Wohler DC 2000 User manual

Pressure Computer DC 2000
Contents
1. Specification ......................... 2
2. Controls .................................. 4
3. Measuring mode menu ..... 7
3.1 Pressure measurement ..... 7
3.2 Flow Speed ........................... 8
3.3 Temperature measurement .
...................................................
3.4 Humidity measurement ...10
4. Stresstest (TRGI) ............... 11
5. Maintest (TRGI) ..................13
6. Leakage rate .......................14
7. Min., Max.,
Mean Value menu ............. 16
8. Setup menu......................... 17
8.1 Basic setting ....................... 17
8.2 Logo entry ........................... 20
. Logger/IR fuction menu ..22
10. Changing the battery .......24
11. Set for the leak test ..........27
12. Accessories + guarantee 31
13. Declaration of conformity 32
14. Quick start guide ....................
central section ...................32

Manual Instructions
2
1. Specification
Pressure computer DC 2000 is a high-precision, multifunctional multimeter for
registering differential pressure, flow rates, temperature and humidity (optional). The
extremely large dynamic range of the device, even in the basic version, means that in
addition to highly-sensitive measurements of the smallest pressure levels in the Pascal
range for draught and gas pressure measurements, it is also possible to determine the
volume of a leak and to check seals in the main test according to DVGW-TRGI, as well
as measurements for stress tests in preliminary testing. A maximum measurement
range of up to 2 bar and a bursting pressure of 3 bar guarantee adequate safety even
for higher pressure ranges. The user is guided through all measurements by means of
display texts.
Even the basic version,in which all measured values can be stored in a logger, can also
be used to measure (room) climate. A temperature sensor is integrated for this
standard in addition to the pressure sensor. As an option, the area of application can
be extended with an integratable air humidity sensor and/or an external temperature
sensor. Depending on the sensing rate, all measured values can be “logged” for
several years and transferred to the PC by means of the integrated IrDA interface.
Measurement protocols can be output directly on a HP thermal printer together with
the company’s own “LOGO”. The extremely low power consumption is facilitated by
innovative processor technology in which power consumption is automatically and
dynamically adapted to the measuring task. Even in the mode requiring maximum
power consumption (6 mA, two standard batteries (2 x Mignon, 2Ah) provide
continuous operation for more than 300 hours. In logger mode this increases to several
years (6400 measurements x 4 hours) without replacing the batteries or memory
overflow if an interval of 4 hours is selected between measurements. The pressure
meter can be used for gaseous media (air or inert gas) as well as for liquids, such as
water or heating oil.
The processor’s calculating module enables simple manipulations of the measured
values, so that, for example, the leak rate is automatically displayed in liters per hour or
the flow speed measured with a Prandtl tube is displayed in m/s.
1. Specification

3
Manual Instructions
Eng ishh
1.1 Measurement va ues
Differential pressure measurementDifferential pressure measurement
Differential pressure measurementDifferential pressure measurement
Differential pressure measurement (temperature-compensated Piezo sensor)
Measuring range: +/-2 bar
1 Pa resolution in the range –125,00 hPa to +125,00 hPa, otherwise 10 Pa
Accuracy: <3% o.rd., in the range <+-200 Pa. better than +/-6 Pa
Internal temperature measurementInternal temperature measurement
Internal temperature measurementInternal temperature measurement
Internal temperature measurement (NTC)
Measuring range: -5 °C to 55 °C
Accuracy: <+-4 °C
Resolution: 1 °C
External temperature measurementExternal temperature measurement
External temperature measurementExternal temperature measurement
External temperature measurement (optional probe, order no. 605 or 611)
Measuring range: -1 , °C to + , °C
Accuracy: <+-2 °C
Resolution: 0,1 °C
T 8: <120 sec, at 1.5 m/s
Humidity measurementHumidity measurement
Humidity measurementHumidity measurement
Humidity measurement (optional, order no.7203)
Measuring range: 0% to 100% rh (relative humidity), non-condensing
Accuracy: <+/-5 % rh, in the range 0 to 60% rh, otherwise <10 % rh
Resolution: 1% rh
1.2 Ca cu ated va ues
Pressure unitsPressure units
Pressure unitsPressure units
Pressure units: Conversion into mbarmbar
mbarmbar
mbar, hPa, Pa, mmH2O, PSI, hPa, Pa, mmH2O, PSI
, hPa, Pa, mmH2O, PSI, hPa, Pa, mmH2O, PSI
, hPa, Pa, mmH2O, PSI in accordance with the
general rules of conversion.
TT
TT
Temperature unitsemperature units
emperature unitsemperature units
emperature units: Conversion from °C°C
°C°C
°C into °F°F
°F°F
°F in accordance with the general rules of
conversion.
Flow: Flow:
Flow: Flow:
Flow: according to Prandtl, display in meters per secondmeters per second
meters per secondmeters per second
meters per second, automatic continuous density
correction by means of temperature signal, range:0.0 to 150.0 m/s
Leakage rateLeakage rate
Leakage rateLeakage rate
Leakage rate: According to DVGW-TRGI worksheet G624 in liters per hourliters per hour
liters per hourliters per hour
liters per hour.
The material data required for the conversion of different gas types can be selected from
a database stored in the device.
Drop in pressure: streetest and maintestDrop in pressure: streetest and maintest
Drop in pressure: streetest and maintestDrop in pressure: streetest and maintest
Drop in pressure: streetest and maintest as per DVGW-TRGI, worksheet G600
Statistical key values: minimum, mean, maximumStatistical key values: minimum, mean, maximum
Statistical key values: minimum, mean, maximumStatistical key values: minimum, mean, maximum
Statistical key values: minimum, mean, maximum of all measurement and calculation
values in the relevant unit of measurement.
Date and time:Date and time:
Date and time:Date and time:
Date and time: Output to measurement protocols
1. Specification

