TLV DR8-3P User manual

Manufacturer
Kakogawa, Japan
is approved by LRQA Ltd. to ISO 9001/14001
ISO 9001
ISO14001
Instruction Manual
Clean Steam Direct-Acting Pressure Reducing Valve
Featured Models: DR8-3P/DR8-3EP/DR8-6P/DR8-6EP
172-65613M-08
Publication date 8 November 2023
Copyright © 2023 TLV CO., LTD.

Table of Contents
Introduction ............................................................................................................................... 3
Safety Considerations .............................................................................................................. 4
Specifications ........................................................................................................................... 6
Acceptable Operating Range ................................................................................................... 7
Correct usage of the product .................................................................................................... 8
Configuration .......................................................................................................................... 11
Installation .............................................................................................................................. 13
Adjustment .............................................................................................................................. 16
Maintenance ........................................................................................................................... 17
Disassembly ........................................................................................................................... 18
Reassembly ............................................................................................................................ 23
Troubleshooting ...................................................................................................................... 24
TLV EXPRESS LIMITED WARRANTY ................................................................................... 27
Service ................................................................................................................................... 29
2

Introduction
Thank you for purchasing the TLV DR8 clean steam direct-acting pressure reducing valve.
This product has been thoroughly inspected before being shipped from the factory. When
the product is delivered, before doing anything else, check the specifications and external
appearance to make sure nothing is out of the ordinary. Also be sure to read this manual
carefully before use and follow the instructions to be sure of using the product properly.
The TLV DR8 clean steam direct-acting pressure reducing valve has been developed
especially for the food, beverage and pharmaceutical industries. This product has an angle
type structure with special polishing applied to internal parts to minimize areas for condensate
to accumulate, and prevent contamination inside the product. Additionally this product has a
structure that is easily disassembled to make internal cleaning convenient.
If detailed instructions for special order specifications or options not contained in this manual
are required, please contact TLV for full details.
This instruction manual is intended for use with the model(s) listed on the front cover.
It is needed not only for installation, but also for subsequent maintenance, disassembly/
reassembly and troubleshooting. Please keep it in a safe place for future reference.
3

Safety Considerations
• Read this section carefully before use and be sure to follow the instructions.
• Installation, inspection, maintenance, repairs, disassembly, adjustment and valve opening/
closing should be carried out only by trained maintenance personnel.
• The precautions listed in this manual are designed to ensure safety and prevent equipment
damage and personal injury. For situations that may occur as a result of erroneous handling,
three different types of cautionary items are used to indicate the degree of urgency and the
scale of potential damage and danger: DANGER, WARNING and CAUTION.
• The three types of cautionary items above are very important for safety: be sure to observe
all of them as they relate to installation, use, maintenance and repair. Furthermore, TLV
accepts no responsibility for any accidents or damage occurring as a result of failure to
observe these precautions.
Cautionary items and definitions
Danger
Indicates an urgent situation which poses a threat of death or serious injury
Warning
Indicates that there is a potential threat of death or serious injury
Caution
Indicates that there is a possibility of injury or equipment/product damage
Safety considerations for the product
Caution
Install properly and DO NOT use this product outside the recommended operating
pressure, temperature and other specification ranges. Improper use may result in such
hazards as damage to the product or malfunctions that may lead to serious accidents. Local
regulations may restrict the use of this product to below the conditions quoted.
Caution
Take measures to prevent people from coming into direct contact with product outlets.
Failure to do so may result in burns or other injury from the discharge of fluids.
Caution
When disassembling or removing the product, wait until the internal pressure equals
atmospheric pressure and the surface of the product has cooled to room temperature.
Disassembling or removing the product when it is hot or under pressure may lead to discharge of
fluids, causing burns, other injuries or damage.
Caution
Be sure to use only the recommended components when repairing the product, and NEVER
attempt to modify the product in any way. Failure to observe these precautions may result in
damage to the product and burns or other injury due to malfunction or the discharge of fluids.
Caution
Use only under conditions in which no freeze-up will occur. Freezing may damage the
product, leading to fluid discharge, which may cause burns or other injury.
4

Caution
Use only under conditions in which no water hammer will occur. The impact of water hammer
may damage the product, leading to fluid discharge, which may cause burns or other injury.
5

