ABB FlexPLP IRPLP 220 User manual

ROBOTICS
Product manual
FlexPLP IRPLP 220

Trace back information:
Workspace Systems version a10
Checked in 2019-04-12
Skribenta version 5.3.012

Product manual
FlexPLP IRPLP 220
Document ID: 3HAW050041018-001
Revision: C
© Copyright 2016 - 2018 ABB. All rights reserved.
Specifications subject to change without notice.

The information in this manual is subject to change without notice and should not
be construed as a commitment by ABB. ABB assumes no responsibility for any errors
that may appear in this manual.
Except as may be expressly stated anywhere in this manual, nothing herein shall be
construed as any kind of guarantee or warranty by ABB for losses, damages to
persons or property, fitness for a specific purpose or the like.
In no event shall ABB be liable for incidental or consequential damages arising from
use of this manual and products described herein.
This manual and parts thereof must not be reproduced or copied without ABB's
written permission.
Keep for future reference.
Additional copies of this manual may be obtained from ABB.
Original instructions.
© Copyright 2016 - 2018 ABB. All rights reserved.
Specifications subject to change without notice.
ABB AB, Robotics
Robotics and Motion
Se-721 68 Västerås
Sweden

Table of contents
7Overview ...........................................................................................................................................
9Product documentation, IRC5 ..........................................................................................................
11How to read the product manual ......................................................................................................
131 Safety
131.1 Introduction ...................................................................................................... 141.2 General safety information .................................................................................. 141.2.1 Safety in the machine controller system ...................................................... 151.3 Safety risks ...................................................................................................... 151.3.1 Safety risks during installation and service work ........................................... 171.3.2 Safety risks related to tools/workpieces ....................................................... 181.3.3 Safety risks related to pneumatic/hydraulic systems ...................................... 191.3.4 Safety risks during operational disturbances ................................................ 201.3.5 Risks associated with live electric parts ....................................................... 211.4 Safety actions related to the FlexPLP .................................................................... 211.4.1 Safety fence dimensions ........................................................................... 221.4.2 Fire extinguishing .................................................................................... 231.4.3 Emergency release of the FlexPLP device axes ............................................ 241.4.4 Brake testing .......................................................................................... 251.4.5 Safe use of the Teach Pendant Unit ............................................................ 261.4.6 Work inside the FlexPLP's working range .................................................... 271.4.7 Translate the information on safety and information labels .............................. 281.5 Safety stops ..................................................................................................... 281.5.1 What is an emergency stop? ..................................................................... 301.6 Safety related instructions .................................................................................. 301.6.1 Safety signals in the manual ......................................................................
332 Product description
332.1 Product overview .............................................................................................. 342.2 Terminology ..................................................................................................... 352.3 Principle structure ............................................................................................. 352.3.1 Modularity .............................................................................................. 372.3.2 Axes combinations .................................................................................. 382.3.3 Driving types .......................................................................................... 392.3.4 Vertical axis mounting and cable chain ........................................................ 402.4 Performances ................................................................................................... 402.4.1 FlexPLP IRPLP 220 overall specifications .................................................... 412.4.2 FlexPLP IRPLP 220 motor specifications ..................................................... 422.5 Dimensions ...................................................................................................... 422.5.1 Dimensions 1-axis FlexPLP IRPLP 220 ........................................................ 442.5.2 Dimensions 2-axis FlexPLP IRPLP 220 ........................................................ 472.5.3 Dimensions 3-axis FlexPLP IRPLP 220 ........................................................ 492.6 Weight ............................................................................................................
513 Unpacking and handling
513.1 Pre-requisites for reception ................................................................................. 523.2 Unpacking and acceptance ................................................................................. 543.3 Handling/lifting .................................................................................................
574 Installation and commissioning
574.1 Introduction ...................................................................................................... 584.2 Mechanical installation ....................................................................................... 584.2.1 Introduction ............................................................................................ 594.2.2 Mounting surface (fastening of the FlexPLP IRPLP 220 to the floor plate) .......... 624.2.3 Mounting surfaces (fastening of an axis or customer equipment) .....................
Product manual - FlexPLP IRPLP 220 5
3HAW050041018-001 Revision: C
© Copyright 2016 - 2018 ABB. All rights reserved.
Table of contents

634.2.4 Jogging axes of a unit with FlexPendant ...................................................... 684.2.5 Fastening of a unit to the floor plate ............................................................ 704.3 Cabling and control ........................................................................................... 704.3.1 Connectors and internal equipment wiring ................................................... 714.3.2 Control architecture ................................................................................. 734.3.3 Controller capabilities .............................................................................. 754.3.4 Examples of configurations ....................................................................... 814.3.5 Configuration files ...................................................................................
835 Calibration
835.1 Introduction / When to calibrate ........................................................................... 845.2 Calibration points .............................................................................................. 855.3 Edit motor calibration offset ................................................................................ 875.4 Fine calibration ................................................................................................. 905.5 Update of the revolution counters .........................................................................
936 FlexPLP addin application GUI
936.1 Introduction ...................................................................................................... 946.2 Workflow of the FlexPLP addin ............................................................................ 946.2.1 Soft Calibration ....................................................................................... 1056.2.2 Shim Offset ............................................................................................
1137 Maintenance
1137.1 Introduction ...................................................................................................... 1157.2 Maintenance schedule ....................................................................................... 1167.3 Inspection ........................................................................................................ 1177.4 Lubrication ....................................................................................................... 1197.5 Driving belt (tension check, adjustment and replacement) ......................................... 1237.6 SMB Battery pack replacement ............................................................................ 1257.7 Repair information .............................................................................................
1278 Decommissioning
1319 Reference information
1319.1 Introduction ...................................................................................................... 1329.2 Unit conversion ................................................................................................. 1339.3 Bolt, screws, tightening torques ........................................................................... 1349.4 Standard toolkit ................................................................................................ 1359.5 Special tools ....................................................................................................
13710 Spare parts
13710.1 Introduction ...................................................................................................... 13810.2 Spare parts - Ballscrew type ................................................................................ 14010.3 Spare parts - Rack & Pinion type .......................................................................... 14210.4 Covers ............................................................................................................ 14310.5 Cables ............................................................................................................
6 Product manual - FlexPLP IRPLP 220
3HAW050041018-001 Revision: C
© Copyright 2016 - 2018 ABB. All rights reserved.
Table of contents