Manual Instructions
4
1.3 Logger function
Scope: 6400 measurementsScope: 6400 measurements
Scope: 6400 measurementsScope: 6400 measurements
Scope: 6400 measurements with pressure, temperature and humidity readings, i.e.
maximum 1 ,200 measured values.
Measuring values are also held in memory for over 10held in memory for over 10
held in memory for over 10held in memory for over 10
held in memory for over 10 years, even without batteries.
IrDA data transferIrDA data transfer
IrDA data transferIrDA data transfer
IrDA data transfer is even possible during registration
Selectable sensing intervalsSelectable sensing intervals
Selectable sensing intervalsSelectable sensing intervals
Selectable sensing intervals:30 s,1 Min,10 Min,30 Min,1h,3h,4h
Check for undervoltage
1.4 Technica data
Power consumptionPower consumption
Power consumptionPower consumption
Power consumption from two Mignon batteries, type AA or dry cell batteries:
-Operation mode: approx. 6 mA,
-“Off “ mode and logger mode approx. 70 µA for time and processor
Interfaces:Interfaces:
Interfaces:Interfaces:
Interfaces:
-Infrared data transfer to the PC
-Local printout on HP thermal printer, order no. 130
Storage temperatureStorage temperature
Storage temperatureStorage temperature
Storage temperature: -20 °C to +60 °C
Operating temperatureOperating temperature
Operating temperatureOperating temperature
Operating temperature: -5 °C to +60 °C in logger mode (without display),
with display 0 °C -50 °C
Weight: approx. 450 g including protective pocket and magnet, excluding hose
Dimensions: 54 x 165 x 52 mm
2.Contro s and ports
Figure 1 below shows the display and controls of the DC 2000. The display always shows
the trend on the left (), the numeric value in the center and the associated unit of
measurement on the right. When a key is pressed, a cursor is also displayed on the
edge of the display, indicating a subprogram on the display sticker. If this cursor flashes,
then this menu item is active.
The key function is similar to that on a mobile phone. In general, the left “+” key allows
you to increase or decrease a numeric entry or to move the cursor position ↑ (1) on the
edge of the display to the right or left (see figure).
Double-clicking “+” briefly changes the direction of counting from incrementing to
decrementing or switches the direction of the cursor steps from right to left. A point in the
middle of the display (2) shows this reverse function. Another double click switches back
to positive increment or cursor direction.
2. Controls

5
Manual Instructions
Eng ishh
Example: Pressing the “+” key moves the cursor from the position shown “Preliminary
Test” (see 1) to the right to “Main Test”. You can return to the “Preliminary Test” position
by double-clicking (see 2: “ “ indicates an active reverse function) and then clicking
once.
Figure 1: DC 2000 display and controls
The “ENTER” key“ENTER” key
“ENTER” key“ENTER” key
“ENTER” key in the middle of the control panel confirms the numeric entry or acti-
vates the program selected by the cursor position.
The right “C I/O “ key“C I/O “ key
“C I/O “ key“C I/O “ key
“C I/O “ key has two functions. When pressed once it cancels a mistakenly
started menu item or an incorrect numeric entry. If the key is held down, then the device
switches off after 3 seconds.
2. Controls
2
1Unit of active
measurement

Manual Instructions
6
Figure 2 shows all components and connections of pressure computer DC2000.
Figure 2:Connections and ports of pressure computer DC 2000
A hose with an internal diameter of 5-6 mm or, depending on the version of the DC 2000,
a quick-action connection type DN 2.7 can be attached. Silicon hoses should not be
used in higher pressure ranges as this material can be subject to perforations at an
overpressure of only 1 bar, leading to leaks. As shown in figure 2, the back of the DC
2000 contains diffusion apertures for registering the room’s moisture (optional) and tem-
perature. The integrated temperature measurement is also used to compensate for the
pressure in the pressure sensor. Combustion air temperature gauge A 7 (order no. 605)
or combustion air sensor A 7 (order no. 611) with 2 meter cable can be used externally
as a precision temperature sensor with an extended measuring range (-1 . °C to + .
°C).
In order to read the logger, the measuring data is transferred to the PC via the infra-red
interface (order no. 631).
2. Controls
+ Overpressure
- Underpressure
Externa
Temperature port
IrDA interface
Humidity sensor
(Rear)

