IAI ELECYLINDER User manual

Specifications
Installation
Wiring
Operation
Preventive/
Predictive Maintenance
Parameters
Troubleshooting
Maintenance and
Inspection
External Dimensions
Life
Warranty
Appendix
ELECYLINDER
ch.1
ch.2
ch.3
ch.4
ch.5
ch.6
ch.7
ch.8
ch.9
ch.
10
ch.
11
ch.
12
Instruction Manual
EC-ST15
First Edition ME3799-1C


Please Read Before Use
Thank you for purchasing our product.
This instruction manual explains the handling methods, structure and maintenance of this product,
providing the information you need in order to use the product safely.
Before using the product, be sure to read this manual and fully understand the contents explained
herein to ensure safe use of the product.
The DVD enclosed with the product contains instruction manuals for IAI products.
When using the product, refer to the necessary sections of the applicable instruction manual by
printing them out or displaying them on a PC.
After reading the instruction manual, keep it in a convenient place so that whoever is handling the
product can refer to it quickly when necessary.
[Important]
• This instruction manual is an original document dedicated for this product.
• This product cannot be used in ways not shown in this instruction manual. IAI shall not be
liable for any result whatsoever arising from the use of the product in any other way than
what is noted in the manual.
• The information contained in this instruction manual is subject to change without notice for
the purpose of product improvement.
• If any issues arise regarding the information contained in this instruction manual, contact our
customer center or the nearest sales office.
• Use or reproduction of this instruction manual in full or in part without permission is prohibited.
• The company names, names of products and trademarks of each company shown in the
text are registered trademarks.

ELECYLINDER Instruction Manual Configuration
Product name Instruction manual name Control
number
ELECYLINDER Quick Start Guide ME3765
ELECYLINDER Instruction Manual
(this document) ME3799
PC Compatible Software for RC/EC RCM-101-MW/RCM-101-USB
Instruction Manual ME0155
Touch Panel Teaching Pendant TB-02/02D Instruction Manual ME0355
Touch Panel Teaching Pendant TB-03 Instruction Manual
Wireless communication ME0375
Touch Panel Teaching Pendant
TB-03 Instruction Manual
Wired communication
For position controller
ME0376

Contents
Safety Guide ······························································································· Intro-1
Precautions for Handling ··············································································· Intro-9
International Standard Compliance ································································ Intro-11
Precautions for Handling Wireless Operation ··················································· Intro-12
Precaution for Axis Operation with Wireless Connection ···································· Intro-14
Part Names ······························································································ Intro-15
Chapter 1 Specifications
1.1 Checking the product ······························································ 1-1
Components ································································································ 1-1
How to read the model nameplate ···································································· 1-2
How to read the model number ········································································ 1-3
1.2 Mechanical specifications ························································· 1-4
Stopper cylinder EC-ST15 ·············································································· 1-4
Duty ratio ·································································································· 1-10
1.3 Options ·············································································· 1-11
RCON-EC connection specification (Model: ACR) ············································· 1-11
With brake (Model: B) ·················································································· 1-11
Home reverse specification (Model: NM) ························································· 1-11
PNP specification (Model: PN) ······································································· 1-11
Battery-less absolute encoder specification (Model: WA) ···································· 1-11
Wireless communication specification (Model: WL) ············································ 1-11
Wireless axis operation specification (Model: WL2) ············································ 1-12
2-circuit power supply specification (Model: TMD2) ············································ 1-12
1.4 Accessories ········································································ 1-13
Power I/O cable ·························································································· 1-13
Power I/O connector ···················································································· 1-14
Chapter 2 Installation
2.1 Precautions for transportation ··················································· 2-1
2.2 Installation and storage/preservation environment ························· 2-4
Installation environment ················································································· 2-4
Storage/preservation environment ···································································· 2-5
2.3 Installation of stopper cylinder ··················································· 2-6
Installation surface ························································································ 2-6
Mounting orientation Type: EC-ST15L ······························································· 2-6
Fixing bolt ··································································································· 2-7
Square nuts ································································································· 2-7
Body mounting ····························································································· 2-8
Installation to front bracket ············································································ 2-14

Chapter 3 Wiring
3.1 System configuration ······························································· 3-1
3.2 Electrical specifications ···························································· 3-2
Specifications table ······················································································· 3-2
I/O specifications ·························································································· 3-3
Brake release method (for specifications with brakes) ·········································· 3-4
Frame grounding ·························································································· 3-4
3.3 Connection arrangement diagram ·············································· 3-5
3.4 Wiring connections (for connectors) ············································ 3-7
24VDC power supply wiring ············································································ 3-7
PLC wiring ··································································································· 3-9
Connector wiring method ·············································································· 3-10
Brake release wiring ···················································································· 3-12
3.5 Wiring connections (for cables)················································ 3-12
Power I/O cable ·························································································· 3-12
Power I/O cable equipped with 4-way connector ··············································· 3-13
Power I/O cable connection ·········································································· 3-15
24VDC power supply wiring ·········································································· 3-16
PLC wiring ································································································· 3-18
Brake release wiring ···················································································· 3-19
Chapter 4 Operation
4.1 Basic operation ······································································ 4-1
4.2 Teaching tool connections and testing operation ··························· 4-2
Teaching pendant connection ·········································································· 4-2
ELECYLINDER test operation ········································································· 4-3
4.3 Stop position/operating conditions (AVD) setting/adjustment ············ 4-4
Stop position setting/adjustment (forward end/backward end) ································ 4-5
Operating conditions (AVD) setting/adjustment ··················································· 4-6
Pressing operation setting ·············································································· 4-9
4.4 I/O signals ·········································································· 4-11
I/O signal list ······························································································ 4-11
[ST0] [ST1] signals: Movement command input (backward/forward) ······················ 4-12
[RES] signal: Alarm clear input ······································································ 4-13
[BKRLS] input: Brake release input ································································· 4-13
[LS0] [LS1] signals: Position detection output (backward end/forward end) ············· 4-14
[PE0] [PE1] signals: Pressing complete output (backward end/forward end) ··········· 4-15
[*ALM] signal: Alarm output ··········································································· 4-15
Signal input time constant ············································································· 4-15
4.5 Operating method from master device ······································ 4-16
Home return operation/positioning operation: [ST0] [LS0] [ST1] [LS1] signals
··············· 4-16
Pressing operation: [ST0] [ST1] [PE0] [PE1] signals ·········································· 4-19

