SUTO S606 Manual

English
Instruction and Operation Manual
S606
Stationary Breathing Air Quality Analyzer

Dear Customer,
Thank you for choosing our product.
Please read the manual in full and carefully observe operating
instructions stated before you start up the device. The manufacturer
cannot be held liable for any damage that occurs as a result of non-
observance or non-compliance with this manual.
Should the device be tampered with in any manner other than a
procedure which is described and specified in the manual, the warranty
is void and the manufacturer is e empt from liability.
The device is destined e clusively for the described application.
SUTO offers no guarantee for the suitability for any other purpose.
SUTO is also not liable for consequential damage resulting from the
delivery, capability or use of this device.
2 S606

Table of Contents
1 Safety Instructions.............................................................................5
2 Registered Trademarks........................................................................8
3 Application........................................................................................8
4 Features...........................................................................................8
5 Technical Data...................................................................................9
5.1 General Data...............................................................................9
5.2 Operating Conditions.....................................................................9
6 Dimensions......................................................................................11
7 Installation on Site............................................................................12
7.1 Select Installation Location...........................................................12
7.2 Mount on the Wall.......................................................................13
7.3 Electrical Connections..................................................................14
7.3.1 Power Supply.......................................................................15
7.3.2 RS-485 Networking (Modbus/RTU)..........................................15
7.3.3 TCP/IP Networking (Modbus/TCP)............................................15
7.3.4 Alarm Outputs......................................................................16
7.4 Compressed Air Connection..........................................................17
7.5 Water Filling Connector................................................................18
7.6 Calibration Connector..................................................................19
8 Setup..............................................................................................20
9 Operation and Configuration...............................................................20
9.1 Main Screen...............................................................................22
9.1.1 Quick Buttons and Icons........................................................22
9.1.2 Icons in the Status Bar..........................................................22
9.2 Value Screen..............................................................................23
9.3 Graphic Screen...........................................................................23
9.4 Menu........................................................................................24
9.4.1 Sensor Settings ...................................................................24
9.4.2 System Setting.....................................................................25
9.4.3 Service Company Information.................................................26
9.4.4 Calibration of Gas Sensors.....................................................27
9.4.5 Files....................................................................................28
9.4.6 Logger Setting.....................................................................29
9.4.7 Alarm Setting.......................................................................30
9.4.8 Communication....................................................................31
10 Software Installation.......................................................................32
11 Firmware Updates...........................................................................33
12 Calibration.....................................................................................35
12.1 Calibration for DP Sensor and Oil Sensor......................................35
12.2 Calibration for O2,CO, CO2 Sensor..............................................35
12.2.1 Calibration Gases................................................................36
12.2.2 Calibration Procedure...........................................................37
S606 3

13 Optional Accessories........................................................................43
14 Maintenance...................................................................................43
15 Disposal or Waste...........................................................................43
16 Warranty.......................................................................................43
17 Appendi - Modbus Holding Register Table..........................................44
17.1 Modbus Interface......................................................................44
17.2 Modbus Register Table...............................................................45
4 S606

1 Safety Instructions
Safety Instructions
Please check if this instruction manual matches the
product type.
Please observe all notes and instructions indicated in this
manual. It contains essential information which must be
observed before and during installation, operation and
maintenance. Therefore this instruction manual must be read carefully
by the technician as well as by the responsible user / qualified
personnel.
This instruction manual must be available at the operation site of the
flow sensor at any time. In case of any obscurities or questions,
regarding this manual or the product, please contact the manufacturer.
WARNING!
Compressed air!
Any contact with quickly escaping air or bursting
parts of the compressed air system can lead to
serious injuries or even death!
•Do not e ceed the ma imum permitted pressure range. (See
sensors label and/or the specifications written in this manual.)
•Only use pressure tight installation material.
•Avoid that persons get hit by escaping air or bursting parts of the
instrument.
•The system must be pressure less during maintenance work.
WARNING!
Voltage used for supply!
Any contact with energized parts of the product may
lead to an electrical shock which can lead to serious
injuries or even death!
•Consider all regulations for electrical installations.
•The system must be disconnected from any power supply during
maintenance work.
•Do not e ceed the permitted operating parameters as specified in
the data sheet, this manual or written on the instrument.
•Make sure the product is operated in its permitted limitations.
S606 5

