BERMAD C10 User manual

Installation, Operation and
Maintenance Manual (IOM)
Combination
Air Valve Model
Model C10 /C11


Table of Contents
General .....................................................................Page 2
Safety .......................................................................Page 2
Operational Data ......................................................Page 3
Materials and Connections .......................................Page 3
C10 Parts List (¾"-1" / DN20 - DN25) .........................Page 4
C10 Parts List (2" / DN50) ..........................................Page 5
C11 Parts List (¾"-1" / DN20 - DN25) .........................Page 6
C11 Parts List (2" / DN50) ..........................................Page 7
Surge Protection (SP) – Parts List ..............................Page 8
Inflow Prevention (IP) – Parts List ...............................Page 9
Unpacking and post shipment inspection ................Page 10
Site Preparation.......................................................Page 10
Installation ...............................................................Page 11
Operation ................................................................ Page 12
Principles of Operation ............................................ Page 13
Maintenance ........................................................... Page 14
Troubleshooting ...................................................... Page 15
Disassembling C10 / C11 (sizes ¾-1"/ DN25 DN50) ...Page 16
Reassembling C10 / C11 (sizes ¾-1"/ DN25 DN50)....Page 17
Disassembling C10 / C11 (size 2" / DN50)................ Page 20
Reassembling C10 / C11 (size 2" / DN50) ............... Page 21
1

General
The BERMAD C10 / C11 is a high quality combination
Air Valve for a variety of water networks and operating
conditions. It evacuates air during pipeline filling, allows
efficient release of air pockets from pressurized pipes,
and enables large volume air intake in the event of
network draining.
With its advanced aerodynamic design, this double
orifice valve provides excellent protection again air
accumulation and prevents vacuum formation with
improved sealing at low pressure.
This document serves as the Installation, Operation and
Maintenance Manual (IOM) of this valve; it describes the
procedures required for proper usage of the valve.
Safety
Since Air Valves operate in pressurized water systems
you are required to carefully read this manual before
using the valve. Handle the valve with care and make
sure to comply with all the relevant required safety
instructions and standards, general and local.
2

Operational Data
Pressure rating ISO PN10, ANSI / ASME 150
Operating pressure range 0.1-10 bar / 1.5-150 psi
Operating temperature Water up to 60° C / 140° F
Materials and Connections
Body material Glass-reinforced Nylon
Inlet diameter ¾", 1", 2" DN20, DN25, DN50
Connections Threaded Male BSPT / NPT
Outlet types
Sideways, Downwards (DN50/ 2" only)
Additional features (2" / DN50 only):
Surge Protection (C10-SP, C11-SP)
Inflow Prevention (C10-IP, C11-IP)
3

C10 Parts List
Body (#2)
Base (#1)
Float (#3)
O-Ring (#5011)
Kinetic Plug (#6)
Kinetic Plug Legs (#33)
Kinetic Seal (#4)
Peal Seal (#5)
C10 Parts List ¾"-1" / DN20 - DN25
Seals Kit (#60)
Kinetic Plug +
Legs Kit (#40)
4

Body (#2)
Drain Elbow (#8)
Base (#1)
Float (#3)
Peal Seal (#5)
Kinetic Plug (#6)
Kinetic Seal (#4)
C10 Parts List 2" / DN50
Seals Kit (#60)
O-Ring (#5012)
5

C11 Parts List ¾"-1" / DN20 - DN25
Body (#2)
Base (#1)
Float (#3)
Kinetic Seal (#4)
Auto Orifice Seal (#18)
Auto Orifice (#14)
Kinetic Plug (#6)
Kinetic Plug Leg (#33)
O-Ring (Base #5012)
O-Ring (Auto Orifice #5000)
Seals Kit (#60)
Kinetic Plug +
Auto Orifice +
Legs Kit (#40)
6

C11 Parts List 2" / DN50
Body (#2)
Base (#1)
Test Point (#7)
Float (#3)
Auto Orifice (#14)
O-Ring (Auto Orifice #5000)
Kinetic Seal (#4)
O-Ring (Base #5011)
Auto Orifice Seal (#18)
Kinetic Plug (#6)
Seals Kit (#60)
Kinetic Plug +
Auto Orifice +
Legs Kit (#40)
Drain Elbow (#8)
7