Chapter 5 Preventive/Predictive Maintenance
5.1 Preventive/predictive maintenance ············································· 5-1
5.2 Maintenance information ·························································· 5-2
Total travel count ·························································································· 5-2
Total travel distance ······················································································ 5-2
Overload warning level ·················································································· 5-3
5.3 Setting maintenance information ················································ 5-4
Switching to maintenance information window ···················································· 5-4
Basic operation ···························································································· 5-5
Chapter 6 Parameters
6.1 Precautions regarding parameters ············································· 6-1
6.2 How to change parameters ······················································· 6-2
Edit parameters window ················································································· 6-2
Basic operation ···························································································· 6-3
6.3 Parameter list ········································································ 6-5
6.4 Parameter function descriptions ················································· 6-6
Parameter No.1: Operation range adjustment ····················································· 6-6
Parameter No.2: Auto switch "LS" signal detection range adjustment ······················ 6-7
Parameter No.3: Change home return direction ·················································· 6-8
Parameter No.4: Home position adjustment ······················································· 6-9
Parameter No.5: Smooth accel/decel setting ···················································· 6-10
Parameter No.6: Current control setting at stop ················································· 6-11
Parameter No.7: Wireless function setting ······················································· 6-12
Parameter No.8: Power-saving setting ···························································· 6-13
Chapter 7 Troubleshooting
7.1 Troubleshooting confirmations ··················································· 7-1
7.2 Troubleshooting diagnosis ························································ 7-4
7.3 Troubleshooting with no alarm generated ···································· 7-6
Operation failure ··························································································· 7-6
Abnormal or unstable operation ······································································· 7-8
7.4 Troubleshooting by alarm groups ············································· 7-10
Alarm group A: Overload alarm ······································································ 7-11
Alarm group B: Motor abnormality alarm ·························································· 7-12
Alarm group C: Controller abnormality alarm ···················································· 7-13
Alarm group D: Controller-encoder abnormality alarm ········································ 7-14
Alarm group E: Supply voltage/power capacity abnormality alarm ························· 7-15
Maintenance warning 1: Total travel count ························································ 7-16
Maintenance warning 2: Total travel distance ···················································· 7-16
Maintenance warning 3: Overload warning level ················································ 7-17

Chapter 8 Maintenance and Inspection
8.1 Precautions for maintenance and inspection work ························· 8-1
8.2 Inspection items and schedule ·················································· 8-3
Stopper cylinder ··························································································· 8-3
Grease supply timing (Guideline) ····································································· 8-3
8.3 Visual inspection items ···························································· 8-4
External visual inspection ··············································································· 8-4
Internal visual inspection ················································································ 8-5
8.4 Cleaning ············································································· 8-10
External cleaning ························································································ 8-10
8.5 Greasing method ·································································· 8-11
Stopper cylinder ························································································· 8-11
8.6 How to replace components···················································· 8-14
Controller replacement ················································································· 8-14
Wireless communication circuit board replacement
(Controller cover (End cover assembly) replacement) ········································ 8-17
Reversing cover, Gasket replacement ····························································· 8-19
Belt replacement························································································· 8-24
Motor replacement ······················································································ 8-32
Chapter 9 External Dimensions
9.1 Stopper cylinder external dimensions ·········································· 9-1
EC-ST15L ··································································································· 9-1
Chapter 10 Life
10.1 Concept of life for stopper cylinder ··········································· 10-1
10.2 Concept of life for controller ···················································· 10-1
Chapter 11 Warranty
11.1 Warranty period ··································································· 11-1
11.2 Scope of the warranty ··························································· 11-1
11.3 Honoring the warranty ··························································· 11-1
11.4 Limited liability ····································································· 11-2
11.5 Conformance with applicable standards/regulations, etc.,
and application conditions ······················································ 11-2
11.6 Other items excluded from warranty ········································· 11-2
Chapter 12 Appendix
12.1 Index ··············································································· 12-1
12.2 Revision history ··································································· 12-4

Safety Guide
Intro-1
Safety Guide
The Safety Guide is intended to permit safe use of the product and thus to prevent risks and property
damage. Be sure to read it before handling the product.

Safety Guide
Intro-2
Safety Precautions for Our Products
Common safety precautions for the use of robots in various operations are indicated here.
No. Operation Precautions
1 Model
Selection
● This product is not intended or designed for applications where high levels of
safety are required, and so cannot guarantee that human lives will be
protected. Accordingly, do not use it in any of the following applications.
(1) Medical equipment used to maintain, control or otherwise affect
human life or physical health
(2) Mechanisms or machinery designed for the purpose of moving or
transporting people (vehicles, railway facilities, aviation facilities etc.)
(3) Machinery components essential for safety (safety devices etc.)
● Do not use the product outside the range of the specifications. Otherwise, the
product life may be drastically shortened, and product damage or facilities
stoppage may occur.
● Do not use it in any of the following environments.
(1) Locations with flammable gases, ignitable objects or explosives
(2) Locations with potential exposure to radiation
(3) Locations with ambient temperature or relative humidity exceeding the
specifications range
(4) Locations where radiant heat is applied by direct sunlight or other
large heat source
(5) Locations where condensation occurs due to abrupt temperature
changes
(6) Locations with corrosive gases
(sulfuric acid, hydrochloric acid, etc.)
(7) Locations exposed to significant amounts of dust, salt or iron
powder
(8) Locations subject to direct vibration or impact
● For an actuator used in vertical orientation, select a model which is equipped
with a brake. If a model without brake is selected, the moving parts may fall
when the power is turned OFF, causing accidents such as injury or workpiece
damage.

