MKS 252D User manual

-~
ARTISAN
®
~I
TECHNOLOGY
GROUP
Your definitive source
for
quality
pre-owned
equipment.
Artisan Technology
Group
Full-service,
independent
repair
center
with
experienced
engineers
and
technicians
on staff.
We
buy
your
excess,
underutilized,
and
idle
equipment
along
with
credit
for
buybacks
and
trade-ins
.
Custom
engineering
so
your
equipment
works
exactly as
you
specify.
•
Critical
and
expedited
services
•
Leasing
/
Rentals/
Demos
• In
stock/
Ready-to-ship
•
!TAR-certified
secure
asset
solutions
Expert
team
ITrust
guarantee
I
100%
satisfaction
All
tr
ademarks,
br
a
nd
names, a
nd
br
a
nd
s a
pp
earing here
in
are
th
e property of
th
e
ir
r
es
pecti
ve
ow
ner
s.
Find the MKS Instruments 252A-1-VPO at our website: Click HERE

118703-P1
Rev A, 8/96
MKS Type 252D
Exhaust Valve Controller
Artisan Technology Group - Quality Instrumentation ... Guaranteed | (888) 88-SOURCE | www.artisantg.com

Preliminary manual for the
MKS Type 252D Unit
This is a preliminary manual and MKS Instruments makes no claims as to
its accuracy or correctness. Due to continuing research and development
activities, the information contained within this manual, including product
specifications, is subject to change without notice. Please observe all
safety precautions and use appropriate procedures when handling and
operating the Type 252D Unit.
Copyright © 1996 by MKS Instruments, Inc.
All rights reserved. No part of this work may be reproduced or transmitted in any form or by any
means, electronic or mechanical, including photocopying and recording, or by any information
storage or retrieval system, except as may be expressly permitted in writing by MKS Instruments,
Inc.
Baratronis a registered trademark of MKS Instruments, Inc., Andover, MA
Please Note:
MKS Instruments provides these documents as the latest version for the revision indicated.
The material is subject to change without notice, and should be verified if used in a critical
application.
Artisan Technology Group - Quality Instrumentation ... Guaranteed | (888) 88-SOURCE | www.artisantg.com

Table of Contents
iii
Table of Contents
Safety Procedures and Precautions.......................................................................................... 1
Chapter One: General Information......................................................................................... 5
Introduction............................................................................................................... 5
How This Manual is Organized.................................................................................. 7
Customer Support...................................................................................................... 7
Chapter Two: Installation ......................................................................................................9
How To Unpack the Type 252 Unit............................................................................ 9
Unpacking Checklist ..................................................................................... 9
Setup ......................................................................................................................... 11
System Design .............................................................................................. 11
Power and Fuse Requirements....................................................................... 11
Mounting Instructions ................................................................................... 12
Interconnections............................................................................................ 12
Cables........................................................................................................... 14
Chapter Three: Overview....................................................................................................... 19
General Information................................................................................................... 19
Stepping Drive Motor................................................................................................ 20
Front Panel Controls.................................................................................................. 21
Rear Panel Controls................................................................................................... 23
Chapter Four: Operation........................................................................................................25
How To Setup the Controller .....................................................................................25
How To Tune-Up the Controller ................................................................................ 26
How To Use the Normal/Reverse Switch ................................................................... 27
How To Use External Control.................................................................................... 27
Advisory ....................................................................................................... 28
How To Use the Valve Position Option...................................................................... 29
Interconnections............................................................................................ 29
How To Use the Multiple Set Point Option................................................................31
Settings......................................................................................................... 31
Artisan Technology Group - Quality Instrumentation ... Guaranteed | (888) 88-SOURCE | www.artisantg.com

Table of Contents
iv
Selection........................................................................................................31
Interconnections.............................................................................................32
How To Use the Process Limit Option........................................................................33
Controls.........................................................................................................33
Interconnections.............................................................................................34
How To Use the Reverse Limit Switch Option ...........................................................35
Chapter Five: Maintenance and Troubleshooting....................................................................37
General Information ...................................................................................................37
Maintenance...............................................................................................................37
Alignment Procedure.....................................................................................37
Troubleshooting.........................................................................................................40
Appendix A: Product Specifications.......................................................................................43
Appendix B: Model Code Explanation...................................................................................45
Model Code................................................................................................................45
How To Order a Type 252 Unit..................................................................................46
Index ......................................................................................................................................47
Artisan Technology Group - Quality Instrumentation ... Guaranteed | (888) 88-SOURCE | www.artisantg.com

