GE AM-4.16-250-6C User manual

GEI
-
88761
E
INSTRUCTIONS
SUPERSEDES
GEU
88761
D
AND
RENEWAL
PARTS
k
^
VA
)
4
PM
R
D
isco
^
w
G
<
^
T
~
\
\
MAGHE
-
BLAST
CIRCUIT
BREAKER
TYPES
AM
-
4.16
-
250
-
6
C
AM
-
4.16
-
250
-
6
H
AM
-
4.16
-
250
-
7
c
AM
-
4.16
-
250
-
7
H
;
i
71
'
*
‘
.
•
rt
1
J
:
F
/
i
:
i
Ffi
.
4
'
•
rihv
'
i
73
)
K
-
•
•
•
’
V
"
;
1
©
!
?
{
T
:
CONTENTS
1
t
-
i
.
-
*
Introduction
1
•
•
•
N
-
>
?
'
Receiving
,
Handling
and
Storage
-
V
1
Installation
2
-
?
•
Description
of
Operation
4
Adjustments
General
Maintenance
12
©
•••
•
••
•
•
•
•
28
Renewal
Parts
%
f
t
\
!
I
'
&
;
SWITCHGEAR
DEPARTMENT
i
$
GENERAL
^
)
ELECTRIC
PHILADELPHIA
.
PA
.
i
*
>
%
{
*
Courtesy of NationalSwitchgear.com

I
GEI
-
88761
1
1
3
MAGNE
-
BLAST
CIRCUIT
BREAKER
S
AM
-
4.16
-
250
-
6
AM
-
4.16
-
250
-
7
A
Letter
Designation
-
B
,
C
,
and
H
,
used
immediately
following
the
model
number
xndicates
basic
design
features
.
ft
3
i
;
1
INTRODUCTION
1
Vmagne
-
blast
circuit
breaker
is
the
removable
interrupting
element
f
\
use
in
vertical
-
lift
metal
-
clad
switchgear
,
to
provide
reliable
co
\
ol
and
protection
of
power
systems
.
Among
the
many
advantages
of
met
^
clad
switchgear
are
added
protection
to
equipment
and
personnel
,
com
^
fcness
,
simplified
installation
and
reduced
maintenance
.
In
keep
-
ing
i
h
these
features
the
magne
-
blast
breakers
are
designed
for
in
-
terclri
geability
and
maneuverability
,
together
with
reliability
and
low
maintenance
requirements
.
The
magne
-
blast
circuit
breaker
operates
on
the
principle
that
an
arc
can
be
interrupted
in
air
by
sufficiently
elongating
and
cooling
it
.
.
This
is
accomplished
by
means
of
a
strong
magnetic
field
that
lengthens
the
arc
and
forces
it
into
intimate
contact
with
cool
dielectric
ma
-
terial
.
A
sturdy
,
reliable
operating
mechanism
assures
low
mainten
-
w
ance
and
long
life
.
t
"
—
1
The
AM
-
4.16
magne
-
blast
breaker
is
available
in
a
number
of
current
ratings
.
Refer
to
the
breaker
nameplate
for
the
complete
rating
in
-
formation
of
any
particular
breaker
.
The
short
circuit
conditions
to
be
Imposed
on
the
breaker
must
not
exceed
Its
rating
,
nor
should
it
be
^
called
upon
to
operate
at
voltages
or
currents
greater
than
those
o
>
given
on
the
nameplate
.
Since
this
book
is
written
to
cover
several
o
ratings
of
breakers
that
are
of
the
same
general
design
,
all
instruc
-
0
tions
will
be
of
a
general
character
and
all
illustrations
will
be
typical
,
unless
otherwise
specifie
m
VI
«
PROPER
INSTALLATION
AND
MAINTENANCE
ARE
NECESSARY
TO
INSURE
CONTINUED
SATISFACTORY
OPERATION
OF
THE
BREAKER
.
The
following
instructions
will
provide
complete
information
for
placing
the
magne
-
blast
breaker
in
service
and
for
maintaining
satisfactory
operation
.
RECEIVING
,
HANDLING
-
AND
STORAGE
M
Receiving
and
Handling
Each
breaker
is
carefully
inspected
and
packed
by
workmen
experienced
in
the
proper
handling
and
packing
of
electrical
equipment
,
diately
upon
receipt
of
the
circuit
breaker
,
an
examination
should
be
Imme
-
These
instructions
do
not
purport
to
cover
all
details
or
variations
in
equipment
nor
to
provide
for
every
possible
contingency
to
be
met
Should
in
connection
with
installation
,
operation
or
maintenance
,
further
Information
be
desired
or
should
particular
problems
arise
which
are
not
covered
sufficiently
for
the
purchaser
'
s
purposes
,
the
matter
should
be
referred
to
the
General
Electric
Company
.
'
i
!
j
1
Courtesy of NationalSwitchgear.com

GEI
-
88761
If
injury
or
rough
handling
made
for
any
damage
sustained
in
transit
,
is
evident
,
a
damage
claim
should
be
filed
immediately
with
the
trans
-
portation
company
and
the
nearest
General
Electric
Sales
Office
should
be
notified
.
It
is
expected
that
due
care
will
be
exercised
during
the
unpacking
and
Installation
of
the
breaker
so
that
no
damage
will
occur
from
careless
or
rough
handling
,
or
from
exposure
to
moisture
or
dirt
.
Loose
parts
associated
with
the
breaker
are
always
Included
in
the
same
crate
.
Check
all
parts
against
the
packing
list
to
be
sure
that
no
parts
have
been
overlooked
.
Storage
It
is
recommended
that
the
breaker
be
put
into
service
immediately
in
its
permanent
location
.
If
this
is
not
possible
,
the
following
pre
-
cautions
must
be
taken
to
insure
the
proper
storage
of
the
breaker
:
1
.
The
breaker
should
be
carefully
protected
against
condensation
,
preferably
by
storing
it
in
a
warm
dry
room
,
since
water
absorption
has
an
adverse
effect
on
the
insulation
parts
.
Circuit
breakers
for
outdoor
metal
-
clad
switchgear
should
be
stored
in
the
equipment
only
when
power
is
available
and
the
heaters
are
in
operation
to
prevent
condensation
.
2
.
The
breaker
should
be
stored
In
a
clean
location
,
free
from
corro
-
sive
gases
or
fumes
;
particular
care
should
be
taken
to
protect
the
equipment
from
moisture
and
cement
dust
,
as
this
combination
has
a
very
corrosive
effect
on
many
parts
.
3
.
Machined
parts
of
the
operating
mechanism
,
etc
with
a
heavy
oil
or
grease
to
prevent
rusting
.
If
the
breaker
is
stored
for
any
length
of
time
,
It
should
be
inspected
periodically
to
see
that
rusting
has
not
started
and
to
insure
good
mechanical
condition
.
Should
the
breaker
be
stored
under
unfavorable
atmospheric
conditions
,
steps
should
be
taken
to
dry
out
the
breaker
before
it
is
placed
in
service
.
INSTALLATION
5
should
be
coated
•
;
Remove
the
box
barrier
and
front
cover
and
make
a
visual
inspection
to
ascertain
that
the
breaker
and
mechanism
Is
in
satisfactory
con
-
dition
.
Check
all
bearing
surfaces
of
the
mechanism
for
lubrication
.
Refer
to
section
on
Lubrication
(
page
14
)
Charge
the
breaker
closing
springs
manually
using
a
5
/
8
"
ratchet
wrench
to
turn
the
driving
eccentric
(
6
)
Fig
.
(
4
)
.
Turning
the
eccentric
counter
clockwise
will
advance
the
ratcher
wheel
and
compress
tne
springs
.
When
the
springs
have
reached
the
fully
charged
position
the
indi
-
cator
(
3
D
)
Fig
.
(
4
)
will
read
"
CHARGED
"
,
and
the
driving
pawl
will
be
raised
from
the
ratchet
wheel
teeth
.
Additional
turning
of
the
eccentric
will
not
advance
the
ratchet
wheel
.
1
.
1
2
.
i
.
)
2
$
Courtesy of NationalSwitchgear.com

GEI
-
88761
Insert
the
spring
blocking
device
(
4
)
Fig
.
(
4
)
and
manually
dis
-
charge
the
springs
against
the
pins
by
pushing
the
manual
release
button
(
1
)
Fig
.
(
4
)
.
The
springs
are
now
blocked
and
slow
closing
of
the
breaker
contacts
can
be
accomplished
by
again
turning
the
driving
eccentric
with
a
5
/
8
ratchet
wrench
.
During
the
slow
closing
operation
check
to
insure
that
the
mechanism
does
not
stick
or
bind
during
the
entire
stroke
,
that
it
latches
se
-
curely
in
the
closed
position
,
and
that
it
trips
freely
when
the
man
-
ual
trip
lever
is
operated
.
The
breaker
should
not
be
operated
electrically
until
It
has
been
operated
several
times
manually
to
Insure
freedom
of
action
.
At
this
time
,
also
check
the
following
adjustments
:
i
Primary
contact
wipe
Arcing
contact
wipe
Primary
contact
gap
Refer
to
page
7
Refer
to
page
7
Refer
to
page
7
"
DO
NOT
WORK
ON
EITHER
THE
BREAKER
OR
MECHANISM
UNLESS
THE
CLOSING
SPRINGS
ARE
BLOCKED
AND
THE
OPENING
SPRINGS
HAVE
BEEN
TRIPPED
OPEN
OR
MECHANICALLY
BLOCKED
.
THIS
PRECAUTION
IS
REQUIRED
TO
PREVENT
ACCIDENTAL
CLOSING
OR
TRIPPING
.
"
a
.
b
.
c
.
After
the
adjustments
have
been
checked
,
the
springs
can
be
un
-
blocked
.
Rotate
the
driving
eccentric
until
the
indicator
reads
"
CHARGED
"
and
the
ratchet
wheel
no
longer
is
advanced
.
The
blocking
device
can
now
be
removed
.
*
S
&
4
3
.
Attach
test
coupler
to
circuit
breaker
and
operate
electrically
several
times
.
TROL
POWER
CHECK
"
.
Check
the
control
voltage
as
described
under
"
CON
-
H
NOTE
:
If
the
breaker
secondary
wiring
is
to
be
given
a
hi
-
potential
test
at
1500
volts
,
remove
both
the
motor
leads
from
the
terminal
connection
.
Failure
to
disconnect
the
motor
from
the
circuit
may
cause
damage
to
the
winding
insulation
.
Remove
the
test
coupler
and
replace
box
barrier
.
5
.
If
breaker
has
been
stored
for
a
long
period
of
time
,
it
is
recom
-
mended
that
the
Insulation
be
checked
with
a
standard
60
cycle
high
potential
test
.
Refer
to
Insulation
Test
(
page
13
)
.
6
.
Lubricate
the
silver
portion
of
the
primary
disconnect
studs
by
rubbing
a
small
amount
of
contact
lubricant
D
50
H
47
to
form
a
thin
coating
on
the
ball
contact
.
7
.
Refer
to
metal
-
clad
instruction
book
GEH
-
1802
for
final
Instructions
before
Inserting
the
breaker
into
the
metal
-
clad
unit
.
4
.
1
«
s
»
3
Courtesy of NationalSwitchgear.com

f
;
GEI
-
88761
DESCRIPTION
OF
OPERATION
The
inagne
-
blast
breaker
is
composed
of
two
major
parts
,
the
breaker
element
and
the
operating
mechanism
.
The
breaker
element
comprises
three
similar
pole
units
,
each
pole
unit
consisting
of
main
and
arcing
contacts
,
an
interrupter
,
and
an
enclosing
box
barrier
that
segregates
the
interrupting
units
from
each
other
to
provide
insulation
between
phases
as
well
as
from
each
phase
to
ground
.
The
primary
connections
to
the
associated
metal
-
clad
equipment
are
made
through
the
primary
disconnect
studs
.
i
The
ML
-
13
operating
mechanism
shown
in
Figures
1
,
2
,
and
3
is
of
the
stored
energy
type
designed
to
give
high
speed
closing
and
opening
.
The
mechanism
will
operate
on
a
-
c
or
d
-
c
voltage
as
indicated
on
the
breaker
name
plate
.
Closing
and
opening
operations
are
controlled
electrically
by
the
metal
-
clad
or
remote
relaying
,
and
mechanically
by
the
manual
close
and
trip
levers
on
the
breaker
.
All
secondary
connections
from
the
breaker
to
the
metal
-
clad
unit
are
made
through
the
coupler
(
1
)
Fig
.
(
1
)
.
!
j
A
positive
interlock
(
2
)
Fig
.
(
3
)
and
interlock
switch
(
2
)
Fig
.
(
l
)
are
provided
between
the
breaker
and
metal
-
clad
unit
to
prevent
rais
-
ing
or
lowering
of
the
breaker
in
the
unit
while
In
a
closed
position
and
to
prevent
a
closing
operation
when
the
breaker
is
not
in
either
the
fully
raised
or
lowered
position
.
A
plunger
can
also
be
provided
to
operate
an
additional
auxiliary
switch
mounted
in
the
metal
-
clad
unit
.
When
the
breaker
is
interchangeable
with
MS
-
13
solenoid
operated
breakers
in
M
-
26
metal
-
clad
units
,
motor
circuit
fuses
are
mounted
,
on
the
breaker
for
protection
.
These
breakers
are
identified
by
the
"
C
"
suffix
in
the
breaker
nomenclature
.
>
m
In
case
when
breakers
with
ML
-
13
operating
mechanisms
must
match
and
line
up
with
breakers
having
ML
-
11
mechanisms
the
spring
charg
-
ing
circuit
should
be
fused
with
Buss
Company
Fusetrons
as
follows
Control
Voltage
Fuse
Size
Cat
.
No
.
48
v
-
d
-
c
llOv
125
v
-
d
-
c
115
v
-
a
-
c
220
v
-
d
-
c
250
v
-
d
-
c
230
v
-
a
-
c
10
A
FRN
10
FRN
4
FRN
4
FRN
4
FRN
2.5
FRN
2.5
FRN
2.5
4
A
d
-
c
4
A
4
A
\
2.5
A
2.5
A
2.5
A
Spring
Charging
;
The
mechanism
consists
of
a
high
speed
gear
motor
that
compresses
a
set
of
closing
springs
through
the
action
of
a
simple
eccentric
,
ratch
-
et
,
and
pawl
assembly
.
The
rotary
action
of
the
motor
(
2
)
Fig
.
(
4
)
is
converted
to
a
short
straight
stroke
pumping
action
through
the
eccent
-
ric
(
6
)
and
a
lever
that
carries
a
spring
loaded
driving
pawl
(
5
)
.
5
f
3
*
3
I
4
3
Courtesy of NationalSwitchgear.com

