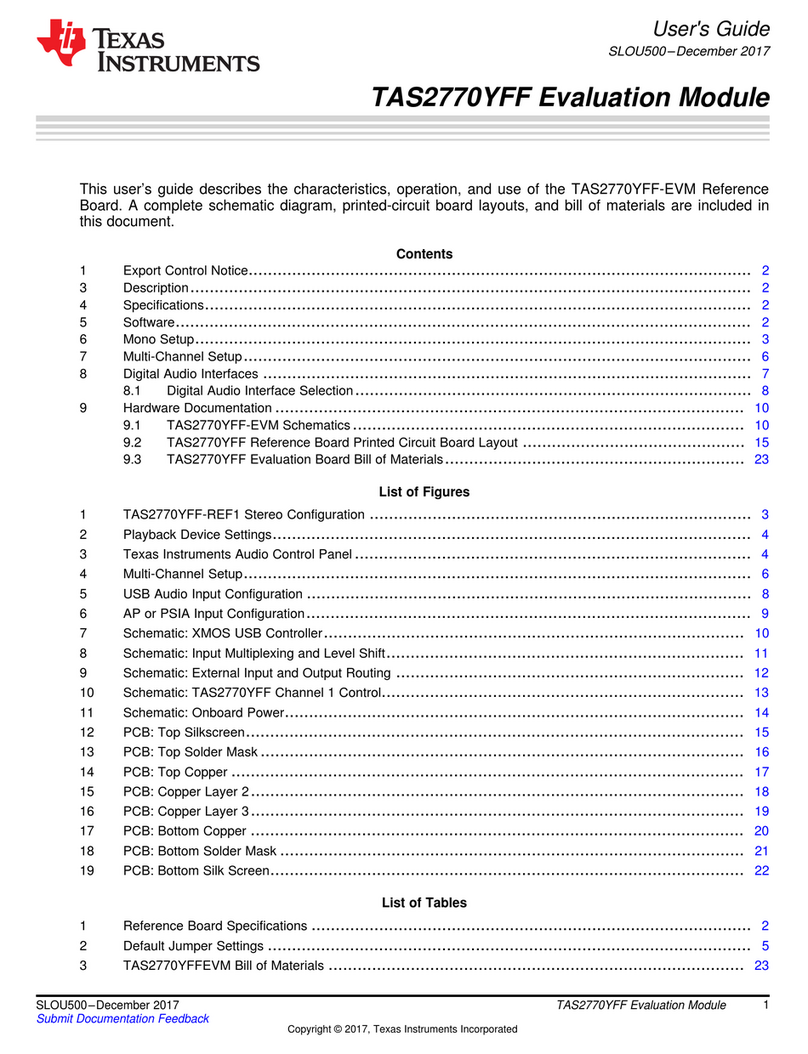
Texas Instruments
Texas Instruments TAS2770YFF User manual

Texas Instruments
Texas Instruments bq24165 User manual
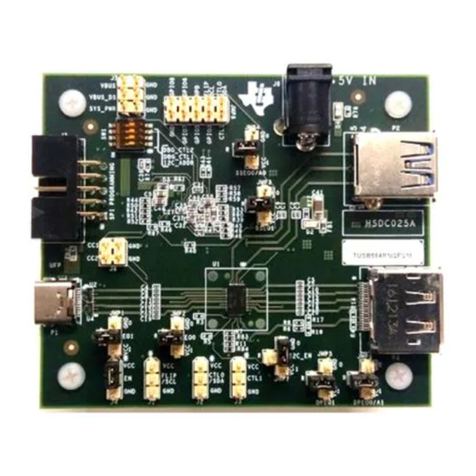
Texas Instruments