Specifications
Caution
Install properly and DO NOT use this product outside the recommended operating
pressure, temperature and other specification ranges. Improper use may result in such
hazards as damage to the product or malfunctions that may lead to serious accidents. Local
regulations may restrict the use of this product to below the conditions quoted.
Use only under conditions in which no freeze-up will occur. Freezing may damage the
product, leading to fluid discharge, which may cause burns or other injury.
Refer to the indications on the spring housing for detailed specifications.
A
H
G
E
F
I
D
B
C
J
K
A Model
B Nominal Diameter
C Maximum Allowable Pressure (PMA)/Maximum Allowable Temperature (TMA) 01
D Maximum Operating Pressure (PMO)/Maximum Operating Temperature (TMO)
E Production Lot No.
F Connection Standard
G CNo. 02
H Inner Diameter
I Connection Standard No.
J Primary Pressure Range
K Secondary Pressure Adjustable Range
01Maximum allowable pressure (PMA) and maximum allowable temperature (TMA) are PRESSURE
SHELL DESIGN CONDITIONS, NOT OPERATING CONDITIONS.
02CNo. (Charge/Mill No.) is displayed for products with options. This item is omitted when there are no
options.
6

Acceptable Operating Range
Model DR8-3P/DR8-3EP DR8-6P/DR8-6EP
Primary Pressure Range 0.2 to 0.4 MPaG 0.4 to 0.8 MPaG
Adjustable Pressure Range 0.018 to 0.3 MPaG 0.27 to 0.6 MPaG
Secondary pressure must not exceed 75% of primary pressure
Minimum Adjustable Flow
Rate Steam: 20 kg/h or more
7

Correct usage of the product
Caution
Install properly and DO NOT use this product outside the recommended operating
pressure, temperature and other specification ranges. Improper use may result in such
hazards as damage to the product or malfunctions that may lead to serious accidents. Local
regulations may restrict the use of this product to below the conditions quoted.
1. The product should be operated only within its specifications.
2. Installing an ON/OFF valve (solenoid valve or motorized valve)
Motorized
Valve
If an on-off valve is required to stop supply of steam or air to the equipment, install
it at the inlet side of the product. If a solenoid valve is installed at the outlet of the
product, it will cause heavy chattering and may lead to damage of the product. (When
the on-off valve opens, the secondary pressure of the product changes from zero to
the set pressure. Passing through an area of the reducing ratio of less than 30:1 where
adjustment is impossible, chattering occurs momentarily.) To save energy, install the on-
off valve as near to the boiler, or compressor, as possible.
Note
To prevent water hammer, it is recommended that a slow-acting motorized on-off valve be
used. If a fast-acting on-off solenoid valve is used for frequent temperature control, the
potential water hammer effect can damage the steam-using equipment and the product.
3. Installing a control valve and a safety valve
Safety Valve
(Releaf valve)
Steam-using
Equipment
A control valve (i.e. for temperature control) installed between the product and the
steam-using equipment (downstream of the product) may raise the pressure between
the product and the control valve when the control valve is closed, depending on their
proximity. Therefore, the control valve should be installed closed to the steam-using
equipment. Also, a safety valve should be installed downstream of the control valve.
Note
When installing a safety valve to protect steam-using equipment, be sure to install it on, or
directly before, the inlet of the steam-using equipment. If the safety valve is installed between
the product and a control valve, an eventual pressure rise could activate the safety valve.
8

Recommended straight pipe runs
If the product is installed either directly before or after an elbow or control valve, unevenness
in flow may result in chattering and unstable pressure. To ensure a stable flow, it is
recommended that the product be installed on straight runs of piping, as illustrated below.
(d = pipe diameter)
1. Inlet (primary) side
• Maintain a straight piping run of 10d or more (L) when a manual valve, a strainer or an
elbow, etc. is installed. (Example: if nominal size is 25 mm, have 250 mm or more)
L
• Maintain a straight piping run of 30d or more (L) when an automated valve (on-off
valve) is installed. (Example: if nominal size is 25 mm, have 750 mm or more)
L
•Maintain a straight piping run of 10d or more (L) at a product inlet side. (Example: if
nominal size is 25 mm, have 250 mm or more)
L
2. Outlet (secondary) side
•Maintain a straight piping run of 15d or more (L) when a manual valve, a strainer or an
elbow, etc. is installed. (Example: if nominal size is 25 mm, have 375 mm or more)
L
• Maintain a straight piping run of 30d or more (L) when a safety valve is installed.
(Example: if nominal size is 25 mm, have 750 mm or more)
L
• Maintain a straight piping run of 30d or more (L) when another pressure reducing valve
is installed. (Two-stage pressure reduction) (Example: if nominal size is 25 mm, have
750 mm or more)
9

L1L2
10

Configuration
①②③④⑤⑥⑦⑧⑨⑩⑪⑫⑬⑭⑮⑯⑰⑱㉒㉓㉔㉕㉖㉗㉘㉙Sizes 15, 20 mm
Sizes 15, 20 mm
Enlarged view: A
Sizes 15, 20 mm
Sizes 25, 38, 40 mm
Size 25 mm
㉚㉚
㉚
AA
A㉚A⑲⑳
㉑
㉛㉚Sizes 38, 40 mm
Option:
11