Safety Guide
Intro-3
No. Operation Precautions
2 Transportation ● When transporting heavy objects, do the work with two or more persons or
utilize equipment such as a crane.
● When working with two or more persons, make it clear who is to be in charge
and communicate well with each other to ensure safety.
● During transportation, carefully consider the carrying positions,
weight, and weight balance, and be careful to avoid collisions or dropping.
● Use appropriate transportation measures for transport.
The actuators available for transportation with a crane have eyebolts attached
or tapped holes to attach bolts. Follow the instructions in the instruction
manual for each model.
● Do not climb onto the package.
● Do not put anything heavy that could deform the package on it.
● When using a crane with capacity of 1t or more, have an operator qualified for
crane operation and sling work.
● When using a crane or equivalent equipment, make sure not to suspend loads
exceeding the equipment's rated load.
● Use a hook that is suitable for the load. Consider the safety factor of the hook
in such factors as shear strength. Also, check to make sure that the hook is
free of damage.
● Do not climb on loads suspended from cranes.
● Do not leave loads suspended from cranes for long periods.
● Do not stand under loads suspended from cranes.
3 Storage
and
Preservation
● For the storage and preservation environment, see the installation
environment. However, give especial consideration to the prevention of
condensation.
● Store the products so as to prevent them from falling over or down in the case
of natural disasters such as earthquakes.

Safety Guide
Intro-4
No. Operation Precautions
4 Installation
and
Startup
(1) Installation of robot body and controller, etc.
● Be sure to securely hold and fix the product (including the workpiece). If the
product falls over, is dropped, or operates abnormally, it may lead to damage
and injury.
Also, be equipped for falls over or down due to natural disasters such as
earthquakes.
● Do not climb on or put anything on the product. Otherwise, this may lead to
accidental falling, injury or damage to the product due to falling objects,
product loss of function or performance degradation, or shortening of product
life.
● When using the product in any of the places specified below, provide sufficient
shielding.
(1) Locations where electrical noise is generated
(2) Locations with strong electrical or magnetic fields
(3) Locations with mains or power lines passing nearby
(4) Locations where the product may come in contact with water, oil or
chemical spray
(2) Cable wiring
● Use IAI genuine cables for connecting the actuator and controller, and for the
teaching tools.
● Do not scratch cables, bend them forcibly, pull them, coil them, snag them, or
place heavy objects on them. Otherwise, this may lead to fire, electric shock,
or abnormal operation due to leakage or conduction malfunction.
● Perform the wiring for the product after turning OFF the power to the unit, and
avoid miswiring.
● When wiring DC power (+24V), be careful with the positive/negative polarity.
Incorrect connections may lead to fire, product breakdown or abnormal
operation.
● Connect the cable connector securely so that there is no disconnection or
looseness. Otherwise, this may lead to fire, electric shock, or abnormal
operation of the product.
● Never cut or reconnect the cables supplied with the product for the purpose of
extending or shortening the cable length. Otherwise, this may lead to fire or
abnormal operation of the product.
(3) Grounding
● Grounding must be performed, in order to prevent electric shocks or
electrostatic charge, enhance noise-resistant performance and control
unnecessary electromagnetic radiation.
● For the ground terminal on the AC power cable of the controller and the
grounding plate in the control panel, be sure to use a twisted pair cable with
wire thickness 0.5mm2 (AWG20 or equivalent) or more for grounding work.
For safeguard grounding, it is necessary to select an appropriate wire
diameter for the load. Perform wiring that satisfies the specifications
(electrical equipment technical standards).
● Perform Class D grounding (former Class 3 grounding, with ground resistance
100Ω or below).

Safety Guide
Intro-5
No. Operation Precautions
4 Installation
and
Startup
(4) Safety measures
● When working with two or more persons, make it clear who is to be in charge
and communicate well with each other to ensure safety.
● When the product is operating or in the ready mode, take safety measures
(such as the installation of safety/protection fences) so that nobody can enter
the area within the robot's movable range. Contact with an operating robot
may lead to death or serious injury.
● Be sure to install an emergency stop circuit so that the unit can be stopped
immediately in an emergency during operation.
● Take safety measures such that turning the power ON alone will not start up
the unit. Otherwise, this may cause the product to start unexpectedly, leading
to injury or product damage.
● Take safety measures such that emergency stop cancel or recovery after
power failure alone will not start up the unit. Otherwise, this may lead to injury
or equipment damage.
● When installation or adjustment operation is to be performed, display signs
such as "Operating: No Power ON!" etc. Sudden power input may cause
electric shock or injury.
● Take measures to prevent workpieces, etc. from falling during power failures
or emergency stop.
● Wear protection gloves, goggles and safety shoes, as necessary, to secure
safety.
● Do not insert fingers or objects into the openings in the product. Otherwise,
this may lead to injury, electric shock, product damage, or fire.
● When releasing the brake on a vertically oriented actuator, be careful that it
does not fall under its own weight, catching the operator's hand or damaging
workpieces.
5 Teaching ● When working with two or more persons, make it clear who is to be in charge
and communicate well with each other to ensure safety.
● Perform teaching operation from outside the safety/protection fence, if
possible. If operation must be performed within the safety/protection fence,
prepare "Work Regulations" and make sure that all the workers acknowledge
and understand them well.
● When operation is to be performed inside the safety/protection fence,
operators should have emergency stop switches available at hand so that the
unit can be stopped at any time if abnormalities occur.
● When operation is to be performed inside the safety/protection fence, have a
monitor standing by in addition to the operator(s) so that the unit can be
stopped at any time if abnormalities occur. Also, keep watch on the operation
so that a third party cannot operate the switches carelessly.
● Place a sign indicating "Operating" where it can be seen easily.
● When releasing the brake on a vertically oriented actuator, be careful that it
does not fall under its own weight, catching the operator's hand or damaging
workpieces.
* Safety/protection fence: If there is no safety/protection fence, the movable
range should be indicated.