Overview
About this manual
This manual contains instructions for:
• the characteristics of the FlexPLP IRPLP 220
•mechanical and electrical installation instructions for the FlexPLP IRPLP 220
• maintenance instructions for the FlexPLP IRPLP 220
• spare parts
Usage
This manual should be used when working during:
• installation, from lifting the FlexPLP IRPLP 220 to its work site and securing
it to the foundation, to making it ready for operation
• maintenance work
• repair work
Who should read this manual?
This manual is intended for:
• installation personnel
• maintenance personnel
• repair personnel.
Prerequisites
A maintenance/ repair/ installation personnel working with an ABB FlexPLP IRPLP
220 must:
• be trained by ABB and have the required knowledge of mechanical and
electrical installation/repair/maintenance work.
Organization of chapters
The manual is organized in the following chapters:
ContentChapter
Safety information that must be read through before performing
any installation or service work on the FlexPLP IRPLP 220.
Contains general safety aspects as well as more specific inform-
ation about how to avoid personal injuries and damage to the
product.
Safety
Specifications and characteristics of the FlexPLP IRPLP 220.Product description
Information relative to the steps following the reception of the
FlexPLP IRPLP 220, until its installation.
Unpacking and handling
Required information about lifting and installation of the FlexPLP
IRPLP 220 and installation of cabling.
Installation and commis-
sioning
Information about calibration of the system.Calibration
Step-by-step procedures that describe how to perform mainten-
ance of the FlexPLP IRPLP 220. Based on a maintenance
schedule that may be used in the work of planning periodical
maintenance.
Maintenance
Continues on next page
Product manual - FlexPLP IRPLP 220 7
3HAW050041018-001 Revision: C
© Copyright 2016 - 2018 ABB. All rights reserved.
Overview

ContentChapter
Environmental information about the FlexPLP IRPLP 220.Decommissioning
Reference information may be useful for the understanding of
this manual.
Reference information
List of the spare parts available for the FlexPLP IRPLP 220.Spare parts
References
Document IDReference (ABB manuals)
3HAC021313-001Product manual - IRC5
3HAC050944-001Operating manual - Service Information System
3HAC051016-001Application manual - Additional axes and stand alone controllers
3HAC050941-001Operating manual - IRC5 with FlexPendant
3HAC050948-001Technical reference manual - System parameters
3HAC050917-001Technical reference manual - RAPID Instructions, Functions and
Data types
Revisions
DescriptionRevision
First edition.-
The following updates are done in this revision:
• Minor editorial changed.
• Calibration point, without calibration index system removed.
• Specification of rack & pinion updated.
• Spare parts updated.
•Edit Motor Calibration Offset added.
• Number of the motions changed.
A
Changes made in:
• FlexPLP addin is applied to improve the efficiency of calibration
and setting offset procedures, see FlexPLP addin application GUI
on page 93.
•Deleted the stroke information, and add protection detail in Product
overview on page 33.
• Changed the axis name of nominal payload in Robustness on
page 59.
• Added a contact strategy for customers, see Workflow of the
FlexPLP addin on page 94.
• Added material disposing symbol and related description in
Symbol on page 128.
B
Changes made in:
• Added warning about grease KLÜBER Microlube GB0.
C
8 Product manual - FlexPLP IRPLP 220
3HAW050041018-001 Revision: C
© Copyright 2016 - 2018 ABB. All rights reserved.
Overview
Continued

Product documentation, IRC5
Categories for user documentation from ABB Robotics
The user documentation from ABB Robotics is divided into a number of categories.
This listing is based on the type of information in the documents, regardless of
whether the products are standard or optional.
All documents listed can be ordered from ABB on a DVD. The documents listed
are valid for IRC5 robot systems.
Product manuals
All hardware, manipulators and controllers will be delivered with a Product manual
that contains:
• Safety information
• Installation and commissioning (description of mechanical installation,
electrical connections)
•Maintenance (description of all required preventive maintenance procedures
including intervals)
• Repair (description of all recommended repair procedures including spare
parts)
• Additional procedures, if any (calibration, decommissioning)
• Reference information (article numbers for documentation referred to in
Product manual, procedures, lists of tools, safety standards)
• Parts list.
• Foldouts or exploded views.
• Circuit diagrams (or references to circuit diagrams).
Technical reference manuals
The technical reference manuals describe the manipulator software in general and
contain relevant reference information.
•RAPID Overview: An overview of the RAPID programming language.
•RAPID Instructions,Functions and Data types: Description of all RAPID
instructions, functions and data types.
•RAPID Kernel: A formal description of the RAPID programming language.
•System parameters: Description of system parameters and configuration
workflow.
Application manuals
Specific applications (for example, software or hardware options) are described
in Application manuals. An application manual can describe one or several
applications.
An application manual generally contains information about:
• The purpose of the application (what it does and when it is useful)
•What is included (for example, cables, I/O boards, RAPID instructions, system
parameters)
Continues on next page
Product manual - FlexPLP IRPLP 220 9
3HAW050041018-001 Revision: C
© Copyright 2016 - 2018 ABB. All rights reserved.
Product documentation, IRC5

