Penn A11 Series User manual

A11 Series Low Temperature Cutout Control
Installation Guide
Applications
A11 Series low temperature cutout controls are available
with single-pole, single-throw (SPST) or single-pole,
double-throw (SPDT) contact action. Applications include
the sensing of low temperature conditions to avoid
overcooling or icing of hydronic coils, cooling coils, and
liquid handling pipes. The controls are compact and
sturdy, and have an adjustable temperature setpoint
range with a fixed differential. You can access the range
adjustment screw at the bottom of the control, or at the
top of the control when you remove the cover.
Important: All A11 Series coil temperature controls
are designed for use only as operating controls.
Where an operating control failure would result
in personal injury and/or loss of property, it is
the responsibility of the installer to add devices
(safety, limit controls) or systems (alarm, supervisory
systems) that protect against, or warn of, control
failure.
Required tools
Use the following tools to install the control:
• 1/2 in. (1.3 cm) electrical metallic tubing (EMT) bender
• Hole saw
• Tin snips or hack saw
• Vise
• Brackets
• 4 in. (10.1 cm) electrical box covers with a center hole
knockout, or T-752-1001 1/2 in. (1.3 cm) duct flanges
• Nylon tie wraps with holes
• 1/2 in. (1.3 cm) EMT connectors
• 1/4 in. (6.4 mm) poly tubing
• Copper tubing
• EMT or Unistrut
• Conduit hangers or Minerallac straps
• Self-tapping sheet metal screws
• Machine screws and nuts
• A11 Low Temperature Cutout Control
• Element mounting bracket
Mounting
Before you begin:
Do not install A11 controls where the ambient
temperature at the control exceeds 140°F (60°C), or
falls below 0°F (-18°C). Make sure that the maximum
temperature at the sensing bulb does not exceed 250°F
(121°C).
1. Locate the sensing element on the downstream
side of the coil. Expose the element to all areas
where low temperatures may occur.
2. Horizontally serpentine the 20 ft (6.1 m) long
sensing element across the face of the coil to sense
temperatures in all areas.
Ensure that the horizontal pitch of the coil does
not exceed 5° (one in. per ft) for the areas that you
want to protect. See Figure 1.
Mounting considerations
The primary purpose of a low limit cutout is to prevent a
coil from freezing. Before you mount the control, consider
the following factors:
• It is vital that you protect the lower 6 in. (15.20 cm) of
the coil, because cool air drops to the bottom of the
coil.
• If the tubes in the coil freeze, the coil can crack and
leak. As water leaks from the coil, the control system
may sense the reduced water pressure and increase the
flow of water to compensate for the loss, which causes
even more damage.
• It is important to follow all instructions to install low
limit controls because the low limit controls incorporate
a vapor-charged sensing element. The vapor in the
element creates a change in pressure with a change
in temperature within the sensing element, eventually
causing the electrical switch in the device to open or
close.
• The size of the duct work or air handling unit system in
which you install the device may require more than one
low limit control to adequately protect the entire coil.
• System accessibility affects how you mount the device.
Larger Air Handling Units (AHUs) often provide access
to the coil, providing you space to effectively serpentine
the capillary across its face. (See Mounting in an
accessible location.) Smaller AHUs or duct work may
not provide direct accessibility, which means you need
to pre-assemble the control before installation. (See
Mounting in an inaccessible location.)
• Mount the sensing element with a slight decline of
approximately 1 in. (25 mm) for every 1 ft (305 mm) of
drop, as illustrated in Figure 1 and listed in Table 1.
997-358 Rev. J
2021-08-20
A11A, A11B, A11D, A11E

Figure 1: Mounting sensing element inside coil
Note: Allow for 1 in. (25 mm) of drop per 1 ft (305
mm) of run.
Table 1: Maximum drop by unit width
Unit width, ft (m) Maximum drop per
segment, in. (mm)
Callout A Callout B
5 (1.5) 5.25 (133)
10 (3.0) 10.50 (267)
15 (4.6) 15.75 (400)
20 (6.1) 21.00 (533)
25 (7.6) 26.25 (667)
30 (9.1) 31.50 (800)
Alternate installations
Alternate installations are shown in Figure 2 and Figure
3. If you select these installation methods, mount the
temperature control above the sensing element whenever
possible. If you cannot mount the control above the
element, loop the capillary or element slightly below the
control, then route the element toward the top of the coil,
and begin serpentining in a downward direction from the
top of the coil.
