SUTO S452 Manual

English
Instruction and Operation Manual
S452
Thermal Mass Flow Meter
for Heavy Duty and x Applications (Inline)

Dear Customer,
Thank you for choosing our product.
Please read the operating instructions in full and carefully observe them
before starting up the device. The manufacturer cannot be held liable
for any damage which occurs as a result of non-observance or non-
compliance with this manual.
Should the device be tampered with in any manner other than a
procedure which is described and specified in the manual, the warranty
is void and the manufacturer is e empt from liability.
The device is designed e clusively for the described application.
SUTO offers no guarantee for the suitability for any other purpose.
SUTO is also not liable for consequential damage resulting from the
delivery, capability or use of this device.
2 S452

Table of Contents
1 Safety instructions......................................................................4
2 Registered trademarks.................................................................6
3 Application.................................................................................7
4 Features....................................................................................7
5 Technical data............................................................................8
5.1 General data.........................................................................8
5.2 Electrical data.......................................................................9
5.3 Output signals......................................................................9
5.4 Accuracy .............................................................................9
5.5 Flow ranges..........................................................................9
6 Dimensional drawing.................................................................11
6.1 Thread type........................................................................11
6.2 Flange type.........................................................................12
7 Determining the installation point................................................14
7.1 Additional inlet and outlet sections.........................................15
8 Installation ..............................................................................16
8.1 Installing the S452..............................................................16
8.2 Removing the S452 ............................................................17
8.3 Re-installation after maintenance..........................................17
8.4 Electrical connection ..........................................................18
8.4.1 Connection diagram.......................................................18
8.4.2 Pin assignment..............................................................18
9 Signal outputs..........................................................................20
9.1 Analog and pulse outputs ....................................................20
9.1.1 Analog output...............................................................20
9.1.2 Pulse output..................................................................20
9.2 HART output ......................................................................22
9.3 Modbus Interface ................................................................22
9.4 M-Bus output .....................................................................24
10 Configuration..........................................................................24
11 Optional accessories................................................................26
11.1 Sensor display...................................................................26
11.2 Service kit........................................................................26
12 Calibration..............................................................................27
13 Maintenance...........................................................................27
14 Disposal or waste....................................................................27
S452 3

1 Safety instructions
1 Safety instructions
Please check if this instruction manual matches the
product type.
Please observe all notes and instructions indicated in this
manual. It contains essential information which must be
observed before and during installation, operation and
maintenance. Therefore this instruction manual must be read carefully
by the technician as well as by the responsible user or qualified
personnel.
This instruction manual must be available at the operation site of the
flow sensor at any time. In case of any obscurities or questions,
regarding this manual or the product, please contact the manufacturer.
WARNING!
Compressed air!
Any contact with quickly escaping air or bursting
parts of the compressed air system can lead to
serious injuries or even death!
•Do not e ceed the ma imum permitted pressure range (see
sensors label).
•Only use pressure tight installation material.
•Avoid that persons get hit by escaping air or bursting parts of the
instrument.
•The system must be pressureless during maintenance work.
WARNING!
Voltage used for supply!
Any contact with energized parts of the product, may
lead to a electrical shock which can lead to serious
injuries or even death!
•Consider all regulations for electrical installations.
•The system must be disconnected from any power supply during
maintenance work.
•Any electrical work on the system is only allowed by authorized
qualified personal.
4 S452

1 Safety instructions
ATT NTION!
Permitted operating parameters!
Observe the permitted operating parameters, any
operation exceeding this parameters can lead to
malfunctions and may lead to damage on the
instrument or the system.
•Do not e ceed the permitted operating parameters.
•Make sure the product is operated in its permitted limitations.
•Do not e ceed or undercut the permitted storage and operation
temperature and pressure.
•The product should be maintained and calibrated frequently, at
least annually.
General safety instructions
•It is allowed to use the product in e plosive areas. Please contact
the manufacturer.
•Please observe the national regulations before/during installation
and operation.
Remarks
•It is not allowed to disassemble the product.
•Always use spanner to mount the product properly.
ATT NTION!
Measurement values can be affected by malfunction!
The product must be installed properly and
frequently maintained, otherwise it may lead to
wrong measurement values, which can lead to
wrong results.
•Always observe the direction of the flow when installing the
sensor. The direction is indicated on the housing.
•Do not e ceed the ma imum operation temperature at the sensors
tip.
•Avoid condensation on the sensor tip as this will affect the
accuracy enormously.
S452 5