GEI
-
88761
The
pawl
advances
the
ratchet
wheel
(
3
)
Fig
.
(
3
)
only
a
few
degrees
each
stroke
where
it
Is
held
In
position
by
the
latching
pawls
(
l
)
.
When
the
ratchet
wheel
has
been
rotated
approximately
180
degrees
the
closing
springs
(
6
)
will
be
fully
compressed
.
As
the
ratchet
wheel
continues
to
rotate
,
the
spring
load
will
shift
over
center
and
attempt
to
discharge
.
After
only
a
few
degrees
of
rotation
,
the
closing
roller
(
10
)
Fig
.
(
l
)
will
engage
the
closing
latch
(
ll
)
and
the
compressed
springs
will
be
held
in
repose
until
a
closing
operation
is
required
.
During
the
last
few
degrees
of
the
ratchet
wheel
rotation
the
motor
and
interlock
switches
(
6
)
are
released
and
the
driving
pawl
is
raised
from
the
ratchet
wheel
surface
.
This
allows
the
motor
and
driving
mechanism
to
coast
to
a
natural
stop
expending
all
residual
energy
.
During
the
time
the
springs
are
being
compressed
a
relay
(
6
)
Fig
.
(
6
)
locks
the
closing
power
circuits
open
and
the
relay
will
remain
ener
-
gized
until
the
springs
are
fully
charged
and
the
control
contacts
are
.
re
-
set
.
The
closing
springs
may
be
charged
manually
if
control
voltage
is
lost
.
A
5
/
8
"
ratchet
wrench
can
be
used
to
rotate
the
eccentric
in
a
counter
clockwise
direction
until
the
indicator
reads
"
CHARGED
"
and
the
driving
pawl
no
longer
engages
the
ratchet
wheel
.
The
use
of
the
ratchet
wrench
provides
for
maximum
safety
in
the
event
that
control
power
is
suddenly
restored
without
warning
.
In
this
event
,
the
motor
drive
/
will
take
over
again
and
continues
to
charge
the
springs
.
Ill
Closing
Operation
m
*
Closing
the
breaker
is
accomplished
by
energizing
the
closing
solenoid
or
by
manually
pressing
the
close
button
.
In
either
case
,
the
closing
latch
is
removed
from
the
spring
blocking
location
allowing
the
springs
to
discharge
.
The
energy
of
the
springs
is
applied
to
the
rotation
of
a
cam
(
16
)
Fig
.
(
5
)
that
closes
the
breaker
through
a
simple
linkage
that
remains
trip
free
at
all
times
.
A
monitoring
switch
(
ll
)
Fig
.
(
6
)
on
the
closing
latch
will
start
the
spring
charging
motor
after
it
is
fully
reset
.
Opening
Operation
An
electrical
opening
operation
is
initiated
by
energizing
the
trip
coil
.
This
is
accomplished
either
by
actuating
the
opening
control
switch
on
the
metal
-
clad
unit
or
by
a
combination
of
relays
and
current
devices
used
to
detect
a
fault
on
the
load
side
of
the
breaker
.
By
energizing
the
trip
coil
,
the
trip
plunger
rotates
the
trip
latch
(
j
)
,
Fig
.
(
5
)
J
causing
the
operating
mechanism
linkage
to
collapse
.
The
energy
stored
in
the
opening
springs
is
thus
released
,
opening
the
breaker
.
During
this
operation
,
the
trip
coil
circuit
is
deenergized
,
and
upon
completion
of
the
opening
operation
,
the
operating
mechanism
is
returned
to
its
normal
position
,
ready
for
closing
.
i
II
sm
0
\
5
.
Courtesy of NationalSwitchgear.com

T
-
rvj
.
1
/
I
i
I
i
GEI
-
88761
As
the
breaker
opens
,
the
main
contacts
part
first
,
shunting
the
current
through
the
arcing
contacts
.
An
arc
forms
as
the
arcing
contacts
part
.
See
Pig
.
(
7
)
.
As
the
movable
arcing
contact
(
27
)
is
withdrawn
through
the
slot
or
between
the
arcing
probes
on
the
arc
runner
,
the
upper
end
of
the
arc
is
transferred
to
the
upper
arc
runner
(
4
)
.
To
assist
the
interruption
at
this
point
,
a
stream
of
air
is
emitted
from
the
booster
tube
(
28
)
and
forces
the
arc
onto
the
lower
arc
runner
(
10
)
.
Establish
-
ment
of
the
arc
on
the
runners
automatically
inserts
the
blowout
coils
into
the
circuit
,
introducing
a
magnetic
field
between
the
pole
pieces
which
tends
to
draw
the
arc
away
from
the
arcing
contacts
.
The
inter
-
rupter
contains
one
upper
magnetic
blowout
coil
and
one
lower
blowout
coil
each
individually
connected
in
series
with
its
respective
arc
run
-
ner
.
The
arc
is
forced
outward
along
the
diverging
arc
runners
by
the
magnetic
field
.
At
the
same
time
,
the
arc
is
being
forced
into
the
arc
chute
(
8
)
which
is
composed
of
a
series
of
gradually
interleaving
insulating
fins
.
These
fins
,
which
project
alternately
from
the
two
opposite
inner
sur
-
faces
of
the
chute
,
elongate
the
arc
into
a
gradually
deepening
ser
-
pentine
path
,
so
that
the
electrical
resistance
in
the
path
of
the
arc
is
rapidly
increased
and
the
heat
from
the
arc
is
absorbed
.
The
in
-
creased
resistance
reduces
both
the
magnitude
and
the
phase
angle
of
the
current
,
and
at
an
early
current
-
zero
the
arc
path
is
so
long
and
the
gases
produced
by
the
arc
so
cooled
that
the
arc
cannot
reestablish
itself
,
and
interruption
occurs
.
*
Manual
tripping
follows
the
same
procedure
except
that
instead
of
energizing
the
trip
circuit
,
the
manual
trip
(
ll
)
,
Fig
.
(
2
)
is
used
.
•
Trip
Free
Operation
If
the
trip
coil
circuit
is
energized
while
the
breaker
Is
closing
,
the
trip
plunger
will
force
the
trip
latch
(
8
)
Fig
.
(
5
)
away
from
the
trip
roller
(
9
)
causing
the
mechanism
linkage
to
collapse
and
the
breaker
to
re
-
open
.
The
closing
cam
(
l
6
)
will
complete
its
closing
stroke
and
the
springs
will
re
-
charge
as
in
a
normal
closing
operation
.
1
:
!
;
S
i
V
I
i
&
I
.
'
8
s
:
i
1
;
s
m
;
V
1
1
ADJUSTMENTS
All
adjustments
should
be
checked
during
periodic
inspections
and
whenever
it
becomes
necessary
to
repair
or
replace
parts
that
have
be
-
come
worn
or
defective
while
in
service
.
The
following
adjustments
are
listed
in
the
order
in
which
they
are
to
be
checked
.
First
,
how
-
ever
,
remove
the
breaker
from
the
metal
-
clad
unit
and
remove
the
box
barriers
and
front
cover
.
i
$
$
x
i
vi
"
DO
NOT
WORK
ON
EITHER
THE
BREAKER
OR
MECHANISM
UNLESS
THE
CLOSING
SPRINGS
ARE
BLOCKED
AND
THE
OPENING
SPRINGS
HAVE
BEEN
TRIPPED
OPEN
OR
MECHANICALLY
BLOCKED
.
THIS
MEASURE
IS
REQUIRED
TO
PREVENT
ACCI
-
DENTAL
CLOSING
OR
TRIPPING
.
"
i
$
3
a
ft
%
m
%
6
4
Courtesy of NationalSwitchgear.com

GEI
-
88761
5
Primary
Contact
Wipe
When
the
breaker
is
closed
,
as
shown
in
Fig
.
(
8
)
,
the
stationary
pri
-
mary
contacts
(
.
1
)
should
rise
5
/
16
"
-
f
-
0
—
l
/
l
6
.
Before
checking
this
dimension
be
sure
the
mechanism
is
re
-
set
so
that
the
prop
pin
(
13
)
Fig
*
(
5
)
is
resting
on
the
prop
.
To
obtain
the
proper
contact
adjust
-
ment
,
open
the
breaker
and
,
referring
to
Fig
.
(
9
)
>
loosen
the
check
nut
(
4
)
.
and
turn
the
adjusting
nut
(
3
)
.
Screwing
up
on
the
adjusting
nut
will
decrease
the
primary
contact
wipe
,
down
will
increase
it
.
Tighten
the
check
nut
,
close
the
breaker
and
recheck
the
wipe
.
With
the
primary
contact
wipe
correctly
adjusted
,
the
clearance
between
the
and
the
buffer
block
should
be
l
/
l
6
"
or
greater
(
as
)
when
the
breaker
is
fully
closed
.
m
1
!
contact
arm
shown
in
Fig
B
Arcing
Contact
Wipe
Refer
to
Fig
.
(
8
)
.
Close
the
breaker
until
the
arcing
contacts
just
touch
.
This
can
be
determined
with
the
use
of
a
circuit
continuity
tester
such
as
a
light
indicator
or
bell
set
.
In
this
position
,
the
gap
between
the
stationary
primary
contacts
(
1
)
and
the
movable
primary
contact
(
2
)
should
be
5
/
l
6
"
or
greater
.
This
setting
has
been
made
in
the
factory
and
no
adjustment
is
provided
.
A
wipe
of
less
than
5
/
16
"
is
usually
an
indication
that
the
arcing
contacts
need
to
be
replaced
.
When
making
this
check
,
also
see
that
the
movable
arcing
contact
(
5
)
passes
between
the
slots
or
the
arcing
probes
on
the
upper
arc
runner
with
-
out
touching
,
whichever
is
applicable
.
Primary
Contact
Gap
IP
Refer
to
Fig
.
(
9
)
.
With
the
breaker
closed
,
press
the
manual
trip
button
allowing
the
breaker
to
trip
open
normally
.
Do
not
force
the
contacts
open
wider
by
hand
.
The
gap
between
the
stationary
primary
contacts
(
5
)
and
the
movable
primary
contact
(
6
)
should
be
3
-
13
/
16
"
+
1
/
8
"
—
3
/
16
"
.
To
change
this
gap
,
loosen
the
check
nut
(
17
)
*
Fig
*
(
5
)
(
18
)
on
stud
(
19
)
.
Screwing
the
adjusting
and
turn
the
adjusting
nut
nut
down
will
decrease
the
primary
contact
gap
.
Tighten
the
check
nut
and
remeasure
the
contact
gap
(
close
and
trip
the
breaker
before
check
-
ing
the
measurement
)
.
Trip
Latch
Wipe
Refer
to
Fig
.
(
5
)
*
The
wipe
of
the
trip
latch
(
8
)
on
the
trip
roller
(
9
)
should
be
from
3
/
l
6
"
to
1
/
4
"
.
This
can
be
measured
by
putting
a
film
of
grease
on
the
latch
(
8
)
,
closing
the
breaker
part
way
,
and
tripping
.
The
mechanism
has
the
proper
trip
latch
wipe
when
the
latch
rests
against
the
stop
pin
(
23
)
.
No
adjustment
is
provided
and
a
vis
-
ual
inspection
is
usually
all
that
is
required
.
If
this
setting
is
not
correct
,
look
for
insufficient
travel
of
the
trip
shaft
(
7
)
.
WHEN
WORKING
ON
THE
MECHANISM
IN
THE
CLOSED
POSITION
,
KEEP
FINGERS
CLEAR
OF
THE
LINKAGE
,
AS
ACCIDENTAL
TRIPPING
CAN
CAUSE
SEVERE
INJURY
.
!
isi
7
s
Courtesy of NationalSwitchgear.com

