GEM R470 Tugela User manual

GEMÜ R470 Tugela
Double eccentric butterfly valve with bare shaft
Operating instructions
EN
further information
webcode: GW-R470

All rights including copyrights or industrial property rights are expressly reserved.
Keep the document for future reference.
© GEMÜ Gebr. Müller Apparatebau GmbH & Co. KG
23.08.2021
www.gemu-group.com2 / 30GEMÜ R470 Tugela

Contents
1 General information ............................................. 4
1.1 Information .................................................... 4
1.2 Symbols used ................................................ 4
1.3 Definition of terms ........................................ 4
1.4 Warning notes ............................................... 4
2 Safety information ............................................... 5
3 Product description ............................................. 5
3.1 Construction .................................................. 5
3.2 Additional design features ............................ 6
3.3 Description ..................................................... 7
3.4 Function ......................................................... 7
3.5 Product label ................................................. 7
4 GEMÜ CONEXO .................................................... 7
5 Correct use .......................................................... 8
5.1 Product without special function X .............. 8
5.2 Product with special function X ................... 8
6 Order data ........................................................... 9
6.1 Order codes ................................................... 9
6.2 Order example ............................................... 10
7 Technical data ..................................................... 11
7.1 Medium .......................................................... 11
7.2 Temperature .................................................. 11
7.3 Pressure ......................................................... 11
7.4 Product conformity ....................................... 12
7.5 Mechanical data ............................................ 13
8 Dimensions .......................................................... 15
8.1 Actuator flange .............................................. 15
8.2 Body ............................................................... 17
9 Manufacturer's information .................................. 19
9.1 Delivery .......................................................... 19
9.2 Transport ....................................................... 19
9.3 Storage ........................................................... 19
10 Installation in piping ............................................ 19
10.1 Preparing for installation .............................. 19
10.2 Installation location ....................................... 20
10.3 Installation of the standard version ............. 21
10.4 Installation of the ATEX version ................... 21
11 Commissioning .................................................... 22
12 Operation ............................................................. 22
13 Troubleshooting .................................................. 23
14 Inspection and maintenance ................................ 24
14.1 Cleaning the product ..................................... 24
14.2 ATEX version ................................................. 24
14.3 Removing the butterfly valve from the pip-
ing ................................................................... 24
15 Spare parts .......................................................... 25
15.1 Ordering spare parts ..................................... 25
15.2 Overview of spare parts ................................ 26
15.3 Replacement of spare parts ......................... 26
16 Removal from piping ............................................ 26
17 Disposal .............................................................. 26
18 Returns ................................................................ 27
19 Declaration of Incorporation according to
2006/42/EC (Machinery Directive) ....................... 28
20 Declaration of conformity according to 2014/68/
EU (Pressure Equipment Directive) ...................... 29
GEMÜ R470 Tugelawww.gemu-group.com 3 / 30

www.gemu-group.com4 / 30GEMÜ R470 Tugela
1 General information
1 General information
1.1 Information
•The descriptions and instructions apply to the standard ver-
sions. For special versions not described in this document
the basic information contained herein applies in combina-
tion with any additional special documentation.
•Correct installation, operation, maintenance and repair work
ensure faultless operation of the product.
•Should there be any doubts or misunderstandings, the Ger-
man version is the authoritative document.
•Contact us at the address on the last page for staff training
information.
•A supplement to Directive 2014/34/EU (ATEX Directive) is
included with the product, provided that it was ordered in
accordance with ATEX.
1.2 Symbols used
The following symbols are used in this document:
Symbol Meaning
Tasks to be performed
Response(s) to tasks
– Lists
1.3 Definition of terms
Working medium
The medium that flows through the GEMÜ product.
Control function
The possible actuation functions of the GEMÜ product.
Control medium
The medium whose increasing or decreasing pressure causes
the GEMÜ product to be actuated and operated.
1.4 Warning notes
Wherever possible, warning notes are organised according to
the following scheme:
SIGNAL WORD
Type and source of the danger
Possible
symbol for the
specific
danger
Possible consequences of non-observance.
Measures for avoiding danger.
Warning notes are always marked with a signal word and
sometimes also with a symbol for the specific danger.
The following signal words and danger levels are used:
DANGER
Imminent danger!
▶Non-observance can cause death or
severe injury.
WARNING
Potentially dangerous situation!
▶Non-observance can cause death or
severe injury.
CAUTION
Potentially dangerous situation!
▶Non-observance can cause moderate
to light injury.
NOTICE
Potentially dangerous situation!
▶Non-observance can cause damage to
property.
The following symbols for the specific dangers can be used
within a warning note:
Symbol Meaning
Danger of explosion!
Moving components.
Corrosive chemicals!
GEMÜ products without an operator!
Hot plant components!
Use as end-of-line valve!
Risk of crushing!

