Mandik FDMC Configuration guide


1
TPM 083/12
II. GENERAL INFORMATION 2
1. Description......................................................................................................................... 2
2. Damper Design..…............................................................................................................. 3
3. Communication and control devices..............….................................................................. 6
4. Dimensions, weights........................................................................................................... 9
5. Placement and Assembly.................................................................................................... 10
6. Statement of installations.................................................................................................... 12
7. Suspension of fire dampers................................................................................................. 18
III. TECHNICAL DATA 21
8. Pressure loss...................................................................................................................... 21
9. Coefficient of local pressure loss......................................................................................... 21
10. Noise data......................................................................................................................... 22
IV. MATERIAL, FINISHING 24
11. Material............................................................................................................................. 24
VI. INSPECTION, TESTING 24
12. Inspection, testing............................................................................................................. 24
VI. TRANSPORTATION AND STORAGE 24
13. Logistic terms.................................................................................................................... 24
VII. ASSEMBLY, ATTENDANCE, MAINTENANCE AND REVISIONS 24
14. Assembly.......................................................................................................................... 24
15. Entry into service and revisions......................................................................................... 24
VIII. DATA OF PRODUCT 25
16. Data label.......................................................................................................................... 25
17. Quick review..................................................................................................................... 25
IX. ORDERING INFORMATION 26
18. Ordering key..................................................................................................................... 26
I. CONTENT
These technical specifications state a row of manufactured sizes and models of fire dampers (further only dampers)
FDMC. It is valid for production, designing, ordering, delivery, assembly and operation.

2
TPM 083/12
II. GENERAL INFORMATION
1. Description
1.1. Fire dampers are shutters in duct systems of air-conditioning devices that prevent spreading the
fire and combustion products from one fire segment to the other one by means of closing the air
duct in the points of fire separating constructions.
Dampers blade automatically closes air duct using a shutting spring or an actuating mechanism
back spring. The back spring of the actuating mechanism is started when the thermoelectrical
starting mechanism BAE 72B-S is activated, when a reset button on BAE 72B-S is pushed or
when a power supply of the actuating mechanism is stopped.
The damper is sealed with a silicon packing against smoke penetration after closing the blade. At
the same time, the damper blade is bedded in a material which enlarges its capacity and air
proofs the air duct.
Dampers have one inspection hole, since the shutting device and the inspection hole can be set
into the most advantageous position (with respect to the operation and manipulation with the
control device).
Fig. 1 Fire damper FDMC
1.2. Damper characteristics
• CE certified acc. to EN 15650
• Tested in accordance with EN 1366-2
• Classified acc. to EN 13501-3+A1
• Fire resistance EIS 60
• External Casing leakage class min. C, Internal leakage class 3 (D=200 - 400 mm) and class 2
(D=180 mm) and class 1 (D=100 - 160 mm) acc. to EN 1751
• Cycling test in class C 10000 acc. to EN 15650
• Corrosion resistant acc. to EN 15650
• ES Certificate of conformity No. 1391-CPR-0090/2014
• Declaration of Perfomance No. CDM/FDMC/001/14
• Hygienic assessment of fire dampers - Report No. 1.6/13/16/1
-1
1.3. Working conditions
Exact damper function is provided under the following conditions:
a) Maximum air circulation speed: 12 m.s
Maximum pressure difference: 1500 Pa
b) Dampers could be displaced into position “CLOSED” only in case that ventilator, or Air
Handling Unit is switched off. The goal is the securing of proper closing and safe
function of Fire Damper in case of Fire.
c) The air circulation in the whole damper section must be secured as steady on whole
surface.

3
TPM 083/12
Operation of the dampers does not depend on the direction of air circulation. The dampers can
be located in an arbitrary position.
Dampers are suitable for systems without abrasive, chemical and adhesive particles.
Dampers are designed for macroclimatic areas with mild climate according to EN 60 721-3-3.
Temperature in the place of installation is permitted to range from - 20°C to + 50°C.
2. Damper design
2.1. Design with actuating mechanism
Actuating mechanism
BAT
Fig. 2 Fire damper FDMC - actuating mechanism
Design .40, .50
Design with an actuating mechanism BFL 230-T or BFL 24-T (further only "actuating mecha-
nism"). After being connected to power supply AC/DC 24V or 230V, the actuating mechanism
displaces the damper blade into operation position "OPEN" and at the same time it pre-stretches
its back spring. When the actuating mechanism is under voltage, the damper blade is in the
position "OPEN" and the back spring is pre-stretched. Time needed for full opening of the flap
blade from the position "CLOSED" to the position "OPEN" is maximum 140s. If the actuating
power supply is cut off (due to loss of supply voltage, activation of thermoelectrical actuating
mechanism or pushing the reset button on the thermoelectrical starting mechanism BAT), the
back spring displaces the damper blade into the breakdown position "CLOSED". The time of
displacing the blade from the position "OPEN" to the position "CLOSED" takes maximum 20 s. In
case that the power supply is restored again (the blade can be in any position), the actuating
mechanism starts to re-displace the damper blade into the position "OPEN".
A thermoelectrical starting mechanism BAT, which contains three thermal fuses Tf1 and Tf2, is a
part of the actuating mechanism. These fuses are activated when temperature +72 °C has been
exceeded (the fuse Tf1 when the temperature around the damper and the fuses Tf2 when the
temperature inside the air-conditioning piping has been exceeded). After the thermal fuse Tf1 or
Tf2 has been activated, the power supply is permanently and irreversibly cut off and the actuating
mechanism, by means of the pre-stretched spring, displaces the damper blade into the
breakdown position "CLOSED".
Signalling of blade positions "OPEN" and "CLOSED" is ensured by two firmly set integrated limit
switches.