1 Safety instructions
Storage and transportation
•Make sure that the transportation temperature of the sensor
without display is between -30 ... +70°C and with display between
-10 ... +60°C.
•For transportation it is recommended to use the packaging which
comes with the sensor.
•Please make sure that the storage temperature of the sensor is
between -10 ... +50°C.
•Avoid direct UV and solar radiation during storage.
•For the storage the humidity must be <90% with no condensation.
2 Registered trademarks
SUTO®Registered trademark of SUTO iTEC
MODBUS®Registered trademark of the Modbus Organization,
Hopkinton, USA
HART®Registered trademark of the HART Communication
Foundation, Austin, USA
Android™,
Google Play
Registered trademarks of Google LLC
6 S452

3 Application
3 Application
The S452 Thermal Mass Flow Meter is designed for the e plosive areas
and is mainly used to measure compressed air and process gases in
industrial environments.
The S452 can measure the following parameters for the compressed air
or gases:
•Velocity
•Volume flow
•Total consumption
The default factory settings are: Velocity in m/s, Volume flow in m3/h
and Total Consumption in m3. Other units can be programmed by the
optional display or the service kit.
4 Features
•Direct measurement of mass flow and standard flow without the
need of pressure and temperature compensation.
•In-line types for smaller pipes.
•No moving parts, no clogging.
•All sensor parts which come into contact with the measurement
medium are made of stainless steel 316L.
•Robust metal enclosure suitable for outdoor applications in harsh
environments.
•Wireless Bluetooth interface for sensor settings onsite
•Optional display on the sensor, showing flow rate, consumption,
medium temperature and diagnostic result.
S452 7

5 Technical data
5 Technical data
5.1 General data
Measuring range 0.4 ... 92.7 sm/s (standard range calibration)
0.8 ... 185 sm/s (ma range calibration)
1.0 … 224 sm/s (high speed calibration)
(See section Flow ranges for flow measurement
ranges in different tube diameters)
* sm/s: standard meter per second
Parameters Standard unit flow: m3/h
Available units: m3/min, l/min, l/s, cfm, kg/h,
kg/min, kg/s
Standard velocity unit: m/s
Reference conditions ISO1217, 20°C, 1000 mbar (Standard-Unit)
DIN1343, 0°C, 1013.25 mbar (Norm-Unit)
Principle of
measurement
Thermal mass flow
Sensor PT20 / PT1000
Measured medium Air, gas (non corrosive gas)
Operating temperature -40 ... +100°C (medium temperature)
-40 ... +65°C (ambient temperature)
Humidity of the
measured medium
< 90%, no condensation
Operating pressure 0 ... 4.0 MPa
Housing material Al alloy
Material of the probe
tube, sensor head and
the screwing
Stainless steel 1.4404 (SUS 316L)
Protection class IP67
Dimensions See Chapter Dimensional drawing.
Display (optional) Graphic display, 128 64
Tube diameter DN15 ... DN80
Screwing thread M32 1.5
8 S452