Texas Instruments TUSB564RNQ User manual
Popular Control Unit manuals by other brands

Supermicro
Supermicro SUPERO C9Z590-CG Quick reference guide
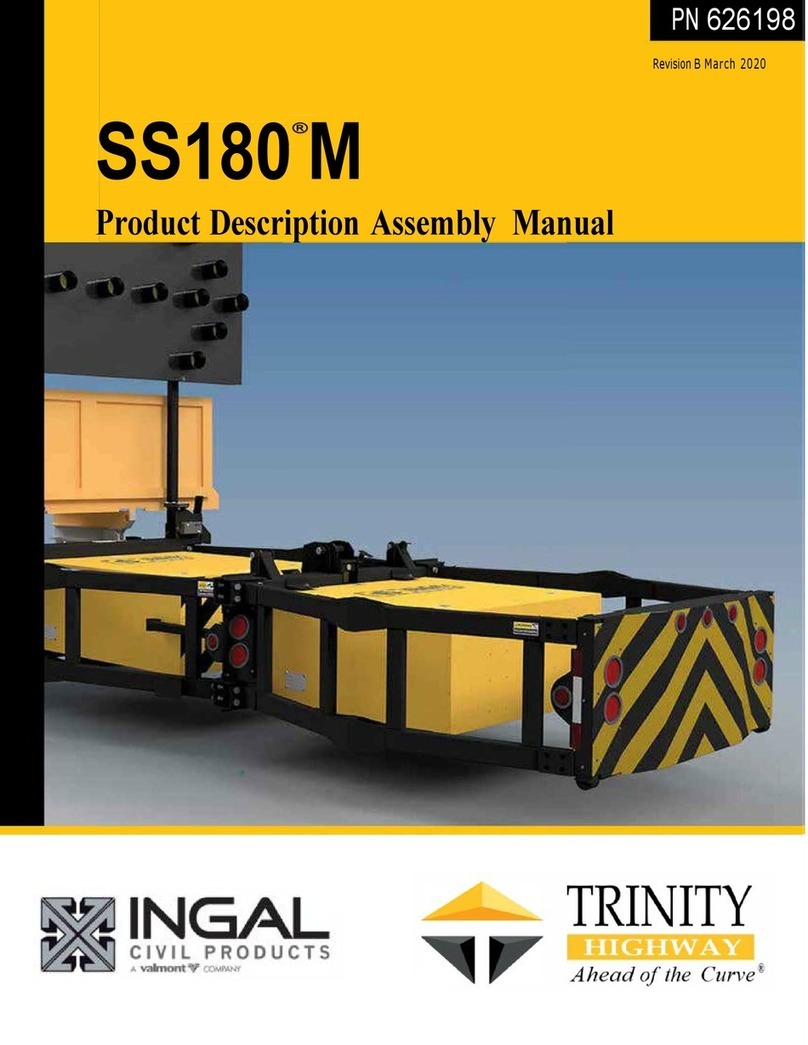
Trinity Highway
Trinity Highway INGAL SS180 M Assembly manual
