ADTEK CS2-SG User manual

CS2-SG-2010-09-27
C2-03-2/11
CS2-SG
STRAIN GAUGE Indicator
DESCRIPTION
CS2-SG Strain Gauge Indicator has been designed with high accuracy
measurement, display and communication of DC signal 0~1.0/~4.0mV
or 0~10.0/~40.0mV as like as Load Cell or Strain Gauge.
The meter supports Field Calibration function. It can be calibrated
with sensor(Load Cell/Strain Gauge) to meet machinery structure.
They are also building in 4 Relay outputs, 3 External Control Inputs, 1
Analogue output and 1 RS485(Modbus RTU Mode) interface with
versatile functions such as control, alarm, re-transmission and
communication for a wide range of machinery and testing equipments
applications.
FEATURE
●Measuring load cell, strain gauge signal 0~1.0/~2.0/~4.0/~10.0/~20.0/~40.0mV/V(Specify)
●Field calibration with load cell or strain gauge to meet the system requirement
●4 relay can be programmed individual to be a Hi / Lo / Hi Latch / Lo Latch / Go energized with Start Delay /
Hysteresis / Energized & De-energized Delay functions, or to be a remote control.
●Analogue output and RS 485 communication port in option
●3 external control inputs can be programmed individual to be Tare (Relative PV) / PV Hold / Maximum or
Minimum Hold / DI (remote monitoring) / Reset for Relay Energized Latch….
●CE Approved & RoHS
APPLICATIONS
●Testing Equipments for weight/force Measuring, Alarm, Control and Communication with PC/PLC
●Leakage testing equipment by tare and relay function.
●Weighting control for packing machine, filling machine.
ORDERING INFORMATION
CS2−SG−
Input
Signal
−
Relay
Output
−
Analogue
Output
−
RS 485
Port
−
Excitation
Supply
−
Aux.
Powered
−
*Optional
Function
Customize function is welcome. Please
contact with our sales for detail.
COD
E
I/P RANGE
CODE
I/P RANGE
CODE
RELAY O/P
CODE
ANALOG
O/P
CODE
RS485 PORT
CODE
EXCITATION
CODE
AXU. POWER
S1
1.0mV/V
S8
10.0mV/V
N
None
N
None
N
None
E05
DC 5V
A
AC 115/230V
S2
2.0mV/V
S9
20.0mV/V
R2
2 Relay
V
0(1) ~ 5 V
0 ~ 10 V
8
RS 485
E10
DC 10V
S3
4.0mV/V
SA
40.0mV/V
R4
4 Relay
EO
Specify
ADH
AC 85~264V
DC 100~300V
SO
Specify
I
0 ~ 10 mA
4(0)~20 mA
CODE
OPTION FUNC.
HSM
High Speed
Mode
ADL
DC 20~56V
5DG
5 Digital Display
TECHNICAL SPECIFICATION
Over range indication:
ovfl,when input is over 20% of input range Hi
Underrange indication:
-ovfl,when input is under -20% of input range Lo
Input
Max / Mini recording:
Maximum and Minimum value storage during power on.
Measuring Range
Input Impedance
Excitation Voltage
Display functions:
PV / Max(Mini) Hold / RS 485 Programmable
0~1.0/~2.0/~4.0 mV/V
≥1M ohm
DC 5V, 40mA
or DC 10V, 40mA
Front key functions:
Up and down key can be set to be a function as ECI.
0~10.0/~20.0/~40.0 mV/V
Low cut:
Settable range: -19999~29999 counts
Digital fine adjust:
pVzro: Settable range: -19999~+29999/99999
Calibration:
Digital calibration by front key
pVspn: Settable range: -19999~+29999/99999
Field calibration:
Calibration with sensor input high & low to meet system
structure. And field calibration reset is not change the
accuracy & linear of factory calibration.
Reading Stable Function
Average:
Settable range: 1~99 times
A/D converter:
16 bits resolution
Moving average:
Settable range: 1(None)~10 times
Accuracy:
≤± 0.04% of FS 1C;
Digital filter:
Settable range: 0(None)/1~99 times
Sampling rate:
15 cycles/sec
High speed mode: can be 60cycle/sec(scaling:0~6000)
Control Functions(option)
Response time:
≤100 m-sec.(when the AvG = “1”) in standard
Set-points:
Four set-points
Input range:
Input High and Low programmable
Control relay:
Four relays
aIhi:Settable range: 0.00~100.00% of input range
Relay 2 & Relay 3: Dual FORM-C, 5A/230Vac, 10A/115V
aIlo: Settable range: 0.00~100.00% of input range
Relay 1 & Relay 4: Dual FORM-A, 1A/230Vac, 3A/115V
Relayenergizedmode:
Energized levels compare with set-points:
Display & Functions
Hi / Lo / Go.12 / Go.23 / Hi.HLd / Lo.HLd; programmable
LED:
Numeric: 5 digits, 0.8”(20.0mm)H red high-brightness LED
DO function: Energized by RS485 command of master.
Relay output indication: 4 square red LED
Energizing functions:
Start delay / Energized & De-energized delay / Hysteresis /
RS 485 communication: 1 square orange LED
Energized Latch
E.C.I. function indication: 3 square green LED
Start band(Minimum level for Energizing): 0~9999counts
Max/Mini Hold indication: 2 square orange LED
Start delay time: 0:00.0~9(Minutes):59.9(Second)
Display range:
-19999~29999; 5 Digital Display:-19999~99999
Energized delay time: 0.00.0~9(Minutes):59.9(Second)
Scaling function:
lOsc:Low Scale; Settable range: -19999~+29999/99999
De-energized delay time: 0.00.0~9(Minutes):59.9(Second)
hIsc: High Scale; Settable range: -19999~+29999/99999
Hysteresis: 0~5000 counts
Decimal point:
Programmable from 0 / 0.0 / 0.00 / 0.000 / 0.0000
CSM-321S
CS2-VA
CSM-321S
CSM-
321S
CSM-
321S
CS2-SG
CSM-321S
CSM-
321S
CSM-
321S
CSM-321S
CSM-
321S
CSM-321S
OPTION 1
OPTION 2
OPTION 3
OPTION 4

CS2-SG-2010-09-27
C2-03-3/11
External Control Inputs(ECI)
DIMENSIONS
Input mode:
3 ECI points, Contact or open collect input, Level trigger
Functions:
Relative PV (Tare) / PV Hold / Reset for Max or Mini. Hold /
92.0+0.2
44.0+0.2
PANEL CUT-OUT
96.0
48.0
FRONT VIEW
Unit: mm
8.0
12.0
100.0
Dimensions: 96mm x 48mm x 120mm
Panel Cutout: 93mm x 45mm (advise)
DI / Reset for Relay Energized latch
Debouncing time:
Settable range 5 ~255 x (8m seconds)
Analogue output(option)
Accuracy:
≤0.1% of F.S.; 16 bits DA converter
Ripple:
≤0.1% of F.S.
Response time:
≤100 m-sec. (10~90% of input)
Isolation:
AC 2.0 KV between input and output
Output range:
Specify either Voltage or Current output in ordering
Voltage: 0~5V / 0~10V / 1~5V programmable
Current: 0~10mA / 0~20mA / 4~20mA programmable
Output capability:
Voltage: 0~10V: ≥1000Ω;
Current: 4(0)~20mA: ≤600Ωmax
INSTALLATION
Functions:
aOhs(output range high): Settable range: -19999~29999/99999
aOls(output range Low): Settable range: -19999~29999/99999
The meter should be installed in a location that does not exceed the
maximum operating temperature and provides good air circulation.
aOlmt (output High Limit): 0.00~110.00% of output High
Digital fine adjust:
aOzro: Settable range: -38011~+27524
1.0~8.0 mm
FIX HOLDER:
104 mm(L) / W M3
R
L1
RL
2
2
R
L
3
R
L
4
COM
C
I1
1
C
I
2
C
I
3
ENT/FN
?
?
?
Kg
PANEL CUT-OUT:
92+0.2(W) x 44+0.2(H) mm
aOspn: Settable range: -38011~+27524
RS 485 Communication(option)
Protocol:
Modbus RTU mode
Baud rate:
1200/2400/4800/9600/19200/38400 programmable
Data bits:
8 bits
Parity:
Even, odd or none (with 1 or 2 stop bit) programmable
Address:
1 ~ 255 programmable
Remote display:
to show the value from RS485 command of master
Distance:
1200M
CONNECTION DIAGRAM
Terminate resistor:
150Ωat last unit.