Surge Protection (SP) – Parts List
Surge Seal (#11)
Grid (#10)
Surge Extension (#9)
Drain Elbow (#8)
8

Inflow Prevention (IP) – Parts List
Inflow Seal (#11)
O-Ring (#5074)
Grid (#10)
Surge Extension (#9)
Drain Elbow (#8)
9

Unpacking and post shipment inspection
Make sure that till the actual installation the valve
remains dry and clean in its original package.
Unpack the valve and make sure that all the wrapping
materials are removed.
Before installation it is necessary to inspect that
no damage to the valve occurred during shipment;
do not install a damaged valve!
Verify that the valve to be installed meets the design
specifications of the specific installation site; take
extra care and make sure that the expected system
pressure complies with the pressure rating of the valve.
Site Preparation
Air Valves located above ground should be protected
from freezing, contamination and vandalism.
If the valve is to be installed in a pit, make sure that
the pit has proper drainage and sufficient dimensions
for servicing the valve.
Flush the pipeline prior to the Air Valve installation in
order to prevent damage to the valve internals due
to large debris carried by the water during startup.
The C10 / C11 Air Valves are not to be used
in systems containing high suspended solids;
consider selecting other BERMAD Air Valve models
for such water type.
10

Installation
Typical Applications
Main Irrigation Networks – Air relief, protection against
air accumulation and vacuum formation downstream
of pumps, along supply lines and at elevations in main
irrigation networks.
Irrigation Control Heads – Air relief, protection against
air accumulation and vacuum formation in filtration
and fertilization stations and downstream of main
control valves.
Infield Systems – Protection against air accumulation
and vacuum formation in proximity to water meters
and automatic regulators.
Landscape Irrigation – Protection against air
accumulation and vacuum formation.
Please note:
1. If required a Down Outlet and a Connection to a
Drainage Pipe can be fitted to the 2" / DN50 valve’s
outlet.
2. Depending on the specific installation requirements
a Surge Protection (SP) or an Inflow Prevention (IP)
device may be added to the Air Valve.
11

Installation instructions
Install the Air Valve as close as possible to the pipe,
at a high point of its circumference, in vertical position
(within 5 degrees of vertical alignment)
and with its inlet facing down.
The diameter of the pipe connecting
the Air Valve with the pipeline should
be at least equal to the Air Valve inlet
diameter.
Install a shutoff valve between
the Air Valve and the pipeline
for allowing easy inspection
and maintenance.
Operation
Start-up and first operation
Open the shutoff valve and verify that the Air Valve
connections are not leaking; if needed follow the
troubleshooting instruction section of this document.
Please note that at the first time the valve is filled up
some water may exit through its outlet port.
Prevent water hammer during startup and pipeline
filling by maintaining the velocity lower than 0.5m / sec
(1.6 feet / sec). Consider adding the Surge Protection
feature in systems where higher velocity is expected.
12

Principles of Operation
Pipeline Filling
During the filling process of a pipeline, high air flow
is forced out through the kinetic orifice of the Air Valve.
Once water enters the valve’s chamber, the float buoyed
upward causes the kinetic orifice to close.
The unique aerodynamic structure of the valve body
and float ensures that the float cannot be closed before
water reaches the valve.
Pressurized Operation
During pressurized operation of the pipeline, air
accumulates in the upper part of the Air Valve chamber,
causing the float to gravitate downwards. This in turn
causes the automatic orifice to open, releasing the
accumulated air. Once the air is discharged, the water
level and float rise, causing the automatic orifice to close.
Pipeline Draining
When a pipeline is drained, a negative differential
pressure is created causing atmospheric air to push
the float down. The kinetic orifice stays open and air
enters the valve chamber, preventing vacuum formation
in the pipeline.
13