7
Manual Instructions
Eng ishh
3.The Measuring Mode menu
After power-on, the device carries out a self-test. After this the time and date are dis-
played. If the device’s logger function was activated, then the text “Log” appears instead
of the self-test, followed by current measurement and storage values, before the device
switches off again. No hose may be connected and no differential pressure may be
output as long as a flashing cursorflashing cursor
flashing cursorflashing cursor
flashing cursor indicates subprogram
P=0P=0
P=0P=0
P=0
, because the device isdevice is
device isdevice is
device is
stabilizing and its zero point is being determinedstabilizing and its zero point is being determined
stabilizing and its zero point is being determinedstabilizing and its zero point is being determined
stabilizing and its zero point is being determined .
The subsections in this chapter describe the basic functions in the Measuring ModeMeasuring Mode
Measuring ModeMeasuring Mode
Measuring Mode
menu item. For this, the cursor should be moved to the Measuring Mode subprogram by
pressing the “±“ key“±“ key
“±“ key“±“ key
“±“ key three times followed by “ENTER” (cursor flashes under MeasuringMeasuring
MeasuringMeasuring
Measuring
ModeMode
ModeMode
Mode) (see figure 3).
Figure 3:Selection of the Measuring Mode menu
3.1 Pressure measurement
The Measuring ModeMeasuring Mode
Measuring ModeMeasuring Mode
Measuring Mode subprogram is activated with the “ENTER” key. Afterwards the
cursor flashes and the display shows the text “DRUCK” (PRESSURE) together with the
unit of measurement “mbar”. You can now press the “+” key to switch to all available
units and confirm with “ENTER”. The following five units of pressure measurement can be
selected: Pa, hPa, mbarPa, hPa, mbar
Pa, hPa, mbarPa, hPa, mbar
Pa, hPa, mbar, mmH2O, PSI, mmH2O, PSI
, mmH2O, PSI, mmH2O, PSI
, mmH2O, PSI
The Measuring Mode, AUTOMeasuring Mode, AUTO
Measuring Mode, AUTOMeasuring Mode, AUTO
Measuring Mode, AUTO item produces an alternating display of pressure, tempera-
ture and moisture values in the last selected units for pressure and temperature.
Overpressure on the connector piece marked (+)(+)
(+)(+)
(+) and underpressure on the connector
piece marked (-)(-)
(-)(-)
(-) leads to a positive differential pressure display. If the pressure differen-
tial rises above 134. hPa, then the device automatically switches over to the higher
measuring range up to 2000.0 hPa. If the pressure drops below 125.0 hPa from this high
pressure range, then the display again switches to a resolution of 1 Pa.
3. Measuring Mode menu

Manual Instructions
8
3.2 Measuring the speed of flow according to Prandtl3.2 Measuring the speed of flow according to Prandtl
3.2 Measuring the speed of flow according to Prandtl3.2 Measuring the speed of flow according to Prandtl
3.2 Measuring the speed of flow according to Prandtl
A Prandtl storage pipe can be used to measure the slow speed of the air in m/s. To
activate measurement, press the “+” key in the Measuring ModeMeasuring Mode
Measuring ModeMeasuring Mode
Measuring Mode menu until the text
“Prandtl “ appears with unit of measurement “m/s “.
The overall pressure of the storage pipe is connected to the (+) overpressure connector
and the static pressure is connected to the (-) underpressure connector of the DC 2000
(see figure 4).
Firstly, the device must be “tared” when the medium has settled (P=0). After this, the
sensor is inserted into the gas or air stream as parallel as possible and with the point in
the opposite direction and the measured values are read out. The current flow speed v is
automatically calculated according to GI. (1). The air density p in GI (1) in turn depends
on the absolute air pressure pakt and the current temperature T.
ρ
Air density 1,2 kg/m3
vFlow Speed m/s
∆pPressure differential Pa, measured with Prandtl pipe
pakt Current absolute air pressure, manual entry in Setup menu item
(reference value 1013 hPa)
V
Air temperature °C
IThe absolute air pressure pakt can be set in the Setup ->Absolute Pressure menu item.
This setting is also used to determine the leakage rate in chapter 6.
If the temperature T of the air stream to be measured deviates from the room temperature
of the DC 2000, the combustion air temperature sensor can be inserted in the stream in
parallel with the Prandtl pipe via the 2 m cable connection. In this way, the air density p is
automatically tracked in accordance with the temperature T measured according to GI.
(2).
2. Measuring Mode Menu
(
T( °C )
+ 273
K
) • 1013
hPa
with:
ρ
= 1,2 •
kg/m3
•
2 3
K
•
ρ
akt (
hPa
)(2)
2 x ∆
ρ
ö
ρ
V
= (1)

Manual Instructions
Eng ishh
Figure 4:Prandtl pipe, order no. 487 with combustion air temperature sensor A 7 order
no. 611 for automatic correction of density
3.3 Temperature measurement
In order to activate temperature measurement, the “+” key is pressed in the MeasuringMeasuring
MeasuringMeasuring
Measuring
ModeMode
ModeMode
Mode menu until the word “Temperature” appears with unit of measurement ”°C “. Press-
ing “+” again switches to unit of measurement “°F “..The “ENTER“ key confirms the se-
lected measuring mode and switches back to display.
An external temperature gauge can be connected at any time. In this case, the device
automatically switches to the external sensor, which can be seen from the higher resolu-
tion of 0.1 °C.
For precision measurements, the five-digit calibration number (e.g. cal. no. 10208) should
be entered under the menu item Setup, TLOffSetup, TLOff
Setup, TLOffSetup, TLOff
Setup, TLOff. This calibration number is imprinted on a
metal foil on every temperature sensor. If no external gauge is connected, then the tem-
perature of and internal sensor is displayed which is also used for temperature compen-
3. Measuring Mode Menu
stat.
pressure
total air pressure
temperature
sensor
(optimal)
-+