21
22
24
25
23
27
28
26
29
30
31
33
32
34
Relay 3
b
c
a
Relay 2
b
c
a
Relay 1
a
c
Relay 4
a
c
Analogue
output
A
B
RS 485
port
ECI1
ECI3
COM
ECI2
External Control Input
FG
1
2
4
5
3
6
7
8
9
10
11
12
14
15
13
Excit.
Supply
Terminal blocks:
10A/300Vac, M2.6,
M2.6, 1.3~2.0mm2
(16~22AWG)
AC 86~265V
DC 100~300V
DC 20~56V
AC230V
AUX. POWER
AC115V
ADH
ADL
mV/V
SIGNAL
INPUT
Electrical Safety
Dielectric strength:
AC 2.0 KV for 1 min, Between Power / Input / Output / Case
Insulation resistance:
≥100M ohm at 500Vdc, Between Power / Input / Output
Isolation:
Between Power / Input / Relay / Analogue / RS485 / E.C.I.
EMC:
EN 55011:2002; EN 61326:2003
Safety(LVD):
EN 61010-1:2001
Environmental
Operating temp.:
0~60 ˚C
Operating humidity:
20~95 %RH, Non-condensing
Temp. coefficient:
≤100 PPM/˚C
Storage temp.:
-10~70 ˚C
Enclosure:
Front panel: IEC 529 (IP52); Housing: IP20
Please check the voltage of power supplied first, and then connect to
the specified terminals. It is recommended that power supplied to the
meter be protected by a fuse or circuit breaker.
Mechanical
Dimensions:
96mm(W) x 48mm(H) x 120mm(D)
Panel cutout:
92mm(W) x 44mm(H)
Power Supply
AC115/230V
AC85~264V
Filter or Transformer
L
N
G
L
N
G
1A Fuse
7
9
10
8
Case material:
ABS fire-resistance (UL 94V-0)
Mounting:
Panel flush mounting
Terminal block:
Plastic NYLON 66 (UL 94V-0)
10A 300Vac, M2.6, 1.3~2.0mm2(16~22AWG)
Weight:
550g / 350g(Aux. Power Code: ADH or ADL)
Power
Power supply:
AC115/230V,50/60Hz;
Load Cell connection RS485 Communication Port
RS485 Port
4
5
6
A
B
Max. Distance: 1200M
Terminate Resistor
(at latest unit):
120~300ohm/0.25W
(typical: 150ohm)
11
12
14
15
13
10Vdc
Excit.S
mV Input
Output
Output
0VE.S.
+VE.S
.
Load
Cell
Optional: AC 85~264V, DC 100~300V, DC 20~56V
Excitation supply:
DC 5V/10V, 40mA maximum in standard
Power consumption:
5.0VA maximum
Back up memory:
By EEPROM
FRONT PANEL
R L1
RL2
2
RL3
RL4
COM
CI11
CI2
CI3
ENT/FN
?
?
?
Kg
Comm. status
Relay status
Indication
Operation Key
Control Input
status
Engineer Unit
Display screen
M.H
Max. Hold status
M.H
Mini. Hold status
CSM-321S
CS2-VA
CSM-321S
CSM-
321S
CSM-
321S
CS2-SG
CSM-321S
CSM-
321S
CSM-
321S
CSM-321S
CSM-
321S
CSM-321S

CS2-SG-2010-09-27
C2-03-4/11
FUNCTION DESCRIPTION
Other functions :
The meter is also support relative PV (∆PV) and PV hold
functions that set in [eci group]. Please refer to
explain of ECI functions.
Input & Scaling Functions
Input range:
Analogue input High and Low programmable
The meter has to be specified and fixed according to ordering code (ex.
0~2.0mV/V in factory. If the meter has to install in difference range of
input, the meter can be set in function aIlo and aIhi of input
group to meet the input signal.
For example: The meter is 0~2.0mV/V input, and the signal from sensor
is 0~1.5mV/V. Please get into [input group] to set aIhi (Analogue
input High) to be 75.00%(2.0mV/V x 75.00% = 1.5mV/V), then the meter
has been changed the input range to 0~1.5mV/V and the all relative
parameters will work base on 0~1.5mV/V. The meter doesn’t need
re-calibration after change the aIlo and aIhi .
Low cut:
Settable range from -19999~+99999 counts.
The users can set the value range.
1. If set the positive value (X1) here to display "0" which it
expressed to be low-cut the PV between "+X1 (plus)" &
"-X1(minus)" /absolute value
PV< l Setting value (X1) l, the display will be shown 0
EX: Low Cut is set for 0.50. If the display is from
-0.50~+0.50, that will be 0.
Low Cut set to be +0.50
Low Cut is set for 0.50, if the PV is
from -0.50~+0.50, that display will be 0.
PV according
to input signal
Present
Value
Low cut
function
0.50
-0.50
)50
[lOcut]
X1
X1
Default Input: aIlo: 0.00%, aIhi: 100.00%
lOsc: 0.00, hIsc: 150.00
Change to aIlo: 0.00%, aIhi: 75.00%
SCALE
INPUT
0.00
199.99
0V
2.0mV/V
1.0mV/V
100.00
0.00%
100.00%
50.00%
1.5mV/V
75.00%
150.00
*The setting maycourse display lower resolution. Please set lower resolution
when the input signal has been high compressed.
2. If set the negative value (X2) here to display "X2" which it
expressed to be low-cut the PV that it's under the X2 setting
value;
PV< Setting value(X2), the display will be shown X2.
EX: Low Cut is set for -0.01. If the display is < -0.01, and all
the display will be -0.01.
Scaling function:
Low Cut set to be -0.10
-0.10
Low cut
function
Low Cut is set for -0.10, if the PV is
under (< =-0.10), that display will be -0.10.
Present
Value
PV according
to input signal
-)10
[lOcut]
X2
Setting the [ lOsc](Low scale) and [ hIsc](High scale) in [input
group] to relative input signal. Reverse scaling will be done too.
Please refer to the figure as below,
Default: [lOsc]: )00, [hIsc]: 10)00
Change to [lOsc]: 5)00, [hIsc]: 19(99
SCALE
INPUT
)00
19(99
10)00
5)00
Reverse slop
[hIsc]
[hIsc]
[lOsc]
[lOsc]
%
)00
%
5)00
%
10)00
*Too narrow scale may course display lower resolution.
Digital fine adjust:
Settable range: -19999~+29999
Users can get Fine Adjustment for Zero & Span of PV by front key of the
meter, and “Just Key In” the value which user want to show in the
current input signals.
Especially, the [pVzro] & [pVspn] are not only in zero & span of PV, but
also any lower point for [pVzro] & higher point for [pVspn]. The meter
will be linearization for full scale.
The adjustment can be clear in function [ZSclr]
Default Input:[ lOsc]: )00, [ hIsc]: 19(99
Digital fine adjustment:
input 2.75mV, [pVzro]set to be 8)00
input 9.00mV, [pVspn]set to be 17)00
Display: Low point from 55.00 to 80.00
Highpointfrom180.00to 170.00
SCALE
INPUT
0V
10.0mV
5.0mV
2.75mV
9.00mV
19(99
[ hIsc ]
[ lOsc ]
)00
10)00
18)00
5%00
8)00
17)00
Excit. Pw.
10Vdc
Sensor
1.0mV/V
Display & Functions
Max / Mini recording:
The meter wills storage the maximum and minimum value in
[ user level] during power on in order to review drifting of PV.
Display functions:
PV / Max(Mini) Hold / RS 485 programmable in [dsply]
function of [input group]
(Please refer to step A-07)
Present Value pv:
The display will show the value that Relative to Input signal.