Surge Protection (Anti-slam)
The anti-slam device (SP) is fitted to the Air Valve
outlet. In the event of pressure surge, it partially closes
the valve's outlet. The approaching water column
decelerates due to the resistance of the rising air
pressure in the valve.
Inflow Prevention
The inflow prevention (IP) is a Normally Closed check
device fitted on the valve's outlet and preventing flow
of atmospheric air into the valve.
Please note
During initial pipeline filling as well as during the
automatic air release some water may exit through
the valve outlet.
To ensure a completely dry environment near
the Air Valve, a drainage pipe can be connected
to the valve outlet
Maintenance
Inspection
The valve does not require any specific maintenance,
however a periodical inspection of the seals is
recommended for removing debris and foreign objects.
14

Troubleshooting
Symptom Action
Leakage at the
inlet connection
Tighten the valve connection, use
thread sealant. Check whether any part
is damaged.
Leakage at
the valve body
Tighten the valve's body,
check the O-Ring.
Leakage at
the valve's outlet
Dissemble and inspect the valve's
orifices, float and seals.
Flush the valve to remove debris,
Remove any foreign objects, check
and replace any damaged part.
Valve does
not release air
or allow air intake
Verify that the operation pressure does
not exceed the valve's rated working
pressure.
Check and removed foreign objects,
Clean the valve's internal parts, replace
if necessary.
Consult BERMAD if the symptom
continues.
15

Disassembling C10 / C11
(sizes ¾ - 1" / DN25 DN50)
1. Release the valve’s cover (Part #2) by turning it
counterclockwise, un-screw and remove it from the
valve’s base (Part #1). Make sure that the valve parts,
seated within the cover do not fall out of the cover.
2. Inspect the valve basis O-Ring (Part #5011) and if
necessary replace it with a new one. Make sure that
the new O-Ring is seated correctly in its designated
groove in the valve’s basis.
3. Pull the float assembly (Part #3) out of the valve’s cover.
4. Disconnect the Kinetic Plug (Part #4 from the float
(Part #3) using its Snap Legs.
5. Inspect the float’s peal seal (Part #5 or #18)
and the float (Part #3) for wear and tear.
6. If necessary replace the old parts.
16

Fig. A (C11)Fig. A (C10)
Fig. C
Fig. B
Fig. D
Reassembling C10 / C11
(sizes ¾ - 1" / DN25 DN50)
1. Wet the Kinetic Seal
(Part #4) with water and
install it on the Kinetic
Plug (Part #6) with its
raised edges side facing
upward. See figure A.
2. For C10 (sizes ¾ - 1" / DN20 DN25).
a. Wet the new peal seal (Part #5)
with clean water. Use the Insertion
Assistance Handle and insert the
peal seal (Part #5) to its designated
groove in the kinetic plug (Part #6)
as shown in Figure B.
b. Use the Insertion
Assistance Handle
and insert the of the
peal seal (Part #5) to
its designated groove
in
the automatic float
(Part #3), insert the "legs" (Part #33)
to the kinetic plug (Part #4) and
then to the 2 holes in the automatic
float (Part #3). See Figure C.
c. Once the Peal Seal is correctly
seated in place, cut the insertion
assistance handles and discard them.
See Figure D.
17