• How to install included or required hardware.
• How to use the application
• Examples of how to use the application
Operating manuals
The operating manuals describe hands-on handling of the products. The manuals
are aimed at those having first-hand operational contact with the product, that is
production cell operators, programmers, and trouble shooters.
The group of manuals includes:
•Emergency safety information
•General safety information
•Getting started, IRC5 and RobotStudio
•IRC5 with FlexPendant
•RobotStudio
•Introduction to RAPID
•Trouble shooting, for the controller and manipulator.
10 Product manual - FlexPLP IRPLP 220
3HAW050041018-001 Revision: C
© Copyright 2016 - 2018 ABB. All rights reserved.
Product documentation, IRC5
Continued

How to read the product manual
Reading the procedures
The procedures contain references to figures, tools, material and so on. The
references are read as described below.
References to figures
The procedures often include references to components or attachment points
located on the device/controller. The components or attachment points are marked
with italic text in the procedures and completed with a reference to the figure where
the current component or attachment point is shown.
The denomination in the procedure for the component or attachment point
corresponds to the denomination in the referenced figure.
The table below shows an example of a reference to a figure from a step in a
procedure.
NoteAction
Shown in the figure Location of
gearbox on page 120.
Remove the rear attachment screws, gearbox.8
Reference to required equipment
The procedures often include references to equipment (spare parts, tools, and so
on.) required for the different actions in the procedure. The equipment is marked
with italic text in the procedures and completed with a reference to the section
where the equipment is listed with further information, i.e. article number, dimension.
The denomination in the procedure for the component or attachment point
corresponds to the denomination in the referenced list.
The table below shows an example of a reference to a list of required equipment,
from a step in a procedure.
NoteAction
Art. no. is specified in Required
equipment on page 57.
Fit a new sealing, 2 to the gearbox.3
Safety information
The manual includes a separate safety chapter that must be read through before
proceeding with any service or installation procedures. All procedures also include
specific safety information when dangerous steps are to be performed.
For more information, see Safety on page 13.
Product manual - FlexPLP IRPLP 220 11
3HAW050041018-001 Revision: C
© Copyright 2016 - 2018 ABB. All rights reserved.
How to read the product manual

This page is intentionally left blank

1 Safety
1.1 Introduction
Overview
The safety information in this manual is divided in two categories:
• general safety aspects, important to attend to before performing any service
work on the device. These are applicable for all service work and are found
in General safety information on page 14.
• specific safety information, pointed out in the procedure at the moment of
the danger. How to avoid and eliminate the danger is either detailed directly
in the procedure, or further detailed in separate instructions, found in Safety
related instructions on page 30.
Product manual - FlexPLP IRPLP 220 13
3HAW050041018-001 Revision: C
© Copyright 2016 - 2018 ABB. All rights reserved.
1 Safety
1.1 Introduction

1.2 General safety information
1.2.1 Safety in the machine controller system
Validity and responsibility
The information does not cover how to design, install and operate a complete
system, nor does it cover all peripheral equipment, which can influence the safety
of the total system. To protect personnel, the complete system must be designed
and installed in accordance with the safety requirements set forth in the standards
and regulations of the country where the machine controller is installed.
The users of ABB industrial machine controllers are responsible for ensuring that
the applicable safety laws and regulations in the country concerned are observed
and that the safety devices necessary to protect people working with the machine
controller system are designed and installed correctly. Personnel working with
machine controllers must be familiar with the operation and handling of the industrial
machine controller, described in the applicable documents, e.g. User’s Guide and
Product Manual.
Connection of external safety devices
Apart from the built-in safety functions, the machine controller is also supplied with
an interface for the connection of external safety devices. Via this interface, an
external safety function can interact with other machines and peripheral equipment.
This means that control signals can act on safety signals received from the
peripheral equipment as well as from the machine controller.
Limitation of liability
Any information given in this manual regarding safety, must not be construed as
a warranty by ABB that the industrial machine controller will not cause injury or
damage even if all safety instructions are complied with.
Related information
SectionDetailed in documentType of information
Installation and commis-
sioning
Product manual for the machine controllerInstallation of safety
devices
Operating modesOperating manual - IRC5 with FlexPend-
ant
Change operating
modes
Installation and commis-
sioning
Product manual for the machine controllerRestricting the working
space
SafetyProduct manual for the machine controllerSafety information
about the
machine controller
14 Product manual - FlexPLP IRPLP 220
3HAW050041018-001 Revision: C
© Copyright 2016 - 2018 ABB. All rights reserved.
1 Safety
1.2.1 Safety in the machine controller system