List of Fi
g
ures
List of Tables
v
List of Figures
Figure 1: Standard Pressure Control Setup................................................................................ 13
Figure 2: 253 Valve Connected in Parallel with an Isolation Valve........................................... 13
Figure 3: Front Panel Controls.................................................................................................. 21
Figure 4: Rear Panel Controls................................................................................................... 23
Figure 5: Process Limit Set Point Control................................................................................. 33
List of Tables
Table 1: Valve Connector Pinout..............................................................................................15
Table 2: Transducer Connector Pinout......................................................................................16
Table 3: Interface Connector Pinout..........................................................................................17
Table 4: Four-Step Sequence....................................................................................................20
Table 5: Valve Position Option Pinout......................................................................................30
Table 6: Multiple Set Point Option Pinout ................................................................................32
Table 7: Process Limit Option Pinout .......................................................................................34
Table 8: Test Point Voltages.....................................................................................................39
Table 9: Troubleshooting Chart ................................................................................................41
Artisan Technology Group - Quality Instrumentation ... Guaranteed | (888) 88-SOURCE | www.artisantg.com

List of Figures
List of Tables
vi
Artisan Technology Group - Quality Instrumentation ... Guaranteed | (888) 88-SOURCE | www.artisantg.com

Safety Procedures and Precautions
1
Safety Procedures and Precautions
DO NOT SUBSTITUTE PARTS OR MODIFY INSTRUMENT
Do not install substitute parts or perform any unauthorized modification to the instrument.
Return the instrument to an MKS Calibration and Service Center for service and repair to ensure
that all safety features are maintained.
SERVICE BY QUALIFIED PERSONNEL ONLY
Operating personnel must not remove instrument covers. Component replacement and internal
adjustments must be made by qualified service personnel only.
DO NOT SERVICE OR ADJUST ALONE
Do not attempt internal service or adjustment unless another person capable of rendering first aid
and resuscitation, is present.
GROUNDING THE PRODUCT
This product is grounded through the grounding conductor of the power cord. To avoid electrical
shock, plug the power cord into a properly wired receptacle before connecting it to the product
input or output terminals. A protective ground connection by way of the grounding conductor in
the power cord is essential for safe operation.
DANGER ARISING FROM LOSS OF GROUND
Upon loss of the protective-ground connection, all accessible conductive parts (including knobs
and controls that may appear to be insulating) can render an electrical shock.
GROUND AND USE PROPER ELECTRICAL FITTINGS
Dangerous voltages are contained within this instrument. All electrical fittings must be of the
type specified, and in good condition. All electrical fittings must be properly connected and
grounded.
USE THE PROPER POWER CORD
Use only the power cord and connector specified for your product.
Use only a cord in good condition.
Artisan Technology Group - Quality Instrumentation ... Guaranteed | (888) 88-SOURCE | www.artisantg.com

Safet
y
Procedures and Precautions
2
USE THE PROPER POWER SOURCE
This product is intended to operate from a power source that does not apply more than 250 Volts
RMS between the supply conductors, or between either of the supply conductors and ground. A
protective ground connection by way of the grounding conductor in the power cord is essential
for safe operation.
USE THE PROPER FUSE
Use only a fuse of the correct type, voltage rating, and current rating, as specified for your
product.
KEEP AWAY FROM LIVE CIRCUITS
Do not replace components with power cable connected. Under certain conditions, dangerous
voltages may exist even with the power cable removed. To avoid injuries, always disconnect
power and discharge circuits before touching them.
DO NOT OPERATE IN EXPLOSIVE ATMOSPHERES
To avoid explosion, do not operate this product in an explosive atmosphere unless it has been
specifically certified for such operation.
KEEP AWAY FROM VALVE OPENING
Keep fingers, other body parts, and other materials away from the valve opening when the valve
is in operation.
Artisan Technology Group - Quality Instrumentation ... Guaranteed | (888) 88-SOURCE | www.artisantg.com