No. Part Name A 01 B 01 C 01 D 01
1 Body
2 Valve ✔
3 Diaphragm ✔
4 Protective Sheet ✔
5 Spring Housing
6 Upper Diaphragm Retainer
7 Coil Spring
8 Cap
9 Lower Diaphragm Retainer
10 Spacer
11 Spring Washer
12 Locknut
13 Plain Washer
14 Retainer Gasket ✔ ✔ ✔
15 Spring Retainer
16 Locknut
17 Adjustment Screw
18 Valve Guide ✔
19 Inlet Clamp Gasket ✔ ✔ ✔
20 Snap Ring ✔
21 Slide Bearing ✔
22 Body Clamp
23 Body Clamp Bolt 02
24 Body Clamp Nut 02
25 Spring Washer 02
26 Inlet Clamp 02
27 Inlet Clamp Bolt 02
28 Inlet Clamp Nut 02
29 Spring Washer 02
30 Adapter
31 Valve Guide Gasket ✔ ✔ ✔
01A: Maintenance kit, B: Repair kit for diaphragm, C: Repair kit for valve, D: Repair kit for valve guide
02Number of parts: 2 pieces
Note
The face-to-face length for the sizes 15 and 20 mm (optional) is 18 mm longer than the standard
size.
12

Installation
Caution
Install properly and DO NOT use this product outside the recommended operating
pressure, temperature and other specification ranges. Improper use may result in such
hazards as damage to the product or malfunctions that may lead to serious accidents. Local
regulations may restrict the use of this product to below the conditions quoted.
Take measures to prevent people from coming into direct contact with product outlets.
Failure to do so may result in burns or other injury from the discharge of fluids.
Installation, inspection, maintenance, repairs, disassembly, adjustment and valve opening/
closing should be carried out only by trained maintenance personnel.
1. Blowdown
Before installing the product or supplying steam to the product, be sure to blow down all
piping thoroughly. If this is not possible, perform a blowdown using the bypass valve.
Blowdown is especially important for newly installed piping or after the system has
been shut down for a long period of time. This will reduce operation failure caused by
condensate or foreign matter.
The bypass valve should not be opened too quickly. If a safety valve (or relief valve) is
installed, perform blowdown staying clear of pressurized blow-out. To perform blowdown,
close the inlet valve (A) first, then the outlet valve (B), and open the bypass valve (C). Do
not open valves too quickly.
ST
PG
SV (RV)
BPV (C)
DR8
ST
PG
Vi (A)
Vo (A)
2. Removing protective caps and seals
Before installation, be sure to remove all protective seals and caps. (Found in 2 locations,
on the product inlet and outlet(s).)
3. Installation angle
Install the product vertically, so that the arrow mark on the body points horizontally in the
direction of flow.
Allowable inclination is 10 degrees in the fore-aft direction and 15 degrees in the plane
perpendicular to the flow line.
15˚ 15˚
10˚
10˚
13

4. Piping support
Install the product, paying attention to avoid excessive load, bending and vibration.
Support the inlet and outlet pipes securely.
5. Maintenance space
Leave sufficient space for maintenance, inspection and repair.
110 110
260
6. Piping size/diffuser
If it is expected that the secondary steam flow velocity will be more than 30 m/s (100 ft/s),
install a diffuser in order to keep the flow velocity below 30 m/s (100 ft/s). If the distance
between the product and the steam-using equipment is great, a possible drop in pressure
should be taken into consideration when selecting the piping size.
If the secondary steam flow velocity is expected to be more than 30 m/s (100 ft/s), install a
diffuser in order to keep the flow velocity below 30 m/s (100 ft/s). If the distance between
the product and the steam-using equipment is great, a possible drop in pressure should be
taken into consideration when selecting the piping size.
b
a
Diffuser
Straight piping (d = pipe diameter)
a 10d or longer upstream
b 15d or longer downstream
14

7. Two-stage pressure reduction
Employ two-stage pressure reduction if the required reduction is not possible due to
product operating range limitations (when it is not possible to reduce to the desired
pressure using a single pressure reducing valve).
Bypass Valve
Bypass Valve
Pressure
Gauge
Pressure
Gauge Outlet
Inlet
Steam Trap Steam Trap
DR8
DR8
Outlet
Valve
Outlet
Valve
Inlet
Valve
Inlet
Valve
8. Accessories
Always install a bypass line. At the inlet and outlet, install a pressure gauge and a shut-off
valve.
Ball valves, which will not retain condensate, are recommended for inlet and outlet shut-off
valves. The bypass pipe should be at least 1/2of the size of the inlet (primary side) pipe.
Bypass Valve
Pressure
Gauge
Ball
Valve
Pressure
Gauge
Ball
Valve
Steam
Trap
Steam
Trap
Safety Valve
(Relief Valve)
15

