Stratus SAE-C12XE Guide

1
Model No. SAE-C12XE
Direct drive 2 post Lift
Single point electric release
Lifting Capacity 12,000 lbs
Installation & Operation &
Maintenance Instructions
I
mportant
Note
1. This equipment can not be installed, operated or repaired without reading instructions.
2. Electricity must be hooked up by certified electrician.
3. Do not use this equipment beyond its rated capacity.

2
TABLE OF CONTENTS
1. Packing, transport and storage......................................................................................................................................3
1.1 Packing .................................................................................................................................................................3
1.2 Transport .............................................................................................................................................................3
1.3 Storage..................................................................................................................................................................4
2. Technical specifications................................................................................................................................................5
2.1 Equipment plan .....................................................................................................................................................6
3. Safety............................................................................................................................................................................7
3.1 Important notices ................................................................................................................................................7
3.2 Qualified personnel .............................................................................................................................................7
3.3 Danger notices .....................................................................................................................................................7
3.4 Training................................................................................................................................................................8
3.5 Warning signs ......................................................................................................................................................8
4. Installation.....................................................................................................................................................................9
4.1 Tool required .......................................................................................................................................................9
4.2 Checking for room suitability ...........................................................................................................................10
4.3 Lighting...............................................................................................................................................................10
4.4 Floor requirement .............................................................................................................................................10
4.5 Site layout...........................................................................................................................................................10
4.6 Assembly diagram .............................................................................................................................................11
4.7 Assemble columns.............................................................................................................................................11
4.8 Installation overhead top beam .......................................................................................................................11
4.9 Position columns ...............................................................................................................................................13
4.10 Adjust carriage...............................................................................................................................................13
4.11 Install cables (2 Cables in total )...................................................................................................................14
4.12 Routing the safety release cable ...................................................................................................................14
4.13 Installation of power unit.........................................................................................................................................15
4.14 Connection of hydraulic hoses .................................................................................................................................15
4.15 Make the electrical connection ................................................................................................................................15
4.16 Oil filling and bleeding..............................................................................................................................................16
4.17 Installation of lifting arms and adjustment of arm locks............................................................................16
5. Check before start-up..................................................................................................................................................17
5.1 General checks ...................................................................................................................................................17
5.2 Mechanical safeties for proper installation.....................................................................................................17
5.3 Equalizer cable for proper installation............................................................................................................17
5.4 Hydraulic system for proper operation...........................................................................................................17
5.5 Check with load..................................................................................................................................................17

3
6. Operation and use...........................................................................................................................................................18
6.1 Controls ..............................................................................................................................................................18
6.2 Vehicle positioning ............................................................................................................................................18
6.3 Lifting..................................................................................................................................................................18
6.4 Standing..............................................................................................................................................................19
6.5 Lowering ............................................................................................................................................................19
6.6 Install limit switch.............................................................................................................................................19
6.7 Install the limiter switch inside of the main column ......................................................................................19
6.8 Connect the limiter switch connector to the motor........................................................................................19
7. Maintenance................................................................................................................................................................20
7.1 Ordinary maintenance ......................................................................................................................................20
7.2 Periodic maintenance........................................................................................................................................20
8. Troubleshooting..........................................................................................................................................................21
9. Parts list.......................................................................................................................................................................22
9.1 Main column and parts list ...............................................................................................................................22
9.2 Packing list .........................................................................................................................................................24
10. Special notes............................................................................................................................................................25
10.1 Environmental damage .................................................................................................................................25
10.2 Dismantling ....................................................................................................................................................25
10.3 Disposal ..........................................................................................................................................................25
10.4 Noise declaration...........................................................................................................................................25
1. Packing, transport and storage
All packing, lifting, handling, transport and unpacking operations are to be performed exclusively byexpert
personnel with knowledge of the lift and the contents of this manual.
1.1 Packing
The packing of the lift is delivered in following components:
a.1 base unit packed in a steel frame, wrapped up in non-scratch material, including all the accessories.
b.1 power unit packed in a carton box
1.2 Transport
➢See Fig 1, packing can be lifted or moved by lift trucks, cranes or bridge cranes. In case of slinging, a second person
must always take care of the load, in order to avoid dangerous oscillations. During loading and unloading operation,
goods must be handled by vehicles or ships.
➢At the arrival of the goods, verify that all items specified in the delivery notes are included. In case of missing parts,
possible defects or damage due to transport operations.
➢If finding missing parts, possible defects or damage due to transport, one should examine damaged cartons
according to <<Packing List.>> to verify the condition of damaged goods and missing parts, also the person in charge or

4
the carrier must be immediately informed.
➢The machine is heavy goods! Don’t take manpower load and unload and transporting way into consideration, the
safety of working is important.
➢Furthermore, during loading and unloading operation goods must be handled as shown in the picture.
1.3 Storage
➢The machine equipment should be stocked in the warehouse, if stocked outside should do the disposal well of
waterproof.
➢Use box truck in the process of transport, use container storage when shipping.
➢The control box should be placed perpendicularly during the transport; and prevent other goods from extrusion.
The temperature for machine storage: -10ºC-- 40ºC