1.3 Safety risks
1.3.1 Safety risks during installation and service work
Overview
This section includes information of general safety risks to be considered when
performing installation and service work on FlexPLP device.
General risks during installation and service
• The instructions in the Product Manual - Installation and Commissioning
must always be followed.
• Emergency stop buttons must be positioned in easily accessible places so
that the FlexPLP device can be stopped quickly.
• Those in charge of operations must make sure that safety instructions are
available for the installation in question.
• Those who install the FlexPLP device must have the appropriate training for
the FlexPLP device system in question and in any safety matters associated
with it.
Nation/region specific regulations
To prevent injuries and damage during the installation of the FlexPLP device, the
regulations applicable in the country concerned and the instructions of ABB
Robotics must be complied with.
Non-voltage related risks
• Safety zones, which have to be crossed before admittance, must be set up
in front of the FlexPLP's working space. Light beams or sensitive mats are
suitable devices.
•Turntables or the like should be used to keep the operator out of the FlexPLP's
working space.
• The axes are affected by the force of gravity when the brakes are released.
In addition to the risk of being hit by moving FlexPLP parts, you run the risk
of being crushed by the FlexPLP axes.
•When dismantling/assembling mechanical units, watch out for falling objects.
• Be aware of stored heat energy in the controller.
• Never use the FlexPLP device as a ladder, i.e. do not climb on the device or
other part during service work. There is a serious risk of slipping because
of the high temperature of the motors or oil spills that can occur on the device.
To be observed by the supplier of the complete system
• The supplier of the complete system must ensure that all circuits used in the
safety function are interlocked in accordance with the applicable standards
for that function.
Continues on next page
Product manual - FlexPLP IRPLP 220 15
3HAW050041018-001 Revision: C
© Copyright 2016 - 2018 ABB. All rights reserved.
1 Safety
1.3.1 Safety risks during installation and service work

• The supplier of the complete system must ensure that all circuits used in the
emergency stop function are interlocked in a safe manner, in accordance
with the applicable standards for the emergency stop function.
Complete FlexPLP device
DescriptionSafety risk
CAUTION
Motors and gears are HOT after running the device!
Touching the motors and gears may result in burns!
Hot components!
Removed parts may result in col-
lapse of the device!
WARNING
Take any necessary measures to ensure that the device
does not collapse as parts are removed, e.g. secure the
vertical axis with fixtures if removing driving belt of ho-
rizontal axes.
Cabling
DescriptionSafety risk
CAUTION
The cable packs are sensitive to mechanical damage!
They must be handled with care, especially the connect-
ors, in order to avoid damaging them!
Cable packs are sensitive to
mechanical damage!
Gearboxes and motors
DescriptionSafety risk
CAUTION
Whenever parting/mating motor and gearbox, the gears
may be damaged if excessive force is used!
Gears may be damaged if excess-
ive force is used!
16 Product manual - FlexPLP IRPLP 220
3HAW050041018-001 Revision: C
© Copyright 2016 - 2018 ABB. All rights reserved.
1 Safety
1.3.1 Safety risks during installation and service work
Continued

1.3.2 Safety risks related to tools/workpieces
Safe handling
It must be possible to safely turn off tools. Make sure that guards remain closed
until the tools turn off.
It should be possible to release parts by manual operation (valves).
Safe design
End effectors must be designed so that they retain workpieces in the event of a
power failure or a disturbance of the controller.
CAUTION
Ensure that an end effectors is prevented from dropping a workpiece, if such is
used.
Product manual - FlexPLP IRPLP 220 17
3HAW050041018-001 Revision: C
© Copyright 2016 - 2018 ABB. All rights reserved.
1 Safety
1.3.2 Safety risks related to tools/workpieces

1.3.3 Safety risks related to pneumatic/hydraulic systems
General
Special safety regulations apply to pneumatic and hydraulic systems.
Residual energy
•Residual energy may be present in these systems. After shutdown, particular
care must be taken.
• The pressure in pneumatic and hydraulic systems must be released before
starting to repair them.
Safe design
• Gravity may cause any parts or objects held by these systems to drop.
• Dump valves should be used in case of emergency.
• Shot bolts should be used to prevent tools, and so on, from falling due to
gravity.
18 Product manual - FlexPLP IRPLP 220
3HAW050041018-001 Revision: C
© Copyright 2016 - 2018 ABB. All rights reserved.
1 Safety
1.3.3 Safety risks related to pneumatic/hydraulic systems

1.3.4 Safety risks during operational disturbances
General
• The FlexPLP device is a flexible tool which can be used in many different
industrial applications.
• All work must be carried out professionally and in accordance with the
applicable safety regulations.
• Care must be taken at all times.
Qualified personnel
• Corrective maintenance must only be carried out by qualified personnel who
are familiar with the entire installation as well as the special risks associated
with its different parts.
Extraordinary risks
If the working process is interrupted, extra care must be taken due to risks other
than those associated with regular operation. Such an interruption may have to be
rectified manually.
Product manual - FlexPLP IRPLP 220 19
3HAW050041018-001 Revision: C
© Copyright 2016 - 2018 ABB. All rights reserved.
1 Safety
1.3.4 Safety risks during operational disturbances