Keep the loop as short as possible, maximum of 4 ft (1.2
m). If you mount the control below the sensing element,
prevent possible nuisance alarms by mounting the control
in a conditioned space. When using the A11 Series control,
coil the excess capillary inside the conditioned space and
secure. The excess capillary is the small capillary between
the control and sensing element.
Figure 2: Mounting options - inside the duct
Figure 3: Mounting options - outside the duct
Table 2: Mounting options
Callout Description
A Control mounted inside duct, duct
surrounded by unconditioned space
B Control mounted inside duct, space
surrounding duct is unconditioned
C Ductwork installed inside conditioned space
only
D Ductwork installed in heated space only
E Ductwork inside heated or unheated space
Mounting guidelines
CAUTION
Risk of Environmental and Property Damage
Avoid sharp bends in capillary tubes. Sharp bends
can weaken or kink capillary tubes, which may result
in refrigerant leaks or restrictions of flow.
A11 Series Low Temperature Cutout Control Installation Guide2

CAUTION
Risk of Environmental and Property Damage
Coil and secure excess capillary tubing away from
contact with sharp or abrasive objects or surfaces.
Vibration and sharp or abrasive objects in contact
with capillary tubes can cause damage that may
result in release of the chemical charge in the
sensing element, which may result in damage to the
environment or property.
CAUTION
Risk of Property Damage
Do not dent or deform the sensing bulb. Dents or
deformations in the sensing bulb can change the
calibration, may cause the control to operate at
temperatures other than the setpoint, and may result
in other property damage.
Important:
• When you drill holes or drive screws to mount the
sensing elements, be careful not to puncture or
damage hydronic coils.
• Use only the mounting screws supplied with the
Universal Mounting Bracket to avoid damage to
the internal components. Be careful not to distort
or bend the control case when you mount the
control to an uneven surface. The use of other
screws or bending the control case voids the
warranty.
• Locate the control case and bellows where the
ambient temperature is always warmer than
the setpoint. The control operates only from
the lowest temperature along any 14 in. to 16
in. (356 mm to 406 mm) length of the sensing
element.
• Locate low temperature cutout controls in areas
protected from the effects of weather. If you
mount the control in an area that is exposed to
the weather or other wet environments, equip it
with an outdoor enclosure.
• It is important to mount the low temperature
cutout control in the correct location. Expose the
capillary to all areas on the coil where a risk of low
temperatures is present.
Observe the following guidelines when you mount A11
Series low temperature cutout controls.
• Mount the control upright in an accessible location,
where the control body, capillary tube, and sensing
bulb are not subject to damage, and the control is in
the highest possible position of the entire installation.
• Mount the control upstream from mixed air or chilled
water coils.
• Mount the control downstream from preheat coils.
• Mount the control upright on flat, vertical, or horizontal
surfaces using accessory brackets. These controls have
NEMA 1 enclosures.
• Mount the capillary in a serpentine fashion so that it
slopes gently downhill at an angle not greater than 5°.
Do not permit any dips, bends, or kinks in the capillary,
and install the last segment within 6 in. (152.4 mm) of
the bottom of the coil.
Figure 4: Control capillary orientation
Table 3: Control capillary orientation
Callout Description
A Correct. Orient the capilliary horizontally.
B Incorrect. Do not orient the capilliary
vertically.
Mounting in an accessible location
Before you begin:
Sometimes, the coil face offers nothing that can hold
the tie-wrapped sensing element. In these cases, use
1/2 in. (13 mm) EMT, hard copper tubing, or Unistrut to
build supports to fasten the sensing element. Fasten the
sensing element to fixed supports to hold the element
in place and prevent movement in the air stream. Field-
fabricated supports often take the form of a rack with
vertical supports. To determine the proper location, see
Figure 1.
1. Determine the best mounting location for the low
temperature cutout control. Locate the control
as high as possible on the side of the duct or on
a nearby wall, panel, or structural support. The
optimum mounting position is with the element
bellows pointing down.
2. When you mount the control directly to a flat
vertical surface, insert two screws or bolts through
the two outer holes on the back of the control case.