GEI
-
88761
Trip
Latch
Clearance
Refer
to
Fig
.
(
5
)
.
With
the
breaker
in
the
tripped
position
and
the
closing
springs
charged
,
check
the
clearance
between
the
trip
latch
(
8
)
(
9
)
.
It
should
measure
1
/
32
"
to
l
/
l
6
"
.
and
the
trip
roller
Prop
Clearance
Refer
to
Fig
.
(
5
)
.
With
the
breaker
closed
as
far
as
possible
,
that
is
,
with
the
springs
blocked
and
the
cam
(
16
)
rotated
so
that
the
prop
pin
(
13
)
is
at
its
maximum
height
over
the
prop
(
l
4
K
tween
the
prop
and
prop
pin
should
be
l
/
l
6
"
to
5
/
32
.
No
adjustment
is
provided
and
a
visual
inspection
is
usually
all
that
is
required
.
Release
Latch
Wipe
Refer
to
Fig
.
(
6
)
.
The
wipe
between
the
release
latch
(
3
)
and
roller
(
2
)
should
be
3
/
16
"
to
1
/
4
"
.
If
re
-
setting
is
required
,
loosen
,
set
,
and
re
-
tighten
adjustment
nut
and
screw
(
4
)
.
Release
Latch
Monitoring
Switch
the
clearance
be
-
The
release
latch
must
be
fully
re
-
set
and
the
monitoring
switch
opera
-
ted
before
the
motor
will
start
.
The
switch
should
be
wiped
by
the
striker
so
that
the
clearance
between
the
striker
and
switch
mounting
bracket
(
20
)
Fig
.
(
6
)
is
1
/
32
"
or
less
.
To
obtain
this
adjustment
bend
the
switch
striker
.
Be
s
re
the
latch
is
fully
re
-
set
before
making
any
adjustments
.
Motor
and
Relay
Switches
g
.
(
6
)
(
about
and
rotate
and
support
With
the
closing
springs
blocked
rotate
the
switch
cam
(
l
)
Fi
until
the
switch
striker
(
8
}
has
traveled
the
maximum
amount
180
degrees
rotation
of
cam
)
.
Loosen
mounting
bolt
(
14
)
switch
support
(
15
)
until
the
gap
between
the
striker
(
8
)
(
15
)
is
1
/
32
"
or
less
.
Interlock
Switch
Wipe
Refer
to
Fig
.
(
10
)
.
Rotate
the
Interlock
shaft
(
l
)
manually
clockwise
to
release
the
interlock
switch
arm
(
2
)
.
The
point
at
which
the
con
-
tacts
make
can
be
determined
with
a
circuit
continuity
tester
sucn
as
a
light
indicator
or
bell
set
.
To
obtain
adjustment
on
the
interlock
(
3
)
,
bend
the
interlock
switch
arm
(
2
)
until
there
is
a
maximum
of
1
/
32
"
clearance
to
the
switch
mounting
plate
(
4
)
.
SI
I
3
switch
I
,
r
£
Auxiliary
Switch
§
The
auxiliary
switch
(
9
)
,
Fig
.
(
ll
)
Is
mounted
on
the
left
side
of
the
operating
mechanism
.
The
shaft
of
the
position
indicator
(
8
)
operates
the
auxiliary
switch
shaft
which
opens
and
closes
‘
the
"
a
"
and
"
b
"
con
-
tacts
.
The
"
a
"
contacts
are
open
when
the
breaker
is
open
and
the
"
b
"
contacts
are
open
when
the
breaker
is
closed
.
The
"
a
"
contacts
should
close
when
the
breaker
primary
contact
gap
is
a
minimum
of
1
"
.
The
"
b
"
contacts
need
only
to
be
checked
to
see
that
they
are
open
when
the
breaker
Is
closed
.
No
adjustment
is
provided
and
a
visual
Inspection
is
usually
all
that
is
required
.
I
%
%
I
1
i
*
3
n
n
.
8
I
I
Courtesy of NationalSwitchgear.com

GEI
-
88761
i
;
Driving
Pawl
Adjustment
'
®
The
driving
pawl
(
5
)
Pig
.
(
4
)
must
advance
the
ratchet
wheel
(
3
)
Pig
.
(
3
)
sufficiently
on
each
stroke
to
allow
the
latching
pawls
(
l
)
to
fall
into
the
ratchet
teeth
.
This
should
be
checked
with
the
maximum
closing
spring
load
against
the
driving
members
.
With
the
mechanism
unblocked
,
hand
charge
the
closing
springs
with
the
manual
charging
wrench
until
they
are
slightly
more
than
half
charged
.
Slowly
rotate
the
charging
wrench
until
the
driving
pawl
(
5
)
Fig
.
4
has
traveled
through
its
return
stroke
and
check
the
maximum
clearance
between
the
pawl
and
the
ratchet
tooth
.
Rotate
the
charging
wrench
until
the
driv
-
ing
pawl
has
advanced
the
ratched
tooth
to
its
maximum
travel
.
Now
Jtheck
the
clearance
between
the
ratchet
tooth
and
the
latching
pawl
(
l
)
Pig
.
(
3
)
.
The
clearance
should
be
approximately
equal
for
both
the
driving
and
latching
pawls
and
not
less
than
.
015
"
in
either
case
.
If
adjustment
is
required
for
either
pawl
the
springs
must
first
be
fully
charged
and
blocked
.
Loosen
seven
motor
support
bo
]
'
.
s
(
1
)
Pig
.
(
15
)
and
move
entire
motor
assembly
to
the
rear
if
the
clearance
is
under
,
the
minimum
at
the
latching
pawls
,
and
to
the
front
if
the
clear
-
ance
is
under
the
minimum
at
the
driving
pawl
.
Move
the
motor
assembly
approximately
twice
the
dimensional
increase
required
at
the
pawl
.
Be
certain
the
motor
assembly
is
moved
straight
forward
or
rearward
and
tighten
the
one
bolt
on
the
right
side
of
the
mounting
frorae
first
to
assure
proper
alignment
.
After
tightening
the
remaining
bolts
the
springs
should
be
released
and
the
clearance
again
checked
as
described
^
above
.
AUXILIARY
DEVICES
Latch
Checking
Switch
Refer
to
Pig
.
(
12
)
.
Rotate
the
trip
latch
(
4
)
clockwise
(
looking
at
the
left
side
of
the
mechanism
)
by
pressing
the
manual
trip
lever
to
open
the
latch
checking
switch
operating
arm
(
3
)
.
Allow
the
trip
latch
to
reset
slowly
and
determine
the
point
at
which
the
contacts
make
by
using
a
circuit
continuity
tester
,
such
as
a
light
indicator
or
bell
set
.
The
contacts
of
the
latch
checking
switch
should
Just
make
when
the
gap
between
the
trip
latch
(
4
)
and
the
stop
pin
(
5
)
located
on
the
crank
(
7
)
is
l
/
l
6
"
.
There
should
be
a
minimum
of
1
/
64
"
between
the
operating
arm
(
3
)
Pig
.
(
12
)
and
the
switch
support
(
1
)
.
To
obtain
_
adjustment
of
the
latch
checking
switch
(
2
)
bend
the
latch
checking
©
switch
operating
arm
(
3
)
.
Plunger
Interlock
Refer
to
Pig
.
(
13
)
.
With
the
breaker
in
the
closed
position
,
the
vert
-
ical
distance
"
A
"
from
the
top
of
the
Interlock
bolt
(
l
)
to
the
bottom
of
the
elevating
bar
(
3
)
should
be
16
-
21
/
32
"
plus
or
minus
1
/
16
"
.
To
change
this
adjustment
,
add
or
remove
washers
(
2
)
.
ajjg
9
Courtesy of NationalSwitchgear.com

GEI
-
88761
Spring
Release
Interlock
A
spring
release
interlock
shown
in
Pig
.
(
14
)
will
assure
that
the
breaker
contacts
are
open
and
the
closing
springs
discharged
when
inserting
or
removing
the
breaker
from
the
metal
-
clad
unit
.
If
the
closing
springs
are
charged
and
/
or
the
breaker
is
in
the
closed
position
when
being
inserted
or
withdrawn
from
the
metal
-
clad
unit
,
the
release
interlock
will
trip
the
breaker
open
and
hold
the
mechan
-
ism
in
a
trip
-
free
position
vrhile
discharging
the
closing
springs
.
Auxiliary
Fuses
Refer
to
Fig
.
(
15
)
.
On
breakers
with
"
C
"
suffix
,
a
set
of
protect
-
ing
fuses
(
4
)
are
mounted
on
the
front
of
the
breaker
.
These
fuses
will
be
the
primary
protection
devices
for
the
closing
control
cir
-
cuits
oh
those
breakers
that
are
used
in
metal
-
clad
units
designed
for
solenoid
operated
breakers
.
Inspection
and
Test
1
.
For
ease
in
reviewing
the
adjustments
,
the
following
are
recapitulated
:
a
.
Primary
contact
wipe
:
5
/
16
"
-
j
-
0
—
l
/
l
6
"
.
b
.
Arcing
contact
wipe
:
5
/
16
"
or
greater
(
gap
at
primary
contacts
)
.
c
.
Primary
contact
gap
:
3
-
13
/
16
"
+
1
/
8
"
—
3
/
16
"
.
d
.
Trip
latch
wipe
:
3
/
16
"
to
1
/
4
"
with
trip
latch
resting
against
stop
pin
.
e
.
Trip
latch
clearance
:
1
/
32
"
to
l
/
l
6
"
.
f
.
Prop
clearance
:
l
/
l
6
"
to
5
/
32
"
.
1
g
.
Release
latch
wipe
:
3
/
16
"
to
l
/
4
"
.
h
.
Release
latch
monitoring
switch
:
maximum
clearance
1
/
32
"
.
i
.
Motor
and
relay
switch
:
maximum
clearance
1
/
32
"
.
j
.
Interlock
switch
:
maximum
clearance
1
/
32
"
.
k
.
Auxiliary
switch
"
a
"
contacts
close
when
breaker
primary
contact
gap
is
1
"
or
greater
.
l
.
Driving
and
Latching
Pawl
:
minimum
clearance
to
ratchet
teeth
.
015
"
.
m
.
Latch
checking
switch
contacts
make
when
the
gap
between
the
trip
latch
and
the
stop
pin
is
1
/
16
"
.
n
.
Plunger
Interlock
:
16
-
21
/
32
"
plus
or
minus
l
/
l
6
"
with
breaker
closed
.
2
.
Check
all
nuts
,
washers
,
bolts
,
cotter
pins
,
and
terminal
connec
-
tions
for
tightness
.
3
.
Inspect
all
wiring
to
make
sure
that
no
damage
has
resulted
during
installation
,
and
test
for
possible
grounds
or
short
circuits
.
4
.
See
that
all
bearing
surfaces
of
the
mechanism
have
been
lubricated
.
Refer
to
the
section
on
LUBRICATION
.
5
.
Operate
the
breaker
slowly
with
the
manual
charging
wrench
and
note
that
there
is
no
excessive
binding
or
friction
and
that
the
breaker
can
be
moved
to
the
fully
opened
and
fully
closed
positions
.
10
Courtesy of NationalSwitchgear.com

GEI
-
88761
6
.
See
that
any
place
where
the
surface
of
the
paint
has
been
damaged
is
repainted
immediately
.
7
.
Check
the
trip
coil
plunger
and
the
release
coil
plunger
to
see
that
they
move
freely
.
Opening
and
Closing
Speeds
n
The
closing
speed
of
the
arcing
contact
of
the
breaker
should
be
a
mini
-
mum
of
11
feet
per
second
.
This
represents
the
average
speed
of
the
mov
-
able
arcing
contact
from
a
point
1
"
before
the
tip
is
tangent
to
the
lower
surface
of
the
slot
or
probes
on
the
upper
arc
runner
to
the
tan
-
gent
position
.
The
opening
speed
of
the
arcing
contact
should
be
a
minimum
of
12
feet
per
second
.
This
represents
the
average
speed
over
3
"
from
the
point
when
the
tip
on
the
movable
contact
is
tangent
to
the
lower
surface
of
the
slot
or
probes
on
the
upper
runner
.
Control
Power
Check
m
After
the
mechanism
has
been
closed
and
opened
slowly
several
times
with
the
maintenance
closing
wrench
and
the
mechanism
adjustments
are
checked
as
described
,
the
operating
voltages
should
be
checked
at
the
release
coil
,
trip
coil
,
and
motor
terminals
.
For
electrical
operation
of
the
mechanism
,
the
control
power
may
be
either
an
alternating
or
di
-
rect
current
source
.
The
operating
ranges
for
the
closing
and
tripping
voltages
are
given
on
the
breaker
nameplate
.
The
following
ranges
are
standard
:
m
Closing
Range
Nominal
Voltage
Tripping
Range
Min
.
Max
.Min
.
Max
.
60
v
d
-
c
125
v
d
-
c
l
40
v
d
-
c
250
v
d
-
c
280
v
d
-
c
125
v
a
-
c
250
v
a
-
c
34
28
48
v
d
-
c
llOv
d
-
c
125
v
d
-
c
220
v
d
-
c
250
v
d
-
c
115
v
a
-
c
230
v
a
-
c
50
v
d
-
c
115
v
d
-
c
130
v
d
-
c
230
v
d
-
c
260
V
d
-
c
125
v
a
-
c
250
v
a
-
c
80
60
90
70
160
120
.
180
140
95 95
-
'
,
V
:
190
190
80
S
If
the
closed
circuit
voltage
at
the
terminals
of
the
coil
or
motor
does
not
fall
in
the
specified
range
,
check
the
voltage
at
the
source
of
power
and
line
drop
between
the
power
source
and
breaker
.
When
two
or
more
breakers
operating
fr
-
m
the
same
control
power
source
are
required
to
close
simultaneous
]
„
,
the
closed
circuit
voltage
at
the
Closing
coil
or
motor
of
each
breaker
must
pall
within
the
specified
limits
.
11
Courtesy of NationalSwitchgear.com