1.3.5 Risks associated with live electric parts
Voltage related risks, general
• Although troubleshooting may, on occasion, have to be carried out while the
power supply is turned on, the FlexPLP device must be turned off (by setting
the mains switch to OFF) when repairing faults, disconnecting electric leads
and disconnecting or connecting units.
• The mains supply to the FlexPLP device must be connected in such a way
that it can be turned off outside the device's working space.
Voltage related risks, controller IRC5
A danger of high voltage is associated with the following parts:
•Be aware of stored electrical energy (DC link, Ultra Cap unit) in the controller.
•Units inside the controller, e.g. I/O modules, can be supplied with power from
an external source.
• The mains supply/mains switch
• The transformers
• The power unit
• The control power supply (230 VAC)
• The rectifier unit (400-480 VAC and 700 VDC. Note: Capacitors!)
• The drive unit (700 VDC)
• The drive system power supply (230 VAC)
• The service outlets (115/230 VAC)
• The customer power supply (230 VAC)
• The power supply unit for tools, or special power supply units for the
machining process.
•The external voltage connected to the control cabinet remains live even when
the device is disconnected from the mains.
• Additional connections.
Voltage related risks, FlexPLP
A danger of high voltage is associated with the FlexPLP device in:
• The power supply for the motors (up to 800 VDC).
• The user connections for tools or other parts of the installation (max. 230
VAC, see chapter Installation and commissioning in the Product manual).
Voltage related risks, tools, material handling devices, and so on.
Tools, material handling devices, and so on may be live even if the FlexPLP control
system is in the OFF position. Power supply cables which are in motion during the
working process may be damaged.
20 Product manual - FlexPLP IRPLP 220
3HAW050041018-001 Revision: C
© Copyright 2016 - 2018 ABB. All rights reserved.
1 Safety
1.3.5 Risks associated with live electric parts
Table of contents
Other ABB Valve Positioner manuals
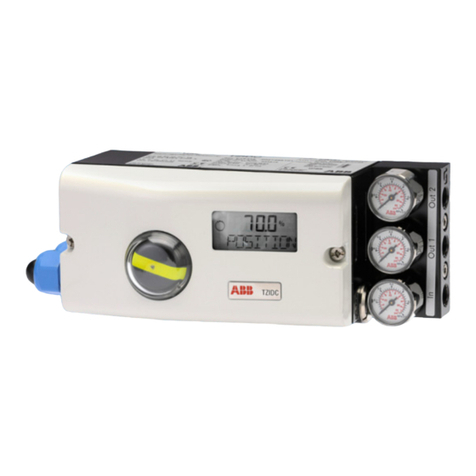
ABB
ABB TZIDC Original operating manual
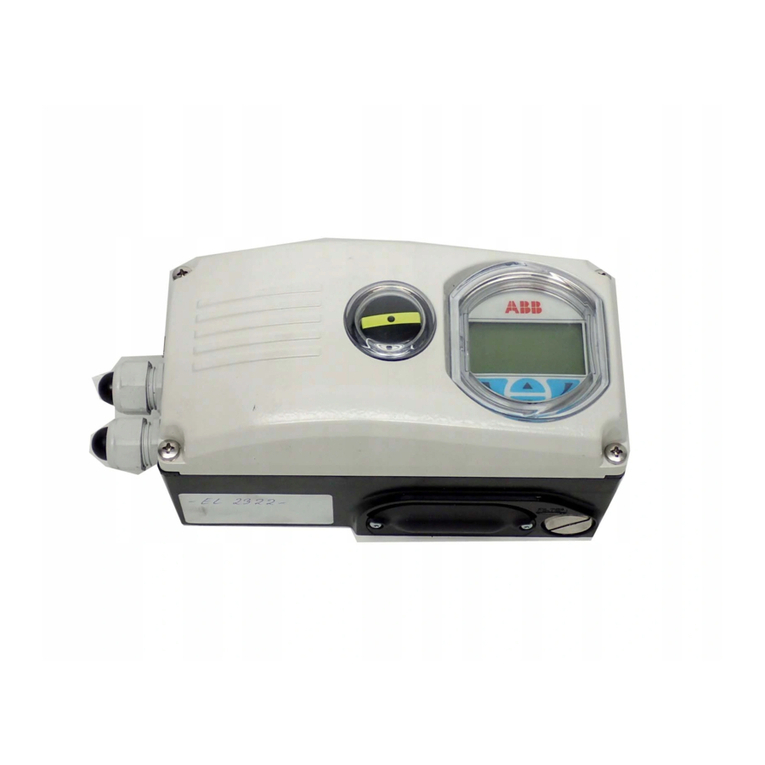
ABB
ABB PositionMaster EDP300 Installation and operation manual

ABB
ABB TZIDC Installation and operation manual

ABB
ABB PositionMaster EDP300 User manual

ABB
ABB TZIDC Training manual
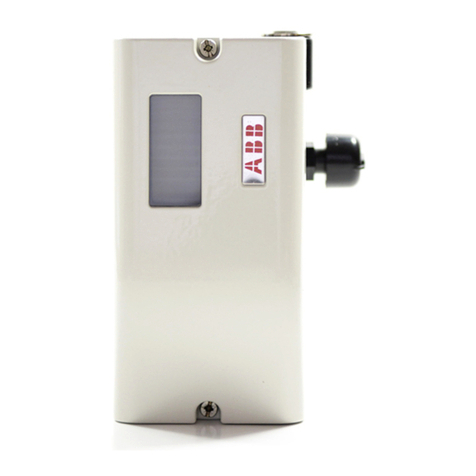
ABB
ABB TZIDC-110 Training manual