Safety Procedures and Precautions
3
Definitions of WARNING, CAUTION, and NOTE messages used throughout the manual.
Warning The WARNING sign denotes a hazard. It calls attention to a
procedure, practice, condition, or the like, which, if not
correctly performed or adhered to, could result in injury to
personnel.
Caution The CAUTION sign denotes a hazard. It calls attention to an
operating procedure, practice, or the like, which, if not correctly
performed or adhered to, could result in damage to or destruction of
all or part of the product.
Note The NOTE sign denotes important information. It calls attention to a
procedure, practice, condition, or the like, which is essential to highlight.
Artisan Technology Group - Quality Instrumentation ... Guaranteed | (888) 88-SOURCE | www.artisantg.com

Safet
y
Procedures and Precautions
4
This page intentionally left blank.
Artisan Technology Group - Quality Instrumentation ... Guaranteed | (888) 88-SOURCE | www.artisantg.com

Chapter One: General Information Introduction
5
Chapter One: General Information
Introduction
The MKS Type 252D Exhaust Valve Controller controls a stepper motor powered exhaust valve
(MKS Type 253) to maintain a constant pressure in a vacuum system by varying the pumping
speed. The 252 controller can provide a ±15 VDC output and will accept pressure inputs from a
variety of transducers. The front panel controls allow selection of the input range, control loop
tuning, and automatic and manual valve control. An error meter is provided to assist you in
tuning the control loop. External signals can be used to command the external set point and open
or close the valve.
Typically, a pressure control system consists of three basic parts:
•The pressure sensor
•The controller and control valve
•The system whose pressure is to be controlled
The pressure sensor will usually be an MKS BaratronCapacitance Manometer whose output is
0 to 10 VDC. Provision for other inputs (0 to 1 VDC or 0 to 100 mV) has been built into the
controller so that other transducers may be used. The pressure (vacuum) system consists of a
chamber and a pumping system. Typically, users want to control the mass flow of gas entering
the system while the system pressure is maintained by the 252 controller and 253 control valve
(refer to Figure 1, page 13).
The 252 controller’s new 15-pin Type “D” connector allows you to connect the unit to a Type
253B throttle valve. If you install the 252 controller into an existing system that uses the old
(hex) connector cables, an adapter cable is required (refer to Valve Connector, page 15, for more
information).
Artisan Technology Group - Quality Instrumentation ... Guaranteed | (888) 88-SOURCE | www.artisantg.com

Introduction Cha
p
ter One: General Information
6
The 252 controller takes the DC pressure transducer signal, compares it to the set point, and
positions the valve so that it will drive the actual pressure to the set pressure. The 252 controller
contains the three modes of control action found in most current industrial controllers:
proportional, derivative, and integral. Briefly, these functions are as follows:
1. Proportional gives a valve action (position) that is instantaneously a linear function of
the error signal. For example:
Signal to valve = K1x Error (K1is adjustable by the gain pot)
2. Derivative action provides a signal to the valve that is proportional to the rate of change
of the error signal. For example:
Signal to valve = K2x d (Error) (K2is adjustable by the phase pot)
dt
A simple description of this mode of control is that it provides an anticipation element, or
the valve reaches its proper steady state position sooner than without derivative. This is
apparent when setting up the system; the derivative, or phase lead control tailors the
under or overshoot. In other words, it cancels out the build-up of lags already built into
the system.
3. Integral action provides an additional valve signal which is proportional to the length of
time that an error signal exists. For example:
Signal to valve = ∫d (Error) / dt.
In other words, as time passes, the valve position changes which reduces the signal error
to zero.
Artisan Technology Group - Quality Instrumentation ... Guaranteed | (888) 88-SOURCE | www.artisantg.com

Chapter One: General Information How This Manual is Or
g
anized
7
How This Manual is Organized
This manual is designed to provide instructions on how to set up, install, and operate a Type 252
unit.
Before installing your Type 252 unit in a system and/or operating it, carefully read and
familiarize yourself with all precautionary notes in the Safety Messages and Procedures
section at the front of this manual. In addition, observe and obey all WARNING and
CAUTION notes provided throughout the manual.
Chapter One: General Information, (this chapter) introduces the product and describes the
organization of the manual.
Chapter Two: Installation, describes how to mount the instrument in your system.
Chapter Three: Overview, gives a brief description of the instrument and its functionality.
Chapter Four: Operation, describes how to use the instrument and explains all the functions and
features.
Chapter Five: Maintenance and Troubleshooting, describes basic maintenance procedures and
how to troubleshoot a problem should the 252 unit malfunction.
Appendix A: Product Specifications, lists the specifications of the instrument.
Appendix B: Model Code Explanation, describes the instrument’s model code and how to order
the unit.
Customer Support
Standard maintenance and repair services are available at all of our regional MKS Calibration and
Service Centers, listed on the back cover. In addition, MKS accepts the instruments of other
manufacturers for recalibration using the Primary and Transfer Standard calibration equipment
located at all of our regional service centers. Should any difficulties arise in the use of your Type
252 instrument, or to obtain information about companion products MKS offers, contact any
authorized MKS Calibration and Service Center. If it is necessary to return the instrument to
MKS, please obtain an ERA Number (Equipment Return Authorization Number) from the MKS
Calibration and Service Center before shipping. The ERA Number expedites handling and
ensures proper servicing of your instrument.
Please refer to the inside of the back cover of this manual for a list of MKS Calibration and
Service Centers.
Warning All returns to MKS Instruments must be free of harmful,
corrosive, radioactive, or toxic materials.
Artisan Technology Group - Quality Instrumentation ... Guaranteed | (888) 88-SOURCE | www.artisantg.com

