EMKO esm-4450 User manual

ESM-4450 48x48 1/16 DIN Process Controller
- 4 4 digits process set (SV) display
(TC, RTD, mV , V , mA )
- Dual or multi point calibration for oltage / Current input
- Adaptation of PID coefficients to the system with Auto-tune and
Self-tune
- Manual/Automatic mode selection for control outputs
- Bumpless transfer
- Programmable heating, cooling and alarm functions for control
outputs
- Motorized valve control function
- 8 steps profile control ( Ramp & Soak ) function and start-hold-
stop by using logic input module
- Remote set point function by using analogue input modules
- Retransmission of process value or process control by using
0/4...20 mA Current Output Module
- Hardware configuration by using input/output modules
Z Z Z
Z
Z
V
- Detection of heater failure by using 0...5A CT input moduleV
digits process (PV) and
- Universal process input
- Optional secondary sensor input
- Configurable ON/OFF, P, PI, PD and PID control forms
- Smart I/O module system
- RS-232 (standard) or RS-485 (optional) serial communication
with Modbus RTU protocol
ESM-4450 48 x 48 1/16 DIN
Universal Input PID Process Controller with
Smart I/O Module System
Instruction Manual. ENG ESM-4450 02 V09 10/05

2
Instruction manual of ESM-4450 Process Controller consists of two main sections.
Explanation of these sections are below. Also, there are other sections which include order
information and technical specifications of the device. All titles and page numbers in instruction
manual are in “ ” section. User can reach to any title with section number.
In this section, physical dimensions of the device, panel mounting, electrical wiring,
module mounting to the device, physical and electrical installation of the device to the system are
explained.
In this section, user interface of the device, how to access to the parameters, description of
the parameters are explained.
CONTENTS
Installation:
Operation and Parameters:
Also in these sections, there are warnings to prevent serious injury while doing the
physical and electrical mounting or using the device.
Explanation of the symbols which are used in these sections are given below.
This symbol is used to determine the dangerous situations as a result of an electric
shock. User must pay attention to these warnings definitely.
a
cThis symbol is used for safety warnings. User must pay attention to these
warnings.
In parameters section, for making relevant parameters to be active, determined
module must be installed to Module-1 or Module-2 socket.
This symbol is used to determine the important notes about functions and usage of
the device.
ABOUT INSTRUCTION MANUAL
i

3
1.PREFACE............................................................................................................................................
2.INSTALLATION....................................................................................................................................
3.ELECTRICAL WIRINGS......................................................................................................................
4.DEFINITIONS AND SPECIFICATIONS OF MODULES......................................................................
5.CONNECTION TERMINALS OF INPUT/OUTPUT MODULES AND CONNECTION WIRINGS........
1.1 GENERAL SPECIFICATIONS
1.2 ORDERING INFORMATION
2.1 GENERAL DESCRIPTION
2.2 DIMENSIONS
2.3 PANEL CUT-OUT
2.4 ENVIRONMENTAL RATINGS
2.5 PANEL MOUNTING
2.6 INSTALLATION FIXING CLAMP
2.7 REMOVING FROM THE PANEL
3.1 TERMINAL LAYOUT AND CONNECTION INSTRUCTIONS
3.3 CONNECTION OF DEVICE SUPPLY VOLTAGE INPUT
3.4 PROCESS INPUT CONNECTION
3.4.1 TC (THERMOCOUPLE) CONNECTION
3.4.3 CONNECTION OF SERIAL TRANSMITTERS WITH CURRENT
OUTPUT
3.4.5 CONNECTION OF TRANSMITTERS WITH VOLTAGE OUTPUT TO PROCESS
INPUT
4.1 INPUT MODULES
4.1.1 EMI-400 DIGITAL INPUT MODULE
4.1.2 EMI-410 0/4...20mA CURRENT INPUT MODULE
4.1.4 EMI-430 TC OR 0...50mV INPUT MODULE
4.1.5 EMI-440 PT-100 INPUT MODULE
4.2 OUTPUT MODULES
4.2.1 EMO-400 RELAY OUTPUT MODULE
4.2.2 EMO-410 SSR DRIVER OUTPUT MODULE
4.2.3 EMO-420 DIGITAL (TRANSISTOR) OUTPUT MODULE
4.2.4 EMO-430 0/4 ...20mA CURRENT OUTPUT MODULE
4.3 INSTALLING AND PULLING OUT INPUT/OUTPUT MODULES
4.4 TO STICK INPUT/OUTPUT MODULES’ LABELS TO THE DEVICE
5.1 CONNECTION WIRINGS FOR INPUT MODULES
5.1.3 CONNECTION OF SERIAL TRANSMITTER (LOOP POWERED) TO EMI-410
0/4...20mA CURRENT INPUT MODULE
5.1.4 CURRENT TRANSFORMER CONNECTION TO EMI-420
5.1.5 CONNECTION OF EMI-430 TC OR INPUT MODULE
5.1.6 USING EMI-430 TC or 0...50mV INPUT MODULE AS 0...50mV INPUT
1.3 WARRANTY
1.4 MAINTENANCE
3.2 ELECTRICAL WIRING DIAGRAM
3.4.2 RTD CONNECTION
PROCESS INPUT
(LOOP POWERED)
3.4.4 PROCESS INPUT CONNECTION OF 3-WIRE TRANSMITTERS WITH CURRENT
OUTPUT
3.5 RELAY OUTPUT CONNECTION
3.6 GALVANIC ISOLATION TEST VALUES OF ESM-4450 PROCESS CONTROLLER AND
INPUT/OUTPUT MODULES
4.1.3 EMI-420 0...5A CT INPUT MODULE
4.1.6 EMI-450 0...10V INPUT MODULE
5.1.1 CONNECTION OF EMI-400 DIGITAL INPUT MODULE
5.1.2 CONNECTION OF 3-WIRE TRANSMITTER TO EMI-410 0/4...20mA CURRENT
INPUT MODULE
0...5A CT INPUT
MODULE
0...50mV
Z
Z
Z
Z
Z Z
V
Z
Z
V
Z
CONTENTS
Page 6
Page 30
Page 21
Page 14
Page 9