www.gemu-group.com 5 / 30 GEMÜ R470 Tugela
2 Safety information
The safety information in this document refers only to an indi-
vidual product. Potentially dangerous conditions can arise in
combination with other plant components, which need to be
considered on the basis of a risk analysis. The operator is re-
sponsible for the production of the risk analysis and for com-
pliance with the resulting precautionary measures and re-
gional safety regulations.
The document contains fundamental safety information that
must be observed during commissioning, operation and main-
tenance. Non-compliance with these instructions may cause:
•Personal hazard due to electrical, mechanical and chemical
effects.
•Hazard to nearby equipment.
•Failure of important functions.
•Hazard to the environment due to the leakage of dangerous
materials.
The safety information does not take into account:
•Unexpected incidents and events, which may occur during
installation, operation and maintenance.
•Local safety regulations which must be adhered to by the
operator and by any additional installation personnel.
Prior to commissioning:
1. Transport and store the product correctly.
2. Do not paint the bolts and plastic parts of the product.
3. Carry out installation and commissioning using trained
personnel.
4. Provide adequate training for installation and operating
personnel.
5. Ensure that the contents of the document have been fully
understood by the responsible personnel.
6. Define the areas of responsibility.
7. Observe the safety data sheets.
8. Observe the safety regulations for the media used.
During operation:
9. Keep this document available at the place of use.
10. Observe the safety information.
11. Operate the product in accordance with this document.
12. Operate the product in accordance with the specifications.
13. Maintain the product correctly.
14. Do not carry out any maintenance work and repairs not de-
scribed in this document without consulting the manufac-
turer first.
In cases of uncertainty:
15. Consult the nearest GEMÜ sales office.
3 Product description
3.1 Construction
C
2
3
4
5
6
7
8
9
10
11
12
13
15
14
16
17
18
19
20
21
22
1
Item Designation Material
1 Shaft see order code (order
data)
2 Hexagon screw Stainless steel
3 Packing washer 1.4408
4 Upper packing PTFE
5 Medium packing PTFE
6 Lower packing PTFE
7 Packing washer PTFE
8 Carbon bushing Carbon
9 Body see order code (order
data)
10 Spring washer Stainless steel
11 Hexagon nut Stainless steel
12 Shaft bearing PTFE coated steel
13 Shaft bearing PTFE coated steel
14 Static spring Stainless steel
15 Sealing washer Stainless steel
16 Lower cap same as body
17 Hexagon screw Stainless steel
18 Disc pin Steel
19 Disc see order code (order
data)
20* Seat see order code (order
data)
21 Seat retainer
22 Hexagon screw Stainless steel
3 Product description

www.gemu-group.com6 / 30GEMÜ R470 Tugela
3 Product description
Item Designation Material
C CONEXO label with RFID
chip
* available as spare part
3.2 Additional design features
Double-eccentric design
e
f
Shaft axis
Flow central line
Trace of the disc
During operation, the disc directly disconnects from the seat,
thereby reducing friction between the seat and disc, as well as
the torque.
This design is particularly low-wear and this, together with the
temperature-resistant carbon bushing, increases the service
life.
Spherical surface
The disc is designed with a spherical surface for improved
mechanical behaviour under pressure and temperature fluctu-
ations.
Shaft blow-out protection
There is a chamfer at the upper end of the shaft which acts as
an additional safety measure in case the shaft breaks.
Flow direction
Flow direction
Shut-off seal material
TFM™ is made from conventional PTFE and a 1% proportion
of perfluoropropyl vinyl ether (PPVE). While the properties of
conventional PTFE (excellent chemical resistance, application
in a wide temperature range and resistance to embrittlement
or ageing, etc.) are maintained, the PPVE additive leads to a
better distribution of the PTFE particles and thus to a higher
density of the polymer structure.
This leads to the following additional advantages:
• Significantly improved cold flow properties (measured as de-
formation under load):
The same cold flow properties as PTFE with 25% glass fibres.
• Reduced gas permeability and increased blocking properties
• The smooth surface results in less abrasion of the shut-off
seal and fewer abraded particles in the medium.

www.gemu-group.com 7 / 30 GEMÜ R470 Tugela
3.3 Description
The GEMÜ R470 double eccentric metal Tugela butterfly valve
has a bare shaft with a top flange, in accordance with EN ISO
5211. The butterfly valve is available in nominal sizes DN50
to 600 and in standardized installation lengths API 609 cat-
egory A (DIN 3202 K1).
3.4 Function
The product controls a flowing medium after a manual, pneu-
matic or motorized actuator has been mounted.
3.5 Product label
The product label is located on the valve body. Product label
data (example):
Design in accordance with order data
Device-specific data
Year of manufacture
Item number
The month of manufacture is encoded in the traceability num-
ber and can be obtained from GEMÜ. The product was manu-
factured in Germany.
The operating pressure stated on the product label applies to
a media temperature of 20 °C. The product can be used up to
the maximum stated media temperature. You can find the
pressure/temperature correlation in the technical data.
4 GEMÜ CONEXO
The interaction of valve components that are equipped with
RFID chips and an associated IT infrastructure actively in-
crease process reliability.
Thanks to serialization, every valve and every relevant valve
component such as the body, actuator or diaphragm, and
even automation components, can be clearly traced and read
using the CONEXO pen RFID reader. The CONEXO app, which
can be installed on mobile devices, not only facilitates and im-
proves the "installation qualification" process, but also makes
the maintenance process much more transparent and easier
to document. The app actively guides the maintenance techni-
cian through the maintenance schedule and directly provides
him with all the information assigned to the valve, such as
test reports, testing documentation and maintenance histor-
ies. The CONEXO portal acts as a central element, helping to
collect, manage and process all data.
For further information on GEMÜ CONEXO please visit:
www.gemu-group.com/conexo
4 GEMÜ CONEXO