4
TPM 083/12
Fig. 3 Actuating mechanism BELIMO BFL 230-T
BFL 230-T
BFN 230-T
12 S3S1 S2 S5S4 S6
AC230 V, open-close
NL1
Caution: Power supply voltage!
<5° <80°
AT
Tf Tf LED
Notes
The actuator must be protected by a fuse that does not exceed 16 A.
Parallel connection of other actuators possible. Observe the performance data.
Combination of power supply voltage and safety extra-low voltage not permitted
at the both auxiliary switches.
1 = blue
Cable colours:
2 = brown
S1 = violet
S2 = red
S3 = white
S4 = orange
S5 = pink
S6 = grey
Fig. 4 Actuating mechanism BELIMO BFL 24-T(-ST)
BFL 24-T
BFN 24-T
12 S3S1 S2 S5S4 S6
AC/DC 24 V, open-close
Connection via safety isolating transformer.
<5° <80°
AT
Tf Tf LED
Notes
Parallel connection of other actuators possible. Observe the performance data.
Combination of power supply voltage and safety extra-low voltage not permitted
at the both auxiliary switches.
~
- +
Plug connection to communication
and power supply units:
Application examples for integration
into monitoring and control systems
or into bus networks can be found in
the documentation of the connected
communication and power supply unit.
(-ST)
1 = blue
Cable colours:
2 = brown
S1 = violet
S2 = red
S3 = white
S4 = orange
S5 = pink
S6 = grey
Actuating mechanism BELIMO BFL, BFN 230-T BFL, BFN 24-T(-ST)
Nominal voltage AC 230 V 50/60 Hz AC 24 V 50/60 Hz
DC 24 V
Power consumption - motoring
- holding 3,5/5 W
1,1/2,1 W 2,5/4 W
0,8/1,4 W
Dimensioning 6,5/10 VA (Imax 4 A @ 5 ms) 4/6 VA (Imax 8,3 A @ 5 ms)
Protection class II III
Degree of protection IP 54
Running time - motor
- spring return <60 s
~ 20 s
Ambient temperature
- normal duty
- safety duty
- non-operating temperature
- 30 °C … 55 °C
The safe position will be attained up to max. 75°C
- 40 °C … 55 °C
Connecting - motor
- auxiliary switch cable 1 m, 2 x 0,75 mm (BFL/BFN 24-T-ST) with 3-pin plug-in connectors
cable 1 m, 6 x 0,75 mm (BFL/BFN 24-T-ST) with 6-pin plug-in connectors
Thermal trips duct outside temperature 72 °C
duct inside temperature 72 °C
2
2
Tab. 2.1.1. Actuating mechanism BELIMO BFL24-T(-ST), BFN 24-T(-ST), BFL 230-T a BFN 230-T

5
TPM 083/12
2.3. Design with the communication and supply device
Design .60
Design with the communication and supply device BKN 230-24 and the actuating mechanism
BFL 24-T-ST. It simplifies electrical wiring and interconnection of fire damper. It facilitates on site
check and enables central control and checks of fire damper by means of a simple 2-conductor
wiring.
BKN 230-24 functions as a decentralized network device for supplying the actuating mechanism
BFL 24-T-ST with a spring back drive on one hand and on the other hand it transmits the signal
information about the fire damper position OPERATION and FAILURE through 2-conductor
wiring to the central. Control command SWITCHED ON - SWITCHED OFF from the central
through BKN 230-24 goes through the same wiring to the actuating mechanism.
To simplify the connection, the actuating mechanism BFL 24-T-ST is equipped with connecting
plugs that are inserted directly to BKN 230-24. BKN 230-24 is supplied with a conductor and an
EURO plug to be connected to the 230V mains.
2- conductor wiring is connected to BKN 230-24 by means of terminals 6 and 7.
If the drive is supposed to be controlled without any signal from the central, it can be switched on
by means of a bridge between the terminals 3 and 4. A green LED pilot light on BKN 230-24 is
on when voltage is present in the drive (AC 24V). If the button on BAE 72-S is switched on or if
the power supply (e.g. by a signal from ELECTRICAL FIRE SIGNALISATION) is disconnected,
the fire damper position will be "FAILURE".
Communication and supply device BKN 230-24 has to be placed near the damper. It is necessary
for easy connection of actuating system equipped by BKN 230-24 device.
Fig. 5 Fire damper FDMD with actuating mechanism
and BKN
BAT
BKN
Actuating mechanism
Tab. 2.3.1. Communication and Supply Device BKN 230-24
2
Communication and Supply Device BKN 230-24
Nominal voltage AC 230V 50/60Hz
Power consumption 3,5 W (operating position)
Dimensioning 11 VA (including actuating mechanism)
Protection Class II
Degree of protection IP 42
Ambient Temperature
Storage Temperature - 30 °C … + 50 °C
- 40 °C … + 50 °C
Connection - mains
- drive
- terminal board
Cable 0,9 m with EURO plug of 26 type
6 pole plug, 3 pole plug
screw terminals for conductor 2x1,5 mm