GEI
-
88761
’
!
Electrical
closing
or
opening
is
accomplished
by
merely
energizing
the
closing
or
trip
coil
circuit
.
Control
switches
are
provided
for
this
purpose
on
the
metal
-
clad
unit
.
It
is
also
possible
to
trip
or
close
the
breaker
manually
by
pressing
the
manual
trip
lever
(
11
)
Fig
.
(
2
)
or
the
manual
close
button
(
7
)
.
Before
the
breaker
is
finally
raised
into
position
in
the
metal
-
clad
unit
,
rub
a
small
amount
of
G
-
E
contact
lubricant
D
50
H
47
on
the
sil
-
vered
portion
of
the
breaker
studs
to
form
a
thin
coating
for
con
-
tacting
purposes
.
GENERAL
MAINTENANCE
Dependable
service
and
safer
power
equipment
are
contingent
upon
the
unfailing
performance
of
the
power
circuit
breaker
.
To
maintain
such
service
,
it
is
recommended
that
a
definite
inspection
and
maintenance
schedule
be
set
up
and
followed
,
as
serious
shutdowns
can
often
be
avoided
by
locating
potential
sources
of
trouble
in
an
early
stage
.
A
periodic
lubrication
of
parts
subject
to
wear
is
also
vitally
im
-
portant
for
the
successful
operation
of
the
breaker
.
BEFORE
ANY
MAINTENANCE
WORK
IS
PERFORMED
,
MAKE
CERTAIN
THAT
ALL
CON
-
TROL
CIRCUITS
ARE
OPENED
AND
THAT
THE
BREAKER
IS
REMOVED
FROM
THE
METAL
-
CLAD
UNIT
.
DO
NOT
WORK
ON
THE
BREAKER
OR
MECHANISM
WHILE
IN
THE
CLOSED
POSITION
UNLESS
THE
PROP
AND
TRIP
LATCH
HAVE
BEEN
SECURELY
WIRED
OR
BLOCKED
TO
PREVENT
ACCIDENTAL
TRIPPING
.
DO
NOT
WORK
ON
THE
BREAKER
OR
MECHANISM
WHILE
THE
SPRINGS
ARE
CHARGED
UNLESS
THEY
ARE
SECURED
IN
THAT
POSITION
BY
THE
MAINTENANCE
SPRING
BLOCKING
DEVICE
.
Periodic
Inspection
The
frequency
of
periodic
inspection
should
be
determined
by
each
operating
company
on
the
basis
of
the
number
of
operations
(
including
switching
)
,
the
magnitude
of
currents
interrupted
,
and
any
unusual
operations
which
occur
from
time
to
time
.
Operating
experience
will
soon
establish
a
maintenance
schedule
which
will
give
assurance
of
proper
breaker
condition
.
On
installations
where
a
combination
of
fault
duty
and
repetitive
operation
is
encountered
,
an
inspection
is
recommended
after
any
severe
fault
operation
.
The
following
instruc
-
tions
list
the
main
points
to
be
included
in
an
inspection
and
,
a
num
-
ber
of
general
recommendations
.
Arc
Chutes
4
f
3
$
•
j
1
%
I
It
is
not
necessary
to
inspect
the
arc
chutes
unless
there
is
evidence
of
damage
or
if
the
arc
chutes
are
removed
for
any
reason
.
When
in
-
specting
an
arc
chute
,
it
should
be
disassembled
and
the
following
points
noted
:
1
.
Scale
formed
over
the
surface
of
the
arc
chute
must
not
be
removed
,
but
loose
particles
collected
in
the
chute
should
be
blown
out
.
2
.
Cracks
which
have
formed
in
the
fins
of
the
arc
chute
are
to
be
ex
-
pected
in
ceramic
materials
of
this
type
when
subjected
to
the
severe
heat
of
an
arc
.
These
cracks
do
not
interfere
with
the
operation
of
the
device
in
any
way
and
should
be
disregarded
.
•
-
!
:
!
*
a
S
;
I
j
$
'
I
.
"
3
t
12
-
i
3
.
3
Courtesy of NationalSwitchgear.com

I
I
GEI
-
88761
3
.
If
the
arc
chute
has
suffered
any
mechanical
injury
due
to
dropping
or
accidental
striking
,
resulting
in
the
actual
breaking
off
of
fins
,
replacement
of
the
chute
will
be
necessary
.
Small
broken
corners
on
the
exhaust
end
of
the
chute
will
not
interfere
with
its
per
-
formance
and
can
also
be
disregarded
.
4
.
The
plastisol
flexible
covering
for
the
pole
pieces
(
17
&
18
)
Fig
.
(
16
)
and
the
upper
mounting
support
(
10
)
Fig
.
(
16
)
should
be
in
-
spected
for
breaks
in
the
insulation
.
If
there
are
holes
or
breaks
in
the
insulation
they
should
be
repaired
or
the
part
replaced
.
Breaker
Contacts
is
By
removing
the
box
barrier
the
movable
and
stationary
primary
contacts
and
the
movable
arcing
contacts
can
be
inspected
.
The
stationary
arc
-
ing
contacts
can
be
inspected
only
after
removing
the
arc
chute
assem
-
bly
,
as
explained
under
REPAIR
AND
REPLACEMENT
.
If
the
contacts
are
burned
or
pitted
,
they
should
be
made
smooth
with
a
fine
file
.
if
After
completing
inspection
of
the
contacts
,
check
the
contact
adjust
-
ments
as
specified
under
ADJUSTMENTS
.
Mechanism
A
careful
inspection
should
be
made
to
check
for
loose
nuts
or
bolts
and
broken
retaining
rings
.
All
cam
,
roller
,
and
latch
surfaces
should
be
inspected
for
any
evidence
of
damage
or
excessive
wear
.
Lubricate
the
mechanism
as
outlined
below
,
then
,
using
the
manual
charging
wrench
,
open
and
close
the
breaker
several
times
to
make
certain
that
the
mechanism
operates
freely
throughout
its
entire
stroke
.
Check
the
mechanism
adjustments
as
specified
under
ADJUSTMENTS
.
Check
all
terminal
connections
.
i
|
|
®
Bushings
and
Insulation
The
surface
of
the
bushings
should
be
kept
clean
and
unraarred
to
pre
-
t
vent
moisture
absorption
.
If
the
Insulation
surface
should
become
damaged
,
it
should
be
sanded
and
cleaned
,
and
should
be
refinished
with
either
clear
varnish
or
clear
resin
.
Allow
to
dry
smooth
and
hard
.
!
All
other
insulation
parts
on
the
breaker
should
be
kept
clean
and
dry
.
Smoke
or
dust
collected
between
inspection
periods
should
be
wiped
off
,
and
If
dampness
is
apparent
,
heaters
should
be
installed
to
insure
dry
-
ness
.
m
Insulation
Test
When
Insulation
has
been
repaired
or
replaced
,
or
when
breaker
has
been
stored
under
adverse
conditions
,
it
Is
recommended
that
the
in
-
sulation
be
checked
before
the
breaker
is
placed
in
service
.
A
stand
-
ard
60
cycle
high
potential
test
at
14
,
000
volts
RMS
will
normally
in
-
dicate
whether
the
breaker
is
satisfactory
for
service
.
With
the
breaker
contacts
in
the
fully
open
position
,
apply
the
high
potential
to
each
terminal
of
the
breaker
individually
for
one
minute
with
all
other
terminals
and
the
breaker
frame
grounded
.
.
After
high
potential
Sgsg
*
.
.
rtv
13
Courtesy of NationalSwitchgear.com

GEI
-
88761
tests
are
made
;
on
organic
insulating
materials
,
these
materials
Mould
be
inspected
for
visible
leakage
current
paths
,
and
necessary
action
must
be
taken
to
replace
insulation
that
may
have
been
affected
by
moisture
absorp
-
tion
.
If
the
breaker
secondary
wiring
is
to
be
given
a
hi
-
potential
test
at
1500
volts
,
remove
both
of
the
motor
leads
from
the
terminal
board
.
Failure
to
disconnect
the
motor
from
the
circuit
may
cause
damage
to
the
winding
in
-
sulation
.
LUBRICATION
In
order
to
maintain
reliable
operation
,
it
is
important
that
all
circuit
breakers
be
properly
lubricated
at
all
times
.
Most
of
the
bearings
and
rolling
surfaces
utilize
a
new
type
of
dry
lubrication
that
will
require
no
maintenance
and
will
last
the
life
of
the
equipment
.
Only
few
bearings
and
surfaces
listed
in
the
chart
Fig
.
(
20
)
require
lubrication
.
These
have
been
properly
lubricated
,
during
assembly
at
the
factory
,
using
the
finest
grades
of
lubricants
available
.
However
,
even
the
finest
oils
and
greases
have
a
tendency
to
oxidize
with
age
,
as
evidenced
by
hardening
and
darken
-
ing
in
color
.
Elimination
of
the
hardened
lubricant
is
essential
for
the
proper
operation
of
circuit
breakers
.
Also
frequent
operation
of
the
breaker
causes
the
lubricant
to
be
forced
out
from
between
the
bearing
surfaces
.
A
simple
lubrication
will
often
clear
up
minor
disturbances
which
might
be
mistaken
for
more
serious
trouble
.
A
definite
lubrication
schedule
should
be
set
up
taking
into
consideration
the
frequency
of
operation
of
the
breaker
and
local
conditions
.
Until
such
a
schedule
is
worked
out
,
the
breaker
should
be
lubricated
at
each
periodic
inspection
and
also
whenever
it
is
overhauled
,
in
accordance
with
the
lubrication
chart
,
Fig
.
(
20
)
.
It
Is
also
recommended
that
all
circuit
breakers
be
operated
at
regular
intervals
to
insure
the
user
that
the
equipment
is
operating
freely
.
The
lubrication
chart
,
Fig
.
(
20
)
is
divided
Into
two
methods
of
lubrication
.
The
first
method
outlines
the
maintenance
lubrication
which
should
be
per
-
formed
at
the
time
of
periodic
maintenance
,
and
requires
no
disassembly
.
The
second
method
outlines
a
lubrication
procedure
similar
to
that
performed
on
the
breaker
at
the
factory
,
but
should
be
used
only
in
case
of
a
general
overhaul
or
disassembly
for
other
reasons
,
or
if
the
operation
of
the
break
-
dr
becomes
slower
.
General
Electric
Lubricants
D
50
H
15
and
D
50
H
47
are
available
in
1
/
4
#
col
-
lapsible
tubes
.
It
is
so
packaged
to
insure
cleanliness
and
to
prevent
oxidation
.
Hfe
Method
of
Cleaning
Bearings
Whenever
cleaning
is
required
,
as
indicated
in
the
lubrication
chart
,
the
following
procedures
are
recommended
:
Sleeve
Bearings
The
sleeve
bearings
used
throughout
the
linkage
utilize
Teflon
surfaces
and
do
not
require
lubrication
.
After
a
number
of
operations
,
the
surface
will
acquire
a
thin
black
film
.
Do
not
remove
this
film
unless
there
is
evi
-
dence
of
outside
contaminates
,
such
as
dry
or
hardened
grease
.
If
contami
-
.
V
v
Hi
14
§
Courtesy of NationalSwitchgear.com