5
2. Technical specifications
Machine model
SAE-C12XE
Lifting capacity
12,000lbs (5,500kg)
Lifting Height
83.07"(2110MM)
Minimum height
3.94"(100M)
Lifting time
About 50 sec
Voltage
220V
Frequency
60Hz
power
2.2KW/3HP
Hydraulic oil
46#/68#
Working temperature
41°F - 104°F
ambient humidity
30-95%
Machine noise
< 76dB(A)
Equipment weight
2350 bs (1066kg)

6
2.1 Equipment plan

7
3. Safety
3.1 Important notices
➢This ultra thin low lift is specially designed for lifting motor vehicles that weighs within its outmost lifting capacity.
Users are not allowed to use it for any other purposes. Otherwise, we, as well as our sales agency, will not bear any
responsibility for accidents or damages of the lift. Make sure to pay careful attention to the label of the lifting capacity
attached on the lift and never try to lift cars with its weight beyond.
➢Read this manual carefully before operating the machine so as to avoid economic loss or personnel casualty
incurred by wrong operation. Without professional advice, users are not permitted to make any modification to the
control unit or whatever mechanical unit.
3.2 Qualified personnel
➢Only these qualified staff, who have been properly trained, can operate the lift.
➢Electrical connection must be done by a competent electrician.
➢People who are not concerned are not allowed in the lifting area.
3.3 Danger notices
➢Do not install the lift on any asphalt surface.
➢Read and understand all safety warnings before operating the lift.
➢The lift, if is not specially designed upon customer’s request, is not fit for outdoor use.
➢Keep hands and feet away from any moving parts. Keep feet clear of the lift when lowering.
➢Only these qualified people, who have been properly trained, can operate the lift.
➢Do not wear unfit clothes such as large clothes with flounces, tires, etc, which could be caught by moving parts of
the lift.
➢To prevent evitable incidents, surrounding areas of the lift must be tidy and with nothing unconcerned.
➢The lift is simply designed to lift the entire body of vehicles, with its maximum weight within the lifting capacity.
➢Always ensure the safety latches are engaged before any attempt to work near or under the vehicle.
➢Make sure to place the lifting pads to the positions as suggested by vehicle makers and when gradually lift the
vehicle to the desired height, operators should be certain that the vehicle will not slant, roll-over or slide in lifting process.
➢Check at any time the parts the lift to ensure the agility of moving parts and the performance of synchronization.
Ensure regular maintenance and if anything abnormal occurs, stop using the lift immediately and contact our dealers for
help.
➢Lower the lift to its lowest position and do remember to cut off the power source when service finishes.
➢Do not modify any parts of the lift without manufacturer’s advice.
➢a. If the lift is going to left used for a long time, users are required to:
➢b. Empty the oil tank;
➢c. Lubricate the moving parts with hydraulic oil.

8
3.4 Training
➢Only these qualified people, who have been properly trained, can operate the lift. We are quite willing to provide
professional training for the users when necessary.
➢Attention: For environment protection, please dispose the disused oil in a proper way.
3.5 Warning signs
➢All safety warning signs attached on the machine are for the purpose of drawing the user’s attention to safety
operation. The labels must be kept clean and need to be replaced when they are worn-out or have dropped. Read the
explanations of the labels carefully and try to memorize them.

9
4. Installation
➢
Only skilled technicians, appointed by the manufacturer, or by authorized dealers, must be allowed to carry out
installation. Serious damage to people and to the lift can be caused if installations are made by unskilled personnel
➢
Always refer to the exploded views attached during installation.
4.1 Tool required
Rotary Hammer Drill D.20
Carpenter’s Chalk
Hammer
Screw Sets
Level Bar
Tape Measure (7.5m)
English Spanner (12")
Pliers
Ratchet Spanner With Socket (28#)
Socket Head Wrench (3#, 5#, 8#)
Wrench set
(10#, 13#, 14#, 15#, 17#, 19#, 24#, 27#, 30#)
Lock Wrench