6
TPM 083/12
Fig. 6 Communication and Supply Device BKN 230-24
Tab. 2.3.2. Communication and Supply Device BKN 230-24
2
Communication and Supply Device BKN 230-24
Nominal voltage AC 230V 50/60Hz
Power consumption 3,5 W (operating position)
Dimensioning 11 VA (including actuating mechanism)
Protection Class II
Degree of protection IP 42
Ambient Temperature
Storage Temperature - 30 °C … + 50 °C
- 40 °C … + 50 °C
Connection - mains
- drive
- terminal board
Cable 0,9 m with EURO plug of 26 type
6 pole plug, 3 pole plug
screw terminals for conductor 2x1,5 mm
3.1. BKS 24-9A communication and control device is used for group control and checks of 1 to 9 fire
dampers with the actuating mechanism BFL 24-T-ST in connection with the supply and
communication device BKN 230-24. Signalisation of the damper position is individual; the
dampers can be controlled and tested only as a group. BKS 24-9A is intended for use in the
distribution board and displays the operation situations and failure reports of the connected fire
dampers. It is possible to signalise functions such as the damper position and failure reports or to
transmit them further to the system by means of integrated auxiliary switches. BKS 24-9A
receives signals from BKN 230-24 through the two-conductor wiring and issues control
commands. Proper damper operation is indicated by two light LED diodes:
Control ON = position OPERATION
Control OFF = position FAILURE
If the fire dampers do not reach the given position in time tolerable for displacing, the appropriate
light diode FAILURE starts to flash and K1 contact is opened (current failure). In case that the
faulty damper finally reaches its given position, K1 is closed and the failure report lights up shines
(the failure is saved in memory).
K2 - the auxiliary contact - is used for signalisation of the flap position to the master device. Function
of this auxiliary contact can be programmed through the terminal 14 according to the Tab. 3.1.1.
3. Comm nication and control devices

7
TPM 083/12
Fig. 7 Communication and Control Device BKS 24-9A
3.2. BKS 24-1B communication and control device is used for control and checks of fire dampers with
the BFL 24-T-ST actuating mechanism in conjunction with the BKN 230-24 supply and
communication device. BKS 24-1B receives information about the situation of the fire damper
through the BKN 230-24 supply and communication device and issues controlling commands.
The device is intended for building in into the distribution board. Light diodes on the front side of
the device indicates the operating situations of the damper and breakdowns of the whole system.
Nonpotential auxiliary contacts enable connection to the master control system (indication of the
damper position, failure reports, release of the ventilators etc.).
Tab. 3.1.1. BKS 24 -9A contacts K1 and K2
K1 Function Contact
Situation State
Current Failure 15 16
No Failure 15 16
Programming K2 Auxiliary Contact
Function Interconnection State
K2 contact is on if all the
damperss are open 14 11
17 18
K2 contact is on if the damper
No. 1 is open 14 12
K2 contact is on if all the
dampers are closed 14 open
Function check can be done in the position OPERATION by means of pushing the TEST button.
While the button is pushed, the flap blade is turning into the position FAILURE. Fault function is
indicated by a report "FAILURE".
2
Tab. 3.1.2. Communication and Control Device BKS 24-9A
Communication and Control Device BKS 24-9A
Nominal voltage AC 24 V 50/60Hz
Power consumption 3,5 W (operating position)
Dimensioning 5,5 VA
Protection Class III (safe small voltage)
Degree of protection IP 30
Ambient Temperature 0 … + 50 °C
Connection Terminals for conductor 2 x 1,5 mm

8
TPM 083/12
3.3. BKS 24-1B communication and control device is used for control and checks of fire dampers with
the BFL 24-T-ST actuating mechanism in conjunction with the BKN 230-24 supply and
communication device. BKS 24-1B receives information about the situation of the fire damper
through the BKN 230-24 supply and communication device and issues controlling commands.
The device is intended for building in into the distribution board. Light diodes on the front side of
the device indicates the operating situations of the damper and breakdowns of the whole system.
Fig. 8 Communication and control device BKS 24-1B
Tab. 3.3.1. Communication and Control Device BKS 24-1B
Communication and Control Device BKS 24-1B
Nominal voltage AC 24 V 50/60Hz
Power consumption 2,5 W (operating position)
Dimensioning 5 VA
Protection Class III (safe small voltage)
Degree of protection IP 30
Ambient Temperature 0 … + 50 °C
Connection Into ZSO-11 connector which is not a part of BKS 24-1B.
ZSO-11 connector has screw terminals 11 x 1,5 mm
4
BKS2 -1B
7
8
2
10
1
5
9
an insulation
transformer
~
AC 24 V
damper position
breakdown
Notice: Relay contacts are drawn
without power
11
b
a
2-conductor wiring
to KN230-24
Control
on /off
Reset
Test
External buton
optional
be interchanged
6
3
AC
24V
damper position
operation
Reset
Test
open
closed
alarm
failure
Connection through
conection can
Power supply AC 2 V
Check test cca 35sec
, starting with switching AC 24 on or pressing
«Reset/Test» button
Current failure,
possible cause: • short circuit or interruption of 2-conductor wiring
or damper failure (at KN..) • Power supply AC 230V missing • defective
thermoelectrical starting • smoke detector activated • exceeded operation time
Failure saved in memory
• Fault in system signalled, system check should be
done
Damper (drive) turning into
the direction
of breakdown position
Damper (drive) in
breakdown position
Damper (drive) turning into
the direction
of operating position
Damper (drive) in
operating position
Signals and diagnosis
light diodes contacts Description
Cause/Course
state
open closed alarm
closed
flashing
63
6 3
6 7
64
6 4
63
63
67
switched
closed closed
closed closed
closed closed
closed
closed
closed
closed
closed
closed
closed
closed
open open open
open
open
open
flashing
flashing
• damper blocked
not available
2