Maximum Hold maXhd / Minimum Hold miNhd :
The meter will keep display in maximum(minimum) value
during power on, until manual reset by front key in [User
level], rear terminal is close [External Control Input(ECI)]
or press front down or up key to reset (according to setting,
please refer to the function of the ECI Group)
Please find the
M.H
sticker that enclosure the package
of the meter to stick on the right side of square orange LED
Max. ( Mini.) Hold & Reset
Reset the Max
(Mini) Hold by
ECI or F. Key
O
N
Level
Trigger
Maximum Hold
Present
Value
Remote Display by RS485 command rs485 :
The meter will show the value that received from RS485
sending. In past, The meter normally receive 4~20mA or 0~10V
from AO or digital output from BCD module of PLC. We support
a new solution that PV shows the value from RS485 command
of master can so that can be save cost and wiring from PLC.
CS2-VA
CSM-321S
CSM-
321S
CSM-
321S
CS2- SG
CSM-321S
CSM-
321S
CSM-
321S
CSM-321S
CSM-
321S
CSM-321S

CS2-SG-2010-09-27
C2-03-5/11
Reading Stable Function
Hi / Lo / Go Relay Energized
Hi Setting
Hi Relay Energized
ON
Lo Setting
Lo Relay Energized
ON
ON
Go Relay Energized
ON
ON
Average display:
Jittery Display caused by the noise or unstable signal. User can set the times to average
the readings, and to get smoothly display.
The meter’s sampling is 15cycle/sec. If the [avg](Average) set to be 3 to
express the display update with 5 times/sec. The meter will calculate the sampling 1-3
and update the display value. At meantime, the sampling 4-6 will be processed to
calculate.
Average set to be 3
…….
Sample 1
Sample 2
Sample 3
Sample 4
Sample 5
Sample 6
…….
Display Update Value =
(Sample 1 + Sample 2 + Sample 3)/3
Display Update Value =
(Sample 4 + Sample 5 + Sample 6)/3
Remark: The higher average setting will cause the response time of
Relay and Analogue output slower.
Hi.HLd hIhld (Lo.HLd lOhld) :
The relay energized with latched function is for electrical
safety and human protection.
For example, a current meter relay installed for the over
current alarm of motor. Generally, over current of motor
caused by over load, mechanical dead lock, aging of insulation
and so on.
Above cases will alarm in the meter, if the user doesn't figure
out the real reason and re-start the motor. It may damage the
motor. The functions of Hi.HLd & Lo.HLd are designed must
be manual reset the alarm after checking out and solving the
issue. It's very important idea for electrical safety and human
protection.
As the PV Higher (or lower) than set-point, the relay will be
energized to latch except manual reset by from key in [ user
level]or [eci](ECI) set to be rYrst is closed.
Moving average:
Jittery Display caused by the reasons as like as noise or unstable signal. User can set
the times to average the readings, and get smoothly display.
The meter’s sampling is 15cycle/sec. If the [ Mavg](Moving Average) set to be 3
expressed the display update with 15 times/sec.,
In the first updated display value will be same as average function. In the next updated
display value, the function will get the new fourth sample (sample 4) then throw away the
first sample (sample 1) that the newest 3 samples(sample 2,3,4) will be calculated for the
updated display value.
Moving Average set tobe 3
Sample 1
Sample 2
Sample 3
Sample 4
Sample 5
Sample 6
…….
In first 3 samples, Display Update Value
= (Sample 1 + Sample 2 + Sample 3)/3
Display Update Value
= (Sample 2 + Sample 3 + Sample 4)/3
Display Update Value
= (Sample 3 + Sample 4 + Sample 5)/3
Display Update Value
= (Sample 4 + Sample 5 + Sample 6)/3
…….
Remark: The higher moving average setting wouldn’t cause the
response time of Relay and Analogue output slower after first 3
samples.
Hi(Lo) Energized Latch & Reset
Hi.HLd(High Hold)
Relay Energized
ON
Reset therelayHold
byECI or Front Key
ON
Level Trigger
Hi Setting
hIhld
[ry_.md]
rYrst
[ ecI_]
[ry_.sp]
DO function do:
The function has been designed not only a meter but also an
I/O interface. In the case of motor control cabinet can't get the
remote function. It's very easily to get the ON/OFF status of
switch from CS2 series with RS485 function.
If the [ry_.md]had been set do, the relay will be
energized by RS485 command directly, but no longer to
compare with set-point.
Digital Filter:
The digital filter can reduce the magnetic noise in field.
The digital filter can reduce the influence of spark noise caused by
magnetic of coil.
If the values of samples are over digital filter band (fix in firmware and about
5% of stable reading) 3 times (Digital Filter set to be 3) continuously, the
meter will admit the samples and update the new reading. Otherwise, it
will be as treat as a noise and skip the samples.
Start delay band and Start delay time:
The functions have Been designed for,
►To avoid starting current of inductive motor (6 times of rated current)
with alarm.
►If the ry_.md relay energized mode had been set to be lo(Lo) or
lOhld(Lo & latch). As the meter is power on and no input to display
the "0" caused the relay will be energized. User can set a band and
delay time to inhibit the energized of relay.
Control Functions(option)
Relayenergizedmode:
Hi / Lo / Go-1.2 / Go-2.3 / Hi.HLd / Lo.HLd / DO programmable
Hi hi(Fig.1-):
Relay will energize when PV > Set-Point
Lo lo(Fig.1-):
Relay will energize when PV < Set-Point
Hi / Lo Relay Energized
Fig.1
Hi Setting
Hi Relay Energized
ON
Lo Setting
Lo Relay Energized
ON
hi
lo
[ry_.sp]
[ry_.sp]
[ry_.md]
Start band rYsb (Fig.2-): Settable range from 0~9999 Counts
Start delay time rYsd (Fig.2-): Settable range from 0.0(s)~9(m)59.9(s);
Start Delay
Fig.2
Start Delay Time
Start Band
Hi Setting
Relay
Energized
ON
Inhibit
Inhibit
[ rYsb]
[ry_.sp]
[ rYsd]
Go-1.2 go-!2:
This function is programmable in Relay 4 only.
If the Relay 4 set to be Go function, the relay will compare
with [ry!sp] and [ry@sp].
Go relay energized when the condition is
[ry!sp](Hi) > PV > [ry@sp](Lo)
Hysteresis ry_.hy (Fig.3-): Settable range from 0~9999 Counts
As the display value is swing near by the set point to cause the relay on
and off frequently. The function is to avoid the relay on and off frequently
such as compressor…….etc.,
Go-2.3 go-@3:.
This function is programmable in Relay 4 only.
If the Relay 4 set to be Go function, the relay will compare
with [ry@sp] and [ry#sp].
Go relay energized when the condition is
[ry@sp](Hi) > PV > [ry#sp](Lo)
Relay energized delay ry_.rd (Fig.3-): Settable range from 0.0(s)~9(m)59.9(s);
The function is to avoid the miss action caused by noise. Sometime, the
display value will swing caused by spark of contactor…etc.. User can set
a period to delay the relay energized.
CSM-321S
CS2-VA
CSM-321S
CSM-
321S
CSM-
321S
CS2-SG
CSM-321S
CSM-
321S
CSM-
321S
CSM-321S
CSM-
321S
CSM-321S

CS2-SG-2010-09-27
C2-03-6/11
Relay de-energized delay ry_.fd (Fig.3-): Settable range from 0.0(s)~9(m)59.9(s);
Hi(Lo) Energized Latch & Reset
Hi.HLd(High Hold)
Relay Energized
ON
Reset therelayHold
byECI or Front Key
ON
Level Trigger
Hi Setting
hIhld
[ry_.md]
rYrst
[ ecI_]
[ry_.sp]
Energized / De-energized
Delay & Hysteresis
Fig.3
ON
Hysteresis
De-energized
delay time
Hi Setting
Relay
Energized
[ry_.sp]
[ry_.hy]
[ry_.rd]
[ry_.fd]
Energized delay time
Debouncing time:
The function is for avoiding noise signal to into the meter. And The basic
period is 8mseconds. It means you set the number that has to multiple 8
m-seconds.
For example: [debnc]set to be 5, it means 5 x 8mseconds = 40mseconds
External Control Inputs(ECI)
The three external control inputs are individually programmable to perform
specific meter control or display functions. All E.C.I. have been designed
in level trigger actions. Please pay attention, the ECI1 or ECI2 input will
be disable while UP or Down Key has been set to be “yes”.
Analogue output(option)
Please specify the output type either an 0~10V or 4(0) ~ 20mA in
ordering. The programmable output low and high scaling can be based
on various display values. Reverse slope output is possible by reversing
point positions.