3. For C11 (sizes ¾- 1" /DN20 DN25)
a. Insert the Orifice seal
(Part #18) to its groove
on the float (Part #3),
See Figure E.
b. Take the kinetic plug (part
#4), which includes the
automatic orifice (Part #14)
and O-Ring (part #5000).
Connect the 2 "legs"
(Part #33) to the
kinetic plug (part #6),
See Figure G.
c. Insert the "legs" (Part #33)
to the 2 holes in the
automatic float (Part #3),
See Figure H.
4. Make sure that the valve’s
basis O-Ring (Part #5011)
is fully inserted to its
groove within the basis.
See Figure I.
5. Insert the complete float
assembly to its place
in the Valve Cover (Part #2),
See Figure J.
Fig. E
Fig. H
Fig. G
Fig. I Fig. J
18
This manual suits for next models
1
Table of contents
Other BERMAD Control Unit manuals
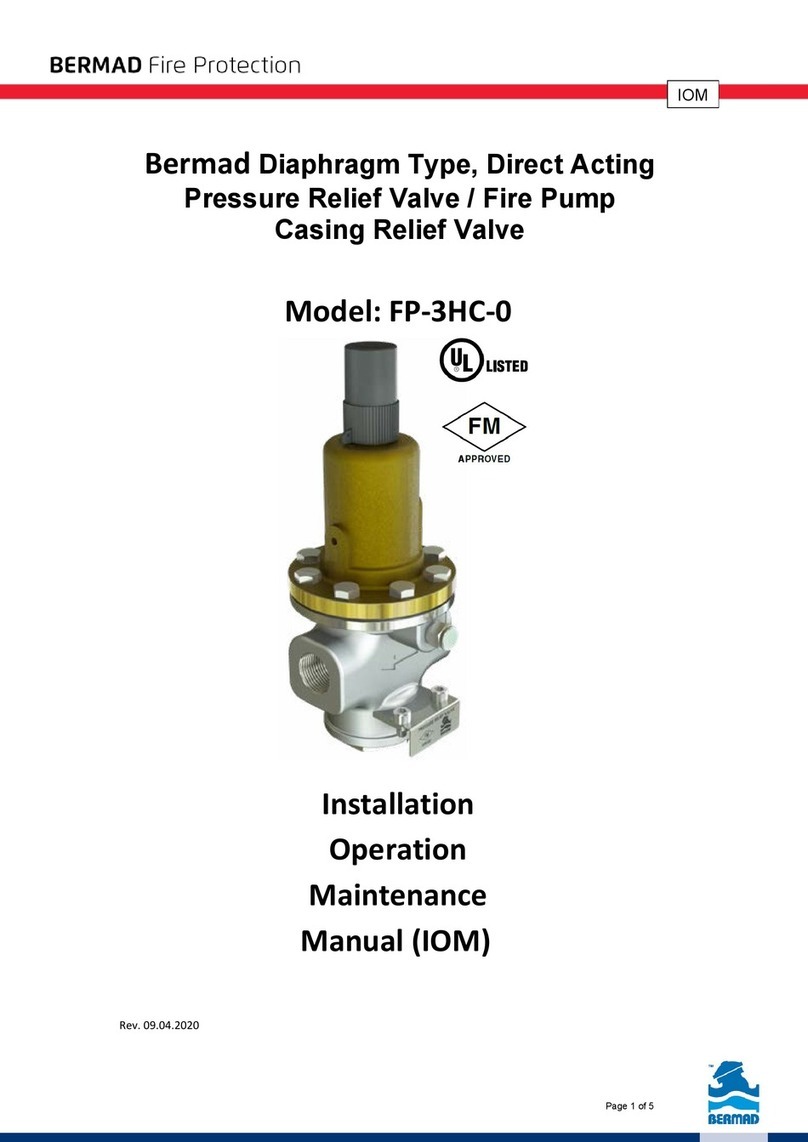
BERMAD
BERMAD FP-3HC-0 Instruction manual
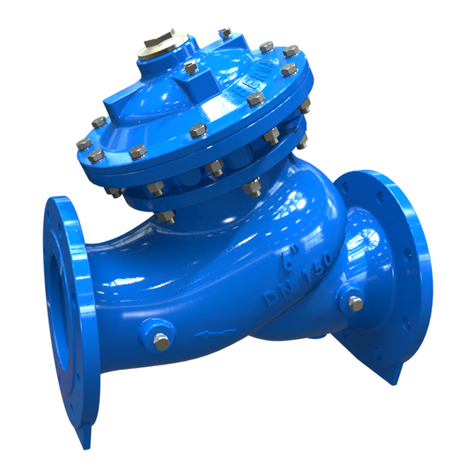
BERMAD
BERMAD 700 Series User manual