Manual Instructions
10
sation for the pressure signal and optional moisture sensor signal.
Thus, when room temperature and moisture are being continuously measured, the hous-
ing should not be exposed to any direct sunlight or heat.
3.4 Humidity measurement (optiona )
To activate humidity measurement, press the “+” key in the Measuring ModeMeasuring Mode
Measuring ModeMeasuring Mode
Measuring Mode menu until
the word “humidity” appears with unit of measurement “%“. The “ENTER” key confirms
the selected mode and switches back to display. The diffusion aperture on the back of
the housing should not be covered.
The humidity sensor is a laser-trimmed, capacitive sensor element with chip-integrated
signal processing. It can be retrofitted or replaced by the user himself (order no.:7203).
For this, the two calibration values should be entered in the Setup menu under Hmoff (in
this case Zero offset=0.833V,figure 6) or under Hmslope (Slope=31.3 mV). The slop value
derived from the calibration protocol provided should be rounded to one decimal place
(in this case:31.311 mV ->31.3).
Figure 5:Position 1 of the humidity sensor after the battery cover has been removed
3. Measuring Mode Menu
1

11
Manual Instructions
Eng ishh
Figure 6: Calibration protocol for a humidity sensor
3.5 Automatica y a ternating disp ay
The Measuring Mode, AUTOMeasuring Mode, AUTO
Measuring Mode, AUTOMeasuring Mode, AUTO
Measuring Mode, AUTO item produces an alternating display of pressure, tempera-
ture and humidity readings in the last selected units for pressure and temperature
4. Stresstest (DVGW-TRGI) menu
The preliminary test according to DVGW – TRGI worksheet G 600 with lines with operat-
ing pressures of up to 100 mbar can be executed and documented very easily with the
DC 2000.
First the line should be closed and a suitable test stopper should be inserted.
The DC 2000 should be switched on before it is connected to the test stopper. After
taring, the VV
VV
Vorprüfungorprüfung
orprüfungorprüfung
orprüfung (preliminary test) menu item is activated with the “±“ key.
4. Preliminary Test

Manual Instructions
12
4. Preliminary Test
The DC 2000 prompts you to increase pressure until you reach test pressure (e.g. 1 bar).
If the overpressure connector has been mistakenly confused with the underpressure
connector, then the word “exchange” appears on the display. The stabilization phase
starts when the pressure reaches the preset test pressure (default setting:
wand period
=2 minutes). If the pressure remains within the tolerance range of +-10% of the test
pressure during this stabilization phase, then the actual loss of pressure test (default
setting: period = 10 minutes) starts after the stabilization period has elapsed. The remain-
ing test period and the current pressure values are displayed alternately. The position
within this tolerance range in the stabilization phase and therefore the start of the stabili-
zation period is symbolized in the display by the following trend display . After the
test period has elapsed, the cursor flashes on StresstestStresstest
StresstestStresstest
Stresstest and the results are displayed.
You can browse through the results with the “±“ key:
Difference:54,4 hPa
“±“ key
Starting pressure:1000.3 hPa
“±“ key
Duration:10:00
“±“ key
Stopping pressure: 45. hPa
“±“ key
Running text: “Print,..“ activate printout with the “ENTER” key
“±“ key
Difference:54.4 hPa
“±“ key
etc.
This result can also be printed out subsequently under the menu item Log./IRLog./IR
Log./IRLog./IR
Log./IR and PrintPrint
PrintPrint
Print
or transferred to the PC.
The protocol is only deleted after the logger has started or after another test according to
TRGI.

13
Manual Instructions
Eng ishh
5. Main Test
5. Maintest (DVGW-TRGI) menu
The main test according to DVGW – TRGI worksheet G 600 with lines with operating
pressures of up to 100 mbar can also be executed and documented very easily with the
DC 2000.
First the line should be closed and a suitable test stopper should be inserted.
The DC 2000 should be switched on before it is connected to the test stopper. After
taring, the MaintestMaintest
MaintestMaintest
Maintest menu item is activated with the “±“ key.
The DC 2000 prompts you to increase pressure until you reach test pressure (e.g. 1 bar).
If the overpressure connector has been mistakenly confused with the underpressure
connector, then the word “tauschen” (exchange) appears on the display. The stabilization
phase starts when the pressure reaches the preset test pressure (default setting:
wand
period
=2 minutes). If the pressure remains within the tolerance range of +-10% of the
test pressure during this stabilization phase, then the actual loss of pressure test (default
setting: period = 10 minutes) starts after the stabilization period has elapsed. The remain-
ing test period and the current pressure values are displayed alternately.. The position
within this tolerance range in the stabilization phase and therefore the start of the stabili-
zation period is symbolized in the display by the following trend display ↑↓. After the test
period has elapsed, the cursor flashes on Maintest and the results are displayed. You
can browse through the results with the “±“ key:
Difference:17.7 hPa
“±“ key
Starting pressure:110,83 hPa
“±“ key
Duration:10:00 (minutes)
“±“ key
Stopping pressure: 3.14 hPa
“±“ key
Running text: “Print,..“ activate printout with the “ENTER” key
“±“ key
Difference:17.7 hPa
“±“ key

Manual Instructions
14
6. Measuring leakage rates
This result is stored in the DC 2000 and can also be printed out subsequently under the
menu item Log./IRLog./IR
Log./IRLog./IR
Log./IR and PrintPrint
PrintPrint
Print or transferred to the PC.
The protocol is only deleted after the logger has started or after another test according to
TRGI.
6. Leakage rate according to DVGW worksheet G 624
The determination of leakage rates according to DVGW worksheet G 624 can also be
executed and documented very easily with the DC 2000.
First the line should be closed and a suitable test stopper should be inserted. After this,
the line volume should be determined from the pipe lengths and diameters.
The diagram in figure 7 should provide some help.
There is a larger version of the diagram on the front of the central insertion.
Figure 7:Diagram to help determine the content of the pipe