Customer Support Cha
p
ter One: General Information
8
This page intentionally left blank.
Artisan Technology Group - Quality Instrumentation ... Guaranteed | (888) 88-SOURCE | www.artisantg.com

Chapter Two: Installation How To Un
p
ack the T
yp
e 252 Unit
9
Chapter Two: Installation
How To Unpack the Type 252 Unit
MKS has carefully packed the Type 252 unit so that it will reach you in perfect operating order.
Upon receiving the unit, however, you should check for defects, cracks, broken connectors, etc.,
to be certain that damage has not occurred during shipment.
Note Do not discard any packing materials until you have completed your
inspection and are sure the unit arrived safely.
If you find any damage, notify your carrier and MKS immediately. If it is necessary to return the
unit to MKS, obtain an ERA Number (Equipment Return Authorization Number) from the MKS
Service Center before shipping. Please refer to the inside of the back cover of this manual for a
list of MKS Calibration and Service Centers.
Caution Only qualified individuals should perform the installation and any
user adjustments. They must comply with all the necessary ESD and
handling precautions while installing and adjusting the instrument.
Proper handling is essential when working with all highly sensitive
precision electronic instruments.
Unpacking Checklist
Standard Equipment
•Type 252 Unit
•Type 252 Instruction Manual (this book)
•Power Cable
Note 1. Metal, braided, shielded cables are required to meet CE Mark
certification.
2. To order metal, braided, shielded cables, add an “S”after the cable
type designation. For example, to order a standard cable to connect
the 252 controller to a Type 627 transducer, use part number
CB258-1-10; for a metal, braided, shielded cable use part number
CB258S-1-10.
Artisan Technology Group - Quality Instrumentation ... Guaranteed | (888) 88-SOURCE | www.artisantg.com

How To Unpack the Type 252 Unit Cha
p
ter Two: Installation
10
Optional Equipment
•Rack Mounting Kit:
RM-6
•Electrical Connector Accessory Kit:
252D-K1
•Input Cables:
CB250-7-6 Connects the 252 unit to a Type 270/690 system
CB254-2-10 Connects the 252 unit to Type 122, 124, 223, 622,
and 623 transducers
CB254-1-10 Connects the 252 unit to Type 121 and 122
transducers
CB254-4-10 Connects the 252 unit to a Type 220 transducer
CB258-1-10 Connects the 252 unit to Type 127, 258, 358, 558,
624, 626, and 627 transducers
CB128-2-10 Connects the 252 unit to Type 128, 625, and 628
transducers
CB254-17-6 Connects the 252 unit to Type PDR-C-1C/2C,
PDR-D-1, and PDR-5B power supply/readouts
CB120-3-10 Connects the 252 unit to a Type 120 transducer with
a separate input power connector
•Valve Cable:
CB252-16-10 Connects the 252D unit to a 253B valve
•Valve Adapter Cable:
CB252-17-1 Replaces a 252A-C unit with a 252D unit
Artisan Technology Group - Quality Instrumentation ... Guaranteed | (888) 88-SOURCE | www.artisantg.com