3. When you mount the control to a flat horizontal
surface, use the two inner holes with the mounting
bracket and the supplied screws.
4. Build and install any field-fabricated supports that
are necessary to hold the sensing element in place.
5. Use the control’s mounting bracket as a template
to mark the location for the mounting screws.
6. Drill an 5/16 in. (8 mm) entry hole for the sensing
element.
7. Feed the entire length of the sensing element
through the entry hole.
A11 Series Low Temperature Cutout Control Installation Guide 3

Important: On A11 low temperature cutout
controls, the brass tubing just below the
bellows is not temperature sensitive and
can be mounted in the ambient space
temperature. The copper sensing element
begins below the solder bead. This part is
temperature-sensitive, and you must properly
position it to work correctly.
8. Use the mounting bracket and self-tapping screws,
to fasten the control to the side of the duct.
9. Start at the bottom of the coil and secure the far
end of the sensing element.
10. Secure the sensing element with 1/4 in. (6.4 mm)
poly sleeve and tie wraps.
11. Position and mount the sensing element within
6 in. (152 mm) of the bottom of the coil.
12. Work your way back up to the bellows, stringing
the sensing element in a serpentine fashion
horizontally across the face of the coil, as shown in
Figure 4.
13. Successive horizontal runs of the sensing element
should be inclined slightly upward.
14. Make sure that horizontal runs of the sensing
element are no more than 12 in. (305 mm) away
from each other.
Note: On a wide coil, you could be left with
a very small S to get back up to the control.
Locate this topmost bend in the correct
position to use up any remaining slack in
the length of the sensing element. You may
need to build a support for the bracket at that
turning point.
15. To prevent damage caused by vibration or
abrasion, place a short piece of 1/4 in. (6 mm) poly
sleeve around the capillary at the point where it
passes through the entry hole in the duct work. Slit
the tubing lengthwise to permit easy installation.
You do not normally need caulking or sealant when
you use the right size hole and tubing.
16. At the bends, use a TE-6001-8 Averaging Element
Mounting Bracket to obtain the correct radius and
protect the sensing element. The radius of each
bend of the sensing element must be at least 3 in.
(76 mm), but not exceed 14 in. (355 mm).
Mounting in small ducts with
inaccessible coils
Note:
• Begin mounting at the bottom and work up to the
thermostat.
• When the duct is covered with insulation, mount
stat to standard electrical box and cover.
Figure 5: Mounting Low Temperature Cutout Controls
in small ducts with inaccessible coils
Table 4: Mounting controls in small ducts with
inaccessible coils callouts
Callout Description
A A11
B Support the element at both ends and every
2 in. to 3 in. along the element. Consider using
a short piece of poly over the element or
capilliary at the supports.
C Use 3/8 in. copper or 1/2 in. EMT to support
the element.
D Must be within 6 in. of the bottom of the coil.
The bottom is the most important part of the
coil to protect.
E Minimum of 1 ft horizontal sensing. No coils
on the flat portion of the bracket.
F Mount the element at a slight downward
incline. Keep the loops horizontal or below
and make them the same size.
G Cut a hole of minimum 2 1/4 in. in size. Use
1/2 in. box connectors on each end of the EMT
to secure it to the box covers.
A11 Series Low Temperature Cutout Control Installation Guide4

Mounting in an inaccessible location
1. Determine the mounting location for the low limit
control.
- Avoid any moving parts within the duct, such
as dampers.
- When the duct is covered with insulation,
mount the control to a standard electrical
4- square box and cover.
2. Using Figure 5 as a guide, measure the duct and
calculate the required length and height of the
element support.
3. Use 1/2 in. (1.3 cm) of EMT to build the support
assembly outside of the duct.
Note: You can substitute 3/8 in. (1 cm) of
hard copper tubing for 1/2 in. (13 mm) of
EMT when you build the support. These
instructions assume the use of EMT.
4. Starting at the bottom of the coil, distribute the
sensing element around the support and use a tie-
wrap to secure it in place. Keep the loops horizontal
or inclined slightly downward at an angle not
greater than 5° and uniform in size (see Figure 5).
5. Consider the use of Minerallac conduit hangers
or equivalent to provide anchoring points on the
support where needed.