15
Manual Instructions
Eng ishh
After automatic taring, the Leakage rateLeakage rate
Leakage rateLeakage rate
Leakage rate menu item is activated with the “±“ key.
The DC 2000 prompts you to increase pressure until you reach test pressure (e.g. 100
bar). If the overpressure connector has been mistakenly confused with the underpressure
connector, then the word “tauschen” (exchange) appears on the display. The stabilization
phase starts when the pressure reaches the preset test pressure (default setting:
wand
period
=2 minutes). If the pressure remains within the tolerance range of +-10% of the
test pressure during this stabilization phase, then the actual loss of pressure test (default
setting: period = 10 minutes) starts after the stabilization period has elapsed. The remain-
ing test period and the current pressure values are displayed alternately. The position
within this tolerance range in the stabilization phase and therefore the start of the stabili-
zation period is symbolized in the display by the following trend display ↑↓. After the test
period has elapsed, the cursor flashes on MaintestMaintest
MaintestMaintest
Maintest and the results are displayed. You
can browse through the results with the “±“ key:
Difference: . hPa
“±“ key
Starting pressure:108.83 hPa
“±“ key
Duration:1 min
“±“ key
Stopping pressure: 8. 6 hPa
“±“ key
Leakage rate:8.3 l/h hPa
“±“ key
Running text: “Print,..“ activate printout with the “ENTER” key
“±“ key
Difference: . hPa
“±“ key
etc.....
This result is stored in the DC 2000 and can also be printed out subsequently under the
menu item Log./IRLog./IR
Log./IRLog./IR
Log./IR and PrintPrint
PrintPrint
Print or transferred to the PC.
The protocol is only deleted after the logger has started or after another test according to
TRGI.
6. Measuring leakage rates

Manual Instructions
16
The leakage rate is calculated automatically according to the following formulae (3) & (4)
and thereby corresponds to the procedure set out in DVGW-TRGI worksheet G 624:
Volume of gas leakage when operating in l/h
Volume of air leakage at test pressure
p
Bmax
Operating pressure of gas on-site
p
Start
Test pressure at start of measurement
p
Stop
Test pressure at end of measurement
pakt Absolute air pressure, manual entry in Setup menu item under abs.abs.
abs.abs.
abs.
pressurepressure
pressurepressure
pressure (basic value 1013 hPa)
f
(abs. viscosity air)/(abs. viscosity of gas), selection stored in Setup under
Gas
Tmess
Duration of measurement converted into hours (basic value 1 min)
Vpipe
Content of test section in L, according to figure 7
7. Min., Max. and AVG va ues menu
The three left hand cursor items on the bottom of the display indicate statistical key
figures for all measurement and calculation values. The detection of the relevant mini-
mum and maximum and the calculation of the mean value (AVG) can be reset with the
P=0P=0
P=0P=0
P=0
function. When the mean value is calculated, the effectiveness of smoothing can be
set to GI. (5) with the ALPHA value. The lower the value for ALPHA, the greater the effect
of smoothing. ALPHA can be set from 0.01 to 0. using the Setup ->ALPHASetup ->ALPHA
Setup ->ALPHASetup ->ALPHA
Setup ->ALPHA menu item
7.Min-, Max and AGV values
VL =
V pipe
T mess
pakt+ pStart
pakt + p Stop
•
•- 1 (4)
VB= VL • •
f
••(3)
pBmax
pStart
•
VB
•
VL

17
Manual Instructions
Eng ishh
.
AVG new
=ALPHA • current measured value ++(1-ALPHA)• AVG
old
AVG
new
Mean value at current time
AVG
old
Mean value one second previously
ALPHA Weight factor for current measured value (0.01..0. )
8. Setup menu for basic settings and ogo entry
The setup menu is used to set the basic configuration. All settings are preserved after the
device is switched off or the battery is changed.
8.1 Basic settings
After the setup menu is selected, a series of settings can be made with the “+” key. These
are explained below. The quick reference guide in chapter 13 also offers a good over-
view.
1. Setup ->Runden
When the rounding function is switched on, the last position in the display is switched to
a resolution of 5 digits. In the case of a Pascal display, for example, this leads to a
reduced resolution of 5 Pa. Instead of the 1 Pa resolution. In the event of pressure varia-
tions, this leads to a much steadier display, but the delay effects typical of a message are
lost. All calculated values continue to be determined internally with the high resolution.(On/
Off, default: Off)
2 .Setup ->Gas
This menu allows the type of gas and therefore the relative viscosity in Gl.(3) to be se-
lected (default: natural gasnatural gas
natural gasnatural gas
natural gas)
8. Setupmenu