www.gemu-group.com8 / 30GEMÜ R470 Tugela
5 Correct use
5 Correct use
DANGER
Danger of explosion!
▶Risk of severe injury or death.
●Do not use the product in potentially
explosive zones.
●Only use the product in potentially ex-
plosive zones confirmed in the declara-
tion of conformity.
WARNING
Improper use of the product
▶Risk of severe injury or death.
▶Manufacturer liability and guarantee will be void.
●Only use the product in accordance with the operating
conditions specified in the contract documentation and in
this document.
The product is designed for installation in piping systems and
for controlling a working medium.
●Use the product in accordance with the technical data.
5.1 Product without special function X
The product is not intended for use in potentially explosive
areas.
5.2 Product with special function X
With the special version X order option, the product is inten-
ded for use in potentially explosive areas in zone 1 with gases,
mists or vapours and zone 21 with combustible dusts in ac-
cordance with EU Directive 2014/34/EU (ATEX).
The product has the following explosion protection marking:
Gas: II -/2 G Ex h -/IIB T6 …T3 -/Gb X
Dust: II -/2 D Ex h -/IIIC T150°C -/Db X
The product has been developed in compliance with the fol-
lowing harmonized standards:
•EN 1127-1:2011
•ISO 80079-36:2016
•ISO 80079-37:2016
The product can be used in the following ambient temperat-
ure ranges: -20 °C…+70 °C
For use in potentially explosive areas, the following special
conditions or operation limits must be observed:
Index X is applied to the ATEX marking.
The following special conditions must be complied with:
•Temperature class depending on the temperature of the
conveyed medium and the clock frequency
•Not permissible as an end-of-line valve

6 Order data
Other configurations available on request. Please check the availability with GEMÜ before ordering.
Order codes
1 Type Code
Butterfly valve, bare shaft
(double-eccentric), Tugela
R470
2 DN Code
DN 50 50
DN 65 65
DN 80 80
DN 100 100
DN 125 125
DN 150 150
DN 200 200
DN 250 250
DN 300 300
DN 350 350
DN 400 400
DN 450 450
DN 500 500
DN 600 600
3 Body configuration Code
Wafer design,
face-to-face dimension FTF API609 table 3, EN 558
series 108, EN 558 series 109
W
4 Operating pressure Code
10 bar 2
16 bar 3
20 bar 4
25 bar 5
40 bar 6
5 Connection type Code
PN 10 / flange EN 1092, face-to-face dimension
FTF EN 558 series 108
2
PN 16 / flange EN 1092, face-to-face dimension
FTF EN 558 series 108
3
PN 25 / flange EN 1092, face-to-face dimension
FTF EN 558 series 20
5
PN 40 / flange EN 1092, face-to-face dimension
FTF EN 558 series 109
6
ANSI B16.5, Class 150, face-to-face dimension FTF
EN 558 series 108
D
ANSI B16.5, Class 300, dimension FTF EN 558
series 109
M
6 Body material Code
1.4408 / ASTM A351 / CF8M 4
6 Continuation of Body material Code
1.0619 / ASTM A216 WCB, CDP coated 20 µm,
for non-European countries,
1.0619 is not a material for pressure equipment
according to 2014/68/EU
5
7 Disc material Code
1.4408 / ASTM A351 / CF8M A
8 Shaft material Code
1.4542, ASTM 564 630 6
9 Shut-off seal material Code
TFM 1600 (FDA certification) T
10 Liner fixing Code
Loose liner L
11 Actuator flange Code
F05, flange type DIN EN ISO 5211 F05
F07, flange type DIN EN ISO 5211 F07
F10, flange type DIN EN ISO 5211 F10
F12, flange type DIN EN ISO 5211 F12
F14, flange type DIN EN ISO 5211 F14
12 Actuator flange Code
F07, flange type DIN EN ISO 5211 07
F10, flange type DIN EN ISO 5211 10
F12, flange type DIN EN ISO 5211 12
F14, flange type DIN EN ISO 5211 14
F16, flange type DIN EN ISO 5211 16
13 Shaft connection and size Code
Square, diagonal, WAF 11 mm D11
Square, diagonal, WAF 14 mm D14
Square, diagonal, WAF 17 mm D17
Square, diagonal, WAF 22 mm D22
Square, diagonal, WAF 27 mm D27
Square, diagonal, WAF 36 mm D36
14 Special version Code
Without
ATEX certification X
15 CONEXO Code
Without
Integrated RFID chip for electronic identification
and traceability
C
6 Order data
www.gemu-group.com 9 / 30 GEMÜ R470 Tugela

Order example
Ordering option Code Description
1 Type R470 Butterfly valve, bare shaft
(double-eccentric), Tugela
2 DN 300 DN 300
3 Body configuration W Wafer design,
face-to-face dimension FTF API609 table 3, EN 558 series 108, EN 558
series 109
4 Operating pressure 4 20 bar
5 Connection type 6 PN 40 / flange EN 1092, face-to-face dimension FTF EN 558 series
109
6 Body material 4 1.4408 / ASTM A351 / CF8M
7 Disc material A 1.4408 / ASTM A351 / CF8M
8 Shaft material 6 1.4542, ASTM 564 630
9 Shut-off seal material T TFM 1600 (FDA certification)
10 Liner fixing L Loose liner
11 Actuator flange F14 F14, flange type DIN EN ISO 5211
12 Actuator flange 16 F16, flange type DIN EN ISO 5211
13 Shaft connection and size D27 Square, diagonal, WAF 27 mm
14 Special version Without
15 CONEXO Without
6 Order data
www.gemu-group.com10 / 30GEMÜ R470 Tugela