6. Place a 1/2 in. (1.3 cm) EMT connector on each end
of the support. These connectors protrude through
the knockout hole on the 4 in. (10.1 cm) box covers,
which are used as mounting plates at each end of
the support.
7. At the upper end of the duct, use a large hole saw
of minimum size 2-1/4 in. (57 mm) to drill the entry
hole for the sensing element or support assembly.
8. At the lower end of the duct, drill another hole. Use
the same hole saw that you used to cut the entry
hole.
9. A larger hole provides easier access for mounting.
Position this hole so that the lower portion of the
sensing element is within 6 in. (152 mm) of the
bottom of the coil.
10. Cut a notch in another 4 in. (10.1 cm) box cover.
Use the notch to secure the upper end of the
support assembly. Locate the notch so that you can
position the capillary (whip) close to the support.
See Figure 6.
11. Place a 4 in. (10.1 cm) box cover, with the center
knockout removed, over the upper end of the
support assembly, and use a lock nut to fasten the
support to the box cover.
12. Feed the sensing element or support assembly
through the entry hole at the upper end, and
position the lower end of the support to protrude
through the exit hole at the bottom on the far side.
13. Place a 4 in. (10.1 cm) box cover with the center
knockout removed over the end of the support and,
using a lock nut, fasten the support in place at the
lower end.
Figure 6: 4-square cover upper mount with center 1/2
in. knockout.
Table 5: 4-square cover upper mount callouts
Callout Description
A Use a hacksaw to cut a slot for the
sensor to pass through.
B Use a drill to cut a 1/4 in. hole. Cover the
element with poly for protection.
C To secure 1/2 in. EMT to the box cover.
14. Carefully place the capillary tube in the slot and
apply a short piece of 1/4 in. (6.4 mm) poly tubing,
slit lengthwise, around the capillary where it passes
through the notch.
15. Screw down the corners of the box cover to hold
the upper end of the support assembly in place.
16. Use the mounting bracket and self-tapping screws
to fasten the control to the side of the duct,
ensuring a downhill element all the way to the
bottom of the control.
Wiring
For most AHU installations, it is more cost-effective to wire
the low limit and other safeties with low voltage Class 2
wiring and add a shutdown relay at the motor starter.
This practice provides the control to share raceways with
other low voltage cables for the system.
CAUTION
Risk of Electric Shock
Disconnect power supply before making electrical
connections to avoid electric shock.
Important: Make all wiring connections in
accordance with local, national, and regional
regulations. Do not exceed the electrical ratings.
A11 Series Low Temperature Cutout Control Installation Guide 5

Setup and adjustments
Important:
• Do not adjust the pointer beyond the highest
or lowest indicator marks on the control’s
temperature scale. Adjusting the pointer beyond
the indicator marks may damage screw threads,
may cause inaccurate control operation, and
voids the warranty. Also, most controls with
spot sensitive sensing elements used for coil
protection are set and sealed at 35°F (1.6°C).
Attempting to set them lower can damage the
control.
• After adjusting the control settings and before
leaving installation, verify equipment and control
operation, and verify control setpoint with a
reliable thermometer.
Adjust the setpoint by turning the adjustment screw until
the pointer is opposite the cutout point that you want.
Access the adjustment screw at the bottom of the control
or at the top when you remove the cover.
Checkout procedure
Before you leave the installation, observe at least
three complete operating cycles to make sure that all
components function correctly. When used as a low
temperature cutout control, simulate operation by
actuating contacts to confirm that electrical connections
are correct.
Operation
The A11D and A11E models have SPDT contact action;
models A11A and A11B have SPST contacts. When 16 in.
(406 mm) or more of an A11 control’s sensing bulb senses
a temperature equal to or lower than the setpoint, the
contacts open on SPST controls, or the circuit between the
Red and Yellow terminals open on SPDT controls.
The A11A and A11D models lock out when the
temperature decreases below the control’s temperature
setpoint. Manual reset is a requirement of these models.
Press and release the reset lever after the temperature
increases 12F° (6.7C°) or more above the setpoint in order
to reset. The A11B and A11E automatically reset on an
increase in temperature.
Note: A11 Series low temperature cutout controls
have 6.1 m of 3.2 mm O.D. tubing and 1.2 m capillary
(20 ft of 1/8 in. O.D. tubing and 4 ft capillary.)