5 Technical data
Weight 1.25 kg (instrument only, and the measuring
section is not included)
5.2 lectrical data
Power supply 16 ... 30 VDC, 5 W
5.3 Output signals
Analog output See section 9.1.1
Pulse output See section 9.1.2
HART output See section 9.2
Modbus output See section 9.3
M-Bus output See section 9.4
5.4 Accuracy
Accuracy* ±(1.5% of reading + 0.3% full scale)
Stated accuracy at: Ambient/process temperature +23°C ±3°C
Ambient/process humidity <90%, no
condensation
Process pressure at 0.6 MPa
Repeatability 0.25% of reading
* The specified accuracy is valid only within the minimum and ma imum
flow rates that are stated in Section 5.5.
5.5 Flow ranges
The stated flow ranges are valid under the following conditions:
Standard flow in air; Reference pressure: 1000 hPa; Reference
Temperature: +20°C
Inch DN S-Range (m3/h) M-Range (m3/h) HS-Range (m3/h)
½” DN15 0.2 ... 45.6 0.4 ... 91.0 0.48 ... 110
¾” DN20 0.4 ... 89.1 0.9 ... 178 1.09 ... 215
1” DN25 0.6 ... 148 1.2 ... 295 1.82 ... 357
1½” DN40 1.5 ... 367 2.9 ... 732 4.36 ... 886
2” DN50 2.4 ... 600 4.8 ... 1,198 7.26 ... 1,450
2½” DN65 4.1 ... 1,027 8.2 ... 2,049 --
3” DN80 5.7 ... 1,424 11.4 ... 2,841 --
S452 9

5 Technical data
Remarks:
•To calculate flow ranges based on pipe and reference conditions in
your site, download and install the "Flow range calculator" tool for
free from http://www.suto-itec.com.
•To fast access the tool download page, enter "flowrange" (without
spaces) in the search field and click the search result.
•The total consumption value is saved to the permanent memory
every 5 minutes. If within these 5 minutes the device is powered
off, it will restore the last consumption value which was saved in
the last cycle.
10 S452

6 Dimensional drawing
6 Dimensional drawing
6.1 Thread type
Unit: mm
Type
Pipe
nominal
size
inch (DN)
L
total
length
(mm)
L1
inlet
length
(mm)
H
total
height
(mm)
H1
from pipe
center to
casing top
(mm)
R
xternal
Thread
S452-1/2” 1/2”(DN15) 300 210 210.8 200.15 R 1/2”
S452-3/4” 3/4”(DN20) 475 275 213.6 200.15 R 3/4”
S452-1” 1” (DN25) 475 275 217 200.15 R 1”
S452-1¼” 1¼”(DN32) 475 275 221.35 200.15 R 1¼”
S452-1½” 1½”(DN40) 475 275 224.3 200.15 R 1½”
S452-2” 2” (DN50) 475 275 230.3 200.15 R 2”
S452-2½” 2½”(DN65) 475 275 246 208 R 2½ ”
S452-3” 3” (DN80) 475 275 259 214.5 R 3”
S452 11

6 Dimensional drawing
6.2 Flange type
Unit: mm
Type
Pipe
nominal
size
inch (DN)
L
total
length
(mm)
L1
inlet
length
(mm)
H
total
height
(mm)
H1
from pipe
center to
casing top
(mm)
Flange ( N 1092-1
PN40)
ØD
(mm)
ØK
(mm)
n ØL
(mm)
S452-1/2” 1/2”(DN15) 300 210 247.65 200.15 95 65 4 Ø14
S452-3/4” 3/4”(DN20) 475 275 252.65 200.15 105 75 4 Ø14
S452-1” 1” (DN25) 475 275 257.65 200.15 115 85 4 Ø14
S452-1¼” 1¼”(DN32) 475 275 270.15 200.15 140 100 4 Ø18
S452-1½” 1½”(DN40) 475 275 275.15 200.15 150 110 4 Ø18
S452-2” 2” (DN50) 475 275 282.65 200.15 165 125 4 Ø18
S452-2½” 2½”(DN65) 475 275 300.55 208 185 145 8 Ø18
S452-3” 3” (DN80) 475 275 314.45 214.5 200 160 8 Ø18
12 S452