4
5.1.7 CONNECTION OF EMI-440 PT-100 INPUT MODULE
5.1.8 CONNECTION OF EMI-450 0...10V INPUT MODULE
5.2 CONNECTION WIRINGS FOR OUTPUT MODULES
5.2.1 EMO-400 RELAY OUTPUT MODULE CONNECTION
5.2.2 EMO-410 SSR DRIVER MODULE CONNECTION
5.2.3 EMO-420 DIGITAL (TRANSISTOR) OUTPUT MODULE CONNECTION
5.2.4 EMO-430 0/4 ...20mA CURRENT OUTPUT MODULE CONNECTION
5.2.5 TO GET 0...10V WITH EMO-430 0/4 ...20mA CURRENT OUTPUT MODULE
6.1 CABLE CONNECTION BETWEEN RS-232 TERMINAL OF THE DEVICE AND PC
6.2 CONNECTION FOR RS-485 SERIAL COMMUNICATION
6.3 INSTALLING RS-232 / RS-485 SERIAL COMMUNICATION MODULES TO THE
DEVICE
7.1 DEFINITION OF FRONT PANEL
7.2 OBSERVATION OF OPTIONAL MODULES AND SOFTWARE REVISION ON THE
DISPLAYS
7.3 ADJUSTMENT OF PROCESS SET VALUE
7.4 ACCESSING TO THE OPERATOR MENU
7.5 ACCESSING TO THE TECHNICIAN MENU
7.6 ADJUSTMENT OF ALARM SET VALUES
7.7 CHANGING AND SAVING PARAMETER VALUES
8.1 OPERATOR PARAMETERS
Z
Z
Z Z
6.CONNECTIONS FOR RS-232 / RS-485 SERIAL COMMUNICATION................................................
7.DEFINITION OF FRONT PANEL AND ACCESSING TO THE PARAMETERS..................................
8.PARAMETERS.....................................................................................................................................
9.FAILURE MESSAGES IN ESM-4450 PROCESS CONTROLLERS...................................................
10.SPECIFICATIONS..............................................................................................................................
8.1.1 PROCESS AND ALARM SET PARAMETERS
8.1.2 SELECTION OF PID TUNE AND OPERATION FORM
8.1.3 FUNCTION SELECTION FOR TOP AND BOTTOM DISPLAY
8.1.4 CONFIGURATION OF RAMP/SOAK FUNCTION AND STEP SET VALUES
8.2 TECHNICIAN PARAMETERS
8.2.1 PROCESS INPUT TYPE AND RELEVANT PARAMETERS WITH PROCESS INPUT
8.2.2 PID CONFIGURATION PARAMETERS
8.2.3 MODULE-1 CONFIGURATION PARAMETERS
8.2.4 MODULE-2 CONFIGURATION PARAMETERS
8.2.5 OUTPUT-3 CONFIGURATION PARAMETERS
8.2.6 GENERAL PARAMETERS
8.2.7 PARAMETERS FOR CONFIGURATION OF SERIAL COMMUNICATION
8.2.8 OPERATOR AND TECHNICIAN PASSWORDS
Page 59
Page 119
Page 37
Page 40
Page 116

5
Manufacturer Company Name : Emko Elektronik A.S.
Manufacturer Company Address: DOSAB, Karanfil Sokak, No:6, 16369 Bursa, Turkiye
The manufacturer hereby declares that the product conforms to the following
standards and conditions.
Product Name : Process Controller
Model Number : ESM-4450
Type Number : ESM-4450
Product Category : Electrical equipment for measurement, control and
laboratory use
Conforms to the following directives :
73 / 23 / EEC The Low Voltage Directive as amended by 93 / 68 / EEC
89 / 336 / EEC The Electromagnetic Compatibility Directive
Has been designed and manufactured according to the following specifications
EN 61000-6-4:2001 EMC Generic Emission Standard for the Industrial Environment
EN 61000-6-2:2001 EMC Generic Immunity Standard for the Industrial Environment
EN 61010-1:2001 Safety Requirements for electrical equipment for measurement,
control and laboratory use
EU DECLARATION OF CONFORMITY

ESM series process controllers are designed for measuring and controlling temperature
and any process value.They can be used in many applications with their universal process input,
multifunction control outputs, selectable alarm functions, serial communication unit and
input/output modules.
Some application fields and applications which they are used are below:
1.Preface
Input/Output Module-1
Process Input
Power Supply
Input
Optional
1.1 General Specifications
ESM-4450
Optional
Optional
Standard
Standard
Standard
Control Output
Alarm Output
Re-Transmission Output
Relay, SSR Driver,
Current Output Module
Digital (Transistor) ,
Analogue Input Modules
TC, PT-100, Voltage/
Current
Z
Universal Process Input
TC,RTD, Voltage/CurrentZ
Universal Supply Input
100-240 V , 50/60HzV
Logic Input Module
- 2nd Sensor Input
- Remote Set Input
- Multi point calibration for
Voltage/Current inputZ
Start and Stop function for
RAMP/SOAK
Selection of Manual /
Automatic operation for
process control output
Control Output
Alarm Output
Heating-Cooling Function
ON/OFF, PID Operation
Auto-Tune, Self-Tune
Automatic/Manual Operation
Input/Output Module-2
Output-3(Relay Output)
Serial Communication RS-232 Baud Rate from 1200 to
19200
Modbus RTU Protocol
RS-485
6
Low Voltage (optional)
Supply Input
24V 50/60Hz ,24V ,
12V
V Z
Z
Glass Motorized valve control
Plastic Profile Control
Petro-Chemistry PID Process Control
Textile Heater Failure detection
Automative
Machine production industries
Application Fields Applications
VCT Input Module - Detection of heater failure