1 Safety Instructions
•Do not e ceed or undercut the permitted storage and operation
temperature, pressure and humidity.
•The product should be maintained and calibrated frequently, at
least annually. For more information, contact customer support.
General safety instructions
•It is not allowed to use the product in e plosive areas.
•Please observe the national regulations before/during installation
and operation.
Remarks
•It is not allowed to disassemble the product.
•Always check the compressed air connectors in terms of stability
and tightness.
ATTENTION!
Measurement values can be affected by malfunction!
The product must be installed properly and frequently
maintained. Otherwise it may lead to wrong
measurement values, which can lead to wrong results.
•The instrument must be operated within or better than
compressed air quality Class 4.4.4 according to the ISO8573-1. If
the air quality cannot reach the specified Class, the device may
show wrong measurement values or even may get damaged.
•Do not e ceed the ma imum operation temperature or pressure.
•Avoid condensation inside the instrument caused by the supplied
air or gas because it harms the instrument and affects the
accuracy.
•It is recommended that before any operation you e amine the
instrument in terms of the measurement accuracy and deviations.
To do this, you may use high efficiency filters for oil vapor and
particle, and the instrument should show low values close to zero.
Additionally, it is recommended you e amine the dew point
measurement to ensure it is working correctly. To do this, you may
use a dry gas with a defined dew point value which should be
reached within several minutes. Or you may use any reference
meter. Only after doing these e aminations, you can rely on the
measurement results after the instrument have been used for
other measurement cycles.
6 S606

1 Safety Instructions
•Always perform a visual inspection in prior to every measurement
before connecting compressed air. If any loose objects are found,
do not connect the compressed air because it may lead to a
damage or injuries.
Storage and transportation
•Make sure that the transportation temperature is between
-10°C ... +50°C.
•For transportation it is recommended to use the packaging which
comes with the sensor.
•Please make sure that the storage temperature of the sensor is
between -10°C ... +50°C.
•Avoid direct UV and solar radiation during storage.
•For the storage the humidity must be <90%, no condensation.
ATTENTION!
Equipment may get damaged!
Please make sure that your measuring point is free
of excessive contamination/dirt. This should be
maintained before every measurement.
•Observe the measuring point always before measurement if it is
free of contamination like water drops, oil drops or other rough
contamination.
•Should water hit the inner electronics, the senors could be
seriously damaged.
•Any rough contamination of particles, water, oil or other impurities
may damage the instrument or affect the accuracy.
•Check your measurement point with the enclosed test kit, by
purging air in prior to the use of the instrument through the test
kit. A clean tissue may help to identify oil, water or any other
lubricants in the air.
S606 7

2 Registered Trademarks
2 Registered Trademarks
SUTO®Registered trademark of SUTO iTEC
MODBUS®Registered trademark of the Modbus Organization,
Hopkinton, USA
3 Application
The S606 is a stationary device to continually monitor the breathing air
quality. It can measure O2, CO, CO2, H2O, Oil, and ensures the breathing
air quality to meet the international standard such as EN 12021, CSA
Z180.1-0, and more. The S606 provides a safe and healthy
environment for the operator.
The S606 is mainly used in the industrial environment. It can not be
used in hazardous or e plosive environment and it is not suitable for
permanent outside applications.
4 Features
•All-in-one device measures O2, CO, CO2, H2O, and Oil.
•Measures additionally the temperature and pressure.
•Visible alarm notification and fle ible alarm threshold
configuration.
•Modbus/RTU (RS-485) and Modbus/TCP (Ethernet) interface are
supported.
•Remote monitoring can be easily realized through a 4G dongle and
the free software.
•User-friendly display with all important information.
•Compressed air connection via 6 mm tube.
•Integrated data logger saves data for later analysis.
•Robust housing and easy installation.
8 S606

5 Technical Data
5 Technical Data
5. General Data
Power supply 100 ... 240 VAC, 50/60 Hz, 50 VA
Display Touchscreen, Size: 5”
Resolution: 800 480 p
Data logger Internal, 30-million values
Interface USB
Ethernet (Modbus/TCP)
RS-485 (Modbus/RTU)
4G/LTE Modem (Optional)
Output 1 internal Relay
8 channel relay module(optional)
Process connection Micro quick connector, full pass through, male
(1.5 m hose with coupling included)
Housing material Sheet steel, powder-coated on the outside
Protection class IP54 (cover closed)
Dimension 600 600 250 mm
Approvals FCC, EC
Weight 34 kg
5.2 Operating Conditions
Measuring medium Compressed breathing air
Humidity of the medium < 40%, non condensation
Temperature of the medium 0°C ... +45°C
Operation pressure 0.4 ... 1.5 MPa(g)
For higher pressure need pressure
reducer e ternally
Storage & Transport temperature -10°C … + 50°C
Ambient temperature 0°C … +50°C
Ambient humidity 0... 90% rH
Sample flow rate 6 LPM@4 MPa(g), depends on input
pressure
S606 9