6 Dimensional drawing
Type
Pipe
nominal
size
inch (DN)
L
total
length
(mm)
L1
inlet
length
(mm)
H
total
height
(mm)
H1
from pipe
center to
casing top
(mm)
Flange (ANSI/B16.5
Class 300)
ØD
(mm)
ØK
(mm)
n ØL
(mm)
S452-1/2” 1/2” (DN15) 300 210 247.65 200.15 95.2 66.5 4 Ø15.7
S452-3/4” 3/4”(DN20) 475 275 258.85 200.15 117.3 82.5 4 Ø19
S452-1” 1” (DN25) 475 275 262.15 200.15 123.9 88.9 4 Ø19
S452-1¼” 1¼”(DN32) 475 275 266.85 200.15 133.3 98.5 4 Ø19
S452-1½” 1½”(DN40) 475 275 277.85 200.15 155.4 114.3 4 Ø22.3
S452-2” 2” (DN50) 475 275 282.75 200.15 165.1 127 4 Ø19
S452-2½” 2½”(DN65) 475 275 303.35 208 190.5 149.3 8 Ø22.3
S452-3” 3” (DN80) 475 275 317.25 214.5 209.5 168.1 8 Ø22.3
S452 13

7 Determining the installation point
7 Determining the installation point
To maintain the accuracy stated in the technical data, the sensor must
be inserted in the center of a straight pipe section with unhindered flow
characteristics.
Unhindered flow characteristics are achieved if the section in front of the
sensor (inlet) and behind the sensor (outlet) are sufficiently long,
absolutely straight and free of obstructions such as edges, seams,
curves and so on.
Please consider that enough space e ists at your site for a adequate
installation as described in this manual.
ATT NTION!
Wrong measurement is possible if the sensor is not
installed correctly.
•Pay attention to the design of the inlet and outlet section.
Obstructions can cause counter-flow turbulence as well as
turbulence in the direction of the flow.
•It is strongly recommended not to install S452 permanently in wet
environment which e ists usually right after a compressor outlet.
14 S452

7 Determining the installation point
7.1 Additional inlet and outlet sections
The S452 with tube diameters from DN15 to DN25 already has the
required inlet and outlet sections. No additional straight sections are
needed.
For the S452 with diameters from DN32 to DN80, the S452 has a
shortened inlet section and requires additional straight sections at the
inlet and outlet. The additional length for the particular diameters are
listed in the table below.
Flow obstructions
before the
measurement
section
Additional
length for
DN32
[mm]
Additional
length for
DN40
[mm]
Additional
length for
DN50
[mm]
Additional
length for
DN65
[mm]
Additional
length for
DN80
[mm]
inlet outlet inlet outlet inlet outlet inlet outlet inlet outlet
Slight curve
(bend <90°C)
175 - 227.8 9.5 362.2 65.5 551.8 144.5 760.8 204.5
Reduction (Tube
narrows towards
measurement
section)
265 - 353.5 9.5 521,5 65.5 758.5 144.5 938.5 204.5
E pansion (Tube
e pands towards
measurement
section)
265 - 353.5 9.5 521.5 65.5 758.5 144.5 938.5 204.5
90°C bend or T
piece
265 - 353.5 9.5 521.5 65.5 758.5 144.5 938.5 204.5
2 90°C bends on
one level
445 - 563 9.5 787 65.5 1103 144.5 1343 204.5
2 90°C bends 3
dimensional change
of direction
985 - 1191.5 9.5 1583.5 65.5 2136.5 144.5 2556.5 204.5
Shut-off valve 1345 - 1610.5 9.5 2114.5 65.5 2825.5 144.5 3365.5 204,5
S452 15

8 Installation
8 Installation
Before installing the sensor, make sure that all components listed below
are included in your package.
Qty Description Part no.
1 S452 Thermal Mass Flow
Meter
S695 0452
1 Sealing ring No P/N
1 Measuring section A1301 ... A1306 (R thread)
A1321 … A1328 (Flange, EN-1092-1)
A1341 … A1348 (Flange, ANSI 16.5)
1 Bluetooth dongle No P/N
1 USB disk (with the service
Software stored)
No P/N
1 Instruction manual No P/N
1 Calibration certificate No P/N
8.1 Installing the S452
The S452 is shipped with the mounted measurement section. When
installing the device, please make sure the following:
•The flow direction indicated on the S452 housing is consistent with
the flow direction of the compressed air or gas.
•The gas flows from the inlet (long pipe section) to the outlet (short
pipe section) as illustrated in the picture below.
16 S452