BERMAD
BERMAD 400E-5D Owner's manual
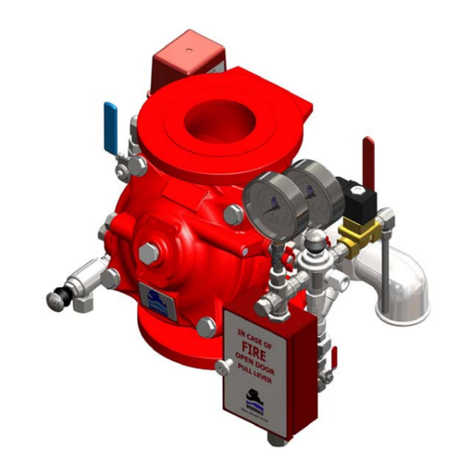
BERMAD
BERMAD 400E-Y General instructions

BERMAD
BERMAD 420 Guide

BERMAD
BERMAD 720 User manual

BERMAD
BERMAD C80 Instruction manual
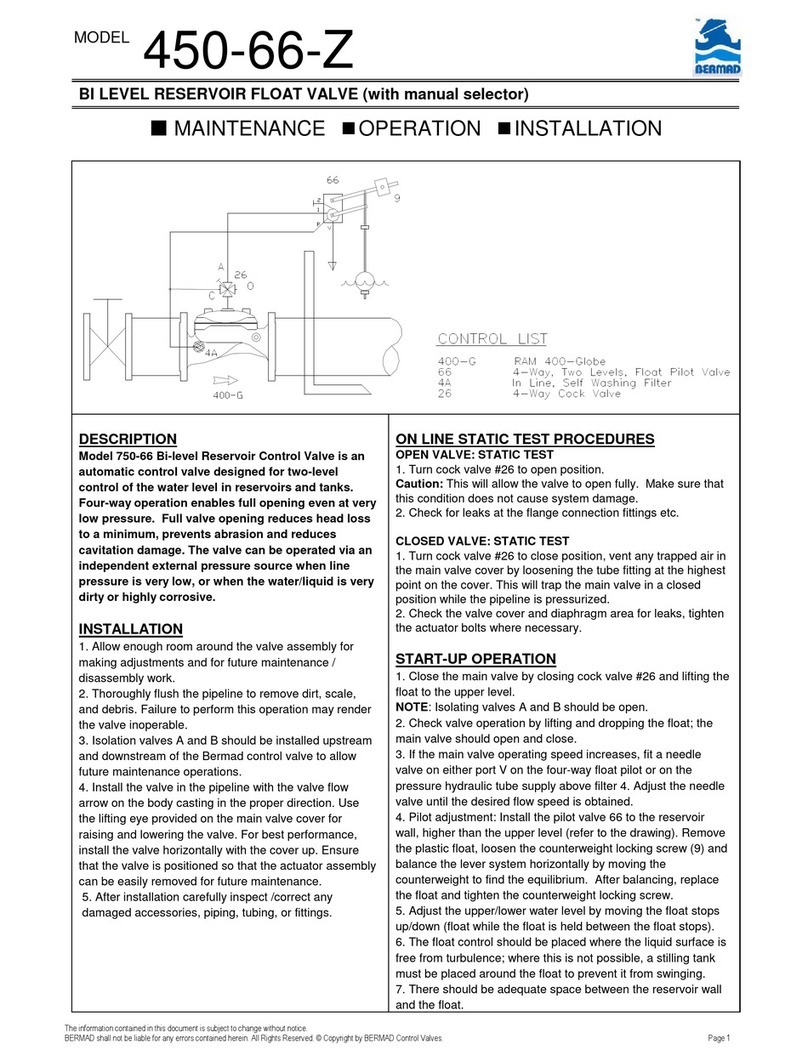
BERMAD
BERMAD 450-66-Z User manual