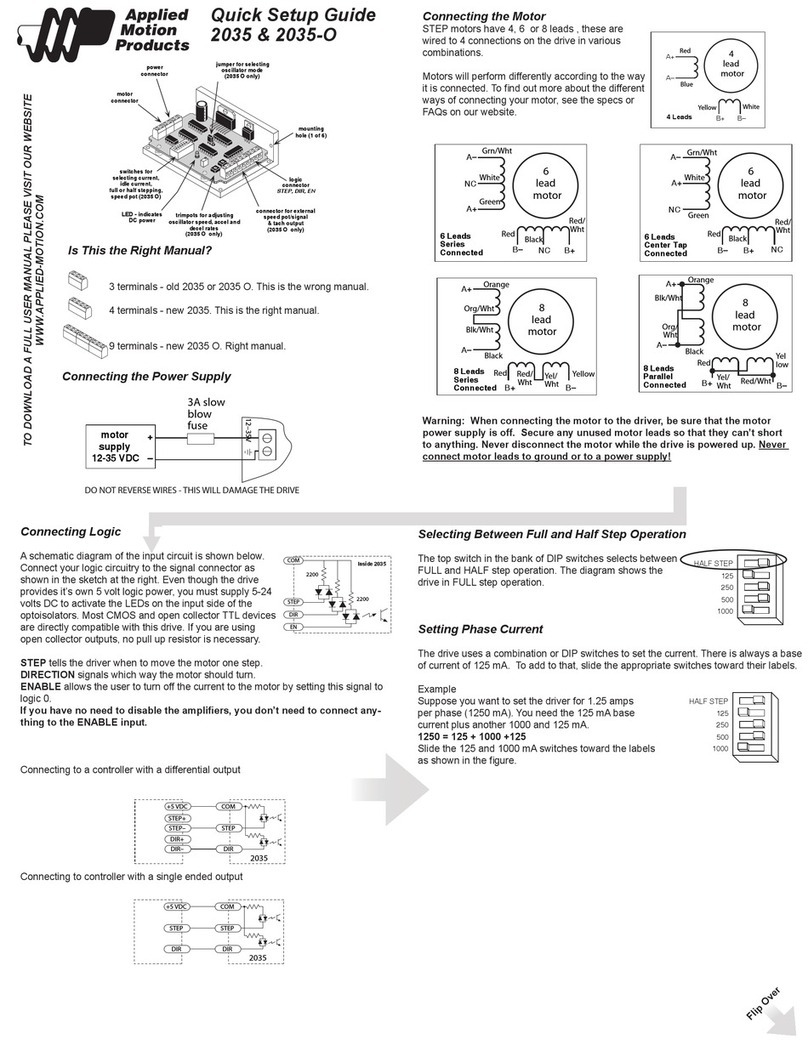
Applied Motion Products
Applied Motion Products 2035 Quick setup guide
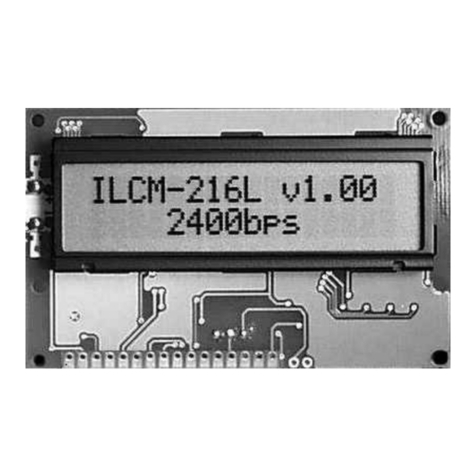
Scott Edwards Electronics
Scott Edwards Electronics ILM-216 user manual

Viessmann