10
4.2 Checking for room suitability
➢
The lift has been designed to be used in covered and sheltered places free of overhead obstructions.
➢
The place of installation must not be next to washing areas, painting workbenches, solvent or varnish deposits. The
installation near to rooms, where a dangerous situation of explosion can occur, is strictly forbidden. The relevant
standards of the local Health and Safety at Work regulations, for instance, with respect to minimum distance to wall
or other equipment, escapes and the like, must be observed.
4.3 Lighting
➢
Lighting must be carried out according to the effective regulations of the place of installation. All areas next to the lift
must be well and uniformly lit.
4.4 Floor requirement
➢
The lift should be fixed on a smooth and solid concrete ground with its strength more than 3000psi, tolerance of
flatness less than 5mm and minimum thickness of 200mm. New concrete must be adequately cured by at least 28
days minimum.
➢
Specifications of concrete must be adhered to. Failure to do so could cause lift failure resulting in personal injury or
death.
➢
A level floor is suggested for proper installation. Small differences in floor slope may be compensated for by proper
shimming. Any major slope change will affect the level lifting performance. If a floor is of questionable slope
considering to pour the new concrete slab.
4.5 Site layout
➢
Now locate the lift according to the floor plan the figure 3, use a carpenters chalk line to layout a grid for the column
locations.
➢
After the column locations are properly marked, use a chalk or crayon to make an outline of the columns on the floor
at each location using the column base plates as a template.
➢
Double check all dimensions and make sure that the bases of each column are square and aligned with the chalk line.

11
4.6 Assembly diagram
4.7 Assemble columns
➢
Assemble main column & extension column, and then stand up the 2 columns (the column with the power unit base
plate is the main column and the other one is the vice column)
➢
Note: Don't drill anchor bolts holes or install anchor bolts now.
4.8 Installation overhead top beam
1. Assemble overhead top beam.
NOTE: The bolts run from inside of the column and then fasten the nuts from outside of the column.

12
2. Install the overhead beam cable pulley
Warning: Symmetrical installation and asymmetrical installation of the cable pulley positions are not universal. In-correct
installation of the pulley positions may cause damage to the cable or the lift.
2.1.For symmetrical installation, use the long shaft and the long shaft sleeve to fix the cable pulley (pre-installed) .
Note: During the installation, the positions of the cable pulley at both ends of the overhead beam should be
installed correspondingly. There may be a gap between the cable pulley and the shaft sleeve, this is for the cable
can be automatically aligned, normal abrasion. Do not add shim to fix the position of pulley, it may cause
abnormal wear of the lift.
2.2.Mounting position of cable pulley
Note: During the installation, the positions of the cable pulley at both ends of the overhead beam should be
installed correspondingly. There may be a gap between the cable pulley and the shaft sleeve, this is for the cable
can be automatically aligned, normal abrasion. Do not add shim to fix the position of pulley, it may cause
abnormal wear of the lift.

13
4.9 Position columns
➢Check if the columns are vertical to the ground with level, insert thin shims (come with package) to adjust when
necessary
Symmetric installation
4.10 Adjust carriage
➢Raise the carriage to the 1st locking position located at the bottom of the column .
Note: You can hear “click” once locked.

14
4.11 Install cables (2 Cables in total )
Symmetric Installation Cable Routing Asymmetric Installation Cable Routing
4.12 Routing the safety release cable
1. The safety lock has been pre-installed.
2. Install safety lock release cable to connect the safety lock on the main column and vice column.
3. Install safety lock cover.
NOTE: Press the single point lock release lever on the main column to check if this lever can release the mechanisms in
both columns at the same time. Adjust the safety lock release cable adjustment screw if necessary, until the lever can
release the mechanisms in both columns at the same time.

15
4.13 Installation of power unit
1. Attach the power unit onto the bracket ;
2. Secure it using nuts M10X20, the locking washers D.10 and washers D.
3.
Mount the bracket with the power unit on the column with screw M8X16
4.14 Connection of hydraulic hoses
Connect the longer hose in between the 2 cylinders, connect the short hose in between the cylinder and the power
unit. Please hand tighten to avoid thread damage, then use hand wrench to fasten completely.
4.15 Make the electrical connection
Make sure all wiring are same as below circuit diagram.
Attention:electrical system connection must be done by licensed electrician.

16
4.16 Oil filling and bleeding
DO NOT run power unit without oil. Damage to pump can occur. If motor gets hot or sounds peculiar, stop immediately
and recheck the electric connection.
If the vented cap is lost or broken, order the replacement. The oil tank must be vented well.
Add about 2.5 gallons of hydraulic oil to the hydraulic fluid reservoir, AW32 during winter time (cold weather), and AW46
during summer time (hot weather).
Make sure there is no oil leak.
Repeatedly raise and lower the lift to bleed trapped air from the cylinders. Power unit testing
**Important Information**
➢Pressure Valve: Clockwise adjustment increases pressure to make the power unit to have more power,
counterclockwise adjustment decreases pressure to make the power unit to have less power.
➢Hydraulic oil Flow Valve: Clockwise adjustment to speed up, counterclockwise adjustment to slow down.
4.17 Installation of lifting arms and adjustment of arm locks
1. Install lifting arms .
2. Lower the carriages down to the lowest position, use the 8# socket head wrench to loose the socket bolt .
3. Adjust moon gear as direction of arrow .
4. Adjust the moon gear and arm lock to make it to be meshed, then tighten the socket bolts of arm lock.