9
TPM 083/12
Fig. 9 Fire damper FDMC, design with actuating mechanism
Position:
1 Damper casing
2 Damper blade
10 Inspection hole covering
14 BAT thermoelectrical starting
mechanism
15 Actuating mechanism
BUILT-IN EDGE
4.2. Weight and effective area
Tab. 4.2.1. Weight and effective area
Size
D a Weight Effective area Sef [m ] Actuating mechanism
100 - 3,1 0,0036 BFL
125 - 3,4 0,0068 BFL
140 - 3,6 0,0092 BFL
150 - 3,7 0,0109 BFL
160 - 3,8 0,0129 BFL
180 - 4,1 0,0172 BFL
200 - 4,4 0,0222 BFL
225 - 4,7 0,0293 BFL
250 9 5,5 0,0374 BFL
280 24 6 0,0484 BFL
315 41,5 6,6 0,0630 BFL
350 59 7 0,0793 BFL
355 61,5 7,3 0,0821 BFL
400 84 8,2 0,1065 BFL
2
4.1. Dimensions
4. Dimensions, weights

10
TPM 083/12
Fig. 10 Blades overlaps
4.3. Blades overlaps
Tab. 4.3.1 Blades overlaps
Blades overlaps Dimension Overlaps
FDMC
Fig. 10 Side without act. mechanism "a" Tab. 4.2.1
These values has to be respected when projecting related air-conditioning ducts.
5.1. Fire dampers are suitable for installation in arbitrary position in vertical and horizontal passages
of fire separating constructions. Damper assembly procedures must be done so as all load
transfer from the fire separating constructions to the damper body is absolutely excluded.
Back-to-back air-conditioning piping must be hung or supported so as all load transfer from the
back-to-back piping to the damper is absolutely excluded. Installation gap must be filled by
approved material perfectly in all the installation space volume (installation gap).
To provide needed access space to the control device, all other objects must be situated at least
350 mm from the control parts of the damper. Inspection hole must be accessible.
Damper blade has to be inside of construction (labelled with BUILD IN EDGE on the damper
body) after installation. The fire damper can also be installed outside the wall construction. Duct
and the damper part between the wall construction and the damper blade (labelled with BUILD
IN EDGE on the protective covering) must be protected with firefighting insulation (see fig. 12).
The distance between the fire damper and the construction (wall, ceiling) must be minimum
75 mm. In case that two or more dampers are supposed to be installed in one fire separating
construction, the distance between the adjacent dampers must be at least 200 mm according to
EN 1366-2 paragraph 13.5.
Exceptions are given in chapter 6.
5. Placement and Assembly

11
TPM 083/12
Fig. 11 The distance between the fire damper and the
construction
min. 200
min. 75
min. 75
Fig. 12 Built-in edge - design with outer mechanical
control or actuating mechanism
260
420
(50)
BUIL-IN EDGE
BUILT-IN EDGE
BUILT-IN EDGE
Fig. 13 Installation opening Fig. 14 Installation opening
5.2. The control mechanism has to be protected (covered) against damage and pollution during
installation process. All fire dampers has to be closed during installation process. The damper
body should not be deformed in the course of bricking in. Once the damper is built in, its blade
should not grind on the damper body during opening or closing.
5.3. Installation opening dimensions (see Fig. 13-14)
5.4. The control mechanism has to be protected (covered) against damage and pollution during
installation process.
All fire dampers has to be closed during installation process. The damper body should not be
deformed in the course of bricking in. Once the damper is built in, its blade should not grind on
the damper body during opening or closing.

12
TPM 083/12
6. Statement of installations
6.1. Statement of installations the fire dampers FDMB and their fire resistance Tab. 6.1.1.
Tab. 6.1.1. Statement of installations
Construction Installation Material of stuffing box Figure
Solid wall
construction
Wet Mortar or gypsum 15
Wet, installation next to
wall, ceiling Mortar or gypsum 17
Dry Stuffing box and fire protection
mastic 16
Solid ceiling
construction
Mokré Mortar or gypsum 18
Dry Stuffing box and fire protection
mastic 19
Gypsum wall
construction
Wet Mortar or gypsum 20
Wet, installation next to
wall, ceiling Mortar or gypsum 22
Dry Stuffing box and fire protection
mastic 21

13
TPM 083/12
6
4
≥50
3
2
≥40
≥100
1
5
3
4
1
≥40
≥100
POSITION:
1 Fire damper FDMC
2 Solid wall construction
3 Mortar or gypsum
4 Duct
2
Fig. 16 Solid wall construction - stuffing box and fire protection mastic
POSITION:
1 Fire damper FDMC
2 Solid wall construction
3 Mineral stone wool min. density 140 kg/m
4 Fire protection mastic min. thickness 1 mm
5 Glass fiber felt with aluminium foil width 50 mm, thickness 5 mm
6 Duct
3
Used materials - example*:
3 - Promapyr, Rockwool Steprock HD
4 - Promastop - P, K
EIS 60
EIS 60
* Stuffing box and fire protection mastic can be replaced by another approved
fire sealing system for damper installation with equivalent material properties.
Fig. 15 Solid wall construction - mortar or gypsum

14
TPM 083/12
Fig. 17 Solid wall construction - installation next to wall, ceiling - mortar or gypsum and mineral wool
≥100
(≥100)+50
A-A
3
2
2
3
POSITION:
1 Fire damper FDMC
2 Mortar or gypsum
3 Mineral stone wool min. density 140 kg/m3
A
A
2
1
3
D-20
3
10 to 50
10 to 50
≤D+100
1
2
2
1
3
D-20
≥100
B-B
2
2
B
B
10 to 50
10 to 50
≤D+100
1
2
2
1
2
1
EIS 60
Notice:
●Gap between damper and construction is filled by mortar or
gypsum and mineral wool
●Wool is fixed to damper body and construction by fire protection
mastic.
●Mineral wool thickness = construction thickness + 50 mm
●Damper axis has to be horizontal
●Installation is valid for ceiling construction