5 Technical Data
Sample rate 1 sample/sec
5.3 Measurement Data
Oil Vapor
Measuring range 0.001 ... 5.000 mg/m³
(Based on 1000 hPa(a), 20°C, 0% relative humidity)
Accuracy 5% of reading ± 0.003 mg/m³
Resolution 0.001 mg/m³
Sensor principle Photo ionization detector
UV lamp lifetime 6,000 working hours or 1 year, whichever comes
first
Oil Mist and Particle Sensor (Only for version S606-C)
Measuring range 0.0 ... 5.0 mg/m³
(Based on 1000 hPa(a), 20°C, 0% relative humidity)
Accuracy 15% of reading ± 0.1 mg/m³
Resolution 0.1 mg/m³
Sensor principle Oil mist and Particle sensor
O2 Sensor
Measuring range 0 … 25%
Accuracy ±(1% of reading + 0.05%)
Resolution 0.1%
Sensor principle Optical o ygen sensor
CO Sensor
Measuring range 0 … 20 ppm
Accuracy ±(5% of reading + 1 ppm)
Resolution 0.1 ppm
Sensor principle Electrochemical sensor
CO2 Sensor
Measuring range 0 … 1000 ppm
Accuracy ±(1% of reading + 25 ppm)
Resolution 1 ppm
Sensor principle NDIR sensor
10 S606

5 Technical Data
H2O (dew point)
Measuring range -100 … +20 °C Td / 0 … 17458.6 mg/m³
Accuracy ±1 °C Td (0 … 20 °C Td)
±2 °C Td (-70 … 0 °C Td)
±3 °C Td (-100 … -70 °C Td)
Resolution 0.1°C Td
Sensor principle QCM + Polymer
Pressure Sensor
Measuring range 0 ... 16 bar(g)
Accuracy 0.5% full scale
Resolution 0.01 bar
Sensor principle Piezzo resistive pressure sensor
6 Dimensions
Dimensions in mm:
S606 11

7 Installation on Site
7 Installation on Site
Make sure that all components listed below are included in your
package.
Qty. Description Item No.
1 S606 Stationary Breathing Air Quality
Analyzer in a wall mountable cabinet
S606-I version:
D500 0606 (with oil
vapor sensor)
S606-C version:
D500 1606 (with oil
mist and particle
sensor)
1 USB OTG memory stick A554 0087
1 Purge filter for pre-measurement (test kit) A554 0604
1 6 mm Teflon hose with quick connector on
one end and compressed air coupling on
the other end, 1.5 m
A554 3316
1 M12 Connector C219 0059
1 Operation and instruction manual No P/N
1 Certificate of calibration No P/N
If you need replacement materials from the list above or need further
useful accessories, contact the manufacturer or your local distributor.
7. Select Installation Location
The device needs to be set up ne t to the measuring point.
The air supply tube should not be bended too strongly and should be
installed with a big curve radius.
ATTENTION!
The device is designed to be operated indoors only.
12 S606

7 Installation on Site
7.3 Electrical Connections
The S606 provides the following electrical connectors:
•The power supply is installed through a PG cable gland. The wires
are connected to the internal screw terminals.
•One M12 connector for Modbus/RTU
•One RJ-45 Ethernet connector for Modbus/TCP
•One M12 connector for conecting the optional 4G LTE modem
•Two PG cable glands to connect to the optional relay output
module
S606 bottom view
14 S606

7 Installation on Site
7.3. Power Supply
The power cable for the 230 VAC is
connected to the terminals inside
of the cabinet, as shown in the
figure on the left.
An internal power supply (P/N:
A554 0111) unit converts AC power
to DC power, suppling power for
the sensors.
ATTENTION!
Please observe voltage ranges and power levels!
7.3.2 RS-485 Networking (Modbus/RTU)
Through the M12 connector, the S606 can be connected to the RS-485
network over the Modbus/RTU protocol.
The RS-485 networking uses the following 3 pins in the M12 connector.
The pin assignment is described below.
Pin No. Assignment Function
4 Data + Modbus Data + signal
5 Data - Modbus Data - signal
1 GND RS-485 Ground of RS-485
7.3.3 TCP/IP Networking (Modbus/TCP)
Through the RJ-45 connector at the bottom, the S606 can be connected
to the TCP/IP network over the Modbus/TCP protocol.
Remove the protection cap and plug in the network cable (RJ-45).
S606 15
1