Adjustment
To avoid problems such as water hammer and to protect steam-using equipment, the product
should be correctly adjusted.
1. It is necessary to blow down all pipe lines thoroughly. The blowdown is especially
important if the line is new or has been shut down for a long period of time.
Take particular care to ensure that matter such as condensate and dirt does not remain
inside the equipment. (Stay clear of any pressurized blow-out from the safety valve.)
2. Make sure that the shutoff valve and the bypass valve located upstream and downstream
of the product are completely closed.
3. Remove the spanner cap, loosen the locknut and turn the adjustment screw
counterclockwise to reduce tension on the coil spring.
Remove the cap and loosen the locknut, then turn the adjustment screw counterclockwise
to free the coil spring.
Cap
Locknut
Adjustment
Screw
Loosen the cap and locknut
Counterclockwise
Fully raise the adjustment screw
4. Slowly, fully open the shutoff valve at the inlet of the product.
5. Slightly open the shutoff valve at the outlet of the product.
6. Turn the adjustment screw clockwise until the desired outlet pressure is obtained. Wait
several minutes.
Clockwise
Clockwise to increase pressure
Counter-
clockwise
Counter-clockwise to decrease pressure
7. Slowly, fully open the shutoff valve at the outlet of the product.
8. After setup, tighten the locknut.
9. (If the inlet shut-off valve is closed first, the safety valve may be tripped.)
16

Maintenance
Caution
Take measures to prevent people from coming into direct contact with product outlets.
Failure to do so may result in burns or other injury from the discharge of fluids.
Be sure to use only the recommended components when repairing the product, and NEVER
attempt to modify the product in any way. Failure to observe these precautions may result in
damage to the product and burns or other injury due to malfunction or the discharge of fluids.
Operational check
To ensure long service life of the product, the following inspection and maintenance should be
performed regularly.
Part Name Inspection and Maintenance Frequency
Diaphragm If hunting or chattering takes place, premature wear may result.
Protective Sheet Check for cracks.
Body (Seat section) If there is chattering or dirt, premature wear may result.
Valve (Seat section) If there is chattering or dirt, premature wear may result.
Valve Guide (Slide Bearing) If hunting or chattering takes place, premature wear may result.
Gaskets Check for deformation or scratches.
17

Disassembly
Caution
When disassembling or removing the product, wait until the internal pressure equals
atmospheric pressure and the surface of the product has cooled to room temperature.
Disassembling or removing the product when it is hot or under pressure may lead to discharge of
fluids, causing burns, other injuries or damage.
It is a recommended practice to dismantle and inspect the product once a year for preventive
maintenance purposes. It is especially important to perform an inspection immediately after
the initial run of a new line or before or after equipment that is out of service for a long period
of time.
(Installation, inspection, maintenance, repairs, disassembly, adjustment and valve opening/
closing should be carried out only by trained maintenance personnel.)
Remove all steam from the piping (both upstream and downstream). Wait for the body to cool
before attempting to remove the product from the line. Then remove the product from the
piping, and secure it in a vise to perform the inspection.
18

Disassembling the adjustment section
Loosen the cap and the locknut first. Loosen the adjustment screw completely and remove the
body clamp.
Adjustment Screw
Spring Housing
Locknut
Cap
Spring Washer
Body Clamp
Body Clamp Bolt
Body Clamp Nut
After removing the spring housing, remove the adjustment screw, spring retainer, and coil
spring.
Important
Check for seizure or any damaged screw threads.
Adjustment Screw
(Reverse thread)
Spring Retainer
(Reverse thread)
Coil Spring
Note: Check the installation
direction and make sure it
is the same direction when
re-assembling. If there are
no markings, mark the top
for future reference.
Note
The spring retainer and coil spring guide cannot be removed individually as they are incorporated
with the coil spring.
19