ABB
ABB TZIDC User manual

ABB
ABB TZIDC-200 User manual
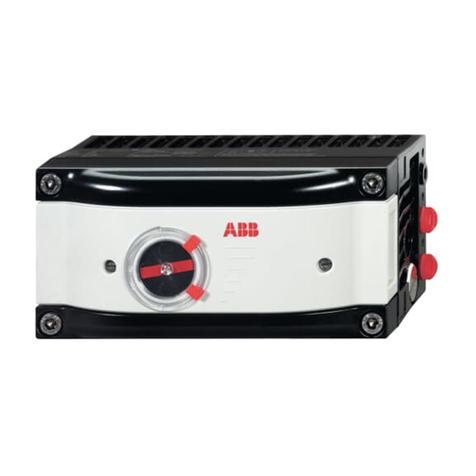
ABB
ABB TZIDC-200 Training manual

ABB
ABB PositionMaster EDP300 User manual
Popular Valve Positioner manuals by other brands
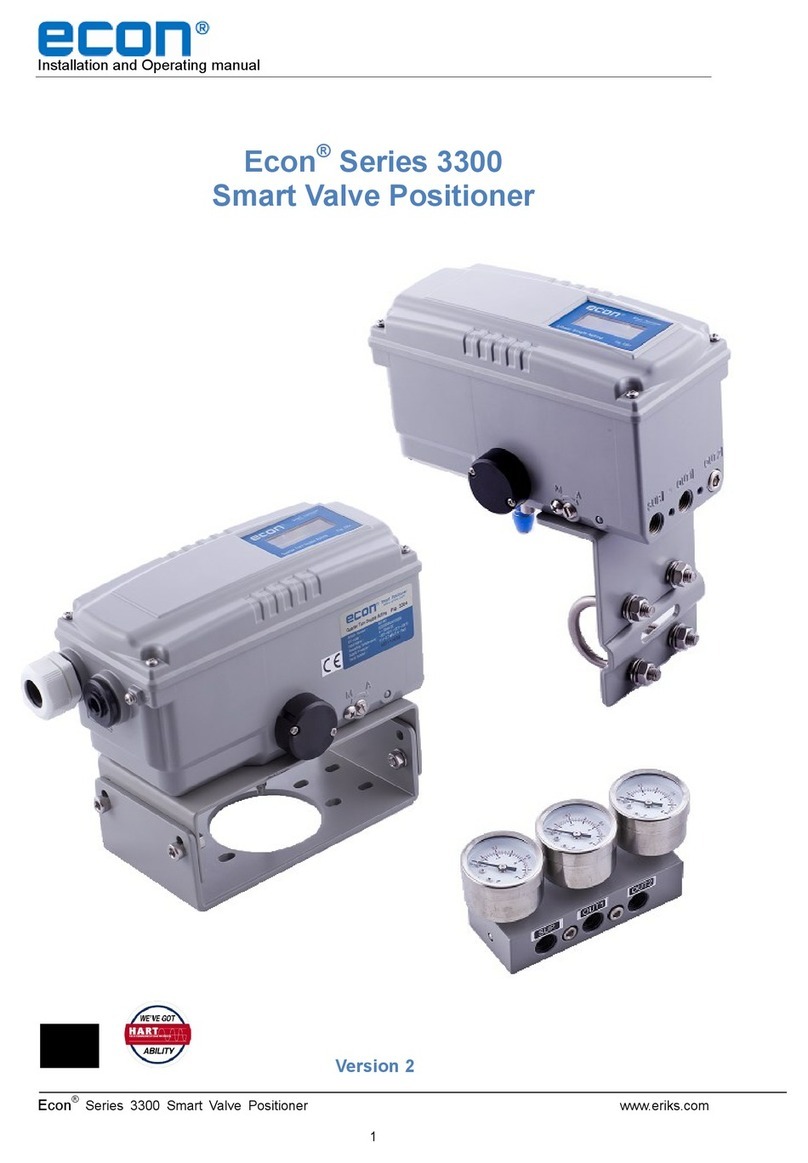