Table 6: A11 Series Low Temperature Cutout Controls
Code
number
Switch
action
Range Differential Maximum
bulb
temperature
Range
adjuster
A11A-1C Manual reset
A11B-1C
SPST
open low 6.7°F (12°C) fixed
A11D-5C Manual reset
A11E-5C
SPDT
35°F to 45°F
(2°C to 7°C)
6.7°F (12°C) fixed
250°F (121°C) Screwdriver
slot
Repair Information
If the A11 Series Low Temperature Cutout Control fails
to operate within its specifications, replace the unit. For
a replacement A11 Series Control, contact the nearest
Johnson Controls® representative.
A11 electrical rating
Table 7: A11 Series electrical rating
Description cULus
Volts AC 50/60 Hz 120 208 240
Full load amperes 16 9.2 8
Lock rotor amperes 96 55.2 48
Resistive amperes 16 9.2 8
Pilot duty 125 VA, 24 VAC to 277 VAC
A11 Series Low Temperature Cutout Control Installation Guide6

A11 conformity declaration
Table 8: Conformity declaration
Information Description
Purpose of the
control
Low temperature cutout control
Construction of
the control
Electromechanical independently
mounted control
Number of cycles 30K cycles auto reset, 6K cycles
manual reset
Method of
mounting the
control
Permanently attached through hole
in mounting bracket
Method of
earthing the
control
Wiring binding screw terminal
Type 1 or Type 2
action
Type 1.B; micro-disconnection
External pollution
situation
Pollution degree 3
Internal pollution
situation
Pollution degree 2
Rated impulse
voltage
4,000 VAC
Ball pressure
temperature
Switch component 302°F (150°C)
Field wiring
rating
Use copper conductors only, rated at
least 194°F (90°C)
Switch SPST (A11A, A11B), SPDT (A11D,
A11E)
Enclosure UL: Type 1 (NEMA)
Wiring
connection
Three color-coded screw terminals,
SPDT only, and one ground terminal
Conduit
connection
One 7/8 in. (22 mm) hole for 1/2
in. (12.7 mm) trade size (or PG16)
conduit
Ambient
conditions
0°F (-18°C) to 140°F (60°C)
Compliance North
America
cULus listed; UL60730,
CSA E60730 File SA516
Product warranty
This product is covered by a limited warranty, details
of which can be found at www.johnsoncontrols.com/
buildingswarranty.
Software terms
Use of the software that is in (or constitutes)
this product, or access to the cloud, or hosted
services applicable to this product, if any, is
subject to applicable end-user license, open-source
software information, and other terms set forth at
www.johnsoncontrols.com/techterms. Your use of this
product constitutes an agreement to such terms.
Single point of contact
APAC Europe NA/SA
JOHNSON CONTROLS
C/O CONTROLS PRODUCT
MANAGEMENT
NO. 32 CHANGJIJANG RD NEW
DISTRICT
WUXI JIANGSU PROVINCE 214028
CHINA
JOHNSON CONTROLS
WESTENDHOF 3
45143 ESSEN
GERMANY
JOHNSON CONTROLS
507 E MICHIGAN ST
MILWAUKEE WI 53202
USA
Contact information
Contact your local branch office:
www.johnsoncontrols.com/locations
Contact Johnson Controls: www.johnsoncontrols.com/
contact-us
A11 Series Low Temperature Cutout Control Installation Guide 7

© 2021 Johnson Controls. All rights reserved. All specifications and other information shown were current as of document revision and
are subject to change without notice.