Manual Instructions
18
Table 1:Relative viscosity of various gases as per Gl.(3) according to DVGW-TRGI
3.Setup ->abso ute air pressure
Here the current local air pressure (QFE) p akt is entered in hPa for Gl.(2) for calculating
speed and for Gl.(4) for determining the leakage rate. Values between 810 hPa and 1065
hPa can be set (default:1013 hPa)
4.Setup ->time & date
The time and date are set here. If less than a minute passes between the removal of an
old battery and the replacement of a new one, then the clock does not need to be ad-
justed. If more time passes, then the time should simply be raised by this amount.
5.Setup ->ALPHA
The weight factor for AVG averaging according to Gl.(5) is set here. ALPHA can accept
values in the range 0.01 to 0. . The lower the value selected for ALPHA, the less notice-
able the current variations in the signal, see also chapter 7.(0.01-0. , default:0. 0)
6.Setup ->stresstest
The test pressure for the preliminary test is set here ( 00 hPa-1200 hPa, default:1Bar).
7. Setup -> stresstest -> duration
The duration of the preliminary test is set here (1-240 min., default:10 minutes).
8. Setup -> main test -> pressure
The test pressure for the main test is set here ( 0-160 hPa, default:110 hPa).
9. Setup -> main test -> duration
The duration of the main test is set here (1-240 min, default:10 min).
8. Setupmenu
Gas type
f
Natural gas 1,7
Air 1,0
City gas 1,3
Propane 2,3
Butane 2,4
Hydrogen 2,0

1
Manual Instructions
Eng ishh
10. Setup -> stabi ization time
This is where the length of time for thermal stabilization is set before starting the prelimi-
nary test or main test and leakage rate determination. If the current pressure value for this
period remains within a tolerance range of +-10% of the set pressure, then measurement
of pressure loss starts automatically. The position within this range, and therefore the
start of the stabilization period, is symbolized in the display by the following trend indica-
tors . Loss of pressure can be measured during the stabilization phase and can
also be started anytime at the press of a button.(1-270 mins., default: 2 min.)
11. Setup ->T off
The calibration number located on the sticker on the external temperature sensor is
entered here.(10100-10300, default:10187)
12. Setup ->Hmofff
The Hmoff calibration number is entered here. Figure 6 in section 3.4 shows an example
of Hmoff =Zero offset=0.833V.(0.5-1.0, default:0.833V)
13. Setup ->Hms ope
The calibration number Hmslope is entered here. Figure 6 in section 3.4 contains an
example of Hmslope =slope =31.3 mV. The value read from the calibration sheet must be
rounded to one decimal place.(25.0-60.0 mV, default:31.3 mV)
14. Setup ->Log rate
The interval between two registrations of the logger is set here. The default setting is 30
sec. This means that a pressure value, temperature value and moisture value is recorded
in the integrated data storage every 30 seconds; see section .2.(default: 30 secs)
15. Setup ->AUTO-OFF
The Auto-Off function can be activated or deactivated here. This is used for automatic
shutdown if there has been no keyboard input for over 30 minutes (default: ON)
16. Setup ->Logo
The logo text for printer output can be entered here; this is explained in the next section,
8.2.(default “WÖHLER MGKG, DC 2000”)
17. Setup ->Defau t
This function restores the setup status on delivery. The logo text is overwritten with the
original Wöhler logo. All sensor calibration values remain unchanged. Accidental activa-
tion of this function is prevented by an additional check question.
8. Setupmenu

Manual Instructions
20
8. Setupmenu
8.2 Logo entry
The following tables 2 & 3 simplify logo entry on the DC 2000.
First you write the required text in the upper table 3 (preferably with a pencil). The first two
lines have 12 characters and will be printed in bold face. The following lines 4 to 6 can
contain a maximum of 24 characters and these are printed as normal.. After this, you
define the ASCII code on a line-by-line and column-by-column basis and enter it in the
code result fields. These values can be entered line-by-line under Setup ->LogoSetup ->Logo
Setup ->LogoSetup ->Logo
Setup ->Logo and
saved.
Table 2: Conversion based on the example of the original logo “WÖHLER MGKG ..“
The table can also be downloaded as an EXCEL file, “LOGO-KONVERTER.XLS “ under
Internet address www.woehler.de/mgkg/DC2000 as “freeware “ (with effect from April
2002). The text is automatically converted into ASCII code there.
Table 3: Template for your own conversions
This manual suits for next models
2
Table of contents
Other Wohler Measuring Instrument manuals

Wohler
Wohler LX 300 User manual

Wohler
Wohler Pandora User manual
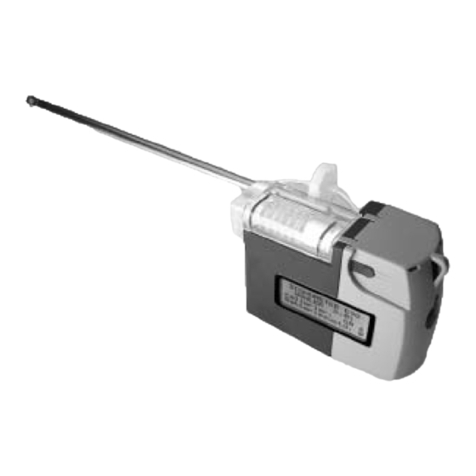
Wohler
Wohler Econometer E 98 User manual

Wohler
Wohler M5 User manual
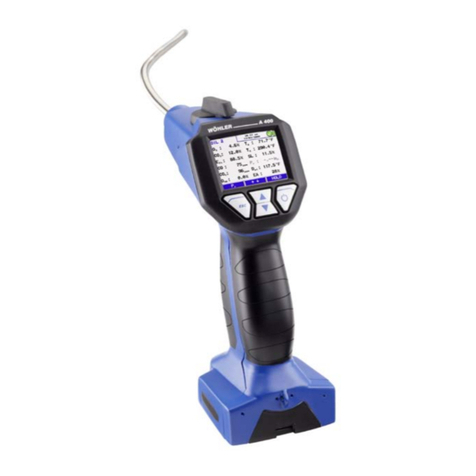
Wohler
Wohler A 400 User manual