Functions:
Relative PV / PV Hold / Reset Max or Mini. Hold / DI / Reset
for Relay Energized latch programmable.
Relative PV reLpv or Tare:
The [ ecI_]can be set to be reLpv function. When the
E.C.I. is closed, the reading will show the differential value.
Output range:
Voltage: 0~5V / 0~10V / 1~5V programmable
Current: 0~10mA / 0~20mA / 4~20mA programmable
Relative PV
Relative
PV(?PV) by
ECI or F.Key
ON
Level
Trigger
Present
Value
reLpv
[ecI_]
ECI_ has closed, and
then PV goes to “0”
ECI_ has opened,
and then display
shows PV
Relative PV
Functions:
Output High / Low scale, output limit, fine adjustment
Output range high [ aOhs]:
To setting the Display value High to versus output range
High(as like as 20mA in 4~20)
Output range low [ aOls]:
To setting the Display value Low to versus output range
Low(as like as 4mA in 4~20)
Set Scaling: [ lOsc]: 0.00, [ hIsc]: 199.99;
Output: [ aOls]: 50.00(Display Value Low),
[ aOhs]: 150.00(Display Value High)
0.00%
100.00%
50.00%
OUTPUT
199.99
100.00
0.00
50.00
150.00
SCALE
[ aOls]
[aOhs]
The range between [ aOhs]and [ aOls]should be over
20% of span at least; otherwise, it will be got less resolution of
analogue output.
PV Hold pVhld:
The [ ecI_]can be set to be pVhld(PV Hold) function.
The display will be hold when the E CI is closed, until the ECI
is to be open. Please refer to the below figures,
PV Hold & Reset
Present
Value
Reset PV Hold
by E.C.I. or
Front Key
O
N
Level
Trigger
ON
ON
PV Hold
pVhld
[ecI_]
Reset for Maximum or Minimum Hold Mrst:
When the [dsply] function in [input group] selected
maXhd or miNhd, the display will show Maximum or
Minimum value.
The [ ecI_] function can be set to be Mrst
function to reset the maximum and minimum value
in [User Level] by terminals of ECI (close). Please
refer to the figure as below.
Output High Limit [ aOlmt]:
0.00~110.00% of output High User can set the high limit of
output to avoid a damage of receiver or protection system.
Set Scaling: [ lOsc]: 0.00, [ hIsc]: 199.99;
Output: [ aOls]: 50.00(Display Value Low),
[ aOhs]: 150.00(Display Value High)
[aOlmt]: 80.00%( of Output Range)
0.00%
100.00%
50.00%
OUTPUT
199.99
100.00
0.00
50.00
150.00
SCALE
Ao.LMt: 80.00%
80.00%
[aOhs]
[ aOls]
[aOlmt]
Max. ( Mini.) Hold & Reset
Reset the maxstorage
whenECI has closed
Reset the Max.
(Mini.) storage
by E.C.I.
O
N
Level
Trigger
Maxi in User Level
Present
Value
Mrst
[ecI_]
Fine zero & span adjustment:
DI di :
The E.C.I can be set to be di function, when the meter
building in RS485 port. It is easier to get remote monitoring a
switch status through the meter as like as DI of PLC.
Users can get Fine Adjustment of analogue output by front key of the
meter. Please connect standard meter to the terminal of analogue
output. To press the front key(up or down key) of meter to adjust and
check the output.
Reset for Relay Energized Latch rYrst:
If the relay energized mode has been set to be
hIhld(Energized latch), and the [ecI_]can be set to be
rYrst(Reset the Relay energized latch). When the PV
meets the condition of relay energizing, the relay will be
energized and latch until the ECI is to be closed.
Zero adjust [aOzro]:
Fine Zero Adjustment for Analog Output;
Settable range: -38011~27524;
Span adjust [aOspn]:
Fine Span Adjustment for Analog Output;
Settable range: -38011~27524;
CSM-321S
CS2-VA
CSM-321S
CSM-
321S
CSM-
321S
CS2-SG
CSM-321S
CSM-
321S
CSM-
321S
CSM-321S
CSM-
321S
CSM-321S

CS2-SG-2010-09-27
C2-03-7/11
RS 485 communication(option)
Field Calibration
CS2 series supports Modbus RTU mode protocol to be used as Remote
Terminal Unit (RTU) for monitoring and controlling in a SCADA
(Supervisor Control And Data Acquisition) system. The baud rate can be
up to 38400 bps. It's not only can be read the measured value and DI
(external control inputs) status but also controls the relays output (DO)
by RS485 communication ports.
In pass time, engineers have take a lot of time to adjust meters or
converter to meet the structure of machinery zero and span for the Load
Cell measuring. Now, our CS2-SG support easier process to do it called
“Field Calibration”.
Please accord to the numbers to do the field calibration
()
R L1
RL2
2
RL3
RL4
COM
CI1
1
CI2
CI3
ENT/FN
?
?
?
Kg
2
caLlo
caLls
3
5
caLhi
caLhs
6
4
Calibration
Low
Calibration
High
1
2
3
4
5
6
1
CS2-SG & SC2-RL APPLICATION MEASURING & RS485 COMMUNICATION
RS 485 Modbus RTU Mode (up to 38400bps)
RS485 wiring 1.2KM maximum
Terminate Resistor:
Analog Output 0~10V/0(4)~20mA
3 External Control Inputs:
Functions: Relative PV / PV hold / Reset for
Max(Mini) / Reset for relay latch / DI
Application: Leakage test / Thermal Switch /
Circuit Breaker / Push Button / …
4 Relay outputs:
Functions: Hi(Lo) alarm / Hi(Lo)
energized hold / Go
function / DO function
RL1
RL2
RL3
RL4
COM
ECI1
ECI2
ECI3
ENT/FN
◄
▲
▼
Kg/cm2
RL1
RL2
RL3
RL4
COM
ECI1
ECI2
ECI3
ENT/FN
◄
▲
▼
Kg/cm2
High Speed Mode: Code: -HSM
According the scaling, the controller can be specify higher sampling rate
up to 60times/second(Average set to be 1). The relay trip, analogue
output will be quicker response according to update of Present Value.
Remote Display:
The meter will show the value that received from RS485 command. In
past, The meter normally receive 4~20mA or 0~10V from AO or digital
output from BCD module of PLC .We support a new solution that PV
shows the value from RS485 command of master so that can be save
cost and wiring from PLC.
Calibration
System calibration by front key. The process of calibration,
please refer to the operating manual
Optional Function
When the [ dsply] set to be RS485, it means, the PV screen will show the
number from RS485 command & data. The data(number) will be same as
PV that will compare with set-point, analogue output and ECI functions so
that is to control analogue output, relay energized and so on.
Customize function with quantities is welcome. Please contact with our
sales for detail. The appendix code of optional function will be added
behind the code of auxiliary power as like as xxx-A-HSM.
CS2 APPLICATION FOR REMOTE DISPLAY FROM RS485 COMMAND
RS 485 Modbus RTU Mode (up to 38400bps)
RS485 wiring 1.2KM maximum
Terminate Resistor:
RL 1
RL 2
RL3
RL4
COM
ECI1
ECI2
ECI3
ENT/FN
◄
▲
▼
Kg/cm2
RL 1
RL 2
RL3
RL4
COM
ECI1
ECI2
ECI3
ENT/FN
◄
▲
▼
Kg/cm2
ERROR MESSAGE
BEFORE POWER ON, PLEASE CHECK THE SPECIFICATION AND CONNECTION AGAIN.