7 Technical data
7.1 Medium
Working medium: Gaseous and liquid media which have no negative impact on the physical and chemical properties
of the disc and seat material.
7.2 Temperature
Media temperature: -60 — 230 °C
Ambient temperature: -20 — 70 °C
Storage temperature: -60 — 60 °C
7.3 Pressure
Operating pressure: Max. permissible pressure of working medium
PS
[bar]
Media of fluid group 1
Category I Category II Category III
Liquid Gas Liquid Gas Gas
10 DN 200 - 600 DN 50 - 100
DN 50 - 600
DN 125 - 350 DN 400 - 600
16 - DN 50 DN 65 - 200 DN 250 - 600
20 - DN 50 DN 65 - 150 DN 200 - 600
25 - - DN 50 - 125 DN 150 - 600
40 - - DN 50 - 100 DN 125 - 600
Pressure/temperature
diagram:
0
10
20
30
40
50
-60 -40 -20 0 20 40 60 80 100 120 140 160 180 200 220 240
Pressure [bar]
PN10, PN16, Class 150
PN25, PN40, Class 300
Temperature [°C]
GEMÜ R470 Tugelawww.gemu-group.com 11 / 30
7 Technical data

Kv values: DN NPS Connection type code 1)
D, 2, 3 M, 5, 6
50 2″ 45.0 45.0
65 2½″ 78.0 78.0
80 3″ 165.0 165.0
100 4″ 400.0 400.0
125 5″ 650.0 650.0
150 6″ 1050.0 1050.0
200 8″ 2200.0 1800.0
250 10″ 3300.0 3150.0
300 12″ 5100.0 4750.0
350 14″ 5800.0 5200.0
400 16″ 8000.0 6900.0
450 18″ 10500.0 9300.0
500 20″ 14000.0 11300.0
600 24″ 21600.0 18500.0
Kv values in m³/h
1) Connection type
Code 2: PN 10 / flange EN 1092, face-to-face dimension FTF EN 558 series 108
Code 3: PN 16 / flange EN 1092, face-to-face dimension FTF EN 558 series 108
Code 5: PN 25 / flange EN 1092, face-to-face dimension FTF EN 558 series 20
Code 6: PN 40 / flange EN 1092, face-to-face dimension FTF EN 558 series 109
Code D: ANSI B16.5, Class 150, face-to-face dimension FTF EN 558 series 108
Code M: ANSI B16.5, Class 300, dimension FTF EN 558 series 109
7.4 Product conformity
Pressure Equipment Dir-
ective:
2014/68/EU
Food: FDA
EAC: The product is certified according to EAC.
Explosion protection: 2014/34/EU (ATEX)
ATEX marking: Special function code X
Gas: II -/2 G Ex h -/IIC T6...T3 -/Gb X
Dust: II -/2D Ex h -/IIIC T150°C -/Db X
www.gemu-group.com12 / 30GEMÜ R470 Tugela
7 Technical data

7.5 Mechanical data
Torques: DN NPS Connection type code 1)
D, 2, 3 M, 5, 6
Maximum pressure differential [bar]
0.0 6.0 10.0 16.0 20.0 0.0 20.0 25.0 40.0 50.0
50 2″ 33.0 33.0 34.0 35.0 37.0 33.0 37.0 38.0 40.0 42.0
65 2½″ 43.0 44.0 45.0 46.0 50.0 43.0 50.0 52.0 57.0 60.0
80 3″ 54.0 56.0 57.0 58.0 64.0 54.0 64.0 67.0 74.0 79.0
100 4″ 68.0 71.0 72.0 74.0 84.0 68.0 84.0 88.0 99.0 107.0
125 5″ 90.0 94.0 96.0 100.0 115.0 90.0 115.0 121.0 139.0 151.0
150 6″ 114.0 120.0 123.0 128.0 149.0 123.0 158.0 167.0 193.0 211.0
200 8″ 181.0 192.0 200.0 211.0 258.0 202.0 280.0 299.0 358.0 397.0
250 10″ 250.0 268.0 280.0 297.0 372.0 287.0 409.0 439.0 530.0 591.0
300 12″ 357.0 387.0 408.0 438.0 567.0 393.0 603.0 655.0 813.0 918.0
350 14″ 559.0 607.0 640.0 688.0 721.0 699.0 861.0 901.0 1023.0 1104.0
400 16″ 950.0 1027.0 1079.0 1156.0 1207.0 1188.0 1445.0 1509.0 1701.0 1830.0
450 18″ 1420.0 1534.0 1611.0 1725.0 1802.0 1629.0 2011.0 2107.0 2394.0 2585.0
500 20″ 1967.0 2144.0 2262.0 2439.0 2557.0 2499.0 3089.0 3237.0 3679.0 3974.0
600 24″ 3324.0 3579.0 3748.0 4003.0 4173.0 3579.0 4429.0 4641.0 5278.0 5703.0
Torques in Nm
1) Connection type
Code 2: PN 10 / flange EN 1092, face-to-face dimension FTF EN 558 series 108
Code 3: PN 16 / flange EN 1092, face-to-face dimension FTF EN 558 series 108
Code 5: PN 25 / flange EN 1092, face-to-face dimension FTF EN 558 series 20
Code 6: PN 40 / flange EN 1092, face-to-face dimension FTF EN 558 series 109
Code D: ANSI B16.5, Class 150, face-to-face dimension FTF EN 558 series 108
Code M: ANSI B16.5, Class 300, dimension FTF EN 558 series 109
GEMÜ R470 Tugelawww.gemu-group.com 13 / 30
7 Technical data