www.penncontrols.com
This manual suits for next models
4
Table of contents
Other Penn Controllers manuals
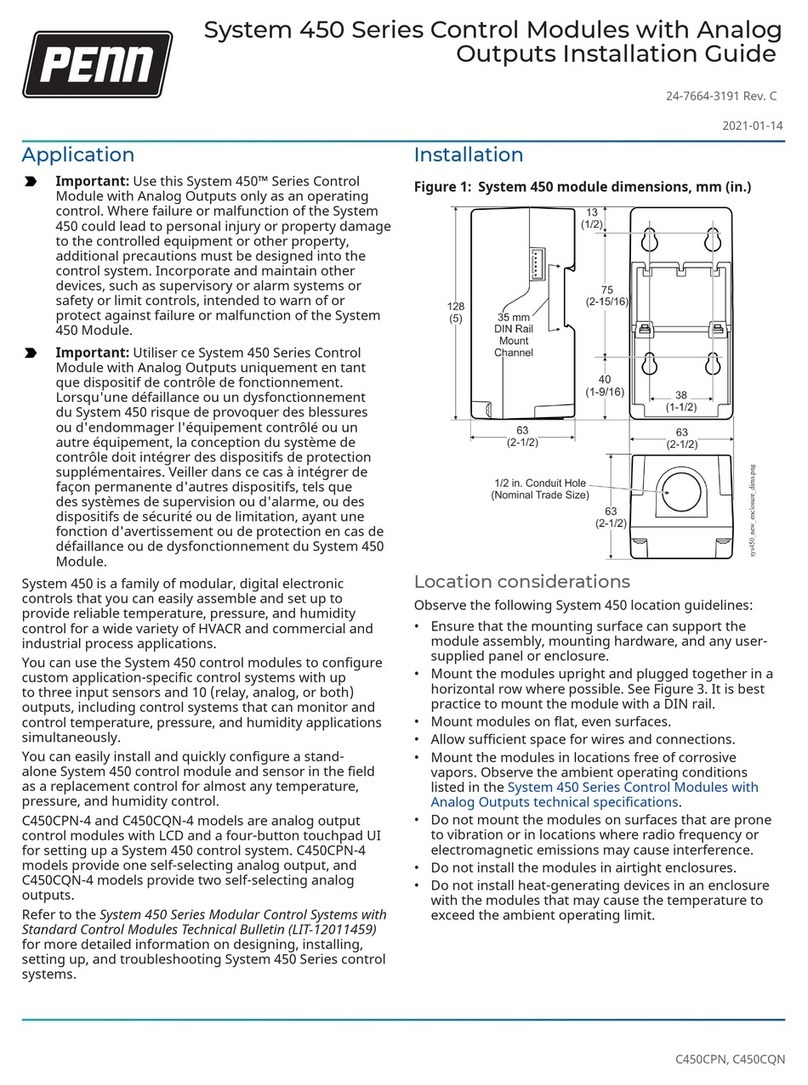
Penn
Penn System 450 Series User manual
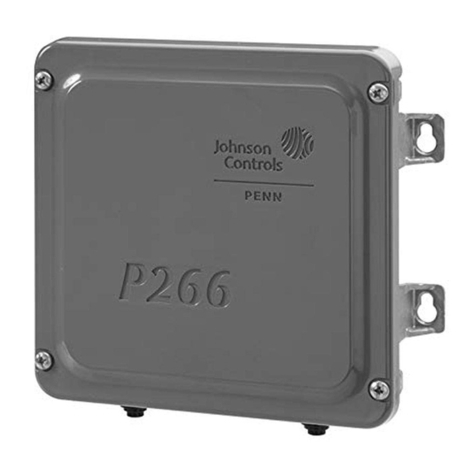
Penn
Penn P266 Series User manual