Disassembling the Diaphragm Section
Hold the valve in place with an adjustable wrench across the flats on the upper part of the
valve and use another wrench to remove the locknut. After removing the locknut, remove the
plain washer, the upper diaphragm retainer and the diaphragm.
Disassembling the Valve Section
Remove the inlet clamp(s) holding the body, valve guide and adapter (for sizes 15 to 20 mm
(1/2to 3/4in) only).
Inlet Clamp
Inlet Clamp Nut
Inlet Clamp Bolt
Adapter
(for sizes 15 to 20 mm (1/2 to 3/4 in) only)
Valve Guide
Body
Spring Washer
Separate the valve guide from the body. The valve comes off with the valve guide.
Adapter
(for sizes 15 to 20 mm (1/2to3/4in) only)
Inlet Clamp Gasket
Disassembling the Valve Guide Section
Adapter
Inlet Clamp Gasket
Valve Guide
Slide Bearing
Snap Ring
Note: Pay attention to the mounting direction.
The slide bearing and snap ring cannot be removed individually as they are incorporated with
the valve guide and must be replaced as a set with the valve guide.
20
Other manuals for DR8-3P
2
This manual suits for next models
3
Table of contents
Other TLV Control Unit manuals
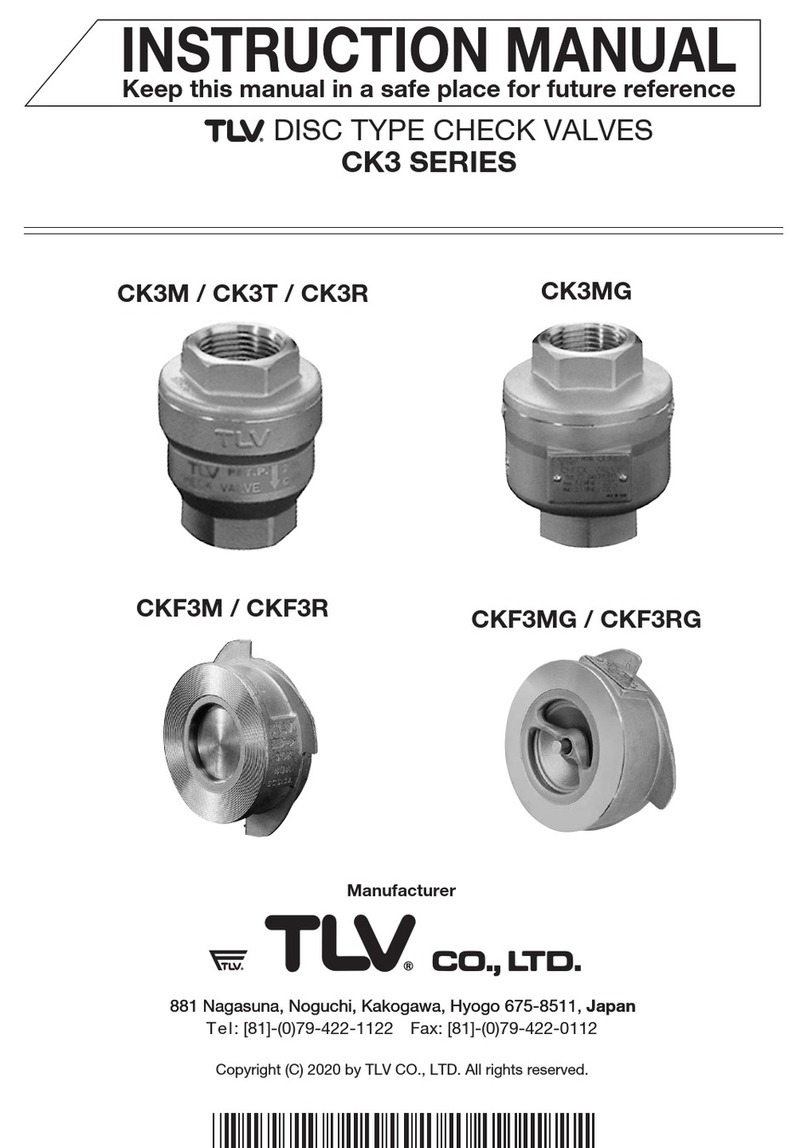
TLV
TLV CK3 Series User manual
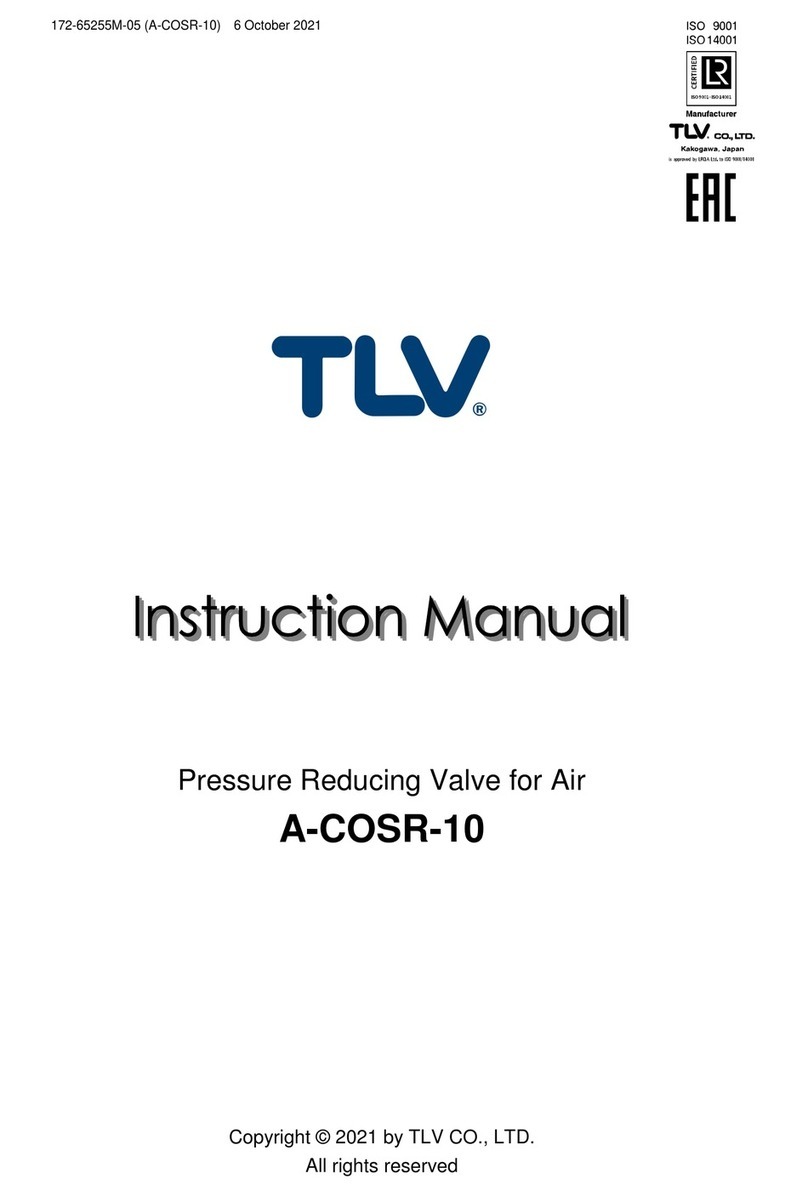
TLV
TLV A-COSR-10 User manual