Weight: DN NPS Connection type code 1)
D, 2, 3 M, 5, 6
50 2″ 3.2 3.2
65 2½″ 3.6 3.6
80 3″ 4.9 4.9
100 4″ 7.5 7.5
125 5″ 8.0 8.0
150 6″ 12.0 14.0
200 8″ 18.0 23.0
250 10″ 31.0 40.0
300 12″ 47.0 66.0
350 14″ 77.0 114.0
400 16″ 96.0 146.0
450 18″ 133.0 212.0
500 20″ 156.0 261.0
600 24″ 268.0 385.0
Weights in kg
1) Connection type
Code 2: PN 10 / flange EN 1092, face-to-face dimension FTF EN 558 series 108
Code 3: PN 16 / flange EN 1092, face-to-face dimension FTF EN 558 series 108
Code 5: PN 25 / flange EN 1092, face-to-face dimension FTF EN 558 series 20
Code 6: PN 40 / flange EN 1092, face-to-face dimension FTF EN 558 series 109
Code D: ANSI B16.5, Class 150, face-to-face dimension FTF EN 558 series 108
Code M: ANSI B16.5, Class 300, dimension FTF EN 558 series 109
Flow direction: Indicated by an arrow on the product
www.gemu-group.com14 / 30GEMÜ R470 Tugela
7 Technical data

8 Dimensions
8.1 Actuator flange
8.1.1 Flange PN10 (code 2), PN16 (code 3), CLASS 150 (code D)
□G
□G
DN 350 - 600
E
øy
øz
øa
øb
øy
øa
□G
DN 50 - 300
DN NPS ISO 5211 øa øb E □G øy øz
50 2″ F05 - 50.0 22.0 11.0 - 4 x 7.0
65 2½″ F05/F07 70.0 50.0 15.0 11.0 4 x 7.0 4 x 7.0
80 3″ F05/F07 70.0 50.0 15.0 11.0 4 x 7.0 4 x 7.0
100 4″ F07 - 70.0 23.0 14.0 - 4 x 9.5
125 5″ F07 - 70.0 23.0 14.0 - 4 x 9.5
150 6″ F07/F10 102.0 70.0 32.5 14.0 4 x 12.0 4 x 9.5
200 8″ F10 - 102.0 34.5 17.0 - 4 x 12.0
250 10″ F10/F12 125.0 102.0 34.0 22.0 4 x 14.0 4 x 12.0
300 12″ F12/F14 140.0 125.0 29.5 27.0 4 x 18.0 4 x 14.0
350 14″ F14/F16 165.0 140.0 12.0 27.0 4 x 22.0 4 x 18.0
400 16″ F14/F16 165.0 140.0 12.0 36.0 4 x 22.0 4 x 18.0
450 18″ F14/F16 165.0 140.0 12.0 36.0 4 x 22.0 4 x 18.0
500 20″ F14/F16 165.0 140.0 12.0 46.0 4 x 22.0 4 x 18.0
600 24″ F14/F16 165.0 254.0 18.0 46.0 4 x 23.0 4 x 19.0
Dimensions in mm
GEMÜ R470 Tugelawww.gemu-group.com 15 / 30
8 Dimensions

8.1.2 Flange PN25 (code 5), PN40 (code 6), CLASS 300 (code M)
□G
□G
DN 350 - 600
E
øy
øz
øa
øb
øy
øa
□G
DN 50 - 300
DN NPS ISO 5211 øa øb E □G øy øz
50 2″ F05 - 50.0 22.0 11.0 4 x 7.0 -
65 2½″ F05/F07 70.0 50.0 15.0 11.0 4 x 9.5 4 x 7.0
80 3″ F05/F07 70.0 50.0 15.0 11.0 4 x 9.5 4 x 7.0
100 4″ F07 - 70.0 23.0 14.0 4 x 9.5 -
125 5″ F07 - 70.0 23.0 14.0 4 x 9.5 -
150 6″ F10 - 70.0 26.0 17.0 4 x 12.0 -
200 8″ F10/F12 125.0 102.0 34.5 22.0 4 x 14.0 4 x 12.0
250 10″ F12/F14 140.0 102.0 30.0 27.0 4 x 18.0 4 x 13.5
300 12″ F14 - 125.0 38.5 27.0 4 x 18.0 -
350 14″ F14/F16 165.0 140.0 12.0 36.0 4 x 22.0 4 x 18.0
400 16″ F14/F16 165.0 140.0 12.0 46.0 4 x 22.0 4 x 18.0
450 18″ F16/F25 254.0 140.0 18.0 46.0 4 x 19.0 4 x 22.0
500 20″ F16/F25 254.0 140.0 18.0 55.0 4 x 19.0 4 x 22.0
600 24″ F25 254.0 254.0 18.0 55.0 4 x 19.0 4 x 22.0
Dimensions in mm
www.gemu-group.com16 / 30GEMÜ R470 Tugela
8 Dimensions

8.2 Body
8.2.1 Flange PN10 (code 2), PN16 (code 3)
C
DN 50 - 300 DN 350 - 600
Ø
D
C
Ø
D
Ø
S
H
BA
BA
H
Ø
S
F
F
DN NPS A B øb C ØD F H ØS
50 2″ 124.0 96.4 50.0 50.0 100.0 - 15.0 38.6
65 2½″ 122.0 101.0 50.0 51.5 105.0 - 49.0 57.0
80 3″ 143.5 115.0 50.0 49.5 132.0 - 69.0 74.0
100 4″ 160.0 128.0 70.0 56.5 158.0 - 91.0 96.0
125 5″ 176.5 148.0 70.0 57.0 186.0 - 103.0 111.0
150 6″ 198.0 157.0 70.0 57.5 216.0 33.0 140.0 144.0
200 8″ 230.0 195.0 102.0 63.0 266.0 35.0 179.0 188.0
250 10″ 273.0 236.0 102.0 71.0 324.0 34.0 231.0 237.0
300 12″ 319.0 262.0 125.0 81.5 381.0 30.0 276.0 283.0
350 14″ 455.0 303.0 140.0 92.0 429.0 17.0 300.0 307.0
400 16″ 490.0 337.5 140.0 101.5 480.0 17.0 347.0 363.5
450 18″ 502.0 353.5 140.0 114.0 533.0 17.0 394.0 414.0
500 20″ 524.0 376.5 140.0 127.0 584.0 17.0 434.0 458.0
600 24″ 625.0 453.5 165.0 154.0 692.0 22.0 524.0 550.0
Dimensions in mm
GEMÜ R470 Tugelawww.gemu-group.com 17 / 30
8 Dimensions