Wohler
Wohler A 550 User manual

Wohler
Wohler VIS 2000 PRO User manual

Wohler
Wohler FA 320 User manual
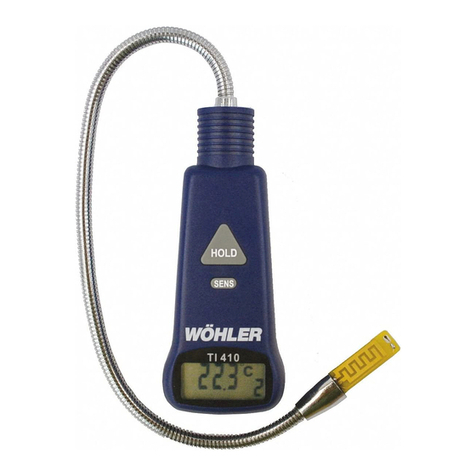
Wohler
Wohler TI 410 User manual
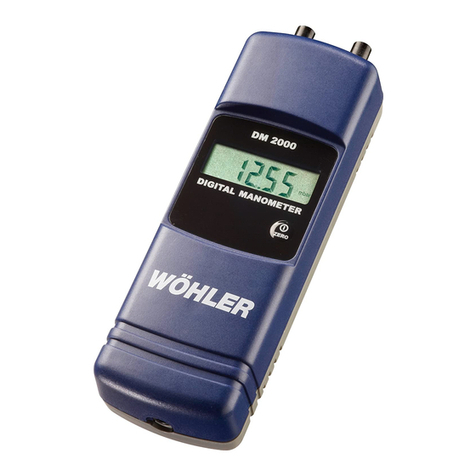
Wohler
Wohler DM 2000 User manual
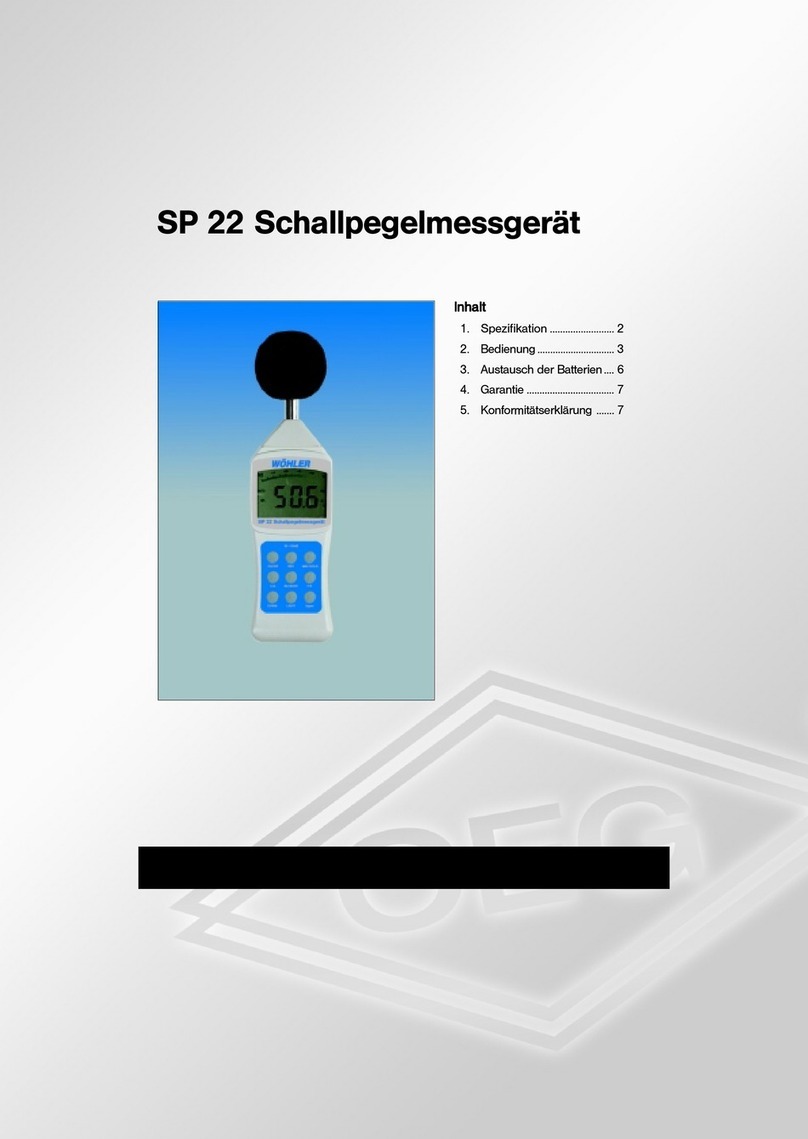
Wohler
Wohler SP 22 User manual
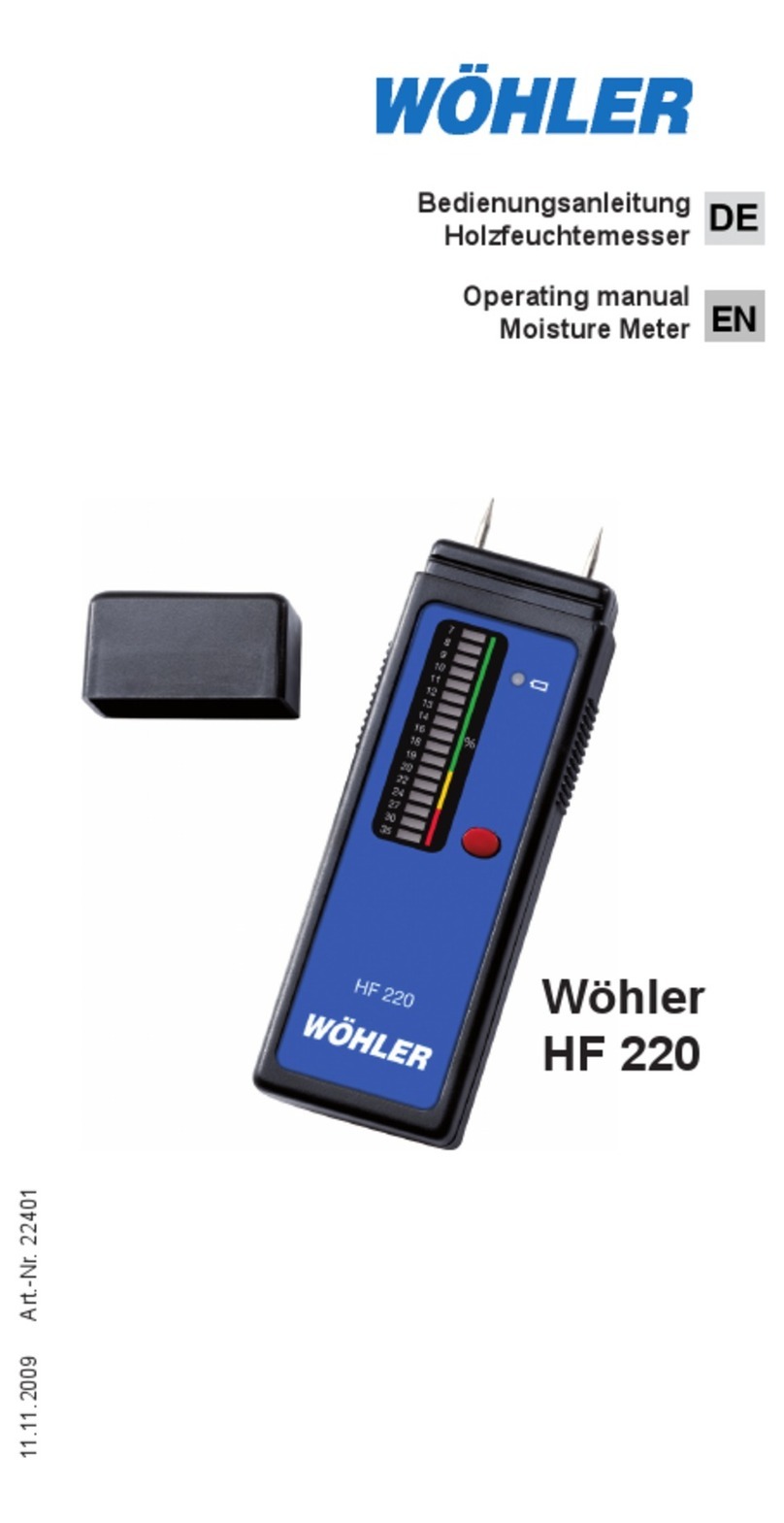
Wohler
Wohler HF 220 User manual