Chapter Two: Installation Setu
p
11
Setup
System Design
The standard one inch 253 valve has a maximum conductance of 150 liters/sec. and a minimum
controllable conductance of about 0.15 liters/sec. Within this range of about 1000 to 1, the 252
controller can provide excellent control if the other system parameters allow. Plumbing should
be as short in length and as large in diameter as possible. Connections can be made directly with
the KF-40 flanges. A wide variety of 253 valves are available from ¾” to 12”. There are three
different flange types. For mounting instructions, refer to the 253 manual.
Tubing between the pressure transducer and the chamber should be less than 6 inches long and no
less than ¼” in diameter. Fittings should be checked to make sure they do not have small drilled
passages and antichambers off the main vacuum chamber should be kept to a minimum as they
might cause stability problems.
If a 270/690 type system is used for pressure measurement, make sure the 270 indicator switch is
in the NORMAL position.
An important consideration is a condition that is peculiar to diffusion pumps called choking. If
too much gas is introduced at too high a pressure, the pumping speed becomes erratic and
changes radically. This behavior is easily recognized by lack of stability and pneumatic noise,
sometimes making control impossible. Reducing the flow to the pump is the only solution.
Another consideration involves removing delays in the system response that make stabilization
difficult or impossible.
Note Diffusion pumps should never be operated at inlet pressures above which
the “top jet”will experience a pressure in excess of 5 x 10-4 Torr.
Power and Fuse Requirements
The power requirements for the 252 controller are:
90 to 132 VAC @ 50-60 Hz
or
198 to 264 VAC @ 50-60 Hz
40 Watts @ 90 VAC 60 Hz minimum
70 Watts @ 132 VAC 50 Hz maximum
The line fuses protect the internal circuitry; both sides of the line are fused. The fuse values are:
100/120 VAC: 0.80 A Slo Blo / 250 V
220/240 VAC: 0.40 A Slo Blo / 250 V
Artisan Technology Group - Quality Instrumentation ... Guaranteed | (888) 88-SOURCE | www.artisantg.com

Setup Cha
p
ter Two: Installation
12
Mounting Instructions
Controller
The 252 can be mounted on any instrument panel or placed on a bench. The mounting position is
not critical and it will operate properly in any position. While the unit is designed and tested to
be operated with no air circulation, it will run much cooler if the air slots are clear to allow
convection air circulation. No special precautions are needed to protect the unit from ordinary
mechanical shock and vibration. A rack mounting kit (RM-6) is available from MKS for single
or dual unit rack mounting.
Valve
The 253 valve should be connected using pipe or hose as large in diameter and as short in length
as possible. Refer to the 253 manual for mounting instructions.
Transducer
The pressure transducer should be mounted so that it is firmly supported, while at the same time,
isolated from any vibration.
Any pressure transducer which delivers at least 0.1 Volt full scale, can be used as the feedback
element for total pressure control.
Interconnections
Figures 1 and 2, page 13, show typical piping and cable interconnection diagrams. Figure 1
shows the usual setup for standard pressure control. Figure 2 shows a system where the 253
valve is connected in parallel with the isolation valve and a 270/690 pressure measurement
system is used.
Connect the valve and transducer to the chamber using short connections with minimum
restrictions. Six inches of ¼” tubing should be maximum. Never reduce the tubing size below
that of the transducer. If the chamber is repeatedly opened to the atmosphere, the transducer
should be protected by an isolation valve.
Artisan Technology Group - Quality Instrumentation ... Guaranteed | (888) 88-SOURCE | www.artisantg.com