8.2.2 Flange PN25 (code 5), PN40 (code 6)
C
DN 50 - 300 DN 350 - 600
Ø
D
C
Ø
D
Ø
S
H
BA
BA
H
Ø
S
F
F
DN NPS A B øb C ØD F H ØS
50 2″ 124.0 96.4 50.0 50.0 100.0 22.0 15.0 38.6
65 2½″ 122.0 101.0 50.0 51.5 105.0 15.0 49.0 57.0
80 3″ 143.5 115.0 50.0 49.5 132.0 18.0 69.0 74.0
100 4″ 160.0 128.0 70.0 56.5 158.0 23.0 91.0 96.0
125 5″ 176.5 148.0 70.0 57.0 186.0 23.0 103.0 111.0
150 6″ 217.5 170.5 70.0 59.0 216.0 26.0 140.0 144.0
200 8″ 250.0 206.5 102.0 73.0 266.0 35.0 179.0 188.0
250 10″ 303.0 248.0 102.0 83.0 324.0 31.0 231.0 237.0
300 12″ 335.5 291.0 125.0 92.0 381.0 39.0 276.0 283.0
350 14″ 470.0 320.5 140.0 117.0 429.0 17.0 300.0 315.0
400 16″ 500.5 365.5 140.0 133.5 480.0 17.0 347.0 363.5
450 18″ 531.0 382.5 140.0 149.0 533.0 17.0 394.0 414.0
500 20″ 593.0 426.5 140.0 162.0 584.0 22.0 434.0 456.5
600 24″ 645.0 498.0 165.0 181.0 692.0 22.0 524.0 550.0
Dimensions in mm
www.gemu-group.com18 / 30GEMÜ R470 Tugela
8 Dimensions

www.gemu-group.com 19 / 30 GEMÜ R470 Tugela
9 Manufacturer's information
9.1 Delivery
●Check that all parts are present and check for any damage
immediately upon receipt.
The product's performance is tested at the factory. The scope
of delivery is apparent from the dispatch documents and the
design from the order number.
9.2 Transport
WARNING
Moving components.
▶Risk of injury.
▶Moving components can cause seri-
ous injury. Only actuate the valve once
it has been fully installed in the relev-
ant system. Actuating the valve when it
has not been installed may lead to dan-
gerous situations.
1. Only transport the product by suitable means. Do not drop.
Handle carefully.
2. After the installation dispose of transport packaging ma-
terial according to relevant local or national disposal regu-
lations / environmental protection laws.
9.3 Storage
1. Store the product free from dust and moisture in its ori-
ginal packaging.
2. Avoid UV rays and direct sunlight.
3. Do not exceed the maximum storage temperature (see
chapter "Technical data").
4. Do not store solvents, chemicals, acids, fuels or similar
fluids in the same room as GEMÜ products and their spare
parts.
10 Installation in piping
10.1 Preparing for installation
WARNING
The equipment is subject to pressure!
▶Risk of severe injury or death.
●Depressurize the plant.
●Completely drain the plant.
WARNING
Corrosive chemicals!
▶Risk of caustic burns.
●Wear suitable protective gear.
●Completely drain the plant.
WARNING
GEMÜ products without an operator!
▶Risk of severe injury or death.
●Do not apply pressure to GEMÜ
products without an operator installed
in piping.
CAUTION
Hot plant components!
▶Risk of burns.
●Only work on plant that has cooled
down.
CAUTION
Leakage
▶Emission of dangerous materials.
●Provide precautionary measures against exceeding the
maximum permitted pressures caused by pressure
surges (water hammer).
CAUTION
Exceeding the maximum permissible pressure.
▶Damage to the product.
●Provide precautionary measures against exceeding the
maximum permitted pressures caused by pressure
surges (water hammer).
CAUTION
Use as end-of-line valve!
▶Damage to the GEMÜ product.
●When using the GEMÜ product as an
end-of-line valve, a mating flange must
be fitted.
CAUTION
Risk of crushing!
▶Risk of severe injury!
●Before performing any work on the
GEMÜ product, depressurize the plant.
10 Installation in piping