SELF-DIAGNOSIS AND ERROR CODE:
DISPLAY
DESCRIPTION
REMARK
ovfl
Display is positive-overflow (Signal is over display range)
(Please check the input signal)
-ovfl
Display is negative-overflow (Signal is under display range)
(Please check the input signal)
ovfl
ADC is positive-overflow (Signal is higher than input range
high 20%)
(Please check the input signal)
-ovfl
ADC is negative-overflow (Signal is lower than input range low
-20%)
(Please check the input signal)
eep
fail
EEPROM occurs error
(Please send back to manufactory for repaired)
aiCng
pv
Calibrating Input Signal do not process
(Please process Calibrating Input Signal)
aic
fail
Calibrating Input Signal error
(Please check Calibrating Input Signal)
aoCng
pv
Calibrating Output Signal do not process
(Please process Calibrating Output Signal)
aoc
fail
Calibrating Output Signal error
(Please check Calibrating Output Signal)
CSM-321S
CS2-VA
CSM-321S
CSM-
321S
CSM-
321S
CS2-SG
CSM-321S
CSM-
321S
CSM-
321S
CSM-321S
CSM-
321S
CSM-321S

CS2-SG-2010-09-27
C2-03-8/11
FRONT PANEL:
R L1
RL2
2
RL3
RL4
COM
CI11
CI2
CI3
ENT/FN
?
?
?
Kg
Comm. status
Relay status
Indication
Operation Key
Control Input
status
Engineer Unit
Display screen
M.H
Max. Hold status
M.H
Mini. Hold status
Numeric Screens
0.8”(20.0mm) red high-brightness LED for 4 2/3 or 5 digital present
value.
I/O Status Indication
●Relay Energized: 4 square red LED
RL1
display when Relay 1 energized;
RL2
display when Relay 2 energized;
RL3
display when Relay 3 energized;
RL4
display when Relay 4 energized;
●External Control Input Energized: 3 square green LED
ECI1
display when E.C.I. 1 close(dry contact)
ECI2
display when E.C.I. 2 close(dry contact)
ECI3
display when E.C.I. 3 close(dry contact)
●RS485 Communication: 1 square orange LED
COM
will flash when the meter is receive or send data, and
COM
flash
quickly means the data transient quicker.
●Max/Mini Hold indication: 2 square orange LEDs
CO
M.H
displayed: When the display function has been selected in
Maximum or Minimum Hold function.
Stickers:
Each meter has a sticker what are functions and engineer label
enclosure.
●Relay energized mode:
H H
H i
L o
L L
D O
●E.C.I. functions mode:
PV.H(PV Hold) /
Tare /
DI(Digital Input)
M.RS(Maximum or Minimum Reset) /
R.RS(Reset for Relay Latch)
●Engineer Label: over 80 types.
Operating Key: 4 keys for
Enter(Function) /
Shift(Escape) /
Up key /
Down key
Setting Status
Function Index
Up key
Increase number
Go back to previous
function index
Down key
Decrease number
Go to next
function index
Shift key
Shift the setting
position
Go back to this function
index, and abort the setting
Enter/Fun
key
Setting Confirmed
and save to EEProm
From the function index to
get into setting status
Pass Word Pcode: Settable range: 0000~9999;
User has to key in the right pass word so that get into【Programming
Level】. Otherwise, the meter will go back to measuring page. If user
forgets the password, please contact with the service window.
Function Lock: There are 4 levels programmable.