7 Installation on Site
7.3.4 Alarm Outputs
S606 provides one relay (I terminal) for summary alarm output (AC
250V 6A/DC 30V 6A) in the S606 cabinet.
The following figure shows the back of the S606 where the relay
terminal I is located.
There is an optional 8 channel relay module available (AC: 0.5 A @ 120
V; 0.25 A @ 240 V. DC: 1 A @ 30 V; 0.3 A @ 110 V).
All the relays on the module can be configured.
The e ample below shows a DC alarm unit wiring.
16 S606

7 Installation on Site
7.4 Compressed Air Connection
The S606 offers a compressed air inlet at the bottom of the cabinet.
S606 bottom view
ATTENTION!
Permissible pressure!
Please observe the maximum permissible incoming
pressure. It must be in between 0.4 and .5 MPa. If
the pressure exceeds, the device will be damaged. If
the pressure is too low, the volume flow will not be
high enough, which will lead to wrong results.
ATTENTION!
Before you connect the device to your point of
measurement, make sure that there is no rough
contamination such as water / oil drops or heavy
dust. This could damage the sensor units.
Please use the purge filter test kit to check the
contamination.
To check the measuring point, do the following:
1. Connect the purge filter test kit onto your measuring point.
S606 17

7 Installation on Site
2. Turn on the purge valve on the test kit and purge some air for a
short period.
3. Check the filter in the test kit for high contamination of water, oil
or dust.
4. If the filter is contaminated severely, stop using the S606 to
measure because this may lead to serious damage. In case you
are not sure, contact the manufacturer.
7.5 Water Filling Connector
To ensure that the measured gas is in a reasonable humidity, a
humidifier is integrated in the S606, thus the CO sensor will not be
damaged because the measured gas is too dry.
The water filling connector is located on the left side of S606. The water
draining connector is located on the bottom of the S606.
When the water level is too low, the low water level indication in the
status bar blinks, which reminds you to fill water for the humidifier.
To fill water, remove the protection caps from the water inlet and air
outlet first, then use a bottle to fill water. Obersve the water level
indication in the status bar. When the high water level indication blinks,
stop to fill. Then put on the two protection caps.
ATTENTION!
Please fill with water before the first use!
After the S606 is functional, refill water in time. The
capacity of the water tank is about 800 ml, and the
humidifier lifetime is about 80 days (base on the
18 S606

7 Installation on Site
general condition). If the water level is too low, the
device will be switched off!
For the injected water, it is recommended to use
pure/demineralized water. Unclean water can cause
scaling and even contaminate sensors.
7.6 Calibration Connector
The calibration connector is located on the left side of the S606. When
the sensors need to be calibrated, remove the connector cap, connect
the calibration hose and do the calibration. When the calibration is finished,
put on the cap to avoid the dust or other substance entering. For more
information see section 12 Calibration.
S606 19