Safety Guide
Intro-6
No. Operation Precautions
6 Trial Operation ● When working with two or more persons, make it clear who is to be in charge
and communicate well with each other to ensure safety.
● After teaching or programming, carry out trial operation step by step before
switching to automatic operation.
● When trial operation is to be performed inside the safety/protection fence, use
the same work procedure, determined in advance, as teaching operation.
● Be sure to confirm program operation at safe speeds. Otherwise, this may
lead to accidents due to unexpected motion caused by program error, etc.
● Do not touch the terminal block or any of the various setting switches while the
equipment is live. Otherwise, this may lead to electric shock or abnormal
operation.
7 Automatic
Operation
● Check before starting automatic operation or restarting after operation stop
that there is nobody within the safety/protection fence.
● Before starting automatic operation, make sure that all peripheral equipment
is ready for automatic operation and that there is no alarm indication.
● Be sure to start automatic operation from outside the safety/protection fence.
● If the product produces abnormal heat, smoke, odor, or noise, immediately
stop it and turn OFF the power switch. Otherwise, this may lead to fire or
damage to the product.
● When a power failure occurs, turn OFF the power switch. Otherwise, this may
lead to injury or product damage due to unexpected product motion during
recovery from the power failure.
8 Maintenance
and
Inspection
● When working with two or more persons, make it clear who is to be in charge
and communicate well with each other to ensure safety.
● Perform the work outside the safety/protection fence, if possible. If operation
must be performed within the safety/protection fence, prepare "Work
Regulations" and make sure that all the workers acknowledge and
understand them well.
● When work is to be performed inside the safety/protection fence, turn OFF the
power switch as a rule.
● When operation is to be performed inside the safety/protection fence,
operators should have emergency stop switches available at hand so that the
unit can be stopped at any time if abnormalities occur.
● When operation is to be performed inside the safety/protection fence, have a
monitor standing by in addition to the operator(s) so that the unit can be
stopped at any time if abnormalities occur. Also, keep watch on the operation
so that a third party cannot operate the switches carelessly.
● Place a sign indicating "Operating" where it can be seen easily.
● For the grease for the guide or ball screw, use appropriate grease according
to the Instruction Manual for each model.
● Do not perform dielectric strength testing. Otherwise, this may lead to damage
to the product.

Safety Guide
Intro-7
No. Operation Precautions
8 Maintenance
and
Inspection
● When releasing the brake on a vertically oriented actuator, be careful that it
does not fall under its own weight, catching the operator's hand or damaging
workpieces.
● The slider or rod may be misaligned from the stop position if the servo is
turned OFF. Avoid injury or damage due to unnecessary operation.
● Be careful not to lose the cover or any removed screws, and be sure to return
the product to the original condition after maintenance and inspection work.
Otherwise, this may lead to product damage or injury due to incomplete
mounting.
* Safety/protection fence: If there is no safety/protection fence, the movable
range should be indicated.
9 Modification
and
Disassembly
● Do not modify, disassemble/assemble, or use maintenance parts not specified
on your own discretion.
10 Disposal ● When the product exceeds its useful life or is no longer needed, dispose of it
properly as industrial waste.
● When removing the actuator for disposal, avoid dropping components when
detaching screws.
● Do not put the product in a fire when disposing of it. The product may rupture
or generate toxic gases.
11 Other ● If you are equipped with a medical device such as a pacemaker, do not
approach the product or its wiring, as the device may be affected.
● See the Overseas Specifications Compliance Manual to check compliance
with overseas standards if necessary.
● For the handling of actuators and controllers, follow the dedicated instruction
manual of each unit to ensure safety.

Safety Guide
Intro-8
Precaution Indications
The safety precautions are divided into "Danger", "Warning", "Caution" and "Notice" according
to the warning level, as follows, and described in the Instruction Manual for each model.
Level Degree of risk to persons and property Symbol
Danger This indicates an imminently hazardous situation which, if the product
is not handled correctly, will result in death or serious injury. Danger
Warning This indicates a potentially hazardous situation which, if the product
is not handled correctly, could result in death or serious injury. Warning
Caution
This indicates a potentially hazardous situation which, if the product
is not handled correctly, may result in minor injury or property
damage. Caution
Notice
This indicates a situation in which, while injury is not a likely result,
the precautions should be observed in order to use the product
appropriately. Notice

Precautions for Handling
Intro-9
Precautions for Handling
1. The Safety Guide attached with the product is intended to permit safe use of
the product and thus to prevent risks and property damage. Be sure to read it
before handling the product.
2. Do not attempt any handling or operation that is not indicated in this instruction
manual.
3. Make sure to secure the ELECYLINDER properly in accordance with this
instruction manual.
If the ELECYLINDER is not securely fixed, this may lead to abnormal noise, vibration, breakdown or
shortened product life.
4. Make sure to observe the usage conditions and environment of the product.
Operation outside the warranty could cause decreased performance or product breakdown.
Use within the allowable range for each item.
Item Cautions
for use
Problems or breakdowns which may
occur if the allowable
range is exceeded
Speed and
acceleration/deceleration
Use within the
allowable range
May lead to abnormal noise, vibration,
breakdown, or shortened product life.
5. Use the product under the allowable load 500N or below for thrust of such as
conveyor.
Operation outside the warranty could cause decreased performance or product breakdown.
Thrust (Vertical Load) Thrust (Vertical Load)