15
TPM 083/12
1
3
6
≥40
150*
2
4
≥50
5
POSITION:
1 Fire damper FDMC
2 Solid ceiling construction
3 Mineral stone wool min. density 140 kg/m
4 Fire protection mastic min. thickness 1 mm
5 Glass fiber felt with aluminium foil width 50 mm, thickness 5 mm
6 Duct
Used materials - example**:
2 - Promapyr, Rockwool Steprock HD
3 - Promastop - P, K
3
Fig. 19 Solid ceiling construction - stuffing box and fire protection mastic
Fig. 18 Solid ceiling construction - mortar or gypsum
POSITION:
1 Fire damper FDMC
2 Solid ceiling construction
3 Mortar or gypsum
4 Duct
1
3
4
2
150*
≥40
* min. 110 - Concrete/ min. 125 - Aerated concrete
* min. 110 - Concrete/ min. 125 - Aerated concrete
EIS 60
EIS 60
** Stuffing box and fire protection mastic can be replaced by another approved
fire sealing system for damper installation with equivalent material properties.

16
TPM 083/12
7
1
5
4
≥40
≥100
≥50
2
3
6
Fig. 21 Gypsum wall construction - stuffing box and fire protection mastic
POSITION:
1 Fire damper FDMC
2 Gypsum plate
3 Fire resistant insulation
4 Mineral stone wool min. density 140 kg/m
5 Fire protection mastic min. thickness 1 mm
6 Glass fiber felt with aluminium foil width 50 mm, thickness 5 mm
7 Duct
Used materials - example*:
4 - Promapyr, Rockwool Steprock HD
5 - Promastop - P, K
Fig. 20 Gypsum wall construction - mortar or gypsum
4
5
≥40
≥100
2
3
POSITION:
1 Fire damper FDMC
2 Gypsum plate
3 Fire resistant insulation
4 Mortar or gypsum
5 Duct
1
* Stuffing box and fire protection mastic can be replaced by another approved
fire sealing system for damper installation with equivalent material properties.
Installation opening has to be
reinforced by profile (UW, CW).
Profil is fixed by screws ≥3,5 mm
with corresponding length. Distance
between screws ≤200 mm.
Installation opening has to be
reinforced by profile (UW, CW).
Profil is fixed by screws ≥3,5 mm
with corresponding length. Distance
between screws ≤200 mm.
EIS 60
EIS 60
3

17
TPM 083/12
Fig.. 22 Gypsum wall construction - installation next to wall, ceiling - mortar or gypsum and mineral wool
≥100
(≥100)+50
A-A
3
2
2
3
10 to 50
10 to 50
≤D+100
1
2
2
1
3
D-20
≥100
B-B
2
2
10 to 50
10 to 50
≤D+100
1
2
2
1
A
A
2
1
3
D-20
3
B
B
2
1
POSITION:
1 Fire damper FDMC
2 Mortar or gypsum
3 Mineral stone wool min. density 140 kg/m3
Installation opening has to be
reinforced by profile (UW, CW).
Profil is fixed by screws ≥3,5 mm
with corresponding length. Distance
between screws ≤200 mm.
Installation opening has to be
reinforced by profile (UW, CW).
Profil is fixed by screws ≥3,5 mm
with corresponding length. Distance
between screws ≤200 mm.
EIS 60
Notice:
●Gap between damper and construction is filled by mortar or
gypsum and mineral wool
●Wool is fixed to damper body and construction by fire protection
mastic.
●Mineral wool thickness = construction thickness + 50 mm
●Damper axis has to be horizontal
●Installation is valid for ceiling construction

18
TPM 083/12
7. S spension systems
7.1. Mounting to the ceiling wall
Size As
[mm ]
Weight G [kg]
for 1 piece for 1 pair
M8 36,6 22 44
M10 58,0 35 70
M12 84,3 52 104
M14 115 70 140
M16 157 96 192
M18 192 117 234
M20 245 150 300
Fig. 23 Mounting to the ceiling wall
Without
anchor
With
anchor
1
2
3
With hinge plate and
anchors
4
5
1
6
5
1
2
120
50
Hinge plates
100
150
Load capacities of threaded hanger rods F [N] at the
required fire resistance 90 minutes
2
Position:
1 Threaded rod M8 – M20
2 Nut
3 Washer
4 Coupling Nut
5 Anchor
6 Hinge plate - min. thickness 10 mm
80
7.2. Horizontal installation
Fire dampers can be suspended by using threaded rods and a mounting profiles. Load the
suspension system depend on weight of the fire damper.
Damper assembly procedures must be done so as all load transfer from the fire separating
constructions to the damper body is absolutely excluded. Back-to-back air-conditioning piping
must be hung or supported so as all load transfer from the back-to-back piping to the damper is
absolutely excluded.
Threaded rods longer than 1,5 m require fire-resistant insulation.
Threaded rod fixing to the ceiling construction - see fig. 23