8 Setup
8 Setup
The S606 is configured e -work and ready to measure when you get it.
The setup settings are saved in the device and will not be lost even
after a power failure.
The device also enables you to change the e -work settings. For more
information, see section 9.4.
ATTENTION!
If you have problems setting up the device, contact
the manufacturer or your local dealer for assistance.
If a power failure occurs during the measurement,
the measurement data will not be saved.
9 Operation and Configuration
When the S606 is
powered on, the
initialization screen is
displayed with an
active progress bar.
During the
initialization, the device
configures the sensors
and runs initialization
routines.
Attention displays after
initialization, reminding
user to use the test kit
to avoid the sensor
damaged because of
the contamination.
20 S606
Table of contents
Other SUTO Measuring Instrument manuals
Popular Measuring Instrument manuals by other brands
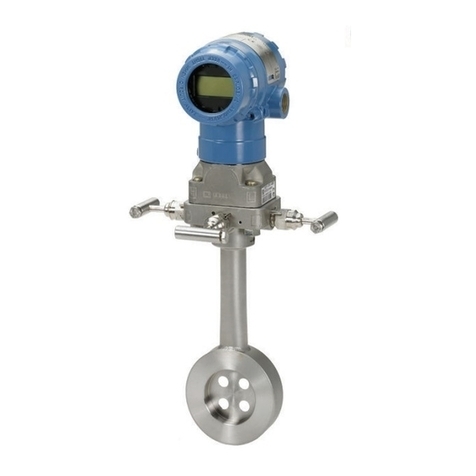
Emerson
Emerson Rosemount 2051CF series quick start guide
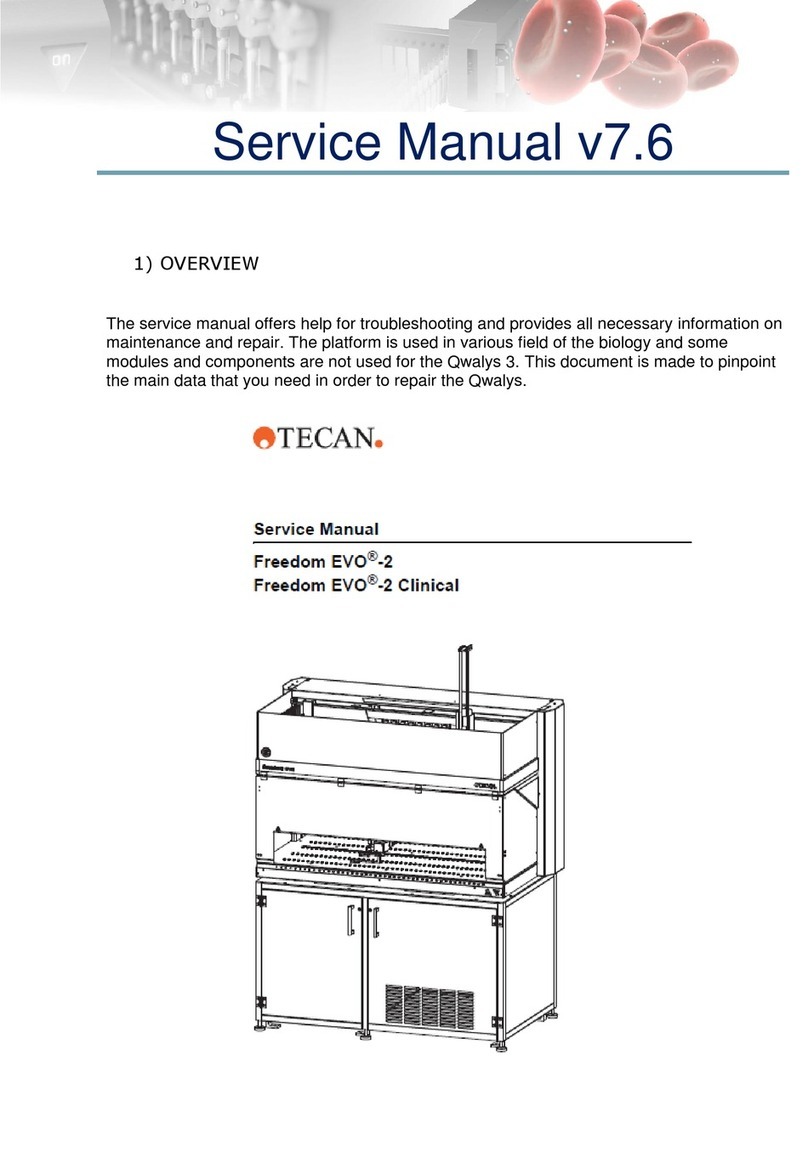
tecan
tecan Freedom EVO-2 Service manual
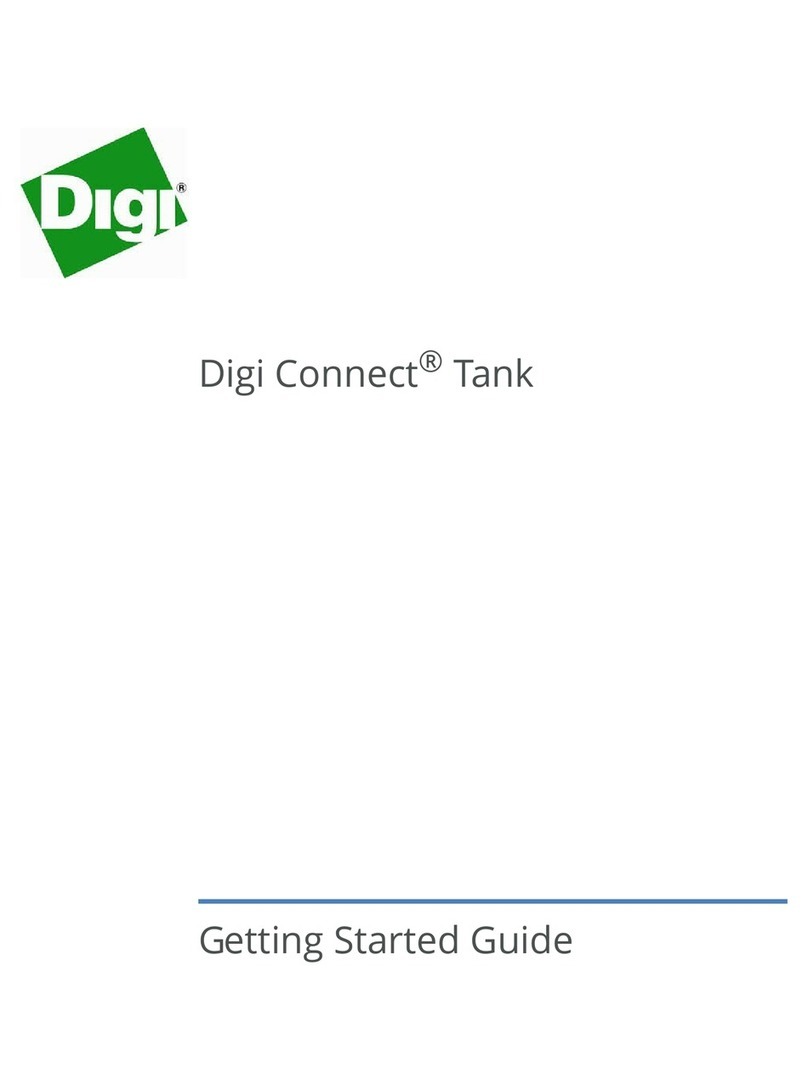
Digi
Digi Connect Tank Getting started guide