BERMAD
BERMAD C15 User manual

BERMAD
BERMAD 430-Z-3W Owner's manual
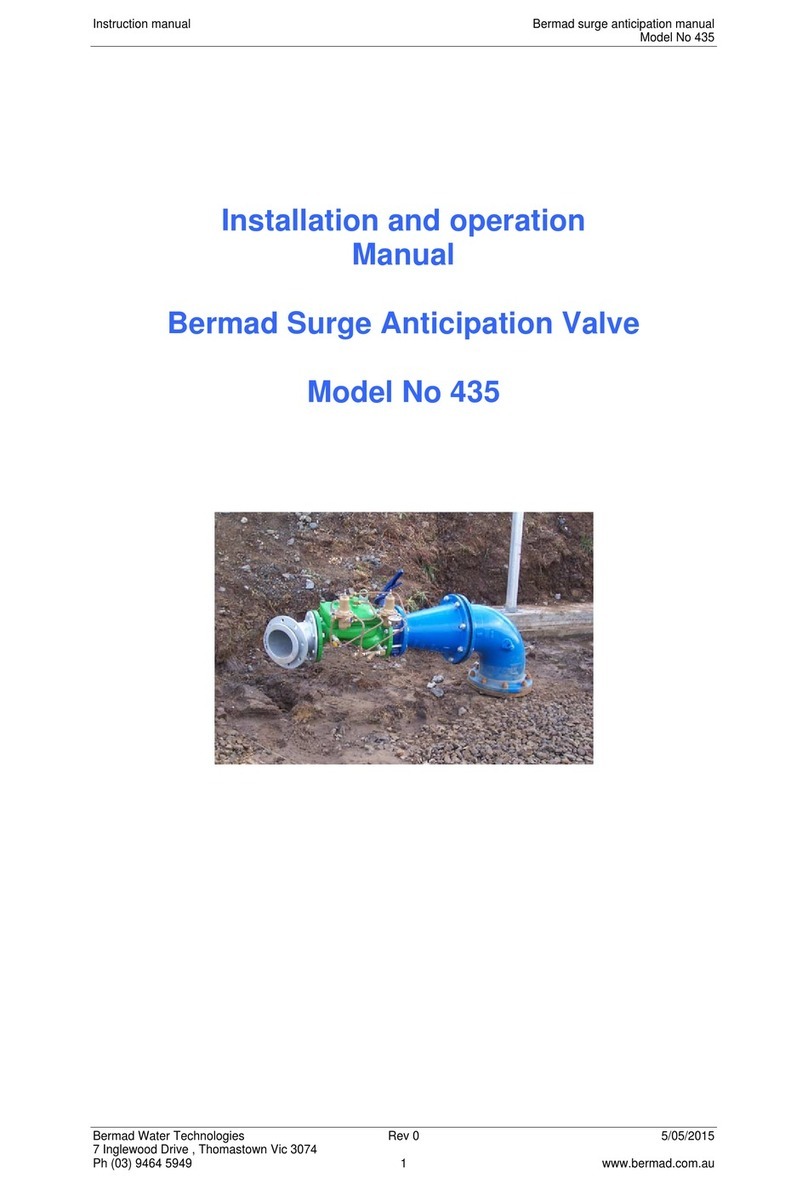
BERMAD
BERMAD 435 User manual