GEI
-
88761
nants
are
present
they
should
be
removed
by
immersing
the
link
and
bear
-
ing
in
clean
petroleum
solvent
or
similar
cleaner
and
using
a
stiff
brush
.
Do
not
remove
the
bearings
from
the
links
.
DO
NOT
USE
CARBON
TETRACHLORIDE
.
The
hinge
of
the
primary
contact
arm
(
24
)
Pig
.
(
7
)
should
be
disassembled
,
cleaned
,
and
lubricated
with
G
-
E
D
50
H
47
lubricant
at
general
overhaul
per
-
iods
.
The
main
shaft
bearings
(
24
)
Pig
.
(
5
)
and
the
driving
pawl
lever
bearing
should
be
removed
,
cleaned
,
and
lubricated
with
G
-
E
D
50
H
15
lubricant
at
general
overhaul
periods
.
Roller
&
Needle
Bearings
The
cam
follower
bearings
(
6
)
Pig
.
(
5
)
,
latch
roller
bearing
(
9
)
,
and
cam
shaft
bearings
(
25
)
Fig
.
(
5
)
should
be
first
removed
from
the
mechanism
and
the
inner
race
disassembled
.
They
should
then
be
placed
in
a
container
of
clean
petroleum
solvent
or
similar
cleaner
.
DO
NOT
USE
CARBON
TETRACHLOR
-
IDE
.
If
the
grease
in
the
bearings
has
become
badly
oxidized
,
it
may
be
necessary
to
use
alcohol
(
type
used
for
thinning
shellac
)
to
remove
it
.
Ordinarily
,
by
agitating
the
bearings
in
the
cleaning
solution
,
and
using
a
stiff
brush
to
remove
the
solid
particles
,
the
bearings
can
be
satis
-
factorily
cleaned
.
Do
not
handle
the
bearings
with
bare
hands
as
deposits
from
the
skin
onto
the
bearings
are
inductive
to
corrosion
.
If
the
bear
-
ings
are
touched
,
the
contamination
can
be
removed
by
washing
in
alcohol
.
After
the
bearings
have
been
thoroughly
cleaned
,
spin
them
in
clean
new
light
machine
oil
until
the
cleaner
or
solvent
is
entirely
removed
.
Allow
this
oil
to
drain
off
and
then
repack
them
immediately
with
G
-
E
lubricant
D
50
H
15
being
sure
all
metal
parts
are
greased
.
The
removable
seals
should
then
be
replaced
.
NOTE
:
If
it
becomes
necessary
to
clean
the
bearings
in
alcohol
(
shellac
thinner
)
,
be
sure
the
alcohol
is
perfectly
clean
,
and
do
not
allow
the
bearings
to
remain
in
the
alcohol
more
than
a
few
hours
.
If
it
is
desir
-
able
to
leave
the
bearings
in
the
alcohol
for
a
longer
time
,
an
inhibited
alcohol
such
as
is
used
for
anti
-
freeze
should
be
used
.
Even
then
the
bearings
should
be
removed
from
the
alcohol
within
twenty
-
four
hours
.
Esso
Anti
-
Freeze
and
Du
Pont
Zerone
are
satisfactory
for
this
purpose
.
Precautions
againat
the
toxic
effects
of
the
alcohol
must
be
exercised
by
wearing
rubber
gloves
and
by
using
the
alcohol
in
a
well
ventilated
room
;
excessive
exposure
to
the
fumes
is
sometimes
unpleasant
to
personnel
.
Washing
the
bearings
in
the
light
oil
and
draining
should
follow
immediate
-
ly
,
then
apply
the
lubricant
.
Bearings
that
are
pressed
into
the
frame
or
other
members
such
as
the
ec
-
centric
drive
bearings
(
7
)
Fig
.
(
15
)
should
not
be
removed
.
After
remov
-
ing
the
shaft
and
inner
race
the
bearing
can
usually
be
cleaned
satisfac
-
torily
with
petroleum
solvent
or
a
similar
cleaner
and
a
stiff
brush
.
Follow
the
procedure
outlined
above
using
a
light
machine
oil
and
G
-
E
lubricant
D
50
H
15
before
reassembling
the
inner
race
and
shaft
.
Rolling
Surfaces
m
11
m
mm
)
A
number
of
rolling
and
rubbing
surfaces
in
the
mechanism
have
been
lubri
-
cated
with
a
baked
-
on
,
dry
,
molybdenum
disulfide
coating
.
This
requires
no
maintenance
and
should
last
the
life
of
the
breaker
.
;
15
Courtesy of NationalSwitchgear.com

GEI
-
88761
RECOMMENDED
MAINTENANCE
FOR
MAGNE
-
BLAST
BREAKERS
APPLIED
TO
REPETITIVE
SWITCHING
DUTY
1
.
Magne
-
blast
breakers
applied
to
repetitive
operation
such
as
switching
arc
furnaces
and
motors
should
be
serviced
and
maintained
according
to
the
following
schedule
:
A
.
Every
2000
Operations
,
or
Every
Six
Months
-
Whichever
Comes
First
1
.
Remove
the
box
barriers
.
2
.
Wipe
all
insulating
parts
clean
of
smoke
deposit
and
dust
,
with
a
clean
dry
cloth
,
Including
the
bushings
,
and
the
inside
of
the
box
barriers
.
3
.
All
areas
In
the
throat
area
of
the
arc
chute
should
be
thoroughly
cleaned
by
using
sandpaper
.
This
cleaning
should
be
performed
any
time
the
arc
chute
Is
removed
.
The
arc
chute
fins
should
not
be
cleaned
.
Whenever
the
arc
chute
is
removed
,
loose
dust
and
dirt
should
be
blown
out
before
replacing
arc
chutes
.
4
.
Primary
Contacts
-
Inspect
the
condition
of
the
stationary
con
-
tact
fingers
and
movable
contact
blocks
.
Badly
pitted
or
burned
contacts
should
be
replaced
.
(
Note
:
Burned
primary
contacts
in
-
dicate
the
probable
need
for
arcing
contact
replacement
)
.
If
the
contact
surfaces
are
only
roughened
or
galled
,
they
should
be
smoothed
with
crocus
cloth
or
draw
filed
.
After
contact
dressing
the
primary
contacts
should
be
greased
lightly
with
D
50
H
47
.
5
.
Arcing
Contacts
-
When
the
arcing
contact
wipe
is
less
than
the
minimum
specified
under
ADJUSTMENTS
,
the
contacts
should
be
re
-
placed
.
The
contacts
should
be
inspected
for
uneven
wear
and
/
or
damage
using
a
mirror
to
Inspect
the
stationary
contacts
.
Nor
-
mally
it
will
not
be
necessary
to
remove
the
arc
chutes
for
this
2000
operation
servicing
unless
inadequate
wipe
or
contact
condi
-
tion
indicate
a
need
for
replacement
.
When
the
arc
chutes
are
removed
,
the
contact
braids
,
coil
protectors
,
and
other
parts
subject
to
arcing
should
be
checked
for
possible
cleaning
or
re
-
placement
.
Do
not
grease
the
arcing
contacts
under
any
circum
-
stances
.
6
.
Check
the
breaker
and
mechanism
adjustments
as
summarized
under
INSPECTION
AND
TEST
.
The
necessary
readjustments
should
be
made
as
described
under
ADJUSTMENTS
.
7
.
The
breaker
and
operating
mechanism
should
be
carefully
inspected
.
for
loose
nuts
,
bolts
,
retaining
rings
,
etc
.
,
all
cam
,
latch
and
roller
surfaces
should
be
Inspected
for
damage
or
excessive
wear
.
The
buffer
blocks
and
their
retainers
on
the
bottom
of
tne
sta
-
tionary
contact
support
should
be
inspected
for
possible
need
of
replacement
.
i
*
"
.
16
Courtesy of NationalSwitchgear.com

GEI
-
88761
8
.
The
contacts
of
the
control
relay
should
be
inspected
for
wear
and
cleaned
if
necessary
.
Lubricate
the
breaker
operating
mechanism
in
accordance
with
the
table
under
LUBRICATION
.
H
9
.
10
.
Inspect
all
wiring
for
tightness
of
connections
and
possible
dam
-
age
to
insulation
.
11
.
After
the
breaker
has
been
serviced
,
it
should
be
slowly
closed
and
opened
,
as
described
in
INSTALLATION
,
to
be
sure
there
Is
no
binding
or
friction
and
that
the
breaker
contacts
can
move
to
the
fully
opened
and
fully
closed
postlions
.
Its
electrical
operation
should
then
be
checked
using
either
the
test
cabinet
or
the
test
couplers
.
B
.
After
Every
10
,
000
Operations
m
1
.
In
addition
to
the
servicing
done
each
2
,
000
operations
,
the
arc
chutes
should
be
removed
from
the
breaker
and
disassembled
to
permit
a
detailed
Inspection
of
insulation
,
blow
-
out
coils
,
arc
runners
and
assemblies
which
can
become
contaminated
by
arc
pro
-
ducts
.
2
.
The
blow
-
out
coils
should
be
carefully
examined
and
if
the
in
-
sulation
has
been
cracked
,
shrunk
or
eroded
from
arc
action
and
heat
so
that
the
turns
of
the
coils
are
not
fully
insulated
from
each
other
,
the
coils
should
be
replaced
.
All
connections
should
be
checked
for
tightness
.
II
3
.
The
arc
runners
should
be
inspected
and
replaced
when
any
part
of
their
area
has
been
reduced
to
25
$
of
the
original
metal
thickness
as
a
result
of
arc
erosion
.
4
.
Check
the
stationary
arc
contacts
to
assure
that
the
arcing
con
-
tacts
are
in
good
condition
and
that
their
connections
are
tight
.
Insulating
material
that
is
carbonized
and
cannot
be
satisfactor
-
ily
cleaned
should
be
replaced
.
Any
parts
damaged
or
severely
burned
and
/
or
eroded
from
arc
action
should
be
replaced
.
NOTE
:
Fine
cracks
may
develop
in
the
fins
of
the
arc
chute
sides
.
This
is
to
be
expected
with
ceramic
materials
when
subjected
to
the
high
heat
of
an
arc
and
may
be
disregarded
unless
they
are
long
and
present
a
possibility
of
fin
sections
breaking
completely
off
.
Small
broken
corners
on
the
exhaust
end
of
the
arc
chute
will
not
Interfere
with
its
performance
and
can
also
be
disre
-
garded
.
The
cup
bearing
and
the
contact
ring
at
the
hinge
point
of
the
contact
blade
should
be
disassembled
,
Inspected
,
cleaned
,
and
re
-
lubricated
with
G
-
E
contact
lubricant
D
50
H
47
.
The
contact
ring
should
be
inspected
for
wear
and
replaced
when
reduced
in
thick
-
ness
to
less
than
1
/
32
"
.
sc
5
.
6
.
Hi
!
7
.
s
17
Courtesy of NationalSwitchgear.com