Precautions for Handling
Intro-10
6. If return operations are continued over a short distance, they may rapidly
degrade the film of grease.
Continuous return operation within a distance less than 30mm may cause the grease film to degrade
rapidly.
As a guideline, in every 5,000 to 10,000 cycles, have approximately 5 cycles of return operation over
a 50mm distance or more to regenerate the oil film. Continued use of the actuator in that state may
lead to breakdown.
In extreme cases, flaking may occur on the guide.
7. Base oil may separate from the grease and leak from the inside of the
ELECYLINDER to the exterior due to the operating environment, mounting
orientation, operating conditions, etc.
Protect the peripheral equipment if base oil adhesion negatively affects them.
8. Grease has been applied to the outer periphery of the rod and guide shaft for
the rod type.
Protect the peripheral equipment if grease adhesion negatively affects them.
9. The structure between the rod tip adapter and the front bracket forms a floating
feature in order to absorb impact, joint between the rod tip adapter and the rod
is fixed. Therefore, the rod tip adapter has play in the axial and rotary
directions.
Rod
Rod tip adaptor
Guide shaft
Guide shaft
Front bracket

International Standard Compliance
Intro-11
International Standard Compliance
The ELECYLINDER complies with the following overseas standards.
Refer to the Overseas Standard Compliance Manual (ME0287) for more detailed information.
If it is necessary to announce EC Declaration of Conformity with this product built in your facility, as this
product itself declares the conformity to EU Directives in some specific conditions as stated below, you
would be able to utilize this declaration.
EU Directives Applicable for EC Declaration of Conformity
EMC Directive (2014/30/EU) • • • • • To be checked in CE marking described in product nameplate.
RoHS Directive (2011/65/EU) • • • • Same as above.
RE Directive (2014/53/EU) • • • • • • To be checked in EC Declaration of Conformity.
EC Declaration of Conformity proving conformity to RE Directive may be modified without notice according
to addition of conformed models, specification change and so on. Visit our homepage (http:/www.iai-robot/)
or contact our sales site if necessary.
CE Marking UL
RoHS Directive EMC Directive RE Directive
○ ○ ○ -