www.gemu-group.com20 / 30GEMÜ R470 Tugela
10 Installation in piping
NOTICE
Suitability of the product!
▶The product must be appropriate for the piping system
operating conditions (medium, medium concentration,
temperature and pressure) and the prevailing ambient
conditions.
1. Ensure the product is suitable for the relevant application.
2. Check the technical data of the product and the materials.
3. The external pressure must not exceed 1 bar PSa.
4. Pressure surges are not permissible. The plant operator
must plan appropriate precautionary measures.
5. The pressure differential must not exceed the maximum
operating pressure.
6. The butterfly valve may only be used with a bonded liner
up to 0.2 bar abs.
7. The plant operator must ensure fire protection is in place.
Regularly service electrical equipment designed for pre-
ventive fire protection in compliance with DIN VDE
0100-610 (IEC/EN 61557).
8. Keep appropriate tools ready.
9. Use appropriate protective gear as specified in plant oper-
ator's guidelines.
10. Observe appropriate regulations for connections.
11. Installation work must be performed by trained personnel.
12. Shut off plant or plant component.
13. Secure the plant or plant component against recommis-
sioning.
14. Depressurize the plant or plant component.
15. Completely drain the plant or plant component and allow it
to cool down until the temperature is below the media va-
porization temperature and cannot cause scalding.
16. Decontaminate, rinse and ventilate the plant or plant com-
ponent properly.
17. Lay piping so that the product is protected against trans-
verse and bending forces, and also from vibrations and
tension.
18. Only install the product between matching aligned pipes
(see following chapters).
19. Please note the flow direction (see chapter "Installation
location").
20. Please note the installation position (see chapter "Installa-
tion location").
21. The valve is not designed for loads caused by earth-
quakes.
22. The plant operator must take into account loads and
torques for the bearing elements.
For valves with a nominal size > DN xx, suitable bearing
elements may need to be used. Design weights and di-
mensions can be found in the datasheets.
10.2 Installation location
1. You can choose the installation position of the GEMÜ
product. If media is contaminated and DN ≥ 300, install
GEMÜ R470 horizontally, so that the lower edge of the disc
opens in-line with flow direction.
2. You can choose the flow direction of the GEMÜ product.
3. Arrange the bolt holes of piping and valves so that they
are not on the two main axes (but rather symmetrical to
them).
Main axis
Main axis
4. The inside diameter of the piping must match the nominal
diameter of the GEMÜ product.
5. The diameter of the pipe flanges should be, in compliance
with the respective nominal size, between "D max" and "D
min" (see table).
DN D max D min
25 32 13
40 47 29
50 60 33
65 74 53
80 96 72
100 113 92
125 140 118
150 169 146
200 223 197
250 273 247
300 323 297
350 363 335
400 417 384
450 465 432
500 518 485
600 618 580
Table of contents
Other GEM Control Unit manuals
Popular Control Unit manuals by other brands
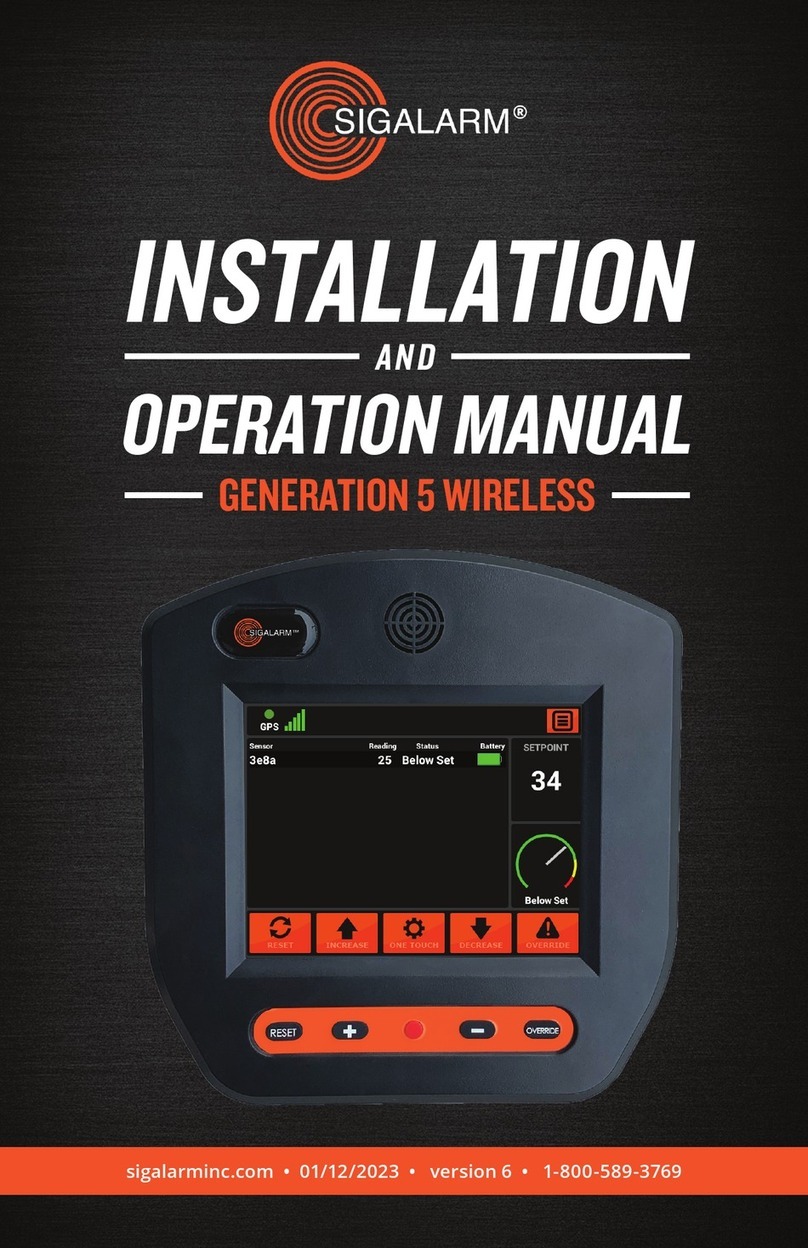
Sigalarm
Sigalarm GENERATION 5 WIRELESS Installation and operation manual

Trenz Electronic
Trenz Electronic TEF1001 Schematics
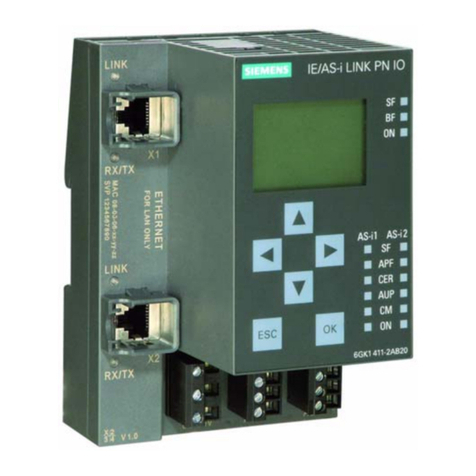
Siemens
Siemens SIMATIC NET IE/AS-INTERFACE LINK PN IO manual