Ametek
Ametek Dunkermotoren BGE 6060 A EC Translation of the original function and connection guide
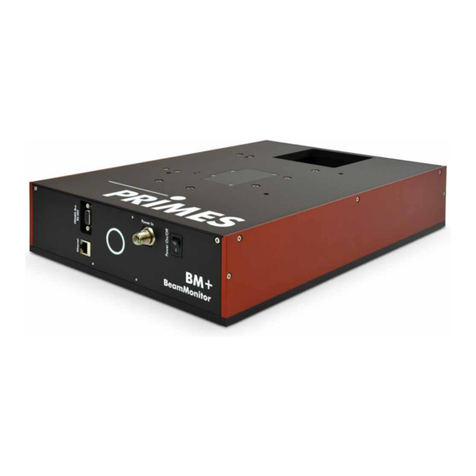
Primes
Primes BM+ 60 Original instructions

Metrohm
Metrohm 912 manual
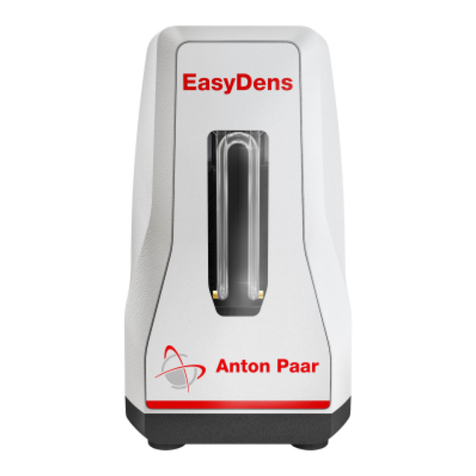
Anton Paar
Anton Paar EasyDens Instruction Manual and Safety Information

