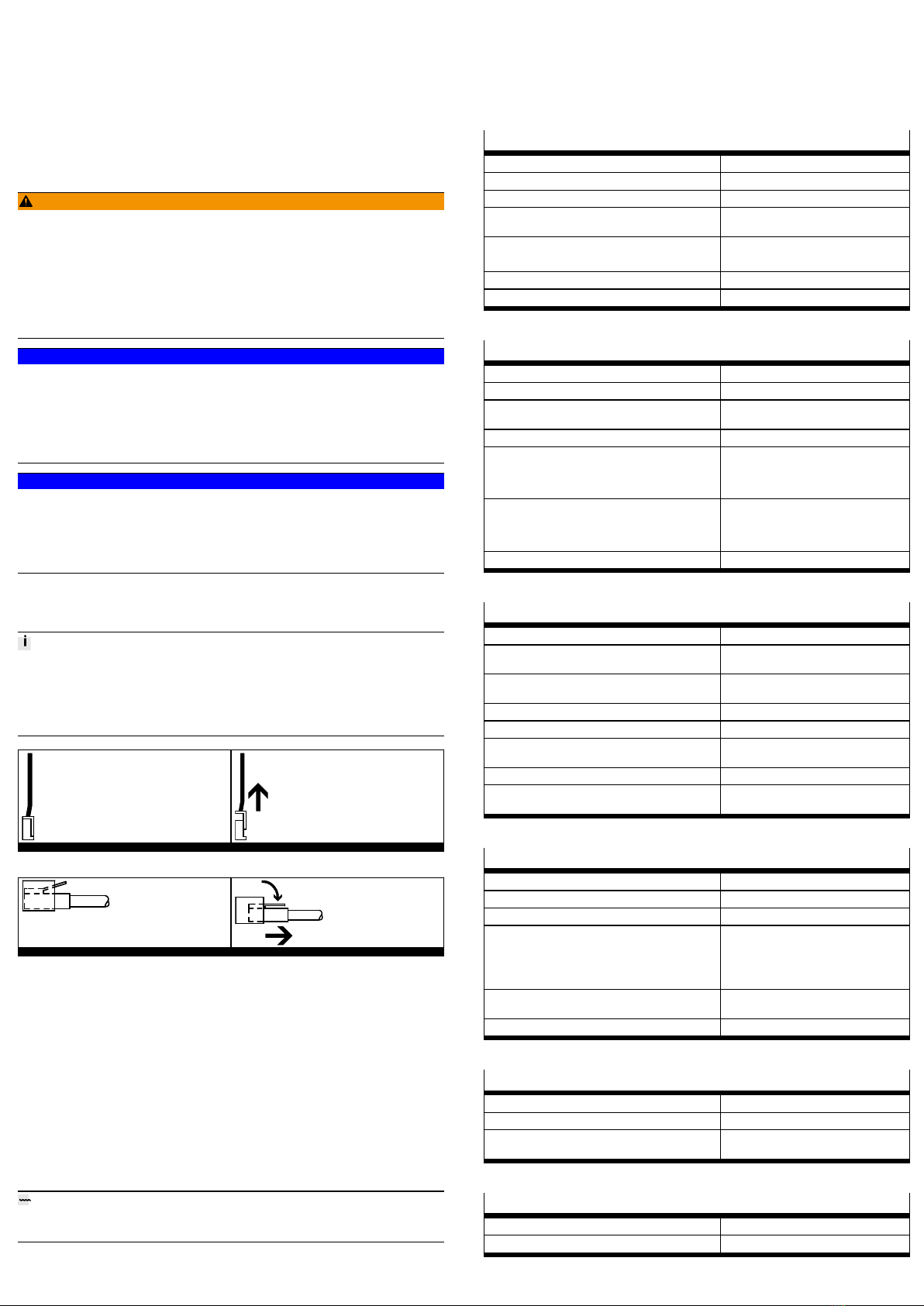
5. Fix the grommet with a size 19 spanner (torque: 3 Nm).
6. Insert the main plug and the RJ45 plug into the sockets provided for this pur
pose.
7. Tighten the strain relief with the spanner. Part of the cable sheath should be
located inside the housing. Make sure that the rubber ring for the strain relief
is correctly under the grommet.
8. Attach cover and screw in the TORX screws (torque: 0.8…1.0 Nm).
Unplug cable
1. Pull the cable with your fingers to unplug the main plug.
2. To RJ45plug, actuate the locking lever.
7.2 Cable installation in the connection shaft
WARNING!