●None none: no lock all.
●User Level user: User Level lock. User can get into
User Level for checking but setting.
●Programming Level eng: Programming level lock.
User can get into programming level for checking but setting.
●ALL all: All lock. User can get into all level for checking but
setting.
Front Key Function
●The
Key can be set to be the same function as the setting of ECI1.
Ex. The ECI1 set to be pVhld and the function [E1=up]set to be
yes in [eci group]. When user presses
Key, the PV will hold
as like as ECI1 close.
●The
Key can be set to be the same function as the setting of ECI2.
Ex. The ECI2 set to be reLpv and the function [E2=dn]set to be
yes in [eci group]. When user presses
Key, the PV will show
relative value as like as ECI2 close.
If the front key function has been set, the terminal input for ECI
will be disabling.
CSM-321S
CS2-VA
CSM-321S
CSM-
321S
CSM-
321S
CS2-SG
CSM-321S
CSM-
321S
CSM-
321S
CSM-321S
CSM-
321S
CSM-321S

CS2-SG-2010-09-27
C2-03-9/11
OPERATING DIAGRAM (The detail description of operation, please refer to operating manual.)
Power ON
*****
Self-diagnosis
0−0−1
299(9
pv
If the [dsply]
function has
been set rs485
pv: Present
Value
0−4
10000
ry$sp
ry$sp: Relay 4
Set-point
-19999~29999
/99999
0−8
no
Mrst
Mrst: Reset the
saved value of
Maximum &
Minimum
yes / no
cs@sg
Show the model
number
0−1
10000
ry!sp
ry!sp: Relay 1
Set-point
-19999~29999
/99999
0−5
no
rYrst
rYrst: Reset
for energized
Latch of Relay
yes / no
0−9
ver!4
cs@sg
model number
firmware
version
Checking only
ver!4
Show
the firmware
version
0−2
10000
ry@sp
ry@sp: Relay 2
Set-point
-19999~29999
/99999
0−6
)0000
min
min: the
Minimum value
of PV saving
Checking only
0−0−1
299(9
pv
Cyclic to first
page
299(9
ENT
MEASURING
PAGE
Press
1sec
Press
1sec
0−3
10000
ry#sp
ry#sp: Relay 3
Set-point
-19999~29999
/99999
0−7
29999
max
max: the
Maximum value
of PV saving
Checking only
enter
Pcode
ENT
Enter the
password to
access Engineer
Level
YES
PassCode
NO
Default:1000
input
group
ENT
INPUT
GROUP
▲
▼
▼
relay
group
ENT
RELAY
GROUP
▲
▼
▼
eci
group
ENT
EXTERNAL
CONTROL
INPUT (E.C.I)
GROUP
▲
▼
▼
ao
group
ENT
ANALOGUE
OUTPUT
GROUP
▲
▼
▼
A−1
)00
aIlo
aIlo: Analogue
input low
0.00~100.00%
B−1
0
rYsb
rYsb: Start band
for Relay
energized
0~9999counts
C−1
reLpv
ecI1
ecI1: External
Control Input 1
none / reLpv /
pVhld / Mrst /
rYrst / di
D−1
A4-20
aOtyp
aOtyp: Analogue
Output type
selection
V0-10 / V 0-5 /
V 1-5 / A0-10 /
A0-20 / A4-20
A−2
10)00
aIhi
aIhi: Analogue
input High
0.00~100.00%
B−2
)0)0
rYsd
rYsd: Start delay
time for Relay
energized
0.00.0~
9(M).59.9(S)
C−2
pVhld
ecI2
ecI2: External
Control Input 2
none / reLpv /
pVhld / Mrst /
rYrst / di
D−2
)0
aOls
aOls: Analogue
Low Output
versus Low
Scale
-19999~29999
/99999
A−3
0
pVdp
pVdp: Decimal
Point
0 / )0 /
)00 / )000 /
)0000
B−3
hi
ry!md
ry!md: Relay 1
energized mode
off / lo /
hi / lOhld /
hIhld / do
C−3
Mrst
ecI3
ecI3: External
Control Input 3
none / reLpv /
pVhld / Mrst /
rYrst / di
D−3
100)0
aOhs
aOhs: Analogue