17
5. Check before start-up
5.1 General checks
Make sure that the columns are plumb;
Make sure the lift anchored to the ground and all anchor boltstightened.
Make sure the electrical system feeding voltage is equal to that specified in the nameplate on themotor;
Make sure the electric system connection in conformity of the electric plan shown as the electric diagramand for proper
grounding.
5.2 Mechanical safeties for proper installation
Check to make sure that safety latches will properly engage and disengage by manual release;
If latches click out of synchronization, tighten the cable on the one that clicks later.
5.3 Equalizer cable for proper installation
The equalizer cables should be checked weekly for equal tension. Failure to do this will cause uneven lifting. The cables
should always be adjusted so that they are equal tension when resting on the safety locks.
Raise the carriages to check the equalizer cable tension by grasping the adjacent cables between the thumb and the forefinger so
that you can just pull the cables together;
Adjust the cable tensions if necessary;
5.4 Hydraulic system for proper operation
Make sure that the cylinder is located in the center hole in the base of column;
Proper oil level in the tank, refill if needed;
Raise the lift to the full height and keep the motor running for 5 seconds and check all hoses connections to make sure no
leakage. Tighten the connections or reseal if necessary;
Check the lift for reaching its maximum height;
Repeat the air bleeding of cylinders if necessary.
5.5 Check with load
WARNING: please follow carefully the instructions in the coming paragraph for avoiding damages on the lift. Carried
out two or three complete cycles of lowering with the vehicle loaded:
Repeat the checks provided for by 4.14.
Check no strange noise during lifting and lowering.

6. Operation and use
NEVER operate the lift with any person or equipment below. NEVER exceed the rate lifting capacity.
NEVER lift a vehicle in any manner with less than four arms.Always ensure that the mechanical locks are engaged
before any attempt is made to work on or near the vehicle.
Always lift a vehicle on the lifting pads.
NEVER leave the lift in an elevated position unless the safeties are engaged.
If an anchor bolt becomes loose or any component of the lift is found to be defective, DO NOT USE THE LIFT until
repairs are made.
6.1 Controls
Controls for operating the lift are:
Lifting button (Ascends):
When pressed, the power unit is running and the lift can be raised to a desired height until the button is released.
Lowering lever (Descend):
If the mechanical locks are not released, the lift will lower to the nearest lock position.
If both mechanical locks are released, press the lower lever, the lift will lower to the desired height under its weight
and the load lifted until the lever is released.
Locks will automatically reset once the lift ascends approximately 15” from base.
6.2 Vehicle positioning
Positioning the vehicle between columns;
Adjust lift arms so that the vehicle is positioned with the center gravity between the pads. Make sure the arm
safeties are engaged;
Raise the lift by pressing the lifting button until the lifting adaptors contact underside of the vehicle;
Make sure the vehicle is secured
6.3 Lifting
Raise the lift by pushing the lifting button until reaching the desire height.

6.4 Standing
Press the lowering lever to engage the nearest lock position;
Always ensure that the lock in each column is engaged before any attempt is made to work on or near the vehicle.
6.5 Lowering
Raise the lift a little bit by pushing the lifting button to clear off the mechanical locks;
Release the locks manually;
Lower the lift by pressing the lowering lever;
Before removing vehicle from the lift area, position the lift arms to and pads to provide an obstructed exit;
Never drive over the lift arms.
6.6 Install limit switch
6.7 Install the limiter switch inside of the main column
6.8 Connect the limiter switch connector to the motor

7. Maintenance
Only trained people who know how the lift works, can be allowed to service the lift.
To service properly the lift, the following has to be carried out:
use only genuine spare parts as well as equipment suitable for the work required;
follow the scheduled maintenance and check periods shown in the manual;
discover the reason for possible failures such as too much noise, overheating, oil blow-by, etc.
refer to documents supplied by the manufacture or dealer to carry out maintenance.
Before carrying out any maintenance or repair on the lift, disconnect the power supply.
7.1 Ordinary maintenance
The lift has to be properly cleaned at least once a month using self-cleaning clothes.
The use of water or inflammable liquid is strictly forbidden.
Be sure the rod of the hydraulic cylinders is always clean and not damaged since this may result in leakage from seals
and, as a consequence, in possible malfunctions.
7.2 Periodic maintenance
Dailypre-operation
•Checkhydraulicconnectionsandhosesforleaks
•Checkmechanicallocksaudiblyandvisuallywhileinoperation
•Checkarmlocks
•Checkbolts,nutsandscrewsaretight
Every1month
•Checkallcableconnections,pinsandboltstoinsurepropermounting
•Inspectallanchorboltsandretightenifnecessary
•Checkcolumnsforsquare-nessandplumb
•Checkequalizercabletension,adjustifnecessary
•Checksafetycable,adjustit ifnecessary
•Checkallarmpivotpins.Makesuretheyareproperlysecured
•Checkallliftingpads,replaceifnecessary
•Lubricantcolumnswithgrease
•Checkthehydraulicoil,fillorreplaceifnecessary
•Checkhydraulicsystemsforproperoperation
Every12months
•Verifythatallcomponentsandmechanismsarenotdamaged
•Verifytheequalizercablesarenotworn,changeifnecessary
•Checktheelectricalsystemtoverifythatthemotorsoperateproperly(thisworkmust
becarriedoutbyskilledelectricians)
•Emptytheoiltankandchangethehydraulicoil
Table of contents
Other Stratus Lifting System manuals