GEI
-
88761
C
.
Every
SQyOOO
Operations
or
Approximately
Every
Five
Years
-
-
-
Which
-
ever
Conies
First
1
.
At
this
time
the
breaker
should
be
given
a
general
overhaul
and
all
excessively
worn
parts
in
both
the
mechanism
and
breaker
re
-
placed
.
Such
wear
will
usually
be
indicated
when
the
breaker
cannot
be
adjusted
to
instruction
book
tolerances
.
This
overhaul
and
inspection
is
more
detailed
and
will
require
disassembly
of
mechanism
and
breaker
operating
parts
.
2
.
All
roller
and
needle
bearings
in
the
operating
mechanism
should
be
disassembled
,
cleaned
,
and
repacked
with
G
-
E
lubricant
D
50
H
15
as
described
under
LUBRICATION
.
3
.
The
stationary
primary
contact
fingers
should
be
disassembled
and
the
silver
-
plated
pivot
area
of
the
contact
and
contact
sup
-
port
cleaned
and
lubricated
with
G
-
E
lubricant
D
50
H
47
.
4
.
The
breaker
and
operating
mechanism
should
be
serviced
as
des
-
cribed
for
every
2
,
000
operations
and
properly
adjusted
before
being
put
back
into
service
.
2
.
Magne
-
blast
breakers
applied
to
repetitive
operation
such
as
capacitor
switching
should
be
serviced
and
maintained
according
to
the
preceeding
recommendations
,
and
in
addition
,
should
have
items
1
A
1
,
1
A
2
,
and
1
A
3
repeated
at
500
operation
intervals
.
TROUBLE
SHOOTING
Hi
Failure
of
a
breaker
to
operate
properly
will
generally
fall
within
four
general
classes
;
failure
to
trip
,
failure
to
close
or
latch
closed
,
clos
-
ing
springs
will
not
recharge
,
and
overheating
.
The
following
is
a
brief
outline
showing
particular
types
of
distress
that
might
be
encountered
,
together
with
suggestions
for
remedying
the
trouble
:
Failure
to
Trip
1
.
Mechanism
binding
or
sticking
caused
by
lack
of
lubrication
.
REMEDY
:
Lubricate
complete
mechanism
.
2
.
Mechanism
binding
or
sticking
caused
by
being
out
of
adjustment
.
REMEDY
:
Check
all
mechanism
adjustments
,
latches
,
stops
,
auxiliary
devices
,
etc
.
,
in
accordance
with
section
on
ADJUSTMENTS
.
Examine
latch
and
roller
surfaces
for
corrosion
.
i
a
!
i
]
I
1
3
'
!
1
?
!
u
.
.
1
8
*
3
*
.
Damaged
trip
coil
.
REMEDY
:
Replace
damaged
coil
*
4
*
Blown
fuse
in
trip
circuit
.
REMEDY
:
Replace
blown
fuse
after
determining
cause
of
failure
.
5
.
Faulty
connections
in
trip
circuit
.
REMEDY
:
Repair
broken
or
loose
wires
and
see
that
all
binding
screws
are
tight
.
6
.
Damaged
or
dirty
contacts
in
trip
circuit
.
REMEDY
:
Recondition
or
replace
contacts
.
f
*
n
$
i
a
a
a
a
1
>
1
*
3
18
s
;
I
Courtesy of NationalSwitchgear.com
This manual suits for next models
3
Other GE Circuit Breaker manuals
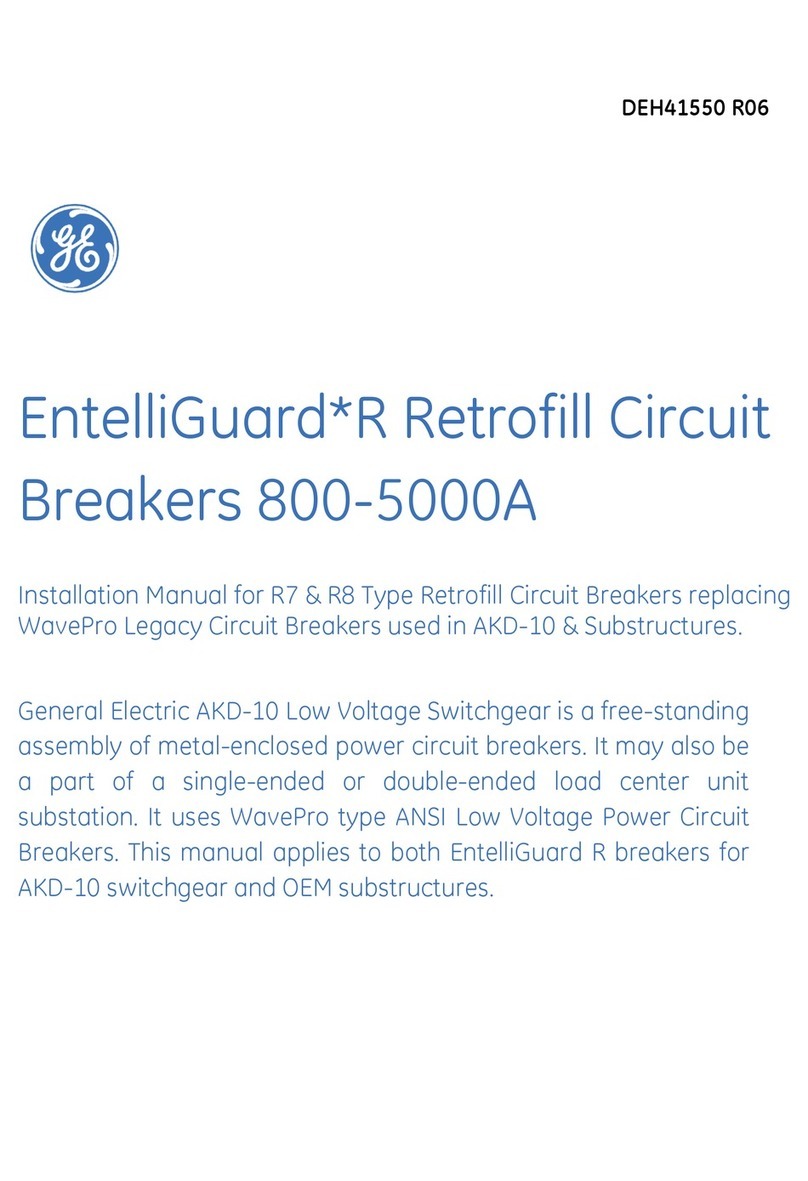
GE
GE EntelliGuard R7 User manual
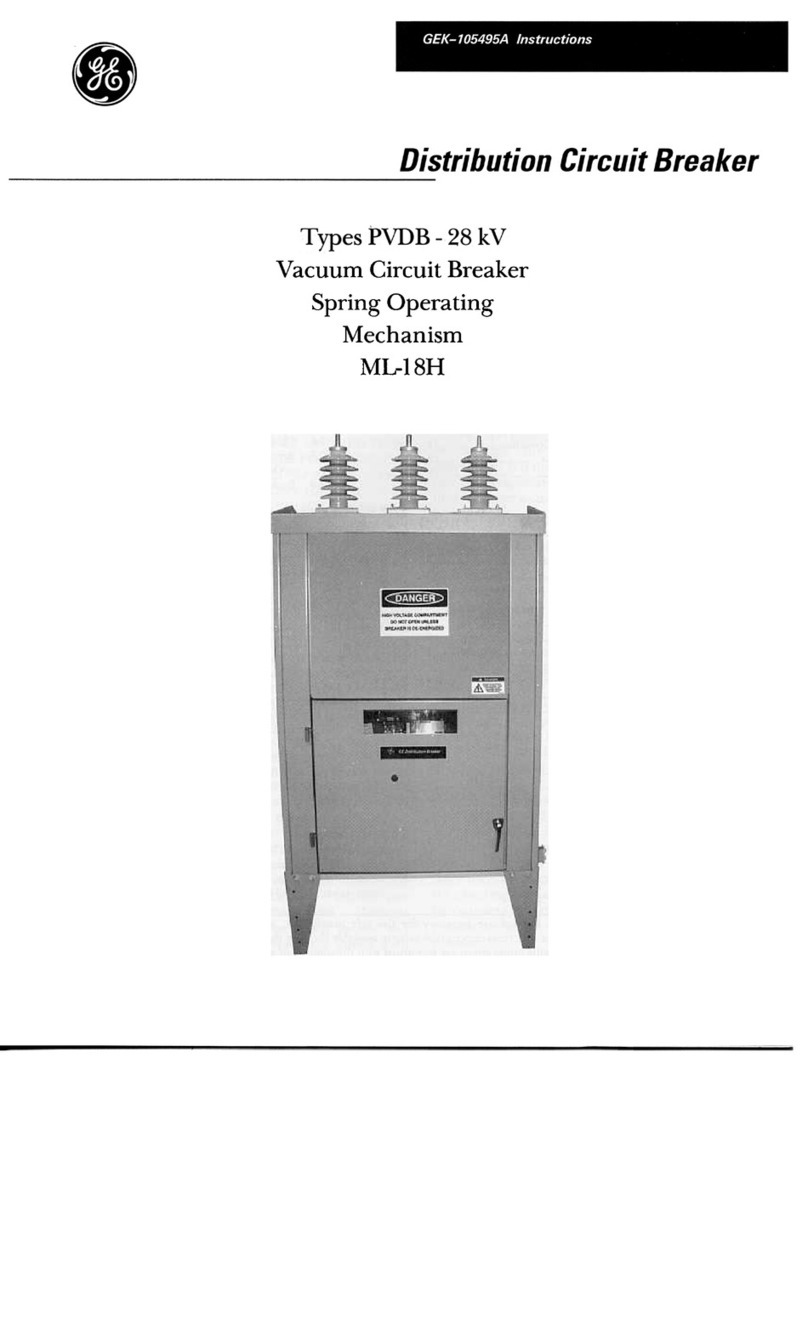
GE
GE PVDB-28kV User manual

GE
GE Spectra Series AMC6FGB User manual
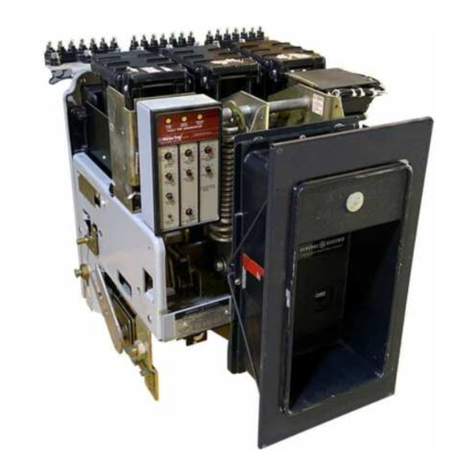
GE
GE AKR-30 Series User manual
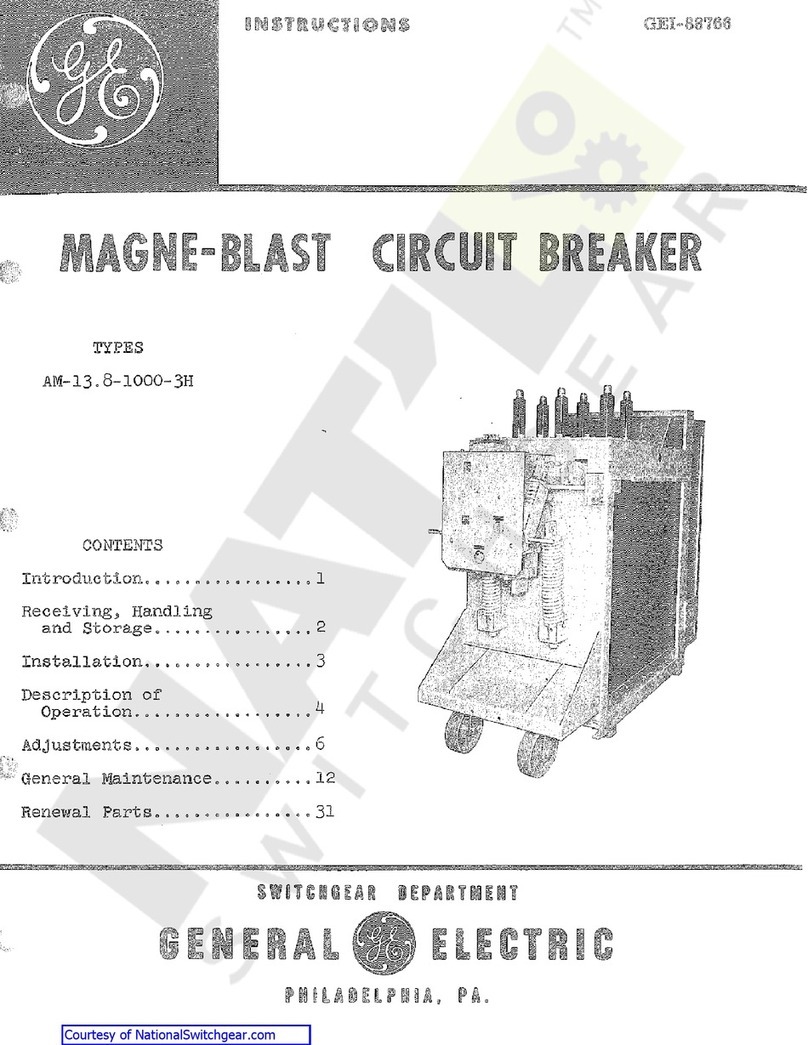
GE
GE Magne-Blast AM-13.8-1000-3H User manual
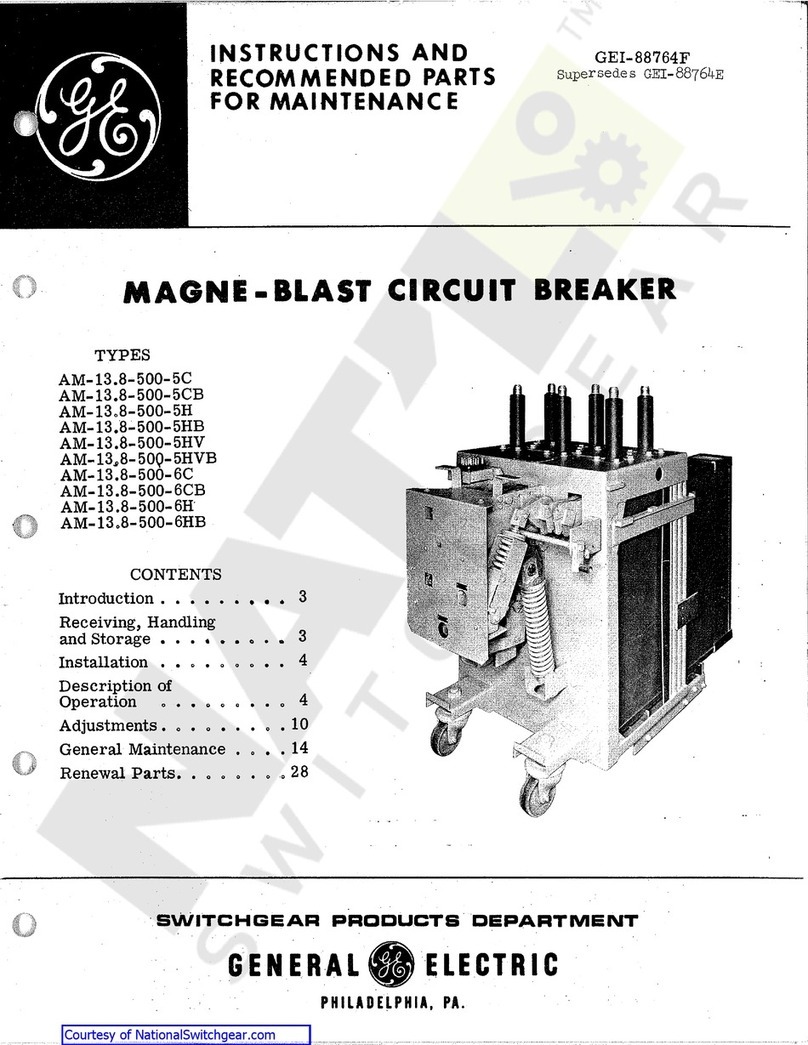
GE
GE AM-13.8-500-5C User manual
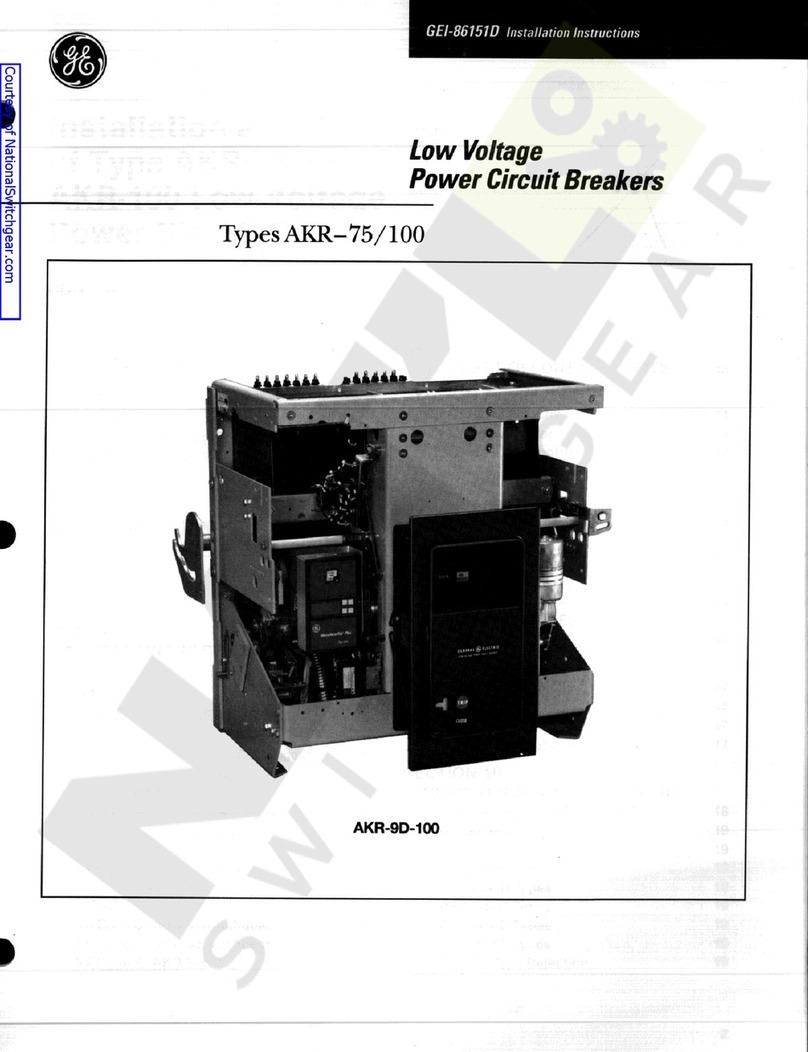
GE
GE MicroVersaTrip AKR-75 User manual
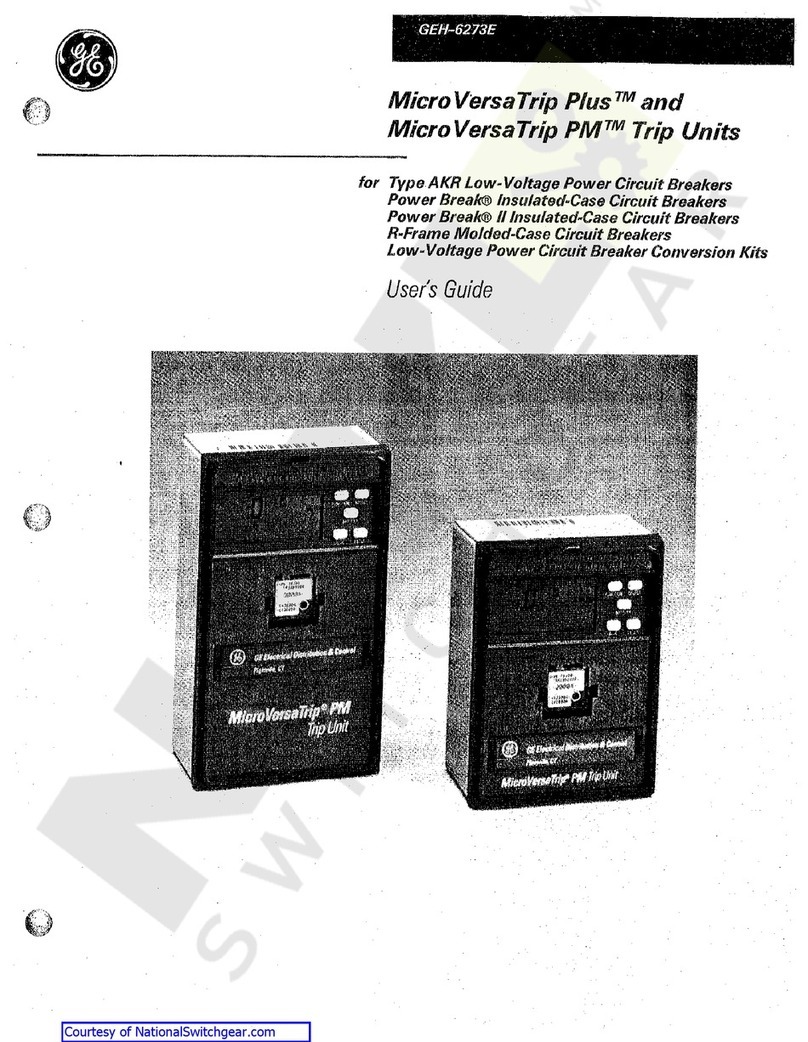
GE
GE MicroVersaTrip Plus User manual