TLV
TLV CK3 Series User manual
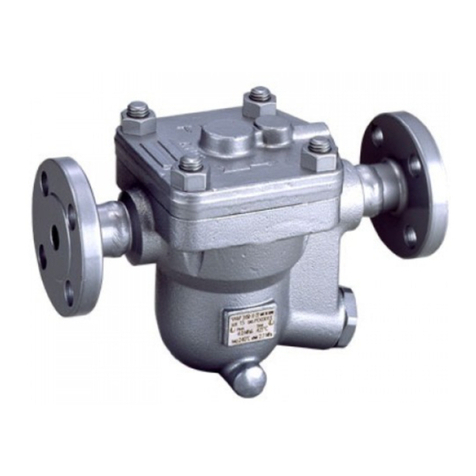
TLV
TLV JH-B series User manual
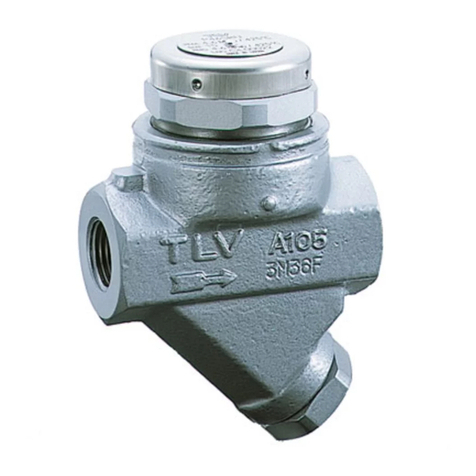
TLV
TLV P Series User manual
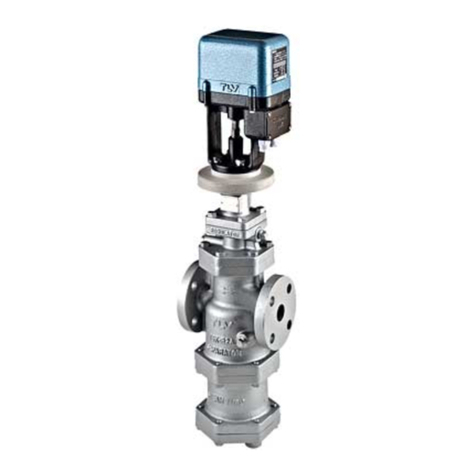
TLV
TLV COSPECT M-COS-3 User manual
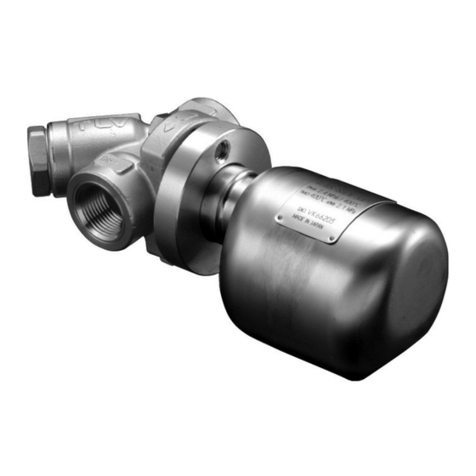
TLV
TLV QUICK TRAP FS Series User manual
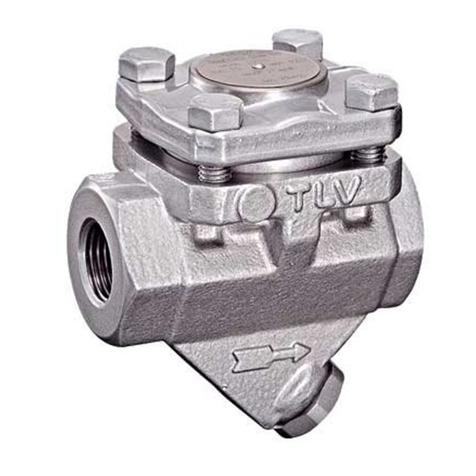
TLV
TLV L Series User manual
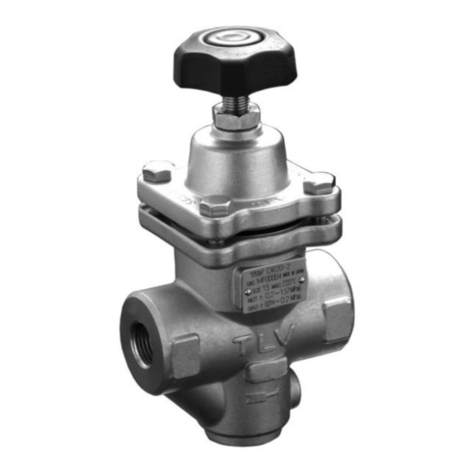
TLV
TLV DR20 User manual
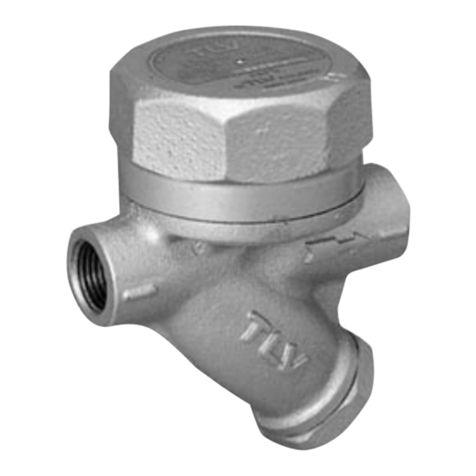
TLV
TLV ThermoDyne A3N-AF3N User manual
Popular Control Unit manuals by other brands
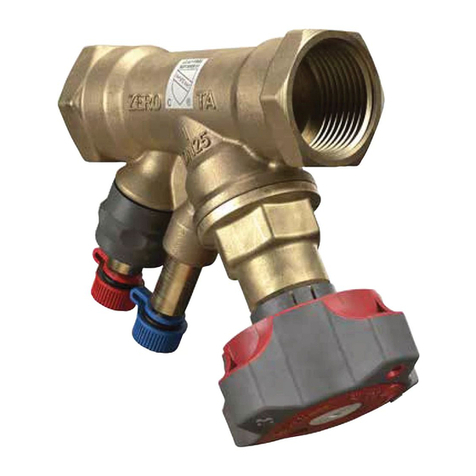
Victaulic
Victaulic KOIL-KIT 799 Series Installation and maintenance instructions