Econ
Econ 3300 Series operating manual
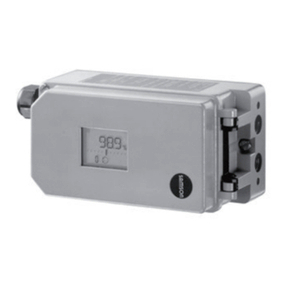
Samson
Samson 3730-4 Mounting and operating instructions
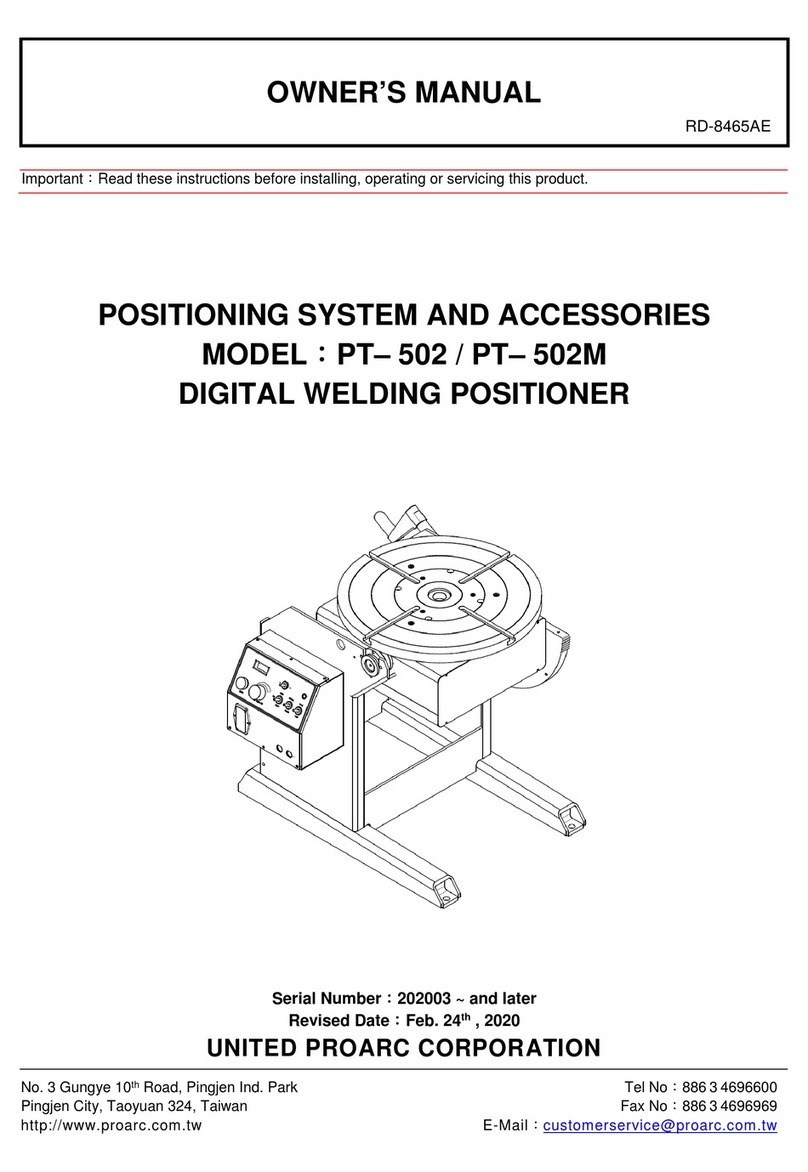
ProArc
ProArc PT-502 owner's manual
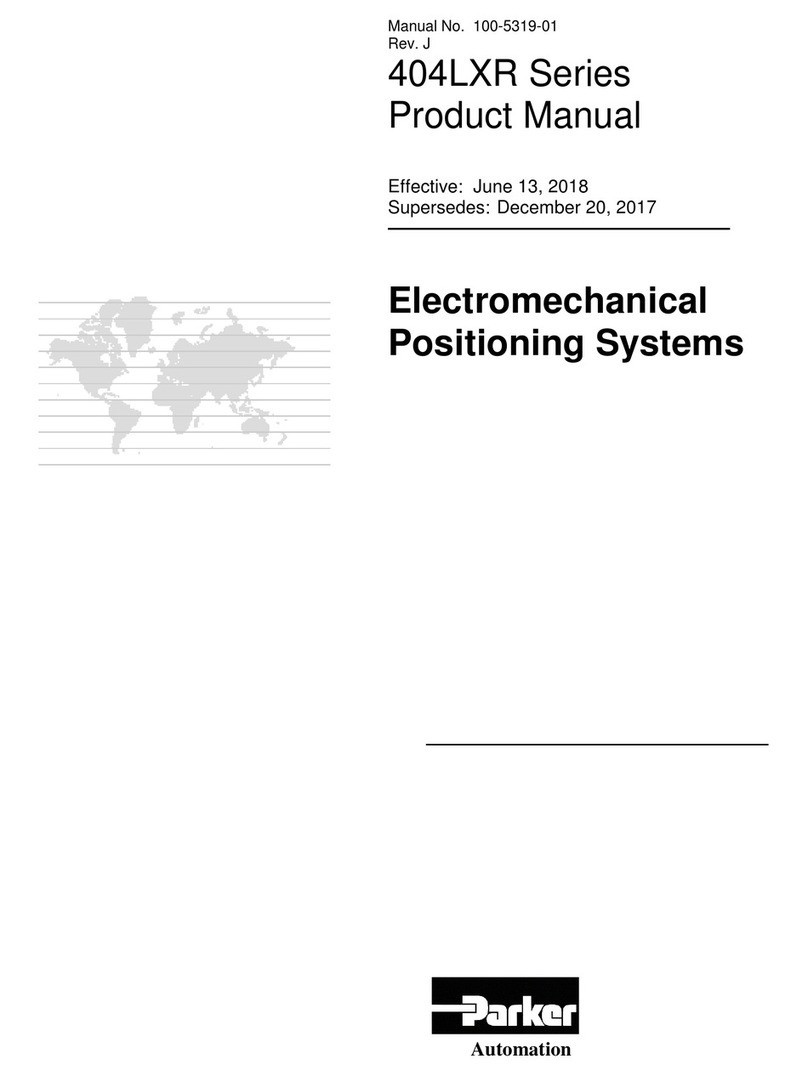