ESM-4450 (48x48 1/16 DIN)
A BC D E FG HI /
/
U V W Z/
/
20 Configurable (Table-1) Table-1
Input Type ScaleBC
1 Relay Output
Output-1E
Table-1
41
42
43
44
45
0...50 mVZ
0...5 VZ
0...10 VZ
0...20 mAZ
4...20 mAZ
-1999
-1999
-1999
-1999
-1999
9999
9999
9999
9999
9999
Input Type ( Voltage and Current)ZScaleBC
0
1
2
None
RS-232
RS-485
Serial CommunicationD
-
EMC-400
EMC-410
Product Code
1.2 Ordering Information
1
V
Z
W
Symbol means Vac,
Symbol means Vdc
Symbol means Vac and Vdc
c
7
Supply Voltage
100-240V (- ) 50/60HzV15%;+10%
24 V (- 50/60Hz 24V (-V Z15%;+10%) 15%;+10%)
12 V (-Z15%;+10%)
A
1
2
6
Customer (Maximum 240V (- ))50/60HzV15%;+10%
9
00
01
02
03
04
07
08
09
None
EMO-400
Relay Output Module
EMO-410
SSR Driver Output Module
EMO-420
Digital (Transistor) Output Module
EMO-430
EMI-400
Digital Input Module
EMI-410
0/4...20 mA Current Input ModuleZ
EMI-420
0...5A CT Input ModuleV
Module-2HI
-
Product Code
Current Output Module ( 0/4 ...20 mA )Z
10
11
TC or 0...50mV Input ModuleZEMI-430
PT-100 Input Module EMI-440
12 EMI-450
0...10 V Input ModuleZ
00
01
02
03
04
07
08
09
10
11
None -
Relay Output Module EMO-400
SSR Driver Output Module EMO-410
Digital (Transistor) Output Module EMO-420
EMO-430
Digital Input Module EMI-400
0/4...20 mA Current Input ModuleZEMI-410
0...5A CT Input ModuleVEMI-420
TC or 0...50mV Input ModuleZEMI-430
PT-100 Input Module EMI-440
Module-1 Product Code
FG
Current Output Module ( 0/4 ...20 mA )Z
12 EMI-450
0...10 V Input ModuleZ
21
39
40
22
23
25
27
27
29
31
33
35
37
24
26
28
28
30
32
34
36
38
L ,Fe Const DIN43710
PT 100 , IEC751(ITS90)
PT 100 , IEC751(ITS90)
L ,Fe Const DIN43710
J ,Fe CuNi IEC584.1(ITS90)
K ,NiCr Ni IEC584.1(ITS90)
R ,Pt13%Rh Pt IEC584.1(ITS90)
S ,Pt10%Rh Pt IEC584.1(ITS90)
T ,Cu CuNi IEC584.1(ITS90)
B ,Pt30%Rh Pt6%Rh IEC584.1(ITS90)
E ,NiCr CuNi IEC584.1(ITS90)
N ,Nicrosil Nisil IEC584.1(ITS90)
C , (ITS90)
R ,Pt13%Rh Pt IEC584.1(ITS90)
S ,Pt10%Rh Pt IEC584.1(ITS90)
T ,Cu CuNi IEC584.1(ITS90)
B ,Pt30%Rh Pt6%Rh IEC584.1(ITS90)
E ,NiCr CuNi IEC584.1(ITS90)
N ,Nicrosil Nisil IEC584.1(ITS90)
C , (ITS90)
J ,Fe CuNi IEC584.1(ITS90)
K ,NiCr Ni IEC584.1(ITS90)
-100°C,850°C
-200°C,650°C
-199.9°C,650.0°C
-100.0°C,850.0°C
-200°C,900°C
-200°C,1300°C
0°C,1700°C
0°C,1700°C
-200°C,400°C
44°C,1800°C
-150°C,700°C
-200°C,1300°C
0°C,2300°C
-199.9°C,900.0°C
-199.9°C,999.9°C
0.0°C,999.9°C
0.0°C,999.9°C
-199.9°C,400.0°C
44.0°C,999.9°C
-150.0°C,700.0°C
-199.9°C,999.9°C
0.0°C,999.9°C
-148°F ,1562°F
-328°F,1202°F
-199.9°F,999.9°F
-148.0°F,999.9°F
-328°F,1652°F
-328°F,2372°F
32°F,3092°F
32°F,3092°F
-328°F,752°F
111°F,3272°F
-238°F,1292°F
-328°F,2372°F
32°F,3261°F
-199.9°F,999.9°F
-199.9°F,999.9°F
32.0°F,999.9°F
32.0°F,999.9°F
-199.9°F,752.0°F
111.0°F,999.9°F
-199.9°F,999.9°F
-199.9°F,999.9°F
32.0°F,999.9°F
Input Type(TC)
Input Type(RTD)
Scale(°C)
Scale(°C)
Scale(°F)
Scale(°F)
BC
BC
All order information of ESM-4450 are
given on the table at left. User may form
appropriate device configuration from
information and codes that at the table and
convert it to the ordering codes.
F i r s t l y, s u p p l y v o l ta g e t h e n
i n p u t / o u t p u t m o d u l e s a n d o t h e r
specifications must be determined. Please
fill the order code blanks according to your
needs.
Please contact us, if your needs are
out of the standards.
EMI-400, EMO-410, EMO-420 and
EMC-410 modules can not be
used in 12V type.Z
i

8
1.3 Warranty
EMKO Elektronik warrants that the equipment delivered is free from defects in material and
workmanship. This warranty is provided for a period of two years. The warranty period starts from
the delivery date. This warranty is in force if duty and responsibilities which are determined in
warranty document and instruction manual performs by the customer completely.
1.4 Maintenance
Repairs should only be performed by trained and specialized personnel. Cut power to the device
before accessing internal parts.
Do not clean the case with hydrocarbon-based solvents (Petrol, Trichlorethylene etc.). Use of
these solvents can reduce the mechanical reliability of the device. Use a cloth dampened in ethyl
alcohol or water to clean the external plastic case.