Chapter Two: Installation Setu
p
13
Figure 1: Standard Pressure Control Setup
690
Figure 2: 253 Valve Connected in Parallel with an Isolation Valve
Artisan Technology Group - Quality Instrumentation ... Guaranteed | (888) 88-SOURCE | www.artisantg.com
This manual suits for next models
3
Table of contents
Other MKS Controllers manuals
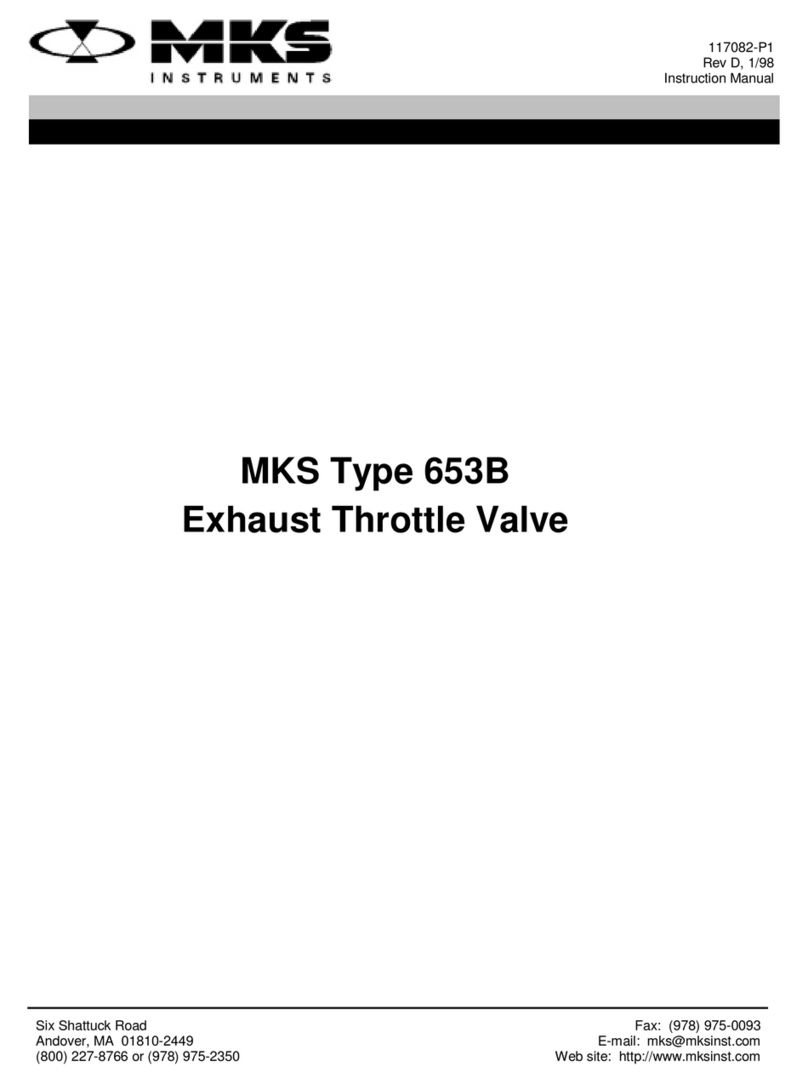