19
TPM 083/12
1
2
3
5
4
Fig. 24 Suspension - horizontal duct
Position:
1 Fire damper
2 Damping pad
3 Extension piece
4 Threaded rod
5Suspension ring
Examples of using materials: HILTI, SIKLA, MÜPRO etc.
7.3. Vertical installation
Fire dampers can be suspended by using threaded rods and a mounting profiles.
Load the suspension system depend on weight of the fire damper.
Damper can be suspended from the ceiling construction or supported above the ceiling construc-
tion. Damper assembly procedures must be done so as all load transfer from the fire separating
constructions to the damper body is absolutely excluded. Back-to-back air-conditioning piping
must be hung or supported so as all load transfer from the back-to-back piping to the damper is
absolutely excluded.
Threaded rods longer than 1,5 m require fire-resistant insulation.
2
5
4
Other manuals for FDMC
3
Table of contents
Other Mandik Fire And Smoke Damper manuals
Popular Fire And Smoke Damper manuals by other brands
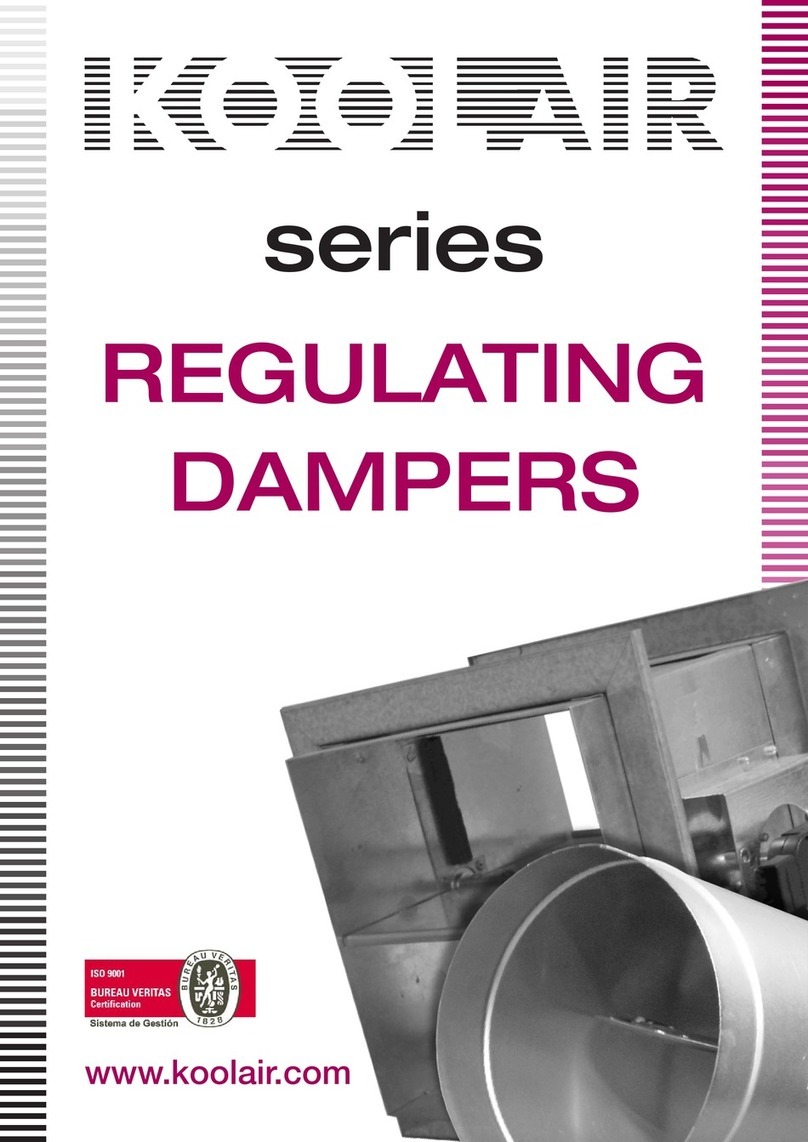
KOOLAIR
KOOLAIR CCR Series manual