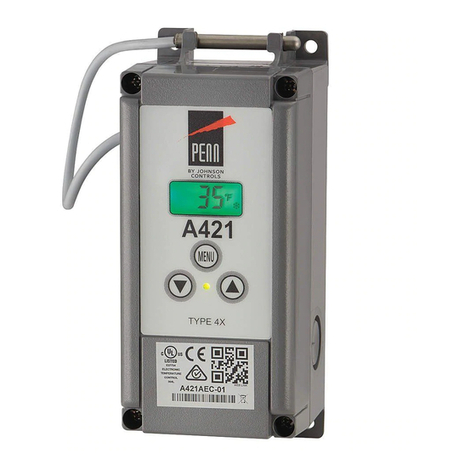
Penn
Penn A421ABC-03C User manual
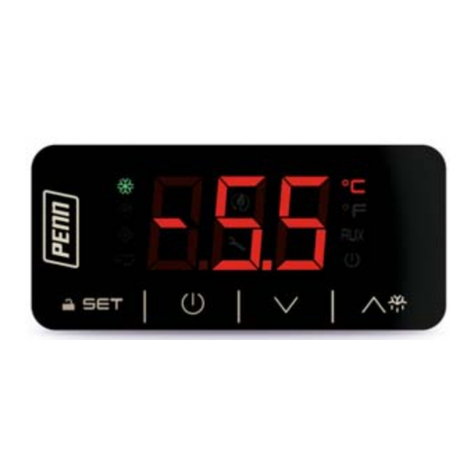
Penn
Penn TC3B23 User manual
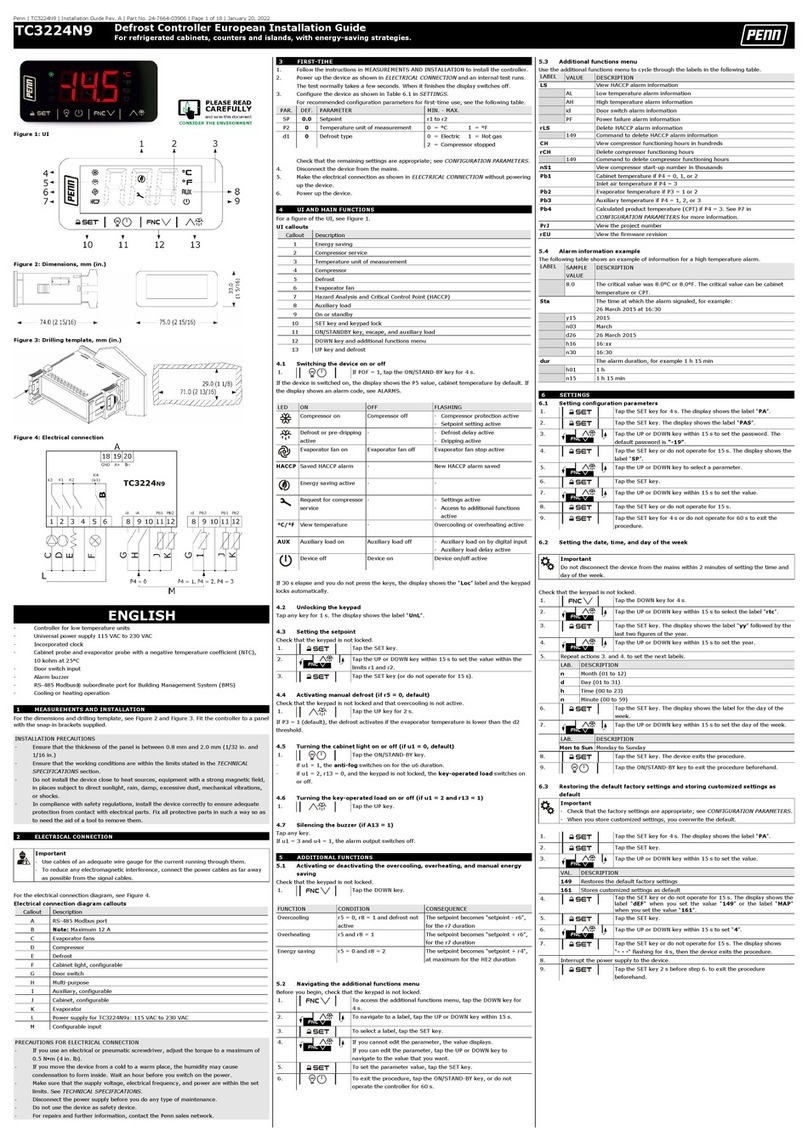
Penn
Penn TC3224N9 User manual
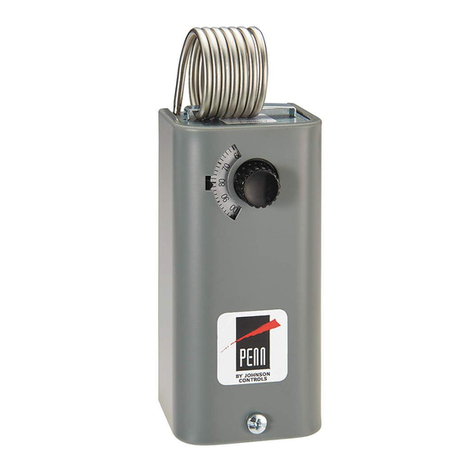
Penn
Penn A19 Series Guide