Stratus
Stratus SAE-P48 Guide

Stratus
Stratus SAE-UT8000 Guide

Stratus
Stratus SAE-C10P Guide
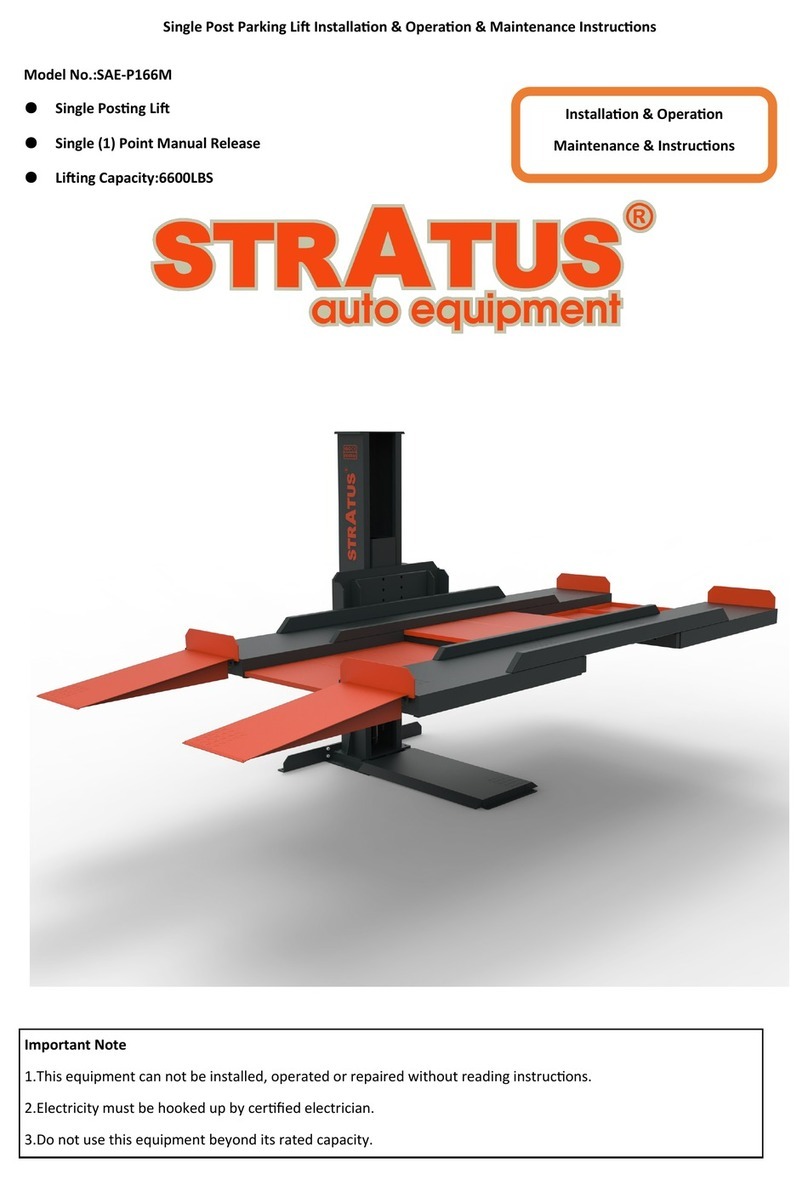
Stratus
Stratus SAE-P166M Guide