Failure of the emergency stop or the enabling function.
Failure of the emergency stop or enabling functions can result in personal injury
and material damage.
• When plugging in, make sure that the main plug engages correctly.
• Check the emergency stop and enabling functions before recommissioning
the handheld terminal CDSAD3RV.
• Check the emergency stop and enabling functions before commissioning the
machine or system.
NOTICE!
Incorrect handling when closing the connection shaft.
Incorrect handling can damage the cables and the connection shaft.
• The seal must be clean, undamaged and in the correct position.
• Do not pinch the cable.
• Screw on the cover of the connection shaft with all screws and tighten to a
torque of 0.8 to 1.0Nm.
NOTICE!
Incorrect handling of the plug when working in the connection shaft.
Incorrect handling can damage the plugs and the socket.
• Do not use sharp objects to remove the plugs.
• Disconnect the main plug by pulling its wires with fingers.
• Press the locking lever to disconnect the RJ45 plug.
When the connection shaft is opened, the connecting cables can be positioned as
shown in the following sections. Before opening the handheld terminal
CDSAD3RV observe the following instructions:
Information for opening the connection shaft
• Place the handheld terminal CDSAD3RV with the display facing downwards
on a flat, clean and soft base so that the handheld terminal CDSAD3RV or its
operating elements are not damaged (e.g. ESD mat).
• To open and close the connection shaft, use a "TORX size 10" screwdriver.
Tab. 7 Unplugging the main plug
Tab. 8 Unplugging the RJ45 plug
8 Maintenance
9 Repair
Repair or maintenance of the product by unauthorised persons is not permitted;
this may invalidate the conformity of the product.
If necessary, replace the complete product.
– If a safety device is defective, the product must be replaced.
– In this case, send the defective product unchanged with a description of the
fault and application to Festo for analysis.
– Check with your regional Festo contact person to clarify the conditions for the
return shipment.
10 Disposal
ENVIRONMENT!
Dispose of the product and packaging according to the applicable provisions of
environmentally sound recycling.
10.1 Safety-related control elements
After expiry of the service life T10D, but no later than after 20 years, the safety
related control elements "Emergency stop device" and "3position enabling
switch" must be permanently disabled.
11 Technical data
11.1 Handheld terminal CDSA-D3-RV
Emergency stop device
Nominal voltage (Ue) [VDC] 24
Minimum current (Ie) [mA] 10 (per contact)
Max. current rating [mA] 1,000 (per contact)
Utilisation category (in accordance with
IEC 6094751)
DC13
Schlegel FRVKOO
– B10D 250,000
Design twocircuit, external wiring
Electrical isolation [VAC] 500 to all other networks
Tab. 9 Emergency stop device
3-position enabling switch
Output type Electromechanical switching contact
Switchable nominal voltage (Ue) [VDC] 24
Nominal voltage tolerance range (in
accordance with EN 611312)
[VDC] 19.2…30
Max. nominal current (Ie) [mA] 500
B10D
– Switch setting 2 106
– Switch setting 3 106
Actuating forces
– From switch position 1 to 2 Typically 3 N
– From switch position 2 to 3 Typically 17 N
Electrical isolation [VAC] 500 to all other networks
Tab. 10 3position enabling switch
Technical data, general
Nominal voltage [VDC] 24
Nominal voltage tolerance range (in
accordance with EN 611312)
[VDC] 19.2…30
Max. interruption duration of the supply
voltage (in accordance with EN 611312)
[ms] £ 10
Max. starting current [A] 5.6 (current limitation available)
Power consumption [W] 12 (500mA at 24 V DC)
Protection class (in accordance with
EN 611312 and/or EN 50178)
III
Degree of protection IP65
CE certification See declaration of conformity
èwww.festo.com
Tab. 11 Technical data, general
Ambient conditions
Operating temperature [°C] 0…40
Storage temperature [°C] –25…70
Relative humidity (noncondensing) [%] 5…95
Vibration resistance (in accordance with
IEC 6006826)
– With 3.5 mm [Hz] 5 £ f < 8.4
– With 1g [Hz] 8.4 £ f < 150
Shock resistance (in accordance with
EN 611312)
[g/ms] 15/11
Max. operating altitude (sea level) [m] 2,000
Tab. 12 Ambient conditions
Mechanical characteristics
Design Housing made of ABS
Flammability UL94V0
Fallproof suitability [m] 1.5 (on industrial floor), then at least
degree of protectionIP54
Tab. 13 Mechanical characteristics
Dimensions, weight
Height [mm] 251
Width [mm] 212