In package ,
- One piece unit
- One piece mounting clamp
- One piece instruction manual
A visual inspection of this product for possible damage occured during shipment is
recommended before installation. It is your responsibility to ensure that qualified
mechanical and electrical technicians install this product.
If there is danger of serious accident resulting from a failure or defect in this unit, power
off the system and separate the electrical connection of the device from the system.
The unit is normally supplied without a power switch or a fuse. Use power switch and fuse
as required.
Be sure to use the rated power supply voltage to protect the unit against damage and to
prevent failure.
Keep the power off until all of the wiring is completed so that electric shock and trouble
with the unit can be prevented.
Never attempt to disassemble, modify or repair this unit. Tampering with the unit may
results in malfunction, electric shock or fire.
Do not use the unit in combustible or explosive gaseous atmospheres.
During the equipment is putted in hole on the metal panel while mechanical installation
some metal burrs can cause injury on hands, you must be careful.
Montage of the product on a system must be done with it’s own fixing clamps. Do not do
the montage of the device with inappropriate fixing clamps. Be sure that device will not fall
while doing the montage.
It is your responsibility if this equipment is used in a manner not specified in this
instruction manual.
Before beginning installation of this product, please read the instruction
manual and warnings below carefully.
2.Installation
c
9

10
2.1 General Description
ESM-4450
Process Controller
SET
°C
O1
°F
O2
O3
REMOTE RAMP MAN AUTO
48 mm / 1.89 inch
48mm / 1.89 inch
Maximum 5mm / 0.2 inch
2.2 Dimensions
Panel surface
(maximum thickness 5mm / 0.2 inch)
Front Panel
IP65 protection
NEMA 4X
Mounting Clamp
Product Label Terminal protection cover
ESM-4450
Process Controller
SET
°C
O1
°F
O2
O3
REMOTE RAMP MAN AUTO
104.5 mm/ 4.11 inch11.5 ± 1 mm /0.45 inch

11
65 mm / 2.56 inch (min)
65 mm / 2.56 inch (min)
46 mm / 1.81 inch (min)
46 mm / 1.81 inch (min)
2.3 Panel Cut-Out

12
Operating Temperature :
Max. Operating Humidity :
Altitude :
0 to 50 °C
90 Rh (non-condensing)
Up to 2000m.
%
Operating Conditions
Forbidden Conditions:
Corrosive atmosphere
Explosive atmosphere
Home applications (The unit is only for industrial applications)
During installation into a metal panel, care should be taken to avoid injury from
metal burrs which might be present. The equipment can loosen from vibration
and become dislodged if installation parts are not properly tightened. These
precautions for the safety of the person who does the panel mounting.
1-Before mounting the device in your
panel, make sure that the cut-out is of the
right size.
2-Check front panel gasket position
3-Insert the device through the cut-out. If
the mounting clamp are on the unit, put out
them before inserting the unit to the panel.
1
2
3
2.4 Environmental Ratings
2.5 Panel Mounting
c
c
O1
O2
O3

13
1-Loosen the screws.
2-Lift the locking tabs located on both the right and left
hand sides and pull the fixing clamp from the device
while holding the unit in place.
3-Pull the unit through the front side of the panel
Before starting to remove the unit from panel, power off the unit and the related
system.
Montage of the unit to a system must be done with it’s own fixing clamps. Do not
do the montage of the device with inappropriate fixing clamps. Be sure that
device will not fall while doing the montage.
The unit is designed for panel mounting.
1-Insert the unit in the panel cut-out from the front side.
2-Insert the mounting clamp from the rear side of the
unit and screw up the fixing screws until the unit
completely immobile within the panel
1
2
1
2
3
2
2.6 Installation Fixing Clamp
2.7 Removing from the Panel
c
c
O1
O2
O3
O1
O2
O3

14
You must ensure that the device is correctly configured for your application.
Incorrect configuration could result in damage to the process being controlled,
and/or personal injury. It is your responsibility, as the installer, to ensure that
the configuration is correct.
Device parameters has factory default values. These parameters must be set
according to the system’s needs.
Only qualified personnel and technicians should work on this equipment. This
equipment contains internal circuits with voltage dangerous to human life.
There is severe danger for human life in the case of unauthorized intervention.
Be sure to use the rated power supply voltage to protect the unit against
damage and to prevent failure.
Keep the power off until all of the wiring is completed so that electric shock and
trouble with the unit can be prevented.
3.Electrical Wirings
1
7
2
8
3
9
4
10
5
11
6
12
3.1 Terminal Layout and Connection Instructions
c
c
c
c
6 mm / 0.236 inch
Wire Size:
18AWG / 1 mm²
Solid /Stranded
12 screws terminal
M3
Optional connections
Torque 0.5 Nm
Screw driver 0.8x3mm
0.5 Nm
a