MKS
MKS 653B User manual
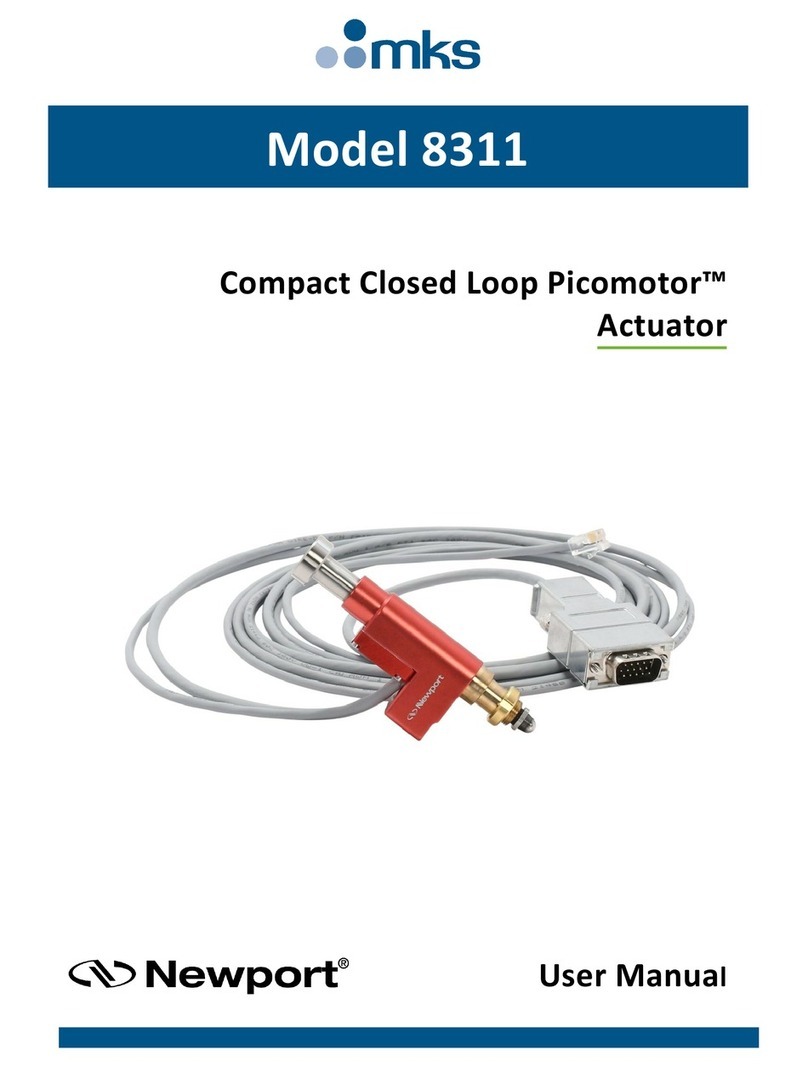
MKS
MKS Compact Closed Loop Picomotor User manual
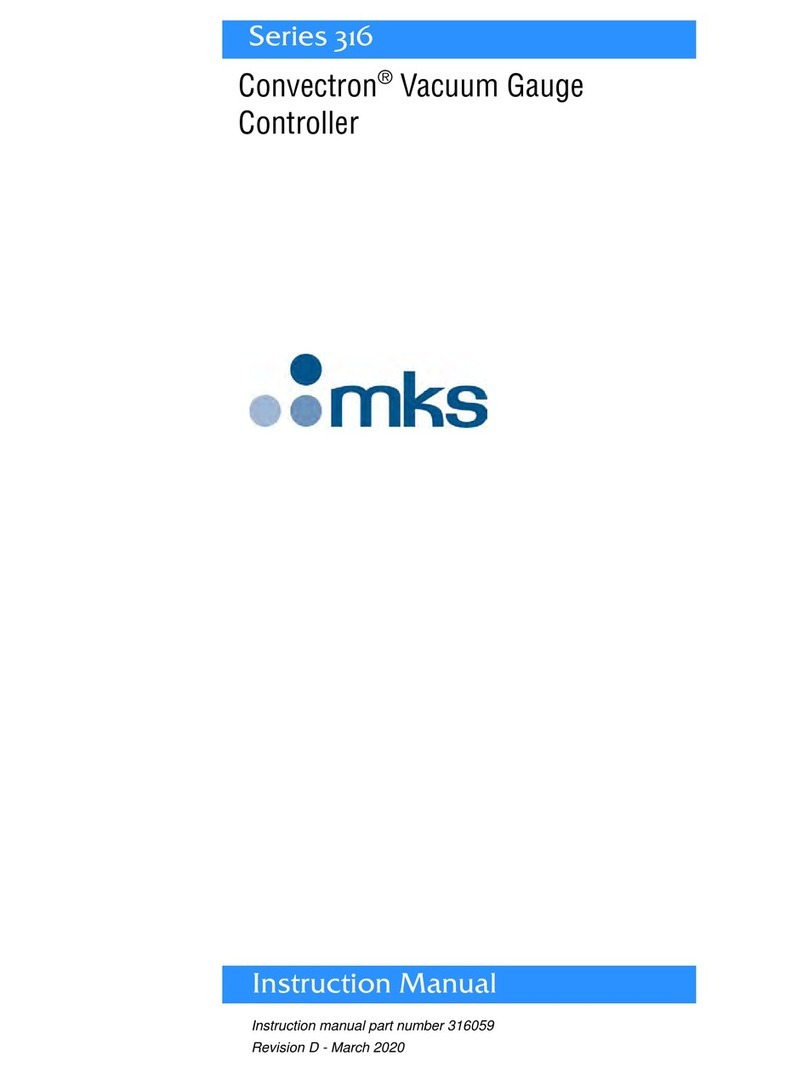
MKS
MKS Convectron 316 Series User manual
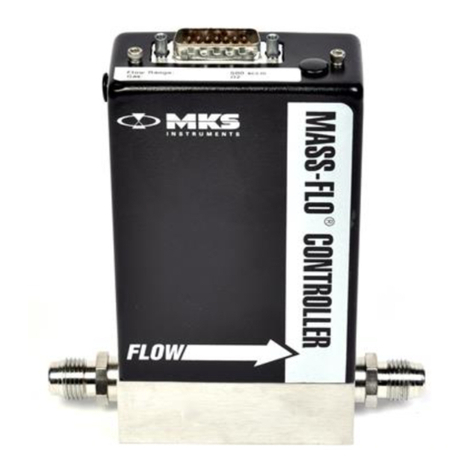
MKS
MKS Mass-Flo 1479A User manual
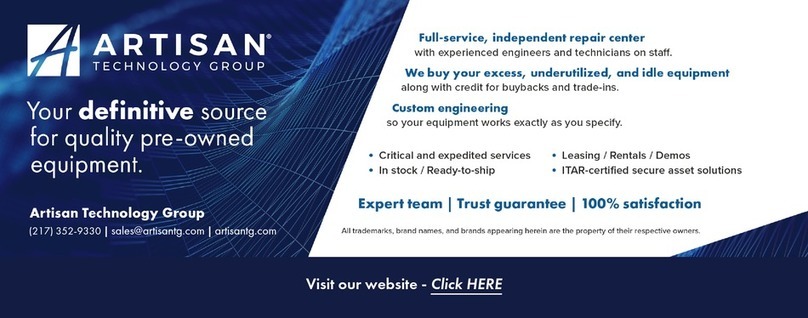
MKS
MKS MKS 153F User manual