SEA
SEA Orion manual
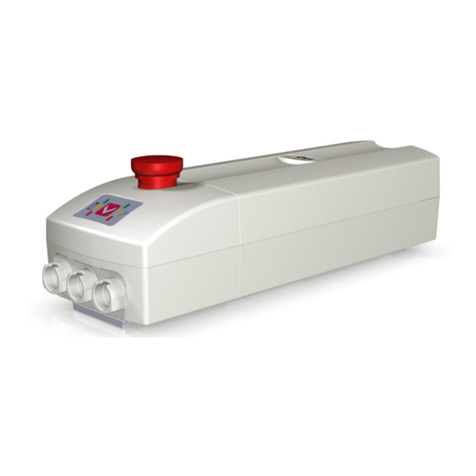
Phoenix Mecano
Phoenix Mecano Dewert Okin ACCUCONTROL 4.5 installation instructions
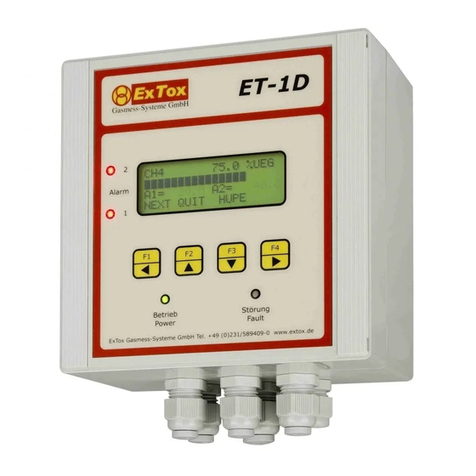
ExTox
ExTox ET-1D Series instruction manual
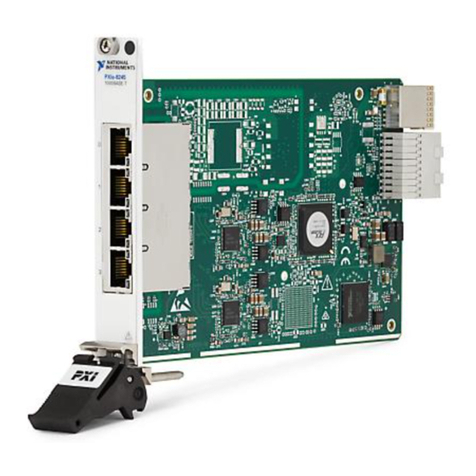
National Instruments
National Instruments PXIe-8245 Getting started guide
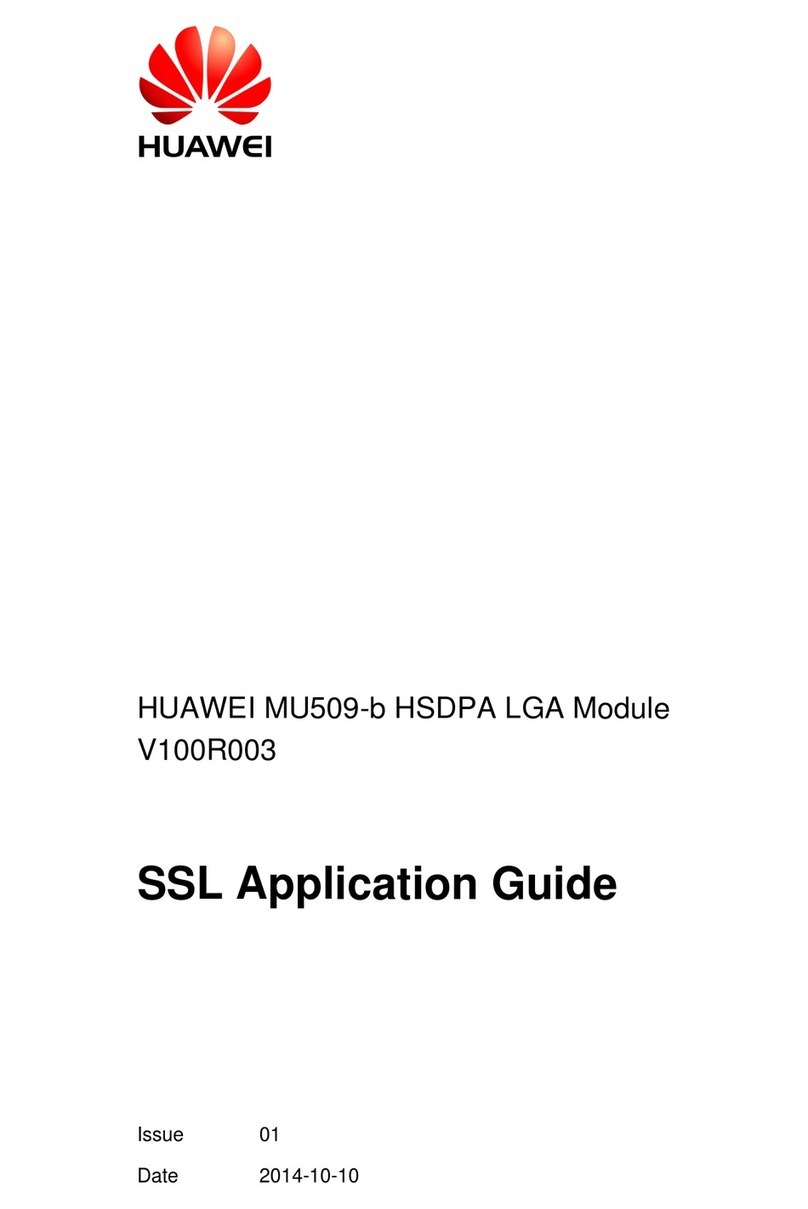
Huawei
Huawei MU509-b Application guide