BERMAD
BERMAD 730-UF Owner's manual
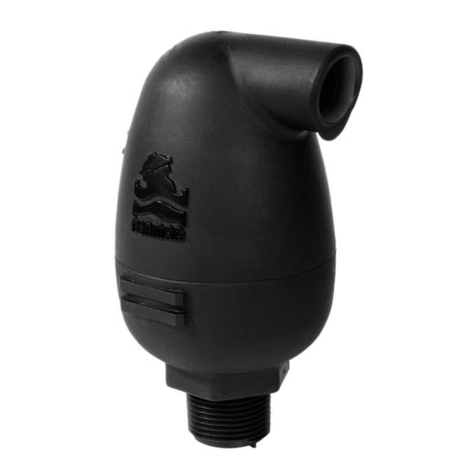
BERMAD
BERMAD C30 User manual
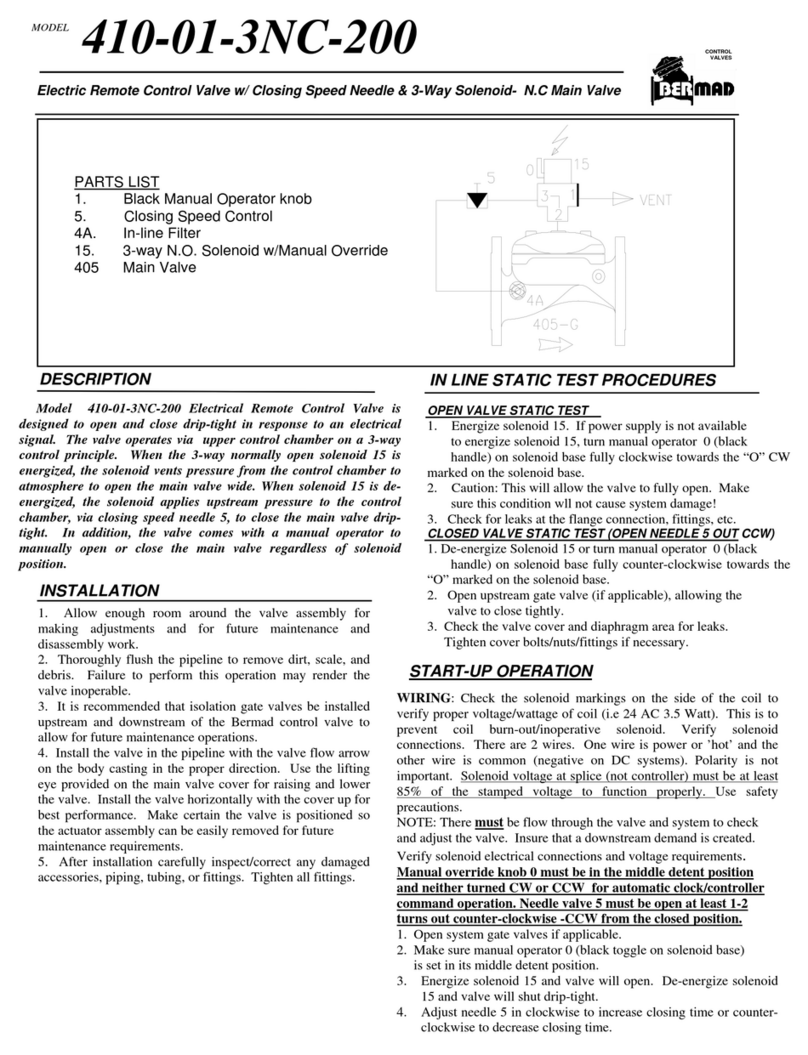
BERMAD
BERMAD 410-01-3NC-200 User manual

BERMAD
BERMAD 400 Series User manual
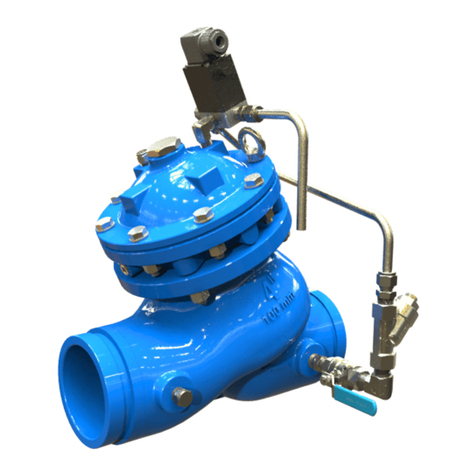
BERMAD
BERMAD BC-710-P User manual

BERMAD
BERMAD 450-60 User manual

BERMAD
BERMAD FP 430-UF Owner's manual
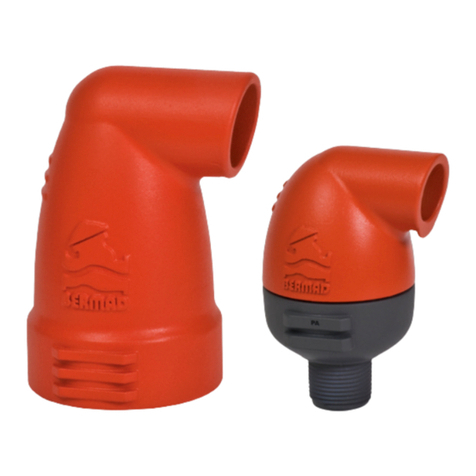
BERMAD
BERMAD K10 User manual

BERMAD
BERMAD 430 User manual