Viessmann vitotronic 200-h operating instructions
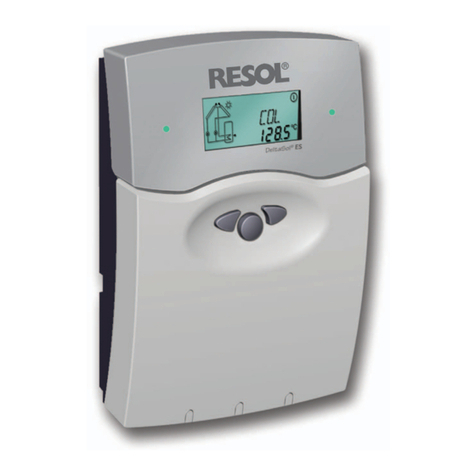
Resol
Resol DeltaSol ES manual
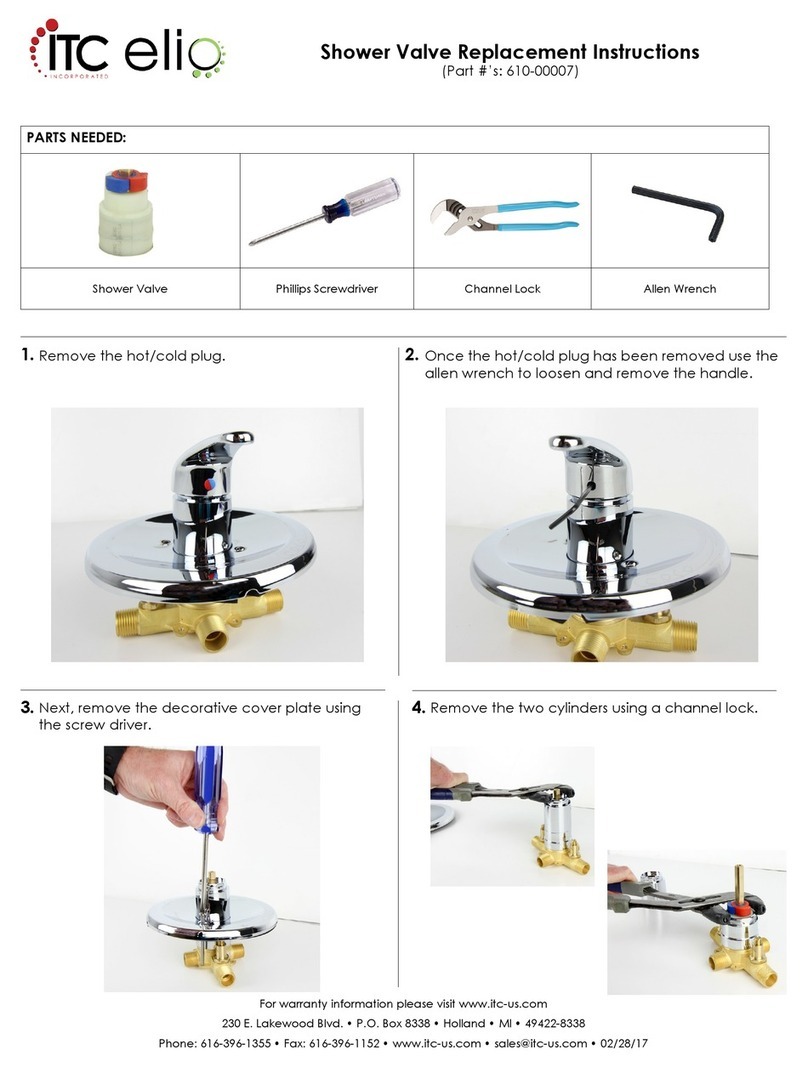
ITC
ITC Elio 610-00007 Replacement instructions
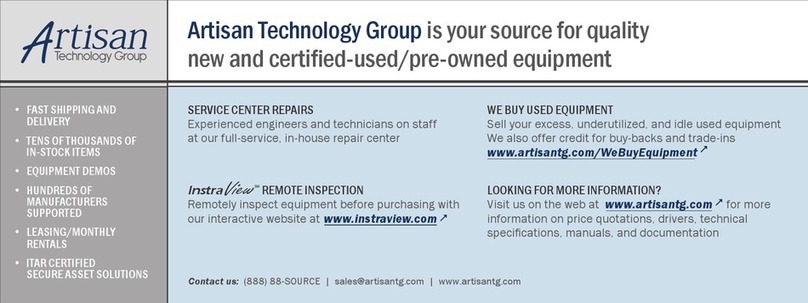