Wohler
Wohler 3343 User manual
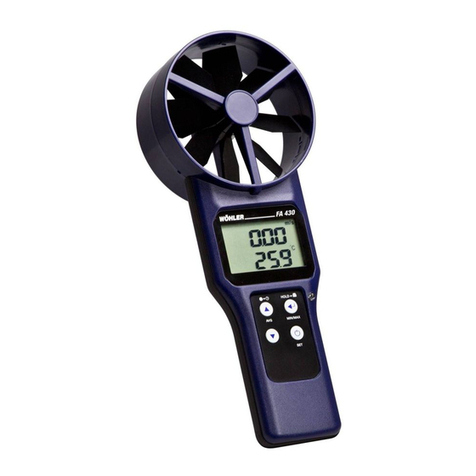
Wohler
Wohler FA 410 User manual

Wohler
Wohler SC 602 User manual
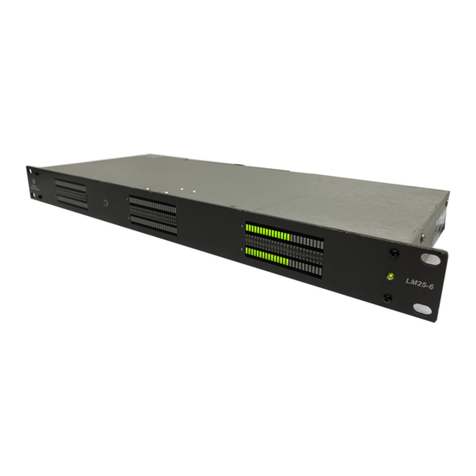
Wohler
Wohler LM25 Analog Series User manual

Wohler
Wohler WA 335 User manual

Wohler
Wohler A 500 User manual

Wohler
Wohler SM 500 User manual

Wohler
Wohler M 603 User manual