Blue Bamboo
Blue Bamboo H50 installation guide
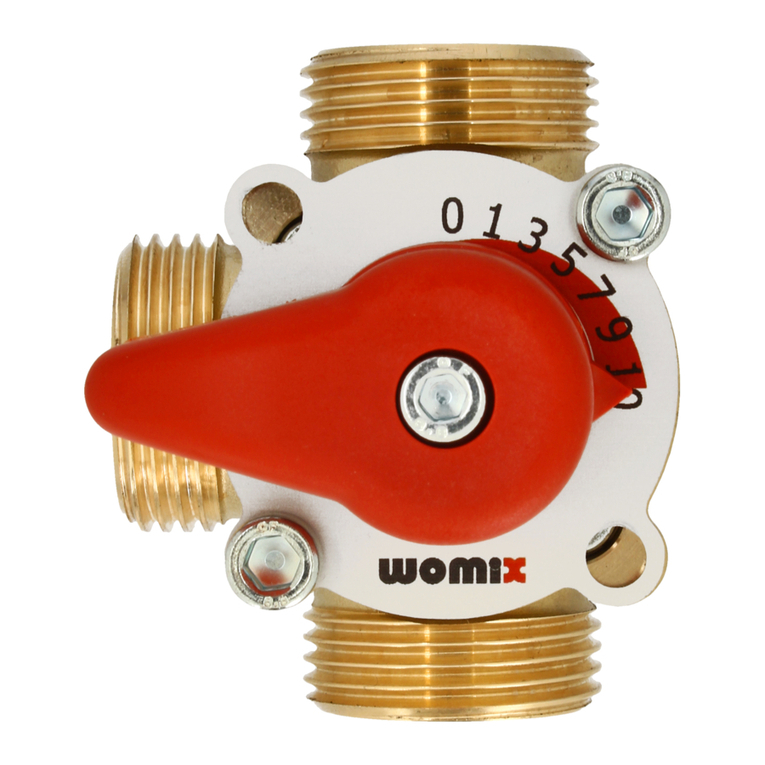
WOMIX
WOMIX MIX M 3-20 Mounting and operating instruction
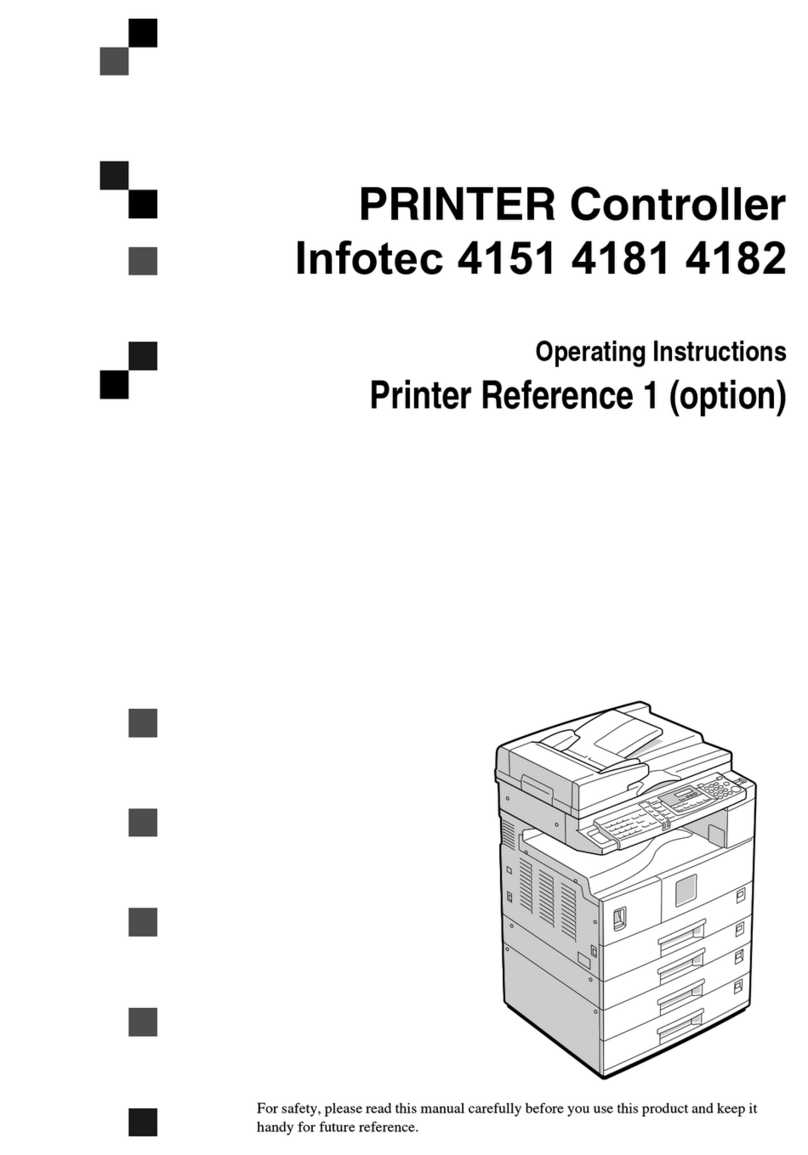
Xerox
Xerox 4151 Printer Reference