Parker
Parker 404LXR Series product manual
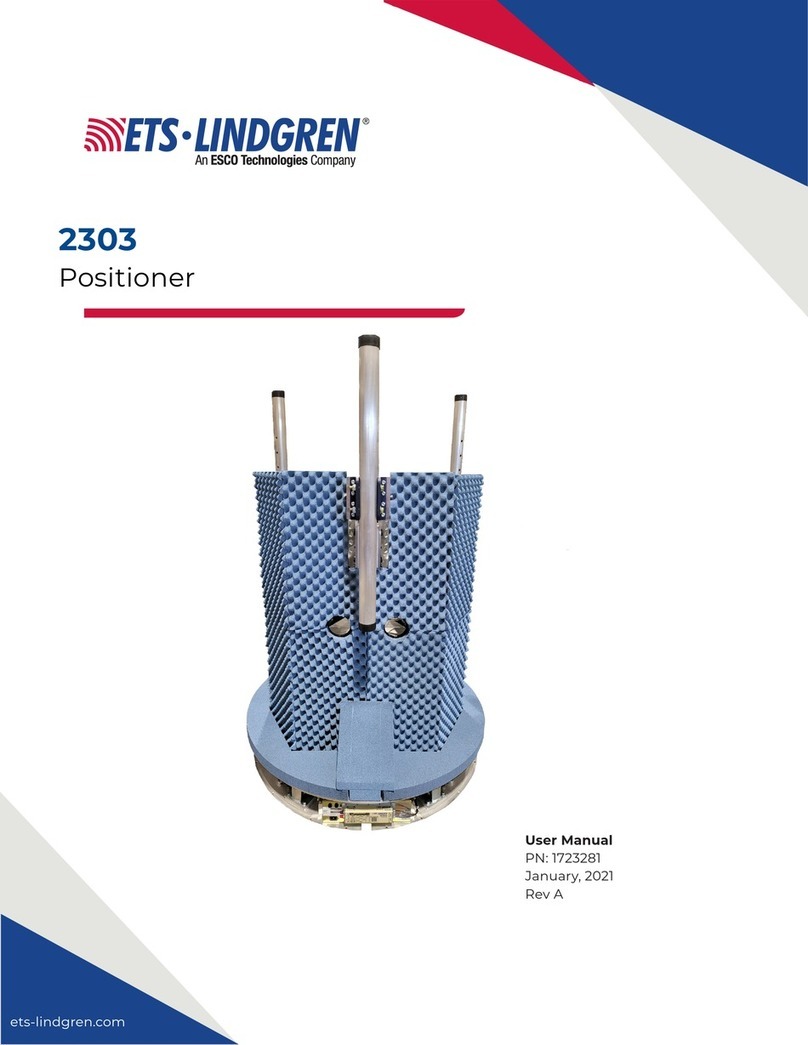
ESCO Technologies
ESCO Technologies ETS-LINDGREN 2303 user manual
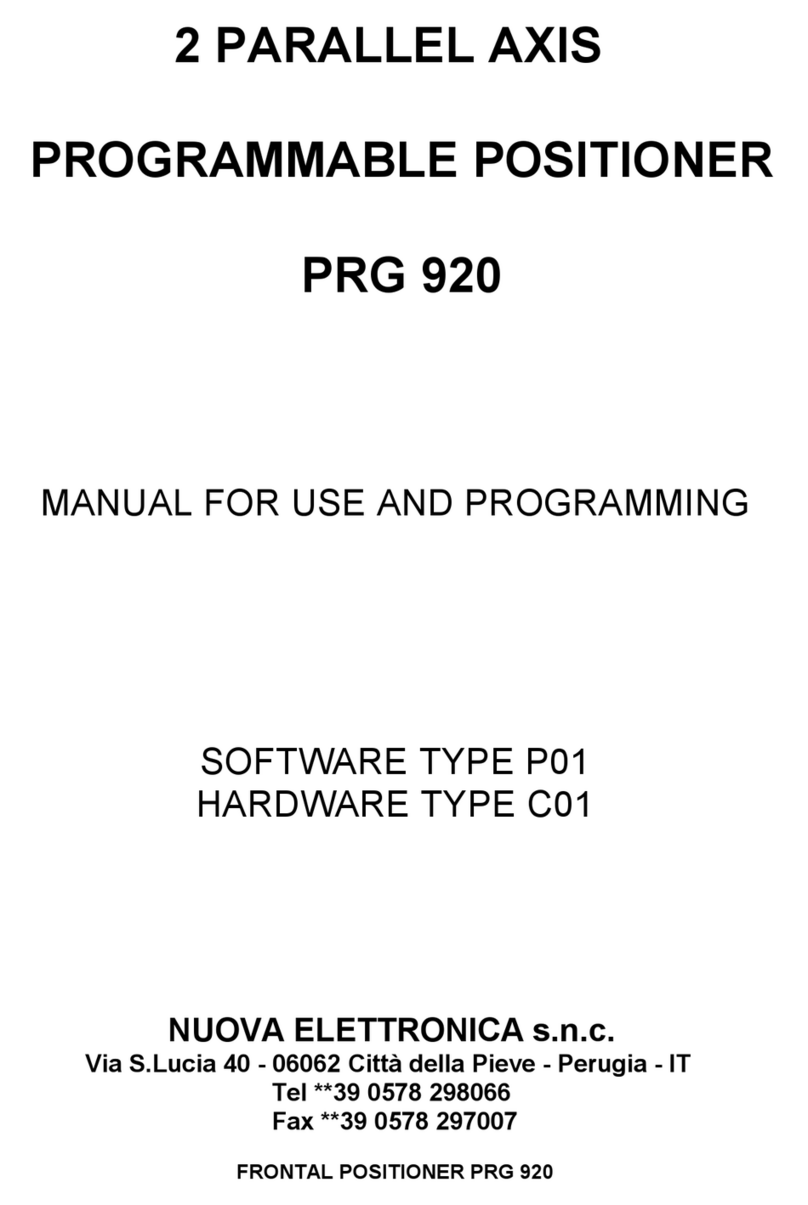
NUOVA ELETTRONICA
NUOVA ELETTRONICA PRG 920 Manual For Use and Programming