Precautions for Handling Wireless Operation
Intro-12
Precautions for Handling Wireless Operation
When the option for wireless communication support (model: WL, WL2) is selected, a
wireless communication circuit board is built into the ELECYLINDER. Certificates and
self-declarations regarding the wireless function are handled under the model name below
for the wireless circuit board.
Model name: IABL3827
This product uses the 2.4 GHz radio band known as an ISM band. This frequency range is
used by various devices such as microwave ovens and wireless LAN, so that
communication may be disrupted by radio disturbance.
Use of this device is permitted within the following countries (regions) only. Use in other
countries (regions) requires certification to be obtained based on the laws and regulations of
the relevant country (region).
Wireless frequency 2,400〜2,483.5MHz
Wireless output +5dBm
【US】
This device complies with Part 15 of the FCC Rules. Operation is subject to the
following two conditions:
1. This device may not cause harmful interference and
2. This device must accept any interference received, including interference that may
cause undesired operation of the device.
FCC RF Radiation Exposure Statement:
This equipment complies with FCC radiation exposure limits set forth for an uncontrolled
environment. End users must follow the specific operating instructions for satisfying RF
exposure limits. This transmitter must not be colocated or operating with any other
antenna or transmitter.
【CANADA】
This device complies with Industry Canada licence-exempt RSS standards.
Operation is subject to the following two conditions:
1. This device may not cause interference, and
2. This device must accept any interference, including interference that may cause
undesired operation of the device
Le présent appareil est conforme aux CNR d'Industrie Canada applicables aux
appareils radio exempts de licence
L'exploitation est autorisée aux deux conditions suivantes:
1. l'appareil ne doit pas produire de brouillage, et
2. l'utilisateur de l'appareil doit accepter tout brouillage radioélectrique subi, même si
le brouillage est susceptible d'en compromettre le fonctionnement.
This manual suits for next models
1
Table of contents
Other IAI Controllers manuals
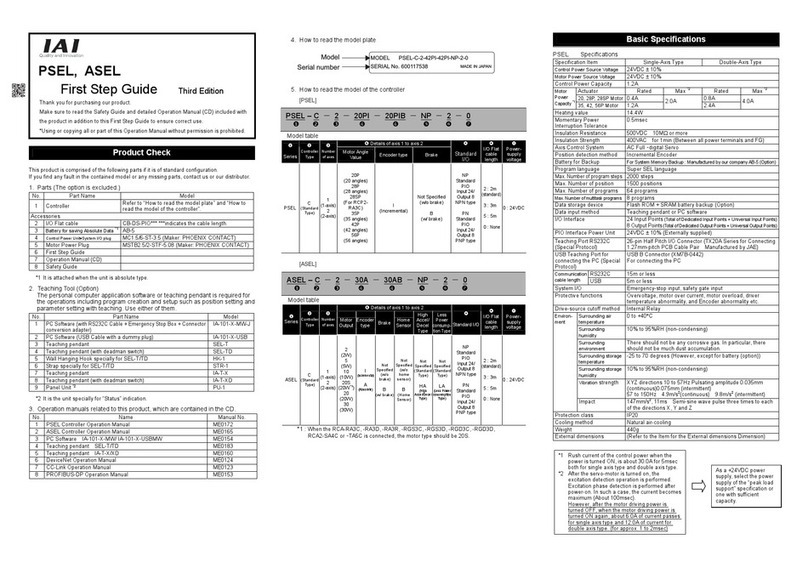
IAI
IAI PSEL series User manual
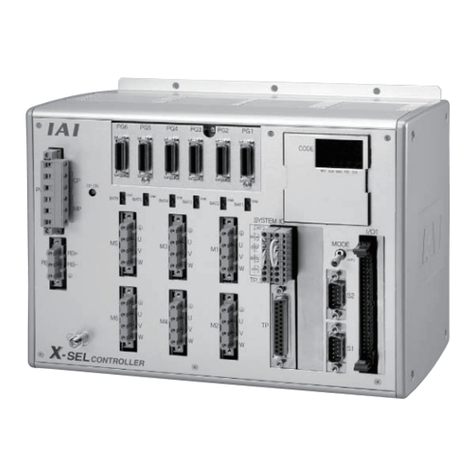
IAI
IAI X-SEL User manual
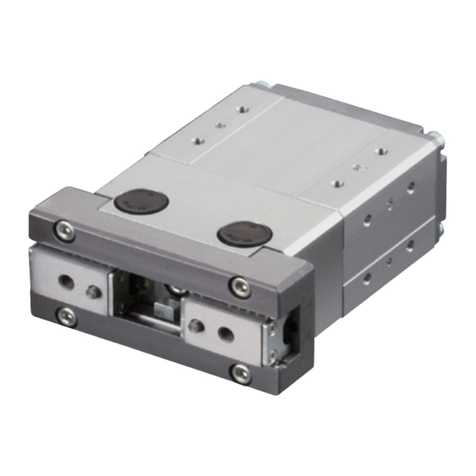
IAI
IAI RCP4 User manual
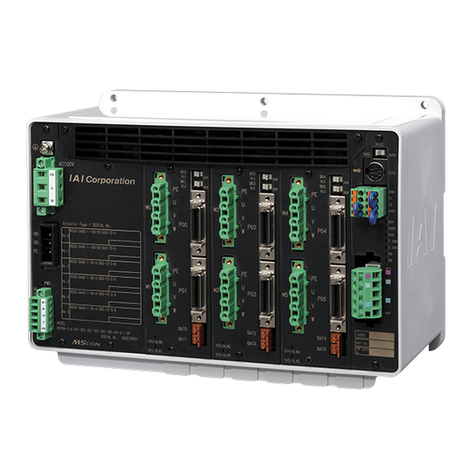
IAI
IAI MSCON User manual
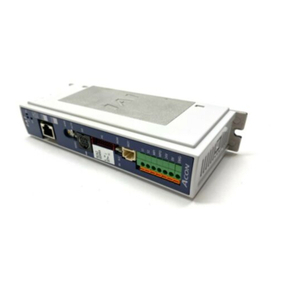
IAI
IAI ACON-C User manual
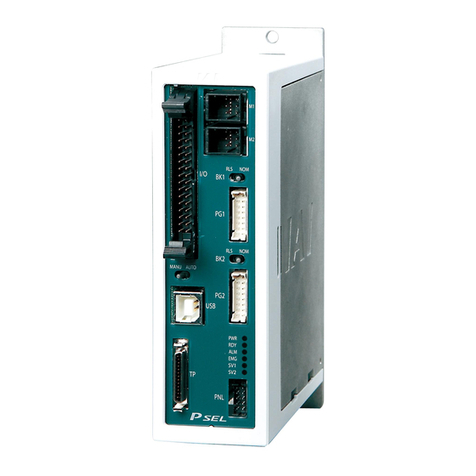
IAI
IAI PSEL User manual
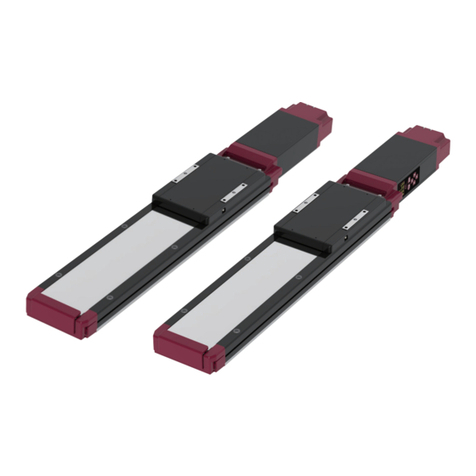
IAI
IAI ELECYLINDER EC-WS10 R Series User manual
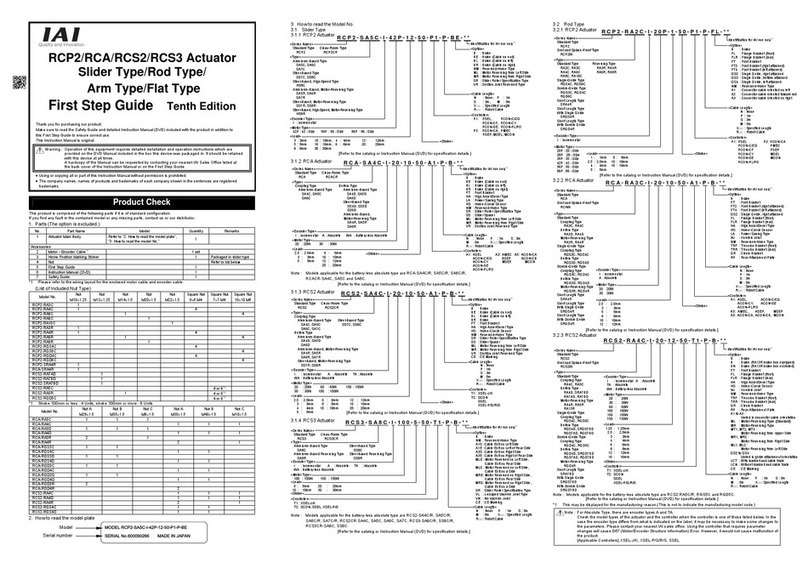
IAI
IAI ROBO Cylinder RCP2 Series User manual
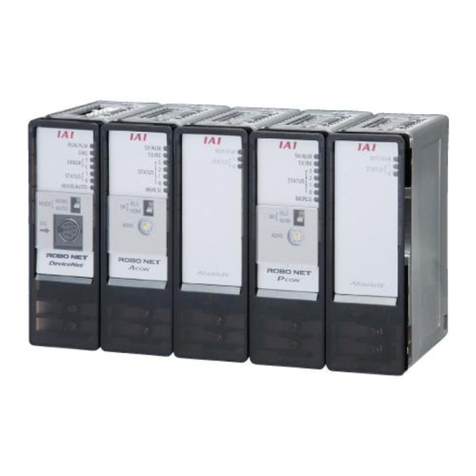
IAI
IAI RoboNet User manual
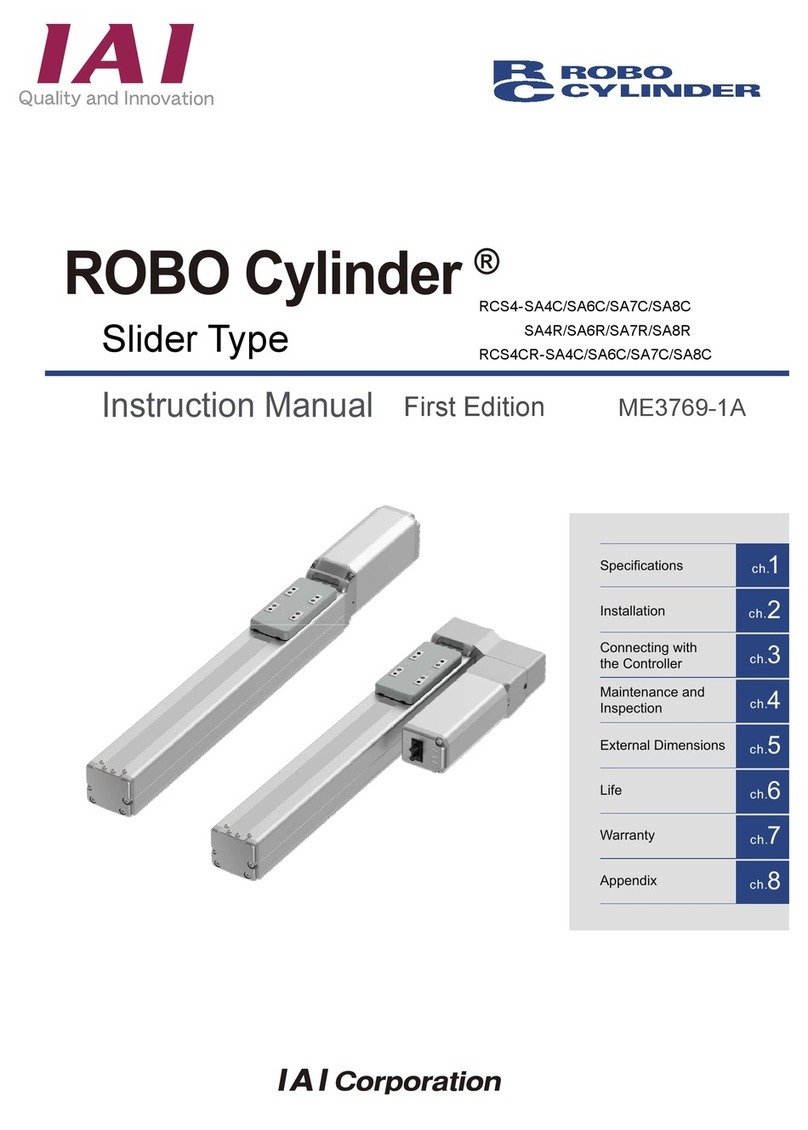
IAI
IAI ROBO Cylinder RCS4- SA4C User manual
Popular Controllers manuals by other brands