8 Installation
8.2 Removing the S452
The following steps e plain the procedure of an appropriate removal of
the S452.
ATT NTION!
Only remove the flow meter if the system is in a
pressure-less condition.
1. Hold the S452.
2. Release the terminal nut at the
connection thread.
3. Pull out the shaft slowly.
4. The measuring section can be closed
with the optional closing cap so the
system can work normally during
maintenance.
8.3 Re-installation after maintenance
•The re-installation of the measurement device is simple because
the S452 fits into the pipe section only in one position.
•Make sure that the O-shaped sealing ring is installed.
S452 17

8 Installation
•Tighten the terminal nut to secure the S452.
8.4 lectrical connection
When installing the cables please consider following points:
•Keep the stripped and twisted length of cable shield as short as
possible.
•Screen and ground the signal lines.
•Unused cable entries must be closed with closers.
•Cable outer diameter should be between 6 and 8 mm.
•Single wire cross section area must be between 0.25 ... 0.75 mm2.
•The thread size for the cable glands is M20 / 1.5.
8.4.1 Connection diagram
Remove the back cover from the S452, and the pin layout is shown
below.
8.4.2 Pin assignment
The S452 provides four output options. The pin assignment of these
options are given in the following table.
Pin Output options
Pulse and analog Modbus M-Bus HART
18 S452

8 Installation
1 GNDSDI GNDSDI GNDSDI GNDSDI
2 +VB+VB+VB+VB
3 -VB-VB-VB-VB
4 SDI SDI SDI SDI
5 DIR DIR DIR DIR
6 DIR DIR DIR DIR
7 SW SW SW NA
8 SW SW SW NA
9 -I1-I1-I1-I1 / -HART
10 +I1+I1+I1+I1 / +HART
11 -I2+D M1 NA
12 +I2-D M2 NA
13 NA GNDMNA NA
14 Earth Earth Earth Earth
15 Earth Earth Earth Earth
16 Earth Earth Earth Earth
Legend to pin assignment
SDI Digital signal (internal use) SW Isolated pulse output
GNDSDI Ground for SDI DIR Flow direction input
+VBPositive supply voltage D+ Modbus data+
-VBNegative supply voltage D- Modbus data -
+l1Positive signal output (analog 1) M M-Bus data
-I1Negative signal output (analog 1) NA Not applicable
+l2Positive signal output (analog 2)
-I2Negative signal output (analog 2)
S452 19