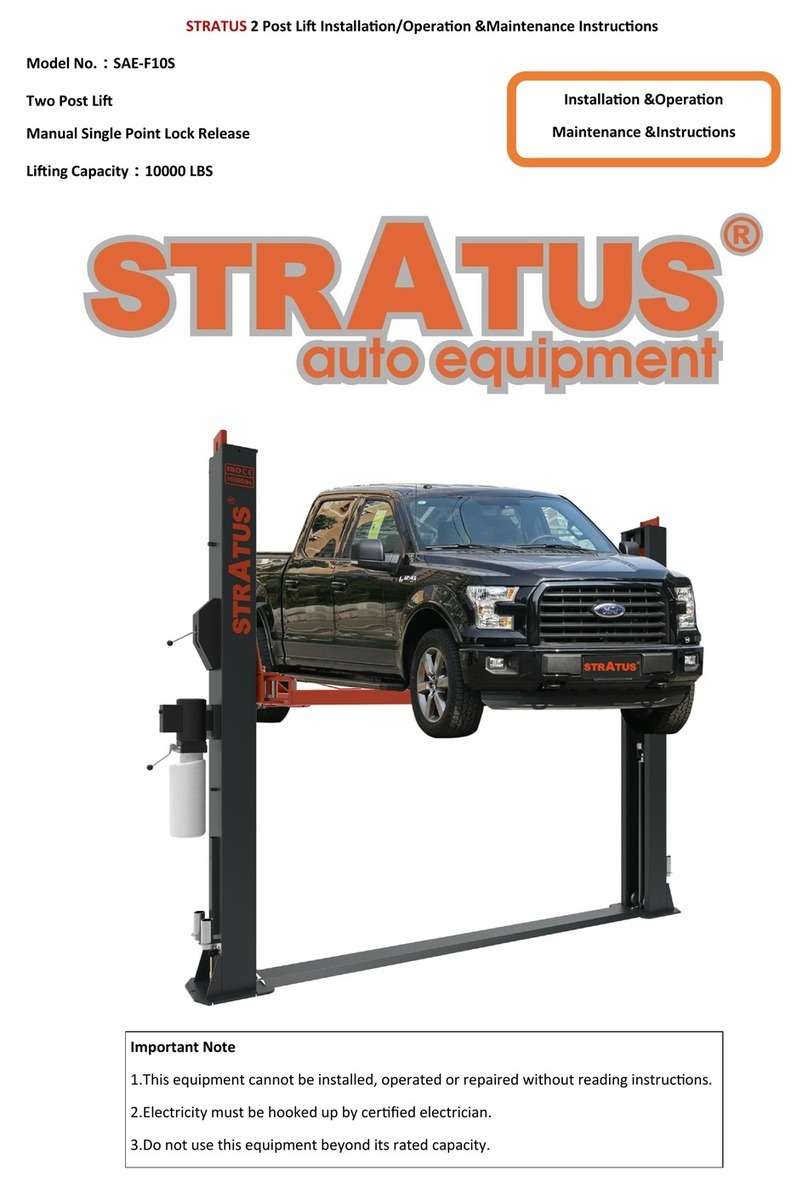
Stratus
Stratus SAE-F10S Installation instructions
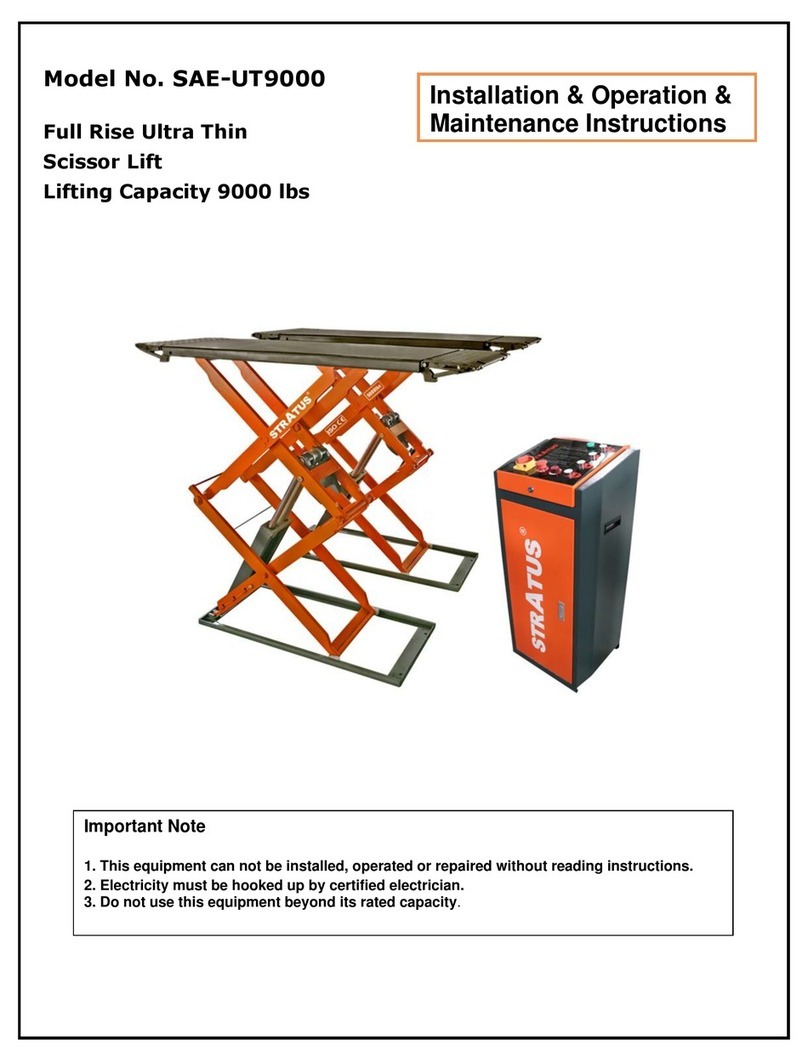
Stratus