3.2 Electrical Wiring Diagram
Universal
Process Input
(TC, RTD, Voltage/Current)Z
Sensor or Transmitter
Supply Voltage
Output-3
Standard Relay Output
Supply Voltage Input
100-240V (- ) 50/60Hz
24 V (- 50/60Hz - 6VA
24V (-
12 V (-
(It must be determined in order)
V
V
Z
Z
15%;+10%
15%;+10%)
15%;+10%) - 6W
15%;+10%) - 6W
- 6VA
Electrical wiring of the device must be the same as ‘Electrical Wiring Diagram’
below to prevent damage to the process being controlled and personnel injury.
c
15
Optional Input/Output Module Terminals
Relay, SSR Driver, Digital or Current
Output Module
Digital, Analogue and CT
Input Modules
V
1
7
2
8
3
9
4
10
5
11
6
12
MODULE-1 MODULE-2
5A@250V V
OUTPUT - 3
12 V Z
Max 50mA
TC
Pt-100
0 - 20mA Z
0 - 50mV
0 - 10V
Z
Z
CAT II
P/N : ESM-4450
Y
a
cCommunication
Socket
CNO
PTC , NTC
Process input, Analogue Module Inputs (EMI-410, EMI-430, EMI-440,EMI-450)
and are in CAT II class.VCT Module Input (EMI-420)
i

Connection of Universal
Supply Voltage Input
Connection of Low Voltage 24
V Supply Voltage InputW
Supply voltage range must be determined in order. While installing the unit,
supply voltage range must be controlled and appropriate supply voltage must
be applied to the unit. Controlling prevents damages in unit and system and
possible accidents as a result of incorrect supply voltage.
There is no power supply switch on the device. So a power supply switch must
be added to the supply voltage input. In accordance with the safety regulations,
the power supply switch shall bring the identification of the relevant
instrument.Power supply switch shall be easily accessible by the user.
3.3 Connection of Device Supply Voltage Input
16
Power switch must be two poled for seperating phase and neutral. On/Off
condition of power switch is very important in electrical connection. On/Off
condition of power switch must be signed for preventing the wrong connection.
If an external fuse is used, it must be on phase connection in supply input.V
If an external fuse is used, it must be on (+) line connection in supply input.Z
Connection of Low Voltage
12V Supply Voltage
Input
Z
Note-1 :
Note-2 :
Note-3 :
There is an internal 33R fusible flameproof resistor in 100-240 V 50/60Hz
There is an internal 4R7 fusible flameproof resistor in 24V 50/60Hz , 24V and 12V
“L” is (+), “N” is (-) for 24V Supply Voltage
External Fuse is recommended.
W
W
V
V Z Z
Z
Supply Voltage
100 - 240 V
(-15%;+10%) 50/60 Hz
V24V (-15%;+10%) 50/60HzV
11
N L
12
12V (-15%;+10%)Z
Note-1
Y
11
L
12
Note-1
Y
11
-
+
12
Note-1
Y
Power
Supply
Switch
c
or 24V (-15%;+10%)Z
c c
aaa
External
Fuse
(1 A T)V
External
Fuse
(24V : 1 A T)
(24V : 1 A T)
V V
Z Z
Note-2
N
Power
Supply
Switch
External
Fuse
(1 A T)Z
Supply Voltage Supply Voltage
Power
Supply
Switch
Make sure that the power supply voltage is the same indicated on the
instrument.
Switch on the power supply only after that all the electrical connections have
been completed.
The instrument is protected with an internal fuse (Please refer to Note1 for
information). In case of failure it is suggested to return the instrument to the
manufacturer for repair.
c
c
c
Fuse
Fuse
Fuse
Note-3
Note-3
Note-3

17
3.4.2 RTD Connection
Note 1 : In 3-wire system, use always cables of the same diameter (min ) Always use
wires of the same gauge and type whether a 2-wire or 3-wire system.
1mm²
Install a jumper between terminals 2 and 3 when using a 2-wire RTD.
If the distance is longer than 10 meters, use 3-wire system
Note 2 :
Note 3 :
3-wire Pt-100 connection
(with line compensation)
(Max. Line impedance is 10 )W
2-wire Pt-100 connection
(without line compensation)
3.4.1 TC (Thermocouple) Connection
123
TC Connect the wires with the polarity as shown in the
figure left.
Always use compensation wire corresponding to the thermocouple used. If
present, the shield must be connected to a proper ground.
3.4 Process Input Connection
i
Input resistance is greater than 10M W.
i
Input resistance is greater than 10M W.
i
1 12 23 3
Pt-100
Note 1 Note 2
Pt-100

18
3.4.4 Process Input Connection of 3-Wire Transmitters with Current Output
Transmitter Transmitter
External
Power
Supply
Note 1
mAZ
PV PV
1 1
3 3
4 4
12 V
Max. 50mA
Z12 V
Max. 50mA
Z
Transmitter connection by using supply
voltage on the device
Transmitter connection by using external supply
voltage source.
Transmitter Transmitter
External
Power
Supply
Note 1
mAZmAZ
PV PV
1 1
3 3
4 4
12 V
Max. 50mA
Z12 V
Max. 50mA
Z
Note 1 : External power supply must be selected according to supply voltage range and
required current for transmitter.
mAZ
3.4.3 Process Input Connection of Serial Transmitters with Current Output (Loop
Powered)
Transmitter connection by using supply
voltage on the device
Transmitter connection by using external supply
voltage source.
Note 1 : External power supply must be selected according to supply voltage range and
required current for transmitter.
Input Resistance is 2R7 .W
i
Input Resistance is 2R7 .W
i