9 Signal outputs
9 Signal outputs
9.1 Analog and pulse outputs
If the S452 is purchased with the output option of analog and pulse
signals, it provides 2 analog outputs and 1 pulse output. All signals are
electrically isolated.
9.1.1 Analog output
The analog output can be used as an active output (current is sourced
through the positive connection pin) or passive output. In the passive
configuration a current signal is modulated into the e ternal signal
voltage.
Active : 4 to 20mA, RL < 400 Ω
Passive : 4 to 20mA, supply voltage 18... 30 VDC, RL < 500 Ω
For HART : RL ≥ 250 Ω
Uncertainty : < 0.3 % of reading
Resolution : 0.005 mA
9.1.2 Pulse output
No switch, no polarity required, galv. Isolate
Ma . rating : 30 VDC, 200 mA
Pulse width : 10 ... 100 msec (depending on flow rate)
The ma imum number of pulse per second is limited to 45 pulse per
second. As a result depending on the flow rate and the selected
consumption unit the ma imum flow rate is limited to the values in the
table below.
20 S452
Other manuals for S452
2
This manual suits for next models
9
Table of contents
Other SUTO Measuring Instrument manuals
Popular Measuring Instrument manuals by other brands
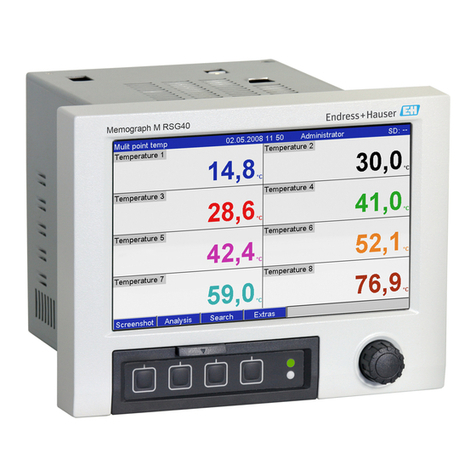
Endress+Hauser
Endress+Hauser Memograph M RSG40 Brief operating instructions
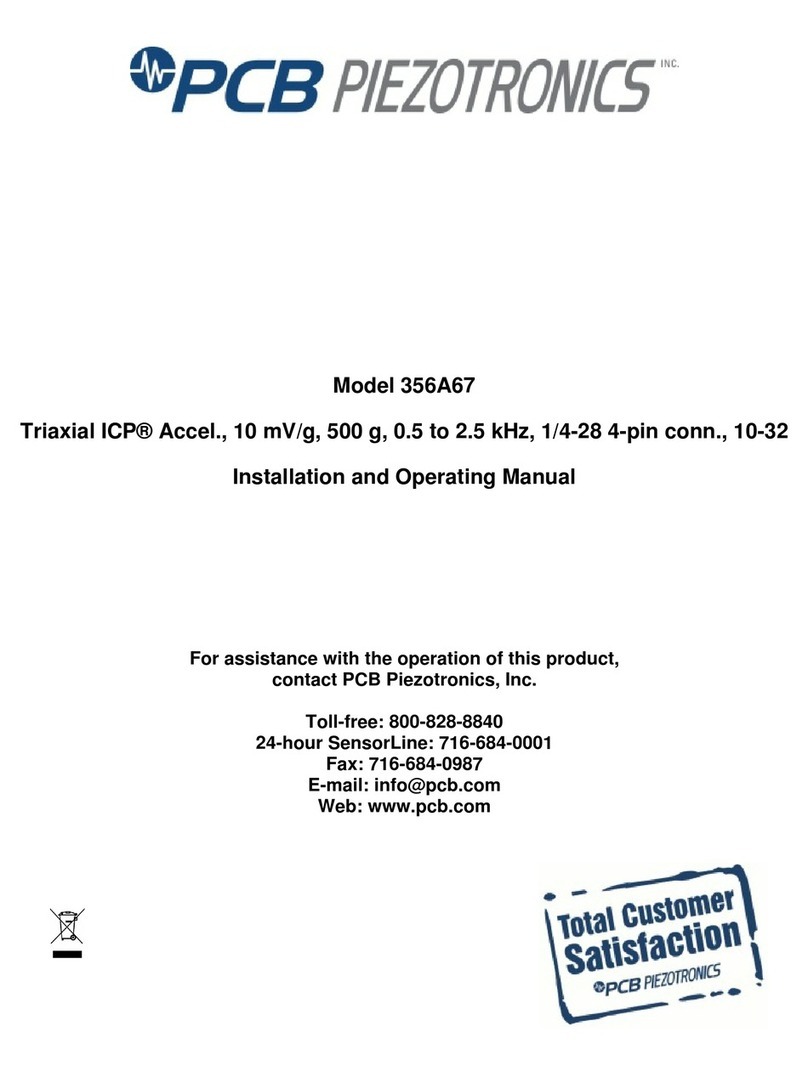
PCB Piezotronics
PCB Piezotronics 356A67 Installation and operating manual
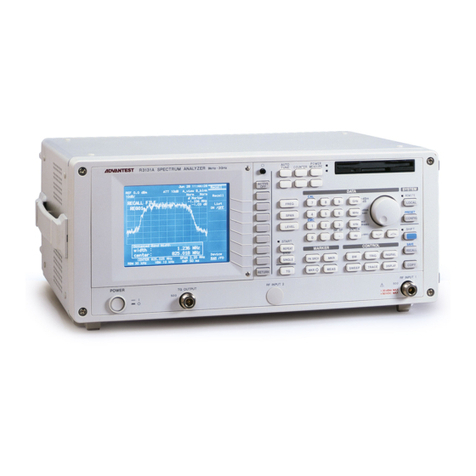
ADVANTEST
ADVANTEST R3131 Series Operation manual
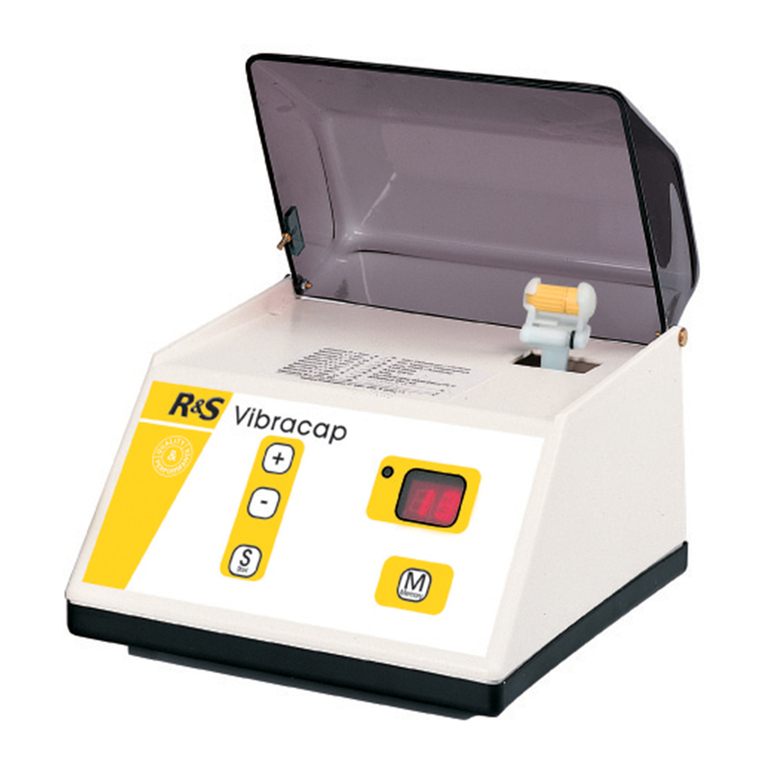
R&S
R&S Vibracap Instructions for use
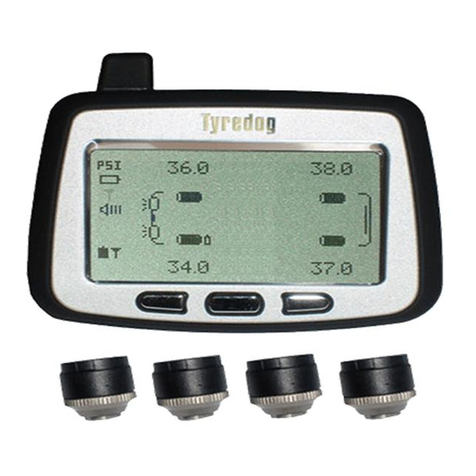
Tyredog
Tyredog TD2000A-X owner's manual
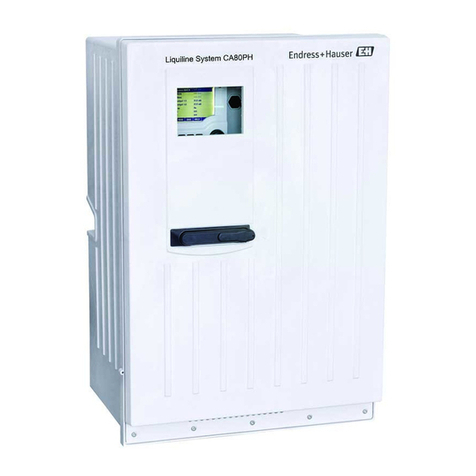
Endress+Hauser
Endress+Hauser Liquiline System CA80PH Brief operating instructions