GE
GE MicroVersaTrip AKR-75 User manual
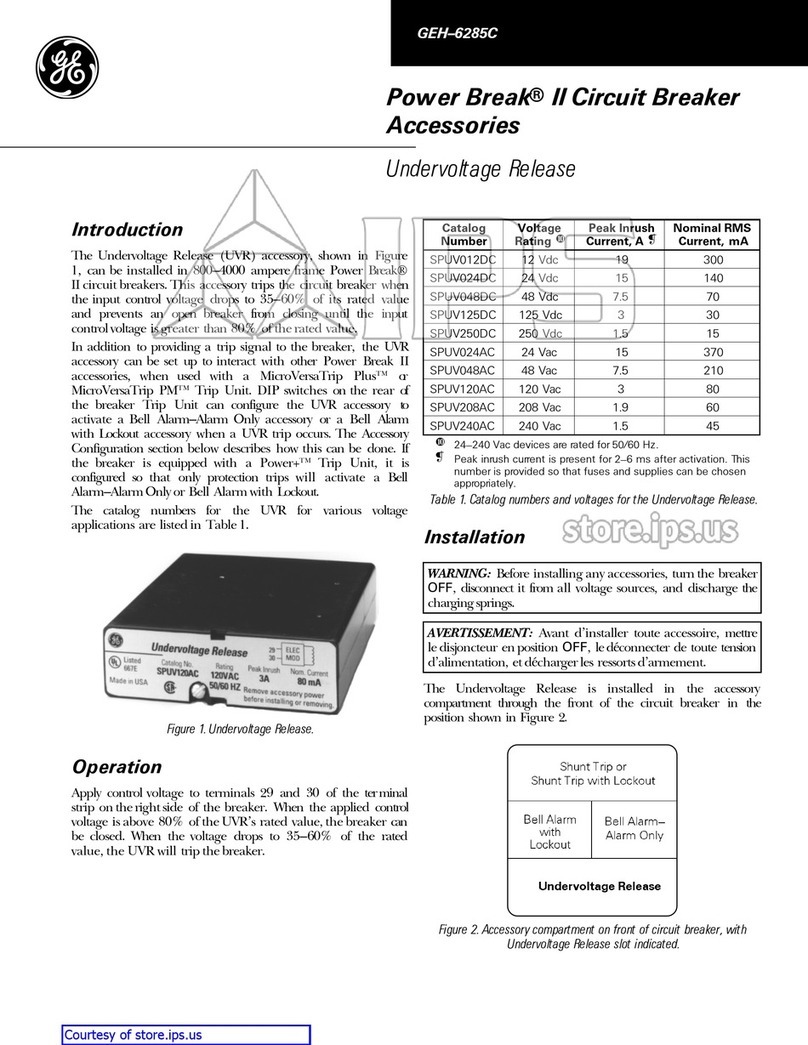
GE
GE Power Break II User manual
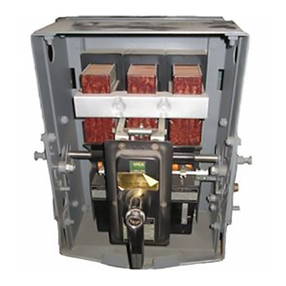
GE
GE AK-1-15 Series User manual

GE
GE FK800 User manual
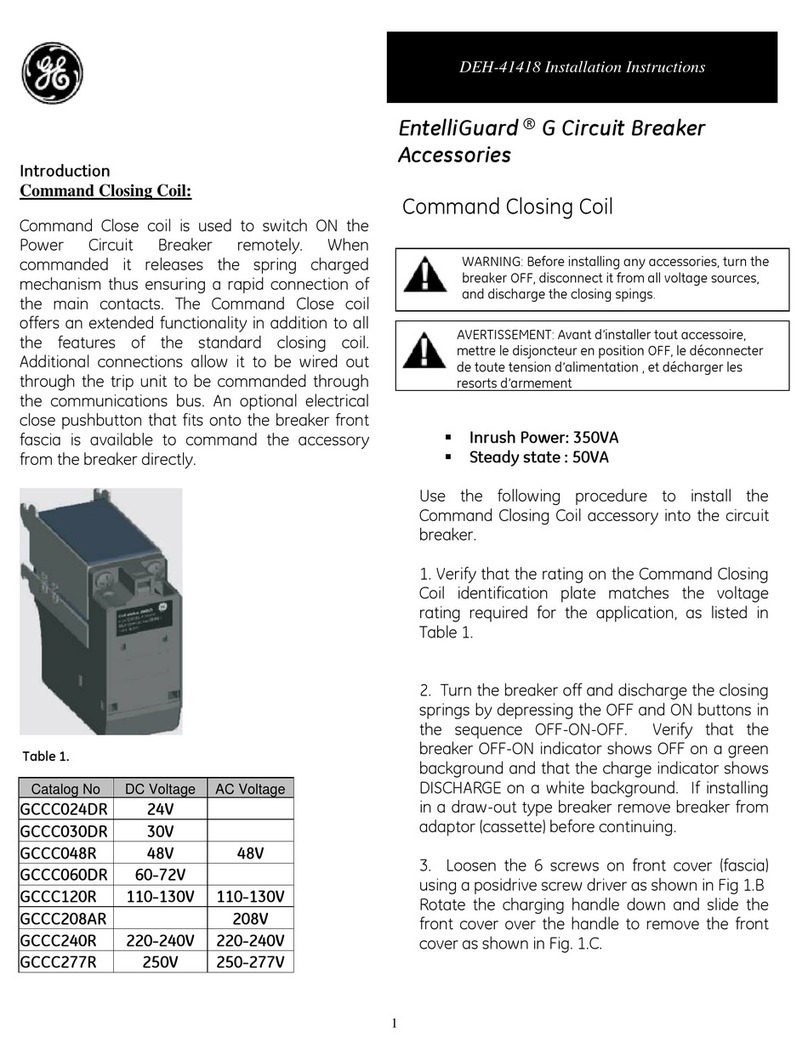
GE
GE GCCC024DR User manual