Xycom
Xycom XVME-956 Series manual
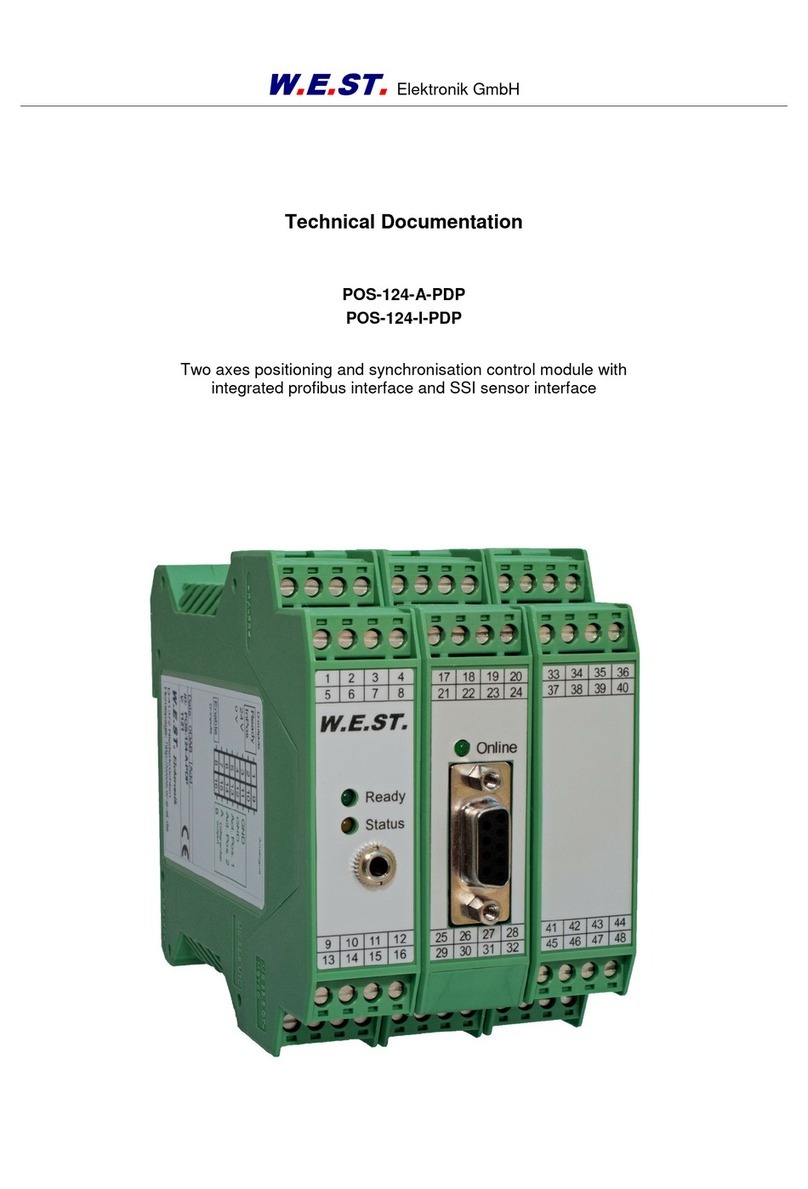
W.E.S.T. Elektronik
W.E.S.T. Elektronik POS-124-A-PDP Technical documentation
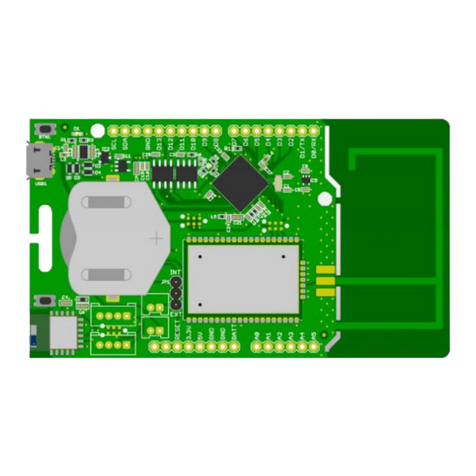
Microchip Technology