Honeywell
Honeywell BK V2 operating instructions
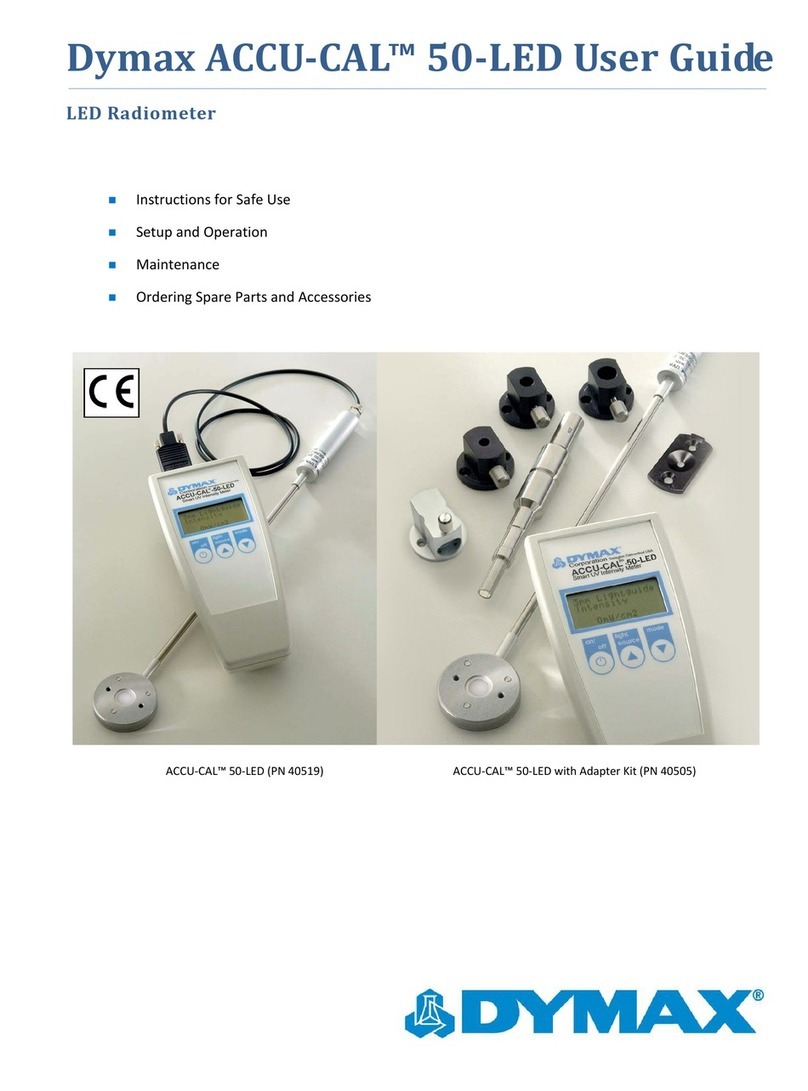
dymax
dymax ACCU-CAL 50-LD user guide
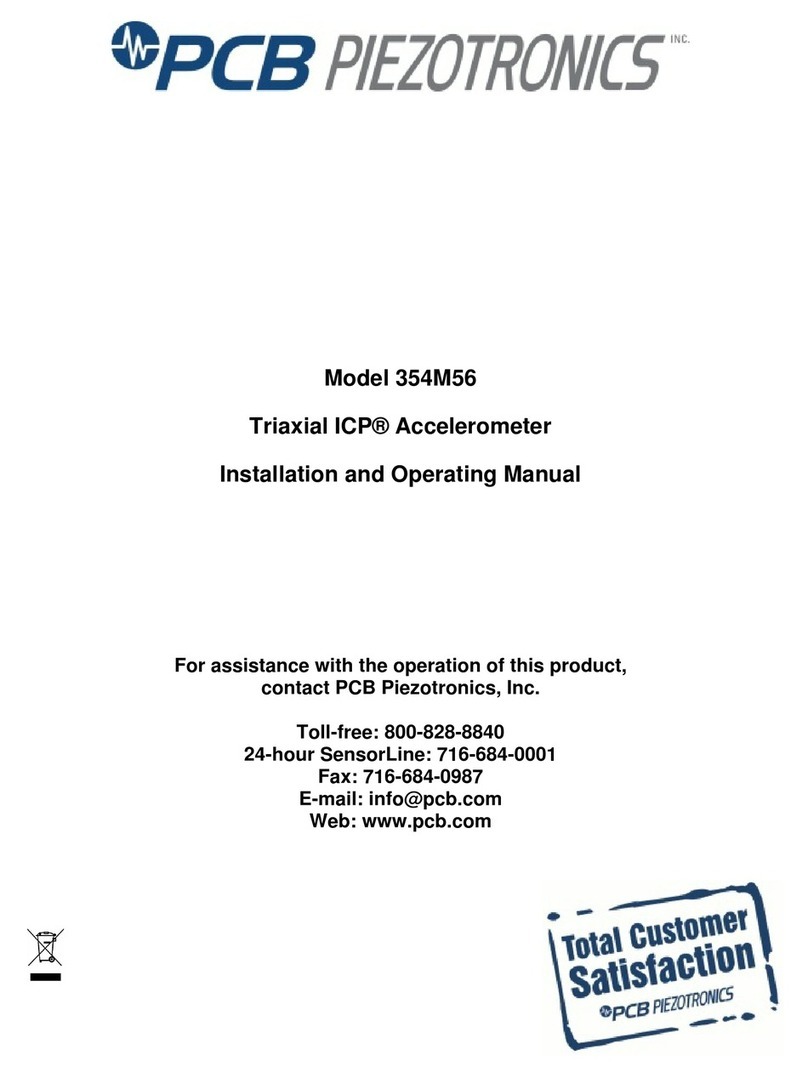
PCB Piezotronics