Stratus SAE-UT9000 Guide
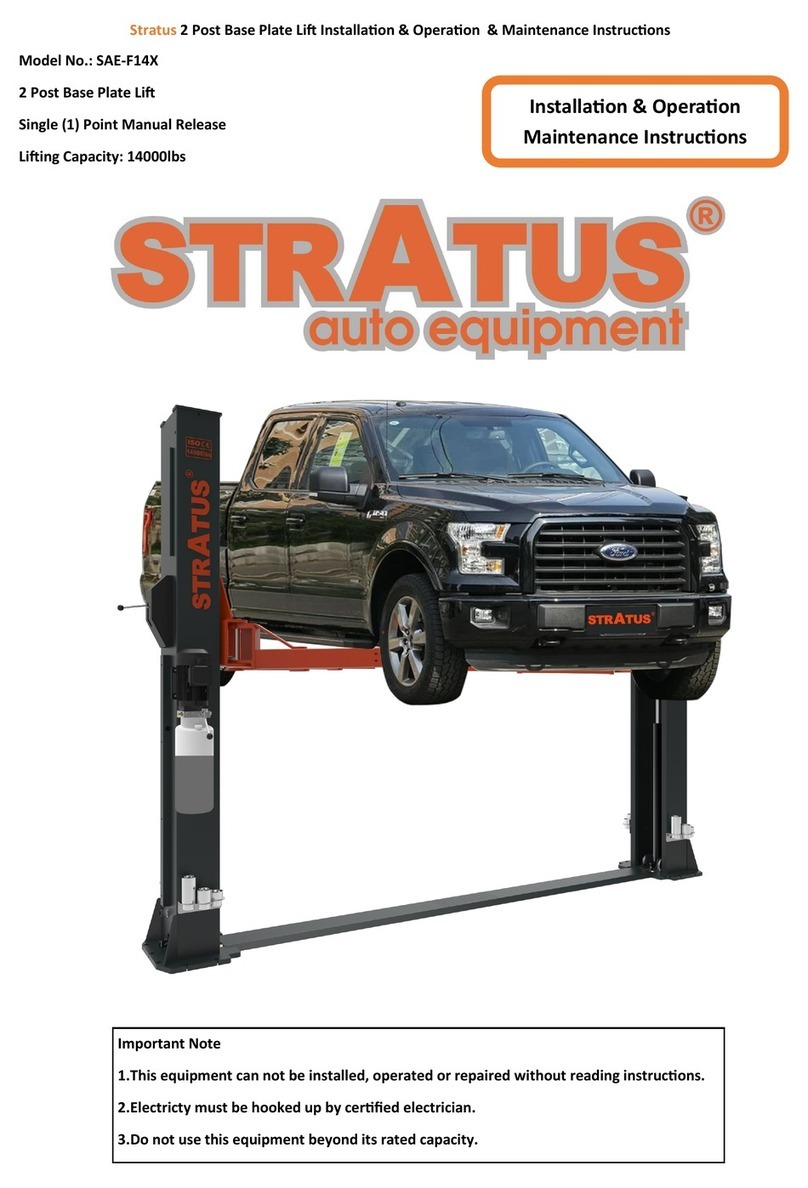
Stratus
Stratus SAE-F14X Guide
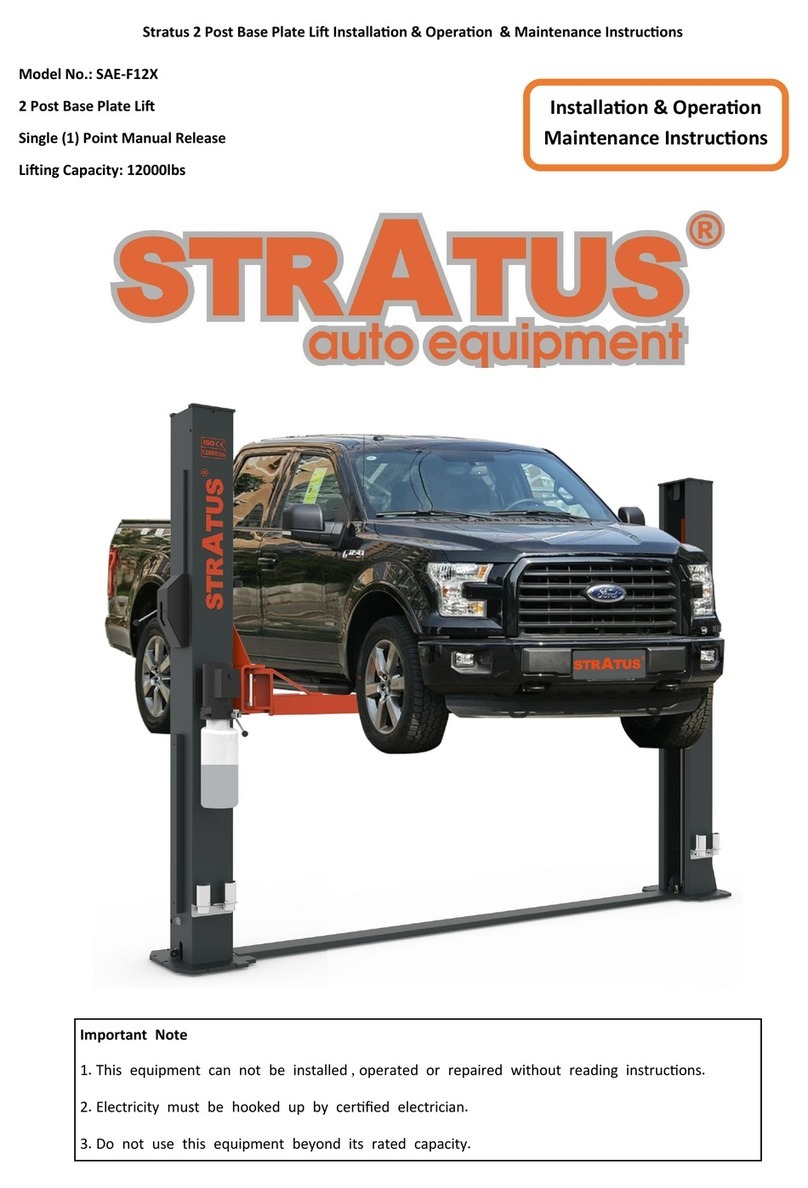
Stratus
Stratus SAE-F12X Guide