19
3.5 Relay Output Connection
Fuses must be selected according to the application.
c
Device
Fuse
Load
L N
Last Control Element
(Contactor)
c
3.4.5 Connection of Transmitters with Voltage Output to Process Input
Transmitter Transmitter
External
Power
Supply
Note 1
mV, VZmV, VZ
PV PV
1 1
2 2
4 4
12 V
Max. 50mA
Z12 V
Max. 50mA
Z
5A T FuseV
Transmitter connection by using supply
voltage on the device
Transmitter connection by using external supply
voltage source.
Note 1 : External power supply must be selected according to supply voltage range and
required current for transmitter.
Input resistance is greater than 10M 0...50mV
Input resistance is 43K for 0...10V
W
W
for Z
Z
i
5
6
C
NO

EMO-430
0/4...20mA
Current OutputModule
Z
0...10 VZ
2000VV
20
3.6 Galvanic Isolation Test Values of ESM-4450 Process Controller and Input/Output
Modules
Supply Input Ground 1
Output-3
Relay Output
5
6
EMO-400
Relay Output Module
7
8
9
10
EMO-410
SSR Driver Module
2000V ( For ESM-4450.1...... )
5 . ......
V
00V ( For ESM-4450 2 )V
2000VV
2000VV
500VV
EMO-420
Digital Output Module
EMI-400
Digital Input Module
EMI-410
Current Input Module
0/4...20mAZ
EMI-440
PT-100 Input Module
Analogue
Inputs
2
3
EMI-420
Input Module
0...5A CT
V
500VV
500VV
500VV
2000VV
2000VV
2000VV
2000VV
2000VV
2000VV
2000VV
2000VV
2000VV
2000VV
EMI-450
2000VV
EMI-430
TC or 0...50mV
Input Module
Z
Input Module
11
12
7
8
9
10
7
8
9
10
7
8
9
10
7
8
9
10
7
8
9
10
7
8
9
10
7
8
9
10
7
8
9
10
7
8
9
10
EMC-410
RS-485 Serial
Communication Module
EMC-400
RS-232 Serial
Communication Module
2000V V
2000V V
500V V
12V
Voltage Output
Z
2000V V
4
Table of contents
Other EMKO Controllers manuals
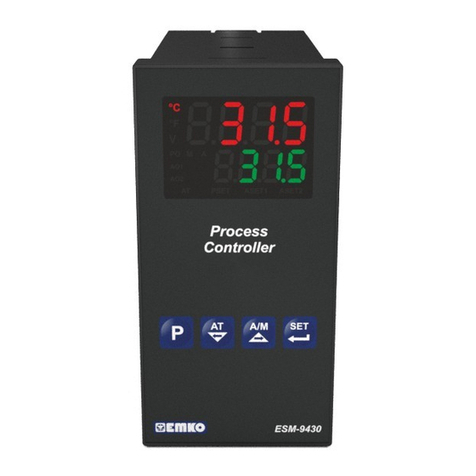
EMKO
EMKO ESM-9430 User manual
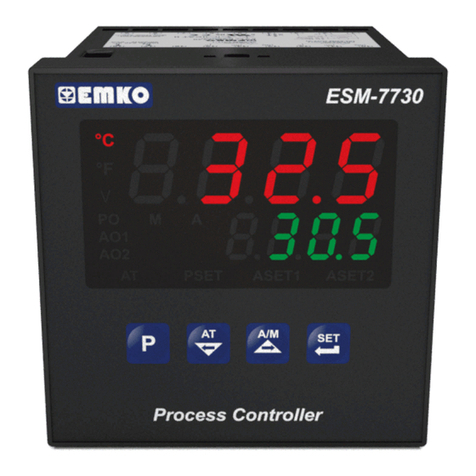
EMKO
EMKO ESM 30 Series User manual
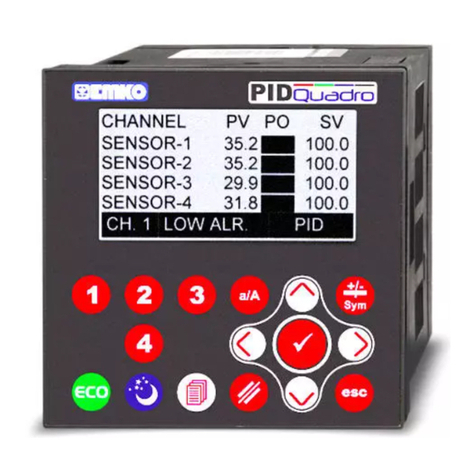
EMKO
EMKO PID QUADRO EPLC9600 User manual
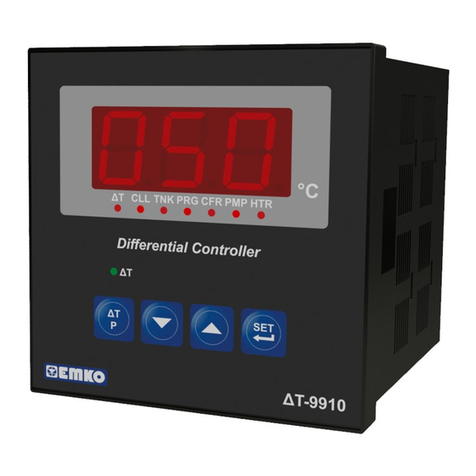
EMKO
EMKO DT-9910 User manual
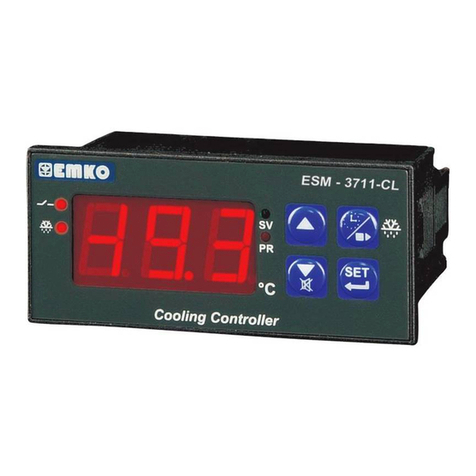
EMKO
EMKO ESM-3711-CL User manual
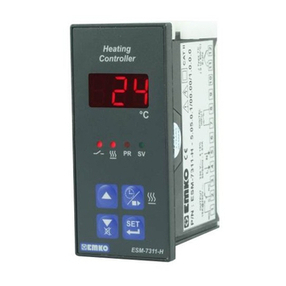
EMKO
EMKO ESM-7311-H User manual