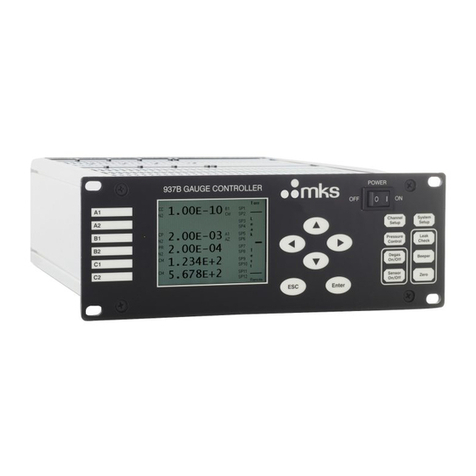
MKS
MKS 937B Series User manual
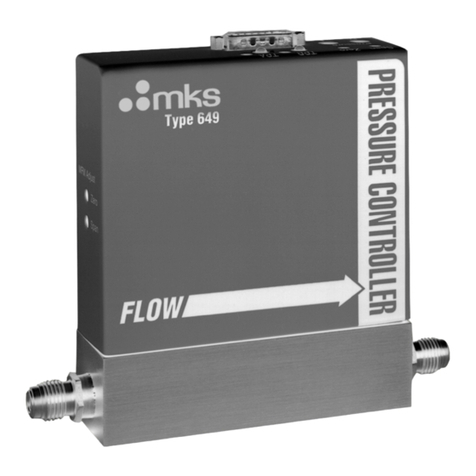
MKS
MKS 649A User manual
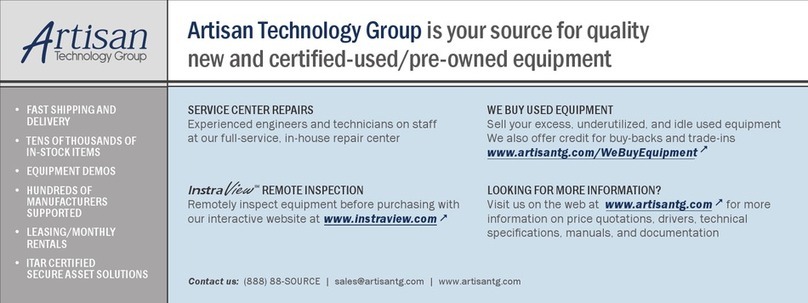
MKS
MKS 252E User manual
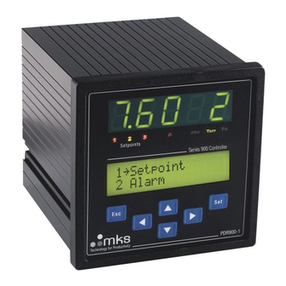
MKS
MKS 900 Series User manual
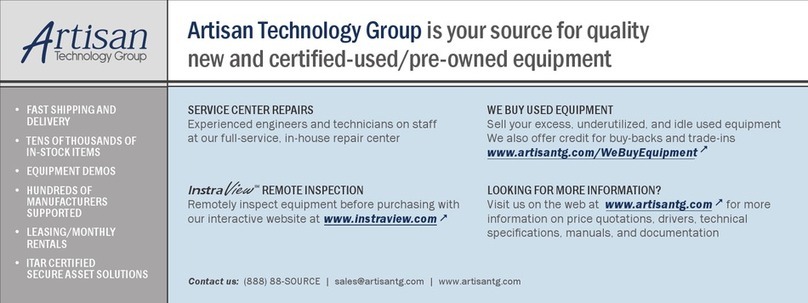
MKS
MKS Mass-Flo 1679B User manual