High Output
versus High
Scale
-19999~29999
/99999
A−4
0
lOsc
lOsc: Low scale
of PV
-19999~29999
/99999
B−4
0
ry!hy
ry!hy: Relay 1
Hysteresis
0~5000 counts
C−4
12
debnc
debnc:
Debouching of
external control
Input
5~255(x8ms)
D−4
0
aOzro
aOzro: Fine Zero
Adjustment for
Analogue Low
Output
-38011~27524
A−5
10000
hIsc
hIsc: High
scale of PV
-19999~29999
/99999
B−5
)0)0
ry!rd
ry!rd: Relay 1
energized delay
time
0.00.0~
9(M).59.9(S)
C−5
no
E1=up
E1=up: ECI.1 set
to be UP Key
function
yes / no
D−5
0
aOspn
aOspn: Fine
Span Adjust. for
Analogue High
Output
-38011~27524
A−6
0
pVzro
pVzro: Fine Low
point
Adjustment for
PV display
-19999~29999
/99999
B−6
)0)0
ry!fd
ry!fd: Relay 1
de-energized
delay time
0.00.0~
9(M).59.9(S)
C−6
no
E2=dn
E2=dn: ECI.2 set
to be Down Key
function
yes / no
D−6
none
ZSclr
ZSclr: Zero &
Span Clear for
Adjustment
none / aOzro /
aOspn / both
Next Page
Next Page
Next Page
CSM-321S
CS2-VA
CSM-321S
CSM-
321S
CSM-
321S
CS2-SG
CSM-321S
CSM-
321S
CSM-
321S
CSM-321S
CSM-
321S
CSM-321S
User Level(5Digi-Display Max range:99999 )
Press
for 1 sec. can back to Measuring
Programming Level(5Digi-Display Max range:99999 )
Press
for 1 sec. can back to Measuring
▼
▲

CS2-SG-2010-09-27
C2-03-10/11
A−7
0
pVspn
pVspn: Fine
High point
Adjustment for
PV display
-19999~29999
/99999
B−7
hi
ry@md
ry@md: Relay 2
energized mode
off / lo /
hi / lOhld /
hIhld / do
D−7
11)00
aOlnt
aOlmt: Analog
Output High
Limit
0.00~110.00%
A−8
none
ZSclr
ZSclr: Clear
Fine Zero &
Span
Adjustment for
PV display
none / pVzro /
pVspn / both
B−8
0
ry@hy
ry@hy: Relay 2
Hysteresis
0~5000 counts
A−9
pv
dsply
dsply: Display
Function
pv / miNhd /
maXhd / rs485
B−9
)0)0
ry@rd
ry@rd: Relay 2
energized delay
time
0.00.0~
9(M).59.9(S)
A−10
0
lOcut
lOcut: Low Cut
Function
-19999~29999
B−10
)0)0
ry@fd
ry@fd: Relay 2
de-energized
delay time
0.00.0~
9(M).59.9(S)
rs485
group
ENT
RS485
GROUP
A−11
5
avg
avg: Average
update for PV
1(None)~
99 times
B−11
hi
ry#md
ry#md: Relay 3
energized mode
off / lo /
hi / lOhld /
hIhld / do
E−1
1
adres
adres: Device
number of the
meter
1~255
A−12
1
Mavg
Mavg: Moving
Average
update for PV
1(None)~
10 times
B−12
0
ry#hy
ry#hy: Relay 3
Hysteresis
0~5000 counts
E−2
9600
baud
baud: Baud
rate
1200 / 2400 /
4800 / 9600 /
19200 / 38400
A−13
0
Dfilt
Dfilt: Digital
filter
0(None)/1~
99 times
B−13
)0)0
ry#rd
ry#rd: Relay 3
energized delay
time
0.00.0~
9(M).59.9(S)
E−3
NstB2
prity
prity: Parity
NstB1 / NstB2 /
odd / even
A−14
0
Pcode
Pcode: Pass
Code for enter
Engineer Level
0000~9999
B−14
)0)0
ry#fd
ry#fd: Relay 3
de-energized
delay time
0.00.0~
9(M).59.9(S)
A−15
none
Flock
Flock: Function
Level Lock
none / user /
eng / all
B−15
hi
ry$md
ry$md: Relay 4
energized mode
off / lo /
hi / lOhld /
hIhld / do /
go-!2 / go-@3
B−16
0
ry$hy
ry$hy: Relay 4
Hysteresis
0~5000 counts
B−17
)0)0
ry$rd
ry$rd: Relay 4
energized delay
time
0.00.0~
9(M).59.9(S)
B−18
)0)0
ry$fd
ry$fd: Relay 4
de-energized
delay time
0.00.0~
9(M).59.9(S)
Plesae refer to operating manual for detail description
CSM-321S