Mitsubishi
Mitsubishi a2 Series Programming manual
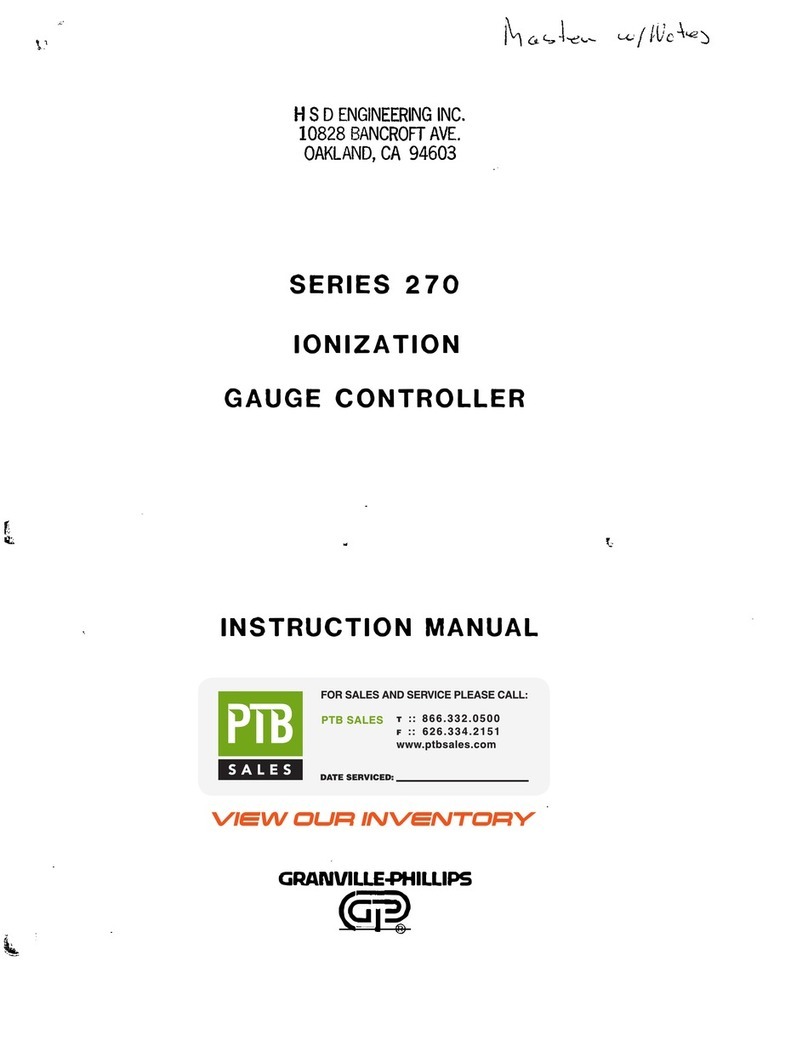
Granville-Phillips
Granville-Phillips 270001 004 instruction manual
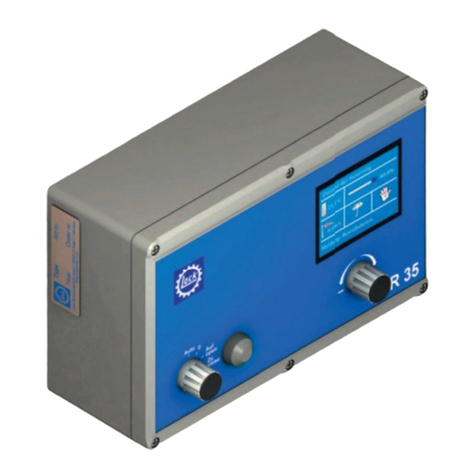
Lock
Lock LSR 35 operating instructions
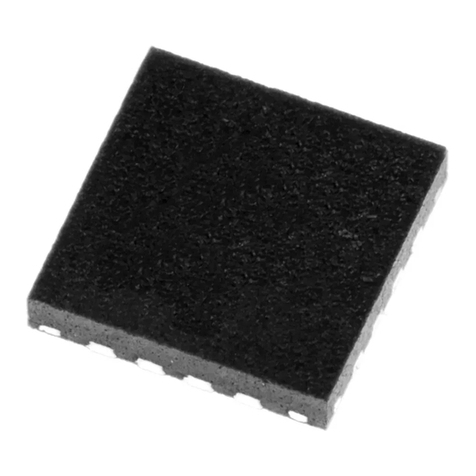
Cypress
Cypress CapSense CY8CMBR2044 Design guide
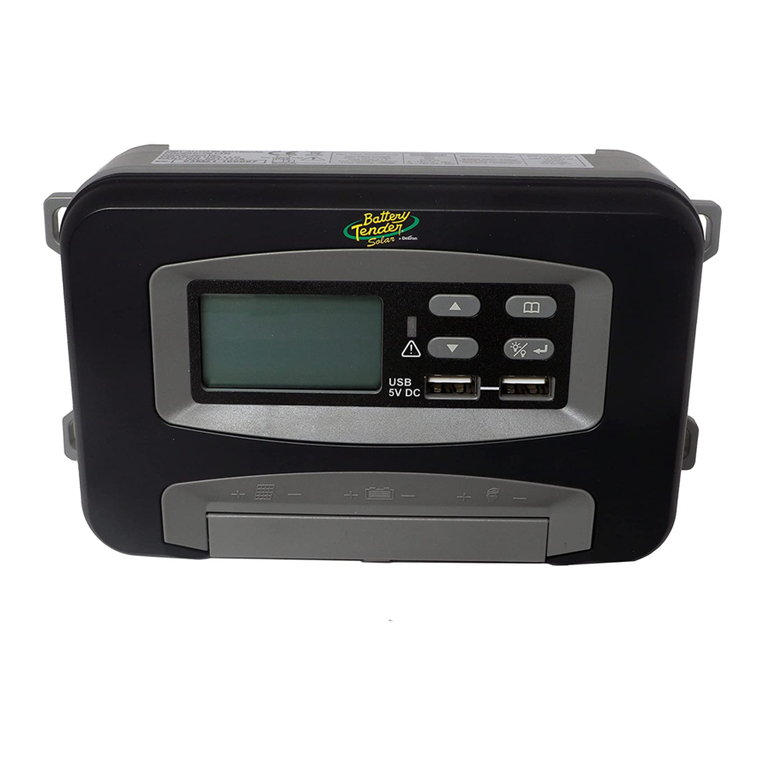
Deltran
Deltran Battery Tender Solar Charger Controller instruction manual
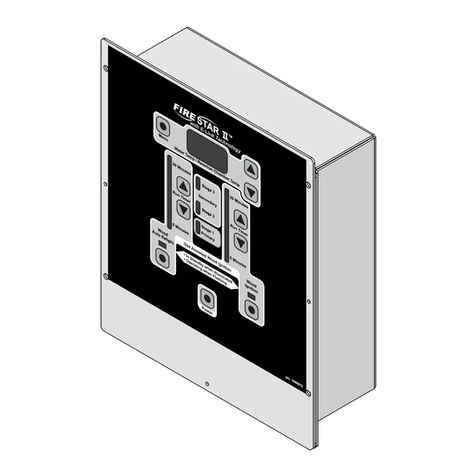
Central Boiler
Central Boiler Fire Star II Operation manual