EMKO
EMKO EAOM-9F ND User manual

EMKO
EMKO EPC-1 User manual
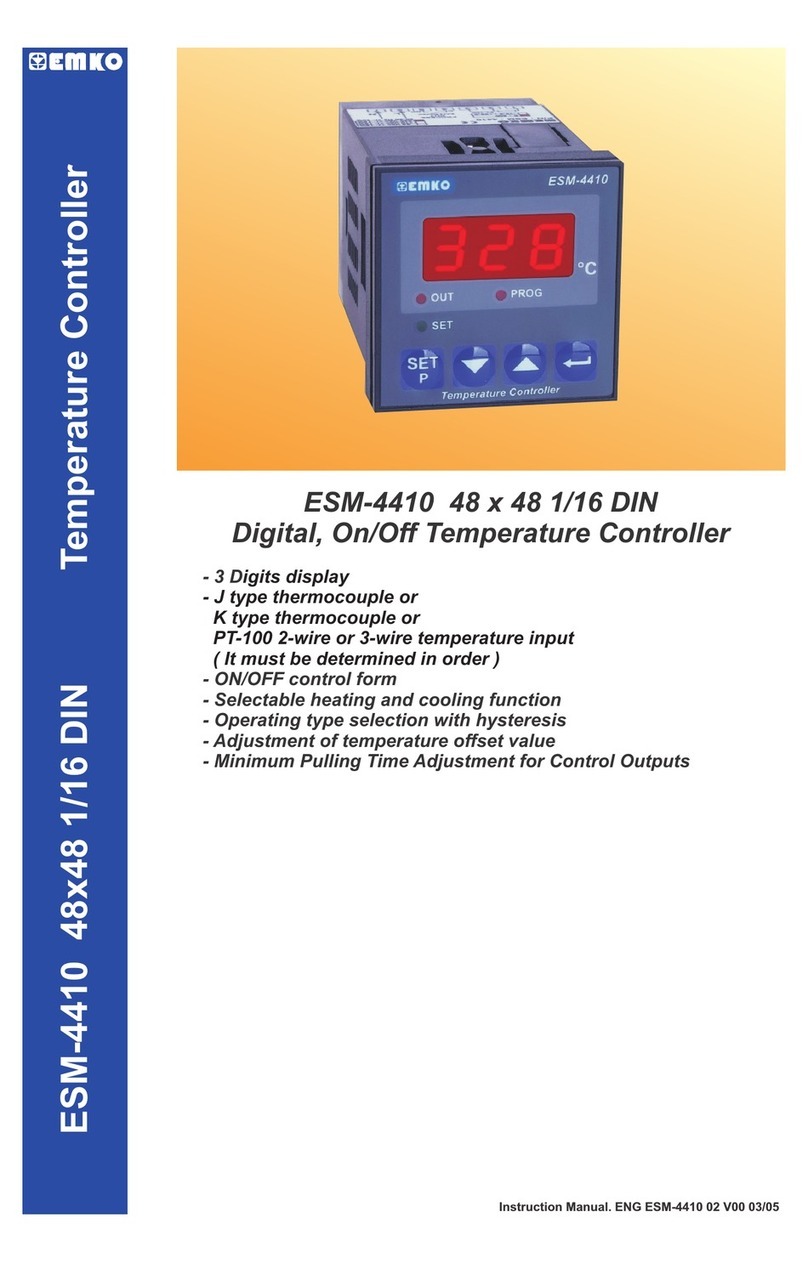
EMKO
EMKO ESM-4410 User manual
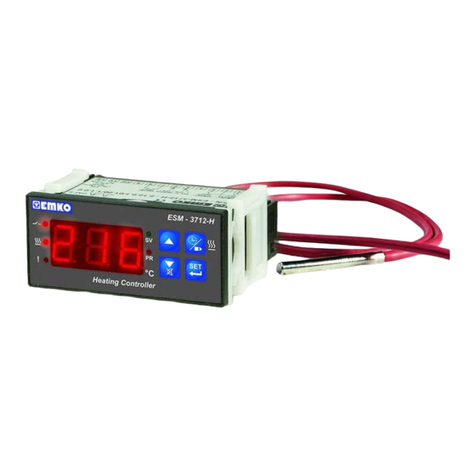
EMKO
EMKO ESM-3712-H User manual