CS2-VA
CSM-321S
CSM-
321S
CSM-
321S
CS2-SG
CSM-321S
CSM-
321S
CSM-
321S
CSM-321S
CSM-
321S
CSM-321S

CS2-SG-2010-09-27
C2-03-11/11
FIELD CALIBRATION
16*88
MEASURING
PAGE
Pcode
enter
&
Enter the
password to
access
Programming
Level
◘Once the user select field calibration, the [lOsc](step A-2)
and [hIsc](A-3) will be instead of [caLls] and [caLhs], and
can not to be change. If user has to change the scaling, it's
the only way to access field calibration level to set in
[caLls](step F-2) and [caLhs](step F-4).
◘Please double check the [lOsc](step A-2) and [hIsc](A-3) are
correct after selection the deflt or field
enter
Fcode
Enter the
password to
access Field
Calibration Level
Pass Code
default=2000
Press
F−1
caLlo
00000
Adjust the structure to be a lower signal output
status (or any lower status) and keep it in stable.
caLlo: Field Calibration Low
Press
to read signal of the lower status.
Press
again to finish the calibration lower point,
and go to next page.
F−2
caLls
00000
caLls: the value to be set is relative to Field
Calibration lower point
Press
to set the value of lower scale
F−3
caLhi
00000
Adjust the structure to be a higher signal output
status (or any higher status) and keep it in stable.
caLhi: Field Calibration High
Press
to read signal of the higher status
Press
again to finish the calibration higher point,
and go to next page.
F−4
caLhs
00000
caLhs: the value to be set is relative to Field
Calibration higher point
Press
to set the value of Higher scale
F−5
Csel
deflt
Csel: Calibration parameter selection
Press
to access the function and stand by
selection
Press
or
to select
(default: defld);
Settable: defld / field
defld (default calibration) field (Field calibration)
CSM-321S
CS2-VA
CSM-321S
CSM-
321S
CSM-
321S
CS2-SG
CSM-321S
CSM-
321S
CSM-
321S
CSM-321S
CSM-
321S
CSM-321S
NO
YES
Other manuals for CS2-SG
1
Table of contents
Other ADTEK Measuring Instrument manuals
Popular Measuring Instrument manuals by other brands
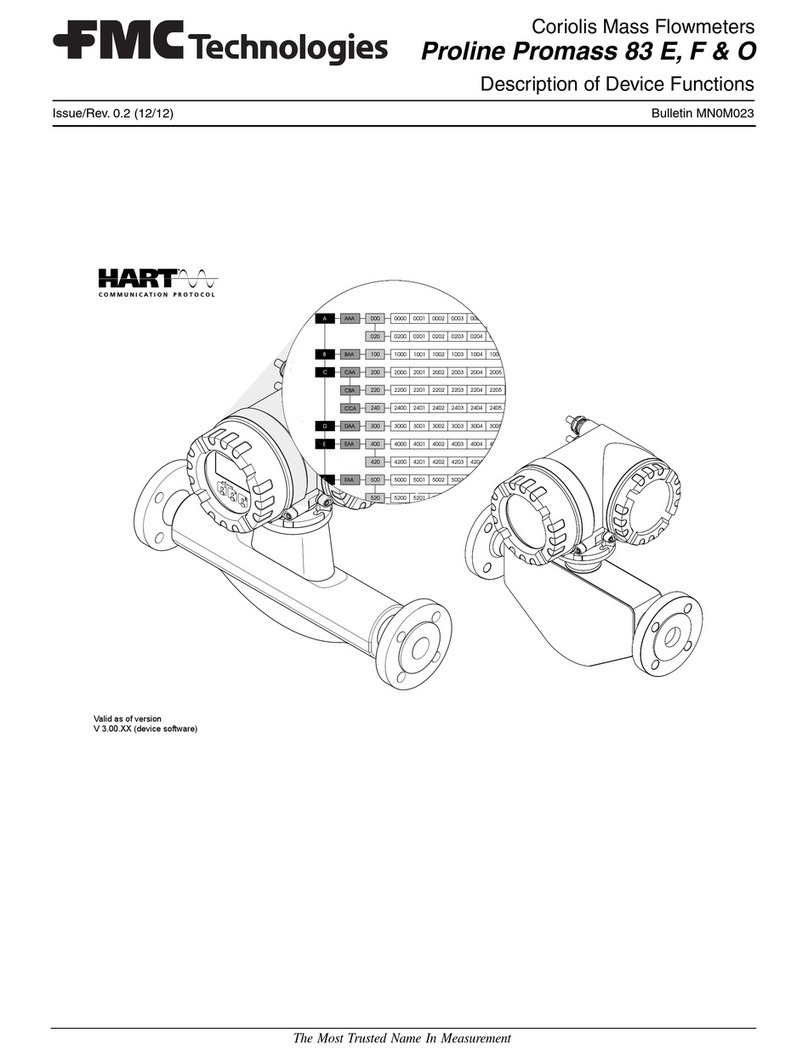
FMC Technologies
FMC Technologies Proline Promass 83 E Description of Device Functions
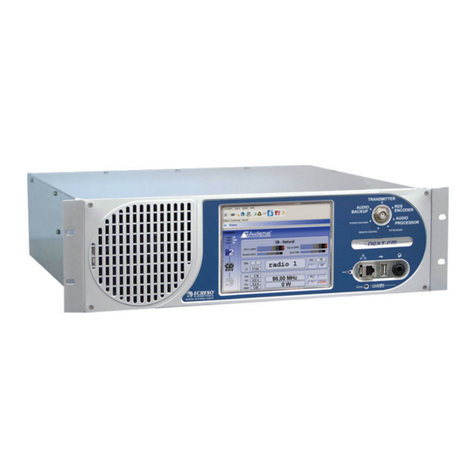
Worldcast Systems
Worldcast Systems ecreso NEXT FM user manual

Sper scientific
Sper scientific 300033 instruction manual

horiba
horiba LAQUA-PC1100 instruction manual
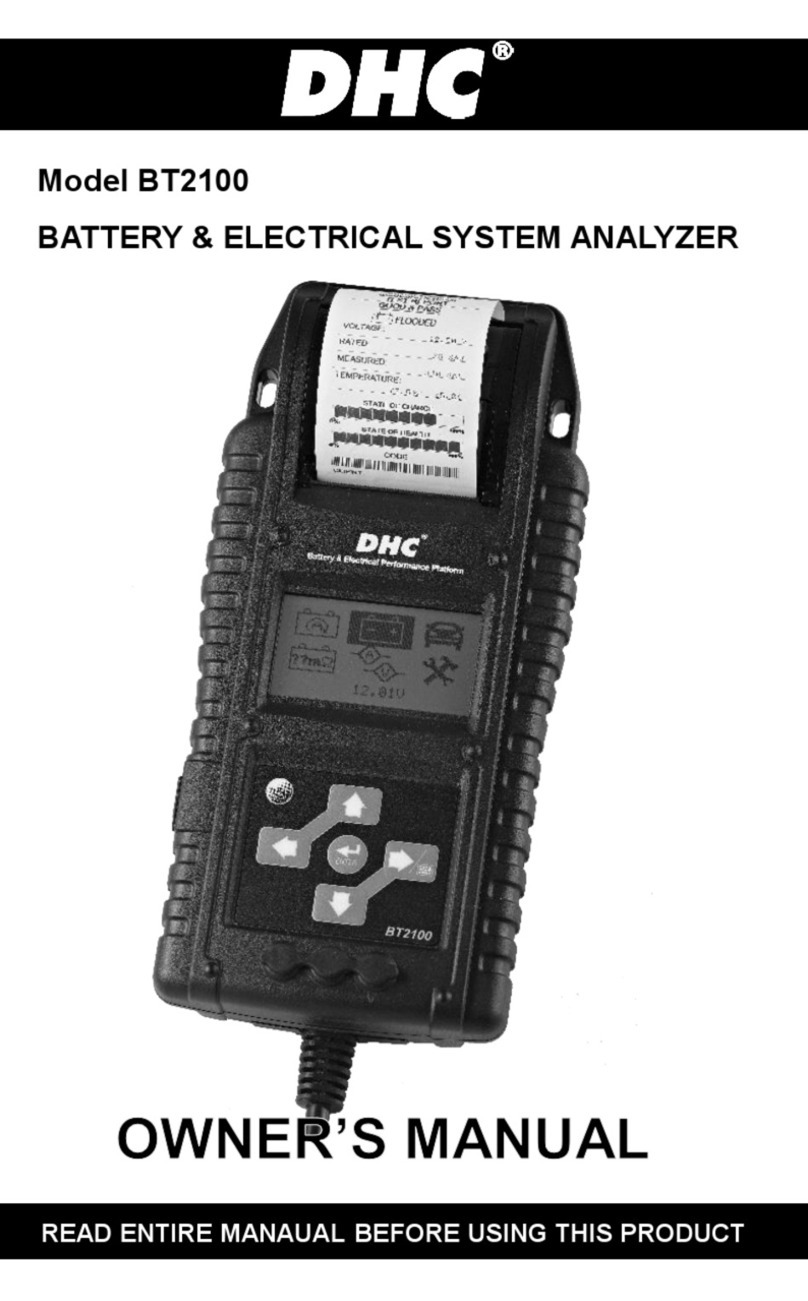
DHC
DHC BT2100 owner's manual

Konica Minolta
Konica Minolta CIVI-36clG instruction manual
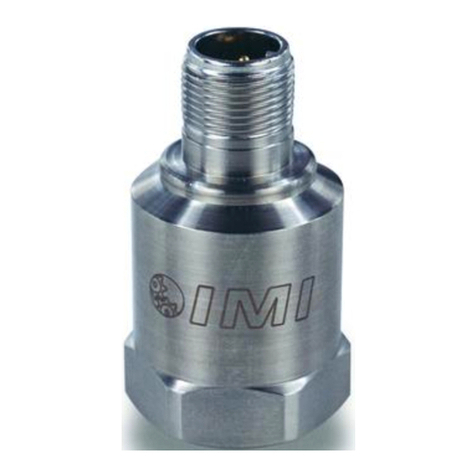
PCB Piezotronics
PCB Piezotronics IMI SENSORS M626B02 Installation and operating manual
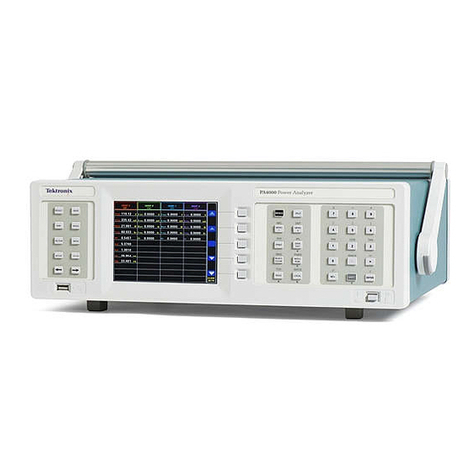
Tektronix
Tektronix PA4000 Series instructions
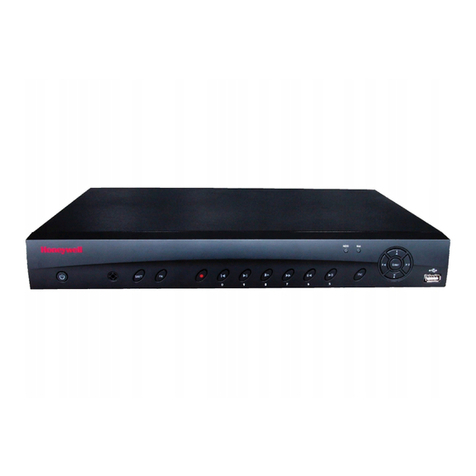
Honeywell
Honeywell HEN04112 user guide
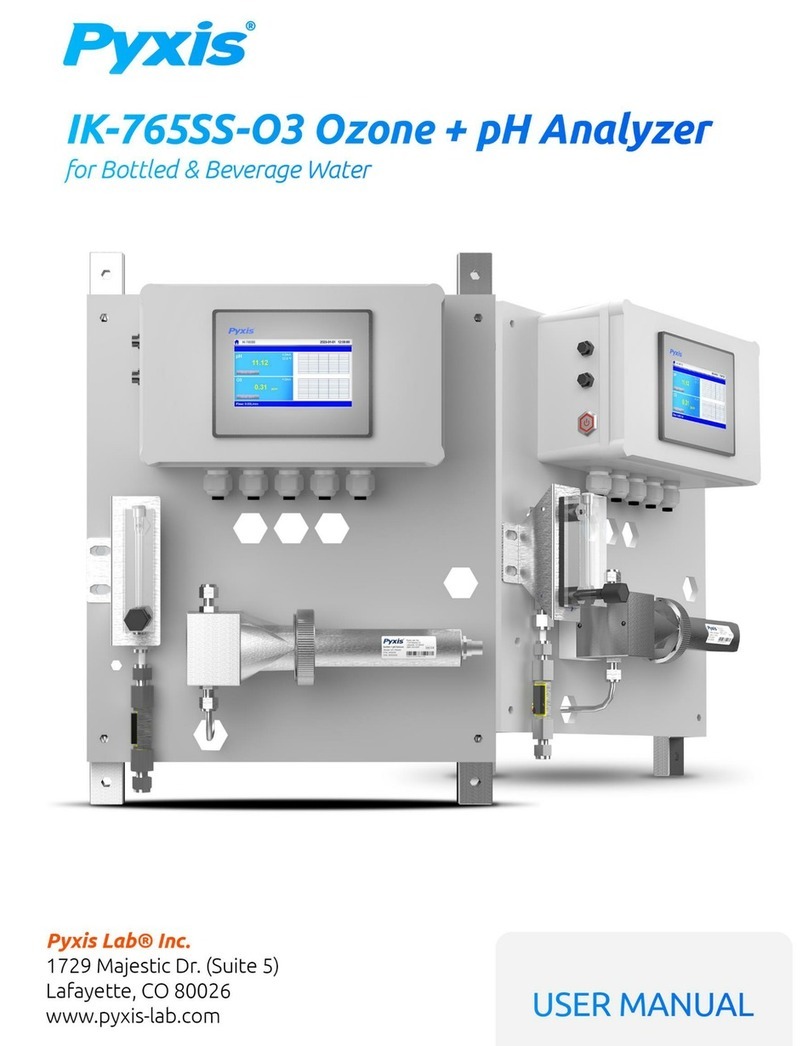
Pyxis
Pyxis IK-765SS-O3 user manual
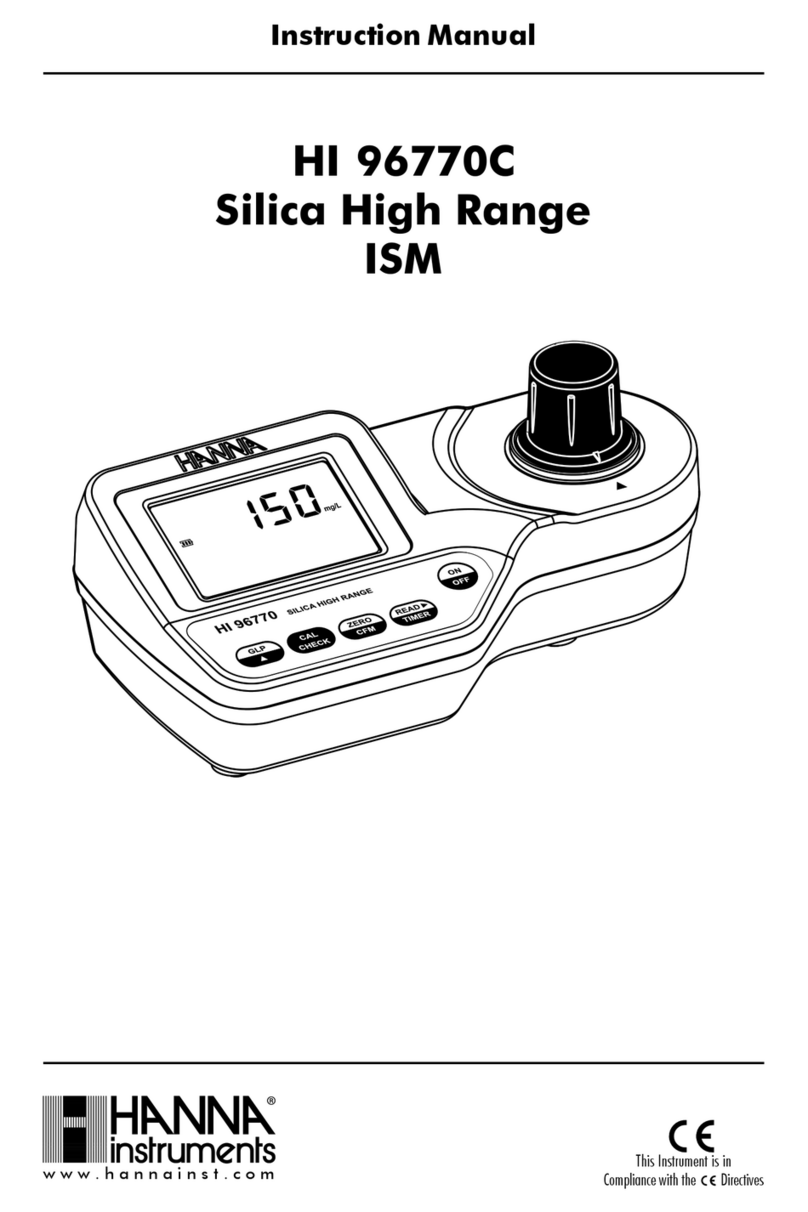
Hanna Instruments
Hanna Instruments HI 96770C instruction manual
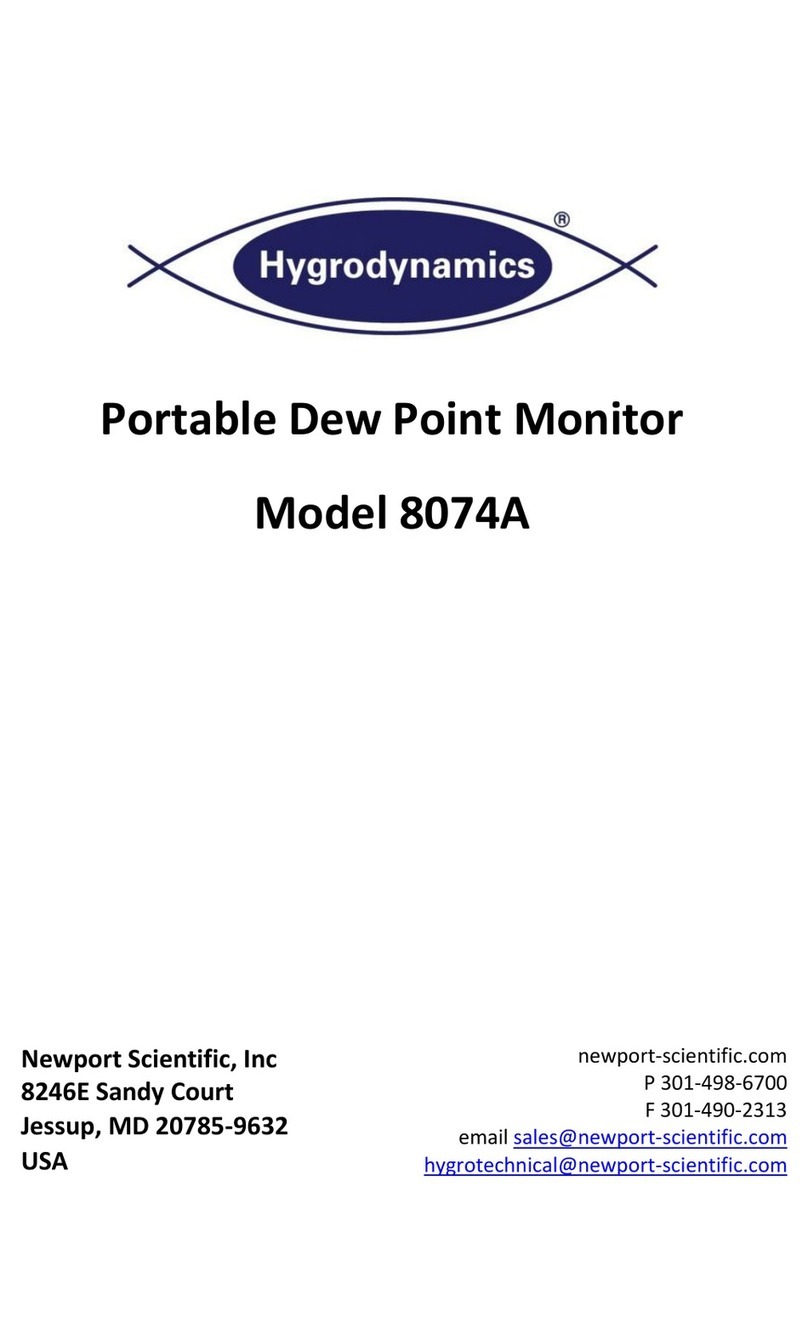
Newport
Newport Hygrodynamics 8074A manual