Stratus
Stratus SAE-P410 User manual
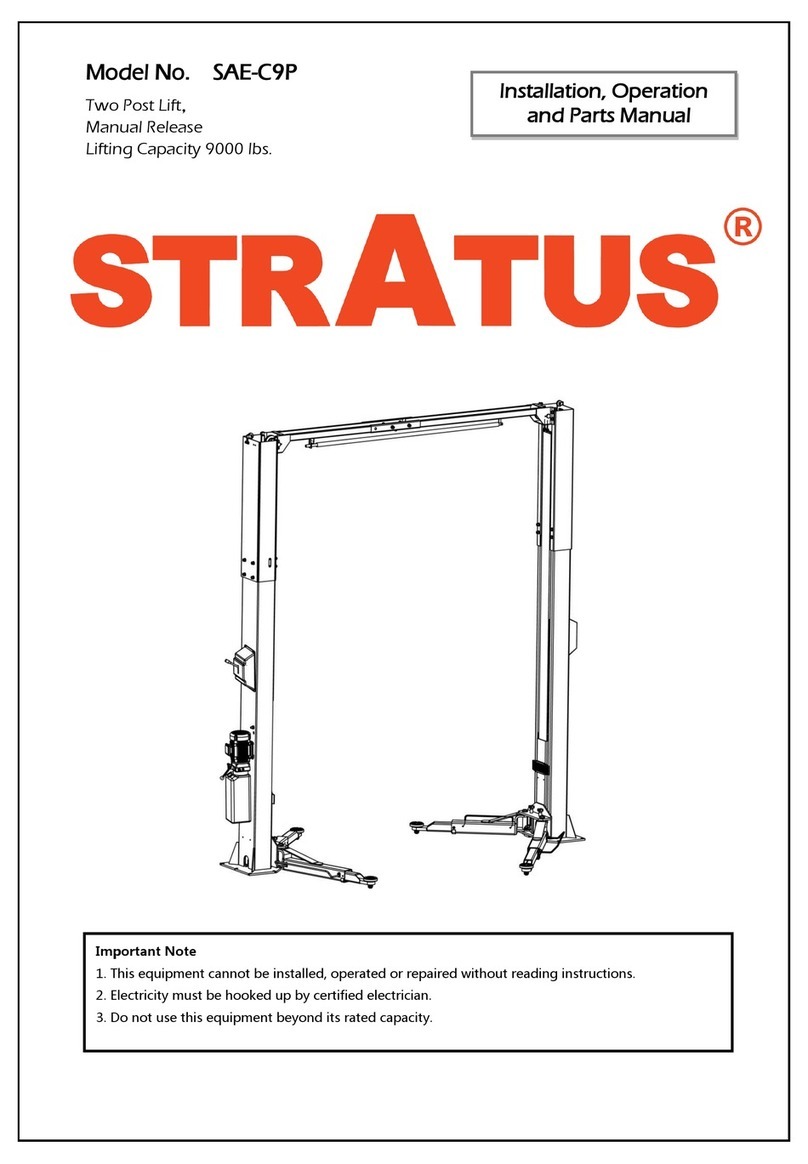
Stratus
Stratus SAE-C9P Guide