Microchip Technology ExpLoRer user guide
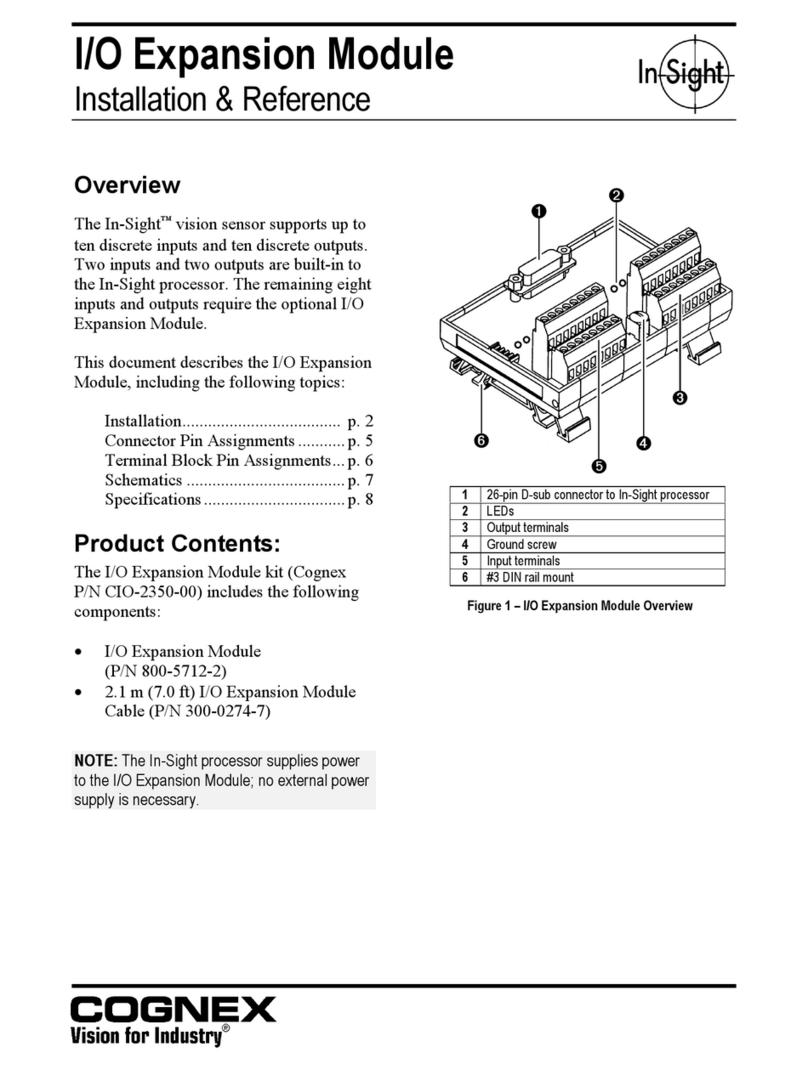
Cognex
Cognex In-Sight I/O Expansion Module INSTALLATION REFERENCE
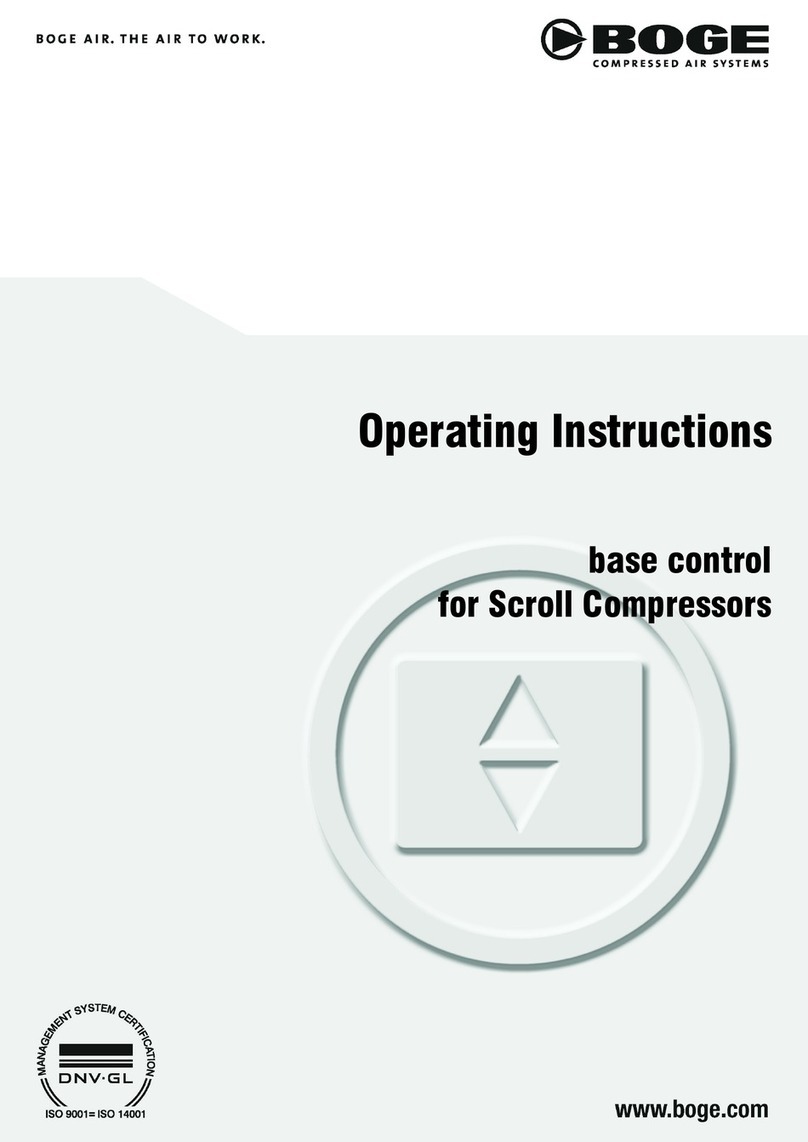
Boge
Boge base control operating instructions