EMKO
EMKO ESM-3711-CN User manual
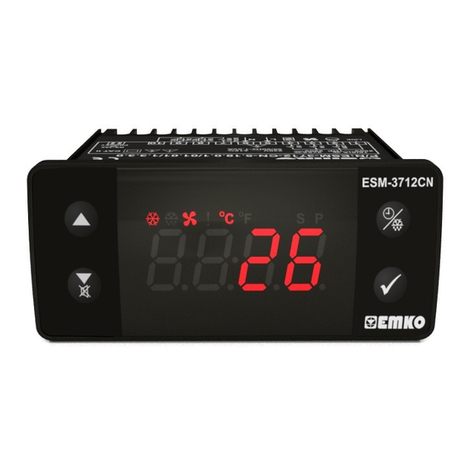
EMKO
EMKO ESM-3712-CN User manual
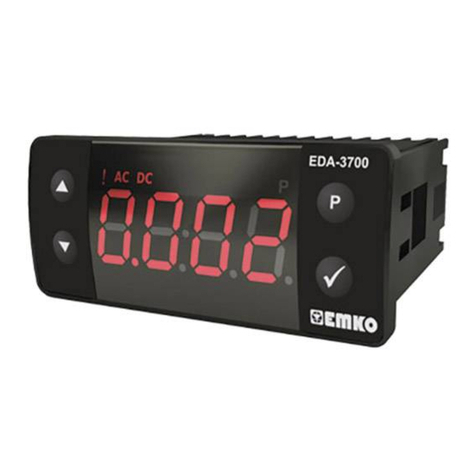
EMKO
EMKO EDA-3700 User manual
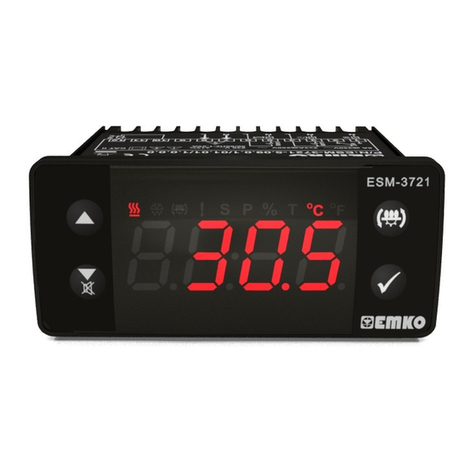
EMKO
EMKO ESM-3721HT User manual
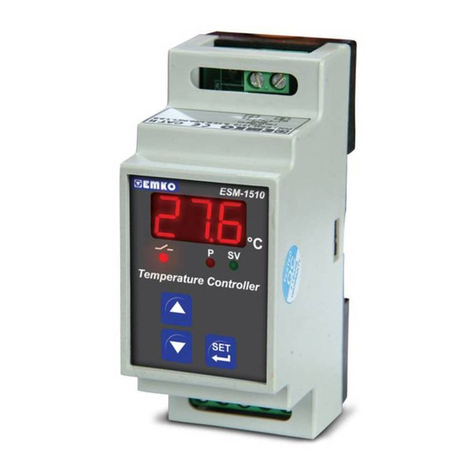
EMKO
EMKO ESM-1510 User manual
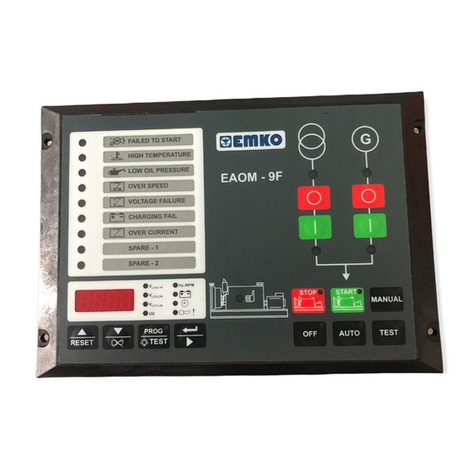
EMKO
EMKO EAOM-9F ND User manual
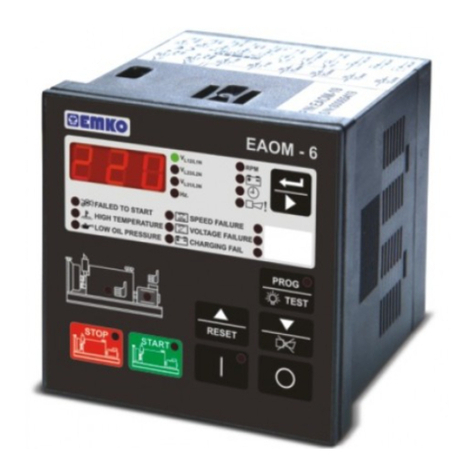
EMKO
EMKO EAOM-6 User manual
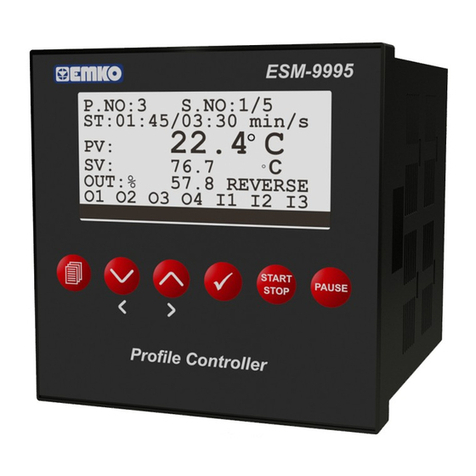
EMKO
EMKO ESM-9995 User manual
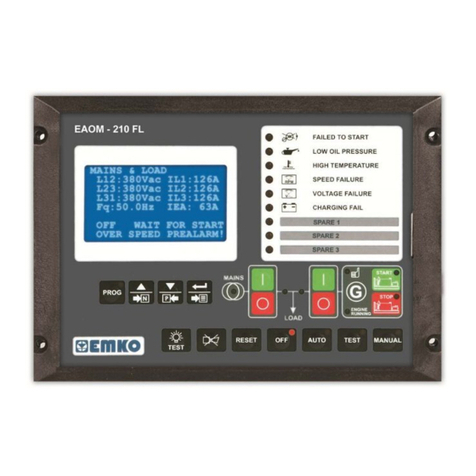
EMKO
EMKO EAOM-210 FLJ User manual
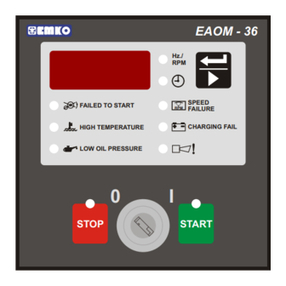
EMKO
EMKO EAOM-36 Series User manual