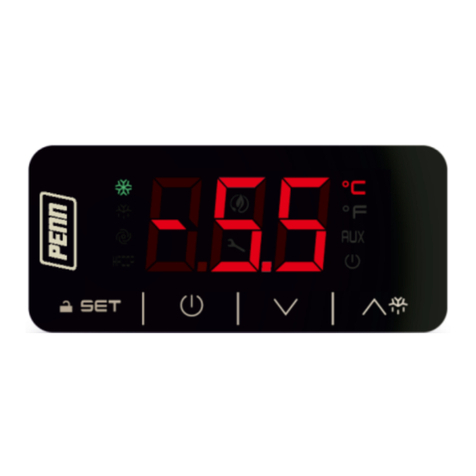
Penn
Penn TC3X21 User manual
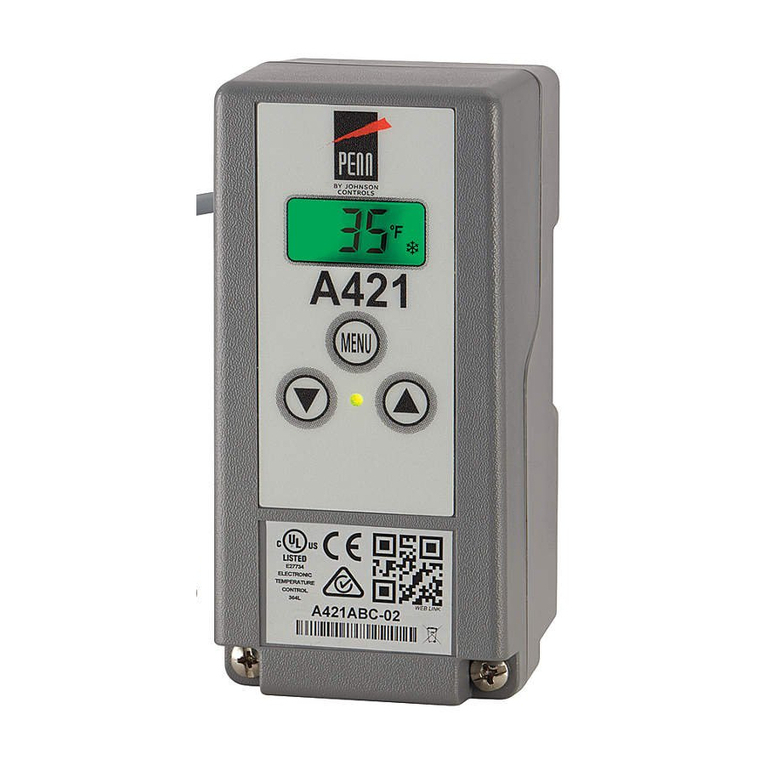
Penn
Penn A421 Series User manual
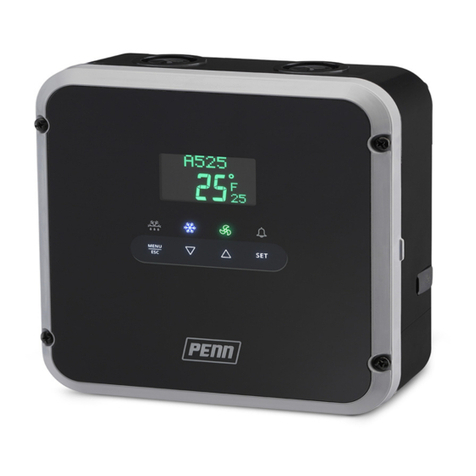
Penn
Penn A52 Series Service manual
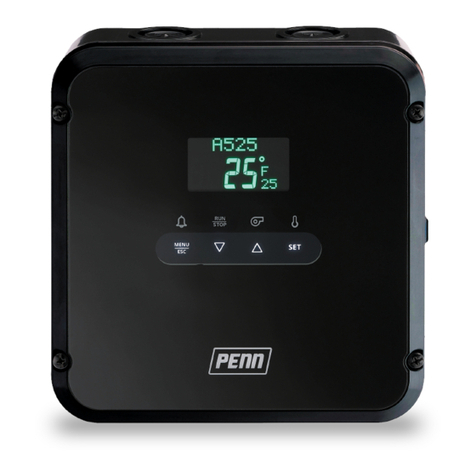
Penn
Penn A525 User manual