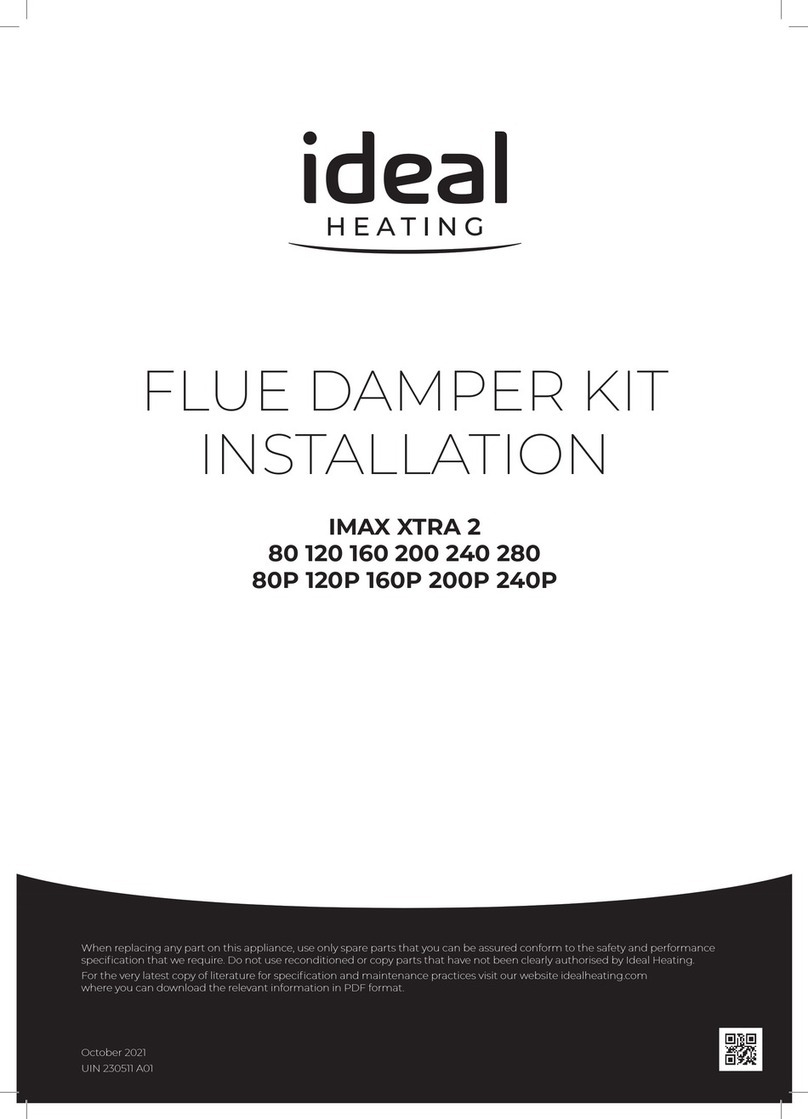
Ideal Heating
Ideal Heating EVOMAX 2 40 Installation
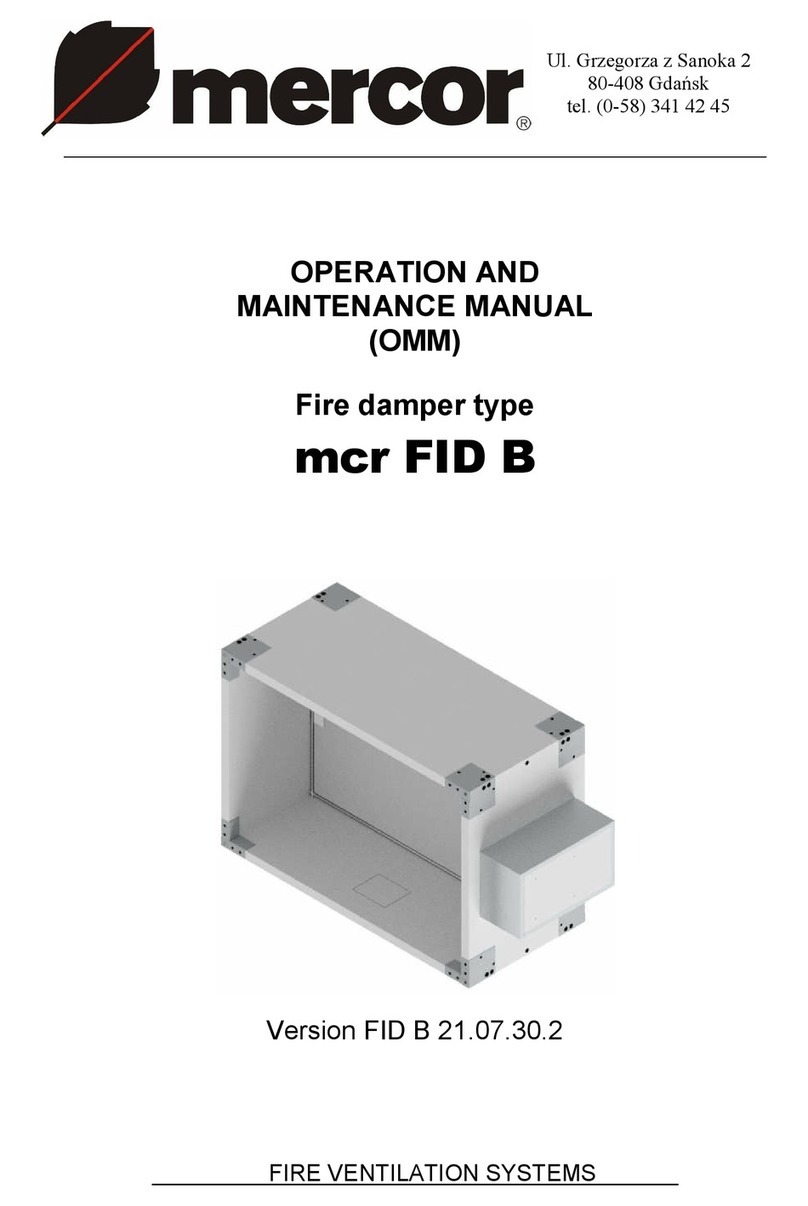
mercor
mercor mcr FID B Operation and maintenance manual
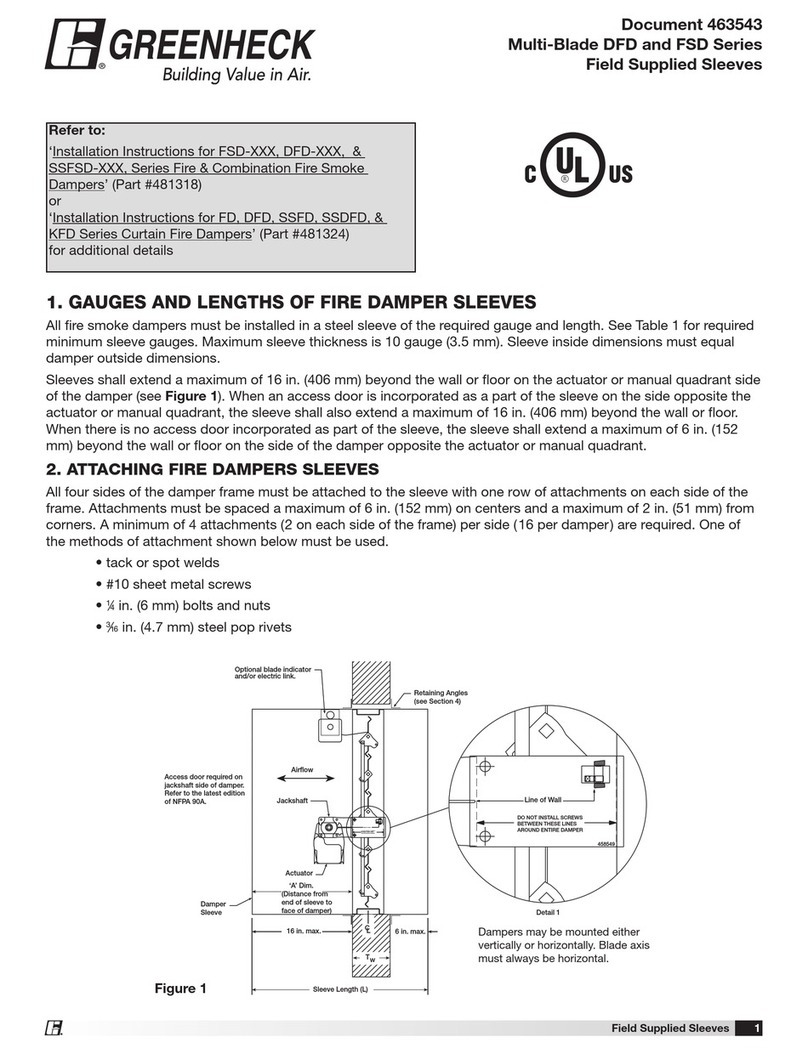
Greenheck
Greenheck Multi-Blade DFD Series manual
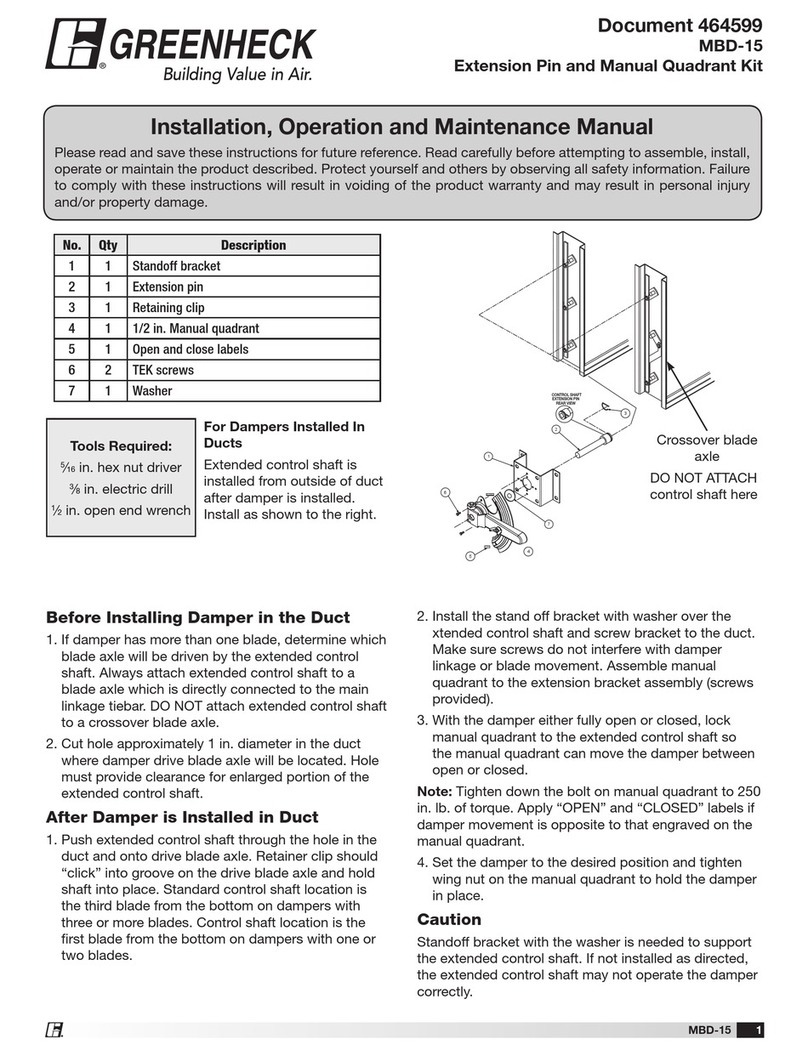
Greenheck
Greenheck MBD-15 Installation, operation and maintenance manual
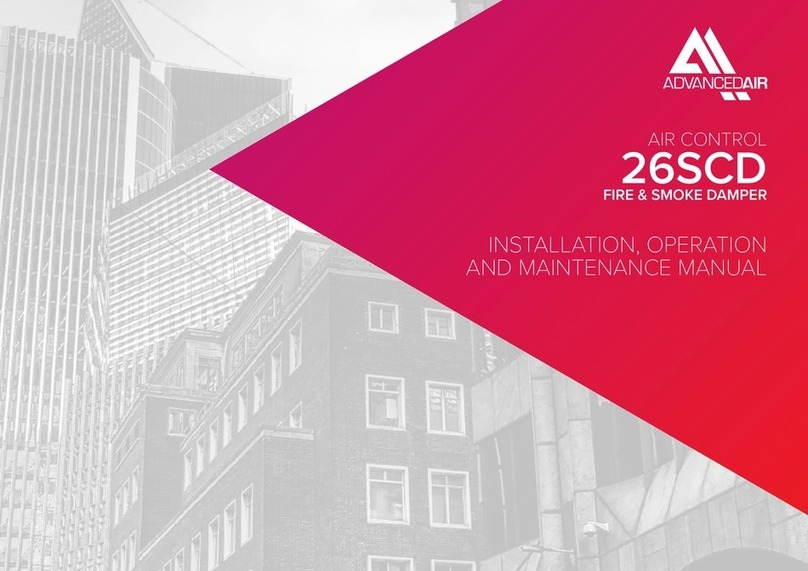
Advanced Air
Advanced Air 26SCD Installation, operation and maintenance manual