GE
GE AKR-3-50 User manual
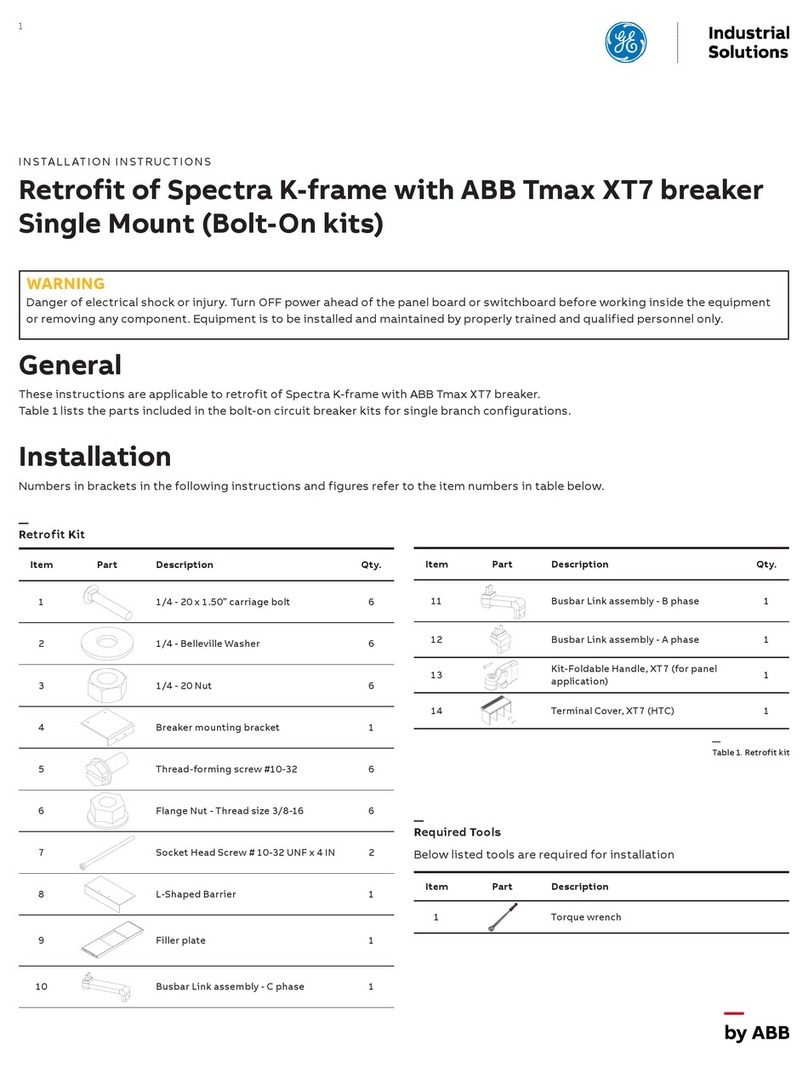
GE
GE Spectra K-frame User manual
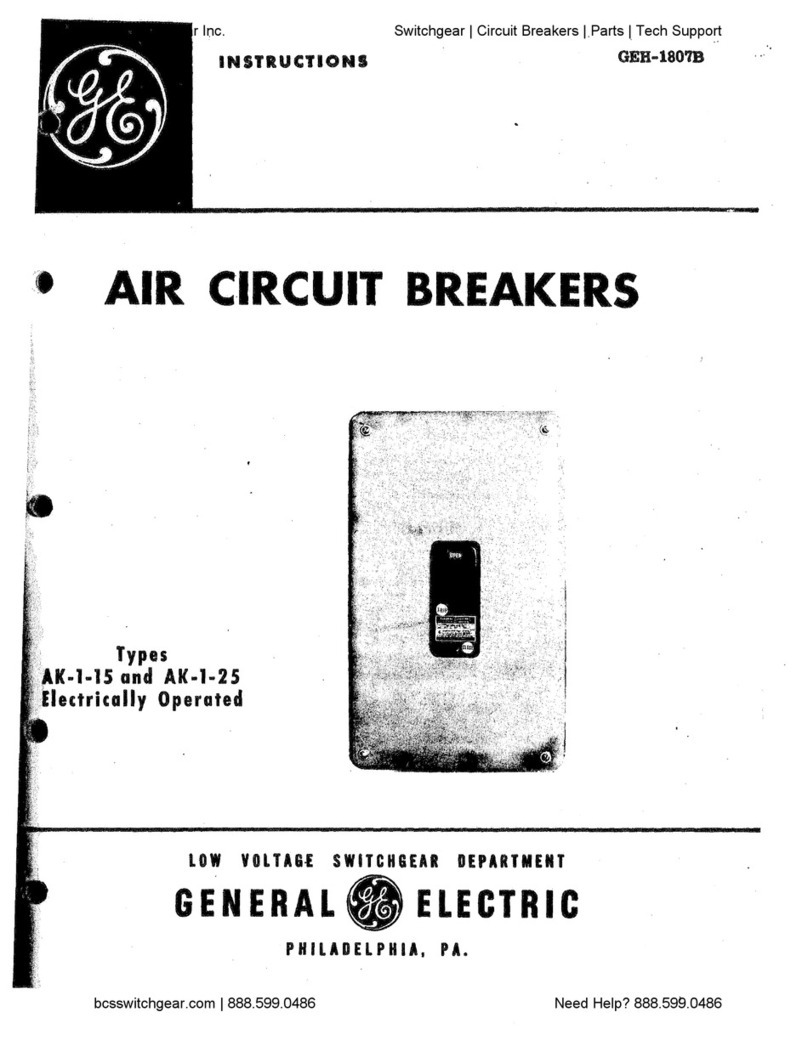
GE
GE AK-1-15 Series User manual
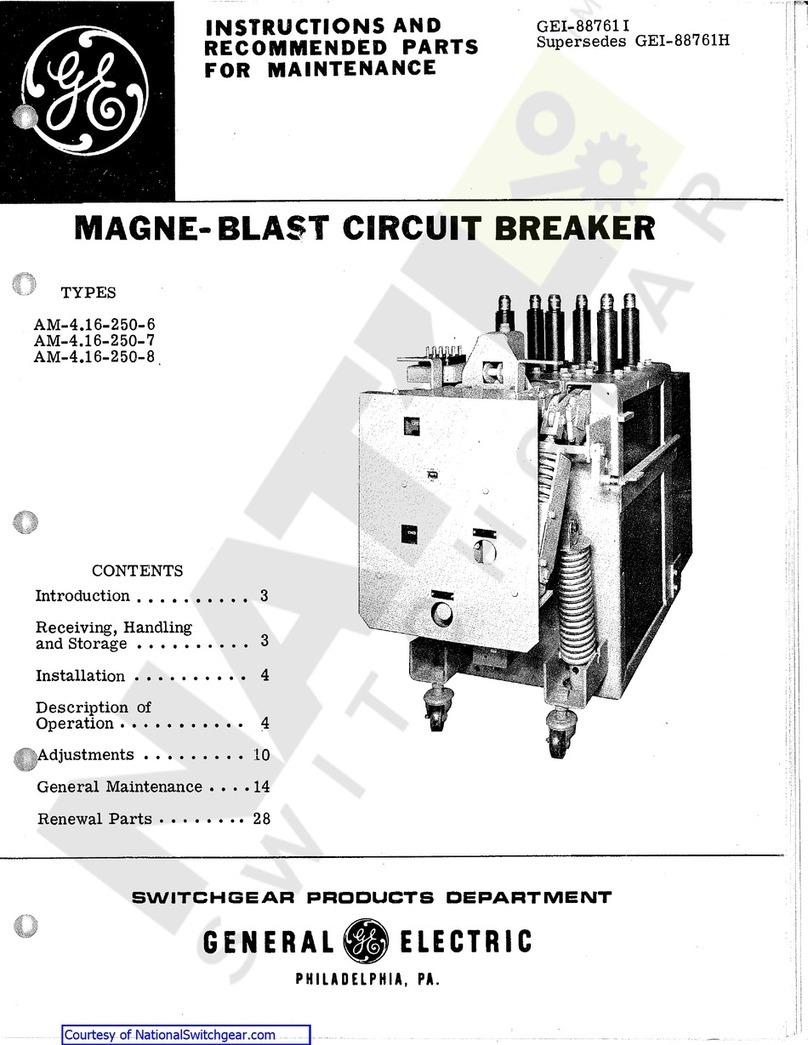
GE
GE AM-4.16-250-6 User manual
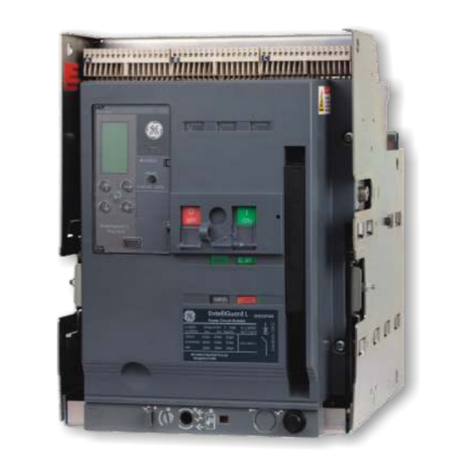
GE
GE EntelliGuard L User manual
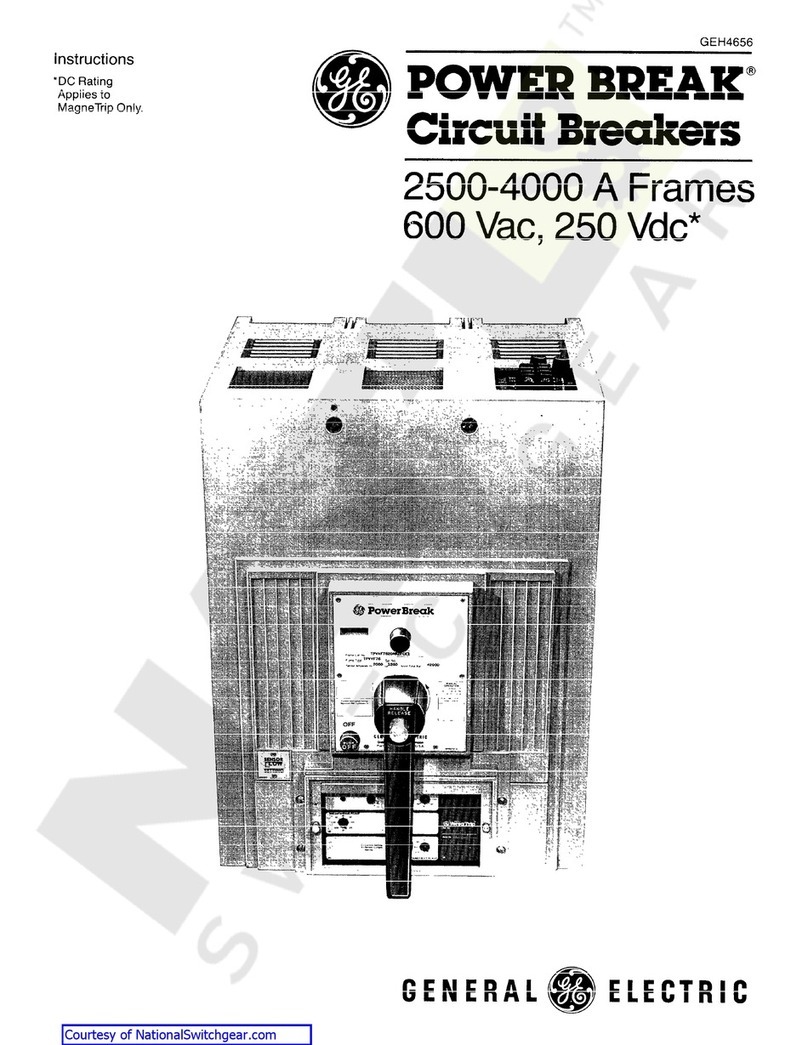
GE
GE POWER BREAK MICRO-VERSATRIP E39ME20 User manual
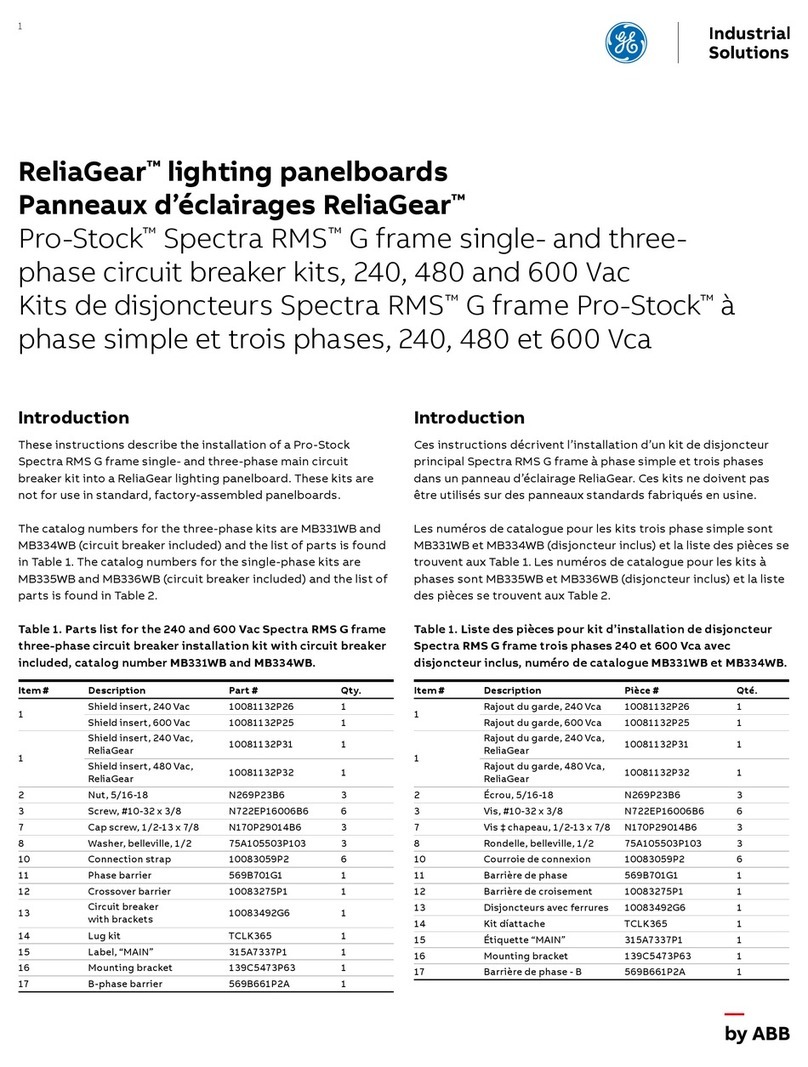
GE
GE ReliaGear Pro-Stock Spectra RMS User manual