PCB Piezotronics 354M56 Installation and operating manual
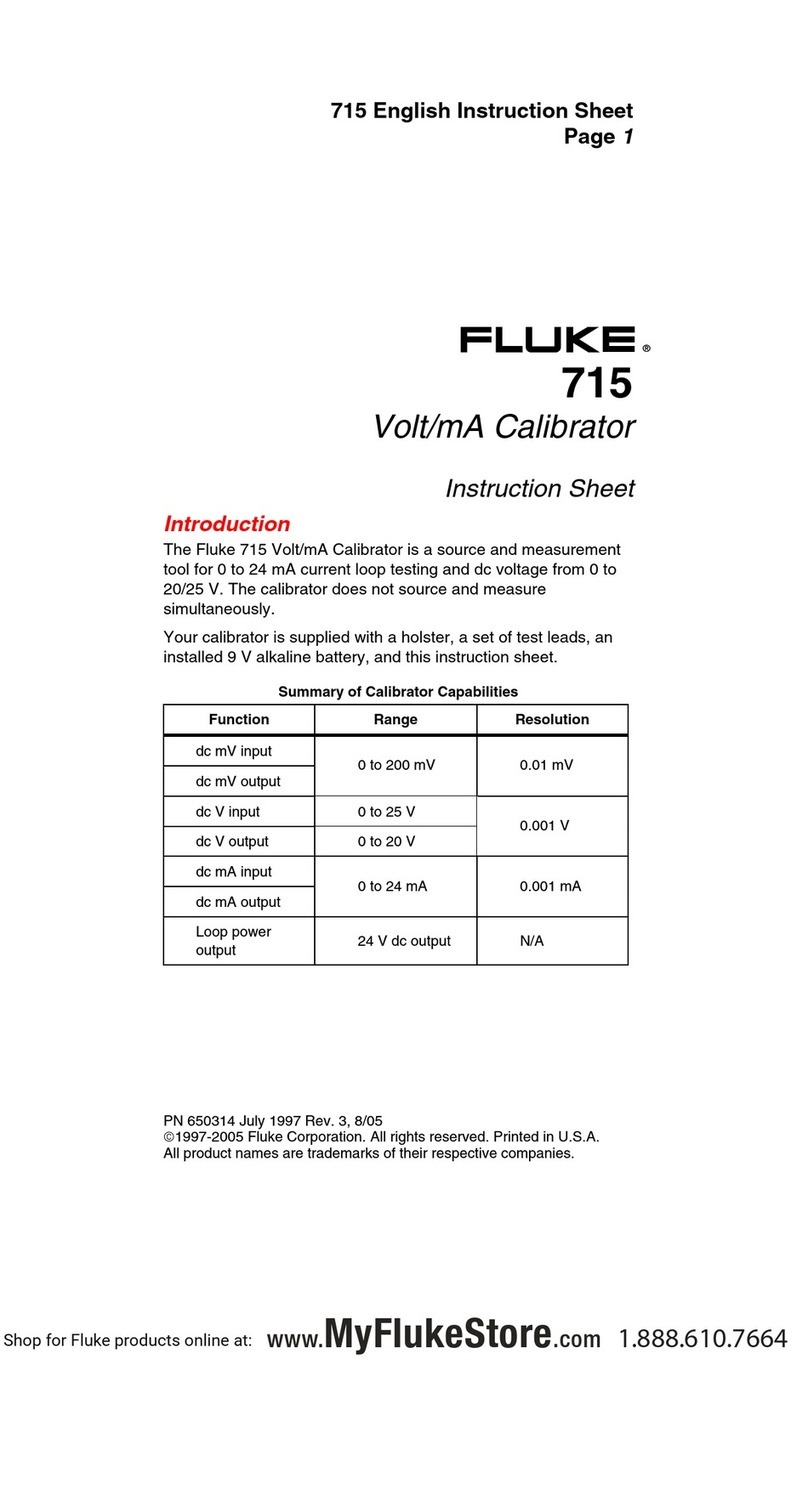
Fluke
Fluke 715 instruction sheet

Dewetron
Dewetron DEWE-30-32 Technical reference manual